Marcos G. Vieira 1, Antonio E. C. Peres 2
1Mina do Germano, Samarco, Mariana, 35420-000, Brazil
2Department of Metallurgical and Materials Engineering, Universidade Federal de Minas Gerais, Belo Horizonte, 31270-901, Brazil
Correspondence to: Antonio E. C. Peres , Department of Metallurgical and Materials Engineering, Universidade Federal de Minas Gerais, Belo Horizonte, 31270-901, Brazil.
Email: |  |
Copyright © 2012 Scientific & Academic Publishing. All Rights Reserved.
Abstract
The influence of dosages of flocculants, dispersants and coagulants on the rheological behavior and state of aggregation and dispersion of an iron ore concentrate slurry was evaluated by determining the degree of dispersion using a settling tube, together with the analysis of flow curves obtained in a concentric cylinder rheometer. These curves were fitted according to models of Herschel-Bulkley and Bingham. The objective was to select reagents that promote a higher slurry thermodynamic stability, at pH 10 (pH used at SAMARCO’s regrinding circuit). These reagents would be evaluated later as grinding aids. None of the evaluated twenty reagents caused significant increases in the slurry’s degree of dispersion. Of the twenty selected reagents, six reduced the fluid consistency index (k coefficient) and apparent viscosity, at the dosage 300 g/t: three polyacrylic acids, silicone acrylate copolymer, citric acid and sodium hexametaphosphate.
Keywords:
Rheology, Iron ore Slurries, Dispersing Agents
1. Introduction
The comminution processes represent a challenge for the mining industry, since they present low mechanical efficiency and high energy consumption. SAMARCO’s regrinding stage corresponds to almost 50% of the energy consumption of its two concentrators. This stage reduces the particle size from 30% -44μm to 87% -44μm, and it is located between the mechanical flotation circuit and flotation columns circuit (recleaner).Some studies reported in the technical literature showed gains in grinding productivity with the use of certain dispersants (referred to as grinding aids). These reagents promoted the reduction of viscosity and/or yield stress, allowing a higher percentage of solids in the mill. This work aimed, in a first step, at selecting reagents that promote reduction of viscosity and/or yield stress at pH 10 (pH used in SAMARCO’s regrinding circuit) as well as contributing to the understanding of the effect of lime in the grinding process (lime is used as a coagulant in the slime thickeners, and the water is recirculated to the process).According to Klein[1], the physical and chemical properties of mineral suspensions determine how the particles interact among themselves and with the aqueous phase. The physical properties affecting the rheological behavior of mineral suspensions are: the solids content and the particles density, size distribution, and shape. The chemical properties affecting the rheological behavior are: pH, dissolved species, inorganic chemical additives (dispersants, coagulants), and organic chemical additives. The major types of interactions that contribute to the rheological properties are classified as hydrodynamic effects and aggregation effects, the magnitude of them being determined by the suspension physical and chemical properties.As a function of the types and magnitudes of the interactions among particulate and aqueous components, the suspensions may present one of the rheological behaviors described on figure 1.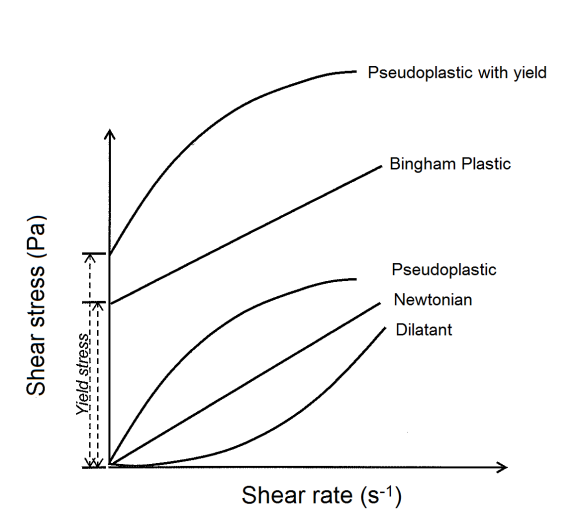 | Figure 1. Types of pulp rheological behavior |
The rheological properties may be described with the use of a simple empirical equation. Some simple equations are presented on table I. Klein[1] presented some considerations on the selection of the best model: (i) the equation must fit data over a wide range of shear rates; (ii) the equation must be simple, with the fewest number of coefficients; (iii) the coefficients must be easily determined; (iv) the coefficients must have physical significance.Table 1. Most common rheological models[1] 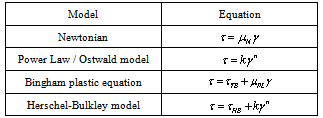 |
| |
|
