Sopingi1, 2, Soemarno3, Bagyo Yanuwiadi4, Agus Suman5
1Doctoral Program of Environmental Science and Technology, University of Brawijaya, Malang, Indonesia
2Government of Nganjuk District, East Java, Indonesia
3Department of Soil Science, University of Brawijaya, Malang, Indonesia
4Department of Biology, Faculty of Mathematic and Natural Sciences, University of Brawijaya, Malang, Indonesia
5Department of Economics and Development Studies, Faculty of Economic and Business, University of Brawijaya, Malang, Indonesia
Correspondence to: Soemarno, Department of Soil Science, University of Brawijaya, Malang, Indonesia.
Email: |  |
Copyright © 2015 Scientific & Academic Publishing. All Rights Reserved.
Abstract
This research was conducted in the central industry of tile and brick in Kaloran and Betet village, Ngronggot Sub-district, Nganjuk District. This study was aimed to analyse the implementation of green industry concept on the small industry of tile and brick in the study area. Questionnaires and interviews used as survey method to obtain data and information from stakeholders in small industries of tiles and bricks. Respondents consisted of 90 entrepreneurs from Kaloran village and 70 entrepreneurs of Betet village. Data were analysed descriptive qualitatively. Evaluation techniques in this study included the assessment on the implementation of green industry, specifically towards the raw materials, production processes, and the final process. The results showed that the brick and tile industry in Nganjuk District generally meets the criteria and indicators of the green industry concept, because the used components are harmless to the environment, effective and efficient, and renewable. Production process includes the application of reduce and reuse concept, fuel and energy management, environmental-friendly human resources, implementation of Standard Operational Procedures (SOP), and equipment modifications. While the final product includes a low/zero emission to meet the environmental quality standards, free from hazardous materials, useful, and comply the concept of recycle and recovery.
Keywords:
Green industry, Small industry, Tile and brick
Cite this paper: Sopingi, Soemarno, Bagyo Yanuwiadi, Agus Suman, The Implementation of Green Industry in Small Industries of Tiles and Brick in Nganjuk District, East Java, Indonesia, Resources and Environment, Vol. 5 No. 1, 2015, pp. 1-8. doi: 10.5923/j.re.20150501.01.
1. Introduction
The sustainable and environmental-friendly concept of natural resources management has been implemented in the production process by using natural raw materials. The implementation of this concept requires the support of commitment and willpower, coupled with the acquisition of knowledge and skills on the procedures of implementation [1]. Sustainable green industry was designed with the aim for reducing the negative environmental impacts on the health of the users. It was also designed to meet the needs of current generations without compromising the ability of future generations to do the similar work.Green industry concept recognized by the International Conference on Green Industry in Asia, Manila, and Philippines in 2009. It also had been cooperated between the United Nations of Industrial Development Organization (UNIDO), United Nations of Environment Program (UNEP), and International Labour Organization (ILO); attended by 22 countries including Indonesia. The Manila Declaration is a commitment for Asian countries in prevention of environmental issues through the efficient use of resources and reduction of carbon gas, especially in the industrial sector. Resource efficiency can be accomplished by applying Reduce, Reuse, and Recycle (3R) as the fundamental of a more clean-production. In the other hand, low-carbon can be achieved by applying the reduction of CO2 emission and correspondence with the Clean Development Mechanism (CDM) [2].Green industry commits to reduce the impact on the environment due to the production process and the resulting product. The commitment implied in efficient and sustainable usage of low-carbon resources in the selection of raw materials, production processes, final products, and services in the industrial activities [3].Production process in green industry prioritizes the efforts to use efficient and effective resource in a sustainable manner. It is purposively to harmonize the industrial development with the environment conservation and provide benefits to the community. Thus, the provision and use of sustainable energy was implemented to encourage the achievement of sustainable development. The utilization of sustainable energy is necessary