Mohammad E. Matarneh
Department of Mechanical Engineering, Al-Balqa Applied University, Al-Huson University College, Jordan
Correspondence to: Mohammad E. Matarneh, Department of Mechanical Engineering, Al-Balqa Applied University, Al-Huson University College, Jordan.
Email: |  |
Copyright © 2016 Scientific & Academic Publishing. All Rights Reserved.
This work is licensed under the Creative Commons Attribution International License (CC BY).
http://creativecommons.org/licenses/by/4.0/

Abstract
The purpose of this work was to study the effect of varying treatment temperature on the kinetics of carbon diffusion during steel Austenitization on H-13 hot work, tool steel mechanical properties. Samples made of H-13 steel were subjected to heat treatment at four different temperatures; 1000, 950, 900, and 850 °C. Samples treated with the highest temperature had the highest fracture resistance in the impact loading test, highest hardness in the hardness test, and highest resistant to plastic deformation in the tensile test. These results indicated that the highest treatment temperature yielded the best improvement in mechanical properties.
Keywords:
H-13 tool steel, Martensitic, Austenitization, Heat treatment, Rockwell Hardness test, Tension test, and Charpy impact test
Cite this paper: Mohammad E. Matarneh, The Effect of Austenitization Treatment Temperature on H-13 Tool Steel’s Mechanical Properties, International Journal of Mechanics and Applications, Vol. 6 No. 4, 2016, pp. 77-82. doi: 10.5923/j.mechanics.20160604.03.
1. Introduction
Austenitization is a group of industrial and metal working processes used to alter the physical, and sometimes chemical, properties of a material. The most common application is metallurgy. Austenitization techniques include annealing, case hardening, precipitation strengthening, tempering and quenching. It is noteworthy that while the term Austenitization applies only to processes where the heating and cooling are applied intentionally for the specific purpose of altering properties, heating and cooling often occur incidentally during other manufacturing processes such as hot forging or welding.This process is of interest in many industrial fields because heat treatment improves the mechanical properties of metals in various applications. For example in die-extrusion aluminum forming, process efficiency and product quality is highly dependent on the die which is made from tool steel. The die must undergo a series of heat treatment processes to obtain specific properties. Because an extrusion die covers around 35%-50% of the total manufacturing cost [1], it is essential to obtain a thorough understanding of both the kinetics and efficiency of die heat treatment in order to achieve superior, quality controlled, and precise process design.Tool steel refers to a group of carbon and alloy steels that are particularly well-suited to be made into tools. Their suitability is a result of their distinctive hardness, resistance to abrasion and deformation, and their ability to hold a cutting edge at elevated temperatures. The presence of carbides in their matrix plays the dominant role in the qualities of tool steel. As a result, tool steels are suited for use in the shaping of other materials with carbon content between 0.5% and 1.5%. Chemical composition of H-13 tool steel H-13 type of steel is identified by the suffix of H as indicated in the American Iron and Steel Institute (AISI) standard. H-13 is chromium type hot work tool steel used in medium extrusion die forging, plastic, nonferrous injection molding cavities, and all type of dies in hot work shock involving applications. Table 1 shows the elemental composition of H-13 steel.Table 1. Elements found in the of H-13 steel 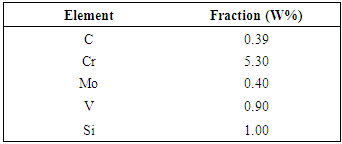 |
| |
|
H-13 is a type of steel alloy were a certain amount of chromium replaces iron to form carbide, which can prevent decarburization by fixing carbon as carbide, which have a high chemical potential [2]. Research shows that an addition of 1% chromium will result in a steel 10.5 MP stronger than normal steel (with the same carbon content), with a slight increase in toughness [3]. Chromium content induced toughness increases the decarburization resistance. Nevertheless, significant decarburization can still be found on heat treated H-13 steel, if the heat treatment was properly controlled [4].In a recent study, Siddiqui [5] showed decreased toughness and increased hardness with increased temperature for steel. Guanghua and Xinmin [6] state that the quenching temperature should be lower than 1080 °C in order to obtain minute grains. Gui and Wang [7] state that H-13 steel wear pattern will change at certain temperatures, steel treated at 600-650°C had a lower wear rate compared to steel treated at 700°C. Bahrami and Anijdana [8] found that samples with Martensitic structure had the highest wear resistance at a low load level of 29.4 N.The purpose of the work presented here was to investigate the effect of heat treatment temperature on the strength, hardness, and impact toughness of H-13 steel, and to develop a reasonable heat treatment process guide to be used in industrial production processes. For that, standard specimens underwent Austenitization at different temperatures, and then their mechanical properties were tested with standard hardness, impact and tensile tests.
