V. K. Srivastava
Department of Mechanical Engineering, Indian Institute of Technology (BHU), Varanasi, India
Correspondence to: V. K. Srivastava, Department of Mechanical Engineering, Indian Institute of Technology (BHU), Varanasi, India.
Email: |  |
Copyright © 2015 Scientific & Academic Publishing. All Rights Reserved.
This work is licensed under the Creative Commons Attribution International License (CC BY).
http://creativecommons.org/licenses/by/4.0/

Abstract
In this study, polymer matrix has modified by nanofillers. Multi walled carbon nanotubes (MWCNTs) filled epoxy resin and graphene nanoplatelets (GnPs) filled epoxy resin have fabricated for the dynamic mechanical and nanohardness analysis. Experimental results showed a substantial enhancement in the decomposition temperature and nanohardness of nanofillers filled epoxy resin composite. The storage modulus, loss modulus and tanδ parameters are dependent on the transition temperature (Tg), which indicates that the elastic modulus of MWCNT/epoxy resin and GnP/epoxy resin composites reduced with the increase of temperature due to the solvent effect. The nano identation results showed that elastic modulus of both nanocomposites increased with increase of nanohardness due to change of morphology. The morphology of the nanocomposites has investigated by SEM. It is clear from SEM results that the uniform dispersion of MWCNT and GnP nanofillers are visible within the polymer matrix.
Keywords:
Multi-Walled carbon nanotubes, Graphine nanoplatelets, Epoxy resin, Viscoelastic modulus, Nanohardness, Glass transition temperature, Scanning electron microscopy
Cite this paper: V. K. Srivastava, Viscoelastic and Nanohardness Behaviour of Nano Particles Filled Epoxy Resin Composites, Nanoscience and Nanotechnology, Vol. 5 No. 5, 2015, pp. 97-104. doi: 10.5923/j.nn.20150505.01.
1. Introduction
Epoxy resins are widely used in various industries due to their unique properties such as high stiffness, adhesion strength and low shrinkage in cure. Many attempts have been incorporated to improve the properties of epoxy resin. One of the major problems in unsaturated polyester epoxy resin is the poor mechanical resistance to cracks because it is very tough to produce flawless materials. As a bonding agent, epoxy resin matrix has the key role of interface bonding with reinforcing materials to transfer the applied load to the reinforcing layer. If interface bond strength in between epoxy resin and reinforcing material is not perfect, the reinforcing materials is debonded due to stress concentration. In this case adhesive layer fails and transfer the load along reinforces material direction [1].During last ten years, tremendous efforts have been made to midify epoxy resins for various applications in high performance indistries by adding micro particles also using different mixing process for the uniform dispersion of fillers [2, 3]. Fillers chosen as reinforcement are usually harder and stiffer than the matrix material. This improves the mechanical properties of epoxy resin composites. However, owing to the limited surface area of contact, the load transfer from epoxy resin to micro fillers occurs to a smaller extent. This could lead to insignificant improvement in compressive strength and impact resistance [4, 5].Due to unique properties of carbon nanotubes (CNTs) and the technological possibilities that CNT/polymer composites offer, including enhanced electrical, thermal, and mechanical properties continues to attract world wide research interest [6]. Carbon nanotubes are expected to offer major enhancements to the thermoset matrix properties by their excellent strength and stiffness, unique thermal stability, and specially, their high surface to valume ratio. The researchers have focused on the processes of uniform distribution and dispersion of the CNTs within the polymer matrix and how the interaction of the polymer chains and CNTs can be promoted. Nano fillers dispersion can also be aided by three mill rolling process, ultrasonic processor, resin transfer moulding (RTM) and surface functionalisation by means of acidor plasma treatments. Many researchers have observed substancial improvements in the epoxy resin properties as a result of introducing single walled carbon nanotubes (SWCNTs) and multi walled carbon nanotubes (MWCNTs) [7]. To get the strong interaction between tubes and polymer matrix, nanotubes must be dispersed uniform in the matrix with suitable mixing process [8]. The mechanical reinforcement of epoxy resin is controlled