Craig Seidelson
Timken Corporation, Washington State University, University of the West of England
Correspondence to: Craig Seidelson, Timken Corporation, Washington State University, University of the West of England.
Email: |  |
Copyright © 2012 Scientific & Academic Publishing. All Rights Reserved.
Abstract
A problem in the manufacturing of precision bearing rings is reduced outer diameter (OD) cylindricity when grinding inner diameter (ID). Shot blasting is used to remove surface scale from hardened rings prior to grinding. The basic hypothesis is that ID grinding releases residual surface stresses from blasting resulting in reduced OD cylindricity. In this study shot blasted rings are found to exhibit 300% reduced OD cylindricity after ID grinding. Moreover, outer diameters show a pronounced 2-point eccentricity after ID grinding. Sand blasting rings, while just as efficient at removing scale, imparts 40% lower residual surface stresses. No changes in cylindricity or eccentricity are found after ID grinding. Experimental data does not contradict the conclusion when residual surface stresses are high ID grinding imparts sufficient thermo-mechanical loading to release stresses resulting in reduced OD cylindricity.
Keywords:
Grinding, Bearings, Retained stress
Cite this paper: Craig Seidelson, Reduced Cylindricity on Outer Diameter when Grinding Rings on Inner Diameter, Science and Technology, Vol. 4 No. 1, 2014, pp. 1-4. doi: 10.5923/j.scit.20140401.01.
1. Introduction
A problem grinding shot blasted rings is decreased outer diameter(OD) cylindricity after grinding inner diameter (ID). Maintaining OD cylindricity is important since the OD serves as the support surface when grinding ID (Figure 1).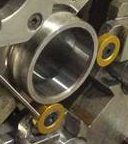 | Figure 1. Supporting Ring on Outer Diameter when Grinding Inner Diameter |
Multiple grind passes are needed to round “popped” rings which increases costs and decreases productivity.When heated in the presence of air steel oxidizes. Oxidation, per Figure 2, appears as a tightly adhered black surface film called “scale.”[1]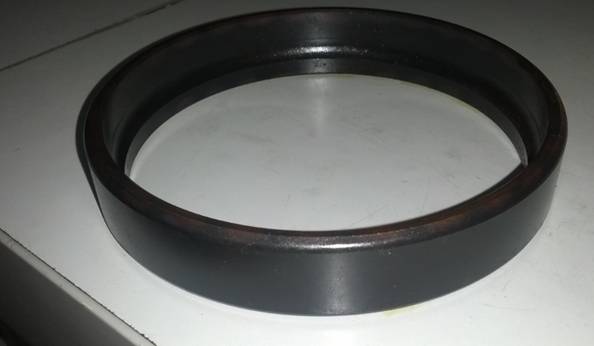 | Figure 2. Scale on Tempered Bearing Ring |
If rings are finish ground without removing scale (per Figure 3) corner radius is not visually acceptable.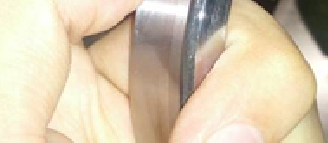 | Figure 3. Corner Radius If Scale Is Not Removed |
While it is possible to prevent scale by tempering parts in a protective environment (i.e. molten salts, exothermic/ endothermic gases or nitrogen) such methods are not economical when compared to removal costs. Common methods of removal include blasting and vibratory polishing. Blasting, unlike polishing, is 20-30 times faster and does not generatewaste water needingtreatment for disposal. It is well documented that blasting workpieces with steel shot(or other media) imparts residual compressive surface stresses[1]. Likewise, there is no shortage of research detailing benefits (and shortcomings) of residual blasting stresses on mechanical performance[2]. What has not been explored ishow problematic residual surface stresses are in the manufacturingof precision rings. The basic hypothesis is that ID grinding releases residual surface stresses resulting in reduced OD cylindricity.
