Mohamed Abuel Kasem Mohamed1, Galal Abd El Azim Ibrahim2, Ahmed Mohamed Ebrahim Rizk2, Mahmoud Mohamed Ahmed2, Ahmed Mohamed El Nozahi3, Nagui Aly Abdel-Khalek4, Hasan Bakheat5
1Principle Investigator of Center of Evaluation and Upgrading Ore Quality in South Valley, Mining and Metallurgical Engineering Dept., Faculty of Engineering, Assiut University, Assiut, Egypt
2Members of Center of Evaluation and Upgrading Ore Quality in South Valley, Mining and Metallurgical Engineering Dept., Faculty of Engineering, Assiut University, Assiut, Egypt
3Ex. General Secretary of Council of Research for Industrial Technologies in the Egyptian Academy of Scientific Research and Technology, Egypt
4Former President of Central Metallurgical Research and Development Institute (CMRDI), Egypt
5Exploration and Evaluation of Mineral Deposit, Egyptian Mineral Resources Authority, Egypt
Correspondence to: Mohamed Abuel Kasem Mohamed, Principle Investigator of Center of Evaluation and Upgrading Ore Quality in South Valley, Mining and Metallurgical Engineering Dept., Faculty of Engineering, Assiut University, Assiut, Egypt.
Email: |  |
Copyright © 2018 The Author(s). Published by Scientific & Academic Publishing.
This work is licensed under the Creative Commons Attribution International License (CC BY).
http://creativecommons.org/licenses/by/4.0/

Abstract
During the beneficiation of phosphate ores, huge amounts of oversize phosphate ores are rejected from crushers. This reject mostly contains low P2O5 content and high gangue content. Phosphates are vital nonrenewable resources. The treatment of phosphate ore wastes of El-Nasr Mining Company, Sepaeya, Egypt aims to upgrade P2O5 percent, adds a new economic value, development of the national income, and aids to clean the mine district. The main aim of this paper is to compare different processing alternatives methods to concentrate and upgrade of phosphate ore tailings assayed 18.37% of El-Nasr Mining Company, Sepaeya, Egypt. The concentration of wastes not only add an economic value but also safe the human, animals, and plants. Two options of sizes obtained from grinding and sieving (-250 µm and -100 µm were separated to obtain the highest grade of P2O5 with the greatest recovery). The leaching process on size -100 µm raised P2O5% from 23.88% to 28.44% with mass recovery of 28.29%. The leaching process on size -250 µm raised P2O5% from 21.41% to 25.51% with mass recovery of 51.69%. For economic production, the grade of P2O5 in the host phosphate rocks should be at least 24%. In this paper, four options of different percentages of P2O5 ranged from 21.41% to 28.44% obtained from different mineral processing operations were economically compared. These options were obtained from suggested capacity of 190,000 ton/year of phosphate ore tailings assayed 18.37% of Nasr Mining Company, Sepaeya, Egypt. The net annual profit was more than 18,000,000 LE for each option. Option_2 (-250 µm resulted from grinding process) was giving the maximum profit (30,330,800 LE), the least payback period (0.16 year), and the maximum accounting rate of return (630%).
Keywords:
Phosphate, Wastes, Crushing, Grinding, Sieving, Leaching, Economics, Payback Period, Rate of Return
Cite this paper: Mohamed Abuel Kasem Mohamed, Galal Abd El Azim Ibrahim, Ahmed Mohamed Ebrahim Rizk, Mahmoud Mohamed Ahmed, Ahmed Mohamed El Nozahi, Nagui Aly Abdel-Khalek, Hasan Bakheat, Economics of Exploitation Phosphate Ore Wastes, International Journal of Mining Engineering and Mineral Processing , Vol. 7 No. 1, 2018, pp. 14-20. doi: 10.5923/j.mining.20180701.02.