by the degree of dispersion and orientation of MWCNTs in the epoxy resin matrix, the aspect ratio of the MWCNTs and the efficiency of stress transfer at the interface between MWCNTs and epoxy resin polymer chains. The mechanisms for the latter are not well understood, but include chemical bonding, van der Waal attractive forces and mechanical interlocking across the length scales. Specifically with regard to MWCNT reinforcement of epoxy resin, other factors such as the effect of MWCNTs on the crosslink density, cure kinetics, and glass transition process are important factors. Additionally, chemical reaction between reactive thermoset precursors and MWCNTs can provide a route for the formation of a 3D network to transfer the effective stress [9].The influence of fluorinated and amine functionalised CNTs on the glass transition temperature (Tg) of different epoxy resin systems are investigated using dynamic mechanical analysis [10, 11]. They reported that the effect of amine functionalised is greater than nonfunctionalised CNT with the increase of Tg and CNT weight filler ratio to 0.8%. This is possible due to consequence of the improved interfacial interactions between nanotube and polymer. The basic properties of CNTs filled epoxy resin nanocomposites for several other technologies have also been examined, including magnetic susceptibility and thermal conductivity [12]. Many properties of CNTs filled epoxy resin nanocomposites can be enhanced by alignment of CNTs during processing. It is very clear that the addition of CNTs filler to epoxy resins alters the cure kinetics of the reaction, and thus physical properties of the epoxy resin, surprisingly few studies on the subject have been published. The thermal mechanical and Raman spectroscopy analysis showed that SWCNTs can act as a strong catalyst for a relatively high weight ratio of filler (>5 wt %) in epoxy resin [13-15]. Graphene is also considered two dimensional carbon nanofiller with a one-atom-thick planar sheet of sp2 bonded carbon atoms that are densely packed in a honeycomb crystal lattice. It is regarded as the thinnest nanomaterial in the universe with tremendous potential [16]. However, graphene is obserbed to have excellent properties, such as high thermal conductivity, superior mechanical properties and high electrical/electronic transport properties [17]. These intrinsic properties of graphene have rendered enormous interest for its possible implementation in a various applications.In this study MWCNTs and GnPs nano fillers were dispersed in epoxy resin using three mill rolling process. The dynamic mechanical and nanohardness properties of the (3 wt %) nanocomposites were measured and results were described with the evidence of nanofillers dispersion status in the epoxy resin by SEM analysis.
2. Experimental
2.1. Materials and Specimen
Araldite (LY-556) 55%, hardener (HY-917) 49% and accelerator (DY-070) 0.28% were used as epoxy resin matrix obtained from Ciba Gaigy Ltd., Mumbai, India. MWCNTs and Graphene nanoplatelets (GnPs) were used as nanofillers. They were obtained from J.K. Impex Company, Mumbai with 99.5% purities. The properties are listed in Table-1.Table 1. Material properties [18] 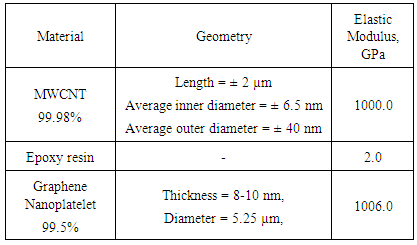 |
| |
|
Firstly, 3 wt % of MWCNT and 3 wt% GnPs nanofillers were manually mixed with the resin (LY-556) separetly. Then batchwise nano filled resins were dispersed using a lab-scale three-roll-mill (EXAKT 120 Advanced Technology GmbH, Germany) process. This process was controlled the introduction of very high shear rate (up to 200,000 s-1) throughout the suspension. The schematic diagram of three mill rolling process is shown in Fig. 1. The pre-dispersed suspension was then given batch wise onto the roll with dwell times of 2 minutes. The dispersive forces on the suspension were acting in the gap (5µm) between the rolls. After dispersion of the MWCNT in resin and GnPs in the resin, the hardener (HY-917) in the weight ratio of 10:1 and accelerator were added in a vacuum dissolver in the mixture of MWCNT/resin and GnPs/resin, in order to avoid trapped air in the suspension. Then the mixtures were placed in a vacuum chamber for 30 minutes to eliminate the bubbles introduced during the rolling process. 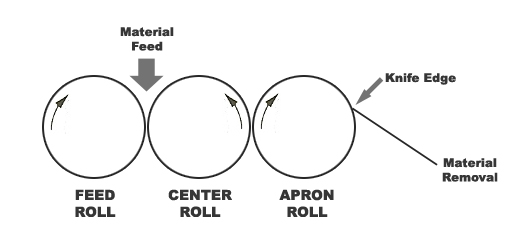 | Figure 1. Schematic diagram of three roll mill process |
After curing, MWCNT/epoxy resin and GnPs/epoxy resin composite specimens were prepared as per the ASTM standards for the measurement of dynamic mechanical and nanohardness properties.
