Jayandran Mohan
Vel Tech Rangarajan Dr. Sagunthala R & D Institute of Science and Technology, Chennai, India
Correspondence to: Jayandran Mohan, Vel Tech Rangarajan Dr. Sagunthala R & D Institute of Science and Technology, Chennai, India.
Email: |  |
Copyright © 2018 The Author(s). Published by Scientific & Academic Publishing.
This work is licensed under the Creative Commons Attribution International License (CC BY).
http://creativecommons.org/licenses/by/4.0/

Abstract
In August 2009, workers were killed and injured as concrete of the tank of a biogas plant near Aluva, India exploded owing to a suspected pressure build-up. The enforcement agencies reported that the plant exploded while three workers were standing on top of the tank. Two bodies were recovered from the site later. Bio Dynamic Biogas plant which is located in Colwick Industrial Estate, Nottingham, UK having the capacity to process 150,000 tonnes of food waste a year and producing 2.5MW electricity. On September 21, 2017 two personnel’s received serious injuries due to explosion & collapse of storage tanker. Similarly, Eight biomass boilers and a shed containing wood chips ignited at Corby Biomass Systems Limited in Fermanagh, Ireland on January 12, 2017. Piles of biomass at the Tracy Storage Facility for Agra Marketing ignited in Tracy, California on May 20. The facility stores organic materials for composting and biofuels. This incidents emphasizes appropriate HAZOP Studies, Risk Assessment reviews, regular monitoring, maintenance and Inspections are required to avoid Fire Accidents and explosions in Biogas Plant. This Paper would act as review for HAZOP Study for Biogas storages and Fire Risk Assessment for different Bio Gas plant feedstock.
Keywords:
Bio Methane, HAZOP, Fire Risk Assessment, Feed stock, Bio Gas Storage
Cite this paper: Jayandran Mohan, Bio Gas Holder HAZOP Study and Semi Quantitative Fire Risk Assessment of Organic Matter - Keys for Fire Accident Prevention in Bio Mass Plant, Journal of Safety Engineering, Vol. 7 No. 2, 2018, pp. 43-49. doi: 10.5923/j.safety.20180702.01.
1. Introduction
Bio gas Plants obtaining raw materials from various sources [1] like cattle wastes, poultry wastes, agricultural wastes, organic wastes like paper, wood wastes, aquatic plants, residues from Food Manufacturing sectors. Bio gas plants basically consist of Fermenter Digester [2] and Storage tank. The above mentioned Feedstock would be charged into the fermenter as liquid slurry. The process flow and layout of bio gas plant as follows, the feedstock would be stored and transferred into feeding module thereby moves into Fermenter or Stage I digester. Bio gas fermenter consists of two inlets. One is to feed the bio mass feed stocks which would be at lower level and other outlet is at top of the fermenter to collect sludge to the sludge collector. The Bio gas would be collected from top of the tank and diverted to Bio gas storage tank. The collected sludge form the Stage I digester would be fed into Stage II Digester to extract the traces of Bio gas. Finally, the Sludge is disposed would be considered as Manure [3] for agriculture fields. The Bio gas collected would undergo gas cleaning process which would be termed as Methane enrichment process in which the methane gas concentration would be increased by purifying the gas. The primary principle of bio gas production would follow anaerobic digestion process in which at the first stage organic matters are converted into non-methanogenic compounds and in the next level it has transformed predominantly into methane gas.In a Bio gas plants the following hazards like common electrical hazards due to misuse of electric comments mainly overloading or absence of overload tripping system, Infections while processing bio waste due to exposure of micro organism, Chemical hazard and respiratory oriented issues, trip & fall, mechanical hazards, health hazards, Chemical Hazards due to exposure to ammonia, Hydrogen Sulfide, Trips and Falls nears Bio gas tanks pits, Heat and Noise hazard due to machine operation may occur. As the organic slurry are stored in temporary tanks and while maintain the confined spaces like Fermenter or tanks the chances for Drowning would be more. As the Digester also contains Hydrogen Sulphide gas the chances for Chemical Asphyxiation would be more. As the workers use to involve in charging the feedstock and to ensure the proper mixing of slurry or while marinating the tanks they use to perform Work at Height activities so appropriate Edge Protection, Guard Rail and Ladder arrangements are required to avoid fall hazards. Near the Digester the process parameters mainly the temperature would be maintained at 71 °C. This temperature range would also be maintained in nearby utilities. Appropriate Hot Insulations, Barricading, warning signage should be implemented so that the workers would not intact with this heat sources and burns can be controlled.Among the above mentioned hazard, in general Fire & Explosion Hazards [4] are predominant and causing more property damage as well as fatalities. Biogas consists mainly of 60% methane