V. K. Srivastava
Department of Mechanical Engineering, Indian Institute of Technology, BHU, Varanasi, India
Correspondence to: V. K. Srivastava, Department of Mechanical Engineering, Indian Institute of Technology, BHU, Varanasi, India.
Email: |  |
This work is licensed under the Creative Commons Attribution International License (CC BY).
http://creativecommons.org/licenses/by/4.0/

Abstract
Solid-vapor reaction process (SVRP) method is used to synthesize the silicon carbide (SiC) nanofibers with the variation of temperature 550-650°C respectively. Synthesize samples are heated at 700°C for 2 hours to burn out the carbon residues. The synthesize SiC nanofibers consist of SiC-SiC with longer length than that of the mother carbon nanofibers. The microstructure of the synthesize sample is characterized by X-ray diffraction (XRD), scanning electron microscopy (SEM) and transmission electron microscopy (TEM). The results indicate that the carbon nanofibers are fully converted into the silicon carbide nanofibers uniformly.
Keywords:
Silicon carbide, Carbon nanofiber, Solid-vapor reaction, X-rays diffraction, Scanning electron microscopy
Cite this paper: V. K. Srivastava, Synthesis of Silicon Carbide Nano Fillers by Solid-Vapor Reaction Process Method, Nanoscience and Nanotechnology, Vol. 8 No. 1, 2018, pp. 7-10. doi: 10.5923/j.nn.20180801.02.
1. Introduction
The reduction of metal precursors to active catalyst have been considered for particle size since sintering of particles into bigger size is critical due to control of size at higher temperature. A variety of synthesis methods are used to produce carbon nanofibers structure. Silicon carbide is a very hard (elastic modulus 424 GPa) with a high dielectric strength, and more than pure silicon. The most studies concerning the catalytic hydro generation of ethylene related to use of nobel metals, such as platinum and paldium. Nickel has been found to exhibit a very high activity for the conversation of ethylene. whereas metals likes copper and iron. Therefore the conversion of silicon into silicon carbide, generally, Arc discharge or plasma decomposing method used and with selective catalysis, since discovery of carbon nanofibers [1]. Silicon carbide nanofibers have been produced by various methods particularly with the synthesized precursor process. Preparation of carbon nano fibers (CNFs) from carbon monoxide or hydrocarbons under milder conditions over a catalyst is regarded as the most promising rout in terms of their purification or isolation from unwanted carbonaceous products, scale-up of production, and handling of the products [2, 3].Consider that after the synthesis of CNFs is fully dispersed with thin root of pyrocarbon on the surface. This show that synthesis routes of lower temperature must be used to get clean surfaces of CNFs without requiring a tedious purification with high cost. However, carbon nanofibers have been adopted as template materials for the preparation of many nanomaterials. Beker et al have frequently investigated Ni alloys including Ni-Fe to synthesis the carbon from methane, ethane, ethylene, CO and their mixture [4]. Ni-Fe mixture is also very useful for catalytic activity. Silicon carbide (SiC) is a very important semiconductor material for electrical devices that are used in severe environments such as under high temperature and high power. Also, silicon carbide has been widely used in abrasives, refractories, ceramics, and catalyst supports due to its high hardness and strength, high elastic modulus, low thermal expansion, and excellent thermal shock resistance [5, 6]. Silicon carbide nanofibers have been produced by various methods and, in particular, by the carbonization of silicon nanowire, the deposition of silica on carbon nanotubes by CVD, the gas-phase chemical deposition of carbon from methane on a silicon substrate using GaN powder, and the carbon-thermic reduction of SiO2. Silicon carbide nano-rods are produced by the pyrolysis of methane on a silicon substrate with a thin layer of nickel (30-100nm). The synthesis of SiC-NTs has been reported in a series of publications in recent years, but there is no weighty evidence that the observed nanofibers are ordinary layer-type SiC-NTs, since they are often identified with the jointly produced SiC nanofibers or carbon nanotubes. Recently, SiC nanofibers and nanofibers have been synthesized by the reaction of SiO with carbon nanotubes and the reaction of Si with nanotubes. However, there are only SiC nanofibers synthesized when using SiO reaction with carbon nanotubes. SiC nanotubes synthesize by the reaction of Si and carbon nanotubes need long dwell time, which is about 100 hours. In our previous studies, SiC micro tubes have been successfully synthesized by the reaction of SiO with carbon template and carbon fibers [7, 8].In this study, Ni-Fe, Ni-Al and Ni-Fe-Al catalysts were supported on carbon nanofibers to prepare the SiC synthesized by thermal decomposition of C2H4. Synthesized microstructures of carbon nanofibers and SiC nanofibers were characterized by XRD, SEM, and TEM methods.