2.2. Dynamic Mechanical Analysis (DMA)
The dynamic mechanical analysis (DMTA-2980, USA) instrument was used to measure the viscoelastic behaviour of nanocomposites, which is shown in Fig. 2. The specimen was tested from room temperature, 25 to 250°C. The heating ramp rate was 5°C and the frequency was 1 kHz. The sample was fixed under double cantilever beam. The data collected was then analyzed to determine the elastic modulus, glass transition temperature (Tg), and trends within the data. 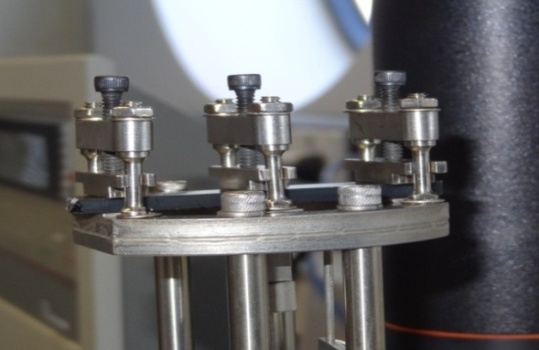 | Figure 2. Sample supported under double cantilever beam test during DMA test |
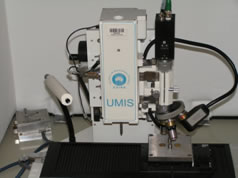 | Figure 3. Ultra-micro Indentation System |
2.3. Nanohardness Analysis
Ultra Micro Indentation System (Fig.3) was used for the measurement of Nanohardness in conjunction with the attached Atomic Force. Microscope was used to examine indents for changes in profile and hardness. The depth range was 2 to 20 micron and dept of resolution was 0.003 nm. The minimum load 2 mN was applied with the load resolution 0.002 mN.
3. Results and Discussion
3.1. Viscoelastic Behaviour
The dynamic mechanical analysis (DMA) of MWCNT/epoxy resin and GnPs/epoxy resin composites provides important insight into the intimate confirmation of the polymer chains in the sample, as well as the interactions of these chains with MWCNT and GnP components in the composite system [5]. The DMA measurements of MWCNT/epoxy resin and GnP/epoxy resin composites allow the evaluation of the temperature dependence of the dynamic modulus and give direct information on various other characteristic structural parameters such as dynamic viscoelastic behavior, glass transition temperature (Tg), storage modulus and loss modulus, and tanδ, as can be identified from Figs. 4-9. The results of these measurements for all type of specimens were compared to evaluate the effect of a magnetic field on the MWCNT/epoxy resin GnP/epoxy resin composites.It can be seen that the storage modulus decreased with the increase of temperature, whereas loss modulus increased with increase of temperature as shown in Figs. 4,5. At low temperatures all the samples show a very high value of the storage elastic