Dinesh Kumar 1, 2, Sonia Nain 1, Hemant Pal 3, Neena 1, 2, Ravi Kumar 2
1Department of Chemistry, Deenbandhu University of Science and Technology, Murthal, India
2Department of Chemistry, Dyal Singh Karnal, India
3Department of Physics, Govt. Post Graduate College Chamba, India
Correspondence to: Sonia Nain , Department of Chemistry, Deenbandhu University of Science and Technology, Murthal, India.
Email: |  |
Copyright © 2016 Scientific & Academic Publishing. All Rights Reserved.
This work is licensed under the Creative Commons Attribution International License (CC BY).
http://creativecommons.org/licenses/by/4.0/

Abstract
Modified physical mixing method was extended to fabricate carbon nanotube reinforced nanocomposites. These nanocomposites were subsequently characterized using Scanning Electron Microscopy, Electron Dispersive Spectroscopy & X Ray Diffraction techniques. Morphological studies revealed that CNTs are homogenously dispersed into silver matrix. Effect of type of CNT reinforcement on hardness & modulus of elasticity was evaluated. A higher increase in hardness & modulus of elasticity was observed for SWCNT/Ag nanocomposites than the MWCNT/Ag nanocomposites which may be attributed to superior thermo physical properties of SWCNTs.
Keywords:
Singlewalled Carbon Nanotubes, Hardness, Modulus of Elasticity, Nanocomposites
Cite this paper: Dinesh Kumar , Sonia Nain , Hemant Pal , Neena , Ravi Kumar , Carbon Nanotube Reinforced Silver Nanocomposites: Effect of Different Carbon Nanotubes on Its Mechanical Behavior, Nanoscience and Nanotechnology, Vol. 6 No. 3, 2016, pp. 39-42. doi: 10.5923/j.nn.20160603.01.
1. Introduction
Silver is an important metal with distinct characteristics. Its excellent thermal & electrical conductivity makes it an attractive material to be used as a metal interconnect in electronic devices. However, Silver is a soft metal & mechanical strength is one of the essential requirements for such materials. Silver-graphite composites have normally been used as interconnects in electronic devices [1, 2]. Superior properties of carbon nanotubes such as high aspect ratio, hardness & exceptional young’s should make them better reinforcement materials to tailor mechanical properties of metal matrix composites [3, 4]. Mechanical properties of CNT/Cu & CNT/Al nanocomposites have been extensively studied but very few reports are available on CNT/Ag nanocomposites [5-7]. Recently, Daush et.al. have reported improvement in hardness & elongation properties on reinforcement of MWCNTs in silver matrix [8]. But reinforcing effect of CNTs can be utilized only if homogenous dispersion of CNTs in metal matrix is achieved. This is a challenging task due to entangled structure of CNTs. In the present study, modified physical mixing method has been extended to fabricate CNT/Ag nanocomposites. Silver metal matrix was reinforced separately with single wall carbon nanotubes (SWCNTs) & multiwall carbon nanotubes (MWCNTs). MWCNTs are cheaper & economically more suitable for industrial applications whereas SWCNTs possess better thermo physical properties such as higher aspect ratio & specific surface area. Effect of different type of CNT reinforcement on mechanical properties of silver matrix nanocomposites has been elucidated in the present work.
2. Experimental Details
2.1. Fabrication & Consolidation of CNT/Ag Nanocomposite
Carbon Nanotube (0, 1.5, 3.0 & 4.5 Volume %) reinforced silver nanocomposites were fabricated using modified physical mixing method [9]. Functionalized nanotubes (SWCNTs & MWCNTs) & silver nanopowder were purchased from Nanoshel, USA. Weighed amounts of as received CNTs were soaked in 100 ml ethanol & sonicated in a probe sonicator for 2hrs. Then, required amounts of silver nanopowders were added to the sonicated solution. Simultaneous magnetic stirring and sonication was carried out for another 2 hrs. All the chemicals employed in the fabrication process were of analytical grade & were used without further purification. The mixture was then dried at 50°C on a hot plate to obtain the CNT/Ag nanopowder. Both MWCNT/Ag and SWCNT/Ag nanopowders were fabricated separately using this method. Samples were compacted at a pressure of 7 tons using a hydraulic press into pallets of size 13mm x 2mm. Sintering of the pallets was carried out in a horizontal tube furnace equipped with a temperature controller at 800°C for 12hrs.
