Ummu Hani 1, Mursyid Hasan Basri 1, Dwi Winarso 2
1School of Business Management, Bandung Institute of Technology, Bandung, Indonesia
2Padjajaran University, Bandung, Indonesia
Correspondence to: Ummu Hani , School of Business Management, Bandung Institute of Technology, Bandung, Indonesia.
Email: |  |
Copyright © 2012 Scientific & Academic Publishing. All Rights Reserved.
Abstract
In healthcare service sector, inventory management and distribution has important role in determining its success. Besides medicines, most of hospital inventories are medical devices and consumable goods such as syringe, bandage, and etc. This study is aiming to observe inventory management and distribution of medical consumables in public hospital and provide solutions for problems that often happened. The methodology of this paper is a case study at a public hospital in Indonesia as developing country. This study is preliminary research, which is future research is to make the optimal scenario of medical consumables inventory and distribution which is can reduce the cost significantly. The result of this paper is there are four most important factor that must be concerned in managing hospital inventory and distribution of medical consumables, efficient use of resources, collaboration with other departments to give customer service improvement.
Keywords:
Hospital, Inventory, Medical Consumables, Distribution
Cite this paper: Ummu Hani , Mursyid Hasan Basri , Dwi Winarso , Inventory Management of Medical Consumables in Public Hospital: a case study, Management, Vol. 3 No. 2, 2013, pp. 128-133. doi: 10.5923/j.mm.20130302.10.
1. Introduction
Recent researches have shown that the enhancing management of distribution and inventory can generate cost savings and increase potential revenue[1]. Any improvements in hospital supply chain can lead to better inventory management, raise supplier relationship management, enhance patient’s satisfaction and elevate effectiveness of hospital employees work flow[2].The recent trends in efficient distribution has caused many industries, including healthcare industry, to focus more on streamlining their supply chain of medical supplies in an effort to be more competitive while still meeting the requirements of their customers.This research takes medical consumables in hospital represent the medical supplies in which have critical role in hospital activities. The sample is disposable syringe as one type of medical consumables.The objective of this research is to learn deep understanding and observe inventory management and distribution of medical consumables in public hospital. This study is preliminary study which is the future research is to make the optimal scenario of medical consumables which is can reduce cost significantly.
2. Literature Review
Supply chain management in healthcare sector is more complex if compared with other industries. It is because patient needs are must be met accurately, in particular the adequate medical supply[3]. Another literature proposed some factors that assist to this complexity. Factor number one is limitation of physician’s knowledge as decision makers regarding supply chain management technique. Second factor is the regulatory pressures. Regulation is very influence the pharmaceutical industry in doing their activities[4].Supply chain activities in healthcare sector are almost similar with other industries. Those activities involve purchasing, inventory management, information and communication systems (ICT) management, food and home care services, and transportation[2].Barriers in practicing the appropriate supply chain management are ongoing and very widespread although there are many different supply chain management techniques that can be used. Unfortunately, only a very limited literature explore about applications of those techniques in developing world.In traditional type of supply chain, the traditional distribution model, the products are shipped from suppliers to distributors and then packed in distribution’s warehouse. The products in pallets shape are sent to each hospital’s warehouse. Afterwards, the products are broken down into smaller quantities and saved until the hospital needs it[1].There is research finds that logistics divisions execute a lot of inter-related activities. For example, ICT as one important part of logistic activities has strong effect and relationship with inventory management. Outsourcing is widely used strategic option in hospitals logistic activities in order to minimize operation cost[2].New environment of healthcare competition is cost conscious, therefore traditional distribution type of supply chain in healthcare sector must be abandoned in order to remain viable and competitive. Revenue opportunities are gathered from driving costs and enhance efficiency[5].The most common inventory situation faced by public hospital is that stock levels are depleted over time and then are replenished by the arrival of a batch of new units[6]. One basic model to determine the optimal order quantity is Economic Order Quantity model. This model considers the tradeoff between ordering cost and holding cost in choosing the quantity each time order in replenishing item inventories[7]. In short explanation, a larger order quantity reduces ordering frequency and ordering cost, but requires a larger inventory holding, in which that’s enhance holding cost and enhance larger storage.EOQ is simple to understand and use but it has several restrictive assumptions which are also disadvantages in practice. Even with these weaknesses, EOQ is a good place to start to understand inventory systems. EOQ assumes[8]:1. Demand rate is constant, uniform, recurring, and known.2. Lead time is constant and known.3. Price per unit of product is constant; no discounts are given for large orders.4. Inventory holding cost is based on average inventory.5. Ordering or setup costs are constant.6. All demands will be satisfied; no stock-outs are allowed.