and other gases like Carbon di oxide, Hydrogen Sulphide. As Methane density is lesser than air, it mostly collected in top of the surface. So that, it is recommended to store [5] to Methane in Spherical Bullets and Bio gas holders rather than tanks. If methane presents in the range of 5 to 15% concentration and if it exposed to 12% Oxygen it leads to severe fire and explosion. Mostly in Bio gas plants, leakage of gas in the transporting pipelines or the heavy pressure build up in the Bio gas holder or the leakage of gas in the vents are the primary causes of fire accidents. Another cause is due to improper storage and insufficient fire control measures in the organic storage area. As Bio gas can be used a efficient fuel and it is acting as an alternative for non renewable fossil fuels, the demand for this gas is increasing day by day. Another important in Bio gas production is, apart from alternative fuel nature it is also considered as effective way of handling waste and considerable amount of solid waste are efficiently managed [6, 7]. The reason why Fire hazards are given high importance in Bio gas plant is, it may cause explosion leads to direct and indirect accident costs like production shut down /delay, Hospitalization of injured workers, loss of skilled man power, severe property damage, business and reputation loss.By analyzing the Major Hazard Incident Data Service (MHIDAS), it is evident the Fire accidents are dominating in Bio Gas plants and the incidents as follows. In Italy on 1997 while repairing concrete silo of biogas plant in the municipal sewage plant due to unsafe welding explosion occurred leads to severe property damage and two were killed in the incident. In Germany on 2006 near Gottingen two fermentation tank of Bio gas plant has bursted and seven million liters of sludge spilled over. Due to this explosion nearby fuel oil tank got damaged and 1000 liters of fuel oil leaked and the overall loss estimation is about €10m. Again on 2007 near Riedlingen in Southern Germany a massive fire explosion occurred in fermenter and bio gas storage tank in which the estimated property damage was around €1.5m.In India on 2009, during the commissioning stage of bio gas reactor near Edathala Panchayat Ernakulam District, the bio waste storage area got exploded as the workers attempted to do welding near to it. Three workers fell into the thick slurry, and two died. Workers, standing nearby including the welder, were thrown away by the explosion and two of them died instantly. In India on 2013 in Solapur Bio gas Energy Ltd, while in the process of maintaining of Bio gas tanks which involves drilling and explosion activity, two labors were severely injured and one was died as the activity carried without doing gas testing. On September 21, 2017 in Bio Dynamic Biogas plant which is located in Colwick Industrial Estate, Nottingham, UK two personnel’s received serious injuries due to explosion & collapse of storage tanker. At Corby Biomass Systems Limited in Fermanagh, Ireland, biomass boilers and a shed containing wood chips got ignited in 2017. In California organic storage material in Tracy storage facility got ignited. During the study, it has observed Fire hazards are prone to occur nearby Bio gas Storages, Bio gas collection & Pipe transporting areas, Biomass Boiler section and Organic Matter Storage area. In the above mentioned areas, the fire hazards are very predominant in Bio gas tanks and Bio Mass Feedstock area.Active monitoring techniques [8] are the key to avoid fire hazards in the Bio gas plants. A regular Hydrostatic testing in Digester and Bio gas tank must be carried out. Before working into the confined spaces appropriate gas testing to be carried out. As the above incidents is clearly indicating along with fire accidents due to methane, the chances of asphyxiation due to presence of Hydrogen Sulphide, Carbon dioxide in gas purifiers and anaerobic digesters. Leakage in Bio gas pipelines and through vents also to be taken care effectively. To effectively execute all the above activities, deep process safety study is highly required in Bio gas Plants. Though the Hazard identification, different levels of risk assessments are required for the Bio gas plants, a two key major hazard areas like Bio gas storage facility and Organic matter storage yard has selected and deep process safety has executed. While doing the process safety study the following techniques were adopted like Understanding the Operations of Bio Gas Plant, Analyzing the accident videos of Bio gas plants with detailed Investigation underpinning immediate, root cause of the accident, detailed study about the operating and storing procedures of Bio gas, assessments of bio gas storage. Bio gas Storage including Gas in & out piping facility and Organic Matter Storage area, as the severity of the fire accidents would be more in this areas. As a proactive control measures, HAZOP review for the Bio gas Storage tanker, Semi Quantitative Risk Assessment of organic matter feedstock has executed and emphasized to be considered as key for fire accident prevention in bio mass plant.