2. Procedures
Sample PreparationH-13 samples with the size of 10×10×2.5 mm3 were cut in a flat shape, with their initial hardness measured (referred to as original samples). Two equal section samples where used: one for determining the characteristic of H-13 and one for the tests. Each section was put through the heat treatment process. All samples were subjected to surface preparation process before any metallographic analysis.Heat TreatmentHeat treatment is a process consisting of four main stages: preheat cycle, Austenite formation stage, quenching, and finally tempering. The target of heat treatment is to harden the material by changing the structure from Austenite, which is large, edge-shaped, coarse, and irregular structure to Martensite, which is fine grain structure of hardened carbide.Hardness TestThe Rockwell hardness test method, used in this work, consists of indenting the test sample material with a diamond cone or hardened steel ball indenter. The indenter is forced into the test material under a preliminary typical minor load (F0) of 10 kgf, as shown in Figure 1A. When equilibrium has been reached, an indicating device, which follows the movements of the indenter and so responds to changes in depth of penetration of the indenter, is set to a datum position. While the preliminary minor load is still applied an additional major load is applied with a resulting increase in penetration, as shown in Figure 1B. When equilibrium is reached again, the additional major load is removed while the preliminary minor load is maintained. Removal of the additional major load allows a partial recovery, thus reducing the depth of penetration, as shown in Figure 1C. The permanent increase in depth of penetration, resulting from the application and removal of the additional major load is used to calculate the Rockwell hardness number. | Figure 1. Working principle of the Rockwell test |
Tension/Tensile TestTension test is widely used to provide basic design information on the strength of materials and it is used as an acceptance test for material specification. The major parameters that describe the stress-strain curve obtained during the tension test are the tensile strength (UTS), yield strength or yield point (σy), elastic modulus (E), percent elongation (∆L%), and the reduction in area (RA%). Toughness, Resilience, Poisson’s ratio can also be found by the use of this testing technique.Loading rate can be set depending on the desired time to fracture. A tensile load is applied to the sample until it fractures. During the test, the load required to make a certain elongation in the material is recorded. A load- elongation curve is plotted by an x-y recorder, so that the tensile behavior of the material can be obtained. An engineering stress-strain curve can be constructed from this load-elongation curve by making the required calculations. Then the desired mechanical parameters can be evaluated by studying the aforementioned curve. Engineering Stress is obtained by dividing the load by the original area of the cross section of the sample:
Engineering stress and strain are independent of the geometry of the specimen. Elastic Region: The part of the stress-strain curve up to the yielding point. Elastic deformation is recoverable. In the elastic region, stress and strain are related to each other linearly:
The linearity constant E is called the elastic modulus which is specific for each type of material. Plastic Region: is the part in the stress-strain diagram after the yielding point. At the yielding point, the plastic deformation begins. Plastic deformation is permanent. At the maximum point of the stress-strain diagram (UTS), necking starts. Tensile Strength is the maximum stress that the material can support.
Because the tensile strength is easy to determine and reproduce property, it is useful in identifying the exact specifications of a product and for quality control purposes. Extensive empirical correlations between tensile strength and properties such as hardness and fatigue strength are often quite useful. For brittle materials, the tensile strength is a valid criterion for design.Ductility is the degree of plastic deformation that a material can withstand before fracture. A material that experiences very little or no plastic deformation upon fracture is termed brittle. It can be expressed either in terms of percent elongation (z) or percent reduction in area (q):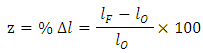
Resilience is the capacity of a material to absorb energy when it is deformed elastically. Toughness is a measure of energy required to cause fracture. Poisson’s Ratio is the lateral contraction per unit width divided by the longitudinal extension per unit length.Tension test is carried out to obtain the stress-strain diagram, to determine the tensile properties, and to consequently obtain valuable information about the mechanical behavior of the material in engineering applications.Impact testThe Charpy impact test (also known as the Charpy V-notch test) is a standardized high strain-rate test which determines the amount of energy absorbed by a material during fracture. This absorbed energy is a measure of a given material's notch toughness and acts as a tool to study the temperature-dependent ductile-brittle transition. It is widely applied in industry, since it is easy to prepare and conduct, with quick and cheap obtained results. A disadvantage is that some results are only comparative [9].
