Shreeranga Bhat1, Prajwal J.1, Pratheek S.1, Kevin Prajwal Pais1, Sonal Rohan Vaz1, Hrish S. R.2
1Department of Mechanical Engineering, St. Joseph Engineering College, Mangaluru, India
2Department of Mechanical Engineering, Vivekananda College of Engineering & Technology, Puttur, India
Correspondence to: Shreeranga Bhat, Department of Mechanical Engineering, St. Joseph Engineering College, Mangaluru, India.
Email: |  |
Copyright © 2017 Scientific & Academic Publishing. All Rights Reserved.
This work is licensed under the Creative Commons Attribution International License (CC BY).
http://creativecommons.org/licenses/by/4.0/

Abstract
In general, this project intends to pinpoint the various problems faced by the plywood industry and to determine optimal solutions to improve its overall performance. The project has the following objectives: to increase productivity by implementing Lean strategy; to eliminate the wastage and non-value added activities; to create an intelligible working environment; and to educate janitorial level people about the benefits of using Lean strategy. The research reported in this project is based on a case study carried out in an industry using Lean PDCA (Plan-Do-Check-Act) approach, 5S tool, and its applications in increasing production. The reason for decreased productivity in the plywood industry was identified and examined at different stages of the project. Wastage and non-value added activities affecting the production process were eliminated by implementing Lean strategy. The project led to the development of an easy and simple working environment. As a result of this, productivity increased by 7.33%, which would be a confounding achievement for the plywood industry.
Keywords:
Lean, 5S, Plywood Industry
Cite this paper: Shreeranga Bhat, Prajwal J., Pratheek S., Kevin Prajwal Pais, Sonal Rohan Vaz, Hrish S. R., A Study on Implementation of Lean Methodology in the Plywood Industry, Management, Vol. 7 No. 5, 2017, pp. 174-179. doi: 10.5923/j.mm.20170705.03.
1. Introduction
1.1. Lean Manufacturing
It is a systematic approach to identifying and eliminating non-value added activities through continuous improvement by flowing the product at the pull of the customer in pursuit of perfection. Over the past two decades, Lean manufacturing has been the business strategy, which guarantees competitiveness and eco- friendliness by concentrating on eliminating waste. Since the resources and energy are finite, new sustainable ways of producing more with less ought to be established. By implementing lean principles, the industry can be made flexible to change their strategies to meet customer expectations by reducing the price and not compromising on the quality of the product [1, 2]. Lean Manufacturing can be thought of as a systematic approach to reducing waste in the production process. Waste can be defined as anything (activities, processes, tools, materials, and personnel) that does not add value to the product or service as viewed by the customer [3]. In the 1940s, Taiichi Ohno and Shigeo Shingo improved upon previous manufacturing techniques, the principles and practices of which eventually also was known as Just-in-Time (JIT) manufacturing [4]. This groundbreaking thinking catapulted Toyota into the global spotlight, and its processes became premier industry practices that everyone aspired to emulate.In a true Lean environment, inventory levels are reduced, hidden problems revealed, and solutions are developed in a way that supports team concepts, participation, new ideas, and a common aim: satisfying the customer. This approach and the results it produces is one of the great differences between Henry Ford's breakthrough processes and Toyota's. Ford was very good at producing one specific type of automobile without variation. Toyota's processes, on the other hand, allowed quick changes that resulted in the delivery of what the customer specifically needed. Lean Manufacturing inspired new ways to eliminate waste.
1.2. About Plywood
It is a sheet material manufactured from thin layers or "plies" of wood veener that are glued together with adjacent layers having their wood grain rotated up to 90 degrees to one another. There are usually an odd number of plies, so that the sheet is balanced and reduces warping. Since plywood is bonded with grains running against one another and with odd number of composite parts, it is very hard to bend it perpendicular to the grain direction of the surface ply. Smaller thinner plywood and lower quality plywood (see average quality plywood photo below and right) may only have their plies (layers) arranged at right angles to each other, though some better quality plywood products will by design have five plies in steps of 45 degrees (0, 45, 90, 135, and 180 degrees), giving strength in multiple axis. A typical plywood panel has face veneers of a higher grade than the core veneers.The principal function of the core layers is to increase the separation between the outer layers where the bending stresses are highest, thus increasing the panel's resistance to bending. As a result, thicker panels can span greater distances under the same loads. In bending, the maximum stress occurs in the outermost layers, one in tension and the other in compression. Bending stress decreases from maximum at the face layers to nearly zero at the central layer. Shear stress, by contrast, is higher in the centre of the panel and at the outer fibres.
