Riina Salmimies 1, Juha Kallas 2, Bjarne Ekberg 3, Antti Häkkinen 1
1LUT Chemistry, Lappeenranta University of Technology, Lappeenranta, 53850, Finland
2Laboratory of Inorganic Materials, Tallinn University of Technology, Tallinn, 19086, Estonia
3Outotec (Filters) Oy, Turku, 20630, Finland
Correspondence to: Riina Salmimies , LUT Chemistry, Lappeenranta University of Technology, Lappeenranta, 53850, Finland.
Email: |  |
Copyright © 2012 Scientific & Academic Publishing. All Rights Reserved.
Abstract
The upgrading of iron ore is a high-tonnage industry where cost efficiency plays an important role. Reducing costs of the filtration section can be done by the introduction of technology which results in decreased specific energy consumption. The use of the ceramic filter medium can offer this advantage. In addition, the filter medium can withstand chemical regeneration beyond that which a conventional filter cloth could, extending the time in operation of the filter elements. To regenerate the filter medium efficiently, the particular blinding processes need to be understood. This study offers new knowledge on the growth of scales in the dewatering of magnetite and hematite slurries. Whereas the magnetite process was highly affected by scale growth, only few observations of scaling were found for the hematite process. Three distinct stages of development of the scale were identified: (1) initial nucleation, (2) overlapping growth, and finally (3) complete solidification.
Keywords:
Iron Ore, Filtration, Scale Growth
1. Introduction
The filterability and several other aspects of the vacuum filtration of iron ore have been investigated earlier but little attention has, so far, been directed to the study of the interactions between the filter medium and different chemical components of the slurry. These interactions are, however, crucial in understanding long-term performance of the filter medium and can rarely be even qualitatively determined in laboratory scale[1]. Particle adhesion has commonly been thought to be the major mechanism resulting in performance decline of the filter medium and has actually been studied to a much further extent[2, 3, 4] than other mechanisms affecting the filter medium. The particles deposit onto the medium, blocking the pores and, consequently, decreasing filtration capacity and increasing cake moisture content. Especially in iron ore processing, where low and even cake moisture content is crucial for the following pelletisation, the performance of the filter medium is vital to achieving this goal.In addition to blocking by slurry particles, crystallisation of solutes during the cake drying process can introduce more adhesion between the particles and the filter media[5]. Besides blinding caused by slurry particles, other mechanisms of blinding, e.g. precipitation of solutes, are assumed to exist but have attracted little attention in the field of cake filtration.In fact, actual differentiation between particle adhesion and solute precipitation, and the significance of those mechanisms in industrial scale has, to the best knowledge of the authors, been rare. The fouling of different membrane materials has for long been of interest in cross-flow membrane filtration and several studies have been published on fouling of ceramic membranes by different chemical constituents[6, 7, 8] but, before the introduction of the ceramic filter medium through the use of the ceramic capillary action technology, has not been needed in high-tonnage cake filtration. The influence of different flocculants, used in copper concentration, on the filtration capacity has been published earlier for the ceramic filter medium[9] and has shown that the filter medium is indeed affected by different chemicals which cause blinding. Similar studies on iron ore have not been found by the authors.In the dewatering of iron ore, the filter medium is treated with backwash after each filtration cycle. In addition, chemical regeneration with ultrasound-assisted oxalic acid washing is employed. The needed frequency for the chemical regeneration depends on the application.Traditional cloth media are chemically and mechanically less stable and applying harsh regeneration methods would most likely damage the material. The cloth is periodically replaced and does not necessitate the understanding of elongated operating periods. In addition, because of significant air penetration of the cloth medium, large vacuum pumps need to be used to generate the driving force for filtration which in turn means high specific energy consumption. The requirement to decrease energy consumption is a powerful incentive to make use of novel filter media.The focus of this paper is to discuss the different stages of scaling of the filter medium through scanning electron microscopy (SEM) images.
2. Methods
Samples of ceramic filter medium used in the dewatering of magnetite and hematite slurries were characterized to obtain data on the scales formed in these dewatering processes. The actual characterisation data was collected by means of X-ray diffraction (XRD) and scanning electron microscopy coupled with energy dispersive X-rays. The XRD data was collected with a Bruker D8 Advance diffractometer from 10 to 90°2Θ with a step size of 0.02°2Θ. A Hitachi S3400 VP-SEM was operated at low vacuum, using a 15 kV acceleration voltage, with the backscatter detector to obtain images of the surface of the samples without coating them.The number of samples analysed from a magnetite dewatering process was 33. The samples were drawn from the central and peripheral areas of the large filter elements. The actual elements had been in use from three to five years. The corresponding number of hematite samples was 11 and was limited by the availability of filter elements from a hematite dewatering process. Exact time in operation was not available for the samples.Here, the emphasis is on the analysis of the SEM images and the details of the XRD data have been left out with the exception that the chemical components identified in the data have been included. In addition, statistical analysis, using principal component analysis (PCA), has been presented elsewhere[10] to identify trends in the data. The analysis has shown that the most significant determining factor in scaling is most likely the local variations in flow conditions. Scale growth is more significant on the peripheral area of the filter element whereas the centre is more likely to show particle adhesion in long-term operation. The observed difference has been suggested to result from differing flow conditions between the different parts of the full-size filter element.
