Sunil Kumar Tripathy , V. Singh , Y Ramamurthy
Research and Development Department, Tata Steel Ltd., Jamshedpur, 831007, India
Correspondence to: Sunil Kumar Tripathy , Research and Development Department, Tata Steel Ltd., Jamshedpur, 831007, India.
Email: |  |
Copyright © 2012 Scientific & Academic Publishing. All Rights Reserved.
Abstract
About 40% of the Indian chromite ore reserves are suitable for metallurgical purpose due to higher Cr:Fe ratio. The present investigation emphasized on the liberation and beneficiation characteristics of Indian chromite oreto improve the Cr: Fe ratio. The off grade chromite sample ofSukinda region, India analysed 40.8% of Cr2O3 with Cr:Fe ratio of 1.7 and 5.8% of SiO2 which was not suitable for metallurgical industry. Detailed characterisation studies were carried out to predict the theoretical limits to improve the Cr/Fe ratio. Mineralogical investigation by using QEMSCAN studies revealed that chromite, hematite, goethite, Fe Silicates and kaolinite are dominating phases in the ore.Half of the Fe was present in the chromite spinel, whereas other 30% and 20% werereported from silicates and iron minerals, respectively. It was predicted from characterisation that, product can be enriched to 2.48 Cr:Fe ratio by discarding the silicate/locked silicate, Fe silicate gangue minerals whereas product quality can be upgraded maximum to 3.58 of Cr:Fe ratio by separating all iron bearing minerals. The beneficiation studies revealed that, the product can be enriched to having Cr:Fe ratio of 2.31 and 3.35 by gravity concentration (wet shaking table) and high intensity magnetic separation (Induced Roll Magnetic Separator) respectively. So the high intensity magnetic separator (Induced Roll Magnetic Separator) was suggested for the quality improvement of the off grade chromite ore ofSukinda region, India.
Keywords:
Chromite, Beneficiation, Mineralogy, Characterisation, QEMSCAN
Cite this paper:
Sunil Kumar Tripathy , V. Singh , Y Ramamurthy , "Improvement in Cr:Fe Ratio of Indian Chromite Ore for Ferro Chrome Production", International Journal of Mining Engineering and Mineral Processing , Vol. 1 No. 3, 2012, pp. 101-106. doi: 10.5923/j.mining.20120103.01.
1. Introduction
Chromite ore is the main source for chromium metal, chemical and refractory. Metallurgical usability of these ores depends on the Cr: Fe ratio besides the Cr content. Forty percentage of Indian chromite reserves are suitable for metallurgical use (Cr:Fe>2.8), 33% for refractory making (Cr:Fe of 2.8-1.8) and 27% for chemical industries (Cr:Fe <1.8)[1-2]. There is heavy demand for metallurgical grade chromite ore due to rapid growth of steel industry and limited availability of such high-grade ore resources. Hence, it has become imperative to improve the Cr/Fe ratio along with Cr content of low/medium grade ore resources[3-4]. Various attempts have been made to improve the Cr/Fe ratio of Indian chromite ores. The Cr/Fe ratio of chromite concentrate was investigated by Murthy et al. and found that it can be improved up to 2.8 by using wet high intensity magnetic separator or gravity concentration equipment such as wet shaking table[5]. The Cr:Fe ratio of the two off grade ferruginous chromite sample from India was improved from 1.85 to 3.0 and 10-30% recovery by high intensity magnetic separator[3]. The ultrafine fraction (below38μm) of tailing at Karagedic chromite concentrate of Turkey assaying 23% Cr2O3 was treated in wet high intensity magnetic separator and column flotation for producing the concentrate assaying 46-48% Cr2O3 with an recovery of 60-65%[6]. Similarly the magnetic separation technique was employed for Anka chromite ore which resulted improvement of Cr2O3 to 48% with Cr:Fe ratio of 6.2 from the feed assaying 36.84% Cr2O3[7]. Significant work has been reported in the literature to improve Cr:Fe ratio of the low/off grade chromite. A thorough physical, chemical, and mineralogicalcharacterization must precede the beneficiation of chromite ore to improve the Cr:Fe ratio. In most of the works reported above, the chromite samples were not relatively rich in Fe content. In the present study, chromite sample of low Cr:Fe ratio was taken up for detailed characterisation to predict the separation and subsequent beneficiation studies for validation.