2. Methodology
The prime objective of this study is to identify and control the Fire accidents in Bio Gas plants based on the past incident Case Study. The past Bio Gas plant explosion accidents indicate that the Bio Gas Holder and Organic Matter Storage area acting as important sources for fire incidents. So, HAZOP review of Bio gas holder and Fire Risk Assessment & review has suggested as the solutions to resolve this issue. To do this research study systematically, the following methodologies were adopted• Bio gas Plant Incident Analysis• Safety Visit to Bio Gas Plant• Understanding Process & Instrumentation Diagram of Bio Gas holders• Hazard Identification in Organic Matter Storage Area• Drafting HAZOP review for Bio Gas Holders• Calculating Semi Quantitative Fire Risk Assessment for different organic matter feed stock which is flammable in nature.Bio Gas Plant Incident Analysis: By gathering the accident data of the Bio Gas Plant which has occurred between 1997 to 2017, it has observed apart from other Hazards like Electrical Hazard and Mechanical Hazards in operating the process equipments, Biological Hazards while handling Organic Slurries, the most predominant one is Fire oriented incidents. Moreover, these fire incidents are causing Major economic as well as property damage to the organization. Also, it is evident this major fire accidents are causing fatalities and major injury to the personnel’s. It has also observed, by analyzing the incident history these fire accidents are occurring mainly due to the leakage or presence of Methane gas and the probability for this gas presence is more across the plant right from slurry mixer tank to Bio gas storage tank. But it is very evident the chances for this Methane Fire Explosion is more near Bio gas tank either due to leak in the pipelines or due to the rupture or leak of Bio gas from the tank or due to unsafe act of the workers while carrying out Hot Works near or inside the confined space of Bio gas storage tank due to improper gas testing while doing hot works like welding mainly during maintenance of the tank. The incident history is clearly indicating that the fire incidents are occurring in three major areas like the Organic Matter Storage area where the hydrocarbon enriched fuel source are existing and in this area the fire accidents are predominant due to improper stacking and storage of fuel substances also mainly due to improper fire detection, control and fire suppression system. This safety issues are mainly due to lack of risk assessment and the management, key Safety personnel’s in understanding the combustible nature of the bio feed stocks especially when they are using mixed feed stocks of assorted organic matter which contains different levels of Methane Content. Similarly, in case of Bio gas tanks irregular maintenance and inspection like carrying out Hydrostatic Testing’s and essential inspection requirements like Hydrostatic Testing not performed in regular basis are also the reasons for fire incidents in this areas. As Methane is light flammable gas, it is always having tendency to rise up, comparing with Fixed Roof Tanks, membrane based storage tank makes the gas to spread uniformly across the surface not only on the top of the tank which may reduce the rupture or pressure forces exerted over the top of the tank. This lack in safety analysis about the tank models also one of the reasons for fire incidents in Bio gas tanks due to heavy pressure especially on the upper most part of the tank. This incident is clearly indicating that the detailed Process Safety Studies, Regular review on this process study report, regular quantified risk assessment, implementing updated technologies as part of continual improvement is essential to control incidents especially fire incidents. Moreover, instead concrete fixed roof tanks, flexible Double Membrane tanks are highly recommended to store Bio gas.Safety Visit to Bio Gas Plant: To understand about the Bio gas plant operation, Safety visit has executed. During this visit Visual Observation inspection technique has adopted. The process operations in the Bio gas plants have observed. The Anaerobic Digestion Process, Organic Storage Yard and Bio gas storage tank, gas pipelines, distribution has observed. By interacting with the workers and the concern Safety Manager the technical issues and the proactive control measure which has implemented has understood. During this Safety Visit the following Hazard Identification technique like Legislation document reference to analysis general Fire Safety precautions and control measures which has required and implemented in the plant has analyzed, The incident data has analyzed and hot spots have identified along with this evaluation of existing control measure have analyzed. The manufacturers & designers suggested recommendation in operating the Process equipment like Slurry mixer, Anaerobic Digester, Bio gas storage tank and the operator mode of operation, maintenance cycle which has adopted in par with designer specification has verified. The Task analysis of the specific major hazard activity like Hot work especially maintenance of Anaerobic Digester and Bio Gas Storage tank has analyzed. During this process, the permit system which has followed for this kind of activities and the checklist which has used also validated. By referring the incident history of that plant, the incident which has occurred for the past 5 years their Trend and Pattern has analyzed. While analyzing this accident history, the hot spot that is the area where the accidents/incidents are happening most frequently has discussed with the Safety Personnel of the company. The documentation check that is Safe System of Work, Permit of work which had given for the past one year has gathered and compared with the incident rates. By doing this