modulus, followed by gradual drops due to second order transactions between 40°C 110°C. The principal drop, due to the glass transaction, is evident for all samples of MWCNT/epoxy and GnP/epoxy resin composites in the range 130°C to 140°C. But, tanδ curves show a peak value at 150°C to 160°C of temperature range. This is indication of glass transaction temperature, as shown in Figs. 6-9. This reveals that the addition of nanofiller improves the elastic properties of the epoxy resin system at elevated temperatures in the rubbery region. The behavior can be explained in terms of an interaction between the nanofillers of MWNTs, GnPs and the epoxy due to the presence of enormous surface area [10].The results clearly indicate that the storage modulus, loss modulus and tan δ are function of temperature, as shown in Figs. 6-9. The increase of tan δ with temperature confirms that tan δ is associated with magnetic field strength. The 3% MWCNT/epoxy resin and 3% GnP/epoxy resin composites show a gradual decrease in the tanδ peak height with increasing magnetic field and an increase in peak location as shown in Figs. 8,9. Since tanδ is a measure of the relative energy distribution in the composite specimen, i.e. it is the ratio between the dissipated energy and the elastic energy of the system, its values decrease due to the more pronounced increase of the storage modulus as compared to that of the loss modulus as a function of the magnetic field strength. The storage modulus, loss modulus and tanδ are inter-related with each others.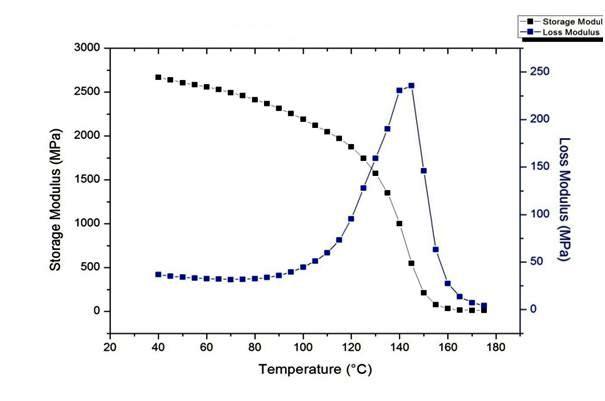 | Figure 4. Variation of storage modulus and loss modulus with temperature in 3wt% MWCNTs/epoxy resin composite |
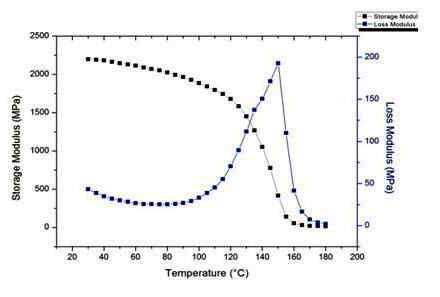 | Figure 5. Variation of storage modulus and loss modulus with temperature in 3wt% GnPs/epoxy resin composite |
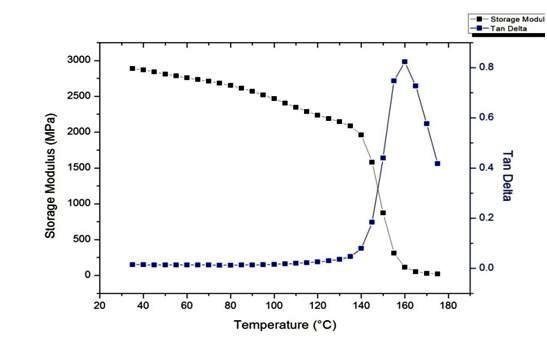 | Figure 6. Variation of storage modulus and tanδ with temperature in 3wt% MWCNTs/epoxy resin composite |
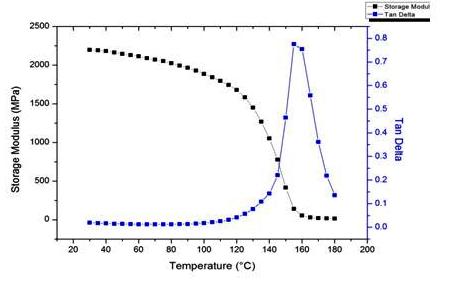 | Figure 7. Variation of storage modulus and tanδ with temperature in 3wt% GnPs/epoxy resin composite |
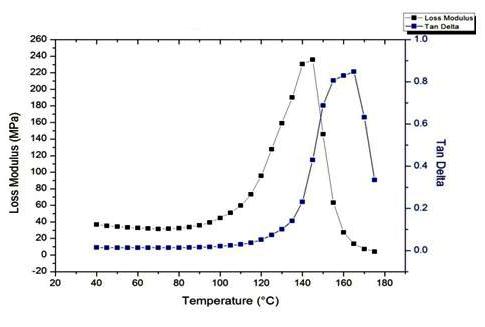 | Figure 8. Variation of loss modulus and tanδ with temperature in 3wt% MWCNTs/epoxy resin composite |