2. Materials and Methods
2.1. Materials
The sample was collected from a typical chromite beneficiation plant of Sukinda region, India. The sample contain 40.75% of Cr2O3, 15.6% of total iron, 10.8% of alumina, 5.8% of silica, 10.7% of MgO, 3.4% of CaO, and 5.4% of loss on ignition (LOI). The material is of ferruginous in nature as it is having Cr/Fe ratio of 1.7.
2.2. Chromite Sample Characterisation
Characterisation studies were carried out to quantify the different mineral phases, their liberation and association with each other. The size analysis of the ore sample was carried out using wet vibratory laboratory sieve shaker. Size wise chemical analysis of the feed sample was carried out by ICP (Inductively Coupled Plasma)analyser. The X-Ray diffraction study was carried out to identify different mineral phases present in the feed sample. Sink and float studies of chromite sample were also carried out by using different organic liquids having specific gravity 2.8, 3.3 and 4.03 at different proportions. QEMSCAN (Quantitative Evaluation of Minerals by Scanning Electron Microscopy)is an automated advanced technique for the rapid characterisationof mineral species and relationships in polished samples byscanning electron microscopy with energy dispersive X-ray spectrometry (SEM–EDS). The technology iswidely used in the mining industry and is gaining increasing recognitionin other areas of research which gives the quantitative modal mineralogical data to trace mineral levels, calculated chemistry, mineralogical association and liberation data, elemental deportment with mineralogical map of the sample[8-9]. Similar studies were carried out by using mineral analysis to predict the performance of different operations[10-14]. Mineralogical characterisation of the chromite sample was carried out by using QEMSCAN 4300 and iExplore software used for data analysis.
2.3. Beneficiation Studies
Separation studies were carried out to validate the predicted result obtained from the advanced characterisation. Gravity separation studies were carried out using laboratory scale shaking table (laboratory model No. 15 S, supplied by M/s The Deister Concentrator Company Inc., USA). It has single deck of rectangular form with 350 x1000 mm, with linoleum as surface material. It is partially riffled, with riffles parallel to the deck motion. The riffles have 5 mm height on the feed end with decreasing height from the feed edge to the concentrate edge. The gap between riffles is 12 mm. The detail regarding the equipment along with experimental procedure was summerised in previous publication[15]. Wash water flow rate was varied by keeping the other variables such as solid concentration at 20% solids by wt., 15 mm of shake amplitude, 200cycles/min. of shake frequency, deck tilt angle of 4 degree and splitter position at 25 cm from the concentrate end were kept constant.A laboratory model induced roll magnetic separator (manufactured by Readings of Lismore, Australia) was used for the test work. The main process variable such as applied current was studied which maintain the magnetic field strength between the magnetic pole and the rotor whereas the other process variables such as roll speed of 120 RPM, feed rate of 150Kg/hr. and splitter position were kept constant. The results of beneficiation studies are discussed in the next section.
3. Results and Discussion
The results of the characterisation and beneficiation studies of the chromite sample are discussed in this section.