2. Experimentation
Reagent grade iron nitrate [Fe(NO3)3·9H2O], nickel nitrate [Ni(NO3)2·6H2O], and nickel aluminum Al(NO3)3 were used to prepare the catalyst. Three kinds of catalysts (Ni-Fe, Ni-Al and Ni-Fe-Al) were prepared by dissolving their nitrate into ethanol using mole ratio 1:1 of the nitrate. The mixed liquid were dried at 70°C after syndicated for 5 minutes, then the dried powder was heated at 110°C for 8 hours. The resulting powder was used as catalyst after grounding.Silicon carbide (SiC) nanofibers were synthesized with the activation of carbon nanofibers and SiO vapor by solid-vapor reaction process (SVRP) at temperature range 550-650°C. Carbon nanofibers were grown using alloys of Ni-Fe, Ni-Al and Ni-Fe-Al catalysts by thermal decomposition of C2H4. After removal of catalyst with 2 mol / l HNO3, the carbon nanofibers were aligned unidirectional into crucible and then placed in center of reaction tube. A solid-vapor reaction occurred between carbon nanofibers and SiO vapor at a range of temperature of 550-650°C and at different dwell times with a heating rate of 5°C / min in an Ar/H2 (160:40) flow of 200 cm2 (ml / min). The pack composition for Si and SiO2 was adjusted with 1:1 mole ratio, which was used as precursors of the SiO vapors.The reaction can be explained as follows [2]. | (1) |
 | (2) |
Now, synthesized samples were heated at 700°C for 2 hours to burn out the carbon residues. Structural analysis of the synthesized materials was carried out using X-ray diffraction (XRD, Philips X-pret MPD, Model PW3040, Eindhoven, Netherlands) employing Cu-Kα radiation. The microstructure of the synthesized materials was observed using a scanning electron microscopy (SEM, JEOL Model JMS-840, Tokyo, Japan) and TEM (Philips-CM200).
3. Results and Discussion