2. Literature Review
2.1. The History of Lean Flow
Lean production approach was pioneered by Toyota, which highlighted Japanese production methods compared with traditional Western mass production systems; it also highlighted the superior performance of the former [5]. The follow-on book, Lean Thinking: Banish Waste and Create Wealth in your Organization (Womack and Jones, 1996), is equally a key step in the history of lean as it summarizes the lean principles, which ‘guide action’. It also coined the phrase ‘Lean Production’. The Toyota Production System was based on continuous flow, which did not depend on long production runs; it was based on the recognition that only a small fraction of the total time and effort to process a product added value to the end customer. Key tools and techniques within the ‘lean’ system included: Kanban- a visual signal to support flow by ‘pulling’ product through the manufacturing process as required by the customer; 5S’s / 5S - a visual housekeeping technique, which devolved control to the shopfloor; Visual control - a method of measuring performance at / on the ‘shop floor’, which was visual and owned by the operator team; Poke-yoke - an ‘error-proofing’ technique; and SMED (single minute exchange of dies) - a changeover reduction technique [6].
2.2. Seven Wastes of Lean Manufacturing
1. Overproduction: Overproduction or storing of extra products is caused due to the mindset of “just in case”, which wastes storage space and production time and energy. If the customer decides later to cancel the order, or there are ordering delays and the product spoils before delivery, it results in wastage [7]. 2. Inventory: This is the other side of the "overproduction" coin. If you order extra raw materials so they are available "just in case", that is also wasteful. The order specs may change, food products may get wasted, or again, the customer may not want the product anymore. 3. Defects: Defects and broken products can lead to customer dissatisfaction, and you spend extra time and money solving the problem, reworking the items, or paying for the customer to dispose of the waste. Shipping damage is also considered a defect.4. Processing: More energy is required to produce their items this could be a result of extra/unnecessary manufacturing steps, using outdated techniques, or not having standard work plans. 5. Motion: Unnecessary motion can happen as a result of an inefficient process, a lack of standardized procedures, or even a lack of training for employees. Wasted motion is a hidden cost because it is not something easily seen, but only through careful observation and communicating with the workers. 6. Transport and Handling: These wastes occur when pallets are not being properly stretch wrapped (wasted material), or a truck is not loaded to use floor space efficiently. Even in handling, it can be something as simple as forklift drivers who need to climb off and on the forklifts to set up or fix a stretch wrapping machine or using a pallet jack to hand deliver pallets to the stretch wrapping machine – all of which are wasted motion.7. Waiting: These are bottlenecks in time, usually due to broken machinery, lack of trained staff, shortage of materials, inefficient planning, or as a result of the six other mudas. At their worst, they can lead to slowed production, delayed shipments, and even missed deadlines. At the very least, this is the time that is paid for but unproductive; you are paying people to sit and wait [7].
2.3. Aim and Objectives
AIMThe aim of this work is to see the application of lean manufacturing in the plywood industry to reduce wastes, and hence, improve the quality and productivity.OBJECTIVESThe objectives of this study are -• To reduce the randomness of work flow, which has an adverse effect on the system performance; and• To enhance the overall productivity of the industry through Lean manufacturing principles.
3. Methodology
In the current study, the Lean tool, PDCA is used to solve the problem. The PDCA cycle or the Deming wheel consists of four phases, viz., Plan, Do, Check, and Act.• PLAN: In the Plan phase, fish bone diagram and Why-Why analysis are utilized to identify the problem.• DO: In the Do phase, the concepts of 5S and layout changes are examined.• CHECK: In the Check phase, the changes are evaluated.• ACT: In the Act phase, the changes are studied thoroughly and implementation of the same is solicited.
4. Case Study
4.1. About the Industry
The plywood industry is one of the prominent manufacturers and suppliers of face veeners and different types of plywood. These companies have been able to satisfy their customers by providing high quality products as per their demand and specification. Currently, they are supplying their products to the states of Karnataka, Kerala, Andhra Pradesh, Tamil Nadu, Maharashtra, and Goa. These companies have attained a respected and reliable position in the domestic market by focusing on fabrication and quality range of various products. They run eight hours a day depending on the demand rate. Their relentless efforts have ensured exponential growth for the companies during the last 4 years.
