Anatoly N. Rozenbaum
Institution of Russian Academy of Sciences, Institute of Automation & Control Processes, Vladivostok, 690041, Russian Federation
Correspondence to: Anatoly N. Rozenbaum, Institution of Russian Academy of Sciences, Institute of Automation & Control Processes, Vladivostok, 690041, Russian Federation.
Email: |  |
Copyright © 2012 Scientific & Academic Publishing. All Rights Reserved.
Abstract
The paper addresses the problem of ensuring reliability of human-machine systems under conditions of uncertainty and limited initial data. The definition of residual operating life is proposed for such systems based on the minimax approach. The developed algorithms are tested on human-machine systems operated in real conditions.
Keywords:
Residual Operating Life, Human-machine System, Individual State, Minimax Estima
Cite this paper: Anatoly N. Rozenbaum, Parameters of Condition and Dependability of Human-Machine System in Operation, Journal of Safety Engineering, Vol. 3 No. 1, 2014, pp. 13-17. doi: 10.5923/j.safety.20140301.02.
1. Introduction
Human–machine systems (HMS) form a large share of industrial and other equipment, in particular, measuring systems. Their reliability is almost always associated with ensuring safety of human as an important and integral part of the systems. On the other hand, there is an interdependence between the machine and its operator. Working capacity violation of human operator can lead and in many cases leads to negative consequences, sometimes even catastrophic. Accordingly, technical failures of HMS may pose a serious hazard for the life not only of the operating staff, but other people as well.However, there are significant differences in the character and progression pattern of a failure depending on whether it occurred in the technical component (TS) or human component (HS) of HMS. These differences make it possible to take separate measures to ensure failure-free operation of HMS on human-operator and technical levels.Such approach is a typical and commonly accepted practice. However, ignoring the relationship between parts of HMS can lead to inadequate assessment of the condition of HMS as a whole. A more expedient approach seems to be in the recognition of the machine part and human operator to be equal partners, with the contribution of each of them to HMS failure-free operation being dependent upon that of the other. In this case, based on the minimax principle (taking into account the worst case scenario), dependability and reliability of the system as a whole may be defined as the dependability and reliability of the part more prone to failures in the given operation period and, consequently, less reliable.
2. Statement of the Problem
Among various indicators of dependability and reliability of technical systems the reliability measure over a predetermined interval of time should be considered as the most general parameter. In practice, it is one of the most widely used parameters. However, its calculation always requires gathering large volumes of data (a priori and a posteriori). Operation of HMS in real life rarely allows us to obtain the required information, in qualitative and/or quantitative terms. In other words, the use of the reliability measure and other statistical parameters (average time of failure-free operation, availability measure, etc.) is difficult in practice. More acceptable ones are the indicators that can be used under conditions of incompleteness and uncertainty of the initial information basis, in particular, those ones using the minimax approach.Among such parameters there is the indicator of residual operating life
. This measure, generally speaking, was developed to estimate the potential failure-free operation time of technical systems with regard to parametric failures[1], so at first let us consider the construction of
when it is used in the task of obtaining reliability of the TS of HMS.Let
be a vector of parameters, which determine the condition of TC.Under the influence of destabilizing factors, vector y changes in operation interval T as an indefinite process y(t), t∈T, y∈Y. When y(t)∈D, ∀t∈T, where D is the operating domain, TS of HMS is operating normally. | (1) |
whereА, В are the set limits;D is an orthogonal parallelepipedThe results of measurements z(t) of parameters y(t) in the interval Tp ⊂ T may contain an additive and statistically uncertain error e(t) | (2) |
With regard to error e(t) it is only known that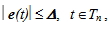 | (3) |
whereΔ is a known vector, whose components are defined by the properties of the measuring equipment (and personnel), i.e. they are determined by the specifications of the measuring equipment, as well as by the specifics of the work, which needs to be done.Let us describe residual operating life of TC as a time interval
wheretn is the time of the latest measurement of Y(t) in the interval Tn ⊂ T,tb is the first moment of y(t) reaching the boundaries of D, i.e. Pt(D).