1. Introduction
Phosphates ores are vital nonrenewable resources used for manufacturing of phosphoric acid, fertilizers and animal feed production [1-5]. The annual consumption of phosphates approached 150 million tons.Wastes produced from the phosphate industry presents many challenges due to the high economic and environmental impacts involved with their disposal. However, the relative scarcity of high-grade phosphate ores has driven researchers to recover and recycle these valuable wastes (secondary sources) [3, 6].The wastes of phosphate ore are mostly of lower grade which needs processing or upgrading for economic utilization. Phosphate ores in terms of quality and P2O5 grade can be divided into three groups: low-grade (12–16% P2O5), intermediate-grade (17–25% P2O5), and high-grade (26–35% P2O5) [7]. Deposits consisting of (28–38% P2O5) are considered commercial-grade and are economic to mine and process [7]. The marketable phosphate is usually 30% P2O5 or higher.There are several physical and thermal treatment beneficiation techniques for upgrading of phosphate ore tailings. In some cases, simple, inexpensive techniques are enough to produce the required grade [8]. For example, crushing and screening are used to get rid of the coarse hard siliceous material, and attrition scrubbing and de-sliming are used to remove the clayey fine fraction [9-10].Tailings and wastewaters produced from the phosphate industry are the main secondary sources of phosphates [11-12]. These low-grade resources can be enriched to increase the grade of P2O5 to meet the requirements for production of P2O5-based fertilizers. In Egypt phosphate ore reserves occur in three main localities namely; Nile valley, new valley in western desert, and the eastern desert along the Red Sea coast. Currently, newly discovered phosphate ores are being mined from Nile valley areas mainly for exportation and partially for local production of fertilizers. However, the mining companies export only the fractions of high grade (over 30% P2O5) while the fractions of low grade is being rejected. This is because such fractions contain different gangue minerals such as calcite and silica.The nature of capital investment may be defined as the use of today's funds to generate tomorrow's profits. Thus, it is vitally important to the future growth and profitability of a company that capital investment decisions should be made as wisely as possible [13-16].A single investment possibility may be referred to as a project. The objective of capital investment appraisal is to provide a rule for deciding in the case of any given capital investment project, whether the project should be undertaken or not. The objective of any capital investment appraisal is to set up a decision rule for accepting or rejecting. Most decision rules for capital investment appraisal operate essentially the following three stages: reduce all available information about the project and its associated each flows to one single number (payback period, net present value, etc.), compare that number with some given threshold or cut-off number, and if the number associated with the project is better than the threshold level, the project is accepted and vice versa [13-16].This paper aimed to compare economically four options of different percentages of P2O5 ranged from 21.41% to 28.44%. These options were obtained from different mineral processing operations and a suggested capacity of 190,000 ton/year of phosphate ore tailings assayed 18.37% of Nasr Mining Company, Sepaeya, Egypt. This capacity was determined according to the market demand.Payback PeriodOne of the major topics which is taught in the field of finance is the rules of capital budgeting, including the payback period and the net present value [13-16].Payback period is the length of time required to recover the initial cash outlay on the project. Accordingly, the shorter the period, the more desirable is the project. As a widely used investment criterion, this seems to offer the following advantages: it is simple both in concept and application, it is a rough and ready method for dealing with risk, and since it emphasizes earlier cash inflows, it may be a sensible criterion when the firm it having problems of liquidity [13].However there are following series limitations: it fails to consider time value of money. Cash inflows in the payback calculation are simply added without suitable discounting. This method ignores cash flows beyond the payback period. This leads to discrimination against projects, which generates substantial cash inflows in later years. Also, it is a major of projects capital recovery, not profitability [13-16].Accounting Rate of ReturnThis is usually termed as rate of return method. This method involves expressing the total expected income from the project as a percentage of its capital investment. This investment appraisal criterion become popular because of the following advantages: it is simple to calculate, it is based on accounting information which is readily available, and it considers benefits over the entire life of the project. However, it is shortcomings are based upon accounting profit not cashflow and it also does not take into account the time value of money [13-16].