2. Materials and Methods
ANSI 52100 steel bearing rings in this study measured 83mm on outer diameter, 70 mm on inner diameter, and 20 mm high. Rings were hardened and tempered. Before grinding, a blasting operation was used to remove temper scale.To evaluate a decrease in OD cylindricity attributed to the release of residual surface stresses during ID grinding 3 tests were performed.Test 1 imparted a high level of residual surface stress on 5 rings. Test 2 imparted a lower level of residual surface stress on 5 rings. And in Test 3, the control group, scalewas removed on5 rings without blasting.Test 1 parameters:• Media was cast steel shot (hardness 54 HRC)• Each steel shot weighed 0.0014 grams and traveled at 95 m/s• 110 kg per minute of shot was blasted for 2 minutes • 50 kg of rings were shot blasted at one timeTest 2 parameters:• Media was Al2O3 abrasive • Each abrasive grain weighted 0.1 micrograms and traveled at 95 m/s• 0.5 kg per minute of abrasive was blasted for2 minutes • 50 kg of rings were shot blasted at one timeTest 3 control group test parameters:• Media was Al2O3 abrasive stones (4mm x 4mm)• 1000 kg tank vibrated at 50 Hz for 1 hour • Tank was loaded with 335 kg of stones, 50 kg of rings and a constant feed/drain of water to maintain 4 liters of polish fluid in the tank In all three tests, the ring grinding process was identical. While the grinding process and tolerances were proprietary to the manufacturer, Table 1 listed values necessaryto interpret results.Table 1. Grinding Parameters 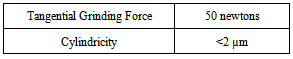 |
| |
|
Grinding power (P) was measured with a watt meter (discounted for machine idle power). Power was converted to tangential grinding force (Ft) using the speed of the grinding wheel (Vs) per Equation (1)[4]. | (1) |
Cylindricity was measured using a least squares method. To evaluate cylindricity profile traces were done in the polar domain.Residual surface stresses were measured using x-ray diffraction. Measurements were taken at the same 3-points (120° apart) per ring. Residual stress tolerances per measurement werealso recorded.
3. Results
Residual surface stresses were presented in Table 21.Table 2. Residual Surface Stress Measurements 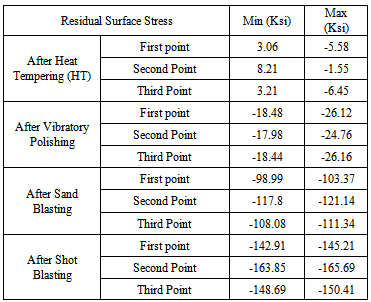 |
| |
|
Shot blasted rings’ OD cylindricity before and after ID grinding were recorded in Table 3.Table 3. Change in Outer Diameter Cylindricity after Inner Diameter Grinding for Shot Blasted Rings 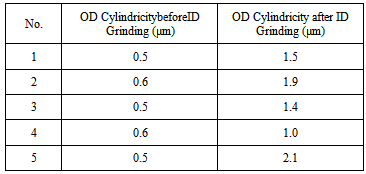 |
| |
|
OD cylindricity traces after ID grinding (Figure 4b) showed 2-point eccentricity not present prior to ID grinding (Figure 4a)2.Sand blasted rings’ OD cylindricity before and after ID grinding were recorded in Table 4.Table 4. Change in Outer Diameter Cylindricity after Inner Diameter Grinding for Sand Blasted Rings 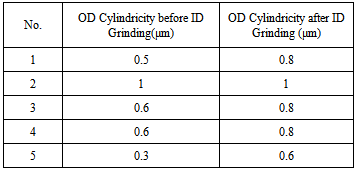 |