3. Results and Discussion
3.1. Chemical Composition
The XRD analysis revealed the major chemical components in all the samples to be (1) aluminium oxide, which is the raw material for the filter medium, (2) magnetite and hematite corresponding the beneficiation processes, and (3) calcium scales. Several different calcium compounds, e.g. gypsum, calcite, and calcium oxalate, were identified in the samples from the magnetite dewatering process. The samples from the hematite dewatering process only showed gypsum.The different chemical components were easily identified by mapping the elemental composition with the EDS. The primary components, identified in the EDS mapping, were aluminium (Al), calcium (Ca), and iron (Fe). The EDS revealed the different elements to be distributed to different particles, as shown in Figure 1. In this case, the calcium compound was found to be calcium sulphate.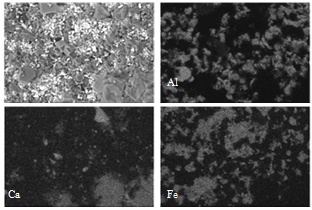 | Figure 1. EDS mapping, showing the distribution of Al, Ca, and Fe, of the surface of a ceramic filter medium used in the dewatering of magnetite |
3.2. Scale Growth
The most significant scaling component in the magnetite dewatering process was calcium oxalate. The growth of the scale can become quite significant and different stages of growth could be seen in the analysed samples. Initially, the scale had started to grow at random sites, as shown in Figure 2. 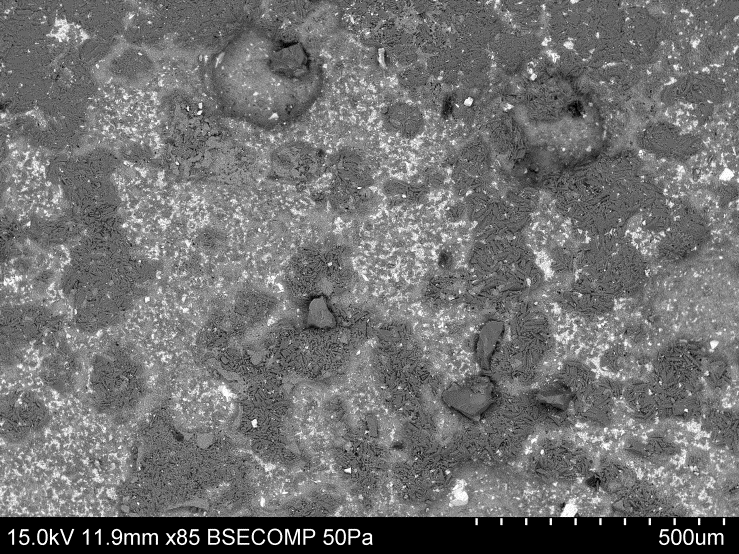 | Figure 2. Initial stages of scale growth, where crystallisation has begun |
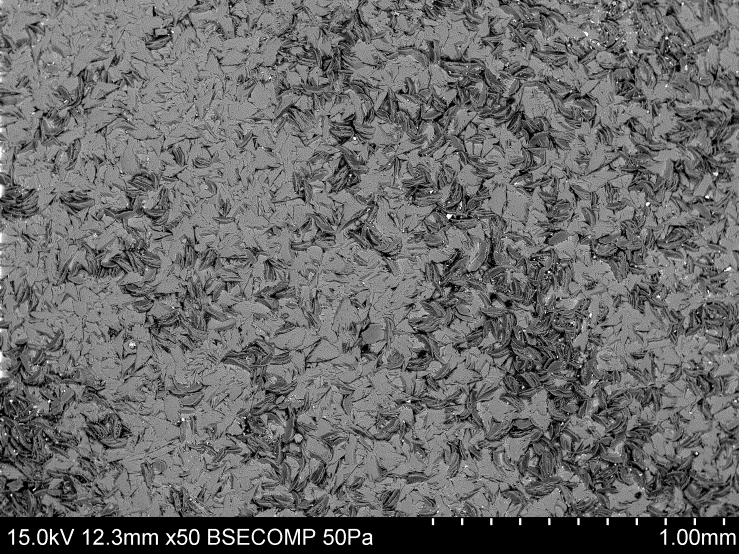 | Figure 3. Overlapping growth of the crystals |