2. Experimental Work
In this paper, different alternative processes were carried out to concentrate and upgrade of phosphate ore tailings.Sample Preparationi- The head sample was mixed thoroughly and divided into 8 similar parts; each part represents about 5 kg with size of -70 mm.ii- The first part which having P2O5 percent about 18.37% was sieved on screen of 5 mm size. The oversize and undersize were chemically analyzed for P2O5 percent. It can be seen that the percent of P2O5 in oversize (-70+50mm) was about 18.34%, while in undersize (-5 mm) was 21.76%.Procedurei- The oversize resulted from sieving the original sample (-70+50mm) was comminuted in three-stage crushing processes (primary, secondary, and tertiary) according to the flowsheet shown in Fig. 1. A representative sample of undersize -5 mm was subjected to sieving and each size fraction was chemically analyzed.ii- A representative sample of crushed ore -5 mm obtained from crushing processes was ground using hammer mill in closed circuit with screen 1 mm. The ground sample (-1 mm) was sieve analyzed and each size fraction was chemically analyzed.iii- Different sizes resulted from grinding process (-250 µm and -100 µm) were chemically analyzed for determination the percentage of P2O5 in each fraction. The final results are illustrated in Table 1.iv- Two representative samples of sizes -250 µm and -100 µm were leached separately at acid to ore ratio 10%, leaching time 15 minutes, agitation speed 1200 rpm, and solid to liquid ratio of 15%. The final products were chemically analysed for determination the percentage of P2O5 in each fraction. The final results are tabulated in Table 1.According to the experimental work shown in Table 1 and Figure 1 of upgrading phosphate ore tailings of Nasr Mining Company, Sepaeya, Egypt, four options of different P2O5 percentages and mass recoveries were obtained.Table 1. Specifications of the different options 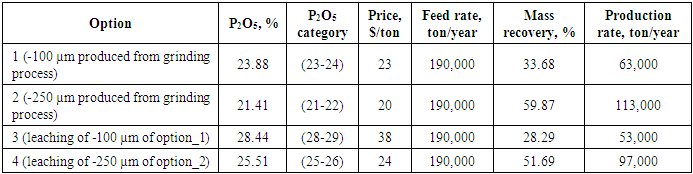 |
| |
|
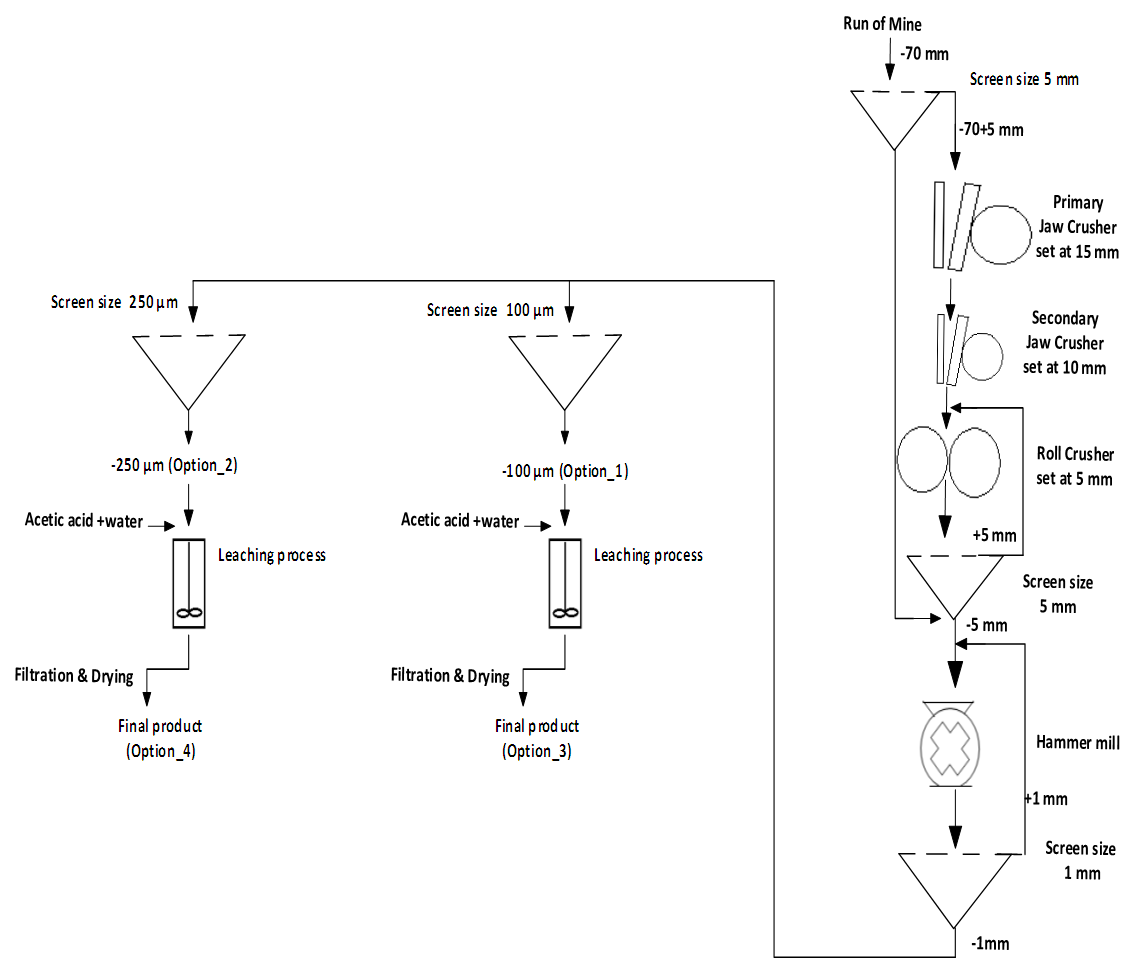 | Figure 1. Flowsheet of the different options resulted from the experimental work of upgrading of phosphate ore tailings of Nasr Mining Company, Sepaeya, Egypt |
3. Results and Discussions
This work compared different processing alternatives methods to concentrate and upgrade of phosphate ore tailings assayed 18.37% of El-Nasr Mining Company, Sepaeya, Egypt. The concentration of wastes not only added an economic value but also saved the human, animals, and plants.Two options of sizes obtained from grinding and sieving (-250 µm and -100 µm) were separated to obtain the highest grade of P2O5 with the greatest recovery. The leaching process on size -100 µm raised P2O5% from 23.88% to 28.44% with mass recovery of 28.29%. The leaching process on size -250 µm raised P2O5% from 21.41% to 25.51% with mass recovery of 51.69%.Four options of different percentages of P2O5 ranged from 21.41% to 28.44% obtained from different mineral processing operations were economically compared.Direct, indirect, fixed capital, and operating costs, as well as electrical power, water, fuel, etc. are calculated using the local prices [17-18]. Direct costs are directly related to the production rate. This includes