3.1. Characterisation Studies
The size distribution of the chromite sample was analysed and given in Figure 1. The feed material is of coarser in size range by varying between 850 to 75 μm. About 80% of total mass having the particle size below 300 μm and 50% is of less than 160 μm. About 25% of the material is having size below 75 μm. Result of the size wise chemical analysis of the feed sample is tabulated in Table 1. From Table 1, it is observed that at intermediate size fraction (250-37 μm), the concentration of Cr2O3 is maximum and lower value i.e. 33.5% is reported at finer size (<25 μm). Similarly the Fe content is minimum at intermediate size interval and highest reported at below25 μm size fraction. It can be noted that the Cr2O3 and Fe are present in inversely to each other at different size fractions which indicates the amenability of the separation of the gangue minerals. The alumina content is uniformly distributed at all size fractions whereas the silica content decreases with particle size.Table 1. Size wise chemical analysis of the chromite ore |
| Size (μm) | (%) Assay Value | Cr2O3 | Fe(T) | Al2O3 | SiO2 | >500 | 35.2 | 20.6 | 12 | 6.5 | 500-250 | 36.8 | 14.5 | 11.8 | 5.6 | 250-150 | 42.6 | 14.9 | 11 | 6.5 | 150-75 | 47.3 | 11.3 | 11.7 | 6.8 | 75-45 | 43.0 | 16.6 | 13.0 | 4.3 | 45-37 | 43.2 | 18.2 | 12.4 | 3.2 | 37-25 | 41.8 | 19.5 | 10.7 | 2.4 | <25 | 33.5 | 24.5 | 11.7 | 5.3 |
|
|
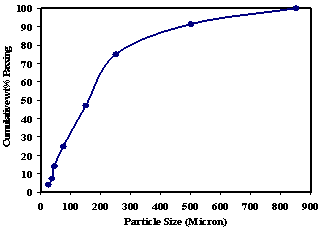 | Figure 1. Size analysis of feed samples |
XRD pattern of the chromite sample is presented in Figure 2 and the minerals are identified by X-Pert High Score software. From the Figure 2, it is observed that along with the chromite, different gangue minerals such as hematite, goethite, kaolinite, gibbsite, quartz are present in the sample.The sink fractions of the heavy liquid studies with different organic liquids by varying the density in between 2.8 and 4.03 was analysed and presented in Figure 3. From Figure 3, it can be observed that for achieving Cr:Fe ratio of more than 2.8, the Cr2O3 content should be higher than 50% in the product. It can be also presumed that the chromite sample contains huge amount of near density minerals such as goethite, hematite, etc.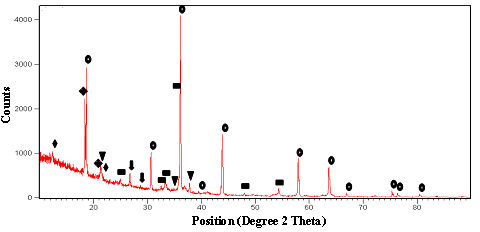 | Figure 2. Diffractogram of the chromite feed sample (: Chromite, ▄: hematite:: Kaolinite, : Gibbsite, ▼: Goethite, : Quartz) |
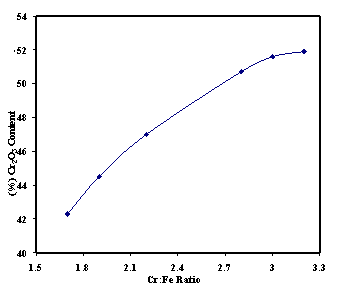 | Figure 3. Relation between grade (% Cr2O3) and Cr:Fe ratio of products |
3.2. Mineral Analysis by using QEMSCAN
The mineral characterisation study of the sample was carried by using QEMSCAN. The particle view and modal mineralogical analysis of the head sample are depicted in Figures4and5 respectively. It can be noted that, concentration of free chromite minerals is high in coarser fractions (>75μm) whereas free iron and silicates grains are more at size <25μm. Inverse relationship between chromite and iron in different sizes support the presence of iron in the form of different iron bearing minerals which showed that about 70% (by weight) of the sample was chromite particles whereas about 20% of the total mass was iron bearing minerals such as goethite 7%, hematite 3%, kaolinite 2% and iron bearing silicates (olivine, pigeonite, etc.) of 11%. Gibbsite and silicate minerals (quartz) are of 1%and 2% respectively. So, it is observed that 10% of the gangue minerals (hematite and goethite) are of near density minerals. 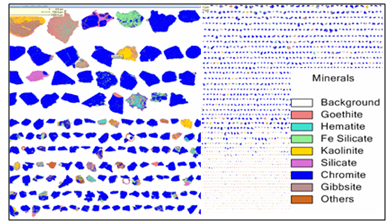 | Figure 4. Particle view of QEMSCAN studies |