4.2. Process Flow
1. Preparation of resinResin is initially prepared for binding of the ply. The resin used here is MUF. The raw materials for the preparation of resin are melanin, urea, and phenol. Around 900kg of resin is prepared every week and stored. About 150kgs of resin is used per day.2. Drying of coreThe core is placed in an open space for about a week. The exposure of the core material to sunlight reduces its moisture content. It is then sent to the dryer or the drying machine for further reduction of its moisture content.3. Face veener preparation The face veener is imported from Burma in bundles of 500 and separated manually as per the daily requirements.4. Core Cutting The de-moisturized core from the dryer is cut into regular shapes using manually operated machines.5. Assembling of plywood The plywood material is assembled prior to hydraulic pressing operation. The core is placed between the face such that the alternative layers of core are parallel to each other. The number or layers of core depends on the thickness of the plywood required.6. Hydraulic Press After the assembled plywood is passed onto the hydraulic press, it is pressed for a certain duration depending upon the thickness of the plywood and temperature maintained.7. Cutting Operation After the pressing operation, the plywood is allowed to cool. It is then passed through the cutting machine to be cut as per the required dimension.8. Sanding Operation Once the cutting operation is completed, both the faces of the plywood is polished using the belt sander.9. Termite Protective Layer Since plywood is prone to termite attack, it is immersed in a chemical liquid and allowed to dry.10. Manual Sanding This is the final step in the manufacturing of the plywood. Here, the finishing of plywood is done manually using sanding scrubs and it is stored. The manufactured plywood is tested for any defected by listening to the sound when it is hammered, and the visual appearance of the plywood is also considered. It is then stacked up and exported.
