Rahul K., Madhukar H. Shetty, Karthik Madhyastha N., Pavana Kumara B., Kenneth Paul D’Souza, Loyd D’Souza
Department of Mechanical Engineering, St Joseph Engineering College, Mangalore, India
Correspondence to: Rahul K., Department of Mechanical Engineering, St Joseph Engineering College, Mangalore, India.
Email: |  |
Copyright © 2017 Scientific & Academic Publishing. All Rights Reserved.
This work is licensed under the Creative Commons Attribution International License (CC BY).
http://creativecommons.org/licenses/by/4.0/

Abstract
Natural fiber reinforced composites materials are gaining enormous attention among academicians and researchers off late. The sustainability and ecofriendly nature, in addition to easy availability and low cost are the main reasons. Several combinations of fiber and filler contents are being tried to come up with materials with enhanced tribological and mechanical properties. The present work deals with the processing and characterisation of banana fiber reinforced epoxy composites with Nano silica filler. The composite material samples were fabricated by pouring a mixture of epoxy and reinforcement into an open mould. Curing was done at room temperature under pressure. Different combinations like 3, 4 and 5%wt of banana fibers along with 0.1% wt of Nano silica fillers were used. The specimen were tested for various mechanical, wear and water absorption properties. It was found that the addition of Nano silica greatly enhanced the wear behaviour of the composite. However slight decrease was reported in the hardness of the material.
Keywords:
Epoxy, Banana fibers, Nano silica
Cite this paper: Rahul K., Madhukar H. Shetty, Karthik Madhyastha N., Pavana Kumara B., Kenneth Paul D’Souza, Loyd D’Souza, Processing and Characterisation of Banana Fiber Reinforced Polymer Nano Composite, Nanoscience and Nanotechnology, Vol. 7 No. 2, 2017, pp. 34-37. doi: 10.5923/j.nn.20170702.02.
1. Introduction
A composite is a macroscopic combination of two or more multiphase distinct materials, having an interface between them. Composite materials are composed of two phases. One is the matrix, which is continuous and surrounds the other phase, often called the dispersed phase or reinforcement.Mankind has been aware of composite materials since several hundred years before Christ and has applied innovative ideas to improve the quality of life. Historical examples of composites are abundant in literature. Significant examples include the use of reinforcing mud walls in houses with bamboo shoots, glued laminated wood by Egyptians (1500 BC) and laminated metals in the forging of swords (1800 AD). Over the past few decades, as a result of research and innovation, a wide variety of composite materials have been developed which have proved to be useful in almost all fields of science and technology.Natural fibres have attracted the interest of researchers, material scientists, and industries, owing to their specific advantages as compared to conventional or synthetic fibres from the past [1]. The attractive and possible advantages, such as reduced tool wear, low cost, and low density per unit volume and acceptable specific strength, along with their sustainable renewable and degradable features are some of the important properties of the natural fibres, which make them suitable to use as filler in polymer composites. Synthetic fibres, such as carbon fibres and glass fibres, create severe ecological, and health hazard problems for the workers employed in manufacturing of their corresponding composites as compared to composites derived from natural fibres [1]. Natural fibre shows comparatively poor fibre/matrix interactions, water resistance, and relatively lower durability [2]. The weaker interfacial or adhesion bonds between highly hydrophilic natural fibres and hydrophobic, non-polar organophilic polymer matrix, leads to considerable decrease in the properties of the composites and, thus, significantly obstructs their industrial utilization and production.Nano-particles are presently considered as a high-potential filler material for the improvement of mechanical and physical properties of polymer composites [3]. As the nano scale fillers are usually free of defects, their applications in the field of polymer composites, setup new trends of prospect to overwhelm the restrictions of traditional/conventional micrometer scale. High matrix-filler interfacial area as a result of uniform and homogeneous dispersion of nanoparticles, are responsible for changing relaxation behaviour as well as in ensuing the mechanical, molecular mobility, and thermal properties [4]. Generally, nano sized filler present in the minor zone whereas only few of the micro particles participate in the plastic zone deformation. This provides a way for the nanofillers to improve fracture and mechanical properties of the matrix having brittle property. Nanofillers, which possess greater aspect ratio are of considerable interest, and, thus, show better reinforcement for the nanocomposites production [5]. Nano fillers are generally incorporated on a weight basis for the nanocomposites development. The composite properties are greatly influenced by the specific surface area of nano fillers, which shows uninterrupted influence. A perfect substitute to traditional or conventional construction and buildings materials are the fibre reinforced polymer composites due to a number of factors, including: higher strength and stiffness with reference to specific gravity; better resistance to corrosion, fire, acids, and natural hazardous environments; non conductivity and non-toxicity; longer service life and lower life-cycle costs; and higher fatigue strength and impact energy absorption capacity [6].The objective of the present work is preparation of banana fiber reinforced polymer nanocomposite with nanosilica as filler. Further study the properties like density, hardness and tribological properties and present a new class of composite material with superior properties.