The peculiar growth of cementation SiC involves the first grown carbide layers located at the outer surface of the coated part. Hence, XRD of this surface describes the structural properties of material obtained after short duration of time. On the other hand, diffraction at the inner surface of totally cemented substrate was appeared as the formation of SiC layers. Figs. 1 (a & b) represent two patterns obtained at temperatures 550°C and 650°C. In both patterns, the main peaks of Si and SiC are visible. However, peaks of Si are disappeared with the increase of temperature from 550°C to 650°C. This clearly indicates that Si substrate is fully converted in SiC layer. From this result, we can see that cementation-SiC growth occurs due to gaseous diffusion of SiO and CO. 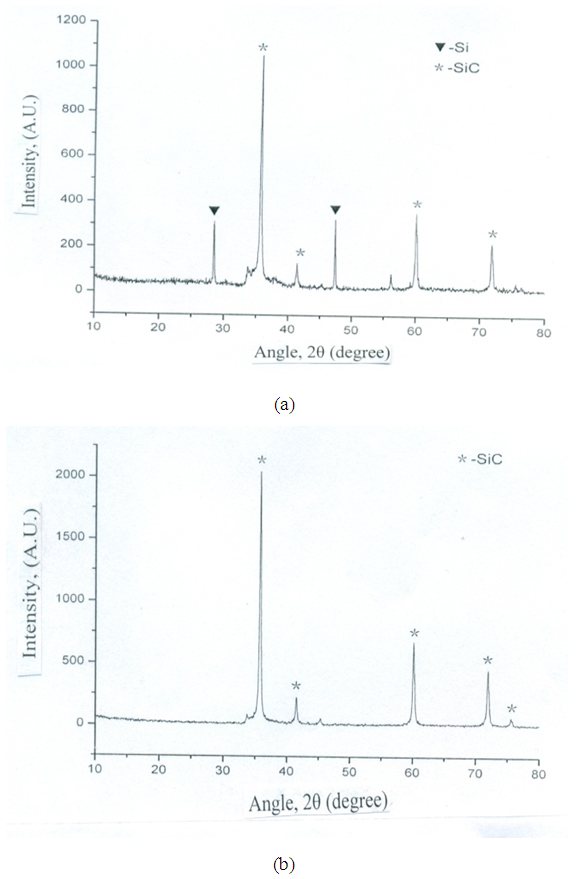 | Figure 1. XRD patterns of SiC nanofibers prepared by carbon nanofibers synthesized at (a) 550°C (b) and 650°C |
Figs. 2 and 3 illustrate micro features of SiC nanofibers produced by synthesis of carbon nanofibers at different temperature of 550°C and 650°C. Two kinds of SiC nanofibers were observed in the product. One part was relatively thick fibers average of 200 nm and the other part appeared as average of 50 nm. However, SiC nanofibers are clearly visible at high temperature 650°C compared to 550°C, as can easily identified from TEM Fig. 4. The fibers were not straight, but entangled, exhibiting many nodes along their axes. The produces fiber showed a fish bone-like texture. All fibers showed much distorted texture but aligned in unidirectional. However, shrinkage of coated layers in the periphery of fibers appeared because of residual stress [3, 4].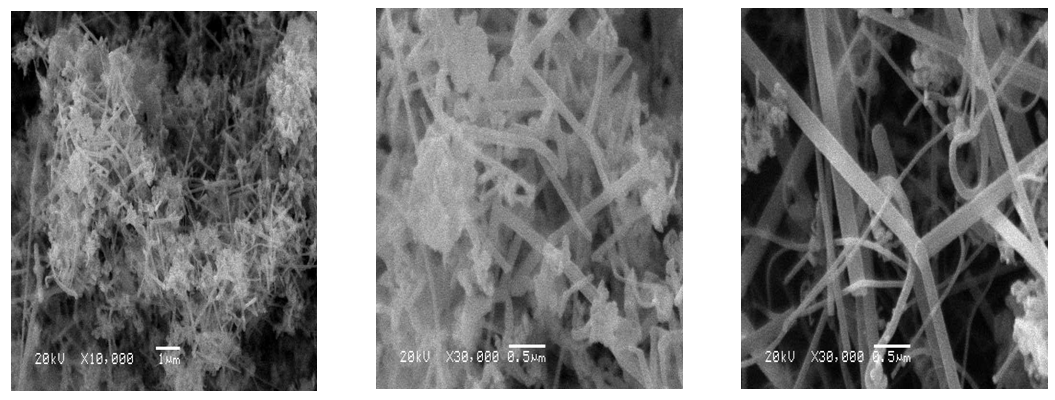 | Figure 2. SEM micrographs of SiC nanofibers prepared by carbon nanofibers synthesized at 550°C |
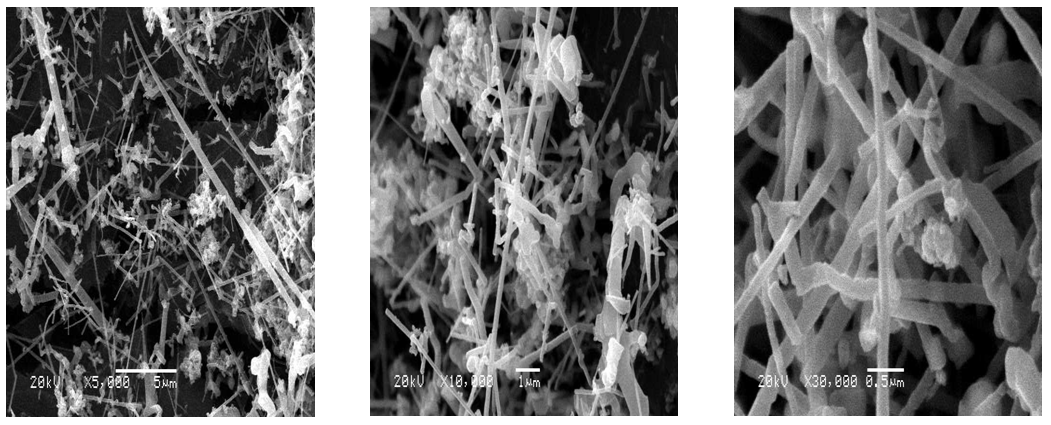 | Figure 3. SEM micrographs of SiC nanofibers prepared by carbon nanofibers synthesized at 650°C |
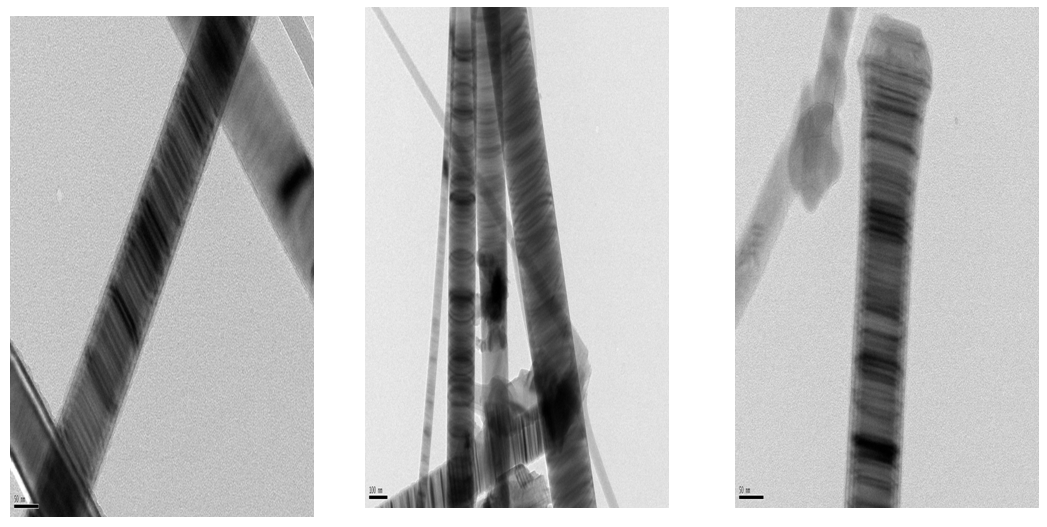 | Figure 4. TEM micrographs of SiC nanofibers prepared by carbon nanofibers synthesized at 550°C |
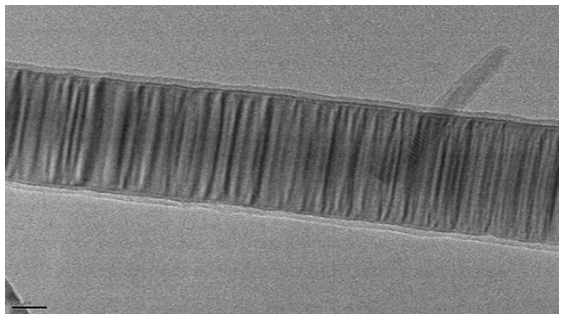 | Figure 5. TEM micrograph of SiC nanofibers prepared by carbon nanofibers synthesized at 650°C |