to develop the green energy concept that integrates the ideas and programs relating to the provision and the using of sustainable energy [4]. Green industry is expected to be a new breakthrough in the industrial world for supporting the creation of sustainable economic and environmental improvements. It becomes a hot topic and the idea has been used as the material of world conference. The hopes laid in this idea, including the economic experts and environmentalists who trying to find the best concept for the realization of the green industry that applicable in different area of the world.As the increasing times and environment conditions, it is expected that each industries apply the green industry concept; the industry with the aim of reducing the negative impact on environment, health, and users [5]. Green industry becomes capital for the industry. Application of the green industry is possible by emphasize the industry to gradually implement the environmental-friendly production – not enforced [6]. Thus the production process result the clean products, including the conservation of raw materials and energy, avoiding the use of hazardous and toxic materials, reduce the amount and toxicity of all waste and released emissions [7].Over time, many researches have been conducted on green industry, both in the terms of concept and application. Hirschnitz et al. [8] found ten indicators of sustainable industry, as follows: 1) environmentally weighted material consumption (EMC) 2) energy intensity by sector 3) production-based CO2 productivity, 4) water consumption by sector, 5) sustainable process index (SPI), 6) water abstraction rates and water stress 7) corporation turnover, added value, and exports of the environmental goods and services sector 8) resource productivity and material productivity 9) total material consumption (TMC) 10) ecological footprint (EF)Kaloran and Betet village of Ngronggot Sub-district is the central industry of tile and brick in Nganjuk District has been operated for decades and claimed as green industry. The use of raw materials of soil and water is sufficient to produce tiles and bricks, the fuel for production also use wood to prevent the combustion of hazard materials. However, the production is directly related to the nature and environment. Therefore, this research was conducted to determine the application of the green industry concept on small industry of tiles and bricks in Nganjuk.
2. Research on Green Industry
Marigo et al. [9] also conducted research with the aim for analysing the capacity of alternative innovation in China. It assessed the development of domestic technology in low-carbon energy factories, e.g. solar photovoltaic (PV). The results showed that since 2005, China has been very good in the sector of transport – in the transportation of raw materials (import-domestic), processing, and distribution.Smith [10] provided information that New Jersey has about 20,000 companies that have the principles of green industry in 2009. Principles of green industries in the country consisted of four aspects, namely: energy efficiency; renewable energy; management and waste reduction; and transportation. Moertinah [11] conducted a research that identifying a more clean-production opportunity that applicable to the textile bleaching of finishing process in the industry of PT. Damaitex, Semarang. The results of the research explained that applicable cleaner production is feasible and saving a great cost for a year (Table 1).Table 1. Applicable Clean Textile Production in PT. Damaitex, Semarang 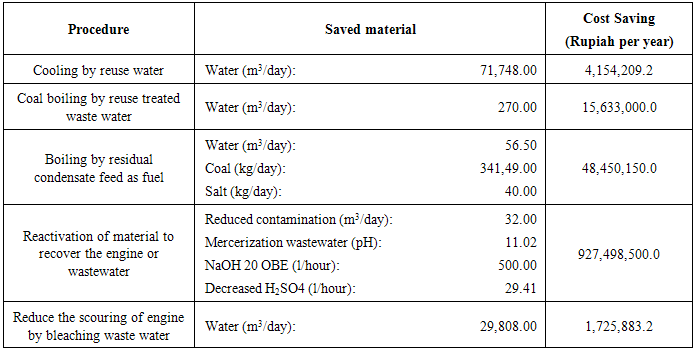 |
| |
|
Ansori [12] assessed the level of need, utilization, distribution, quality, and environmental impact of clay reserves around the centre of the tile industry in Pejagoan and Sruweng Sub-district, Kebumen District. This study includes the mineral distribution, mining activities and existed environmental impacts. Laboratory studies include XRD analysis using a wide angle RINT2000 goniometry and mineral chemistry using AAS method (Atomic Absorption Spectrometer). The environmental impacts include the loss of ground cover and soil fertility, change the topography and destruct the infrastructure. Ansori [12] recommend to localizing the mining area; to restore the top soil on the post-mine reclamation; and ex-mining land use-change into fishing, mining and zoning.Huda [13] explained the effect of temperature combustion and ash addition to the quality of bricks. The composition of 1:0 (soil: ash) shows unstable fuel value. Conversely, the composition 1: ½ indicate a stable value, whereas the ratio of 1: 1 indicates negative value [14].