3. Methodology
This research is a case study at one public hospital in Indonesia. A qualitative study aims to identify cause of problems in hospital medical consumables inventory management. This paper provides depth analysis through in-depth interviews and field observation.In-depth interview is conducted with several staff from some correlated units. The in-depth interview is semi structured interview in which the question has prepared before. While visiting units to conduct interviews, field observations are also conducted through data gathering and observe the real distribution process.
4. Results
4.1. Current distribution process of medical consumables in public hospital
The current distribution process of medical consumables in this public hospital is distracted and doesn’t run properly, which can be seen at figure 1. Its distribution practice is divided by the customer types. In general, there are three types of customer (patient) in public hospital. The first type is “public health assurance” patient. In this type, patient doesn’t have to pay any bill to hospital because all of the bills are certified by government. The insurance is specified for poor people. The second type is “health insurance” patient. This patient type has insurance which is given by private sector or government’s company. The last type is regular patient in which they have no any insurance.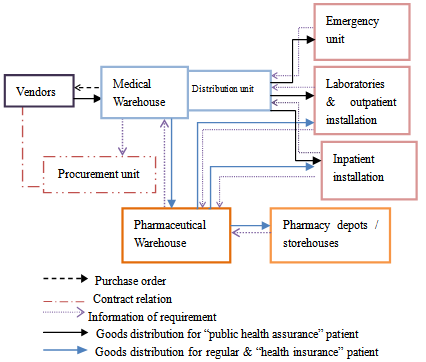 | Figure 1. Current distribution practice of medical consumables |
Although the type and brand of syringe (as a sample of medical consumables) is same for all types of customer, but the distribution is separated. For “public health assurance” (jamkesmas) patients, all medical consumables are distributed from vendors to medical warehouse. Then medical warehouse distributes the goods to the point-of-use (emergency unit, laboratories, outpatient installation, inpatient installation). The goods are distributed in accordance with the demand form through distribution unit. At the end of month, some point-of-uses which have overstock, give back their buffer stock to distribution unit (as a part of medical warehouse).But medical consumables for regular patients and “health insurance” (askes) patients are distributed from medical warehouse to the pharmaceutical warehouse. Then pharmaceutical warehouse be on duty to serve and distribute the goods to all pharmacy storehouses and other point-of-uses in which serve regular patient and “health insurance” patient. The amounts of distributed goods are due to demand based of requirement from storehouses. Information of requirement or demand is directly sent from every point-of-uses. Procurement unit has function to make a contract with vendor every three months. Sharing information is very critical to do between procurement unit and medical warehouse. Every unit has several depots or storehouses. The critical problem is if there any stockout of medical consumables at a storehouse, it can take the medical consumables from other storehouse in which has overstock without put it into monthly report. So, the report of goods inventory turnover is different with the real situation.
4.2. Current inventory policy
Every unit has different inventory review policy. Some of them use periodic review policy; some others use continuous review policy. Data gathering is restricted at medical warehouse which is using periodic review policy. Medical warehouse orders new stock every month to supplier (periodically). The amount of order quantity isn’t based on forecast, but based on last month demand. The lead time of goods distribution from vendor is usually one day. Table 1. Average inventory for each type of syringe in early six month 2012 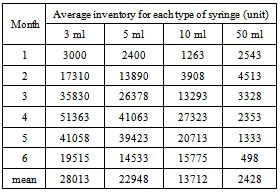 |
| |
|
Large inventories consume cash, increase the investment in the business and can bankrupt if not properly controlled[9]. Table 2. Ending inventory data of syringe for early six month at 2012 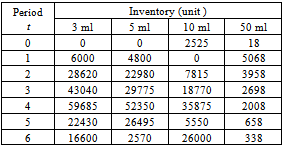 |
| |
|
From the data above, the hospital undergo stockout for 10 ml disposable syringe at the first month. Syringe 3ml and 5 ml also met stockout incident. That’s show how the importance of inventory control.In practice, this public hospital doesn’t use any periodic review calculation every order time. They just order based on demand at previous month. In order to know which the optimal review method, this study compare the current situation with periodic and continuous review calculation.
