Alphonse Sako Avocefohoun1, 2, Rose Mikponhoue3, Mahoudjro Theotime Francis Hounsou4, Roméo Aguiar1, Papin Sourou Montcho1, Gbèssohèlè Justin Behanzin4, Elie Sogbochi1, Alassane Youssao Abdou Karim1
1Laboratory of Study and Research in Applied Chemistry, Polytechnic School of Abomey-Calavi, University of Abomey-Calavi, Cotonou, Benin
2Laboratory of Research and Applied Biology, Abomey-Calavi Polytechnic School, University of Abomey-Calavi, Benin
3Faculty of Health Sciences of Cotonou, Benin
4Laboratory of Pharmacology and Improved Traditional Medicines, Faculty of Science and Technology, University of Abomey Calavi, Benin
Correspondence to: Papin Sourou Montcho, Laboratory of Study and Research in Applied Chemistry, Polytechnic School of Abomey-Calavi, University of Abomey-Calavi, Cotonou, Benin.
Email: |  |
Copyright © 2024 The Author(s). Published by Scientific & Academic Publishing.
This work is licensed under the Creative Commons Attribution International License (CC BY).
http://creativecommons.org/licenses/by/4.0/

Abstract
Occupational Health and Safety (OHS) being one of the most important aspects in any company, prevents or reduces the arduousness at work, ensures the monitoring of the health status of workers, contributes to the traceability of occupational exposures and guarantees good health of employees even after their retirement. The present work aims to study the occupational risks associated with marked physical constraints, the environment and work rhythms at the workstations of the SOBEBRA plant. The methodology consisted of identifying the positions concerned by the arduousness, collecting information concerning each position and processing this information. To carry out this work, we mainly used the texts of the French labor code dated 2005 revised on January 30, 2022. We carried out measurements using the 8852 SI / IEC sound level meter for noise, the CR calibrator: 515 Acoustic Calibrator Cirrus for calibrating the sound level meter, the THGM003 thermo-hygrometer calibrated for temperature and a 600 kg / 100g industrial scale calibrated for measuring masses. The assessment of hardship factors showed that SOBEBRA-Cotonou employees are only exposed to eight factors, two of which are mainly work in successive alternating teams (TESA) and noise (B). The Bottlenecking and Mechanics, Electricity and Automation departments are the most exposed to hardship. The means of controlling hardship factors have been identified and others proposed, which reinforce existing ones.
Keywords:
Hardship factors, Health and safety at work, Industry, SOBEBRA-Cotonou
Cite this paper: Alphonse Sako Avocefohoun, Rose Mikponhoue, Mahoudjro Theotime Francis Hounsou, Roméo Aguiar, Papin Sourou Montcho, Gbèssohèlè Justin Behanzin, Elie Sogbochi, Alassane Youssao Abdou Karim, Factors of Hardship in Companies: Case of the Beninese Brewery Company (SOBEBRA) Cotonou Site, Public Health Research, Vol. 14 No. 2, 2024, pp. 27-34. doi: 10.5923/j.phr.20241402.01.
1. Introduction
Faced with the lengthening of working life, which will lead to an overall ageing of the working population, improving working conditions has become a major challenge for companies [1]. Surveys of working conditions in companies have revealed a persistence of "difficult" working conditions which can have an impact on workers' health and even on their quality of life after retirement [2]. Therefore, work in a company can be subject to constraints of various kinds, which need to be controlled to maintain the health of workers.Work, which contributes to the physical and social well-being of people, can become harmful to health when it is not carried out to a certain extent and under appropriate conditions. This could have harmful consequences on the health of the worker through the occurrence of work accidents for example; effects can also occur when the worker concerned is still working or even when he retires, such as professional wear and tear [3]. Workplace hardship refers to the causes that make work more difficult for employees in a company and at the same time addresses the effects that they can have on health.In general, the literature defines the arduousness of work as a kind of wear and tear on the employee (both physical and psychological), daily discomfort and a probable reduction in life expectancy due to their particular working conditions [4]. While in French labor law since 2012, hardship is defined by exposure to one or more professional risk factors linked to marked physical constraints, an aggressive physical environment or to certain work rhythms likely to leave lasting, identifiable and irreversible traces on health (article D. 4161-1 et seq. of the Labor Code). The hardship that was perceived from the perspective of feelings at work is now associated with the notion of occupational risks. This link between these two concepts could raise questions such as:- from what point is exposure to a risk factor likely to leave identifiable, lasting and irreversible traces on health?- does working in an environment that includes one or more factors induce a situation of hardship?- does working with appropriate personal protective equipment exclude hardship from the work situation?It will sometimes be difficult to answer these questions precisely. Therefore, the implementation of an approach based on actions to prevent occupational risks and continuously improve working conditions appears to be an appropriate response to address the relationships between health, career paths and the extension of careers.Hardship is a public health issue which, of course, can represent an investment for companies in the short term but which, in the long term, will allow them to maintain good productivity, better performance and therefore competitiveness.
