Haruki Tanaka, Yushi Uno, Shintaro Morisada, Keisuke Ohto, Hidetaka Kawakita
Department of Applied Chemistry, Faculty of Science and Engineering, Saga University, 1-Honjo, Saga 840-8502, Japan
Correspondence to: Hidetaka Kawakita, Department of Applied Chemistry, Faculty of Science and Engineering, Saga University, 1-Honjo, Saga 840-8502, Japan.
Email: |  |
Copyright © 2012 Scientific & Academic Publishing. All Rights Reserved.
Abstract
Magnetite was set in the channel of an open system to form the assembled-magnetite membrane controllable by magnet. The starch-granule-dispersed solution (5-50 μm) was flown from the top of the channel to filter starch granule by formed assembled-magnetite membrane. The amount of magnetite was set at 0.1 gram. The length between magnet and magnetite was changed from 0 cm to 3.5 cm to alter the macro-structure of magnetite. It was found that the amount of filtered starch granule was dependent on the length between magnet and magnetite. Detaching the magnet from the magnetite collapsed the macro-structure of magnetite, resulting in the efficient recovery of starch granule by flowing pure water.
Keywords:
Magnetite membrane, Starch granule, Filtration, Separation
Cite this paper: Haruki Tanaka, Yushi Uno, Shintaro Morisada, Keisuke Ohto, Hidetaka Kawakita, Size Filtration of Starch Granules by Novel Assembled-Magnetite Membrane in Open Flow, Science and Technology, Vol. 4 No. 1, 2014, pp. 5-8. doi: 10.5923/j.scit.20140401.02.
1. Introduction
Starch granule is composed of amylopectin and amylose polymerized with mainly glucose monomer at the size of about 1 to 100 micrometer[1]. Their size and distribution have much diversity and dependent on the origin[2]. In cooking, an appropriate control of starch granule’s characteristics, size and shape, enhances the taste. At present, the separation apparatus such as centrifugation etc. has been used. The idea of Molecular Gastronomy to provide the technique of the high quality has been prevailed [3]. The technique for size separation of starch granule is proposed using membrane separation[4], centrifugation[5] and field flow-base separation[6]. Those techniques separate starch granule by the difference of size and density. Separation materials or apparatuses including various separation modes are applicable for various targets in each characteristic. Magnetite moves freely by applying magnet. By the magnetization, the magnetites are assembled in line with magnetic line. Some functional groups are introduced to the magnetite to use for separation of proteins and microorganisms[7,8]. High specific surface area of the magnetite at nano size improves separation performance. The structure of assembled magnetite is dependent on the line of magnetic force, the strength of magnetism, and the distance between the magnet and magnetite.In this study, the filtration of starch granule by the assembled-magnetite membrane set by the magnet in open flow is performed. The magnetite at micro-meter order is synthesized and the assembled magnetite is set by the application of magnet in open flow system as shown in Fig. 1. The density of the assembled magnetite is controlled by the distances. At high density, the gap of the magnetite particles is short. In flowing the starch-granule-containing solution, the starch granule is filtered by the assembled structure. The assembled membrane separates the starch granule at a certain size. By the filtration of starch granule, the cake layer in the upper part of magnetite is formed. The formed cake layer is dependent on the flowing time. To obtain the starch granule filtered, the assembled-magnetite membrane is destroyed by detaching the magnet and then the water is flown through the open system to release the filtered starch granule. 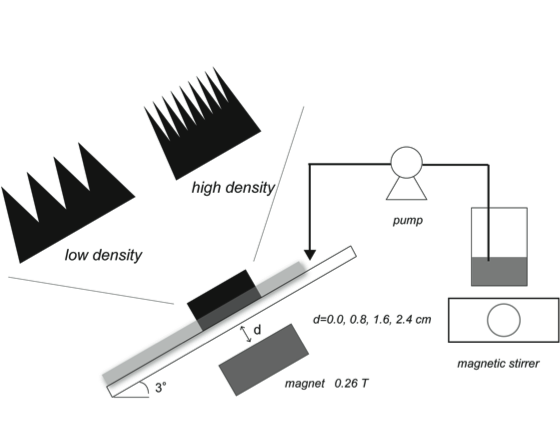 | Figure 1. Illustrated apparatus of the assembled-magnetite membrane by the application of magnetic field |
2. Materials and Methods
2.1. Materials
Starch granule (Potato, KPH7012), FeCl3・6H2O, and FeCl2・4H2O were obtained from Wako Pure Chemical Industries, Ltd. Magnet (2600 G, longitudinal 4.0 cm, side 4.0cm, height 1.0cm) was purchased from BEST Corporation, Japan. Other chemicals used were of analytical grade or higher.