3. Results and Discussion
Tensile Test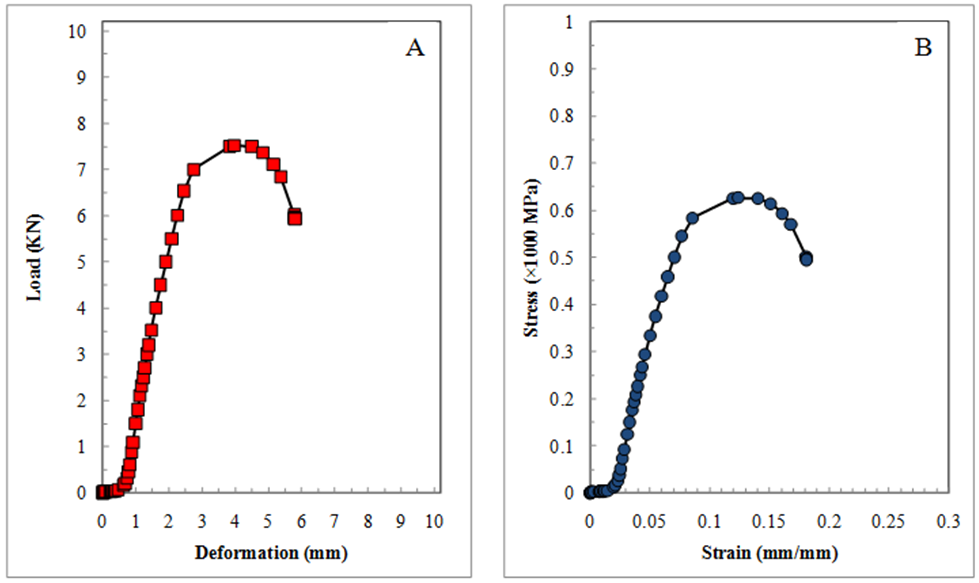 | Figure 2. Applied force vs. deformation (A) and stress-strain curve (B) for the original H-13 sample |
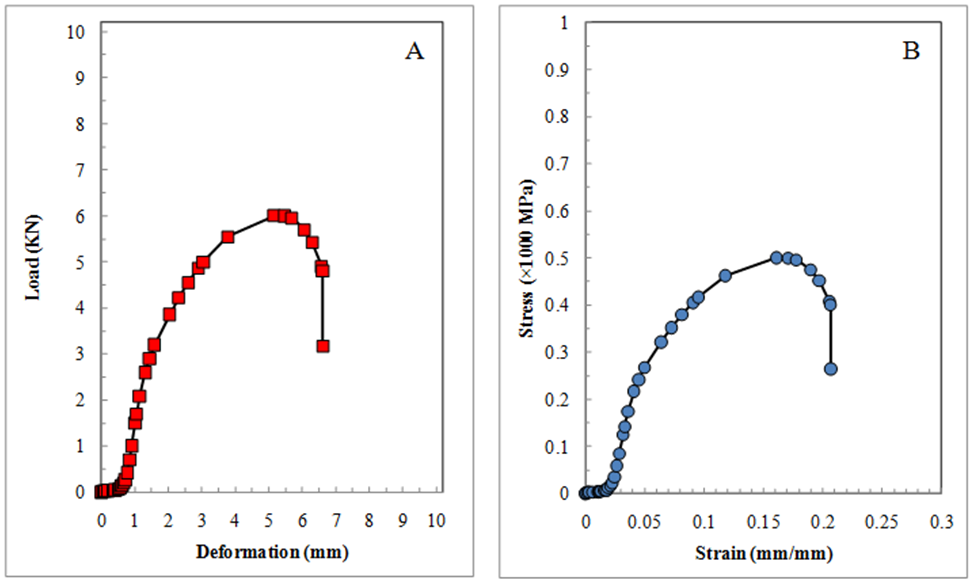 | Figure 3. Applied force vs. deformation (A) and stress-strain curve (B) for the 850° C treated H-13 sample |