2. Material and Methods
We used different devices to collect data during our study: the sound level meter for noise measurement with a calibrator, a thermo-hygrometer for temperature measurement and a scale for mass measurement.
2.1. Sound Level Meter
This is the 8852SI/IEC 61672-1 CLASS 2 sound level meter. It is a digital sound level meter recorder for the one-time or time measurement of sound level in decibels (dB). The sound level meter is easy to install with its tripod and easy to store and transport with its case as shown in the following figure.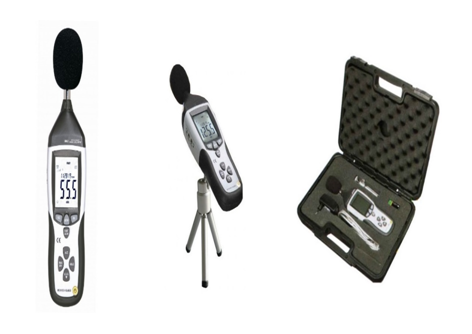 | Figure 1. Digital sound level meter 8852SI/EIC 61672-1 CLASS 2 [5] |
Acoustic calibratorThe CR:515 Calibrator is a precision acoustic calibrator designed to calibrate sound level meters and other noise measuring instruments in the field or in the laboratory in order to have compliant measurements.We used it to calibrate the sound level meter before and after taking the measurements.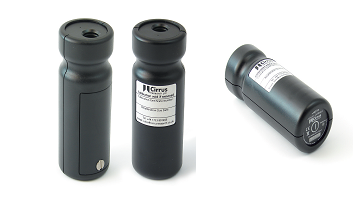 | Figure 2. CR 515 Acoustic Calibrator Cirrus IEC 60942: 2003 |
Thermo-hygrometerThe thermo-hygrometer used is a THGM003 electronic room thermometer for use in a fixed position in a private or professional setting.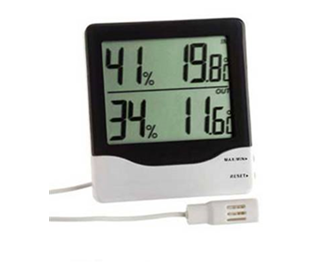 | Figure 3. THGM003 thermo-hygrometer |
Industrial scaleThe scale used to measure the masses is a 600kg/100g industrial scale, made of heat-treated steel.Like other measuring instruments, the scale used is checked every quarter to ensure compliance of the measurements. 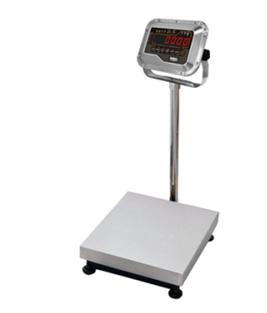 | Figure 4. 600kg/100g industrial scale |
2.2. Methods
The methodological approach consisted of:• conducting documentary research in the libraries of the University of Abomey-Calavi, on the internet and at SOBEBRA. This allowed us to collect information;• identifying positions;• collecting data;• processing data using Excel 2016 software.To identify the positions, we referred to the Single Document for the Evaluation of Professional Risks (DUERP) drawn up by the Quality, Safety and Environment Department to list the positions concerned by the arduousness study.We have identified 53 positions classified into 7 different departments, namely: Purchasing, Maintenance, Laboratories, Manufacturing, Bottling, Quay Logistics and Commercial. We specify that the positions identified only concern those who are working at the factory; administrative staff are therefore not concerned by the study.The DUERP provided us in advance with the potential risks to which workers are exposed at their workstations; it therefore helped us to partially understand the situations experienced by workers well before the information was collected.Furthermore, the DUERP concerns all employers regardless of the size of their company and requires an inventory and classification of risks for each workstation [6]. It contains, among other things, the inventory of risks, the work unit and the calculation of the proportion of employees exposed to