3. Determination of Residual Operating Life of Technical System
To form a criterion describing residual operating life of TC let us use criterion "operating reserve"
, defined for each component y(t) as the distance in the current moment of time between
and the nearest point in Pt(D)[1]. Then it is possible to consider variations of S resulting from the change of y under the influence of destabilizing factors as a uniformly accelerated motion S, i.e. | (4) |
whereSj0 is the value of j-th operating reserve at the beginning of TC operation (corresponds to the nominal status of TC for the j-th component of y, and is given by the specifications of TC operation);Vj is the rate of change of the j-th operating reserve in the direction of the nearest point in Pt(D), ∀t ∈T;aj is the acceleration of change of the j-th operating reserve in the direction of the nearest point in Pt(D), ∀t ∈T.In principle dependence (4) can be viewed as an approximation of yj(t),
found from the well-understood physical considerations. Accordingly, the results of control of y(t), described by relations (2) and (3), can be regarded as the legitimate results of control of S(t). Finding estimate
, t∈T will then correspond to deducing estimate
t∈T from the control result, i.e.
, t∈T. Taking into account dependence (4), determination of
is reduced to working out estimates Vj and
from the results of control z(t), t∈Tp⊂T. Having found
and Pt(D) it is easy to deduce
, with respect to each coordinate
or
.Limited and uncertain initial data in the problem of finding
make it reasonable to use the minimax principle here[2]. Taking into account this principle, residual operating life for TC as a whole can be defined as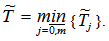 | (5) |
Based on the minimax principle, without making any assumptions or hypotheses on the statistical properties of the aggregate, one can find, in addition to dependence (5), with guaranteed for the existing body of initial data certainty both the interval estimates given by: | (6) |
and the point estimates
, defined as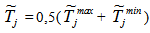 | (7) |
It is easy to see that the estimate (7) is optimal in the sense of minimum of the largest possible estimation error. | (8) |
4. Extension of the Application Area of Residual Operating Life Parameter to HC of HMS
The key problem in constructing the indicator
is a question about the possibility of forming a vector of measured parameters y, which determine the condition of ТS and are sensitive to its changes. Even for complicated TS the answer to this question is easily found from the technical documentation (instruction manuals) of virtually any technical systems, including measuring systems. For biological objects, and, therefore, for HS of HMS, the formation of vector y may constitute quite different and complex task. This task actually belongs to functional medical diagnostics, which, by measuring certain biological parameters, seeks to diagnose the state of a disease that potentially can render a human unable to perform his work functions. In terms of this task it is evident that the measured parameters being far or close to the boundaries of the allowed domain (actually Pt(D)) enables judgment about the possibility of further participation of the personnel in the operation of HMS. For the most part, the parameters of interest are associated with the control of cardiovascular system as the basis for life and health of the human organism as a whole[3].One of parameters is the optical density of myocardium[4]. For its measurement a broad range of introscopy devices have been developed, including cheap, compact and freely available ones. Modern tools to control other parameters of the cardiovascular system in many cases can be designed (or are already available) to be compact and readily available. So when monitoring the condition of TS it is advisable to carry out control over the parameters of HS of HMS as well. In other words, the problem of formation of vector y nowadays is solved sufficiently. Therefore, there is an obvious opportunity to extend the range of the indicator
application to HS of HMS. In doing so it can be noted that the formation of minimax estimates (5-8) both for TS and HS is reduced to the same procedures as described above.Uniformity of the formation procedures of minimax estimates (5-8) makes possible to work out a single unified algorithm for determination of residual operating life of HMS, with due consideration given to its both parts (TS and HS). The algorithm may be presented as follows. With dependencies (2) and (3) in mind, based on the results of monitoring the condition of TS (and HS) one can formulate a system of inequalities 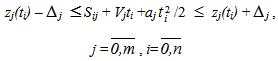 | (9) |