analysis, it has observed No Major fire incidents has occurred in this company for the past 5 years but Major incidents like leak of Bio gas leak at minimum level has occurred near the Bio gas tank similarly minor fire incident has also observed in organic matter storage area. But Major incidents not observed in the Anaerobic Digester and Sludge collector. After understanding the incident history, a detailed observation has done in the plant and few observations that is the unsafe act and the unsafe condition which has existed shared with the Company’s Safety Personnel. This visit has clearly indicated apart from other Hazards, few fire oriented incidents have occurred in the Organic Matter Storage Yard and gas leak in Bio gas plant which can be considered as Major hazard category of the Bio Gas Plant.Understanding Process Instrumentation Diagram of Bio Gas Holders: To understand the Process Safety about Bio Gas Holders tank and to do further study basic analysis of Bio Gas Holders process controls have analyzed. In general, gas flows to be monitored. Each tank have predefined capacity and allowable level of volume that can be stored. It is to ensure that the level should not exceed with that limit. So Flow Meter would be an essential equipment to be installed in the Bio gas tanks and appropriate instrumentation to be done for continuous monitoring of the same. Another important aspect which causing rupture of the tank is Pressure. Tank Design Pressure can be verified from the Process Manual, Design Manual and thumb rule is gas inside the holders should be stored should be less than Design Pressure. To monitor and maintain this, Pressure Gauges to be installed in tank using pressure transducers and appropriate monitoring to be done from the control panel. Temperature is another crucial factor for Methane gas explosions. Temperature sensors like thermocouples to be installed and variations in the temperature to be monitored. Leak detector can be implemented to detect Methane leaks and immediate warning to trigger further emergency procedure. Methane gas flow, pressure at which it is stored inside the tank, temperature which has maintained in the tank are integrated process parameters which has to be sensed through appropriate sensing, gauging equipments. All this readings to be cascaded looped through instrumentation principles and monitored through Industrial automation principles so that the fire, explosion likelihood can be controlled.Hazard Identification in Organic Matter Storage Area [9]: Organic Matter Storage area that is, Bio feed stock storage area is the crucial area in which the fire accidents are use to happen mainly due to lack of fire hazard identification, lack of fire risk assessment and implementation of fire control measure as required. To carry out the fire hazard identification the following steps like Identifying the Fire Hazards in the work place like identifying the other possible fuel source existing the organic matter storage area mainly any liquid fuels mainly diesel /petrol may be kept to operate electric portable electric equipment to be verified. Improper storing and stacking of organic matter has done in storage area to be verified. Presence of ignition sources like damaged electric cables, damaged or unauthorized electric connections if any exist in the storage area to be ensured. Also, any other hot work activities have occurred nearby the storage area to be verified. This can be done by validating Permit to Work Documents that has issued. Finally, presence of oxygen source nearby the storage area to be examined. Especially, if workers are doing gas welding they would use Oxygen Cylinders and Acetylene Cylinders for this process. So, the storing area of these cylinders to be found out and to be ensured whether the layout has properly drafted such a way safe distance has maintained between Storage area and gas cylinder ware house to be confirmed. Once the Hazard identification has done, detailed fire risk assessment to be triggered.Drafting HAZOP review for Bio Gas Holders: After completing the analysis of the process parameters and process instrumentation verification of Bio gas holders. HAZOP [10] review to be executed. During this HAZOP review the validation, evaluation of current control measure would be done and the requirement of additional measure would be recommended. During this process, parameters would be valid and the actions that can be performed by the implemented control measure would be analyzed. So that by doing HAZOP study, what kind of deviation can be happened in the established system can be identified, reason for that can be analyzed, if it not controlled what consequence may occur can be verified. Other way, level of risk mitigation that can be achieved by the implemented control measure and further improvements can be suggested. This Process Safety Study has to be done at regular intervals to ensure the Bio Gas Holder. Most of the fire incidents are occurring in the Bio gas holders either the organization are doing detailed HAZOP study or they are not reviewing HAZOP study at the specified intervals. By analyzing the process parameters, process instrumentation diagram model HAZOP study has drafted for Bio Gas Holder especially for Double Membrane Bio gas Holder.Calculating Semi Quantitative Fire Risk Assessment for different organic matter feed stock which is flammable in nature.: After Hazard Identification has done, the next step is to execute the Fire Risk assessment in the Organic Storage area. During this Fire Risk Assessment, the risk to be evaluated. While doing this assessment, the likelihood for the fire to occur and the impact it would create should be rated. In this assessment the flammability nature of the Bio feed stock would be analyzed based on that only likelihood for fire can be calculated.