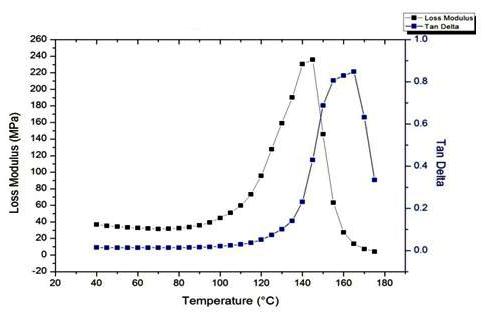 | Figure 9. Variation of loss modulus and tanδ with temperature in 3wt% GnPs/epoxy resin composite |
Basically, storage modulus (G’) is a measurement of the elastic energy stored within the specimen during deformation whereas the loss modulus (G”) is the energy that is the measurement of dampening or dissipation of energy during the deformation of the specimen. From these two different modules, the elastic modulus or complex modulus may be calculated [6], | (1) |
Where σ represents the stress, € represents the strain, G* is elastic modulus. The ratio of the loss modulus to the storage modulus is tan δ.Fig. 10 clearly indicates the viscoelstic behaviour of MWCNT/epoxy resin and GnPs/epoxy resin composites under the DMA test. The results show that the elastic modulus decreases with increase of temperature. The elastic modulus of GnPs/epoxy resin is lower than the MWCNTs/epoxy resin composite because MWCNTs particles are sustained the heat due to tubelar shape.
3.2. Nanohardness
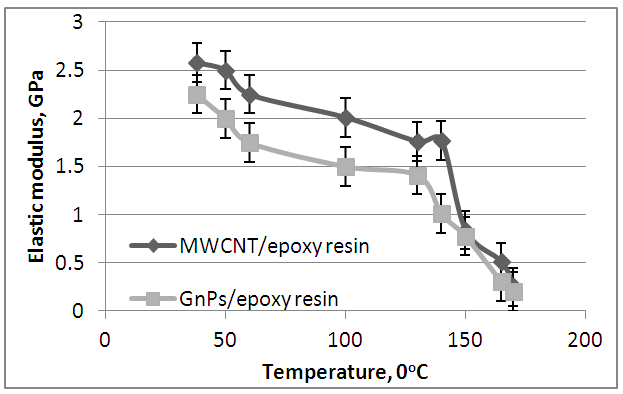 | Figure 10. Variation of elastic modulus with temperature of MWCNTs /epoxy resin and GnPs/epoxy resin composites |
The influence of scratch load on mechanical response of MWCNT/epoxy resin and GnP/epoxy resin composites was investigated by nanoindentation test.The results indiacte that the variation of elastic modulus and nanohardness obtained as a function of the indentation test load for all directions shows that the elastic modulus and nanohardness increases with increasing depth (i.e., increasing applied indentation load), then reaches a saturation value at a higher indentation depth. The average values of nanohardness and elastic modulus were plotted and indicate that the nanohardness dependent on the elastic modulus of MWCNT/epoxy resin and GnP/epoxy resin composites as shown in Fig. 11. 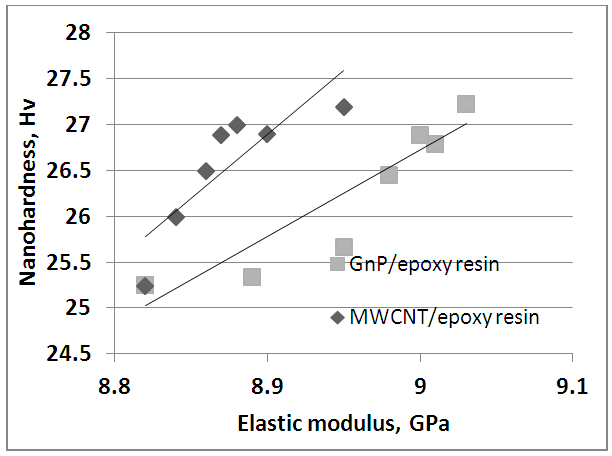 | Figure 11. Variation of nanohardness with elastic modulus of MWCNTs/epoxy resin and GnPs/epoxy resin composites |