2.2. Instrumentation
XRD patterns of samples were recorded on a panalytical 3050/60 Xpert-PRO using a CuKα radiation. Morphology of the samples was analyzed using a scanning electron microscope (SEM) FEI Quanta FEG 450 operated at 15 KV. Hardness & modulus of elasticity of the samples were measured using a CETR- Apex nanoindenter equipped with a berkovich diamond tip.
3. Results & Discussion
3.1. Microstructure Characterization
Microstructure characterization was carried out using X Ray Diffraction, Electron dispersive spectroscopy & Electron microscopy. X-Ray diffraction patterns in figure 1 indicate the crystalline nature of the samples. Diffraction peaks at 38.9°, 45.1°, 65.1° & 78.2° correspond to (111), (200), (220) & (311) reflections of FCC phase of silver. CNTs presence in the sample is indicated by slight hump at 2θ values between 20° – 30°.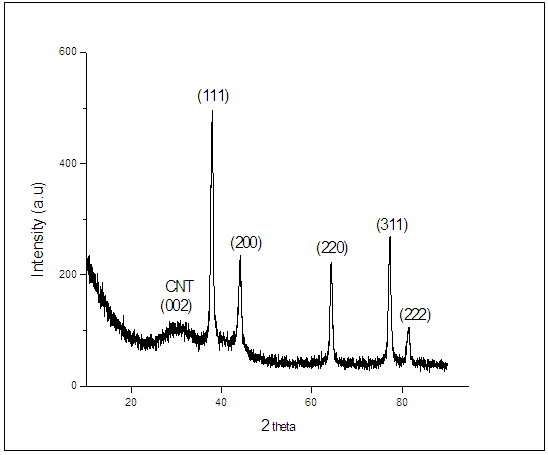 | Figure 1. XRD pattern of CNT/Ag nanocomposite |
Electron Diffraction Spectroscopy was used to analyze the elemental composition of the sample. Figure 2 confirms the volume content of the CNTs in the sample. Peaks at 3.0, 3.2 & 3.4 KeV correspond to binding energies of the silver whereas peak at 0.25 KeV correspond to binding energy of the carbon.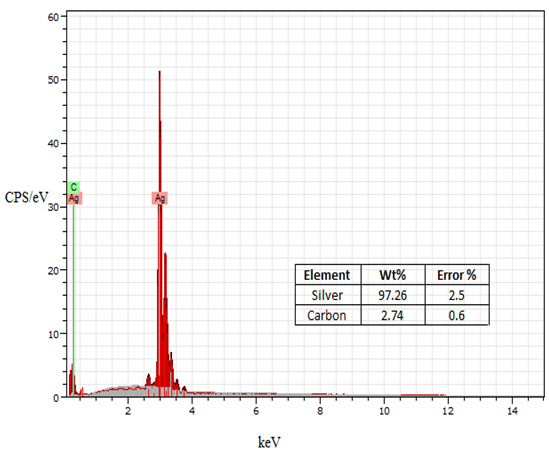 | Figure 2. EDS characteristic profile of CNT/Ag Nanocomposite |
Morphology of the samples is shown in figures 3a-c. It can be clearly seen that CNT’s are homogenously dispersed & embedded into silver matrix. Physical mixing method has been able to prevent agglomeration of CNTs to a large extent. However some agglomerates can be seen in composites reinforced with 4.5 Volume % Carbon Nanotube.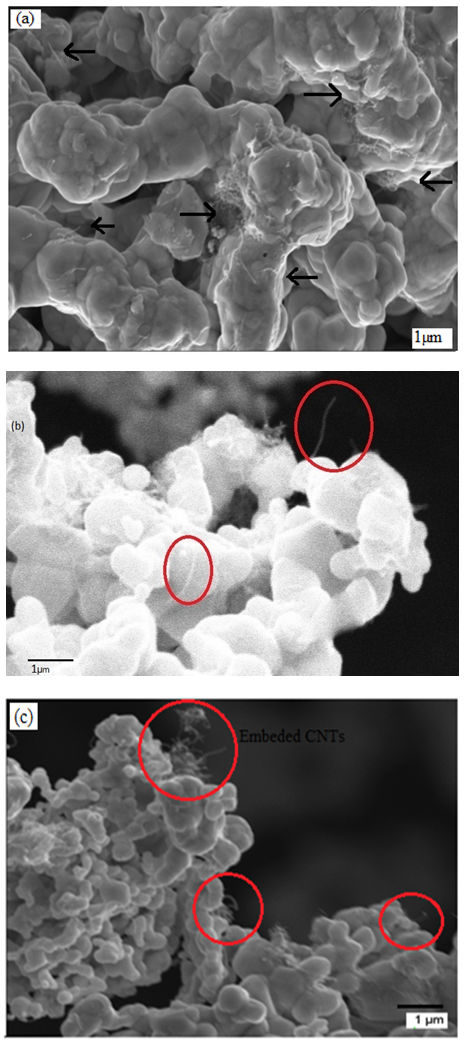 | Figure 3. SEM micrographs of (a) CNT (1.5 vol. %) /Ag, (b) CNT (3 vol. %) /Ag and (c) CNT (4.5 vol. %) /Ag |
3.2. Mechanical Properties