utilities, direct labor, supervision plant, equipment maintenance, payroll overhead, and operating supplies. Indirect costs are not directly related to production rate. This includes services, marketing and sales, public relations, communications, offices furnishing, maintenance, cafeteria, etc. The fixed capital costs include insurance, depreciation, and local taxes. The main assumptions and data calculated are provided by some mining companies in the area of Qusier, Egypt, as well as, by some external companies in manufacturing of comminution equipment [17-19].Determination of plant capacityThe capacity of every operation unit is based on the final beneficiation flowsheet and is calculated according to a suggested capacity of 190,000 ton per year of phosphate ore tailings. This capacity was determined according to the demand for local market and exportation [17]. It is clear that the plant will run with a capacity of about 30 ton per hour.Estimation of equipment productionBased on the information obtained from mining companies, it is concerning the following items [18]:No. of working days per year
300 daysNo. of working hours per day
21 hoursThe proposed plant should have a capacity of 30 ton per hour (21 hour per day) or 630 ton per day. These feed rates of phosphate tailings are applying in the mass balance of the beneficiation flowsheet. The following number of major equipment is determined according to their sizes as shown in Tables 2 & 3.Table 2. Major equipment needed 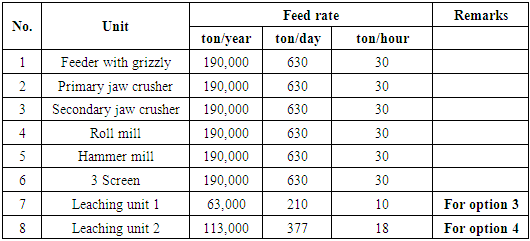 |
| |
|
Table 3. List of auxiliary equipment needed  |
| |
|
Option_1 (-100 µm resulted from grinding process):Estimation of fixed capital costsThe detailed fixed capital costs are calculated for 190,000 ton/year feed rate using the equipment listed in Table 4 [19]. In this table, it can be revealed that Jaw Crucher (Model LC3000X3000) can reduce the feed size from plus 70 mm to minus 5 mm (reduction ratio about 15). This will save the prices of secondary jaw crucher and roll crusher required in Fig. 1 and consequently will reduce the total fixed costs.From Table 4, it can be shown that:Total costs of equipment (FOB China port price) = 159,342 USD = 2,868,156 LE (1 USD = 18 LE)Cost of shipping from China to Egypt [17, 19] = 13,000 USD = 234,000 LE Cost of custom tax (about 10%) = 286,816 LE Cost of Electric Generator = 80,000 USD = 1,440,000 LE The total capital costs = 4,828,972 LE Table 4. Specification of equipment [19] 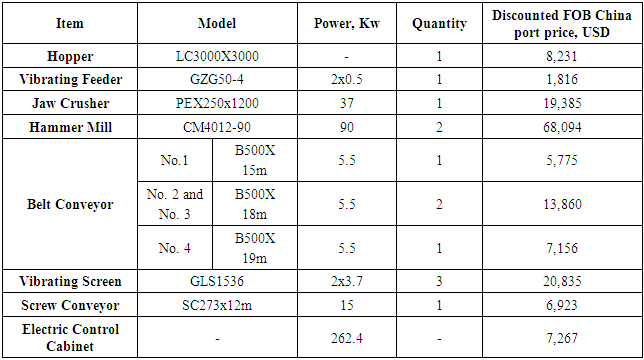 |
| |
|
Calculation of operating costs [18, 20]1. Cost of transporting phosphate tailings from source to plant = 3 LE/ton2. Cost of transporting product (concentrate) to final storage = 3 LE/ton3. Cost of power = 4.4 LE/ton4. Cost of labor = 4 LE/tonFrom Table 5, it can be revealed that:Sum of operating costs = 2,365,000 LE/yearAdding 10% factor of safetyTotal operating costs = 2,601,500 LE/year Table 5. Total operating costs of the plant (production rate = 63,000 ton per year) for option_1 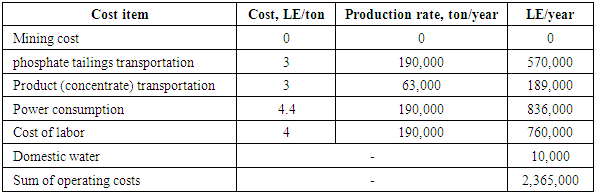 |
| |
|
