Njamba Mike Njamba , Victor Mutambo
University of Zambia, School of Mines, Department of Mining Engineering, Lusaka, Zambia
Correspondence to: Victor Mutambo , University of Zambia, School of Mines, Department of Mining Engineering, Lusaka, Zambia.
Email: |  |
Copyright © 2016 Scientific & Academic Publishing. All Rights Reserved.
This work is licensed under the Creative Commons Attribution International License (CC BY).
http://creativecommons.org/licenses/by/4.0/

Abstract
Baluba mine was commissioned in 1973 and since then over 55 million tonnes of ore has been mined leaving out only 8.4 million tonnes reserves at very low block grade and structurally thin and difficult to mine. The area referred to as Baluba east has the ore body lying below 330 ml and 400 ml. The ore-body has thickness ranging from 6 to 10.5 m with a dip of 21 degrees and erratic grade. Attempt to mine the area in question has not been so successful as the reserves become thinner and also occur in poor ground conditions area. Therefore, this study was undertaken in order to select an appropriate mining method for extraction of the ore between the above mention levels within T- Block from SS 37 to SS 40. The study involved three phases: Analysis of actual geotechnical information at the mine; selection of the mining method using the University of British Columbia method (UBC) and the UNZA Mining method Selection tool. The best Mining method (Single level caving) was then subjected to cost analysis to establish its viability. The total cost calculated for the project was $ 2,990,869.92 and the expected revenue is $ 4,782,590.77 giving a payback period for the investment of approximately 6 months.
Keywords:
Mining method, Ore body, Mining Method Selection tool, Costs
Cite this paper: Njamba Mike Njamba , Victor Mutambo , Design an Appropriate Mining Method for Extraction of Ore between 330ml and 400ml at Baluba East Upper T-Block, International Journal of Mining Engineering and Mineral Processing , Vol. 5 No. 1, 2016, pp. 16-23. doi: 10.5923/j.mining.20160501.03.
1. Introduction
Luanshya copper mines plc needs to maintain and increase copper production in order to remain viable. In so doing it seeks to exploit ore deposits that lie between 330ml and 400ml at Baluma Mine. The problem at hand is to come up with a proper design that will enable the mine to extract the ore in the named area. In order to select the final mining method, three steps were undertaken. The steps involved selecting and ranking the mining methods based on ore-body characteristics using the University of British Columbia (UBC) online method section tool(http://www.edumine.com/tools/mining-method-selection) and the UNZA mining method section Tool (2015). The top three mining methods were then designed using the AutoCAD software. Later the designed top three mining methods were then subjected to development costs and environmental impacts analysis. Finally, the best mining method was subjected to cost analysis to establish its viability.
2. Materials and Methods
The research methodology included review of available geotechnical information between 330ml and 400ml from mining planning and rock mechanics department. Furthermore, other literature was reviewed to establish the effect of choosing a mining method based on geotechnical parameters and other ore-body characteristics. The actual geotechnical information obtained from the mine between levels 330 ml and 400 ml was used as input data for UBC online method selection tool and the Mining Method Selection tool (MMST, UNZA). The UBC mining method selection is a modification of the Nicolas approach (1981), which places more emphasis on stoping method. According to Nicolas, each mining method is ranked according to the suitability of its geometry/grade distribution and ore zone, hanging wall and foot wall rock mechanics characteristics. The four ranks used with corresponding rating are: preferred (3-4); probable (2-1); unlikely (0) and eliminated (-49). The steps in the section process involves: a) listing the geometry/grade distribution and rock mechanics characteristics of the deposit, ore zone, hanging wall and foot wall rock mechanics for each different mining methods and assigning numerical values for each characteristic which are then added up. The mining method which scores highest is then chosen as an appropriate mining method and further subjected to economic evaluation.UBC online method selection tool a modification to the Nicholas system (1981) is the weighting of the categories for the ore geometry, ore zone, hanging and foot walls. To give each of these categories equal weight, the ore zone, hanging wall, and foot wall need to be multiplied by 1.33.The Mining Method Selection tool (MMST) is based on Nicolas system (1981) but in addition to numerical rating of different parameters subjects the feasible mining methods to environmental analysis and development costs.Using the above mentioned tools (UBC and MMST) the three selected top mining methods were then designed using AutoCAD software and later subjected to economic analysis before picking the appropriate mining method.In order to determine which mining method was feasible, there was need to compare the characteristics of the deposit with those required for each mining method; the method(s) that best match where considered technically feasible for the ore geometry and ground conditions and finally evaluated economically so as to come up with a low cost operation (Nicholas, D. E- 1981).Physical and mechanical characteristics of the deposit of the ore zone, hanging wall, and footwall, ore thickness, general shape, dip, plunge, depth below the surface, grade distribution, quality of resource, etc. were numerically rated including the major rock mechanics properties (Nicholas, D. E., 1992).The rock mechanical properties of the ore-body and country rock influence the choice of the mining method in that they determine the type of support offered to generated mine structures (stopes, pillars etc.) which ultimately have a bearing on mining costs (B.H.G. Brady and E.T Brown -2005). Hence, based on generated mine structure, mining methods can be classified as: pillar supported; artificially supported and unsupported (Howard L and Hartman -1992).