Mechanical properties of a composite are influenced by CNT-metal interface, volume of CNT in the composite, CNT distribution into the metallic matrix and type of CNT used as reinforcement. MWCNTs are economical due to their easy availability and are better suitable for industrial applications whereas SWCNTs possess better thermo-physical properties than MWCNTS.Hardness & modulus of the elasticity has been measured using nanoindentation technique. The data has been plotted in figure 4 & 5. Both the mechanical properties are found to improve with increase in CNT reinforcement which may be attributed to large aspect ratio & specific surface area of carbon nanotubes which is considerable higher than that of other reinforcements such as carbon fiber.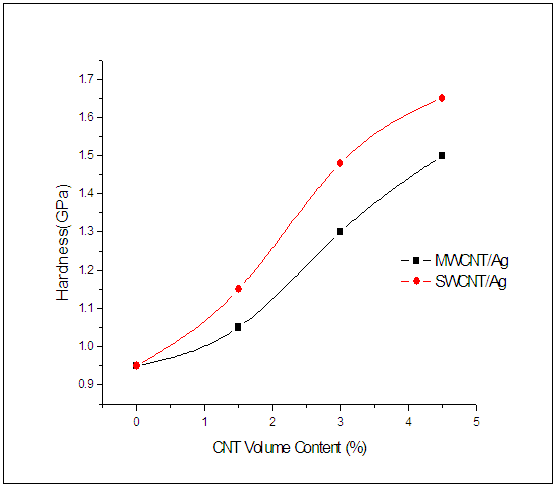 | Figure 4. Hardness of CNT/Ag Nanocomposites |
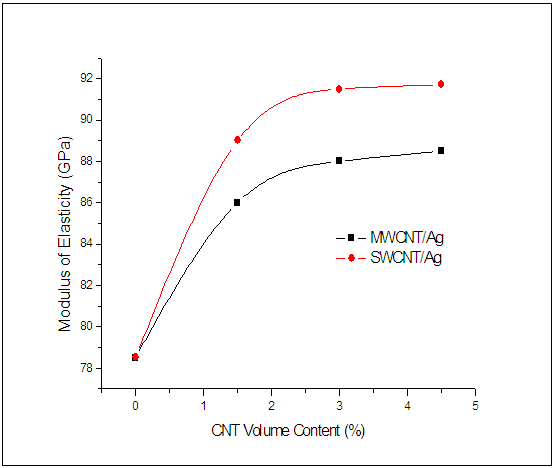 | Figure 5. Modulus of elasticity of CNT/Ag nanocomposites |
Homogenous distribution of the CNTs into silver matrix leads to the creation of a large interface between the two phases. This results into transfer of externally applied load from matrix to CNTs. Anchored CNTs inside the grain boundaries restricts the relative motion of the two phases with respect to each other which results an increase in hardness & modulus of elasticity [10]. Figure 4 & 5 clearly show that single walled carbonnanotube reinforced nanocomposites possess better hardness & a higher modulus of elasticity than the nanocomposites reinforced with multiwalled carbonnanotube. Hardness of a SWCNT/Ag nanocomposite is 1.75 GPa as compared to 1.49GPa for MWCNT/Ag nanocomposite with 4.5 Vol% CNT content. Modulus of elasticity is also higher for SWCNT/Ag than MWCNT/Ag composites with same CNT content. These superior properties of SWCNT/Ag nanocomposites are probably due to higher aspect ratio & specific contact surface area of SWCNTs as compared to MWCNTs. SWCNTs also do not possess any inactive internal layer which makes the transfer of load from silver reinforcement easier.
4. Conclusions
