Bahjat B. Kadhim1, Fadhil K. Farhan2, Batool Daram Balwa1, Warqaa A. Shakir1
1Department of Physics, College of Science, Al-Mustansiriyah University, Iraq
2Ministry of Science and Technology, Iraq
Correspondence to: Bahjat B. Kadhim, Department of Physics, College of Science, Al-Mustansiriyah University, Iraq.
Email: |  |
Copyright © 2017 Scientific & Academic Publishing. All Rights Reserved.
This work is licensed under the Creative Commons Attribution International License (CC BY).
http://creativecommons.org/licenses/by/4.0/

Abstract
This work is expected to introduce a new class of polymer nanocomposite that might find thermal applications. The objective is to develop new class of nanocomposites by incorporating nanoparticles (TiO2 – ZnO) reinforcing phases into a polymeric resin. Thermal properties included thermal conductivity, effiusivity, diffusivity; heat capacity and thermal resistance have been studied for PMMA as a matrix reinforced in terms of volume fraction of TiO2 and ZnO nanoparticles. Ultrasonic dispersion technique is used to prepare the nanocomposites specimens follow with cold casting technique using flash Teflon molds according to standard conditions. Mathis technique is used to measure thermal properties. Thermal conductivity, thermal effusivity and thermal diffusivity results show that the values were increased by succession of volume fraction of fillers. Heat capacity and thermal resistance results show that the values were decreased progressively by succession of volume fraction of fillers.
Keywords:
Thermal conductivity, Effiusivity, Diffusivity, PMMA, Nanocomposites
Cite this paper: Bahjat B. Kadhim, Fadhil K. Farhan, Batool Daram Balwa, Warqaa A. Shakir, Thermal Properties of (TiO2 - ZnO) / PMMA Nanocomposites, Science and Technology, Vol. 7 No. 1, 2017, pp. 1-3. doi: 10.5923/j.scit.20170701.01.
1. Introduction
The main reason behind the wide spread use of polymers is their unique set of properties such as toughness, light weight, low cost, and ease of processing and fabrication. Even though polymers are not the panacea of industry’s material problems, their unique set of properties have made them one of the important classes of materials finding their way into the electronic industries [1].The combination of two different materials, for instance polymeric, is a simple route for combining the attractive features in order to enhance the deficient characteristics of a particular material [2]. Many common examples of composite materials can be found in the world around us. Wood and bone are examples of natural composites [3]. Recent and successful examples of improved properties that can be achieved by using these procedures are offered by adding to a polymeric phase of organic and inorganic filler, for instance hyper branched polymers and hybrid organic – inorganic nanofillers [4, 5]. In particular, polymer composites reinforced with inorganic fillers of dimensions in the nanometer range, known as nanocomposites, have attracted great interest from researchers, due to unexpected synergistic properties derived from the two components. The most studied polymer nanocomposites (PN) are composed of thermoplastic or thermosetting matrix. Numerous applications in the field of electrical engineering require high thermal conductivity, such as insulating materials for power equipment, electronic packaging and encapsulations, computer chips, satellite devices and other areas where good heat dissipation is needed, and this is even more important for polymers reinforced with different types of fillers. Improved thermal conductivity in polymers may be achieved either by molecular orientation or by the addition of highly heat conductive fillers [6]. Temperature, pressure, density of the polymer, orientation of chain segments, crystal structure, the degree of crystallinity and many other factors may affect the thermal conductivity of polymers [7]. In recent years, extensive researches have been performed upon the reliable thermal characteristics of PMMA reinforced by nanoparticles for thermal insulating applications [8-14].