5. Results and Discussions
5.1. Plan
The areas which required improvement was identified through analysis, which consisted of brainstorming and observation of the problem. The fish bone diagram was created to show the causes of low productivity (Figure 1).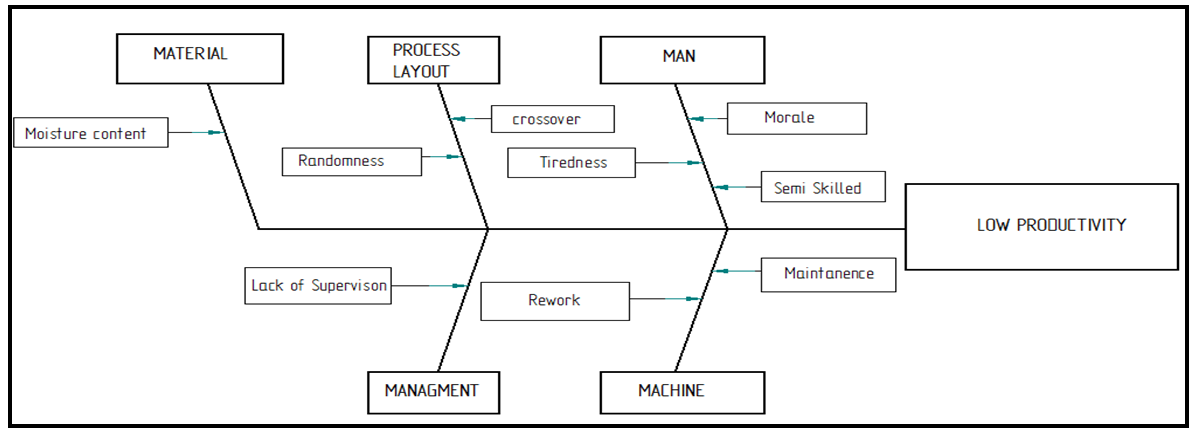 | Figure 1. Fish Bone Diagram |
5.2. Do
The second step in the problem solving process is Do, wherein the layout (Figure 2) and value stream mapping (Figure 3) of the current scenario of the plant is prepared. The first S that is Sort is applied throughout the entire layout. Using this, items that are needed and the items to be relocated and discarded are identified. Then, taking all these aspects in to consideration, a new layout is developed. The changes observed with the incorporation of the revised layout are - • Crossover associated with core veener gets reduced; and• There is increase in productivityThe new layout was also developed in such a way that more floor area was available to do value- added work. The new layout also brought down the inventory of the floor area considerably. 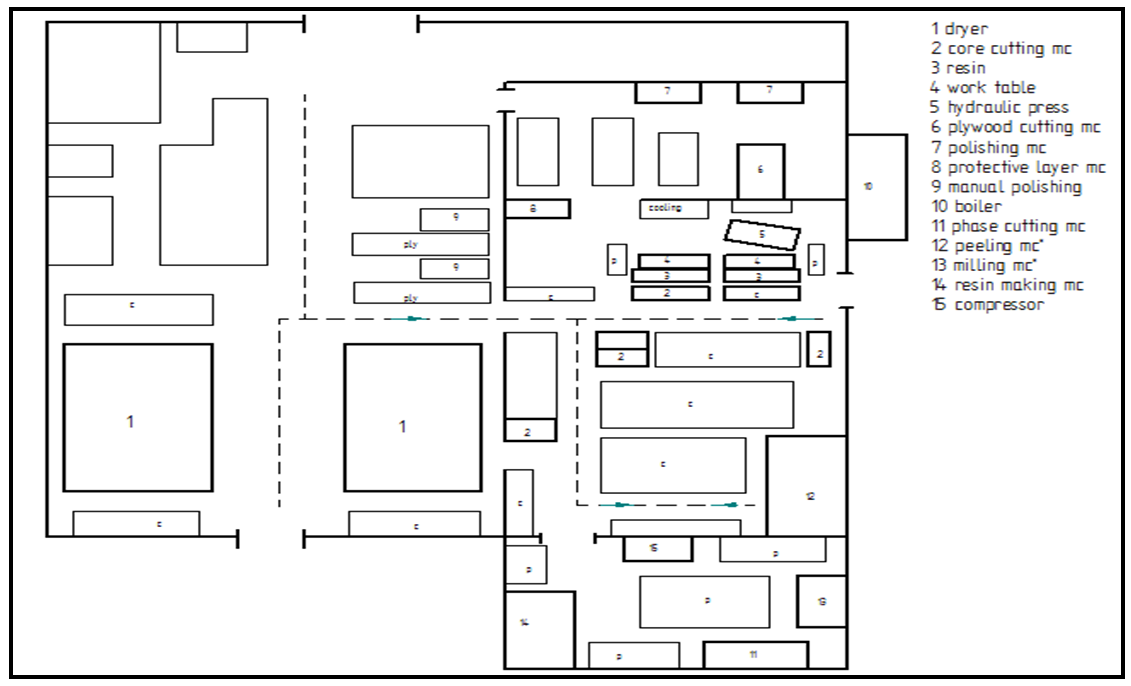 | Figure 2. Actual Layout |
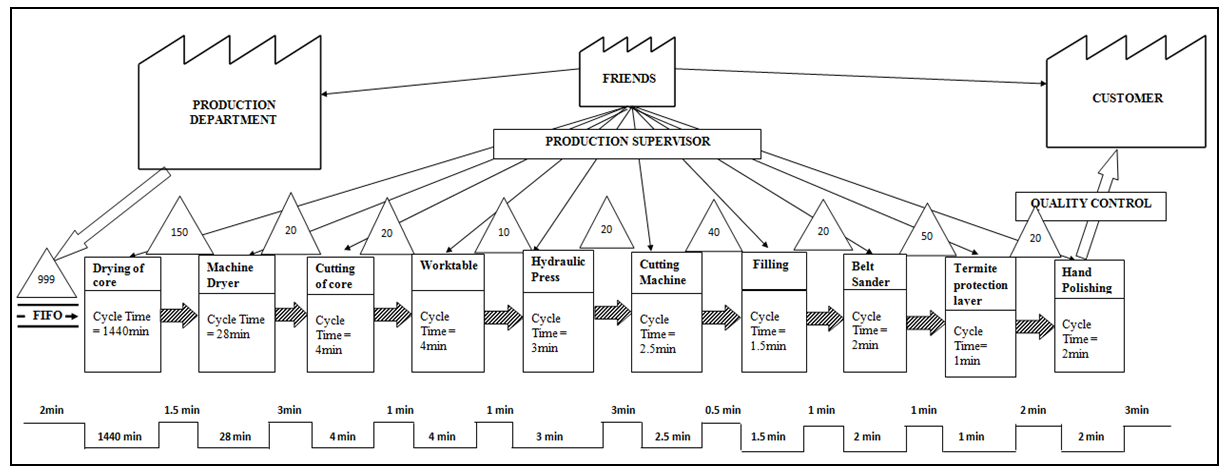 | Figure 3. Actual Value Stream Mapping |
5.3. Check
Value stream mapping (VSM) is an enterprise improvement tool, which assists in visualizing the entire production process, and represents both material and information flow. The goal is to identify all types of waste in the value stream and to take steps to eliminate them (Rother and Shook, 1999). Taking the value stream viewpoint means working on the big picture and not individual processes, and improving the whole flow and not just optimizing the pieces. It creates a common language for the