Modified physical mixing method was used to fabricate CNT/Ag nanocomposites reinforced with both SWCNTs & MWCNTs. Morphological studies confirmed the homogenous distribution of CNTs into silver matrix. Mechanical parameters viz. hardness & modulus of elasticity of various samples were analyzed with reference to variation in different type of CNTs. Nanoindentation testing showed that hardness & modulus of elasticity of SWCNT/Ag nanocomposite are significantly more than the hardness & modulus of elasticity of MWCNT/Ag nanocomposites which may attributed to better thermo physical properties of SWCNTs. We believe improvement in mechanical properties increases the potential of these materials for their applications as metal interconnect in electronic devices.
ACKNOWLEDGEMENTS
We are grateful to Advanced Instrumentation Research Facility (AIRF), JNU (New Delhi) for SEM, EDS & XRD analysis & Central Instrumentation Facility (CIL) at IIT Ropar for nanoindentation testing.
References
[1] | J. Sleziona, J. Wieczorek and M. Dyzia, J. Mass Media Ethics 17, 1 (2006). |
[2] | S.L. Chung, T. Hsu and H.R. Wu, Mater. Lett. 61, 3719 (2007). |
[3] | M. M. Treacy, T. W. Ebbesen and J. M. Gibson, Nature 381, 678 (1996). |
[4] | A. Krishnan, E. Dujradin, T. W. Ebbesen, P. N. Yianilos and M. M. J. Treacy, Physical Review B, 58, 14013 (1998). |
[5] | W. M. Daoush, B.K. Lim, C. B. Mo, D. H. Nam and S. H. Hong, Material Science and Engineering A, 513, 247 (2009). |
[6] | A. K. Srivastava, C. L. Xu, B. Q. Wei, R. Kishore and K. N. Sood, Indian Journal of Engineering and Material Science, 15, 247 (2008). |
[7] | S. H. Joo , S. C. Yoon, C. S. Lee, D. H. Nam, S. H. Hong and H. S. Kim, Journal of Mater. Science, 45, 4652 (2010). |
[8] | W. M. Daoush, B. K. Lim, D. H. Nam and S. H. Hong, J. Exp. Nanosci. 9, 588 (2012). |
[9] | D. Kumar, S. Nain, R. Kumar and H. Pal, Z. Naturfrosch. 70(1) a, 63 (2015). |
[10] | H. Li, A. Misra, Z. Horita, C.C. Koch, N.A. Mara, P.O. Dickerson and Y. Zhu, Applied Physics Letters 95(7), 071907 (2009). |