one or more hardship factors. It aims to increase the protection of the health and safety of employees as well as to improve working conditions within the company [4]. The DUERP is developed in several stages, namely: determination of work units; identification of hazards related to the execution of the work; analysis and assessment of risks; prioritization of risks and development of the prevention program [2].Collection of informationWe visited all the departments where the positions concerned by the arduousness study and observed the workers' work situations. The data is collected from October 2021 to February 2022. We listed all the tasks performed, and identified the exposure situations (frequency, duration and intensity) by referring to the thresholds and conditions set by the regulations. A questionnaire that allowed us to talk with the workers, who told us about their difficulties at the workstation, their feelings as well as the tasks that expose them to arduousness.The mass of the loads handled, the noise intensity at each workstation as well as the temperatures, the inventory of chemicals used by department, the number of technical actions in 30 seconds; are the data collected. Furthermore, we specify here that we had collected the information.Processing of informationIt consisted of analysing the information collected, classifying it, comparing it to exposure situations at regulatory thresholds and declaring workers in a difficult situation or not.For the chemical risk analysis that we had started, we followed the steps chosen by the [7] except that we stopped at stage 3 of the process given the number of chemical products used in the industry and especially because of the overall study of arduousness.1. Inventory of hazardous chemicals used (with a pictogram);2. Recovery and updating of all safety data sheets;3. Analysis of safety data sheets;4. Determination of the frequency of use and the quantity used by each department;5. Assessment of handling and protections in place by product;6. Prioritization of exposures;7. Action plans for reducing chemical risks;8. Creation of regulatory documents (job description/exposure description).For the assessment of hazardous chemical agents, we based ourselves on the risk phrases mentioned in the MSDS to identify the chemical products concerned by the arduousness system; we first analysed, based on the frequency of use of these products, whether the actual contact time exceeds 150 hours per year. Secondly, we declared workers whose contact with chemical products is frequent and permanent to be arduous, but we were unable to determine exactly the duration of exposure (laboratory technicians for example).
3. Results and Discussion
The information from the processing of the information allowed us to present below the stress factors by service. Indeed, the analysis of the hardship factors took into account not only the staff of SOBEBRA but also the providers. So, we put all the information together and processed it together.