The simplest model is the newtonian. The rheology is characterized by a single coefficient, the Newtonian viscosity
. Pseudoplastic and dilatant fluids are commonly modeled with the use of the Power Law (Darley and Grey[2]).The k coefficient is designated as the fluid consistency index and n is the fluid behavior index, related to the newtonian or non-newtonian suspension behavior. For n<1, the fluid is pseudoplastic. For n=1, the system is described by Newton´s equation: k=
. For n>1, the fluid is dilatant. For n<1, an increase in k values means an increase in the apparent viscosity and in the shear stress. Consequently, the aggregation of the particles in the suspension is enhanced. On the other hand, a decrease in k decreases the aggregation degree, the particles in the pulp are dispersed and the values of apparent viscosity and shear stress are lower. For n=1, changes in the k values do not affect the degree of dispersion of the particles in the suspension. The Bingham plastic equation is widely used. The yield stress,
, is the shear stress at which a straight line, passing through the shear stress – shear rate data intersects the shear stress axis and the plastic viscosity,
, is the slope of the line. The equation should be used cautiously, especially when there is limited low shear rate data, as it may be applied incorrectly to suspensions exhibiting shear thinning or yield shear thinning properties.
2. Methodology
The iron ore concentrate sample was composed by increments collected during 10 days from the concentrate thickener feed (Samarco´s concentrator I). A resulting pulp weighing 1,000 kg was dewatered, homogenized by conical piles and stored in 200 L drums. A riffles sample splitter was used to produce samples for the technological tests.The reagents selected for the experiments were: three poliacrylic acids (DPW 410, DPW 510, and DPW 610), sodium poliacrylate and phosphate (AG DISPER), three poliethelenimines (DPW 1210, DPW 1310, and DPW 1410), two amine polyvinyls (DPW 710 and DPW 810), three polyethylene oxides (DPW 910, DPW 1010, and DPW 1110), two acrylamide and sodium acrylate copolymers (Magnafloc 919 and Magnafloc 1011) and two polyacrylamides (Magnafloc 351 and Magnafloc 333), citric acid, sodium hydroxide, sodium hexametaphosphate, and lime.The flowsheet of the experimental procedure is illustrated in figure 2. 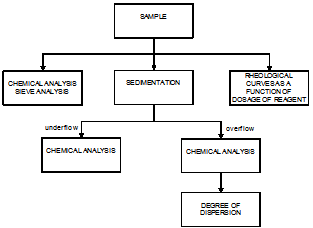 | Figure 2. Flowsheet of the experimental procedure |
The rheological curves were obtained with the use of a coaxial cylinder viscometer (BROOKFIELD, model R/S+, sensor CC3-45). The shear rate was decreased from 500 s-1 at 1 s-1, for 30 s, readings being taken at every second. The flow curves were adjusted with the use of Bingham and Herschel-Bulkley models. The pH was set at 10 for all experiments.All tests were conducted in duplicate and the model coefficients used to construct curves as a function of dosage of the reagents were obtained by the arithmetic mean of each duplicate.Table 2. Size Distribution and Chemical Analyses per Size Range |
| Size (µm) | Cumulative% passing | Fe (%) | SiO2 (%) | Al2O3 (%) | P (%) | LOI (%) | 74 | 97.91 | 57.15 | 12.04 | 0.88 | 0.075 | 5.03 | 53 | 90.15 | 65.80 | 1.87 | 0.42 | 0.056 | 3.39 | 44 | 85.17 | 67.06 | 1.02 | 0.31 | 0.044 | 2.59 | 37 | 80.44 | 67.30 | 0.93 | 0.29 | 0.040 | 2.38 | -37 | - | 67.15 | 1.00 | 0.40 | 0.040 | 2.38 | Calculated head | 66.72 | 1.42 | 0.40 | 0.046 | 2.57 | Analyzed head | 66.84 | 1.36 | 0.38 | 0.045 | 2.64 | Overflow for dispersion test | 65.75 | 1.64 | 0.51 | 0.053 | 3.16 | Underflow | 66.90 | 1.41 | 0.32 | 0.042 | 2.34 |
|
|
The effect of sedimentation was negligible due to three factors: (i) the use of the overflow obtained after three rounds of 5 minutes of settling (particles under 10µm, about 12% w/w); (ii) the use of a decrease ramp of shear rate rather than an increase ramp of shear rate; and (iii) just 30 seconds of readings.The dispersion degree was determined with the use of a sedimentation tube, described by Martins[3]. The pH was set at 10 and the reagents were dosed at 300 g/t, 600 g/t and 900 g/t. possible.