2. Theoretical Considerations
Thermal conductivity can be measured using several different instrumental techniques. One of these is the differential scanning calorimetry (DSC) as well as the Mathis technique. DSC is a thermal analysis technique which measures heat flow into or out of a material as a function of temperature or time [15, 16]. Measurement of glass transition temperature, melting point, crystallinity, and degree of cure are specific examples of some of the more common DSC measurements. The Mathis TCi is based on the modified transient plane source technique. Thermal conductivity can be calculated using the equation [17]: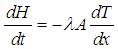 | (1) |
Where: H, Heat (J), t, time (sec), λ, thermal conductivity (W/K. m), T, temperature (K), x, height of test specimen (m), and A, cross sectional area of test specimen (m2). The thermal diffusivity equation (m2 / s) is: | (2) |
Where: Cp: specific heat capacity (J/km. k), ρ: density of sample (km / m3). The effuisivity equation (Ws½ / m 2. k) is: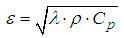 | (3) |
The thermal resistance equation (km. k / J) is:  | (4) |
3. Experimental Work
Nanocomposites are prepared by dispersing nano TiO2 - ZnO kinetically using ultrasonication technique. To achieve better state of dispersion first the nanoparticales were treated with alcoholic medium (ethanol or acetone) for the deagglomeration of the nanoparticle bundles. The treated nanoparticles are then added to the PMMA resin and sonicated for 2 hours at room temperature. Then the mixture is cured under vacuum at (363K) for 10 hours followed by hardener addition by using simultaneous magnetic stirring (100 rpm), for an hour to homogenization. The prepared samples are treated at (353K) for 6 hours in the oven to remove the moisture contents of the samples. The samples are placed between two metal plates under pressure to reduce porosity forming during hardening, before mechanical and thermal measurements. The surfaces of the specimens are mechanically polished to minimize the influence of surface flaws, mainly the porosity. To prepare the nanocomposite samples, molds are made from Teflon. The mold smeared by wax before the mixture is poured into the mold after homogeneity. To calculate the weight of analyzed materials sensitive electronic balance was used. The third generation of Mathis technology expands the capabilities of this rapid, non-destructive thermal conductivity and effusivity testing instrument to a whole new level. The system has broad testing capabilities (0.0- 100) W/m.K in a wide range of temperatures (–323K to 573K). The TCi can be equipped with one or two sensors for increased capacity, and provides accurate thermal analysis of solids, liquids, powders and pastes in less time than any other instrument – only 5 seconds. And because the procedure is non-destructive, samples remain intact undisturbed and reusable after testing.The Mathis TCi is based on the modified transient plane source technique. It uses a one-sided, interfacial, heat reflectance sensor that applies a momentary, constant heat source to the sample. The thick samples are placed directly on the wetted sensor, using an aluminum foil in between in reference according to standard conditions [15]. Aluminum foil is recommended to distribute the heat more evenly over the sample area. Both thermal conductivity and effusivity are measured directly and rapidly, providing a detailed overview of the thermal characteristics of the sample material.
4. Results and Discussion
Thermal properties of the different volume fractions were measured by Mathis TCi technique. The results are summarized in table (1) showed that the results of thermal conductivity (λ) were increased with increasing volume fraction of nano TiO2 and ZnO. Thermal conductivity was improving from 0.22 (W /m.k) for PMMA matrix to 0.44 (W /m.k) for 5 Vol. % of nanoparticles, this because of a good distributions of the fillers and a good thermal conductivity for materials reinforced PMMA matrix according to literature [18].Table 1. Thermal properties by DSC and Mathis TCi 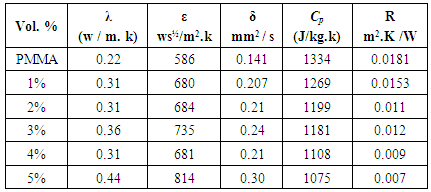 |
| |
|
Thermal effusivity (ε) and diffusivity (δ) were increased with increased volume fractions of nanoparticles. The enhancements of thermal conductivity, thermal effusivity and diffusivity can be explained according to the effect of TiO2 and ZnO nanoparticles reinforced the PMMA matrix, where the polymer materials show a weak thermal conductivity. Thermal conductivities of insulating polymer materials are usually 1-3 orders lower than those of ceramics and metals due to the chain-like structure of polymers; the heat capacity consists of the contribution of two mechanisms: lattice vibrations and characteristic vibrations, which originate from internal motions of the repeating unit. The lattice vibrations are acoustic vibrations, which give the main contribution to the thermal conductivity at low temperatures. The characteristic vibration of the side groups of the polymer chains are optical vibrations, which become visible at temperatures above 100 K generally, the thermal conductivity of amorphous polymers increases with increasing temperature in the glassy region and decrease slowly or remains constant in the rubbery region.Heat capacity (Cp ) results which was dropped from 1334(J/ Kg. K) in PMMA to 1075.62 (J/ Kg. K) in 5 vol. % of nanoparticles due to their low heat capacity. Thermal resistance (R) results were decreased from (0.0181 m2.K /W) for PMMA to (0.007 m2.K /W) for 5 vol. % of nanoparticles. This because of the thermal resistance is reverse of thermal conductivity, so increasing volume fractions of TiO2 – ZnO lead to decreasing of heat capacity of nanocomposites.