The experiment observation clearly indicate that the vapor solid reaction process takes place first in the interface between the SiO source and the carbon nanofibers. A small addition of iron was found to provide thinner and more homogeneous carbon nanofibers. A particular alloy of Ni-Fe supported on the carbon black produced fibers of about 10-30 nm diameter (Fig. 2) under the same conditions where the thick fibers of average 150 nm diameter were synthesized over Ni alone on the carbon black. However, more than 30% iron in the alloy catalyst resulted in increase of diameter of the produced carbon nanofibers. With the restrictions of the top carbon nanofibers and the wall of the crucible, the dispersion of the CO gas can be restrained and it has a long resident time in the crucible, which will enhance reaction and consequently reaction [2]. The evidence for this is the presence of structural SiC non-nanofibers at the bottom of the sample. Therefore, it is the CO gas which plays an important role in the widely distributed diameters of SiC nanofibers on the top layer and in the middle layer due to the epitaxial growth from reaction [6]. Another characteristic of the SiC nanofibers produced in the experiment is their nearly straight shape, which is obviously different from the starting carbon nanofibers which are curved and twisted around one another. It seems that carbon nanofibers are not a shape memory synthesis process.Based on the above analysis, it can be seen that the diameter and shape of the produced SiC nanofibers can be controlled by the local partial pressure of CO gas and the reaction temperature, respectively.
4. Conclusions