3. Hazop Review Study on Bio Gas Holder
The Process Safety HAZOP [11] identifies the possible deviation that may occur in the system. During that adhoc situation, how the possible implemented control measure would effectively work can be found out and the further improvements to manage or to mitigate it would effectively be drafted in the report. As the HAZOP team would composed of many Technical Engineers, HSE Specialist, Line Managers it would be a good brain storming so that different process parameter variation can be analyzed and the whole plant and the process safety can be studied. It his highly recommended that this HAZOP report should be reviewed if any process or technology changes in the plant. It is also suggested to do HAZOP review if new equipment installed or even if legal changes occur. In Bio gas plants, irregular review of HAZOP document is also one cause for the fire incidents. If the HAZOP report is up to date, the safety of the plant would be ensured, as it regularly evaluates the implemented control measure. In the below HAZOP Study, the design features, possible process parameters and the level of deviation with control measure validation has drafted and it is highly recommended that this type of process safety study to be done and importantly regular review to be executed. Comparing with concrete roof tank, Double Membrane Bio Gas Holders are considered are most safe one, as the light gas Methane pressure on top of the tank would be managed effectively in Membrane holders. Double Membrane Bio Gas holder consists of two membranes. The outer membrane acts as a protective layer and the inner membrane used to store the gas. The inner membrane can be monitored by inspection glass. This membrane depends on the fill level it moves up or down. The bottom of the membrane is properly sealed and attached to the foundation by the anchor ring. Each Storage membranes are designed after considering the internal pressure, wind and snow loads. In general, Flame resistant, tear resistant, Fungicide treated, UV protected materials were selected for Membrane Gas Holders.The Fan ensures to maintain the pressure so that it will withstand external forces such as snow fall and wind. To prevent air escaping from the Membrane, Non Return valve has fixed. To monitor the outer membrane pressure, Auto pressure shut off valve arrangement has done. Gauging facilitates the exact usage of storage area and cascades the control devices like flare route. The primary reason for Bio gas holder explosion is due to increase in pressure and leak from the bio gas holder / pipelines. In this HAZOP study main focus has given on Pressure factor.General Design & Process Parameters• Allowable Sizes 10 to 12000 m³• Design Pressure 5 to 50 mbar• Biogas Temperature (Max) +50°C• Acceptable Negative Pressure -2.5mbarStandard Operating Conditions• Ambient Temperature -30°C to +50°C• Permissible Snow Load 150 kg/m2• Permissible Wind Speed 150 km/hHAZOP Study on Double Membrane Bio Gas Holder [12, 13] 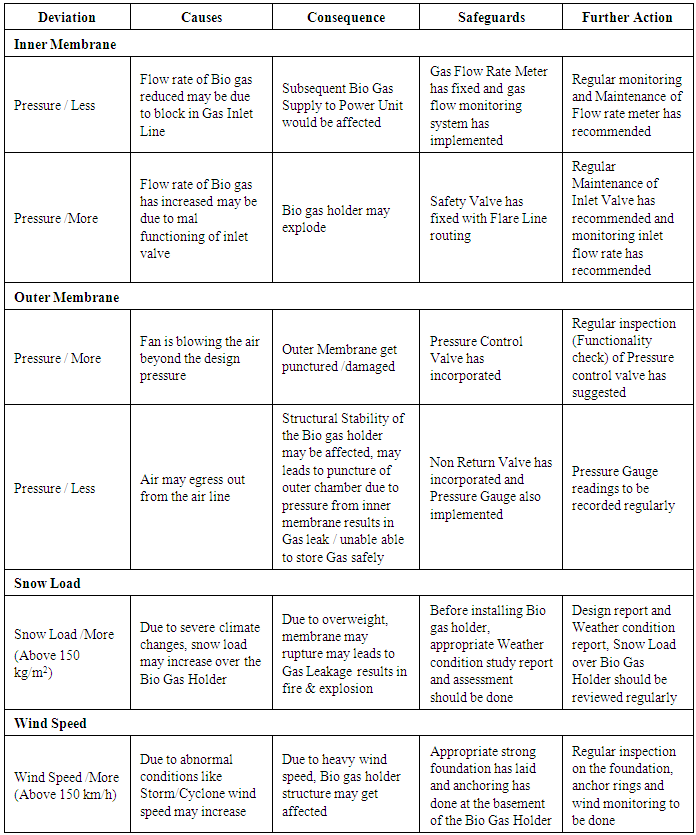 |