3. Research Method
This research used a descriptive-qualitative method, implemented in the village of Betet and Kaloran, Subdistrict of Ngronggot, Nganjuk, East Java, Indonesia. The research carried out in July to December 2012. The study area population comprised of 955 businessmen respondents; 158 in Betet and 797 in Kaloran. Respondents consisted of: tile businessmen: 6 from Kaloran and 7 from Betet; bricks businessmen: 77 from Kaloran and 59 from Betet; and tile and brick businessman: 5 of Kaloran and 6 of Betet. The number of samples was determined by simple random sampling refer to Riduwan [15]. The business groups in the implementation divided as follows: 1). raw brick business group, which only produces bricks and sell them in raw form; 2). bricks business groups, which produces the raw bricks and conduct combustion process; 3). tiles and bricks business group, produce roof tile from raw to final product, but also buy the raw bricks to be burned along with the tile and sold both in final form. Evaluation in this research provides assessment on the implementation of the green industry at every phase, i.e. provision of raw materials, production processes, and the final product. The principles of the green industry which assessed on each process are referred in Table 2.Table 2. Assessed Principle of Green Industry 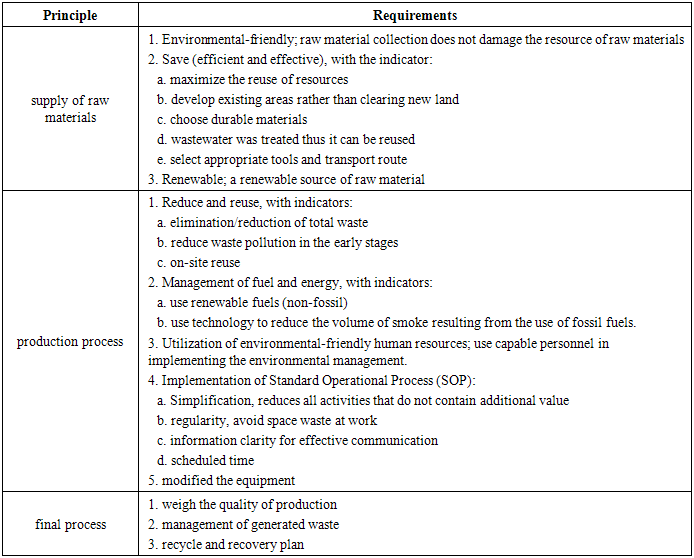 |
| |
|
The principle of raw materials should also meet the requirements of the green industry. It should be low/zero emission; all raw materials were optimally utilized as input by other industrial activities in a single unit. The process should be adapted to meet the environmental quality standards, free of hazardous and toxic materials, non-explosive, non-flammable, non-reactive, does not cause infection, and non- corrosive material.
3. Result and Discussion
3.1. Tile and Brick Production
The main raw material for tiles and bricks is clay-sand mix. For tile, the comparison of the clay and the sand is 2:1, meanwhile bricks are 1:1. Median raw material obtained by purchase the land in the edges of Brantas River, 5 km from the production factory. The raw materials were also taken from the garden soil. Soil purchasing is Rp. 180,000 for brick materials and Rp. 200,000 for the tile materials. This cost includes rent for land, energy transport (mine site to factory), and rent of heavy equipment transportation. Within a month, average bricks production is 10,000; while average tiles production are 3,000. The survey showed that 2 of 5 respondents in Betet Village produce < 5000 bricks and 3 respondents produce 5000-10000 bricks per month. Otherwise, 3 of 6 respondents in Kaloran Village produce < 5000 tiles in a month, while 3 respondents produce approximately 5000-10000 bricks in a month.To make a tile, soil had been milled and then pressed by a press tool according to the types of expected tile. Previously, the press tool lubricated with klentheng oil and fuelled by diesel. The pressed tile laid on tempelang; an instrument made of wood to put the wet tiles, then tempelang compiled into a plangkan. Raw tiles drying process was done under direct sunlight for 12 hours in dry season, while in rainy season it needs up to one week or more. The edges of dried tiles trimmed with a knife, then burned using furnace combustion process or pawon. Fuel used in the combustion process was various, e.g. wood waste (rencek and dongklak) and waste corn cobs (janggel), mixed or separately. The combustion process was done in 15 hours, with the average of furnaces capacity was 10,000 tiles. After burning stages, tiles had been ready to be marketed after sorted out the failed product.Brick making process is generally very similar to the tile-making process. The simple steps begin with extracting the raw materials, e.g. clay or loam. Then the clay was dug to be transported to the site of bricks production. The clay is then poured or mixed with water, stirred so that the water can seep the clay and then left for at least one night. However, usually the brick making process is much simpler. Clay and water has been mixed and stirred manually by hand (or pressed with feet) without milled with molen. The duration of agitation was less than on tile.