2.2. Preparation of Magnetite
FeCl3·6H2O (0.2M) and FeCl2·4H2O (0.1M) are dissolved in 200 mL pure water. Eight mL of sodium hydroxide solution (10M) was added at 500 rpm and 303 K with stirring. After reaction, the solution was sonificated using the sonificator (USK-4, SND Co., Ltd.). The produced particle was recovered. The obtained black particle was washed with pure water and dried. The yield of synthesized particle was 1.9g. The obtained particle was characterized by FT-IR spectroscopy (JASCO FT/IR-410). The specific surface area was determined by nitrogen adsorption analyzed by BET analysis (BELSORP-miniII-SP. BEL Japan). The particle was ground. The surface of the particle was observed by scanning electron microscopy (JSM-5200, JEOL, Japan) and optical microscopy (VH-S5, Keyence, Osaka, Japan).
2.3. Filtration of Starch Granule by Magnetite Membrane in Open Flow
The synthesized magnetite at the amount of 0.1 gram was set at the open flow in Fig. 1. The flow was made from acrylic board. The length and the width of the flow were set at 32 cm and 0.4 cm, respectively. The angle of the flow was set at 3°. The distance between magnet and the magnetite was 0.0cm, 1.6 cm, and 3.5cm. The location of the magnetite in the flow was 10 cm from the upper part of the flow. The assembled-magnetite membrane was observed by CCD camera (UK-02, Miyoshi Corp., Japan). The starch-granule-containing solution (5.0g/L) was flown from the upper part of the flow using peristat pump (MP-1000, EYELA). The flow rate and the temperature were at 1.0 mL/min and 303 K, respectively. The fraction solution flown through the assembled-magnetite membrane was collected and the concentration of starch granule was determined by turbidity (600 nm, UV-VIS 3100 HITACHI). The amount of starch granule filtered was calculated using the following equation, Amount of starch granule filtered[g-starch granule] 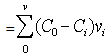 | (1) |
where C0, Ci, and vi are the concentration of starch granule in initial solution, the concentration of starch granule in each fraction, and the volume of each fraction, respectively. Iron ion in the fractions was determined by ICP-AES (ICP-8100, Shimadzu, Japan). The size of starch granule was directly observed by optical microscopy. The sample number observed was more than 300.After the filtration of starch granule by the assembled membrane, the structure of the assembled membrane was destroyed by detaching the magnet from the open flow. Next, 60 mL of pure water was flown at 300 mL/min to recovery the starch granule filtered and the magnetite. The magnetite was recovered from the flown solution by the application of the magnet.
3. Results and Discussion
3.1. Location of Assembled Magnetite in Open Flow
The obtained magnetite was characterized by FT-IR spectroscopy. The hydroxyl group at 3350cm-1 and Fe-O group at 530cm-1 were determined, resulting in synthesizing the magnetite particle. The specific surface area determined was 40 m2/g. Therefore, the obtained magnetite was porous and –OH group was existing on the surface. The image of scanning electron microscopy had the irregularity on the surface. The size of the magnetite was about 1 to 30 μm, from optical microscopy. In water, starch granule was suggested to swell and the size was ranged from 5-50 μm. Starch granules would be filtered by the assembled- magnetite membrane by the size effect. The distance was set