It is clear that nanohardness of MWCNTs/epoxy resin composite gives higher value than the GnPs/epoxy resin composite. However, elastic modulus of GnPs/epoxy resin appears higher value than MWCNTs/epoxy resin composite due to increase of surface area and toughness of epoxy resin. The GnPs nano particles are arranged in the platelets form, which increase the resistance of stress. The most important micro-mechanical mechanism leading to an increase in fracture toughness are due to localized inelastic matrix deformation and void nucleation, debonding and deformations of particles [16]. In general, the plastic zone size of brittle epoxy resin is relatively small compared to nanofilled epoxy resin. When a resin is filled with nano-particles, a significant amount of particles occur in the plastic zone, while in a composite with micro-particles, only a minor number of them are involved in the plastic zone deformation process [5].
3.3. Morphological Behaviour
The fracture surface of MWCNT/epoxy resin composite is much rougher and their crack becomes more random as indicated in Fig. 12 (a & b). This is probably due to the crack expansion is blocked by the MWCNTs network. Furthermore, the MWCNTs with high specific surface area having a firm connection show strong interaction with matrix as shown in Fig. 12 (a). So, the carbon nanotubes effectively, prevent the expansion of micro cracks resulted from the stress concentration as indicated in Fig. 12(b). Therefore, MWCNTs filler improve the viscoelastic and nanohardness properties of epoxy resin composites greatly [9].On the other hand, when the content of MWCNTs is over certain amount, the carbon nanotubes aggregate more seriously, and the MWCNTs dispersion becomes inhomogeneous in the matrix as observed in Fig. 12(b) of 3% wt MWCNT/epoxy resin composite. The network structure of MWCNTs probably decreased and the MWCNTs intertwine together to form a cluster in micro size as shown in the Figs. 12 (a&b). This may be lead to dissipate the energy under viscoelastic deformation of MWCNTs in epoxy resin [11].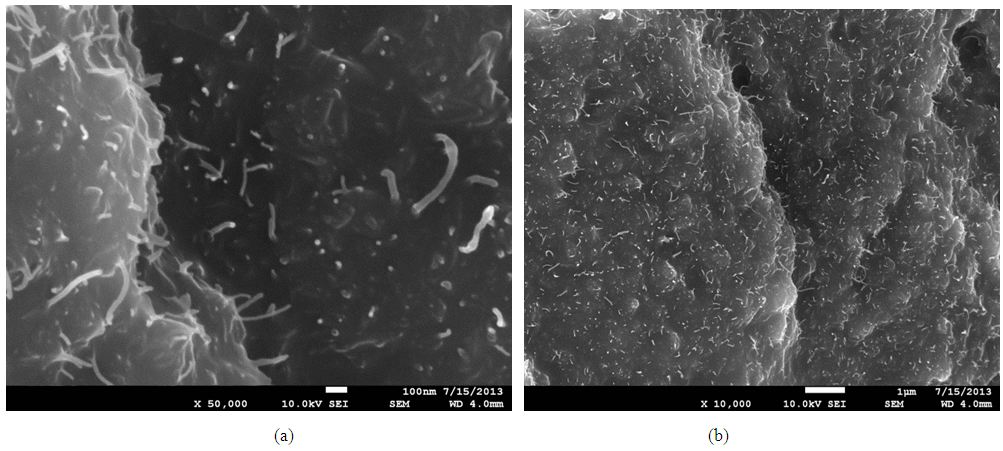 | Figure 12. SEM micrograph showing (a) dispersion of MWCNTs filler and (b) cracks formed in the resin reach area |