3.1.1. Brick Production
In bricks making process, soil that has been mixed with brick mold pressed in a flat frame. Same with the tile, brick drying performed under a direct sunlight for about 12 hours in the dry season, while in the rainy season can be up to one week. The dried bricks’ edges trimmed with a knife then combusted using furnace. The combustion fuelled by waste wood or rice husk for 12 to 24 hours, depend on the capacity of the furnace. However, for people who do not have a furnace, combustion is usually implemented with a simple way of making disposable furnace, which is immediately broken down. Each combustion process could reach 10000 to 20000 bricks. The product components and the amount of costs incurred in the brick industry are as follows. a) Supply of Raw Materials It is consisted of top soil raw materials, labour, tools, and transportation to the location. The total cost for the supply of raw materials is Rp. 180,000 for 2200 bricks. b) Production ProcessProduction process consisted of three elements:• Power; covering power for brick molding, power plug for furnace unloading and combustion. The total cost of supplying energy for producing 1000 brick is Rp. 130,000. • Equipment; main equipment for the production process include brick mold, comb knives, and hoes, supported with plastic cover and water. • Fuel; in the form of rencek firewood, dongklak firewood, corn cob, and rice husk. The average fuel cost to burn 12000 bricks is Rp. 1,250,000.c) Transportation The third component in brick production is transportation; transportation of raw materials to the burning place is Rp. 30,000 per 1000 bricks, with the contract system. Carts used in site are Rp. 500,000 per unit for 5 years. d) WasteFourth component in production processing is waste; including the wages on milled failed-production brick for Rp. 30,000 per m³ and the cost to purchase bags for ashes, Rp. 3,000 per sack.If the industry only produces bricks and sells them in raw form, then the profit is Rp. 5,122.5 for 1000 brick; only 4.71% compared to the industry that produce and sells the brick in mature forms. Although there are extra cost for burning power, furnace and fuel, the profit is Rp. 108, 680. Otherwise, the industry that bought the raw bricks and sells them in the mature form profited for Rp. 75,418 with different cost on the raw brick materials and for plug unloading, burning and furnace (Table 3). Table 3. Production Cost and Profit in Brick Industry 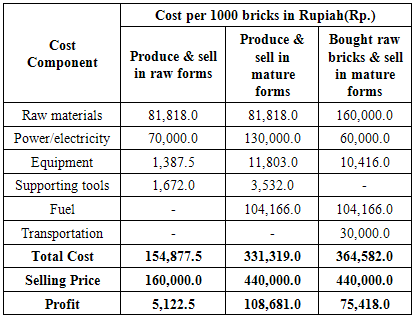 |
| |
|
3.1.2. Tile Production
a) Supply of Raw Materials The cost for the supply of raw materials includes the clay soil as raw materials, labour for loading and unloading, tools, and transportation to the location. The total cost for the supply of raw materials is Rp. 200,000 for 1100 tiles. The raw material is processed into the mill; clay milling costs is Rp. 70,000 for 1100 tiles. b) Production ProcessThe production process covering: • Power; consist of press power, tidal power and unloading furnace, and combustion power. Costs incurred for 1000 tile is Rp. 420,000. • Equipment; The main equipment for the production process include: the press, the base tile, and furnace. • Operations and maintenance; covering the press tool maintenance, provision of additional materials (klentheng oil and diesel). • Fuel; in the form rencek firewood, dongklak firewood, corn cob and corn silk. Rice husk was no use as in brick combustion due to the worse results. The fuel cost to burn ±10000 tiles is Rp. 1,250,000.c) Transportation The transportation from raw tiles to the furnace is Rp. 30,000 per 1000 tiles, with the contract system. Carts used in site are Rp. 500,000 per unit for 16 years. d) WasteFourth component in production processing is waste (similar to bricks processing); including the wages on milled failed-brick product for Rp. 30,000 per m³ and the cost to purchase bags for ashes is Rp. 3,000 per sack. Costs incurred for each 1000 