4.3. Periodic review calculation
In calculating safety stock for periodic review policy, using equations below, with assumption of desired cycle service level (CSL) is 95%[10]:Standard deviation of demand during T + L periods: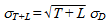 | (1) |
D : average demand per periodσD : standard deviation of demand per periodL : average lead time per periodT : time per periodCSL : desired cycle service level Equation for calculating safety stock and average level inventory: | (2) |
 | (3) |
Table 3. Safety stock and average inventory level for periodic review policy |
| Type of Syringe | SS and AIL for periodic review policy (unit/month) | Safety stock | Average Inventory Level | 3 ml | 14000 | 36600 | 5 ml | 9000 | 21300 | 10 ml | 8500 | 21850 | 50 ml | 650 | 1200 |
|
|
4.4. Continous Review Calculation
This study calculate the economic order quantity (EOQ) for four types of disposable syringe with assumption of holding cost 20% from unit price each year, and order cost 40,000 IDR (about $4 USD) each time order (per lot). Using standard equation of economic order quantity, EOQ for each type of disposable syringe can be computed[10] | (4) |
Table 4. Data of syringe annual demand and EOQ calculation |
| Type of Syringe | Data and calculation | Annual Demand (unit) | Unit price(IDR) | Order Quantity (unit) | 3 ml | 550000 | 484 | 21000 | 5 ml | 300000 | 653 | 13500 | 10 ml | 330000 | 798 | 12700 | 50 ml | 12500 | 10742 | 700 |
|
|
Then, in calculating safety stock for periodic review policy, using equations below, with assumption of desired cycle service level (CSL) is 90%[10]:Standard deviation of demand during T + L periods: | (5) |
D : average demand per periodσD : standard deviation of demand per periodL : average lead time T : review periodCSL : desired cycle service level Equation for calculate safety stock: | (6) |
This study try to compare how if medical warehouse in public hospital use continuous review policy. Many experiments in managing inventories show that continuous review policy has some advantages compare with periodic review policy.The equation f or calculating safety stock on continuous review inventory[10]:Standard deviation of demand during lead time: | (7) |
Given the desired CSL, the required safety inventory (ss): | (8) |
In calculating average inventory level we used:  | (9) |
When using a continuous review policy, a manager orders Q units when the inventory drops to ROP (reorder point). Clearly, a continuous review policy requires technology that monitors the level of available inventory.Table 5. Safety stock and average inventory level for continousreview policy |
| Type of Syringe | SS and AIL for continous review policy | Safety stock | Average Inventory Level | 3 ml | 2000 | 12550 | 5 ml | 1250 | 8000 | 10 ml | 1200 | 7550 | 50 ml | 90 | 450 |
|
|
Table 6. Reorder point for each syringe at continuous review policy |
| Type of Syringe | Reorder point (ROP) | 3 ml | 3500 | 5 ml | 2000 | 10 ml | 2000 | 50 ml | 125 |
|
|
5. Discussion
Some of the problems facing control systems are include the dearth of qualified stores personnel, overstock and under stock, and insufficient storage[10]. The public hospital is facing all of these problems. To overcome those problems, several options of solutions are available. This research try to compare average inventory level between current situation, using periodic calculation, and using continuous calculation.Table 7. Comparison between current average inventory, periodic average inventory level, and continous average inventory level 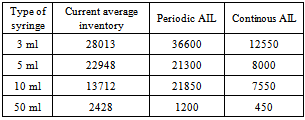 |
| |
|
From table 6 above, it can be seen that continous review policy has the smallest amount of average inventory level among others. Changing the review policy, from periodic to continuous is one of options. In continuous review, the required safety inventory is lower, only about 20% from safety inventory of periodic review policy. It is because in periodic review policy, the safety inventory is used to cover for demand uncertainty over the lead time and the review interval L+T.The continuous review policy also compatible with the characteristic of the product, in which the medical consumables are fast moving products.Another option available is change the scenario of goods distribution, from vendor until patient as a customer. Dividing goods distribution based on type of customers is very complicated and incommode because the type of medical consumables are definitely same. One scenario is developing by the public hospital now is change the distribution system into one line. Vendors send the goods to medical warehouse. Here medical warehouse has function to manage all of the inventories and as the center of inventories information system. Then medical warehouse send the goods in accordance with demand from pharmaceutical warehouse through distribution unit. Pharmaceutical warehouse has function to distribute the goods to all of point-of-uses. There is no separated line for every type of customers anymore.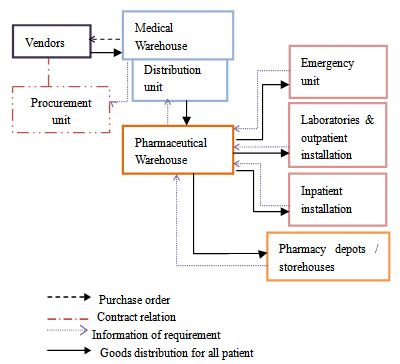 | Figure 2. Distribution scenario for medical consumables by public hospital |
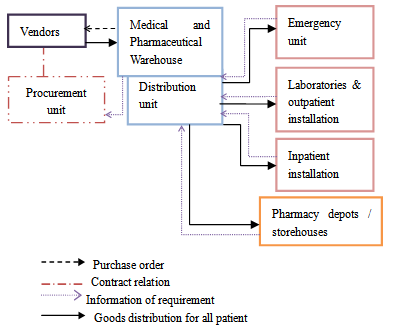 | Figure 3. Another distribution scenario option for medical consumables |