The separation or beneficiation of the minerals is generally depending on the liberation of chromite and other gangue minerals. The main objective of the present investigation is to improve the Cr: Fe ratio of the product by separating iron bearing gangue minerals. In this context the presence of Fe in different mineral phases in the ore wasanalysed and presented in Figure 6 which envisaged that about 50% of the Fe reported from the chromite minerals and other 50% distributed in hematite, goethite and Fe silicate minerals. Chromite was deported in various different combinations of spinels of (Cr,Fe,Al,Mg and O. Cr2O3) in pure chromite varies between 48 to 61 %weight, Al2O3 is 7.10–15.09 %weight, whereas Fe2O3 is very low (0.03–3.20 %weight). The amount of RO to R2O3 varied within a narrow limit of 0.98–1.13, indicating that the chromite was chemically balanced. | Figure 5. Mineral composition of the chromite sample |
The liberation and mineralogical association study were analysed by using the iExplore software. It was evident that about 60% (by wt.) of the chromite are in the free liberated form whereas around 25% of chromite associated with iron silicate minerals. In case of iron rich minerals, hematite was majorly interlocked with goethite and about 25% with chromite; in turn the magnetic susceptibility of the iron bearing minerals decreased which could be difficult for the selective separation of iron bearing minerals from chromite. It is also noted that, very negligible amount (<5%) of hematite grains present in the free form. A minor quantity (each about 15%) of goethite is in the liberated form and interlocked with chromite. 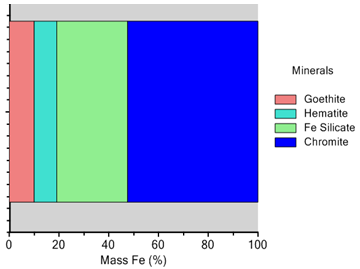 | Figure 6. Elemental deportment of Fe in different mineral phases |
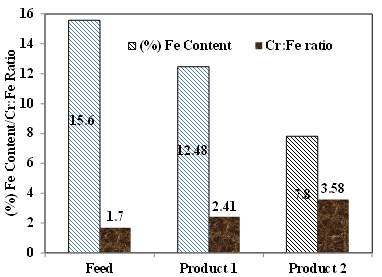 | Figure 7. Separation prediction of iron bearing minerals |
The iron present in the samples can be classified in three categories (a) free iron minerals (b) iron present in chromite minerals and (c) iron associated with gangue minerals. The most important was deportment of iron to improve the Cr/Fe ratio and reported that iron was deported in four major phases (goethite, hematite, Fe silicates and chromite). Half of the Fe was from the chromite spinal and remaining from the iron minerals as well as in iron silicates. From the characterisation studies, the separation of iron bearing minerals and the projected Cr:Fe ratio was predicted and shown in Figure 7. It is observed that, Fe content of the product (Product 1) can be reduced to 12.48% and correspondingly Cr:Fe ratio improved to 2.41 by discarding the silicate gangues and silicate bearing minerals such as olivine. Since the silicates and iron bearing silicates are having density less than 3gm/cc and also there is a difference in specific gravity of silicate bearing minerals and others, so the separation can be simulated by the gravity concentration. Similarly, all the iron bearing minerals are separated from the chromite than the Fe content of the product (Product 2) can be reduced to 7.8 and the Cr: Fe ratio was 3.58. The separation results can achieved by magnetic separation where iron bearing minerals and chromite particles separated by exploiting the magnetic susceptibility between the minerals.