| |
|
For sand blasted rings OD cylindricity traces after ID grinding (Figure 5) did not show 2-point eccentricity.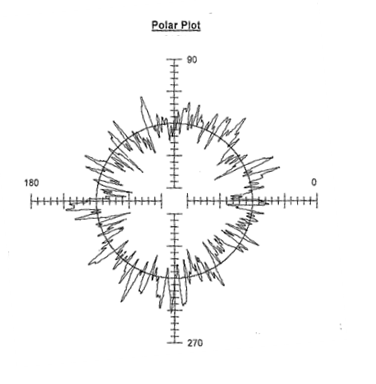 | Figure 4a. Shot Blasted Rings’ Outer Diameter Cylindricity before Inner Diameter Grinding |
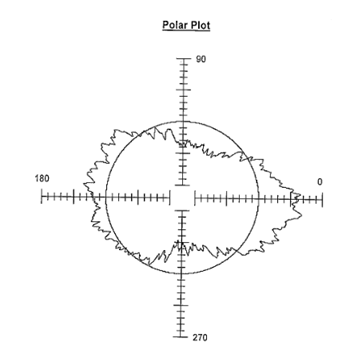 | Figure 4b. Shot Blasted Rings’ Outer Diameter Cylindricity after Inner Diameter Grinding |
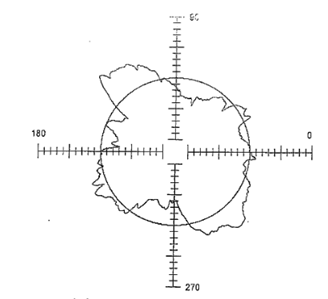 | Figure 5. Sand Blasted Rings’ Outer Diameter Cylindricity after Inner Diameter Grinding |
Vibratory polished rings’ OD cylindricity before and after ID grinding were recorded in Table 5.Table 5. Change in Outer Diameter Cylindricity after Inner Diameter Grinding for Vibratory Polished Rings 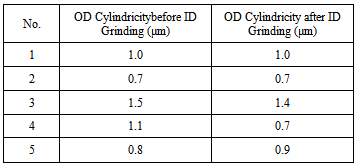 |
| |
|
For vibratory polished rings OD cylindricity traces after ID grinding (Figure 6) did not show 2-point eccentricity.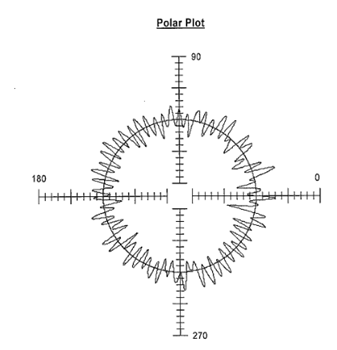 | Figure 6. Vibratory Polish Rings’ Outer Diameter Cylindricity after Inner Diameter Grinding |
4. Analysis
To evaluate whether the release of residual surface stresses during ID grinding could have caused an increase in OD cylindricity Student’s t tests were performed. T tests were single-sided, paired, of repeated measure and accounted for heteroscedastic variance in test data. Differences in cylindricity were evaluated at a 95% confidence interval.For shot blasted rings there was a 99.7% probability OD cylindricity decreased after ID grinding. The 1.04um average OD cylindricity decrease was significant considering (a) this represented a 300% change and (b) cylindricity tolerance was 2 µm. Moreover, outer diameters exhibit a pronounced 2-point eccentricity which did not exist prior to ID grinding.For sand blasted and vibratory polished rings there was no statistical difference in OD cylindricity before and after ID grind. There was also no observed shift in eccentricity.Student’s t tests of X-ray diffraction results showed polishing, sand blasting, and shot blasting imparted different levels of residual surface stress (Figure 7). The -153 ksi average residual compressive surface stress after shot blasting was 40% higher than sand blasting and 6 times higher than polishing. 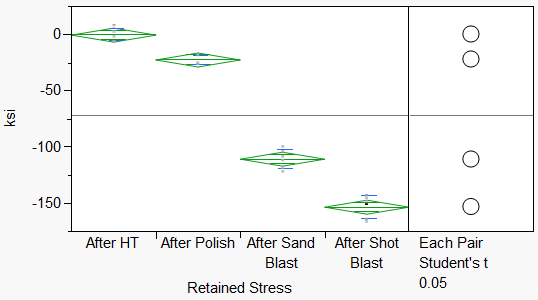 | Figure 7. Residual Surface Stresses on Bearing Rings |
For the ring geometry tested when ID grinding at 50 newtons of force if retained compressive surface stresses were ≤100 ksi no changes in OD cylindricity or eccentricity were observed. If, under the same ID grinding conditions, retained compressive surface stresses were ≥153 ksi, OD cylindricity decreased and eccentricity increased.