tiles is Rp. 842,300 and the selling price of each 1000 tiles is Rp. 950,000. Thus, the profit for each 1000 tiles is Rp. 107,700.The waste from the failed production process of tile, brick and ash can be used and recycled. In every 12000 bricks and 10000 tiles combustions, there are approximately 10% product failures. The failed product processed with soil into fine brick (red cement). Each 1 m3 of fine brick can be obtained from 1500 or 3000 bricks or tiles. Milling costs is Rp. 30,000 per m3, and the selling price of fine brick or tile is Rp. 150,000 per m3. Every 1000 bricks gains from product failure were about Rp. 7,000, while every 1000 tiles gained from failed product is Rp. 2,000.The ashes still also have value. Each burning phase resulted ± 5 sacks of ash. The selling price of ash is Rp. 5,000 per sack. However, employers must provide a price of Rp. 3000 per sack. Income that can be derived from the sale of ash from 1000 bricks is ± Rp. 833 and the income that can be earned from the ash of 1000 tile is ± Rp. 1,000.
3.2. The Supplying and Management of Raw Materials
From the components and the production cost of tiles and bricks, we can obtain representation whether the business meets the green industry indicator or not. The presentation details are as follows.Provision and raw materials management is a planned key for the production sustainability. The main raw material in the production of tiles and bricks at the research site was clay. However, the industry required the additional materials to get a better quality production results, e.g. sand. Both materials are soaked in water to be used as a dough and then ready to be pressed. The use of these materials should be made as efficient as possible so that the sustainability of the production can be effective and efficient in accordance with the needs of production, and also consider the advantages and disadvantages of business. Furthermore, the raw materials should be renewable in the expected of ecology and nature conservation is maintained.In the process of supplying the raw materials, the industry should concern the three provisions. First is the provision of environmental friendly. The main raw material for making tiles and bricks are soil. Most of businessman acquired the soil by buying from other village. Only a slight majority use the garden soil. Kaloran village use less garden soil for raw materials, as it will damage the environment.Currently the soil for raw materials of tiles and bricks in Betet and Kaloran village come from the surrounding area of Brantas River dam; it is 5 km distance from the place of industry. Provider of raw materials is a separate business group. Demand for raw materials to date does not damage the environment, because the raw material is obtained from the less productive agricultural land, even with the low soil dug in the ground, thus can be drained of water and used as paddy fields. However, there is also damaging risk to the environment – even to the dangerous level – i.e. exploitation of raw materials that too close to the embankment of the Brantas River.The second is the provision on saving (efficient and effective) in several criteria: 1) Maximize reuse on the resource. Community brick and tile manufacturers produce press the failed production by re-immersion in water and then destroyed to be re-processed again. This is certainly the consideration on the efficiency of the raw materials that can be re-processed again; 2) develop existing areas rather than clearing new land. Raw materials such as clay and sand pit is the type of mine that takes a long time for recovery, thus to obtain more material means to open a new land elsewhere; 3) selecting durable materials, e.g. clay and sand mix; 4) conduct water treatment thus can be reused. The fourth criterion cannot be applied because the water in the production site is a consumable material, however, they concern on the sufficient amount of water.The last provision