The presence of graphene nanoplatelet confirms the strong interaction with the epoxy resin, which significantly improves the adhesion at interfaces. In general, nanoplatelet can be easily attracted to each other due to their very high specific area and high surface energy [17], due to these properties, nanohardness of GnPs/epoxy resin composite give more value compare to MWCNT/epoxy resin composite [18]. Fig. 13 (a) indicates that the GnP nanofiller agglomerated and resist the formation of crack growth. The images indicate that the GnPs nanofillers are appeared in the thin sheet form, as shown in Fig. 13(b). The aggregation of GnPs to form nanobundles, because of Van der Waal forces [1]. This leads the higher value of hardness compare to MWCNT/epoxy resin composite due to increase in interface bond strength of composite made with graphene nanoplatelet [8].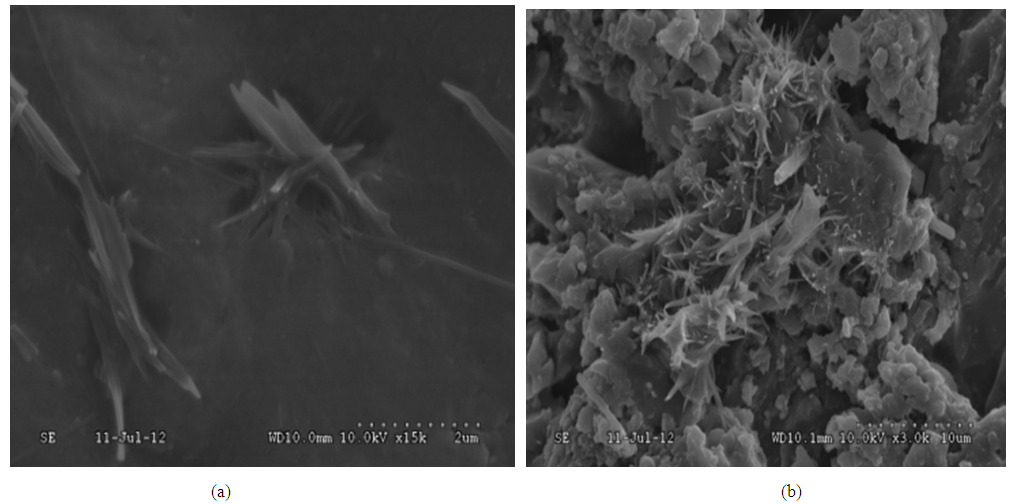 | Figure 13. SEM micrograph showing (a) agglomeration of GnPs filler and (b) graphene nanoplatelet resist the crack path formed in the resin reach area |
4. Conclusions
Based on the experimental work carried out in this study, the following conclusions cab drawn.i. DMA results indicated that the storage modulus decreased with the increase of temperature, whereas loss modulus increased with increase of temperature. The decrease of storage modulus can be interpreted by an increasing susceptibility of agglomeration, leading to less energy dissipating in the system under viscoelastic deformation. This reveals that the elastic modulus of MWCNTs/epoxy resin and GnPs/epoxy resin composites decreased rapidly with increase of temperature. ii. The viscoelastic behaviour of MWCNTs/epoxy resin composite is better than the GnPs/epoxy resin composite due to more dissipation of heat energy from the tubes.iii. The nanohardness increases with increase of elastic modulus marginally. Whereas, GnPs/epoxy resin gives higher value than the MWCNTs/epoxy resin composite, which contribute better interfacial properties of GnPs filler than the MWCNTs filler. iv. Elastic modulus of nanofillers filled epoxy resin composites dependent on the glass transaction temperature and depth of nanoindentation.
ACKNOWLEDGEMENTS
The authors would like to thank Department of Mechanical Engineering, Indian Institute of Technology (BHU), Varanasi-221005, India for their supports.