Financial evaluation of Option_1 [13, 17, 20]Annual return = 63,000*23 = 1,499,000 USD = 26,082,000 LE /year Annual profit = Annual return - Total operating costs = 23,480,500 LE/yearDiscounting 15% taxes = 4,696,100 LE/yearNet Annual profit = 18,784,400 LE/year The payback period = Total capital costs / Net Annual profit = (4,828,972/18,784,400) = 0.26 year The accounting rate of return = Net Annual profit / Total capital costs = (18,784,400 /4,828,972)*100 = 389%From the previous calculations, it can be seen that the payback period of option_1 equals to 0.26 year and the accounting rate of return is about 389%.Option_2 (-250 µm resulted from grinding process)Estimation of fixed capital costsThe detailed fixed capital costs are calculated for 190,000 ton/year feed rate using the same equipment listed in Table 4 of option_1 [19] except the screen size is 250 µm instead of 100 µm.The total capital costs = 4,828,972 LECalculation of operating costsFrom Table 6, it can be revealed that:Sum of operating costs = 2,515,000 LE/yearAdding 10% factor of safety,Total operating costs = 2,766,500 LE/yearTable 6. Total operating costs of the plant (production rate = 113,000 ton per year) for option_2 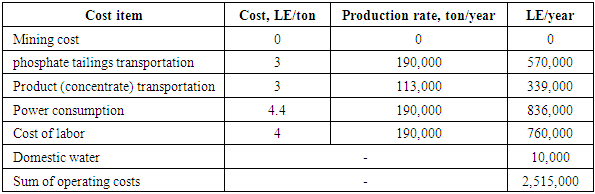 |
| |
|
Financial evaluation of Option_2 [13, 17, 20]Annual return =113,000*20 = 2,260,000 USD/year = 40,680,000 LE /year Annual profit = Annual return - Total operating costs = 37,913,500 LE/yearDiscounting 20% taxes = 7,582,700 LE/yearNet Annual profit=30,330,800 LE/year The payback period = Total capital costs / Net Annual profit = 0.16 year The accounting rate of return = Net Annual profit / Total capital costs = 630%The previous results, illustrated that the payback period of option_2 equals to 0.16 year and the accounting rate of return is about 630%.Option_3 (leaching of -100 µm resulted from grinding process in option_1)Fixed capital costs estimationThe detailed fixed capital costs are calculated for 190,000 ton/year capacity using the equipment listed in Table 4 [19]. In this option, it is used the same equipment as option_1 except the prices of leaching, filtration, and drying units are added.The total capital costs in option_1 = 4,828,972 LEThe price of leaching unit = 4000 USD = 72,000 LEThe price of filtration unit = 5000 USD = 90,000 LEThe price of drying unit = 6000 USD = 108,000 LEThe total capital costs = 5,098,972 LECalculation of operating costsFrom Table 7, it can be revealed that:Sum of operating costs = 8,958,000 LE/yearAdding 10% factor of safetyTotal operating costs = 9,853,800 LE/yearTable 7. Total operating costs of the plant (production rate = 53,000 ton per year) for option_3 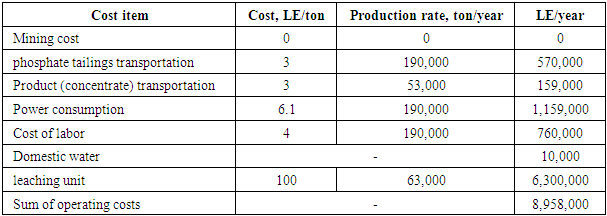 |
| |
|
Financial evaluation of Option_3 [13, 17, 20]Annual return = 2,014,000 USD/year = 36,252,000 LE/yearAnnual profit = Annual return - Total operating costs = 26,398,200 LE/yearDiscounting 20% taxes = 5,279,640 LE/yearNet Annual profit = 21,118,560 LE/yearThe payback period = Total capital costs / Net Annual profit = 0.24 yearThe accounting rate of return = Net Annual profit / Total capital costs = 414%From the above estimations, it can be cleared that the payback period of option_3 equals to 0.24 year and the accounting rate of return is about 414%.Option_4 (leaching of -250 µm resulted from grinding process in option_2)Fixed capital costs estimationThe detailed fixed capital costs are