2. Methodology
2.1. Materials Used
The composite specimen was manufactured using epoxy resin Araldite LY 556 as matrix along with Aradur HY951hardner. The matrix was reinforced with Banana fibers and nano silica filler.
2.2. Fabrication
The composite specimens were fabricated using epoxy as matrix material and 4mm shredded banana fibers along with 0.1%wt nano silica as reinforcement materials. A mould cavity made of mild steel of dimensions 30mm x 30mm x 3mm was used. The epoxy resin and reinforcement materials were thoroughly mixed together and poured into the mould cavity. Curing was done at room temperature under load. Mould release wax was used for easy removal of the prepared specimen. Table 1 provides the details of the specimens prepared.Table 1. Specimens prepared 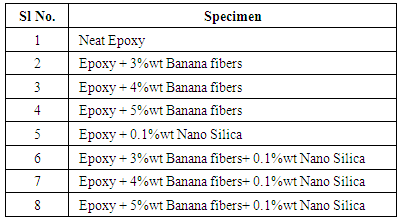 |
| |
|
2.3. Test Description
The prepared specimens were tested for density, Rockwell hardness, water absorption and abrasive wear. The ASTM standards used for each of these tests are listed in table 2.Table 2. ASTM standards 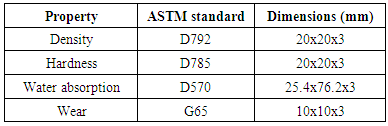 |
| |
|
The abrasive wear test was performed with three sliding distances of 40, 60 and 80 meters with loads of 10, 20 and 30 Newtons.
3. Results and Discussion
3.1. Density
Figure 1 shows the effect of addition of reinforcement on the density of the composite material. It can be observed that there was no significant change in the density of the composite with nano silica as compared to neat epoxy specimen.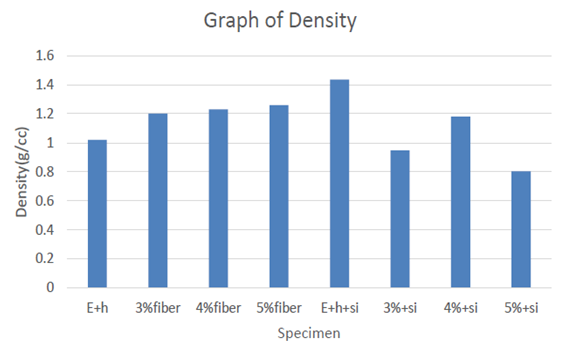 | Figure 1. Density of test specimen |
3.2. Rockwell Hardness
The results from Rockwell hardness testing is shown in Figure 2. It is observed that the addition of nano silica results in a decrease in the hardness of the composite.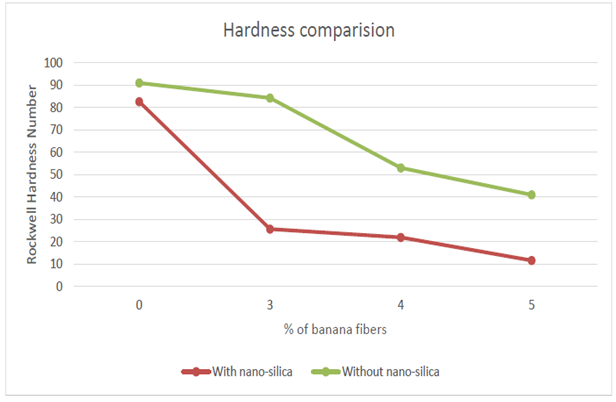 | Figure 2. Rockwell hardness |
3.3. Water Absorption Test
Figure 3 shows a plot of percentage increase in weight of the specimen when soaked in distilled water against the number of days. Clearly it can be noted that the addition of Silica and Banana fibers results in increased water absorption. However, the curves become horizontal after about 10 days in all the specimens which indicates that no further absorption of water occurs.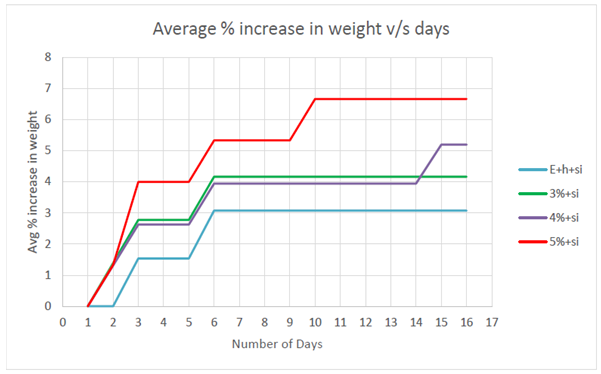 | Figure 3. Plot of amount of water absorbed Vs No of days |
3.4. Abrasive Wear Test