3. Data Collection and Results
3.1. Ore Body Characteristics
The ore-body lying between 330ml and 400ml has a tabular shape with thickness ranging from 6 to 10.5m and dip of 21 degrees. The estimated total tonnage between 300ml and 400ml is 1.1 million tonnes of ore with in situ grades of 2.01% total copper and cut-off grade of 1.23 % tcu.
3.2. Rock Mechanics Properties
The following geomechanical properties (tables 3.2 and 3.3) were collected and used as input data mining method selection tools:Table 3.2. Rock Substance Strength 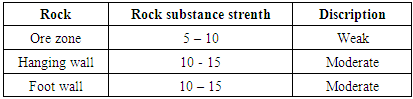 |
| |
|
Table 3.3. Rock Mass Rating 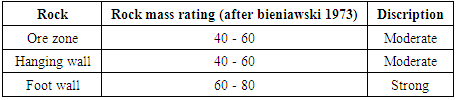 |
| |
|
4. Data Analysis and Discussion
4.1. Mining Method Selection
The purpose of undertaking a selection procedure was to find a suitable mining method that will be economically and environmentally acceptable. Two mining method selection tools were used in evaluating geotechnical parameters: University of British Columbia (UBC) an online advanced version (http://www.edumine.com/tools/mining-method-selection/) and Mining Method Selection Tool (2015), UNZA.
4.1.1. UBC Mining Method Selection
Results obtained from UBC are shown in figure 4.1.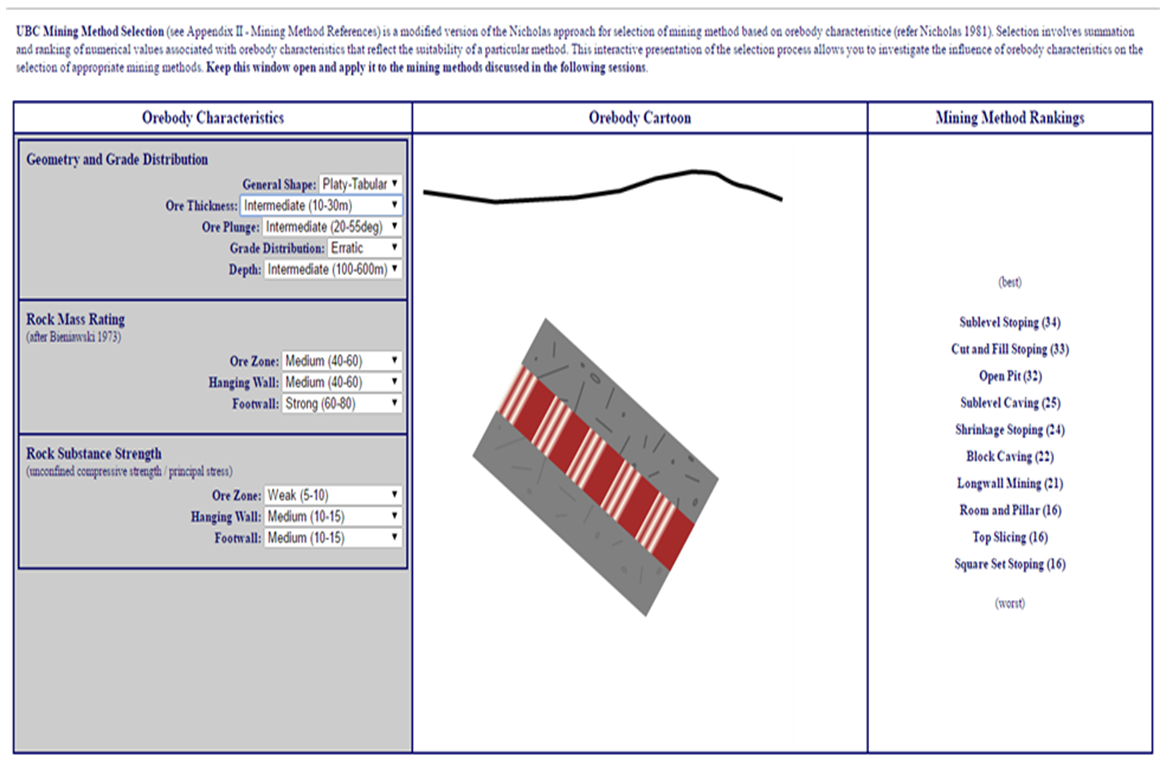 | Figure 4.1. UBC windows as depicted from online |
Results from UBC gave the following top three mining methods in order of ranking: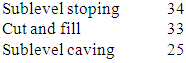
4.1.2. Mining Method Selection Tool (MMST)
Results obtained using the Mining Method Selection Tool (fig. 4.2) gave the following top three mining methods.
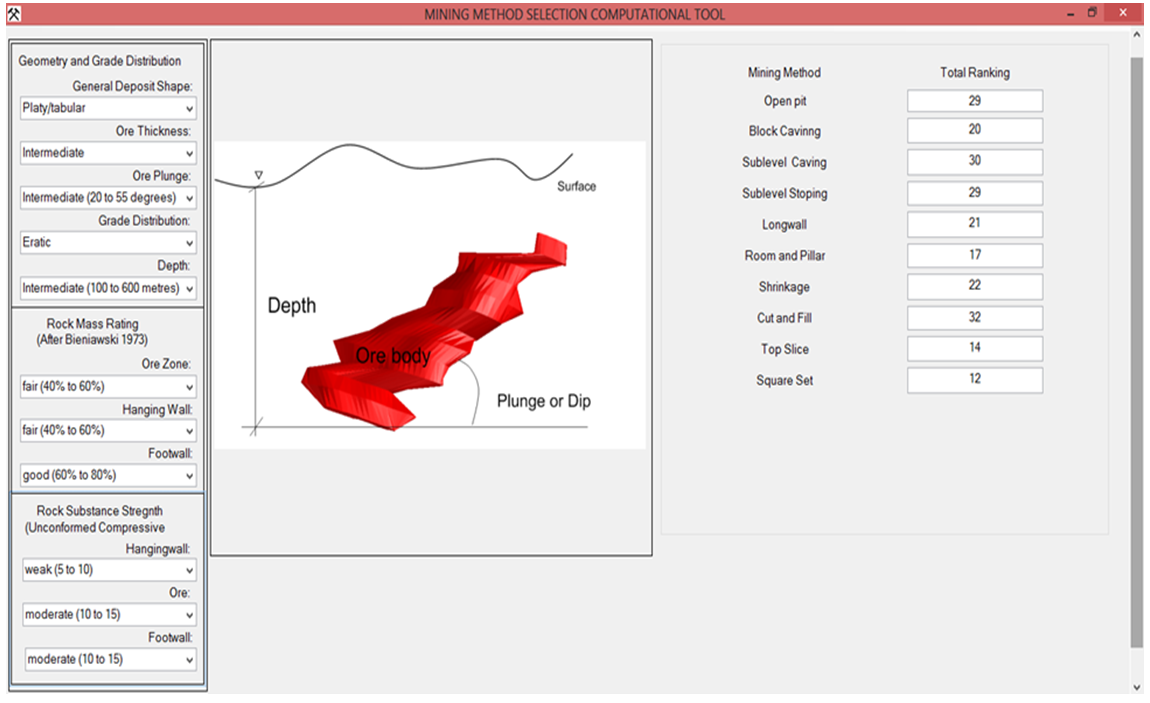 | Figure 4.2. Window depicted from the Mining Method Selection Tool (UNZA) |
The selected methods in both scenarios were then subjected to economic and environmental analysis.