5. Discussion
Previous researchers found heavily shot peened metal to be thermodynamically unstable[4]. Instability was traced back to heterogenous plastic deformations between workpiece core and surface[4]. Prior studies, likewise, found residual stresses could relax significantly under thermo- mechanical loading[4]. The low ID grinding force used in this work resulted in high specific grinding energy[4].It was not inconsistent with prior findings to surmise ID grinding specific energyin this research provided sufficient thermo-mechanical loading to release residual surface stresses. When residual surface stresses were high enough it was not incompatible with the data to conclude their release resulted in decreased OD cylindricality. Following this line of logic the residual surface stresses from polishing and sand blasting were so low their release during ID grinding did not affect OD cylindricality.Besides decreased OD cylindricality, shot blasted rings in this study showed a pronounced shift to 2-point eccentricity after ID grinding. Findings were consistent with prior studies on retained core stresses in rings. Metallic rings, when releasing heat treatment stresses, were found to exhibit eccentricity. This was especially true of rings with large OD to wall thickness ratios[4]. In this study rings had an OD to wall thickness ratio of 12.8 (consistent with a thin wall definition.)[5] It is not incompatible to conclude the release of surface stresses in the rings during ID grinding introduced eccentricity.
6. Future Research
This work provides a foundation for answering future questions. For the ring geometry studied at what minimum retained surface stress level does ID grinding lead to a decrease in OD cylindricity? Is there athreshold specific grinding energy needed to release retained surface stresses? Does this specific grinding energy level vary with ring geometry? If these questions could be answered it may be possible to tailor specific ID grinding energies to the retained stress levels and ring modulus thereby preventing OD cylindricity changes.
Notes
1. A negative sign (-) indicated residual compressive stress2. In all polar traces 1 gradation equals 0.05 µm
References
[1] | VÁŇOVÁ, P. “The Effect of Heat Treatment on the Structure of Scale Layer and its Removing by Pickling in Reducing Melt”. 22ndInternational Conference on Metallurgy and Materials May 15th - 17th 2013. |
[2] | Weingärtner, R. Hoffmeister, J. Schulze, V. “Generation and Determination of Compressive Residual Stresses of Short Penetration Depths.” Materials Science Forum.vol 768-769 pgs 580-586. |
[3] | Shaw, B., Aylott, C., O’Hare, P., Brimble, K. “The Role of Residual Stress on the Fatigue Strength of High Performance Gearing.” International Journal of Fatigue. 2003. volume 25, pg 1279-1283. |
[4] | King, R., Hahn, R. Handbook of Modern Grinding Technology. (1998) Service Network Inc., Auburn, MA. |
[5] | Kirk, D. “Residual Stress in Shot Peened Components.” (2003) Available fromhttp://www.shotpeener.com/library/pdf/2004003.pdf [Retrieved Oct 15 2013] |
[6] | Totten, G., Howes, M., Inoue, T. Handbook of Residual Stress and Deformation of Steel (2002). ASM International. Ohio. |
[7] | Luan, W., Jiang, C., Ji, V. “Thermal Relaxation of Residual Stresses in Shot Peened Surface Layer on TiB2/Al Composite at Elevated Temperatures.”Materials Transactions, Vol. 50, No. 6 (2009) pp. 1499 to 1501. |
[8] | Marinescu, I., Hitchiner, M.,Uhlmann, E., Rowe, W.B., Inasaki, I. Handbook of Machining with Grinding Wheels. CRC Press. 2007 Florida. |
[9] | Da Silva, A.D.,, Guo, Z., Schille, J.P.,, Altan, T.,, Cetlin, P.. “Prediction of Geometric Distortion and Residual Stresses In Hot Rolled and Heat Treated Large Rings Through Finite Element Modeling”. 2012 Brazilian National Research and Development Council report.pp 235-246. |
[10] | Lindeburg, M. Civil Engineering Reference Manual for the PE Exam.(2012) 13th Edition.,Professional Publications Inc.Belmont, CA. |