The growth of the scale could have started at sites where the roughness of the surface has provided a nucleation point. Surface roughness could have been caused by the filter material itself or by slurry particles adhered to the surface.The crystals had continued to grow and started to overlap, forming a network with ridges, as in Figure 3.Although the overlapping of the crystals made it difficult to identify a specific shape for the crystals, closer investigations revealed the crystals to have the envelope-like shape corresponding to the morphology of calcium oxalate monohydrate crystals[11]. Finally, the layer had become so dense, that it seemed to solidify completely, forming a single plate-like structure on top of the surface, as in Figure 4.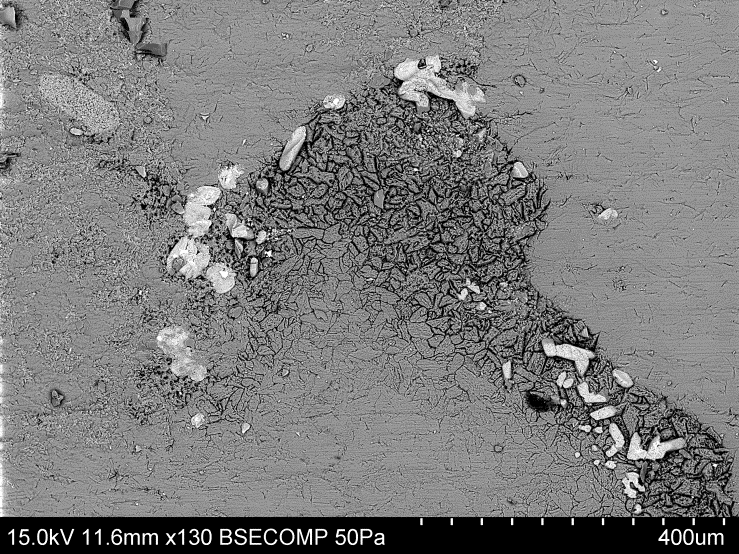 | Figure 4. The stage of solidification of the scale layer |
The central areas in Figure 3 show the scale still being fragmented whereas the areas surrounding it have already solidified.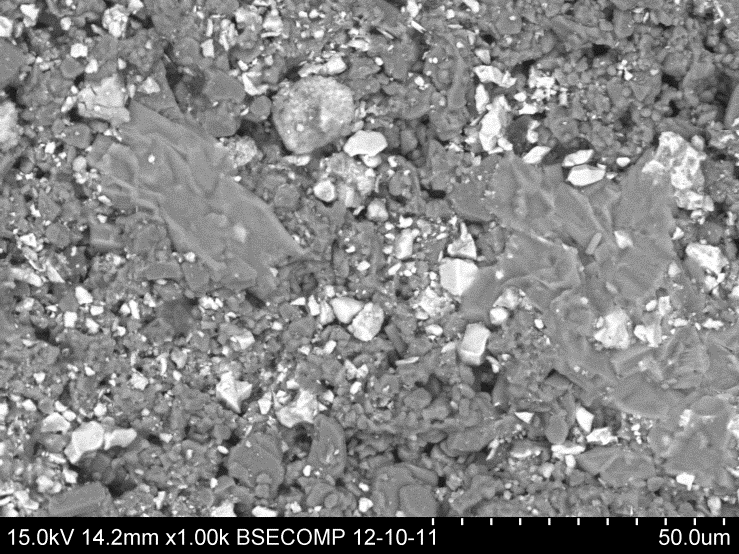 | Figure 5. Gypsum precipitation observed on the surface of the ceramic filter medium used in the dewatering of hematite |
Interestingly, the growth of the same scale, i.e. calcium oxalate, was not seen in the hematite process as in the magnetite process. In fact, scaling by any extraneous compounds was found to be insignificant in comparison to the magnetite dewatering process. The growth of gypsum was observed in the SEM images, as shown in Figure 5, but the observations were merely random and scaling by gypsum was not considered a major issue in the hematite dewatering process.No indication that the scaling would have different stages was found in the SEM images, as the number of observations of the scale was scarce altogether.