4.2. Further Analysis of the Top Three Mining Methods
The mining method employed must be safe and must also permit optimal extraction under the particular geological conditions encountered and also yield the largest net return (Luxbacher, G. W., and Kline, R.J., (1992). Although the mining methods resulting from the selection schemes are all technically feasible, their mining costs may be significantly different. The development costs for the three mining methods were calculated by first designing the mining methods using AutoCAD software.
4.2.1. Environmental Analysis
Environmental analysis involves the impact the mining method will have on the environment. Since the mine is located far from the communities (about 11km), and that the three mining methods would be used at depth for mining a remaining portion of a block, the impact on the environment will be limited.
5. Designs of the Mining Methods
All the three shortlisted mining methods were designed using the software AutoCAD and also following the development standards used at Baluba mine. Figure 4.3 shows the development profile with standard dimensions.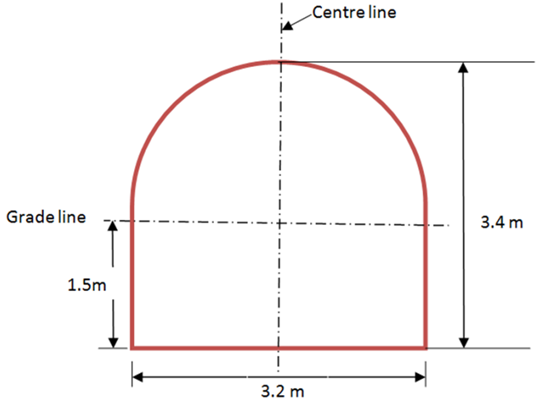 | Figure 4.3. Development profile |
5.1. Design for Sublevel Stoping
Figure 4.4 and figure 4.5 show the plan view and section view of the designed sublevel stoping method. The total number of development metres calculated from the design was 689.36m.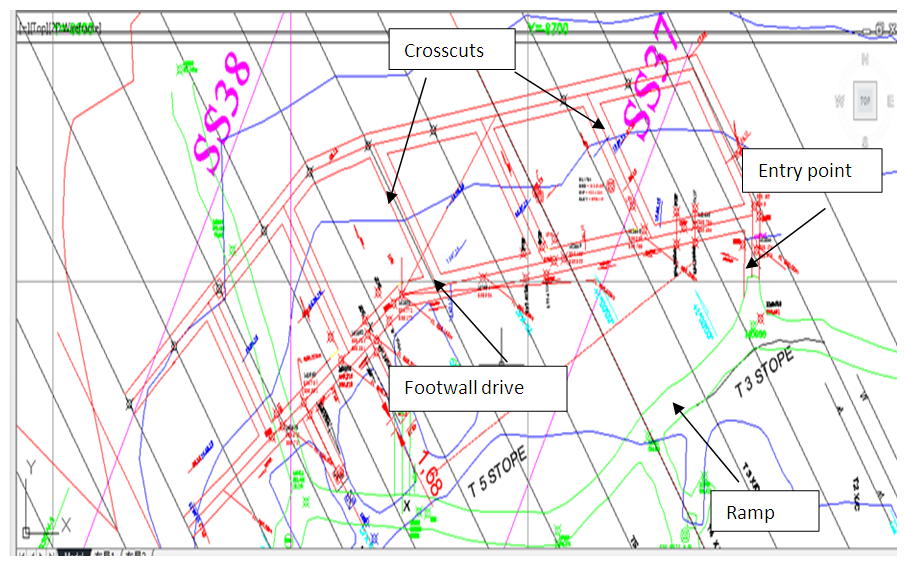 | Figure 4.4. Plan view of sublevel stoping design |
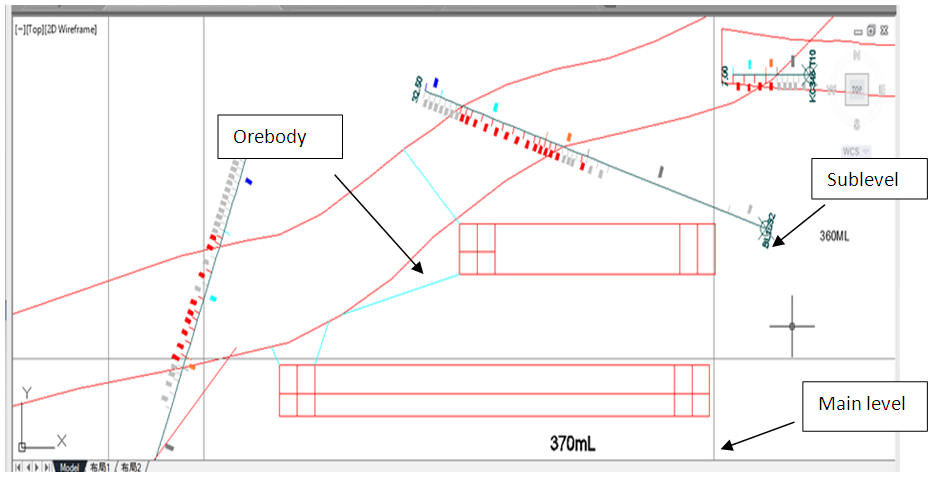 | Figure 4.5. Section view of sublevel stoping design |
5.2. Design for Cut and Fill
The plan and section views of above mining method are shown in figure 4.6 and 4.7 respectively. The total number of development metres was 457.56m.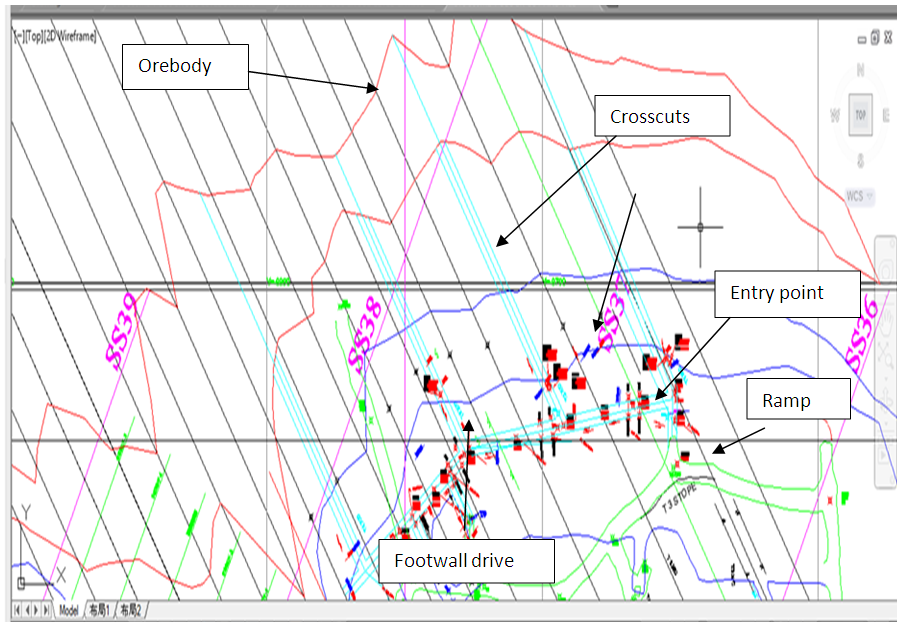 | Figure 4.6. Plan view of cut and fill design |
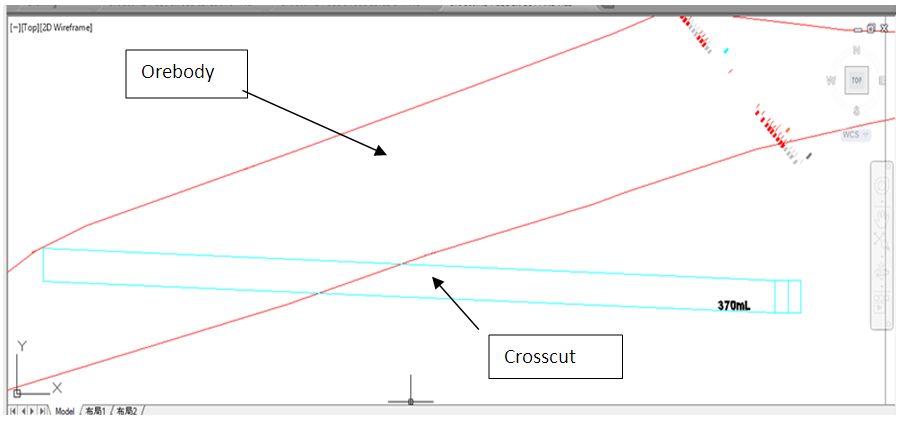 | Figure 4.7. Section view of cut and fill design |
5.3. Design for Sublevel Caving