References
[1] | Ajayan P.M., Schadler L.S., Giannaris C., Rubio A . 2000. The Effect of van der Waals-Based Interface Cohesive Law on Carbon Nanotube-Reinforced Composite Materials. Advanced Mater 12(10):750-753. |
[2] | Allaoui A., Bai S., Cheng H.M., Bai J.B. 2002. Mechanical and Electrical Properties of MWCNT/Epoxy Composites. Compos Sci Technol 62: 1993-1998. |
[3] | Ci L., Bai J. 2006. The Reinforcement Role of Carbon Nanotubes in Epoxy Composites with Different Matrix Stiffness. Compos Sci Technol 66: 599-603. |
[4] | Dehghan M., Al-Mahaidi R., Sbarski I. 2014. Thermo Mechanical Characterization of MWCNTs-Modified Epoxy Resin. Inter J Chem, Molec, Nuclea, Mater Metal Engn 8(2) 119-123. |
[5] | Guadagno L. 2011. Effect of Functionalization on the Thermo Mechanical and Electrical Behaviour of Multi-wall Carbon Nanotube/Epoxy Composites. Carbon 49(6):1919-1930. |
[6] | Gojny F.H., Wichmann M.H.G., Fiedler B., Schulte K. 2005. Influence of Different Carbon Nanotubes on the Mechanical Properties of Epoxy Matrix Composites- A comparative study. Compos Sci Technol 65:2300-2313. |
[7] | Ivanov E. 2011. Effects of Processing Conditions on Rheological, Thermal, and Electrical Properties of Multiwall Carbon Nanotube/Epoxy Resin Composites. J Polymer Sci PartB -Polymer Phys 49(6): 431-442. |
[8] | Li J., Kim J.K. 2007. Percolation Threshold of Conducting Polymer Composites Containing 3D Randomly Distributed Graphite Nanoplatelets. Compos Sci Technol 67: 2114-2120. |
[9] | Li W., Buschhorn S.T., Schulte K., Bauhofer W. 2011. The Imaging Mechanism, Imaging Depth, and Parameters Influencing the Visibility of Carbon Nanotubes in a Polymer Matrix Using an SEM. Carbon 49: 1955-1964. |
[10] | Montazeri A., Javadpour J., Khavandi A., Tcharkhtchi A., Mohajeri A. 2010. Mechanical Properties of Multi Walled Carbon Nanotubes/Epoxy Composites. Mater Design 31: 4202-4208. |
[11] | Montazeri A., Khavandi A., Javadpour J., Tcharkhtchi A. 2010. Viscoelastic Properties of MWNT/Epoxy Composites Using Two Different Using Cycles. Mater Design 31: 3383-3388. |
[12] | Peigney A., Laurent C.H., Flahaut E., Bacsa R.R., Rousset A. 2001. Specific Surface Area of Carbon Nanotubes and Bundles of Carbon Nanotubes. Carbon 39: 507–514. |
[13] | Srivastava V.K. 2012. Modeling and Mechanical Performance of Carbon Nanotube/Epoxy Resin Composites. Mater Design 39:432-436. |
[14] | Wong K.J., Yousif B.F., Low K.O., Ng Y., Tan S.L. 2009. Effects of Fillers on the Fracture Behvaiour of Aprticulate Polyester Composites. J Strain Analysis 45:67-79. |
[15] | Yang B.X., Shi J.H., Parmoda K.P., Goh S.H. 2008. Enhancement of the Mechanical Properties of Polypropylene Using Polypropylene Grafted Multi Walled Carbon Nanotubes. Compos Sci Technol 68: 1068-1114. |
[16] | Yu A., Ramesh P., Itkis M.E., Bekyarova E., Haddon R..C. 2007. Graphite Nanoplatelet-Epoxy Composite Thermal Interface Materials. J of Phys Chemis 111:7565–7569. |
[17] | Zaman I., Phan T.T., Kuan H.C., Meng Q., La L.T.C., Luong L., Youssf O., Ma J. 2011. Epoxy/Graphene Platelets Nanocomposites with Two Levels of Interface Strength. Polymer 52 (7): 1603-1611. |
[18] | Singh S., Srivastava V.K., and Prakash R. 2015. Influences of Carbon Nanofillers on Mechanical Performance of Epoxy Resin Polymer, Appl Nanosci 5: 305-313. |