| |
|
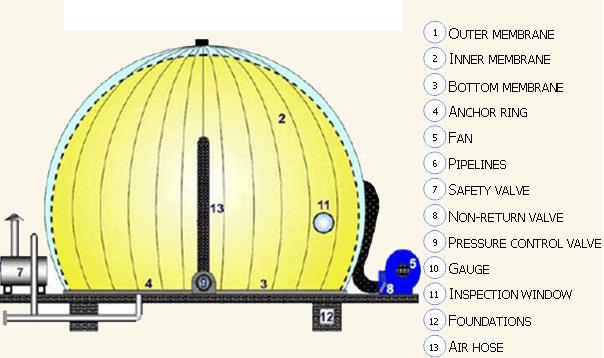 | Figure 1. Double Membrane Biogas Holder |
4. Semi Quantative Risk Assessment on Organic Matter Storage Area
The purpose of the risk assessment [14] is to identify the hazards and to evaluate the risk so that effective control measure can be implemented. Risk Assessment is considered as active monitoring control measures it helps for risk mitigation in advance. The main advantages in Semi Quantitative risk assessment is, it will quantify the risk which will emphasize the risk level so that the High, Medium, Low level risk ranking can be done and accordingly respective control measure can be taken within the specified time scale. There would be a consistency in the approach such as, the likelihood of the hazardous even to occur and the severity it would cause would be rated. Then risk ranking, level of risk can be determined.To produce Bio gas various kinds of organic matter are used. Cattle manure can be considered as one of the best feedstock for Bio gas production. Pig, sheep and goat manure, Poultry droppings, Horse manure, wood chips can also be used as raw materials for Bio gas production. It has generally estimated that 40 to 70 m3 of Bio gas can produced daily if the moisture content is between 85 to 92%. The below table shows the amount of methane present in the feed stocks.Table 1. Methane Content in different Feedstock 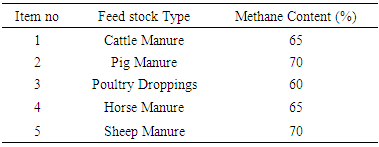 |
| |
|
It is evident that the organic manure feedstock are flammable in nature and appropriate control measures must be taken to avoid fire accidents in the storage areas. By doing semi quantitative risk assessment [15] of the feed stock, the level of fire hazard can be identified.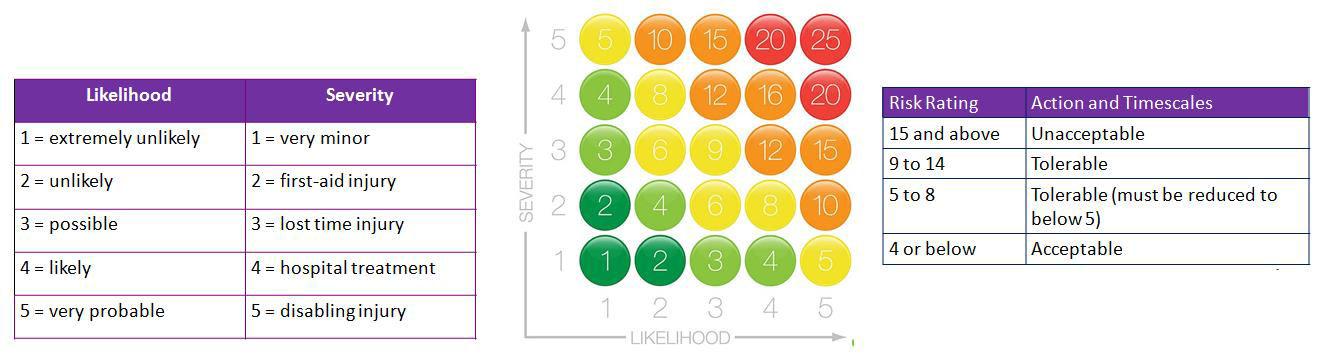 | Figure 2. Semi Quantitative Risk Assessment Inputs |
By referring Table 1, based on the methane content, the feedstock has classified into three categoriesClass I Feedstock (Pig & Ship Manure 70% Methane content)Class II Feedstock (Cattle & Horse Manure 65% Methane Content)Class III Feedstock (Poultry Droppings 60% Methane Content)During Semi Quantative Fire Risk Assessment calculation, it has considered that the Likelihood [16] and Severity of the fire is proportional to the Methane Content percentage in the feed stock.Table 2. Semi Quantative Fire Risk Assessment for different Feed stocks 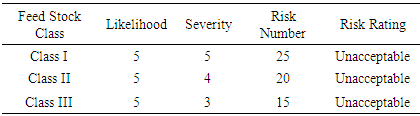 |
| |
|
The above risk assessment is clearly indicating that the appropriate fire deduction, prevention and control system must be implemented, regularly inspected in the Organic Matter Storage Area.
5. Conclusions