The effect of addition of nano silica on the wear properties for sliding distances of 40, 60 and 80m is shown in figure 4, 5 and 6 respectively for loads of 10, 20 and 30 N. From the figure 4, it can be seen that for a sliding distance of 40 m, neat epoxy showed a weight loss of 0.04g. However, with addition of 5% wt of banana fibers, the wear loss reduced to 0.02g. It was possible to further reduce the wear loss to 0.01 g with the addition of 0.1%wt Nano silica filler. A similar trend was noticed when the tests were repeated with different sliding distances which is evident from the figure 5 and 6. Thus the addition of banana fiber and silica was found to have a favorable influence on the wear properties of the composite specimen.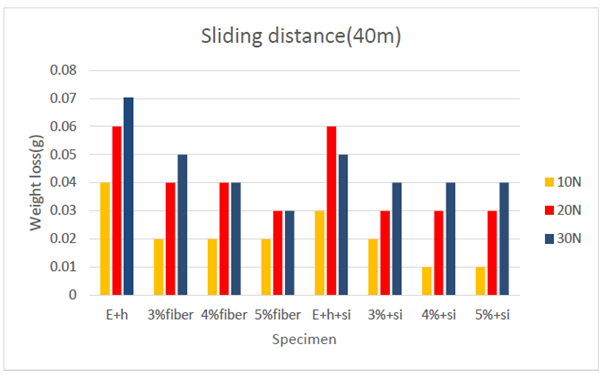 | Figure 4. Wear loss for sliding distance of 40 m |
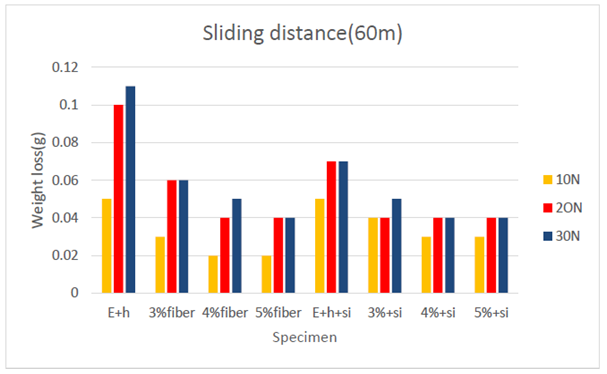 | Figure 5. Wear loss for sliding distance of 60 m |
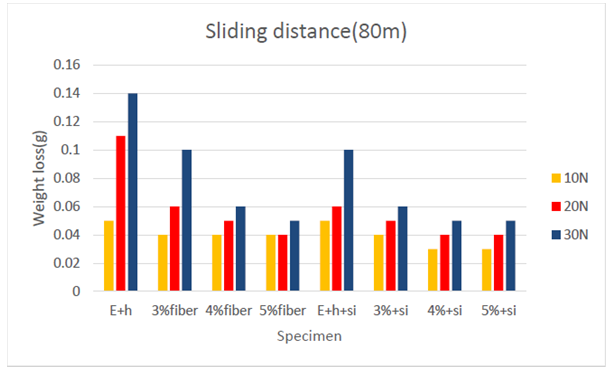 | Figure 6. Wear loss for sliding distance of 80 m |
4. Conclusions
From the present work it can be concluded that the addition of banana fiber to epoxy improves both mechanical and physical properties of the composite. Similarly, addition of Nano silica plays an important role in minimizing the wear loss. However, the tendency of Nano silica to reduce the hardness of the specimen as observed in the present study should be taken into account while using it as a filler.The enormous availability, cheaper and good mechanical properties of banana fiber reinforced composite leads way for the fabrication of lightweight materials that can be used in automobile sector as well as for household purposes.
References
[1] | S.V. Joshia, L.T. Drzal, A.K. Mohanty, S. Arora, “Are natural fiber composites environmentally superior to glass fiber reinforced composites?”, Composites: Part A 35 (2004) 371–376. |
[2] | Roger M. Rowell, Anand R, Sanadi, Daniel F. Caulfield and Rodney E. Jacobson, “Utilization of Natural Fibers in Plastic Composites: Problems and Opportunities”, Lignocellulosic-Plastics Composites, pp. 23-51 (1997). |
[3] | Farzana Hussain, Mehdi Hojjati, “Review article: Polymer-matrix Nanocomposites, Processing, Manufacturing, and Application: An Overview”, Journal of composite materials, Vol. 40, No. 17/2006. |
[4] | Paola Palmero, “Structural Ceramic Nanocomposites: A Review of Properties and Powders’ Synthesis Methods”, Nanomaterials 2015, 5, 656-696. |
[5] | Pedro Henrique Cury Camargo, Kestur Gundappa Satyanarayana, Fernando Wypych, “Nanocomposites: Synthesis, Structure, Properties and New Application Opportunities”, Materials Research, Vol. 12, No. 1, 1-39, 2009. |
[6] | Lippo Lassila, Sufyan Garoushia, Pekka K.V., Eija Sailynoja, “Mechanical properties of fibre reinforced restorative composite with two distinguished fibre length distribution”, Journal of the Mechanical behaviour of biomedical materials 60 (2016) 331-338. |