is selecting appropriate tools and transport road. They use truck transportation for raw materials and Ledok (modified diesel engine that is used as a means of transport), supported by available transport road.Transportation components process can be divided into two sections, namely: a) The transportation of raw materials to the pressed site for tiles or bricks. For the manufacture of bricks and tiles, entrepreneurs try to puts raw materials as close as possible to the site of pressing process. So that the raw materials have been prepared directly to be pressed. However, due to the large amount of press that also requires a large place, resulting difficulties for materials to be directly reach the transport. Transportation is done manually by workers and cart. b) Transport from press site to drying site. Brick pressing conducted in open space thus it can be exposed to direct sunlight. It is different with the less dry condition. Bricks were trimmed subsequently for further pressing. Tiles were dried indirectly, placed in a sheltered spot to avoid repeated removal resulting damage to the tile. Removal from tile to press drying done manually by hand and transported by a single worker, c) Transport brick or tile from the dried site to the combustion furnace (for businesses that manufacture roof tiles/bricks). Brick/tile that have been combusted, dried and taken by cart which driven by human power.Transportation outside the site of business is conducted outside the transport business premises which include (1) the transportation of raw materials from the source to the plant industry, by transport truck; (2) the transportation of fuels from the collectors to the plant industry, by pickup trucks or cars; (3) the transportation of raw brick/tile from the plant to the furnace or combustion site, by truck, pickup, or wagon; and (4) the transportation of mature brick/tile to consumers. Coverage includes shipping outside the area.The third provision is a renewable raw material. Raw materials of brick and tile production in the form of clay and sand can be renewed, but takes a long time. Damage on these resources can naturally recover when environmental resilience equal to or greater than the level of damage that occurs. On the other hand, until now there has been no effort from the parties concerned to reform the existing mine site.
3.3. Clean Production Process
The production process is the subject of an industrial activity, where results from this process can be obtained along with the waste of production. Implementation of the production process should consider the application of reduce and reuse, utilization of environmentally sound resources, SOP implementation, application of factory layout and equipment modifications. In the implementation of reduce and reuse, the process of elimination or reduction of total waste in the production process considering the weather condition. The risk of failure on production in the rainy season is greater than in the dry season. Of 10000 tiles, about 1000 tile failed in the rainy season. Failures caused more quality defects due to the incomplete drying process. In the dry season, for once burning process, ± 300-500 tiles were damaged. The manufacturer showed an effort to reduce waste pollution in the early stages, especially in the used materials which are consumables including water and the combustion process in the final stage. The process of on-site reuse conducted by reuse the generated waste, e.g. ash which usually sold per bag. For fuel waste (ash) from rice husk used as an ingredient to make a light brick, it can be used also as a mixture of brick raw material if the soil quality is not good. While the waste production in the form of failed bricks or tile before combustion can be recycled by soaking it in water, destroyed and reprocessed. Otherwise, if it failed after the combustion, the failed-products recycled to be a mixture of milled and used as building material.