For sublevel caving, a variant method called single level caving was designed due to the orientation of the orebody. Figure 4.8 shows the plan view of the design while the section view is shown in figure 4.9. The total number of development metres was 396.4m.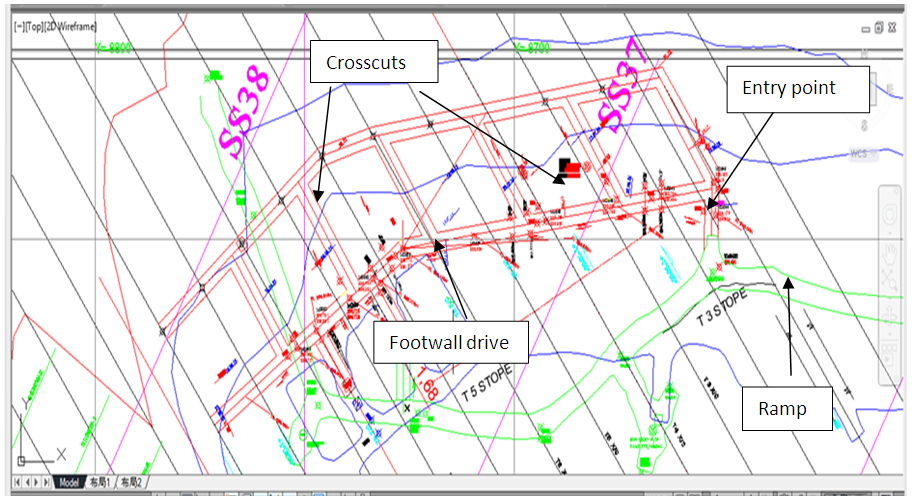 | Figure 4.8. Plan view of sublevel caving design |
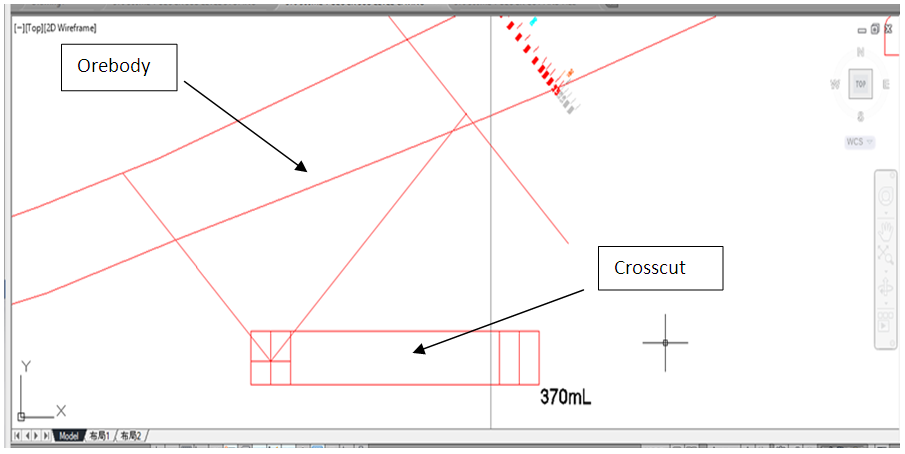 | Figure 4.9. Section view of sublevel caving design |
5.4. Calculations of Development Costs
The cost of development at Baluba mine is $ 1500 per metre. The following are the calculations of development costs for the three mining methods;Cost per metre = $ 1500Total development cost = total number of meters × $ 1500Sublevel stoping
Cut and fill
Sublevel caving
Based on the above calculations, it is evident that sublevel caving had the least development costs compared to sublevel stoping and cut and fill and consequently the mining method was selected despite not initially having scored the highest mark in terms of ranking.