at 0 cm, 1.6 cm, and 3.5 cm. The actual magnetic field as a function of gap distance was measured by Gauss meter (MAGNA, MG-701). The strength of the magnetic field at 0, 1,6, and 3.5 cm was 534, 132, and 38 G, respectively, meaning that with increasing the gap the strength decreased. The observed images of the assembled magnetite is shown in Fig. 2. The ellipsoidal shape of the assembled magnetite was formed by the magnetism of the magnet. The shorter the distance between the magnet and the magnetite, the more dense the more assembled magnetite, decreasing the gap between the magnetite particles. This structure has the possibility of the filtering starch granule as a microfiltration membrane. In the case of 3.5cm, the asymmetric structure of the assembled magnetite was formed by the low magnetization and gravity. 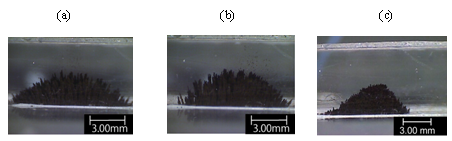 | Figure 2. Optical image of assembled-magnetite membrane formed in open channel. Distance between the magnetite and the magnet; (a) 0.0 cm, (b) 1.6 cm, and (c) 3.5 cm |
3.2. Filtration of Starch Granule by Assembled-Magnetite Membrane
Magnetite membrane has the assembled structure in open flow. Decreasing the gap of the magnetite particles, more colloidal particles were filtered by the narrower pores. The assembled magnetite formed in open flow becomes membrane. The membrane structure is controllable by the amount of the magnetite, the distance between the magnet and the magnetite, and the strength of the magnet. Here, the amount of magnetite was set at 0.1 g constantly, and the distance was changed between 0 cm to 3.5 cm. The starch-granule-containing solution was flown to the assembled-magnetite membrane in open system by peristat pump. The relationship between the flowing time and the filtration ratio of (1-Ci/C0) is shown in Fig. 3 in the case of the distance of 0 cm, 1.6 cm, and 3.5 cm. In flowing the starch-granule-containing solution, the filtration ratio of the starch granule decreased. The more long the distance, the more sharp the reduction of filtration ratio. During flowing, iron ion in each fraction was not determined meaning that no magnetite was not leaked from the assembled membrane.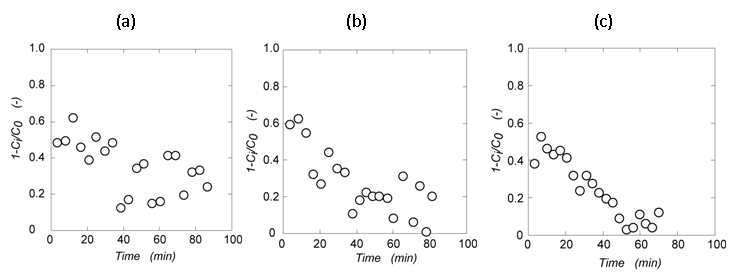 | Figure 3. Filter percentage of starch granule by the assembled-magnetite membrane in change of the distance between the magnetite and the magnet; (a) 0.0 cm, (b) 1.6 cm, and (c) 3.5 cm |
At first stage, the starch granule was filtered by the assembled-magnetite membrane. The filtration scheme of starch granule is shown in Fig. 4; 1) the filtered starch granule formed cake layer in the upper part of the assembled-magnetite membrane, 2) the starch granule overflowed on the top of the cake layer and magnetite, 3) some starch granules flown are penetrated to the gaps of the assembled magnetite by gravity. 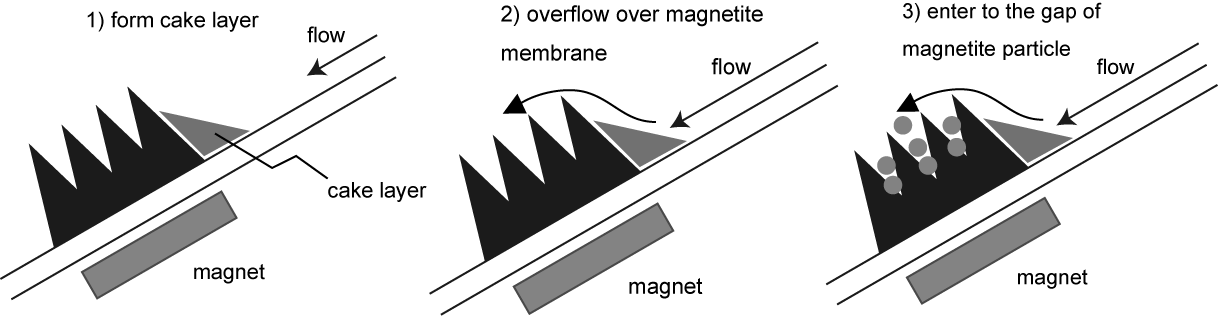 | Figure 4. Filtration phenomena of starch granule by assembled-magnetite membrane |
3.3. Recovery of Filtered Starch Granule