3. Results and Discussion
The size distribution and the chemical analyses per size range of the head sample used in the investigation are presented in table II. The contents of silica, phosphorus, alumina, and LOI are higher in the coarse fractions and the iron content is higher in the fine fractions.Figure 3 presents the dispersion degree, the coefficients k, n, and YS and the plastic viscosity as a function of the dosage and molecular weight of three poliacrylic acids (DPW 410, DPW 510, and DPW 610) and one sodium poliacrylate and phosphate (AG DISPER). A comparison between the effects of these reagents and the blank test indicates: (i) significant decrease in the k coefficient (related to viscosity and yield stress), stronger in the case of poliacrylic acids; (ii) trend to decrease in the yield stress (YS coefficient) and plastic viscosity; (iii) trend to a dilatant pulp behavior, observed from the increase in the n index; (iv) stronger decrease in k, YS, and plastic viscosity in the case of lower molecular weight poliacrylic acids, a trend reported by Klimpel and Hansen[4].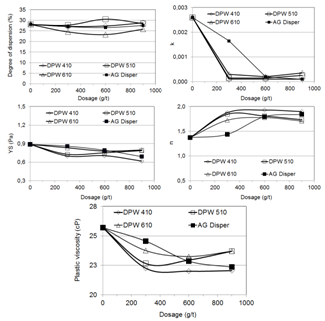 | Figure 3. Dispersion degree, Herschel-Bulkley’s equation coefficients, and plastic viscosity as a function of dosage and molecular weight of polyacrylic acids (DPW 410, DPW 510, and DPW 610) and dosage of sodium polyacrylate and phosphates (AG Disper) |
The decrease in the k, YS indexes and in the plastic viscosity is an indication of a higher level of thermodynamic stability or particles dispersion degree, despite the fact that the dispersion degree curves did not present significant changes. From this group of reagents, DPW 410 caused the major changes in the response parameters.Poliacrylic acids and their salts are among the most effective dispersants used in plant practice and laboratories[5, 6, 7]. Their dispersing mechanism is based on increasing and keeping a high negative charge at the electrical double layer.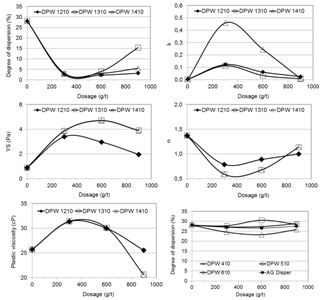 | Figure 4. Dispersion degree, Herschel-Bulkley’s equation coefficients, and plastic viscosity as a function of dosage and molecular weight of poliethelenimines |
Figure 4 presents the dispersion degree, the coefficients k, n, and YS and the plastic viscosity as a function of the dosage and molecular weight of three poliethelenimines (DPW 1210, DPW 1310, and DPW 1410). A comparison between the effects of these reagents and the blank test indicates: (i) increase in the state of aggregation of the particles in the pulp at the addition level 300 g/t, observed from the lower value of the dispersion degree and higher values of the coefficients of the Herschel-Bulkley and Bingham models (k, YS, and plastic viscosity); (ii) dilatant behavior for the higher aggregation degree condition; (iii) higher values of the k coefficient (related to higher viscosity and/or yield stress were achieved with the poliethelenimines presenting the highest molecular weight (DPW 1410); the three reagents led to similar values of the other indexes and dispersion degree. The poliethelenimines are polymers belonging to the class of the poliamines. As such, they are cationic species prone to adsorption onto the negatively charged particles of the iron oxides and quartz. As a consequence the electrostatic repulsion between the particles is reduced, causing the thermodynamic de-stabilisation of the system. Figure 5 presents the dispersion degree, the coefficients k, n, and YS and the plastic viscosity as a function of the dosage and molecular weight of two amine polyvinyls (DPW 710 and DPW 810). A comparison between the effects of these reagents and the blank test indicates: (i) decrease in the k index, stronger at the dosage 600 g/t; (ii) slight trend to increase of the yield stress (YS coefficient); (iii) decrease of the plastic viscosity at the dosage 600 g/t; (iv) similar flow curves for both reagents; (v) slight trend to aggregation shown in the dispersion degree curves in opposition to the trend of decrease in the k coefficient and the plastic viscosity.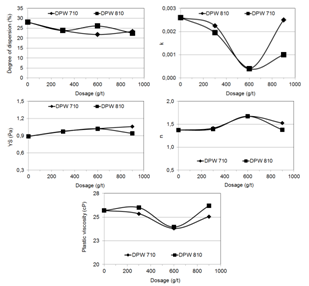 | Figure 5. Dispersion degree, Herschel-Bulkley’s equation coefficients, and plastic viscosity as a function of dosage and molecular weight of two amine polyvinyls (DPW 710 and DPW 810) |