3.4. Burning Process
To manage fuel and energy, they use renewable fuels (non-fossil materials), such as rencek firewood, dongklak firewood, corn cobs, and husks. The fuel costs for burning the bricks and tiles are as follows.The cheapest fuel for tile burning is rencek firewood, while the most expensive is dongklak firewood. Otherwise, the cheapest fuel for brick burning is rice husk and the most expensive is dongklak firewood.Considering that the combustion process of brick and tiles were manually using a fire with fuel of wood, dongklak, corn cob, and rice husk, we assumed that there is no management on the use of modern furnace technology. However, the industry provided a specific site for the burning process.Table 4. Cost of Tile and Bricks’ Burning Process 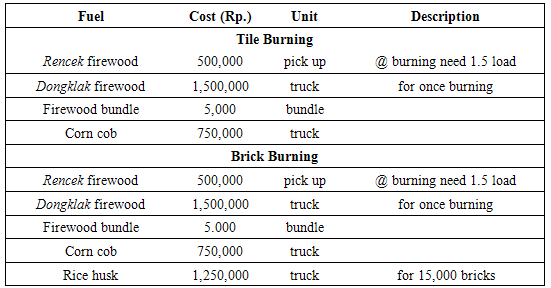 |
| |
|
Utilization of environmentally sound human resources is to consider the use of personnel who are able to carry out environmental management. Power for the production of brick and tile refer to the custom of ancestry and the majority of experts in this industry; even in traditional way. Thus the local brick and tile businessman already understand the effectiveness of production activities.They simplify the implementation of the SOP, by reducing all activities that do not contain added value. All production activities of tiles and bricks should be effective, considering that it is included as simple small industry. Consistency applied by avoiding wasted space in the workplace. The production is placed in a specific site, thus it can be used for subsequent production. Clarity of information is needed in effective communication in all directions. Information on production of tiles and bricks are explained in the manufacturers manual, which emphasize on communication and the use of modern telecommunications.To obtain good products and sustainability on the production cycle, it is necessary to schedule the phases of production process. The production process is also considering the season and the weather. In the dry season, the start of combustion process can be made within 45 days with a combustion capacity of 12000 units. While in the rainy season it takes 75-80 days with a burning capacity of less than 12000. This difference is influenced by the weather that directly affects the drying process. The equipment used to make bricks is still manual; it is a mold shaped timber with a length of 24 cm, width 12 cm, and 5 cm thickness. Whereas tile production use machine for dough preparation and pressing process.
3.5. Final Process
Final process on the industries of brick and tile were comprised of the completion on the combustion process; the process to make the raw products into finished and ready-use products. After the combustion process, tile and brick were moved. They laid four shaped-bricks together to ease the calculation of total production. As for tile, they neatly lined and marked per hundred. Thereafter the production is ready to be marketed. Manufacture criteria of these tiles and bricks industry apply low/zero emission; which in addition to the profit from the sale of bricks and tiles, there is also production waste that can be sold, as well as failed-products of brick and tile and ash (Table 5).Table 5. Calculation of Waste Bricks Failed Products 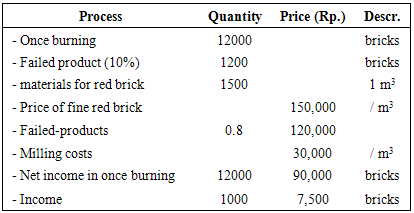 |
| |
|
In every brick burning, as much as 10% of 12000 fail. Table 5 above calculate the number of failed bricks in the maximum production. Production in the dry season, failed bricks is considerably less, ranged 300-500 (4%) for each brick burning.In tile burning, waste products are not much different from the waste of failed-brick. The waste tile for a burning with a capacity of 10000, the resulting product failure is also 10%, estimated within maximum amount of tile production. Production in the dry season showed less failure ± 300 (3%) for each tile combustion. Table 6. Calculation of Waste Bricks Failed Product 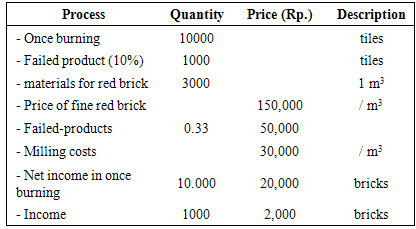 |
| |
|
The waste of failed brick and tile production were reprocessed by means of ground into a fine red brick (red cement). The red cement can be used for building materials with a sales price per m3 for Rp. 150,000. About 1500 red brick or tile was needed to obtain 1 m3 of red cement. Besides reprocessed failed products, tile and brick burning also produces ashes that can be utilized. Ash waste from the production of 10000 bricks/tiles is 5 sacks. The ash is sold as an ingredient or mixture ingredients with low bricks quality. The production of tiles and bricks at the research site established because it is needed by the community and surrounding area of Nganjuk. Because people perceived that tile and brick are the most environmentally friendly product for building materials than other products (e.g. asbestos, iron sheeting, etc). This indicates that the products have standard quality of reliable and environmental-friendly. Table 7. Calculation of Ashes as Side Product for Tile and Brick Burning 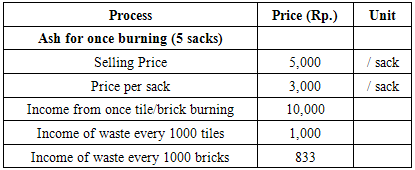 |
| |
|
Environmental quality standards of tiles and bricks production also has been proven free of hazardous materials; either directly or indirectly to the nature. The production of tiles and bricks can be used to meet the needs in the field of construction, used as roof tile and brick wall. Application of recycle and recovery in the production of tiles and bricks were made in two ways, first reprocess waste products for other purposes. It is as described above that tile and brick production in Nganjuk applied the production of zero emissions (clean production). Second, efforts should be made to recover, repair/replace the environmental damage that occurs. Soil excavation taking raw materials from around the Brantas River dam only can be restored in a relatively long time. However, until now there has been no research done to attempt the land recovery.
