Nkeleme Emmanuel Ifeanyichukwu1, Osuji Emmanuel C.2, Nzeneri Oluchukwu P.1, Okoye Ujunnwa Callista3, Enemuo Chinyere Francisca4
1Department of Building, Federal University of Technology Owerri, Nigeria
2Department of Building, Ahmadu Bello University Zaria, Nigeria
3Department of Management Technology, Federal Universty of Technology Owerri, Nigeria
4The Aministrative Staff College of Nigeria (ASCON)
Correspondence to: Nkeleme Emmanuel Ifeanyichukwu, Department of Building, Federal University of Technology Owerri, Nigeria.
Email: |  |
Copyright © 2021 The Author(s). Published by Scientific & Academic Publishing.
This work is licensed under the Creative Commons Attribution International License (CC BY).
http://creativecommons.org/licenses/by/4.0/

Abstract
Health and safety audit in the construction industry especially in a developing country like Nigeria cannot be undermined considering the high risk and casualties experienced over several decades of poor or lack of health and safety practices. The research conducted an overview study of the companies that practice health and safety audit and their implementation. The sample population was drawn from five major states in Nigeria, with high construction activities and the respondents were project/site managers. From the findings it was obvious that health and safety audit was not a subject of consideration among construction firms in Nigeria, as only 17% practiced it. From that percentage, the level of implementation was less than an acceptable mean of 3.0, indicating poor implementation. The research recommends an inclusion of a standard health and safety audit review of previous jobs, as well as a current health and safety plan in the tendering procedures for new contracts.
Keywords:
Health, Safety, Audit, Construction industry, Nigeria
Cite this paper: Nkeleme Emmanuel Ifeanyichukwu, Osuji Emmanuel C., Nzeneri Oluchukwu P., Okoye Ujunnwa Callista, Enemuo Chinyere Francisca, A Review of the Implimentation of Health and Safety Audit Practices on Construction Sites in Nigeria and the Way Foreward, Journal of Safety Engineering, Vol. 10 No. 1, 2021, pp. 1-4. doi: 10.5923/j.safety.20211001.01.
1. Introduction
Safety issues have gained vital importance throughout the construction industry. Many construction companies around the world are implementing safety, health, and environmental management systems to reduce injuries, eliminate illness, and to provide a safe work environment in their construction sites (Rafiq, Dongping and Syed, 2008). According to Muiruri & Mulinge, (2014) Health and safety at construction sites deals with both physical and psychological well-being of workers on construction sites and other persons whose health is likely to be adversely affected by construction activities. It is of primary concern to employers, employees, governments and project participants. Health and safety therefore is an economic as well as humanitarian concern that requires proper management control.In most developing countries, health and safety consideration in construction project delivery is not given priority, and employment of safety measures during construction is considered a burden (Mbuya and Lema, 2004). Health and safety has been identified as a parameter which should be used along with the traditional parameters: cost, quality and time, to measure the success of projects. The reasons for considering safety and health are human factor, legislation and financial issues (Adan, 2004). Jannadi and Bu-Khamsin (2002) summarized the important research on site safety from 1976 to 1993 and concluded that site safety was associated with factors such as site management and control, site supervision and leadership, site safety program, and the influence of the general contractor on subcontractors.An audit is a systematic and wherever possible, independent examination to determine whether activities and related results conform to planned arrangements and whether these arrangements are implemented effectively and are suitable to achieve the organizations policy and objectives. (BS 8800:1996 Guide to Occupational Health and Safety Management System) A safety audit examines and determines whether or not a company’s daily activities and processes conform to their planned health and safety arrangements as well as the government laws. An audit further identifies whether or not the planned arrangements are implemented effectively, and are suitable to achieve the organizations health and safety policy objectives. Often it is a failure in the health and safety management that results in serious incident. Safety audits assist in identifying failures within a system, process or program and the information gathered helps to determine the best course of corrective action.
2. The Four (4) Key Focus of Safety Audit
Audits of work sites are conducted for the purpose of health, safety, and fire hazard identification. Work site audits also provide an evaluation of compliance to Occupational Safety and Health Administration (OSHA) standards relating to ergonomics, respirator use, hearing conservation, blood-borne pathogens and use of personal protective equipment. Safety Audits are primarily to check the effectiveness of the various programs, they do not take the place of regular facility inspections. There are four basic questions a safety audit should answer. The persons or team designated to conduct the audits should take a fact finding approach to gather data. These auditors should be familiar with both the company program and the various local, state and federal requirements.All safety audit comments, recommendations and corrective actions should focus on these four questions:1. Does the program cover all regulatory and best industry practice requirements?2. Are the program requirements being met?3. Is there documented proof of compliance?4. Is employee training effective – can and do they apply specific safe behaviors?