Reasoning from the physics of changes of TS (and HS) condition, system (9) can be supplemented with a restriction that function (4) extremum does not belong to the operation period of TS (and HS), defined as Т =[t0, tk], where t0 and tk are the start and end times of TC operation, i.e. | (10) |
Combination of (9) and (10) gives the restrictions for the following linear programming problems to find the minimax estimates of the unknown aj and
: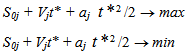 | (11) |
where: t* is an arbitrary fixed point for T \Tp .Based on the solution of problems (11) it is easy to build two sets of estimates (5 - 8) separately for ТС,
and HC,
of HMS. Given the partnering relationship between TC and HS of HMS and using the minimax principle, one can find the estimates
for HMS as a whole from the following expression: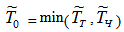
5. Comparison of Control Criteria of Complex Technical Systems
Minimax approach (based on the worst case scenario) is, generally speaking, pessimistic, and therefore yields a pessimistic estimate of the system condition, allowing one to work out appropriate measures for condition management of complicated technical (human-machine) systems. The cost of such control may exceed the cost of an optimistic or statistically based condition management, in particular, the management on basis of the reliability measure criterion. So it is reasonable to compare the control criteria with different physical meanings: the reliability measure criterion in the given time interval and the residual operating life (guaranteed or minimax) criterion.Generally speaking, for the purpose of comparison with the reliability measure indicator in the given time interval P(t) t ∈ T the indicator Sj(t)
should be considered as affinitive to P(t). Then Sj(t)
can be considered a random process, whose characteristics can be given or worked out from the observation results. In addition, the Sj(t)
indicator should be normalized to the interval[0,1]. After normalization the value of the indicator Sj(t)
, t∈Tp ⊂ T allows one to treat it as an integral selective distribution function of the time of failure-free operation of TS, denoted as H. In this case, the values Sj(t)
, t ∈Tp ⊂ T can be interpreted as the presence factor of any length Sj(t) in the interval T and operating domain D.Ht[S(t0); S] belongs to the operating domain. On a basis of monotonically decreasing presence of the line segment[S(t0); S(t)], t ∈ T , in the operating domain D, for any moment of time t ∈ T the following inequality is true 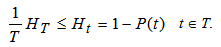 | (12) |
where H, HT, Ht are the values of selective integral distribution function of the time that which are the components of y(t) t ∈ T belonging to the domain D.The obtained inequality allows one to estimate the reliability measure of the operated object in the given time interval T.The indicator HT corresponding to the worst case scenario, can be viewed as the lower boundary of the average time to failure of TS. So the obtained inequality can be used to assess the reliability measure of the operated TC in the interval T.Thus, the indicator S(t), which is more easily computed and more reliable (because it corresponds to practically available operation information of TS), can be used to control operation of TC. Its use is appropriate during the operational activity of TC, when there is no data on such reliability indicators as the reliability measure P(t) t ∈ T.For the sake of comparison let us normalize the indicator S(t) to the interval[0,1]. Then it becomes possible to interpret the normalized indicator Sj(t)
, t∈Tp⊂T, after the substitution of the found values of unknown parameters (after solution of tasks (11)), as an integral selective distribution function of failure-free operation time of TS. Further, one of the statistical measures of consent can be used, in particular, the A.N. Kolmogorov criterion for finding some theoretical distribution of failure-free operation time of TS.The found distribution makes possible to determine the values of the reliability measure of TC in the given time interval.