The results did not indicate that the polyvinyls strongly promote the particles dispersion. It is possible that the cationic groups (NH3+) reduced the magnitude of the negative electrical charge of the particles surface enhancing the aggregation.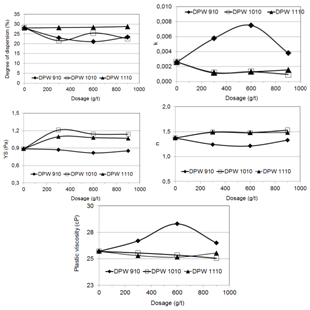 | Figure 6. Dispersion degree, Herschel-Bulkley’s equation coefficients, and plastic viscosity as a function of dosage and molecular weight of three polyethylene oxides (DPW 910, DPW 1010, and DPW 1110) |
Figure 6 presents the dispersion degree, the coefficients k, n, and YS and the plastic viscosity as a function of the dosage and molecular weight of three polyethylene oxides (DPW 910, DPW 1010, and DPW 1110). A comparison between the effects of these reagents and the blank test indicates: (i) the reagents DPW 1010 and DPW 1110 did not affect the rheological characteristics of the pulp; (ii) the reagent DPW 910 presented a trend to promote aggregation of the particles in the pulp indicated by higher values of the k index and the plastic viscosity).Ethoxylated and propoxylated polymeric surfactants are efficient dispersants for hydrophilic particles in the case of predominance of the steric dispersion mechanism[5, 6, 7]. Figure 7 presents the dispersion degree, the coefficients k, n, and YS and the plastic viscosity as a function of the dosage and molecular weight of two acrylamide and sodium acrylate copolymers (Magnafloc 919 and Magnafloc 1011) and two polyacrylamides (Magnafloc 351 and Magnafloc 333). The copolymers are anionic high molecular weight reagents, Magnafloc 919 possessing higher ionic charge. The polyacrylamides are non ionic high molecular weight reagents, Magnafloc 333 presenting the highest molecular weight. It was observed that: (i) the k and YS coefficients and the plastic viscosity were significantly increased, indicating a strong aggregation of the particles, due to a bridging flocculation mechanism; (ii) the dispersion degree of the particles decreased.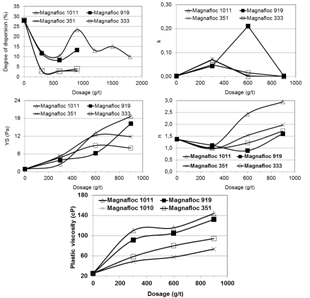 | Figure 7. Dispersion degree, Herschel-Bulkley’s equation coefficients, and plastic viscosity as a function of dosage and molecular weight of two acrylamide and sodium acrylate copolymers (Magnafloc 919 and Magnafloc 1011) and two polyacrylamides (Magnafloc 351 and Magnafloc 333) |
Figure 8 presents the dispersion degree, the coefficients k, n, and YS and the plastic viscosity as a function of the dosage of citric acid, sodium hydroxide, sodium hexametaphosphate, and lime. A comparison between the effects of these reagents and the blank test indicates: (i) the addition of citric acid and sodium hexametaphosphate reduced the k coefficient and the plastic viscosity, indicating enhanced thermodynamic stability of the system; (ii) the addition of 300 g/t sodium hydroxide to the pulp at the pH previously adjusted to 10 promoted a decrease in the k coefficient and in the plastic viscosity; (iii) higher dosages had an opposite effect, probably due to the saturation of reactive sites on the quartz and iron minerals surfaces, ceasing the specific adsorption and promoting a decrease in the dispersion degree, as reported by Brandão[5]; (iv) significant changes were not observed in the yield stress (YS coefficient).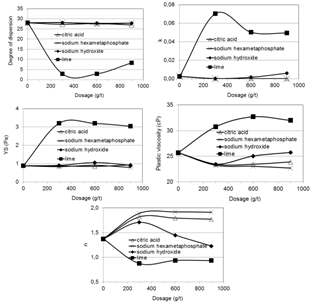 | Figure 8. Dispersion degree, Herschel-Bulkley’s equation coefficients, and plastic viscosity as a function of dosage and molecular weight of citric acid, sodium hydroxide, sodium hexametaphosphate, and lime |