calculated for 190,000 ton/year capacity using the equipment listed in Table 4 [19]. In this option, it is used the same equipment as option_2 except the prices of leaching, filtration, and drying units are added.The total capital cost in option_2 = 4,828,972 LEThe price of leaching unit = 4000 USD = 72,000 LEThe price of filtration unit = 5000 USD = 90,000 LEThe price of drying unit = 6000 USD = 108,000 LEThe total capital costs = 5,098,972 LECalculation of operating costsFrom Table 8, it can be revealed that:Sum of operating costs = 14,090,000 LE/yearAdding 10% factor of safetyTotal operating costs = 15,499,000 LE/yearTable 8. Total operating costs of the plant (production rate = 97,000 ton per year) for option_4 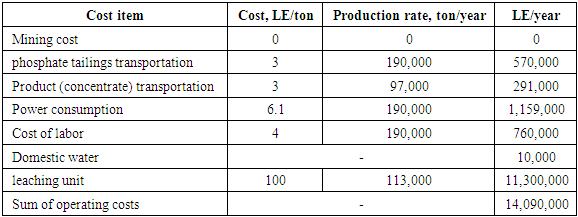 |
| |
|
Financial evaluation of Option_4 [13, 17, 20]Annual return = 2,328,000 USD/year = 41,904,000 LE/yearAnnual profit = Annual return - Total operating costs = 26,405,000 LE/yearDiscounting 20% taxes = 5,281,000 LE/yearNet Annual profit = 21,124,000 LE/yearThe payback period = Total capital costs / Net Annual profit = 0.24 yearThe accounting rate of return = Net Annual profit / Total capital costs = 414%From these calculations, it can be shown that the payback period of option_4 equals to 0.24 year and the accounting rate of return is about 414%.Table 9 showed the final comparison of different suggested options for experimental work of upgrading phosphate ore tailings of Nasr Mining Company. From this table, it can be seen that option_2 resulted the maximum profit (30,330,800 LE), the least payback period (0.16 year), and the maximum accounting rate of return (630%) while option_1 gave the minimum profit (18,784,400 LE), the largest payback period (0.26 year), and the minimum accounting rate of return (389%). Options_3 and 4 gave nearly the same values of net annual profit, payback period, and accounting rate of return.Table 9. Final comparison of different options 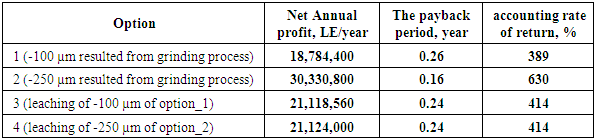 |
| |
|
4. Conclusions
This work compared different processing alternatives methods to concentrate and upgrade of phosphate ore tailings assayed 18.37% of El-Nasr Mining Company, Sepaeya, Egypt. The concentration of wastes not only added an economic value but also saved the human, animals, and plants.Two options of sizes obtained from grinding and sieving (-250 µm and -100 µm) were separated to obtain the highest grade of P2O5 with the greatest recovery. The leaching process on size -100 µm raised P2O5% from 23.88% to 28.44% with mass recovery of 28.29%. The leaching process on size -250 µm raised P2O5% from 21.41% to 25.51% with mass recovery of 51.69%.Four options of different percentages of P2O5 ranged from 21.41% to 28.44% obtained from different mineral processing operations were economically compared. The net annual profit for suggested capacity of 190,000 ton/year was more than 18,000,000 LE at least for each option. This means that applying any of the suggested beneficiation flowsheets, from the economic point of view, is profitable. Option_2 (-250 µm resulted from grinding process) was giving the maximum profit (30,330,800 LE), the least payback period (0.16 year), and the maximum accounting rate of return (630%).