3. Requirements for Evaluating and Improving Health and Safety Audit Practices
According to Occupational Safety and Health Administration (OSHA) (2017), seven (7) requirements have been identified to evaluate and improve health and safety audit practices. These are 1. The use of Performance indicators to track progress toward program goals,2. The use of lagging and leading indicators to track performance, 3. The analyses and sharing of performance data with workers, 4. The initial review (and subsequent annual reviews) conducted by management to evaluate the program and ensure that it is fully implemented and functioning as planned, 5. The involvement of workers in all program review activities, 6. The examination of key processes by the program reviews to ensure that they are operating as intended, and 7. The modification of the program as needed to correct shortcomings.
4. Methodology
A quantitative approach was taken in conducting this research; this is attributed to the large population of construction companies and sites. Questionnaire properly designed to articulate the implementation of health and safety audit among the construction companies was used in the quantitative approach. The research implored multiple techniques of data collection, which includes the random sampling technique, the systematic and the purposive sampling technique. This is due to the complexity of the data and the need to properly articulate and acquire the relevant data for the research. The population was systematically grouped based on areas with high density of ongoing construction works thereby considering five (5) states, such as Abuja, Lagos, Porthacourt, Kaduna and Kano. The research was divided into two phases, the first phase was to identify the number of firms that practiced health and safety audit. This phase involved the random distribution of questionnaires within the proposed states. The second phase went further to group the firms that practiced health and safety audit to determine the conformity of their practices to OSHA requirements. Therefore, a population of 4619 was drawn from the total number of registered construction companies in the Nigerian Corporate Affairs Commission (CAC). A sample size was drawn using the Cochran (1967) formula of sample size determination as shown below. Population Size (N)= 4619Z Score (Confidence Level = 95%)= 1.96Margin of Error (E)= 5%Proportion of the population (P)= 0.8Q value= 0.2For Large PopulationSample Size is calculated using the formula given belowS = (Z2 * P * Q) / E2Sample Size= 245.86Therefore, the sample size for phase two of the research was set at 250 respondents, with 50 from each state.The respondents were site/ project managers and health and safety auditors/officers, this is because of their responsibility in issues relating to health and safety on sites as well as in the decision-making and management of the construction projects. The analysis was conducted using mean, mean error and Standard deviation, to accurately transform, present and validate the data.
5. Findings and Discussion
This section dealt specifically with the respondent’s data as shown in the tables and figures below.Phase one shows the number of Table 1. showing the response of construction firms  |
| |
|
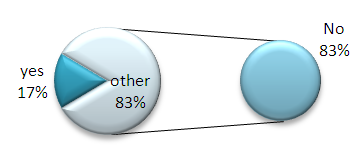 | Figure 1. Companies that carry out health and safety audit (Source: Field survey 2018) |
From figure 1, the number of construction companies involved in health and safety audit practices account for 17%, while those that are not involved in health and safety audit practices account for 83%, this indicates that very few construction companies are involved in health and safety audits in the country. This can further go to explain some of the health and safety issues faced by the construction industry over several decades.Table 2. Showing the response of construction firms that practice health and safety audit 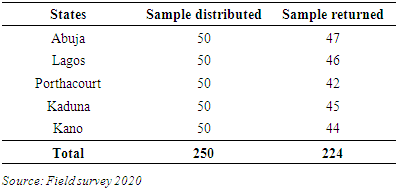 |
| |
|
Table 2 shows the number of questionnaires administered and the respondents in each state. From the table, Abuja had the highest respondents of 47 and total respondents of 224 in all the states. | Figure 2. Number of permanent staffs (Source: Field survey 2020) |
Figure 2, shows the number of permanent staffs employed by the construction company, companies with 0-10 staffs were the least in the practice of health and safety audit which accounts for 7.59% of the respondents, this is followed by companies with 11-50 staffs which accounts for 14.73% of the respondents, companies with 51-100 staffs accounts for 25.0% of the respondents. Companies with staffs above 100 accounted for the highest response (52.68%). This indicates that majority of the companies involved in health and safety audits are large construction firms as identified by Abdul Azeez (2012) which classified construction companies based on staff strength.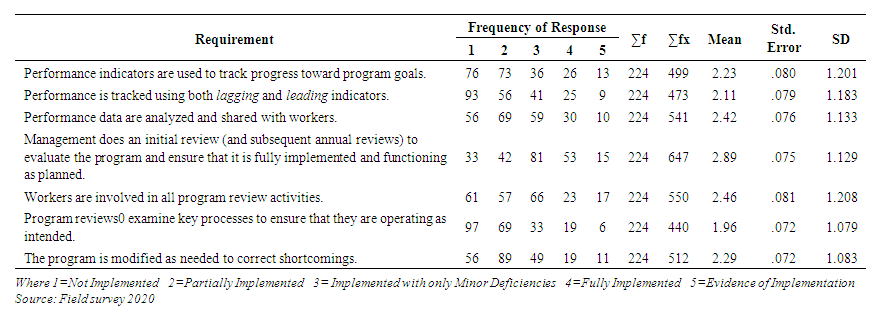 | Table 3. The implementation of health and safety audit |
From table 3 showing the implementation of health and safety audit by construction companies in the country, showed a low level of implementations as all the requirements were below the acceptable mean of 3.0 This aligns with the findings of HSE (2009), Okolie and Okoye (2012) and Uduakobonge, Edidiong and Christian (2016) whose reports reveals the poor state and attention given to Health and Safety. The use of Performance indicators to track progress toward program goals had a mean of 2.23, the use of lagging and leading indicators to track performance had a mean of 2.11. The analyzing and sharing Performance data with workers had a mean of 2.42, the initial review (and subsequent annual reviews) conducted by management to evaluate the program and ensure that it is fully implemented and functioning as planned, had a mean of 2.89. The involvement of workers in all program review activities had a mean of 2.46. The examination of key processes by the program reviews to ensure that they are operating as intended had a mean of 1.96, while the modification of the program as needed to correct shortcomings had mean of 2.29.