4. Conclusions
The significance of the filter medium in the vacuum filtration of mineral concentrates can not be overemphasised. Nevertheless, cake filtration studies are commonly focused on the filterability of different suspensions whereas those in crossflow filtration have recognised the importance of the study of the filter medium. Novel filter medium can provide benefits through energy economy and efficient use of the filter medium. The introduction of the ceramic filter medium to high-tonnage cake filtration has generated a need to understand the interactions between the filter medium and the slurry particles and different solution components of the liquid phase.Common chemicals used in upgrading iron ore include different acids and bases which can, together with elevated calcium content of different process streams, cause unexpected precipitation. In addition, oxalic acid, because of its efficiency in dissolving iron oxides, is used for the chemical regeneration of the filter medium and, again, together with poor quality process water can cause precipitation of the oxalate. The different scaling effects identified in this study are naturally more or less specific to the processes studied here because the nature and extent of any scale is very much determined by process chemistry and conditions. Low temperatures and the chemical components of e.g. process water are major factors which determine the tendency of precipitation of any chemical compounds. This study does, however, describe possible challenges faced in the dewatering of two major iron ore concentrates and thus can provide additional understanding to those in the industry.Differences in scale composition and extent of growth were observed when comparing the magnetite and hematite dewatering processes. Although the dewatering processes of these two ore concentrates are very much similar, the preceding process steps are not. Some distinct differences could explain the observations: (1) water recirculation resulting in the accumulation of calcium or (2) process chemistry contributing to the dissolution of different ore components. The recirculation of water is a desirable goal but the quality of the water is naturally highly dependent on the route through which the water comes into recirculation. If poor quality water is then used in the filtration section, precipitation can occur. Furthermore, the origin of the process water can vary significantly because the process of beneficiation is not the same for these two ores. Whereas the upgrading of magnetite can, to a large extent, be based on physical forces, e.g. magnetism, upgrading hematite can require the use of e.g. flotation where process chemistry becomes more significant.Whereas the chemical regeneration methods developed against iron oxide particle blockage are effective in dissolving magnetite and hematite, they are not targeted at the type of scaling identified here. Different methods of washing to reverse the calcium scaling could be employed to increase the performance of the filter medium. The washing would most likely not have to be as frequent as the current regeneration to dissolve iron oxides.The results presented in this paper show that the interactions between the filter medium and the different slurry and process components should be considered to make efficient use of the technological development of novel filter media.
ACKNOWLEDGEMENTS
The Graduate School of Chemical Engineering is kindly acknowledged for financing this work. The authors also wish to thank Outotec (Filters) Oy for providing the material without which this kind of research could never be possible.
References
[1] | W. Thompson, 1993, Continuous vacuum filtration: small scale tests versus full scale performance, Filtration and Separation, 30, 735-738. |
[2] | W.-M. Lu, K.-L. Tung, and K.-J. Hwang, 1997, Effect of woven structure on transient characteristics of cake filtration, Chemical Engineering Science, 52, 1743-1756. |
[3] | T. Weigert, and S. Ripperger, 1997, Effect of filter fabric blinding on cake filtration, Filtration and Separation, 34, 507-510. |
[4] | R. Wakeman, 2007, The influence of particle properties on filtration, Separation and Purification Technology, 58, 234-241. |
[5] | A. Rushton, A. Ward, and R. Holdich, Solid-liquid filtration and separation technology, 2nd ed., Wiley-VHC Verlag GmbH, 2000. |
[6] | R. Sondhi, Y.S. Lin, and F. Alvarez, 2000, Crossflow filtration of chromium hydroxide suspension by ceramic membranes: fouling and its minimization by backpulsing, Journal of Membrane Science, 174, 111-122. |
[7] | Y. Zhao, J. Zhong, H. Li, N. Xu, and J. Shi, 2002, Fouling and regeneration of ceramic microfiltration membranes in processing acid wastewater containing fine TiO2 particles, Journal of Membrane Science, 208, 331-341. |
[8] | Z. Zhong, W. Xing, X. Liu, W. Jin, and N. Xu, 2007, Fouling and regeneration of ceramic membranes used in recovering titanium silicalite-1 catalysts, Journal of Membrane Science, 301, 67-75. |
[9] | M. Mänttäri, M. Nyström, and B. Ekberg, 1996, Influence of flocculants on the performance of a ceramic capillary filter, Filtration and Separation, 33, 75-80. |
[10] | R. Salmimies, A. Häkkinen, J. Kallas, B. Ekberg, J.-P. Andreassen, B. Ralf, 2011, Characterisation of long-term scaling effects of ceramic filter medium used in the dewatering of iron ore, Proc., Iron Ore 2011, Perth, Australia, 521-527. |
[11] | A. Millan, 2000, Crystal growth shape of whewellite polymorphs: influence of structure distortions on crystal shape, Crystal Growth & Design, 1, 245-254. |