Klimpel and Hansen[4] reported that the viscosity of a copper ore with silicate gangue is increased by NaOH addition levels of 400 g/t or higher. Sodium phosphates adsorb onto mineral particles via hydrogen bonds, van der Waals bonds or covalent type chemisorption[5, 6, 7]. The major dispersion mechanism is increasing and keeping a high negative charge at the electrical double layer. Citric acid presents the ideal chemical structure for an aqueous medium dispersant (by ionization, one or more carboxyl groups adsorb onto the particle, creating a medium or high interfacial electrical charge and orienting one or more hydroxyl groups towards the solution, characterizing a solvation contribution).Silva[8] developed studies on the aggregation state of iron ore suspensions. The major findings of his investigation were: (i) sodium hexametaphosphate was the most efficient inorganic dispersant, in the pH range above 7, in comparison with sodium metasilicate, sodium silicates (SiO2 : Na2O = 2.15, SiO2 : Na2O = 3.25), and borax; (ii) the dispersant action of citric acid was stronger than that of other organic reagents, such as Cataflot P40 and polycarboxylic acid; (iii) zeta potential determinations of quartz and iron oxide in the presence of 400 g/t citric acid and 300 g/t sodium hexametaphosphate showed an increase in the negative surface charge. The effect was more pronounced in the case of hexametaphosphate, in agreement with the reduction of the plastic viscosity observed in the figure 8.
4. Conclusions
The dispersion degree determination with the use of a sedimentation tube combined with the analysis of flux curves and the coefficients of the Herschel-Bulkley’s and Bingham’s models is adequate to describe the pulp rheological behavior under different aggregation and dispersion conditions.None of the twenty reagents evaluated in the investigation promoted significant increase in the dispersion degree of the pulp with the pH previously adjusted to 10. Five reagents promoted reduction of the fluid consistency index and the plastic viscosity at the dosage 300 g/t: three polyacrylic acids (DPW 410, DPW 510, and DPW 610), citric acid, and sodium hexametaphosphate. The dosage increase to 600 g/t and 900 g/t did not change significantly the flux curves. The lowest molecular weight polyacrylic acid (DPW 410) was more effective than the other reagents of the same family regarding the reduction of plastic viscosity, yield stress, and fluid consistency index.
References
[1] | B. Klein, Rheology of mineral suspensions. Lecture Notes. Vancouver, Canada: Department of Mining Engineering UBC, 2002. |
[2] | H.C.H., Darley, and G.R. Grey, “Rheology of drilling fluids”. In: Composition and properties of drilling and completion fluids. Gulf Publishing Company, chapter 5, pp. 184-261, 1988. |
[3] | Martins, L., Pereira, C.A., Galery, R., and Peres, A.E.C., 2010, Dispersion role on an oxidized zinc ore flotation., Minerals and Metallurgical Processing, 27(1), 34–41. |
[4] | Klimpel, R.R., and Hansen, R.D., 1989, The chemistry of mineral slurry rheology control grinding aids., Minerals and metallurgical Processing, 6 (1), 35-43. |
[5] | Gebhardt, J.E., and Fuerstenau, D.W., 1983, Adsorption of polyacrylic acid at oxide-water interfaces., Colloids and Surfaces, 7, 221-231. |
[6] | Ravishankar, S.A., Pradip, Khosla, N.K., 1995, Selective flocculation of iron oxide from its synthetic mixtures with clays: a comparison of polyacrylic acid and starch polymers., International Journal of Mineral Processing, 43, 235-247. |
[7] | Ma, M., 2011. Effect of a low-molecular-weight polyacrylic acid on the coagulation of kaolinite particles. International Journal of Mineral Processing, 99, 17-20. |
[8] | G.M.A. Silva, “Study on the aggregation state of iron ore suspensions”, M.Sc. thesis, CPGEM UFMG, Belo Horizonte, Brazil, April 1994. (in Portuguese). |