From different viewpoint, another distribution scenario can be developed. The pharmaceutical warehouse can be combined with medical warehouse into one big warehouse without omit each function.If the distribution line is shorter, it can minimize data mistakes, and lead time. It’s also simpler system than before. But it needs bigger space to keep the goods. So the addition cost to change the warehouse bigger is critically needed.Those three options of distribution line is needed to be simulated, so we can know which one is the most optimal scenario of distribution line.Significantly the hospital is facing serious problem with the practice of its distribution process and inventory management. From some interviews, there are several factors that need to be concerned, to get solution for the problem. The dominant root cause of this unconformity is this hospital has limitation of warehouse space. Therefore, the appropriate inventory management strategy is reducing until minimum. In their long term planning, the hospital has been considering to implement Just in Time system. This strategy is fit to reduce risk in relating to the warehouse space. Relating with the inventory management and distribution process, the hospital is either lack of employee amount or employee skill. In developing supply chain management system, it really needs high competence of employee. Hospital may have to choose whether improving its staff competencies first or increasing the amount of staff with same capability. There is no significant system that appropriate to be used for managing inventory in this hospital. All of the data collected and inventory checking are still conducted in manual way. IT system is very crucial and has very important role in every supply chain system because it can minimize errors, accelerate data gathering, and simplify all of inventory management process. Resources that are available among the supply chain parties could be utilized more effectively such as human resources, technology and raw materials.In the collaborative environment, each party should be agreeing to work together in order to achieve a common objective[11]. Furthermore, resource-planning decisions such as human resource development and technology planning could be done effectively by considering the capabilities of all parties.The medical and pharmacy warehouse department have to collaborate with IT department to improve the information system. They also have to collaborate with financial department in payment and credit acquaintance of medical consumables purchasing. It is because the length of payment very affects the distribution of medical devices from vendor to hospital. Procurement department also have to be concerned in the collaboration, because it plays important role in making contract with vendor for a couple of month.
6. Conclusions
From this research we can conclude that there are many aspects that can be root cause of problems and have to be the most concerned in improving inventory management and distribution system in hospital, particularly for medical consumables. Problems that often happened in hospital are lack of human resources, inadequate system of information and technology, limited warehouse space, and delayed payment to vendor. Those problems can be solved if hospital is more concerned with these factors: design and practice of medical devices distribution, model of review policy, efficient use of resources, and collaboration with other departments to give customer service improvements. Future researches are developed some scenarios for medical consumables distribution, and simulate them using supply chain simulation software. From simulation, it can show which the most optimal scenario for distributing medical consumables in public hospital.
References
[1] | Rosetti, “Inventory Management Issues in Healthcare Supply Chain”, University of Arkansas, USA, 2008. |
[2] | Xiong Zhi, Shaligram P., “Logistics Innovation Process Revisited: insight from a hospital case study”, International Journal of Physical Distribution and Management, Vol. 41, No. 6, pp. 577-600, 2007. |
[3] | Noorfa Mustaffa, Andrew Potter, “Healthcare Supply Chain Management in Malaysia: a case study”, Emerald Group Publishing, Supply Chain Management: an International Journal, Vol. 14, No.3, pp. 234-243, 2009. |
[4] | Vikram Bhakoo, Prakash Singh, Amrik Sohal, “Collaborative Management of Inventory in Australian Hospital Supply Chain: Practices and Issues”, Emeral Group Publishing Limited, 2012. |
[5] | Susan Heienbuch, “A Case of Succesful Technology Transfer to Healthcare: Total quality management and just-in-time”, MCB University Press, Journal of Management in Medicine, Vol.9, No.2, pp.48-56, 1995. |
[6] | Online available:http://www.ime.unicamp.br/~andreani/MS515/capitulo12.pdf |
[7] | Leroy B. Schwarz, “The Economic Order Quantity (EOQ) Model”, Purdue University, online available: http://www.isye.umn.edu/courses/ie5551/additional%20materials/eoq.pdf |
[8] | Online available:http://faculty.apec.umn.edu/veidman/4821S06/InventoryNotes.pdf |
[9] | Online available: http://www.smbtn.com/books/gb29.pdf |
[10] | Sunil Chopra, Peter Meindl, “Supply Chain Management: Strategy, Planning, and Operation” fourth edition, Pearson, USA, 2010. |
[11] | Abdul Mumini Yusuf, Inventory Control and Economic Order Quantity in National Electric Power Authority (NEPA), Dissertation, St Clements University, 2003. |
[12] | Udin, Z.M, Khan, M.K., Zairi.M. “A collaboratice supply chain management framework: part 1 – planning stage”, Business Process Management Journal, Vol.12 No.3. pp.36-376 , 2006. |