3.3. Beneficiation Studies
It was evident from the detailed characterisation studies that, iron bearing minerals can be separated and consequently the Cr:Fe ratio of the chromite can increase. By keeping this as objective, test work was carried out in gravity concentration by using the wet shaking table and magnetic concentration by high intensity induced roll magnetic separator. The details of the test results are described further.It was found that the silica interlocked with iron mineral grainswhich can be separated from the higher density chromite minerals using the gravity separation methods. Wet shaking table (wilfley table) is a very basic unit operation which is carried out to evaluate the feasibility of gravity separation in mineral beneficiation. The result of the test work is depicted in Figure 8. From the beneficiation of the chromite ore by wilfley table, it is observed that the Cr2O3 can be improved to 48.9% from the feed assaying 40.8% with Cr: Fe ratio of 2.31. The Cr: Fe ratio has varied between 1.7 to 2.3 as there is an increase in the wash water flow rate. The recovery of Cr2O3 in the concentrate fraction is varied from 24.3% to 50.32%. The recovery (%Cr2O3) of concentrate has decreased as there is an increase in the wash water flow rate. It can be possible that the low density gangue minerals such as quartz, gibbsite, kaolinite, Fe silicates etc. having below density 3gm/cc. were effectively separated at this condition. But the major iron bearing minerals are reported to the concentrate fraction along with chromite due to its lower concentration criterion which results in poor Cr: Fe ratio. 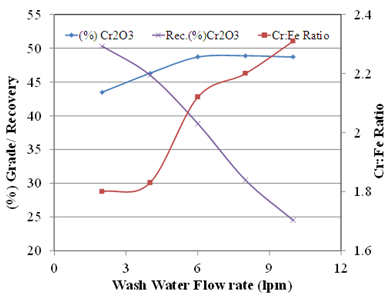 | Figure 8. Results of wet shaking table for chromite beneficiation |
Further improvement in the Cr/Fe is not possible using gravity separation methods. So, high intensity magnetic separation can be used to separate the liberated iron minerals and bring down the Fe as maximum possible.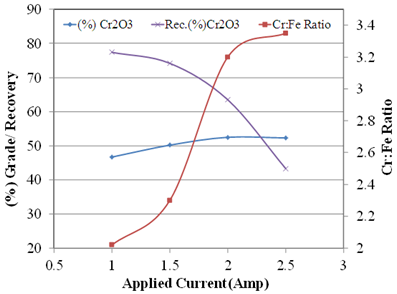 | Figure 9. Test results of magnetic separation by Induced Roll Magnetic Separator (IRMS) |
Magnetic separation utilises the magnetic susceptibility of minerals grains to separate from each other. As the chromite sample contains huge quantities of iron minerals as a gangue, magnetic separator can be utilised for the separation of iron bearing minerals from the chromite. The magnetic separation was carried out in a high intensity induced roll magnetic separator which is of dry high intensity type. The result of the test work on high intensity induced roll magnetic separator (IRMS) is shown in Figure 9. It is observed from the Figure that, the Cr2O3 content of the non-magnetic fraction is enriched up to 52.3%with recovery of 43.34% having Cr: Fe ratio of 3.35. It is observed that as the applied current increases, there is an increase in the grade as well as the Cr: Fe ratio of the nonmagnetic fraction. But beyond 2amp of applied current there is no upgradation in the Cr2O3 content because at higher magnetic intensity the chromite particles are also reported to the magnetic fraction due to its feebly magnetic in nature. It can also be noted that as there is an increase in the applied current, there is decrease in the recovery of %Cr2O3 to the non-magnetic fraction. So from the beneficiation studies on the off grade chromite ore revealed that, the Cr2O3 content can be upgraded to 48.9% with Cr:Fe ratio of 2.31 by gravity concentration whereas the product quality can be enriched to 52.3% Cr2O3 with Cr:Fe ratio of 3.35 by using magnetic separation technique.
4. Conclusions
The advanced characterisation and quality improvement study on chromite ore of Sukinda area, India was investigated to improve the Cr/Fe ratio. The Cr2O3 content is distributed maximum at intermediate size fractions but iron is distributed at coarser and finer fraction. X-Ray Diffraction and QEMSCAN studies revealed that, along with chromite, hematite, goethite, kaolinite, gibbsite, and quartz minerals were present in the ore. About 30% of iron (by wt.) was present in the form of iron silicates which are having low specific gravity and can be separated by gravity separation process. It was predicted from the characterisation that, the chromite ore can be enriched up to 2.48 Cr:Fe ratio by discarding the silicate/locked silicate, Fe silicate gangue minerals whereas product quality can be upgraded maximum up to 3.58 of Cr:Fe ratio by separating iron bearing minerals (hematite, goethite and iron rich silicates). Beneficiation studies revealed that, the product can be enriched to having Cr: Fe ratio of 2.31 with a grade of 48.9% Cr2O3 by gravity concentration (wet shaking table) whereas Cr:Fe ratio of 3.35 with 52.3% Cr2O3can be achievable by using high intensity magnetic separation (IRMS). So the high intensity magnetic separator (Induced Roll Magnetic Separator) can be used improve the quality of the off grade chromite ore of Sukinda region, India.