4. Conclusions
We concluded that the brick and tile industry in Nganjuk district meets the criteria and indicators of the green industry, because the components used are components that do not damage the environment. The supplying of raw materials implements environmental criteria, saving (effective and ineffective), and renewable. Production process includes the application of reduce and reuse, fuel and energy management, utilization of environmentally sound human resources, the application of SOP, and modification of equipment. Final product includes a low/zero emission, processed to meet the environmental quality standards, free from hazardous materials, can be used, and recycled and recovered. However, there are several indicators that should be assessed further, i.e. the harmful to the environment, especially the raw materials taken from the Brantas River dam. Therefore, revitalization is needed to replace the land mine, thus the environment is maintained.
References
[1] | Butar-butar, R. R., Soemarno. 2012. Kompetindum Kajian Lingkungan dan Pembangunan. PDKLP PPSUB, Malang. |
[2] | Manila Declaration on Green Industry in Asia. 2009. Manila, Republic of Philippines. |
[3] | UNIDO, 2014, Green industry for a sustainable and economically viable future,www.unido.org/greenindustry.html, United Nations of Industrial Development Organization. |
[4] | General Directorate of Electricity and Energy, 2009. Initiatives for green energy, www.EnergiHijauDESDM.pdf. Downloaded on May 8th, 2013. |
[5] | Dewata, I., 2011, Develop green industry policy. www.haluan.com, Downloaded on May 13th, 2013. |
[6] | Mutmainnah, A. L., 2011, Green industry is possible, www. jurnas.com/GreenIndustryTidakMustahil.htm, Downloaded on May 2nd, 2013. |
[7] | Djajadiningrat, S. T., 2011, Green economy, Rekayasa Sains: Bandung. |
[8] | Hirschnitz, G. M., Srebotnjak, T., Porsch, L., Grünig, M., Hand, P., and Cerezo, K. T., 2012, Integrating resource efficiency, greening of industrial production and green industries – scoping of and recommendations for effective indicators, Ecological Institute, Berlin, Germany. |
[9] | Marigo, N., Foxon, T. J., and Pearson, P. J. G., 2010. Chinese low-carbon innovation: Developing technological capabilities in the solar photovoltaic manufacturing industry, J. of Knowledge-based Innov. in China, 2(3), 253 – 268. |
[10] | Smith, T., 2009, Division of labor market and demographic research. New Jersey Economics Indicator. |
[11] | Moertinah, S., 2008, The opportunities of clean production on Textiles Industry of Finishing Bleaching, e-prints, Undip.ac.id, Downloaded on May 13th, 2013. |
[12] | Ansori, C., 2010, Analysis of quality reserve and the impacts of clay mining as raw material for sokka tile and brick in Regency of Kebumen, Jurnal tekMira, 6(3), Juli 2010. |
[13] | Huda, M., 2012, Effect of temperature combustion and ash addition to bricks’ quality, Jurnal Neutrino, 4(2), April 2012. |
[14] | Yamane, T., 1967, Statistics: An introductory analysis, 2nd Ed., Harper and Row, New York. |
[15] | Riduwan, 2008, Methods and technique to develop thesis, Alfabeta, Bandung. |