3.1. Dock Logistics
Dock logistics is the section of SOBEBRA that handles the storage of finished products and their delivery at the request of customers. Table 1 shows the number of staff exposed to stress factors in the dock section. From an analysis of this table, it emerges that all workers except Maneuvers work in alternating shifts. Then, the Carists and Tractorists, in addition to the previous factor, are still exposed to two other factors: noise and mechanical vibrations. In this section, Carists (including Tractorists) are therefore the most exposed to the results observed.Table 1. Number of employees exposed to hardship factors in the quayside section 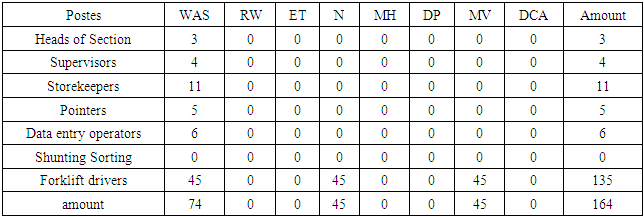 |
| |
|
At the dock, it is noted that factors such as "repetitive work", "manual handling" are negligible and factors such as "extreme temperatures", "painful postures" and "dangerous chemical agents" are absent.The following abbreviations are made in the item-factor contingency tables.Caption: abbreviations for designating factors.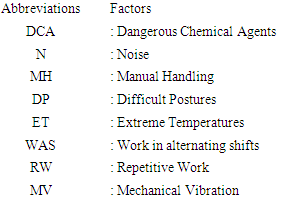
3.2. Raw Materials and Consumables Warehouse (RMC)
The warehouse is responsible for the storage and delivery of raw materials (maize and malt) and consumables (corks, labels, collars, etc.) used in the manufacture of the products. It also stores the chemicals used in the plant. Table 2 shows the number of staff exposed to risk factors in the MPC shop. It can be seen from this table that workers are less exposed to risk factors. However, forklift operators are exposed to noise from the forklift they drive, manual handling of loads (as well as manoeuvring) and mechanical vibrations.Table 2. Number of employees exposed to risk factors in the MPC shop 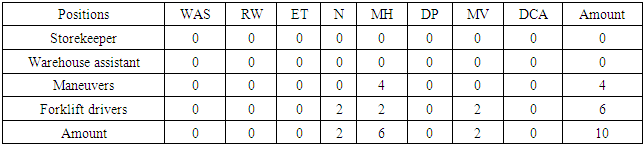 |
| |
|
At the MPC shop, the factors ‘work in alternating shifts’, ‘repetitive work’, ‘extreme temperatures’ and ‘awkward postures’ are absent, while the factor ‘dangerous chemical agents’ is negligible.
3.3. Maintenance, Automation, Dimo Maint and General Services
Maintenance includes mechanics and utilities, welding and turning. Workers in these departments carry out preventive and corrective maintenance on equipment. This department is the second largest in terms of staff numbers after bottling, and is subdivided into several sections.
3.3.1. Locker Factory Section
Table 3 shows the number of operatives exposed to hardship factors in the maintenance crate factory section. The Section Manager, Supervisors and Operators are all exposed to ‘noise’. In addition to ‘noise’, the four Supervisors and the twenty-one Operators are exposed to ‘work in successive alternating shifts’ and only the Operators are still under the effect of ‘dangerous chemical agents’: thinner (H351)1, polyiflex ink (H351; H362); CMR chemical products used for screen printing. Table 3. Number of operatives exposed to risk factors in the maintenance locker factory section  |
| |
|
1: The numbers in bold and underlined preceded by ‘H’ are the risk phrases for the chemicals covered by the arduous working conditions scheme.In this section, the factors ‘repetitive work’, ‘extreme temperatures’ and ‘manual handling of loads’ are negligible. Painful postures’ and “mechanical vibrations” are absent.
3.3.2. Mechanical Sections and General Services
Table 4 shows the number of staff exposed to hardship factors in the mechanical section of the Maintenance Division. Firstly, we note that all the posts are exposed to ‘work in successive alternating shifts’, with the exception of the head of the forklift garage section. Secondly, the thirty-two Mechanics (including Welders and Turners) are exposed to three other factors such as ‘extreme temperatures’, ‘noise’, and ‘dangerous chemical agents’: stainless steel electrodes (H317; H340; H361f; H330; H311; H301; H334; H335; H319; H351; H372 and degreasing agent (H317) These DCAs are used much more by the Welders. The seven machinists and five forklift mechanics are exposed to ‘noise’ and ‘awkward postures’ respectively.Table 4. Number of employees exposed to risk factors in the Mechanical Section of the Maintenance Division 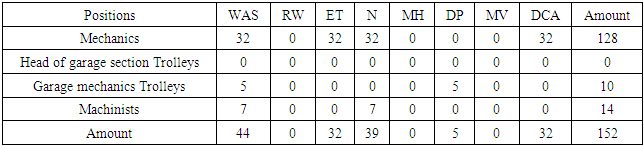 |
| |
|
In the mechanical section, factors such as repetitive work, manual handling of loads, awkward postures and mechanical vibrations are negligible.