The conclusions of this study describing the successful preparation of SiC nanofibers from solid-vapor reaction process, which were obtained through synthesis of carbon nanofiber and SiO at the temperature range of 550-650°C. This demonstrated that the reactions of SiC-C interface were appeared due to the diffusion of carbon substrate with the effect of Ni-Fe, Ni-Al and Ni-Fe-Al catalysts and by thermal decomposition of C2H4. Ni component alone is working as active catalysts for carbon nanofibers synthesis, although iron is almost inactive towards SiC growth. Thus, carbon nanofiber is fully converted into the SiC nanofibers.
ACKNOWLEDGEMENTS
The author would like to thanks, Department of Physics, Institute of Science, BHU and Department of Mechanical Engineering, Indian Institute of Technology, BHU, Varanasi-221005 India for experimental supports.
References
[1] | S. Iijima, “Helical microtubules of graphite carbon”, Nature, Vol. 354, pp. 56-58, 1991. |
[2] | J.H. Kang, H.M Cha, J.H. Lee, Y.G. Jung, H.S. Lee, and V.K. Srivastava, “Synthesis and characterization of non-oxide ceramic coatings on graphite substrates by solid-vapor reaction process”, Progress in Organic Coatings, Vol. 61, no. 2-4, pp. 291-299, 2008. |
[3] | S.A. Lim, S.H. Yoon, Y. Korai, and I. Mochida, “Selective synthesis of thin carbon nanofibers: I. Over nickel-iron alloys supported on carbon black”, Carbon, Vol. 42. pp. 1765-1781, 2004. |
[4] | V.V. Pokropivnyi, and P.M. Silenko, “Silicon carbide nanotubes and nanotubular fibers: synthesis, stability, structure, and classification”, Theoretical and Experimental Chemistry, Vol. 42, pp. 3-15, 2006. |
[5] | Baker RTK, Catalytic growth of carbon filaments, Carbon, 37 (3), 1989. 1989. |
[6] | Park C, and RTK Baker, “Carbon deposition on iron-nickel during interaction with ethylene-hydrogen mixtures”, Journal of Catalysis, Vol. 179, pp. 361-374, 1998. |
[7] | Park C and RTK Becker, Carbon deposition on iron-nickel during interaction with ethylene- carbon monoxide- hydrogen mixtures, Journal of Catalysis, 190, 104-117, 2000. |
[8] | J.H. Sinfelt, J.L. Carter, and D.J.C. Yates, “Catalytic hydrogen analysis and dehydrogenation over copper-nickel alloys”, Journal of Catalysis, Vol. 24, pp. 283-296, 1972. |