Bio gas is one of the non renewable energy sources which would be in great demand in future as it has produced from Organic Waste. Many Countries are constructing Bio Gas Plants and the importance of Process Safety is the key factor to be considered in Bio gas Safety, as the accident rates are increasing.The primary hazard in Bio gas plant is Fire Hazard and Explosion which is majorly occurring in Bio Gas holder and Organic Matter Storage area. By implementing effective Pressure Control in the Bio gas holder and by incorporating effective Fire prevention & control measures in the organic matter storage area the likelihood and severity of the fire incidents can be highly controlled in the Bio Gas Plants. Due to change in ambience conditions and the different feed stocks are used in Bio Gas production, regular HAZOP review on Bio Gas Holder & regular inspection on Fire prevention system in Organic Matter Storage area is highly recommended.
References
[1] | Biomass and Biofuels: Advanced Biorefineries for Sustainable Production and Distribution 1st Edition by Shibu Jose, Thallada Bhaskar. |
[2] | Managing Biogas Plants: A Practical Guide by Mario Alejandro Rosato. |
[3] | Metcalf and Eddy (1979). Wastewater Engineering: Collection, Treatment, Disposal, McGraw-Hill, New York. |
[4] | Tomas Chrebet, Jozef Martinka Assessment of Biogas Potential Hazards. International Journal of Engineering/2012, 39-42. |
[5] | Volkmar Scroeder, Bernd Schalau, Maria Molnarne Explosion protection in biogas and hybrid power plants In: International Symposium on Safety Science and Technology; 2014: Elsevier, China:pp. 259-272. |
[6] | Hurst, P., & Kirby, P. (2004). Health, Safety and Environment: A Series of Trade Union. |
[7] | Educational Manuals for Agricultural Workers. Geneve: International Labour Organisation. |
[8] | Salvi, O., Chaubet, Ch., Evanno, S., (2012). Improving the Safety of Biogas Production in Europe. Revista de Ingeniería, 37, 57-65. |
[9] | Bottelberghs, P.H., (2000). Risk analysis and safety policy development in The Netherlands, Journal of Hazardous Materials 71, 59-84. |
[10] | HAZOP and HAZAN: Notes on the identification and assessment of hazards. By Trevor Kletz, published by IChemE. |
[11] | Hazop & Hazan: Identifying and Assessing Process Industry Hazards, 4th Edition, by Trevor A. Kletz. |
[12] | Practical HAZOPS for Engineers and Technicians Revision 4 David MacDonald B.Sc (Hons.) Instrument Engineering Pg 5-9. |
[13] | Practical HAZOPS for Engineers and Technicians Revision 4 David MacDonald B.Sc (Hons.) Instrument Engineering Pg 37-61. |
[14] | Guidelines for the Management of Change for Process Safety 1st Edition by CCPS (Center for Chemical Process Safety). |
[15] | Quantitative Risk Assessment in Fire Safety by Ganapathy Ramachandran, David Charters. |
[16] | Guidelines for Risk Based Process Safety by CCPS. |