3.3.3. Electrical Sections
Table 5 shows the number of employees exposed to hardship factors in the Electricity section of the Automation, Dimo maint and General Services Division. We note that the eleven bottling and prevention electricians and the six automation electricians are exposed to ‘work in alternating shifts’, ‘extreme temperatures’ and ‘noise’, while the seven general service electricians are only exposed to ‘work in alternating shifts’.Table 5. Number of employees exposed to risk factors in the electricity section of the Automation, Dimo maint and General Services Division  |
| |
|
In the electricity section, factors such as ‘repetitive work’, ‘manual handling of loads’, ‘awkward postures’, ‘mechanical vibrations’ and ‘dangerous chemical agents’ are absent.
3.3.4. Spare Parts Shop (PDR)
Finally, Table 6 looks at the number of staff exposed to hardship factors in the spare parts shop (PDR). In fact, only the six warehouse assistants are exposed to ‘work in successive alternating shifts’.Table 6. Number of employees exposed to risk factors in the spare parts shop (PDR)  |
| |
|
Only the factor of ‘working in successive alternating shifts’ is more pronounced in this shop. Nonetheless, loads of negligible weight are handled, and it should be noted that the temperature of the working environment in hot weather is slightly higher than usual.
3.3.5. Manufacture
This is the department responsible for making beer and soft drinks. It can be divided into three sub-departments: brewing, cellar and blower.Brewing sectionThis sub-department is responsible for preparing the beers. It is supplied with raw materials by the blower, which supplies it with maize and malt in proportions that depend on the type of beer to be produced. Table 7 shows the number of employees exposed to arduous brewing conditions. From its analysis, we note that the four Brewers, the four Brewery Helpers and the nine Blower Labourers are exposed to ‘working in successive alternating shifts’, with the exception of the Section Manager. In addition to this factor, the nine Blower Labourers are exposed to manual handling of loads.Table 7. Number of employees exposed to brewing-related risk factors 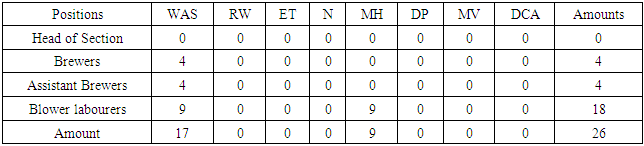 |
| |
|
In this section, the factors ‘repetitive work’, ‘extreme temperatures’, ‘awkward postures’ and ‘mechanical vibrations’ are absent, while ‘noise’ and ‘dangerous chemical agents’ are negligible. The chemicals used in the brewing process are used for tank maintenance and rust removal.
3.3.6. Cellar
This is the section where the beer is fermented, preserved and filtered before being bottled. Several analyses and tests on the products manufactured (beverages), carried out by the Central and Technical Laboratories, are always carried out here to ensure product quality.Table 8 shows the number of employees exposed to arduous work at the winery. We can deduct from this that the three Production Assistants, the four Fermenters, the four Filterers and the five Cellar Workers are all exposed to ‘alternating shift work’.Table 8. Number of employees exposed to hardship factors in the cellar 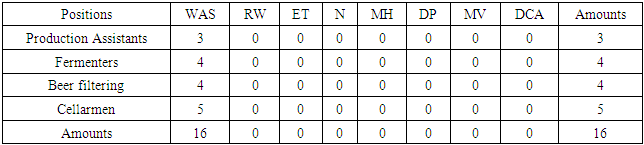 |
| |
|
Nevertheless, in this section, the factors ‘manual handling of loads’, ‘noise’ and ‘dangerous chemical agents’ are experienced by the workers, but the regulatory thresholds are not reached, nor are the conditions met. The factors ‘repetitive work’, ‘extreme temperatures’ and ‘awkward postures’ are absent.
3.3.7. Syrup Section
This is the section where soft drinks are manufactured. This section is also responsible for regular monitoring of the water used in the company.Table 9 shows the number of operatives exposed to hardship factors in the syrup factory. It can be seen that the three syrup makers, the three syrup maker helpers and the three mix drivers are all exposed to ‘working in successive alternating shifts’ and ‘noise’.Table 9. Number of employees exposed to hardship factors at the syrup factory  |
| |
|
It should be noted that the factors ‘manual handling of loads’, ‘awkward postures’, ‘dangerous chemical agents’ and ‘extreme temperatures’ are all covered, but neither the regulatory thresholds nor the conditions are met. The factors ‘repetitive work’ and ‘mechanical vibrations’ are absent.