5.5. Calculations of Tonnages
To calculate the total tonnages for both ore and waste, the strike length was multiplied with the average area and specific gravity using the formula below:
Where: T = tonnage; s = Strike length; A = Average area;
= Specific gravity.The average area and strike length were calculated using the software AutoCAD. While the specific gravity was that of the rocks at Baluba. Tables 4.1 and 4.2 show calculated tonnage of ore and waste respectively.Table 4.1. Total ore tonnages calculated  |
| |
|
Table 4.2. Total waste tonnages calculated  |
| |
|
5.6. Calculation of Total Cost, Revenue and Profit
The following information was used for calculating the total cost:- The cost of producing 1 tonne of finished copper = $ 3100/t- Total tonnage = 59259.02 t- Stope recovery = 85%- Milling recovery = 95%- Grade = 2.01 %
Calculation of revenue
Calculation of profit 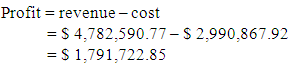
5.7. Calculation of Net Present Value (NPV)
NPV was determined from the following expression:
Where:
cash flow for the jth year J =1, 2, 3……n years i = rate of returnThis can also be expressed as follows:NPV =
- Initial InvestmentTaking i = 15 % n = 1 year
From the NPV criterion the calculated NPV is greater than 0 hence the project is accepted.
5.8. Calculation of Payback Period

Hence the payback period for the investment is approximately 6 months.
6. Conclusions
This study has shown that; Single level caving, which is a variant for sublevel caving is the most appropriate mining method for extraction of ore at 370ml because it meets the criteria of safety, flexibility and low cost. The variant of Sublevel caving (single level caving) had the lowest development costs after the three mining methods were designed and analysed. The total cost calculated for the project was $ 2,990,869.92 and the expected revenue is $ 4,782,590.77 and will produce a profit of $ 1,791,722.85. The NPV for the project was greater than 0 which means the projected is acceptable. Hence from the cost analysis conducted, it was established that the project is viable.
ACKNOWLEDGEMENTS
The author offers heartfelt gratitude to Management of Luanshya Copper Mines for facilitating the study.
References
[1] | Bradley, B.H.G. and Brown, E. T., (1993). Rock Mechanics for Underground Mining, 3rd ed., Chapman and Hall, London. |
[2] | Hartman, H.L., (1987) Introductory to Mining Engineering, John Wiley and Sons, New York. |
[3] | UBC Mining selection Tool (http://www.edumine.com/tools/mining-method-selection). |
[4] | Lewis, R.S., (1964) Elements of Mining, 3rd ed. John Wiley and Sons, London. |
[5] | Luxbacher, G. W., and Kline, R.J., (1992) Mine Planning and Design. SME Mining Engineering Handbook. pp. 1544 -1549. |
[6] | Nicholas, D. E., (1981) Method Selection-A Numerical Approach, Design and Operation of Caving and Sublevel Stoping Mines, pp. 39-51. |
[7] | Njamba, M. N., (2016). Design a mining method for the extraction of ore between 330ml and 400ml from SS 37 to SS 40 at Baluba east upper T-block, Report-Lusaka. |
[8] | Mutambo V.P, Fisonga S (2015). Mining Method Selection Tool, UNZA. |
[9] | Howard L. Hartman (1992) SME Mining Engineering Handbook. Second edition volume 1 PP 33-34. |
[10] | B.H.G. Brady and E.T Brown (2005). Rock mechanics for underground mining. Third edition, Kluwer publishers pp. 349 – 353. |
[11] | Nicholas, D. E., 1992. Selection mining method, SME Mining Engineering Handbook, Ed., Hartman, H. L., 2nd ed., Society for Mining Engineering, Metallurgy and Exploration, Inc: 2090-2106. |