The starch granule filtered was recovered by setting apart the magnet from the assembled magnetite to destroy the membrane structure. The water was flown through the open flow to elute the magnetite and filtered starch granule outside. After elution, the magnetite was recovered by the magnet from the solution and the filtered starch granule was obtained. The recovered magnetite is possibly used for magnetite membrane again. The distance between the magnetite and the magnet was set at 0.8cm. After flowing starch-granule-containing solution and filtration, the filtered starch granule was eluted along with the magnetite in flowing pure water. The recovered starch granule was observed by optical microscopy, as shown in Fig. 5. Compared with size distribution of feed starch granule, the size distribution of filtered starch granule was shifted to the larger size, indicating that the assembled-magnetite membrane is powerful tool to separate the starch granules. Because the gaps of the membrane are controllable, not only starch granules but colloidal particles would be separated and recovered.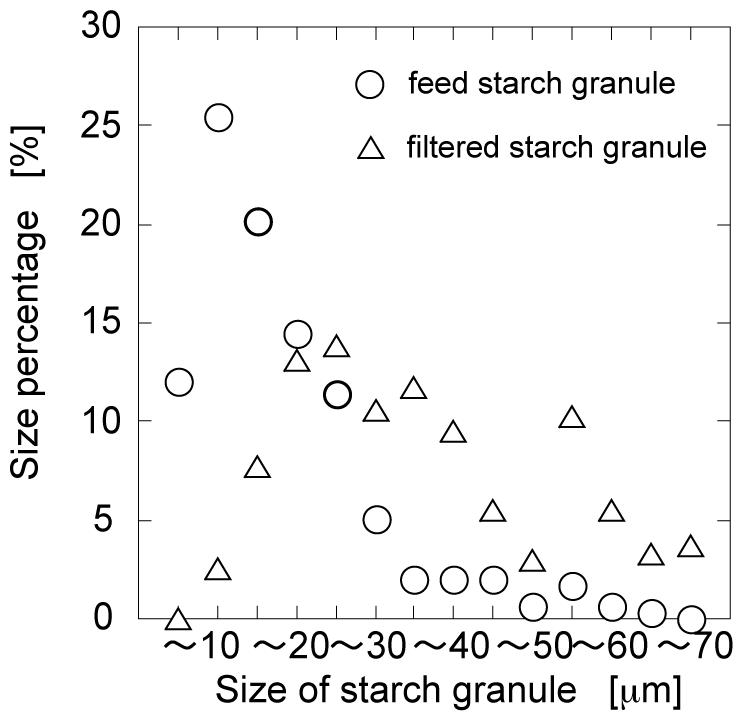 | Figure 5. Size percentage of filtered starch granule by assembled-magnetite membrane. The distance between the magnetite and the magnet was 0.8 cm |
4. Conclusions
Assembled-magnetite membrane by the magnet on open flow was applied for starch granules separation by size effect. The synthesized magnetite was located on the open flow to form the assembled structure. In flowing starch-granule-containing solution, the assembled structure functions as a microfiltration membrane. With changing the distance between the magnetite and magnet, the filtration performance by the magnetite-assembled membrane was changed. After the filtration, the filtered starch granules were recovered by detaching the magnet from open flow and by destroying the macrostructure of the membrane. The observation of starch granules filtered by the optical microscopy demonstrated that the larger size of starch granules was recovered than feed ones. Various pores of the assembled-magnetite membrane regulated by magnet enables us to apply the novel microfiltration membrane for food engineering.
ACKNOWLEDGEMENTS
This work was supported by Saga University Dean’s Grant 2012 for Promising Young Researchers.
References
[1] | Serge, P. and Eric, B. 2010, The molecular structures of starch components and their contribution to the architecture of starch granules: a comprehensive Review. Starch/Stärke, 62, 389-420. |
[2] | Ikeda, D., Ishibashi, K., Noda, T., Hironaka, K., Koaze, H. and Yamamoto, K. 2005, Physicochemical properties of starches from potatoes stored at low temperature. J. Appl. Glycosci., 52, 387-391. |
[3] | Hervé, T. 2006, Food for Tomorrow? How the scientific discipline of molecular gastronomy could change the way we eat?. EMBO reports, 7, 1062-1066. |
[4] | Paul, G. M. and James, K. C. 2012, Extraction of amaranth starch from an aqueous medium using microfiltration: membrane characterization. J. Membrane Sci., 405-406, 284-290. |
[5] | Mahsa, M., Arthur, J. R., Martin, C., Sandra, E. H. and Stephen, E. H. 2003, Partial fractionation of wheat starch amylose and amylopectin using zonal ultracentrifugation. Carbohydr. Polym., 52, 269-274. |
[6] | Moon, M. H. and Giddings, J. C. 1993, Rapid separation and measurement of particle size distribution of starch granules by sedimentation/steric field-flow fractionation. J. Food Sci., 58, 1166-1171. |
[7] | Kekkonen, V., Lafreniere, N., Ebara, M., Saito, A., Sawa, Y. and Narain, R. 2009, Synthesis and characterization of biocompatible magnetic glyconanoparticles. J. Magn. Magn. Mater., 321, 1393-1396. |
[8] | Honda, H., Kawabe, A., Shinkai, M., Kobayashi, T. 1999, Recovery of recombinant Escherichia coli by chitosan-conjugated magnetite. Biochem. Eng. J., 3, 157-160. |