5. Conclusions
Thermal effusivity, thermal conductivity and thermal diffusion increase with increase percentage of nanoparticles (TiO2 – ZnO) values. The heat capacity and thermal resistance decrease with increased volume fraction of nanoparticles.
References
[1] | C. A. Harper, Electronic Packaging and Interconnection Handbook, McGraw Hill. (2004). |
[2] | Di Lorenzo, M.L.; Frigione, M. Compatibilization criteria and procedures for binary blends: A review. J. Polym. Eng., Vol. 17, pp. 429–459. (1997). |
[3] | Lionetto, F.; Frigione, M. Mechanical and natural durability properties of wood treated with a novel organic preservative/consolidant product. Mater Des., Vol.. 30, pp.3303–3307. (2009). |
[4] | Frigione, M.; Calò, E. Influence of an hyperbranched aliphatic polyester on the cure kinetic of a trifunctional epoxy resin. J. Appl. Polym. Sci., Vol. 107, pp. 1744–1758. (2008). |
[5] | Esposito Corcione, C.; Frigione, M. A novel procedure able to predict the rheological behavior of Trifunctional epoxy resin/hyperbranched aliphatic polyester misture. Polym. Test., Vol. 28, pp. 830–835. (2009). |
[6] | H.S. Tekce, D. Kumlutas, I.H. Tavman, “Effect of particle shape on thermal conductivity of copper reinforced polymer composites”, Journal of Reinforced Plastics and Composites, Vol. 26, pp. 113-121, (2007). |
[7] | Y. Yang, “Thermal conductivity”, Physical properties of polymers. Handbook, edited by J.E. Mark, Chapter 10, 2nd ed., Springer, (2007). |
[8] | K. Kurabayashi, “Anisotropic thermal properties of solid polymers” International Journal of Thermophysics, Vol. 22, pp. 277-288, (2001). |
[9] | K. Fukushima, H. Takahashi, Y. Takezawa, M. Hattori, M. Itoh, M. Yonekura, “High thermal conductive epoxy resins with controlled high-order structure”, IEEE Conference on Electrical Insulation and Dielectric Phenomena, Boulder, CO, USA, pp.340-343, (2004). |
[10] | L. Ekstrand, H. Kristiansen, J. Liu, “Characterization of thermally conductive epoxy nano composites”, IEEE 28th International Spring Seminar on Electronics Technology: Meeting the Challenges of Electronics Technology Progress, Austria, pp.19-23, (2005). |
[11] | Z. Han, J.W. Wood, H. Herman, C. Zhang, G.C. Stevens, “Thermal properties of composites filled with different fillers”, IEEE International Symposium on Electrical Insulation, Vancouver, Canada, pp., 497-501, (2008). |
[12] | C-Y. Hsieh, S-L. Chung, “High thermal conductivity epoxy molding compound filled with combustion synthesized AlN powder”. Journal of Applied Polymer Science, Vol. 102, pp. 4734-4740, (2006). |
[13] | Lieutenant. J. Ganesan1, D. Edison Selvaraj, [Experimental analysis of thermal conductivity of enamel filled with micro and Nano Composite of SiO2and TiO2] International Journal of Advanced Research in Electrical, Electronics and Instrumentation Engineering Vol. 2, Issue 7, July. (2013). |
[14] | Bu-Ahn Kim 1 and Chang-Kwon Moon [Study on the Mechanical and Thermal Properties of Tio2/Epoxy Resin Nanocomposites] Manuscript Received, (2013). |
[15] | S.M. Marcus and R.L. Blaine, “Thermal Conductivity of Polymers, Glasses and Ceramics by Modulated DSC”, TA Instruments TA086. (2013). |
[16] | E1952, “Method for Thermal Conductivity and Thermal Diffusivity by Modulated Temperature Differential Scanning Calorimetry”, ASTM International, West Conshohocken, PA. (2013). |
[17] | D. Callister, "Material Science and Engineering, An Introduction"; Sixth Edition, Department of Metallurgical Eng., The University of UTAH, John Wiley and Sons, Inc., USA, (2003). |
[18] | Edison Selvaraj, D., C. Pugazhendhi Sugumaran, and A. Siva Prakash. "Characterization of Electrical and Thermal Properties of Enamel Filled with CNT," Proceedings of the Third International Conference on Trends in Information, Telecommunication and Computing. Springer New York, (2013). |