ACKNOWLEDGEMENTS
The present research work was supported by the Egyptian Academy of Science and Technology with Assiut University, Faculty of Engineering to establish Centre of Evaluation and Upgrading Ores in South Valley (grant # 37). The authors would like to thank Eng. Amr Ateto, demonstrator at Mining & Metallurgical Engineering Dept. Technicians in mineral processing labs are also appreciated.
References
[1] | Mohammadkhani, M., Noaparast, M., Shafaei, S.Z., Amini, A., Amini, E., Abdollahi, H., "Double reverse flotation of a very low grade sedimentary phosphate rock, rich in carbonate and silicate", International Journal of Mineral Processing, 100, 157–165, 2011. |
[2] | Vaneeckhaute, C., Janda, J., Vanrolleghem, P.A., Filip, M.G., Meers, E., "Phosphorus use efficiency of bio-based fertilizers: Bioavailability and fractionation", Pedosphere, 26, 310–325, 2016. |
[3] | Abdel-Zaher, M.A., "Physical and thermal treatment of phosphate ores-an overview”, Int. J. Miner. Process. 85, 59–84, 2008. |
[4] | Jasinski, S.M., "Phosphate Rock", USGS 120–121, 2007. |
[5] | Gharabaghi, M., Noaparast, M., Irannajad, M., "Selective leaching kinetics of low grade calcareous phosphate ore in acetic acid", Hydrometallurgy 95, 341–345., 2009. |
[6] | Alsafasfeh, A., Alagha, L., "Recovery of phosphate minerals from plant tailings using direct froth flotation", Minerals, 7, 145, 2017. |
[7] | Sengul, H., Ozer, K., Gulaboglu, M.S., Chem. Eng. J. 122 (3), 135–140, 2006. |
[8] | Negm, A.A., Abouzeid, A.-Z.M., "Utilization of East Seba'eya Phosphate Plant Tailings", Final Report to the Academy of Scientific Research and Technology, 2002. |
[9] | Al-Fariss, T.F., El-Nagdy, K.A., Abdel-Aleem, F.A., El-Midany, A.A., "Column versus mechanical flotation for calcareous phosphate fines upgrading", Part. Sci. Technol. 5, 488–493, 2013. |
[10] | El-gillani, D.A., Abouzeid, A.-Z.M., Int. J. Miner. Process. 38, 235–256, 1993. |
[11] | De-Bashan, L.E., Bashan, Y. "Recent advances in removing phosphorus from wastewater and its future use as fertilizer" (1997–2003), Water Res., 38, 4222–4246, 2004. |
[12] | Sørensen, B.L., Dall, O.L., Habib, K., "Environmental and resource implications of phosphorus recovery from waste activated sludge", Waste Manag., 45, 391–399, 2015. |
[13] | Femi, A., "The Importance of the Payback Method in Capital Budgeting Decision", M.Sc. Thesis in Business Administration, Fall/Spring 2008. |
[14] | Ardalan, K., "Payback Period and NPV: Their Different Cash Flows", Journal of Economics and Finance Education, Volume 11, Number 2, 1-16, Winter 2012. |
[15] | Waud, R., "Economics", 3rd Australian Edition, Longman, Melbourne, 1996. |
[16] | Chatterjee, K K, "Introduction to Mineral Economics", New Age International, New Delhi, p. 379, 2008. |
[17] | "Export Sector of EL-Nasr Mining Company", 2017. |
[18] | "Local Private Phosphate Mines Contractors", Red sea governorate, Egypt, 2017. |
[19] | "Liming Heavy Industry Science & Technology Co.", Ltd., China, 2017. |
[20] | Ray and Sinha, "Mine and Mineral Economics", PHI-Learning Private Limited, Delhi, Ch. 5, pp. 80-108, 2016. |