production process, thus facilitating more thoughtful decisions to improve the value stream [8].In the Check phase, we validate the changes made in the plan phase. The problems in the industry were found to be mainly because of improper planning of the plant layout. Considering variables like entity per arrival, number of staff, work schedule, process time, and non-value added activity time, a Proposed Layout (Figure 4) and Value Stream Map (VSM) (Figure 5) was created. Certain factors could not have considered due to factory restrictions. Keeping this in mind, cause and effect diagram, the VSM for the proposed layout, was engendered. By collaborating with experts in the field, calculations were done resulting in overall increased productivity of the industry. 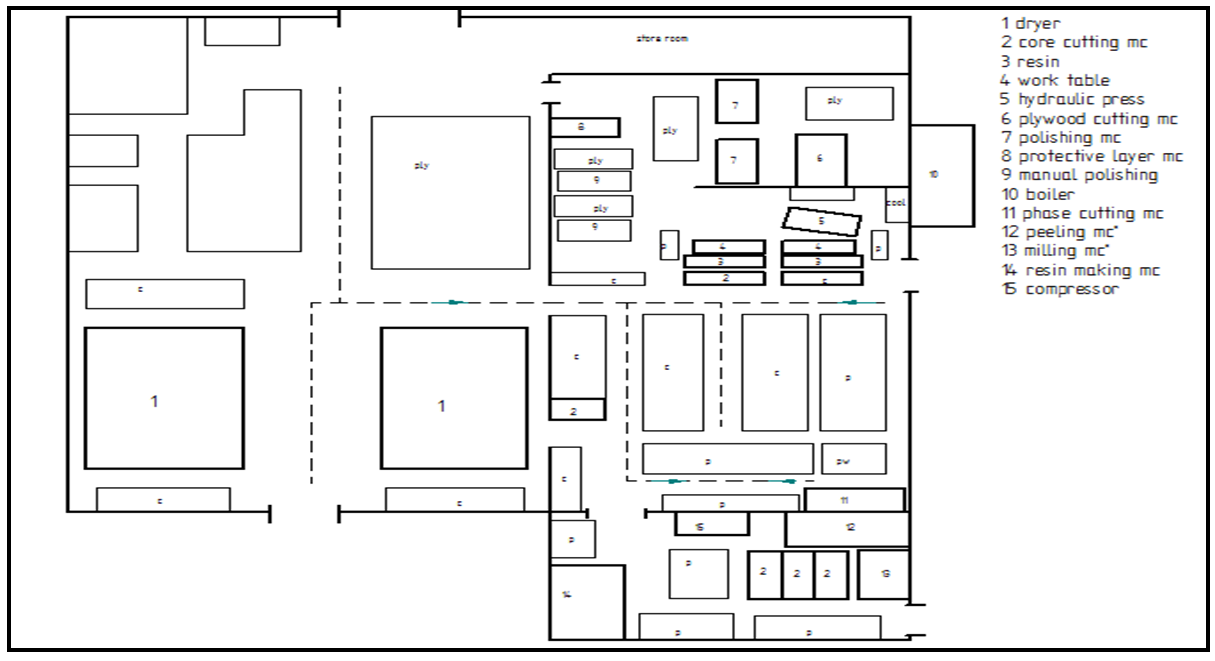 | Figure 4. Proposed Layout |
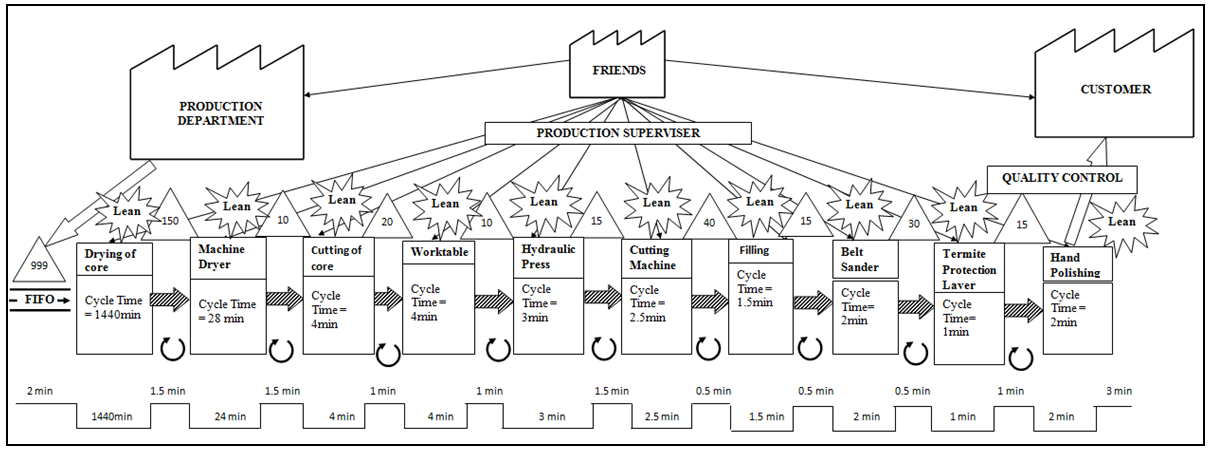 | Figure 5. Final Value Stream Mapping |
Calculation Average number of plywood produced per day=150 ply/ dayNo. of working hours per day=8 hours8 hours= 480 minutesQuantity of plywood produced per minute = 150/480 =0.3125 plyTime saved due to layout modification per hour = 4.21 minutesTime saved per day = 4.21*8=35 minutesTherefore, increase in productivity=0.3125*35=10.94 ply/dayThus, percentage increase in productivity = (100*11)/150= 7.33%
5.4. Act
The changes made in the factory were recommended to be implemented on a permanent basis. The procedures for standardization of the changes are being developed. This phase also involves creating awareness among factory workers and all concerned people about 5S, proper cleanliness, and simple Lean techniques developed.
6. Conclusions