6. Conclusions and Recommendations
Providing “safe and healthy” workplace requires a proactive, preventive approach that seeks to eliminate all risk factors inherent in a job or at least reduce the impact of their occurrence on sites. This process is checked by the term “Health and Safety Audit”. A typically effective Health and Safety Audit should encapsulate the actions managers at all levels take in order to create a safe working environment. a safety audit is the most effective method by which the factors that could affect the health and safety at the construction worksite could be addressed. The actual worksite conditions could be taken into account through the audit and based on the happenings at the worksite, the suggestive measures could be given.From this research, it is however obvious that the country’s construction industry in Nigeria has a long way from achieving a fully healthy and safe working environment considering its poor implementation of the health and safety audit system, which is meant to checkmate poor health and safety practices, and ensure better strategies of mitigating these challenges on construction sites. The research will therefore recommend a proper monitoring and evaluation exercise of construction firms, by relevant stakeholders or regulatory bodies. There should also be an inclusion of a standard health and safety audit review of previous jobs in the tender documents and a current health and safety plan, to ensure compliance.
References
[1] | AbdulAzeez, A. D. (2012). Development of a Prototype Electronic Document and Record Management System (EDRMS) for Small and Medium Building Firms. (Published doctoral thesis), Department of Building, Ahmadu Bello University, Zaria. |
[2] | Adan, E. (2004). Factors affecting Safety on Construction Projects. Department of Civil Engineering, Palestine. |
[3] | Health and Safety Executive, Successful Health and Safety management. HMSO Books, London. (2009). |
[4] | Jannadi, O.A., Bu-Khamsin, M.S. (2002), “Safety factors considered by industrial contractors in Saudi Arabia”, Building and Environment, Vol. 37 No.5, pp. 539–547. |
[5] | Mbuya, E. and Lema, N. M., Towards Development of a Framework for Integration of Safety and Quality Management Techniques in Construction Project Delivery Process. Proceedings of the First International Conference of CIBW107 – Creating a Sustainable Construction in Developing Countries, 11-13 November, (2002). |
[6] | Muiruri G.and Mulinge, C. (2014) Health and Safety Management on Construction Projects Sites in Kenya A Case Study of Construction Projects in Nairobi County. FIG Congress 2014 Engaging the Challenges – Enhancing the Relevance, Kuala Lumpur, Malaysia 16-21 June 2014. |
[7] | Occupational Safety and Health Administration (OSHA). (2017) 29 CFR, Washington, D.C., (www.osha.gov) (December 2017). |
[8] | Okolie, K. C. and Okoye, P.U. Assessment of National Cultural Dimensions and Construction Health and Safety Climate in Nigeria. Science Journal of Environmental Engineering Research, (2012). |
[9] | Rafiq M. C. Dongping F. and Syed M. A. (2008). Safety Management in Construction: Best Practices in Hong Kong. Journal of Professional Issues in Engineering Education and Practice. DOI: 10.1061/(ASCE)1052-3928(2008)134:1(20). |
[10] | Uduakobonge E. Udo, Edidiong E. Usip and Christian F. Asuquo. (2016) Effect of Lack of Adequate Attention to Safety Measures on Construction Sites in Akwa Ibom State, Nigeria. Journal of Earth Sciences and Geotechnical Engineering, vol. 6, no.1, 2016, 113-121 ISSN: 1792-9040. |