6. Using the Algorithm of Determination of Residual Operating Life for Assessing Shipboard HMS Condition
Let us consider application examples of the above approach to determin the indicator
of the shipboard human-machine systems elements.Example 1.The ware of stern bearings can be estimated by calculations based on the clearance measurements. The measurement error is 3 %. The useful life of the propeller shaft bearing T = 20 000 hours, the wear allowance δl is (0 ≤ δl ≤ 4) mm. Table 1 presents the results of measuring the clearance, and table 2 shows the forecast for the bearing condition.Table 1. Results of measuring bearing clearance |
| Time, t×103, hrs. | Clearance, mm | 0.5 | 0.1 | 1.0 | 0.18 | 2.0 | 0.32 | 3.0 | 0.5 | 5.0 | 0.8 | 6.0 | 0.96 | 7.0 | 1.2 | 8.0 | 1.36 | 9.0 | 1.54 | 10.0 | 1.8 |
|
|
Table 2. Results of the forecast for bearing clearance |
| Time, t×103, hrs. | Min y(t), mm | Max y(t), mm | Average y(t), mm | 12.0 | 2.05 | 2.4476 | 2.2488 | 13.0 | 2.13 | 2.8008 | 2.4653 | 14.0 | 2.17 | 3.1829 | 2.6765 | 15.0 | 2.2245 | 3.5947 | 2.9096 |
|
|
Example 2.Table 3. Results of temperature measurement of engine cooling liquid |
| Time, t×103, hrs. | Temperature t0 C | 1.0 | 58.0 | 2.0 | 61.1 | 4.0 | 64.8 | 5.0 | 67.0 |
|
|
The technical condition of the heat-exchange apparatus used for engine cooling can be assessed based on coolant temperature, which is measured with an accuracy of ±2%. Table 3 presents temperature control data and table 4 gives the forecast for the cooling system condition of the shipboard diesel. Useful life of such a system is 10 000 hours, the range of operating temperatures is 40° to 80℃.Table 4. The forecast for temperature of engine cooling liquid |
| Time, t×103, hrs. | Min t0 C | Max t0 C | Average t0 C | 6.0 | 66.5 | 79.63 | 73.07 | 7.0 | 67.14 | 87.0 | 77.07 | 8.0 | 67.83 | 95.5 | 81.67 | 9.0 | 68.56 | 105.13 | 86.84 | 10.0 | 69.3 | 115.9 | 92.6 |
|
|
Example 3.The optical density of myocardium indicator of the crew was determined by the ultrasonic densitometry technique with an error of ±10%. Table 5 shows the myocardium optical density data of interventricular septum, and table 6 gives the corresponding forecast. The age of the electromechanical engineer at the beginning of the survey was 32 years. The frequency of the survey - 1 time per two years, 4 surveys in total.Table 5. Results of measuring optical density of interventricular septum |
| Age (years) | Optical density, (unit measure) | 30 | 11.7 | 32 | 11.7 | 34 | 11.9 | 36 | 11.95 |
|
|
Table 6. The forecast for optical density interventricular septum |
| Age (years) | Min y(t), (unit measure) | Max y(t), (unit measure) | Average y(t), (unit measure) | 38 | 11.86 | 12.4 | 12.13 | 40 | 11.87 | 12.85 | 12.36 | 42 | 11.88 | 13.4 | 12.64 |
|
|
7. Conclusions
Having analyzed the results of the forecasts it should be noted that the application of the proposed approach allows one to determine with certainty the possibility of failure-free operation of HMS based on a small amount of condition monitoring data (desirably both of the technical and human components of HMS). The performed theoretical research and analysis of the practical applications of such investigations show that minimax approach allows to determine with guarantee the possibility of failure-free operation of human-machine system in the conditions of deficiency of initial data. In this case there is no necessity to determine the stochastic properties of perturbations existing in the initial data (result of control). There we also have a possibility to reduce requirements on the model of forecasting parameter drift used in calculations. Particularly on minimax approach, the physical validity of the accepted model has great importance but not its mathematical description, which adequacy is difficult to be established by carrying out numerous mathematical experiments (mathematical modeling) without acceptance of many assumptions.
References
[1] | O.B.Abramov, A.N.Rosenbaum Minimax approach in parametric synthesis of analog technical systems // Automation, Informatics and Control Systems. – №2. – 2003. – с.67-78. |
[2] | V.G.Repin, G.P.Tartakovsky Statistical synthesis under expected uncertainty and adaptation of information systems // Moscow Sovetskoye Radio, 1977, 432p. |
[3] | P. Anokhin Physiological aspects of functional systems (Moscow, Medicine. 1975. – P.295). (in Russian) |
[4] | Deryugin M. Ultrasonic densitometry in diagnostics of myocarditis and cardiosclerosis (M. Deryugin, I. Itskovich, V. Sukhov, I. Belozertseva, E. Onischenko, S. Boytsov. // Vestnik aritmologii .- 2002. - №26. - App.A. - P.193). (in Russian). |