• The application is very simple and can be implemented economically, as it does not require the involvement of highly skilled people. A simple training of the existing workforce is needed.• The 5S, which is a Lean tool, is an effective technique, which serves as a doorway to continued improvement. The five steps provide an immediate improvement by creating a visual workplace. This technique does not follow a single approach, but a multidimensional use of the productivity improvement techniques.• Lean manufacturing mainly involves awareness and involvement leading to a highly productive work environment.
References
[1] | Singh B. and Sharma S.K., Lean Can Be a Survival Strategy during Recessionary Times, International Journal of Productivity and Performance Management, 58(8) 2009, 803-808. |
[2] | Modi D.B. and Thakkar H., Lean Thinking: Reduction of Waste, Lead Time, Cost Through Lean Manufacturing Tools and Technique, International Journal of Emerging Technology and Advanced Engineering, 4(3) 2014, 339-344. |
[3] | Murugananthan V.R., Govindaraj K., and Sakthimurugan D., Process Planning Through Value Stream Mapping in Foundry, International Journal of Innovative Research in Science, Engineering and Technology, 3(3) 2014, 1140-1141. |
[4] | Ghosh M.A., Lean Manufacturing Performance in Indian Manufacturing Plants, Journal of Manufacturing Technology Management, 24(1) 2013, 113-122. |
[5] | Melton T., The Benefits of Lean Manufacturing What Lean Thinking Has to Offer the Process Industries, Chemical Engineering Research and Design Institution of Chemical Engineers, 2005, 662–673. |
[6] | Yash D., and Sohani N., Single Minute Exchange of Dies: Literature Review, International Journal of Lean Thinking, 3(2) 2012, 27-37. |
[7] | Aradhya T.B.U.S., Mehaboobbasha H., Sachin. B.R., Virupakshappa and Vishnu J., Introduction to Lean Manufacturing, International Journal of Engineering Sciences & Management, 2017, pp. 9-12. |
[8] | Gurinder S. and Inderpreet S. A., Just-In-Time Manufacturing: Literature Review and Directions, International Journal of Business Continuity and Risk Management, 3(1) 2012, 57-98. |