3.3.8. Traffic Jam
Also known as ‘packaging’, this is the department in which manufactured beverages are bottled, encapsulated and labelled. This is the department with the highest number of employees and which exposes the most workers, given the number of factors present in this department. Table 10 shows the number of workers exposed to the hardship factors at the bottling plant. We can deduct from this that the three Section Managers, the ten Team Managers, the three Production Assistants, the eighty-six Operators and the eighteen Depalletizing Labourers are all exposed to ‘alternating shift work’ and ‘noise’. Only the Team Leaders and Operators on the one hand, and the Labourers depalletizes on the other, are exposed to ‘extreme temperatures’ and ‘repetitive work’ and ‘manual handling of loads’ respectively, in addition to the two factors mentioned above.Table 10. Number of employees exposed to hardship factors at bottling plants 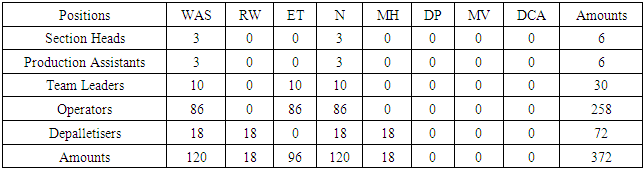 |
| |
|
However, the factors ‘awkward postures’ and ‘mechanical vibrations’ are absent. Certain chemical products such as chlorine, soda, etc. are used in this department for the maintenance, cleaning and descaling of machines.
3.3.9. Laboratory Service
Quality Control is the department responsible for checking raw materials through to finished products, monitoring production processes and analysing wastewater with a view to its disposal. These tasks are assigned to the central laboratory, the technical laboratory and the wastewater treatment plant (STEP) respectively. This is the department that handles the chemicals for the various physico-chemical, microbiological and other analyses.In fact, according to Table 11, all of the twenty laboratory workers, in addition to the four WWTP operators, are exposed to risks associated with ‘dangerous chemical agents’: orthophenylene diamine (H317; H341; H351), potassium chromate (H317; H350i), isooctane (H360) as a result of direct exposure to the products by various routes. In addition to the above factors, the Technical Laboratory Operators are exposed to noise, while the STEP Operators and Technical Laboratory Operators are exposed to ‘alternating shift work’.Table 11. Number of employees exposed to hardship factors in laboratories  |
| |
|
In the course of our work, most of the jobs were taken into account and the analysis of the arduousness factors was carried out for each of them. Using all the above data, the graph in Figure 5 below shows the impact of the factors on workers in each sector of activity at SOBEBRA.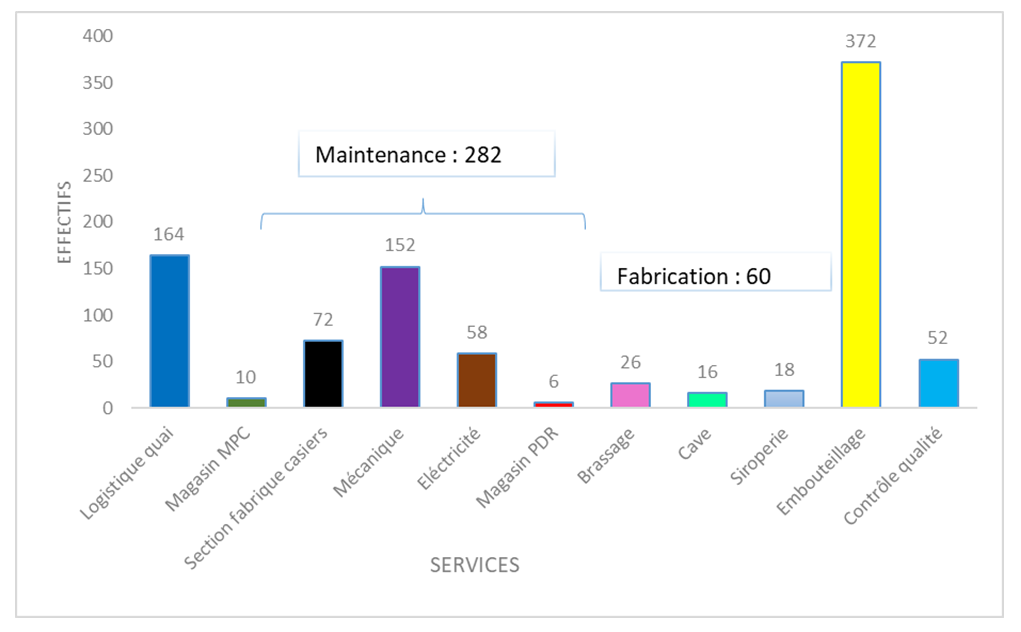 | Figure 5. Number of employees exposed to hardship factors |