ACKNOWLEDGEMENTS
The authors are thankful to Tata Steel Ltd., management for all support, encouragement and permission to publish this work.
References
[1] | O P Varma and T Jaipuriar, “Chrome ore in India: Its strategic importance , domestic resources and gaps, long term projections and future outlook”, Symposium on Strategic minerals of India, Ujjain, India, Apr 20-22, 1973. |
[2] | Y Ramamurthy, S K Tripathy and C R Kumar, “Chrome ore beneficiation challenges & opportunities – A review”, Minerals Engineering, vol. 24, pp. 375–380, 2011. |
[3] | RBRao, BDasand S R SSastri, “Improving grade of Indian chromite ores by high-gradient magnetic separation,” Magnetic and electrical separation, vol.8, pp. 175-183, 1997. |
[4] | S K Tripathy and Y Ramamurthy, “Modelling and optimisation of spiral concentrator of spiral concentrator for separation of ultrafine chromite. Powder Technology,vol. 221, pp. 387-394, 2012. |
[5] | C VGKMurthy, R Sripriya and P VT Rao, “Enrichment of Cr/Fe ratio in chromite concentrate produced in chromite beneficiation plant at Tata Steel”, Trans. Indian Institute of Metals, vol. 47, no. 6, pp. 413-416, 1994. |
[6] | AGuney, GOnal, and TAtmaca, “New aspect of chromite gravity tailings re-processing”, Minerals Engineering, vol 14. no 2, pp. 1527 -1530, 2001. |
[7] | O KAbubakre,R A Muriana and P NNwokike, “Characterization and beneficiation of Anka Chromite ore using magnetic separation process”, Journal of Minerals &Materials Characterization & Engineering, Vol. 6, No.2, pp 143-150, 2007 |
[8] | RDPascoe, M R Power and B Simpson, “QEMSCAN analysis as a tool for improved understanding of gravity separator performance”, Minerals Engineering, vol. 20, pp.487-495, 2007. |
[9] | J D Grobler and J.B. Bosman, “Gravity separator performance evaluation using Qemscanparticle mineral analysis”, The 7th International HeavyMinerals Conference, The Southern African Institute of Mining and Metallurgy, pp. 91-98, 2009. |
[10] | IB Celik, N MCan and JSherazadishvili, ‘'Influence of Process Mineralogy on Improving Metallurgical Performance of a Flotation Plant”, Mineral Processing and Extractive Metallurgy Review, vol. 32: 1, 30 — 46, 2011. |
[11] | L M Santagostino, P RAlves, NShimabukurob, and TBBonas, ‘‘Applied mineralogy as a tool for mine planning of phosphate rock.’’ Minerals Engineering,vol. 14, pp. 1649–1657, 2001. |
[12] | D Sutherland, “Improving plant performance through process mineralogy’’, Cu ’98 –Australian Copper Forum, 1998. |
[13] | D A McCallum, W J Bruckard, M I Prownceby, “Chromite ore- characterisation through to processing”, Met Plant, AusIMM Conference, pp. 1-18, 2008. |
[14] | N O Lotter, A Di Feo, L J Kormos, D Fragomeni, G Comeau, “Design and measurement of small recovery gains: A case study at Raglan concentrator”, Minerals Engineering, vol. 23, pp. 567–577, 2010. |
[15] | S K Tripathy, YRamamurthy and V Singh, “Recovery of chromite values from plant tailings by gravity concentration”,Journal of Minerals and Materials Characterization & Engineering, vol. 10, no.1, pp.13-25, 2011. |