It should be noted that the factors ‘night work’ and ‘activities performed in a hyperbaric environment’ are not observed. Work in successive alternating shifts’ is more frequently observed, followed by “noise” and “extreme temperatures”. Figure 5 shows the number of employees potentially affected by arduous work in the various departments concerned. Maintenance ranks second with an impact of 282, followed by logistics with an impact of 164, the manufacturing department with an impact of 60 and finally the laboratory with an impact of 52. We can therefore deduce that bottling and maintenance staff are the most exposed to stress factors. These two departments are followed by Dockside Logistics, Manufacturing and Laboratory (quality control).
4. Conclusions
Faced with complex and changing regulations, occupational health and safety issues are becoming increasingly important for companies, particularly because of the financial consequences they can have. Our work has enabled us to measure the indicators of control of arduousness factors on four hundred (400) SOBEBRA-Cotonou employees exposed to eight factors, two of which are mainly work in successive alternating shifts and noise. The ‘Bottling’, ‘Mechanics’, ‘Electricity’ and ‘Automation’ departments are the most exposed to arduous work. However, SOBEBRA is very concerned about the health and safety of its workers and has to a large extent taken the appropriate measures to control the factors of arduousness in the Beninese national regulatory context, which is marked by a notorious shortcoming in this area.Nevertheless, for each factor, we have listed the existing measures and proposed means of prevention to enable SOBEBRA to cope better with the arduousness factors.
ACKNOWLEDGEMENTS
The authors are grateful to the staff of the Laboratory for their help in research work.
Scientific Contributions
All authors contributed to the study conception and design. Material preparation, data collection and analysis were performed by Alphonse Sako Avocefohoun, Rose Mikponhoue, Mahoudjro Theotime Francis Hounsou, Roméo Aguiar, Papin Sourou Montcho, Gbèssohèlè Justin Behanzin, Elie Sogbochi and Alassane Youssao Abdou Karim Wrote the first draft of the manuscript. All authors commented on previous versions of the manuscript. All authors read and approved the final manuscript.
References
[1] | M. Gilles, Preventing wear and tear to meet the challenge of aging at work: the experience of the anact network. In Work, Career Path and Prevention of Occupational Attrition. 2020. |
[2] | E. Yilmaz, Work mushroom, statistical evaluation, Center for. 2006. |
[3] | N. Hariri et al., “Évaluation d’impact de l’explosion du port de Beyrouth,” HAL Open Sci., 2021, [Online]. Available: https://hal.archives-ouvertes.fr/hal-03269510. |
[4] | C. Drapier, “La santé des travailleurs immigrés en France Exhausted migrant effect:,” 2021. |
[5] | Moineau Instruments., Notice d’emploi du Sonomètre Enrégistreur 8852SI. 2018. [Online]. Available: www.moineau-instruments.com. |
[6] | C. Radé, C., & Dechristé, Labor Code., In Dalloz. 2005. |
[7] | G. Mohamed and A. Youcef, “Etude de la qualité de l’eau du robinet de la ville de Frenda (TIARET),” Ecol. Fondam. Appliquée, pp. x–xii, 2018. |