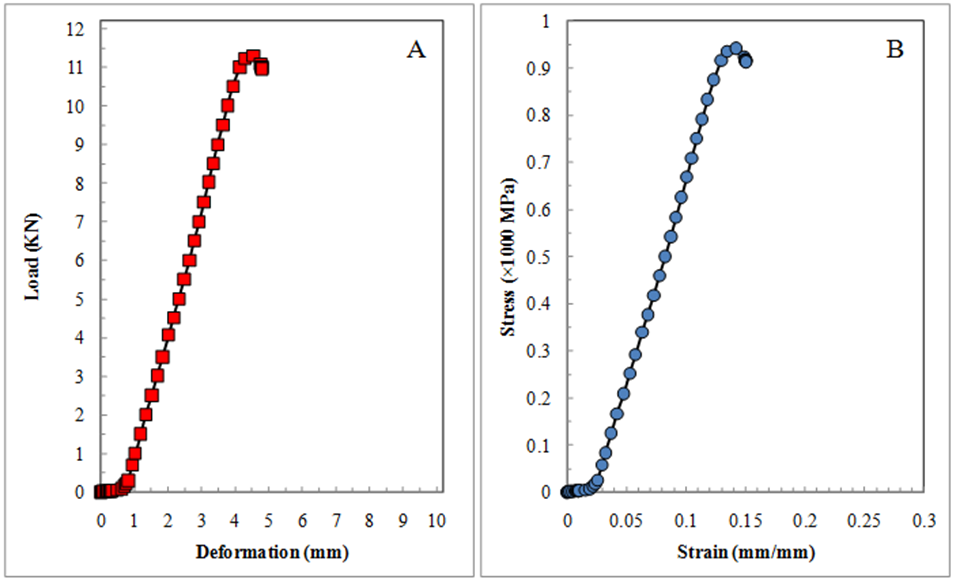 | Figure 4. Applied force vs. deformation (A) and stress-strain curve (B) for the 900 °C treated H-13 sample |
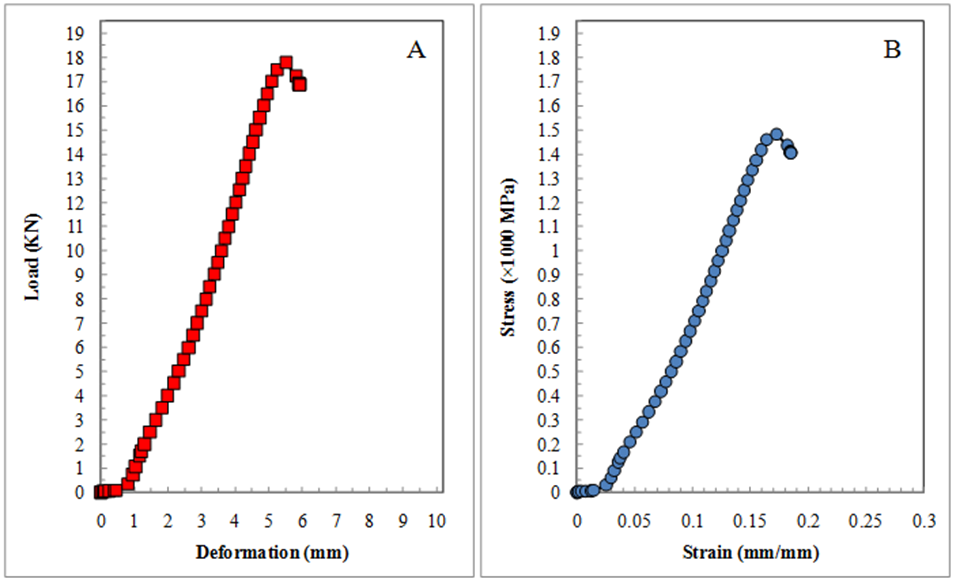 | Figure 5. Applied force vs. deformation (A) and stress-strain curve (B) for the 950°C treated H-13 sample |
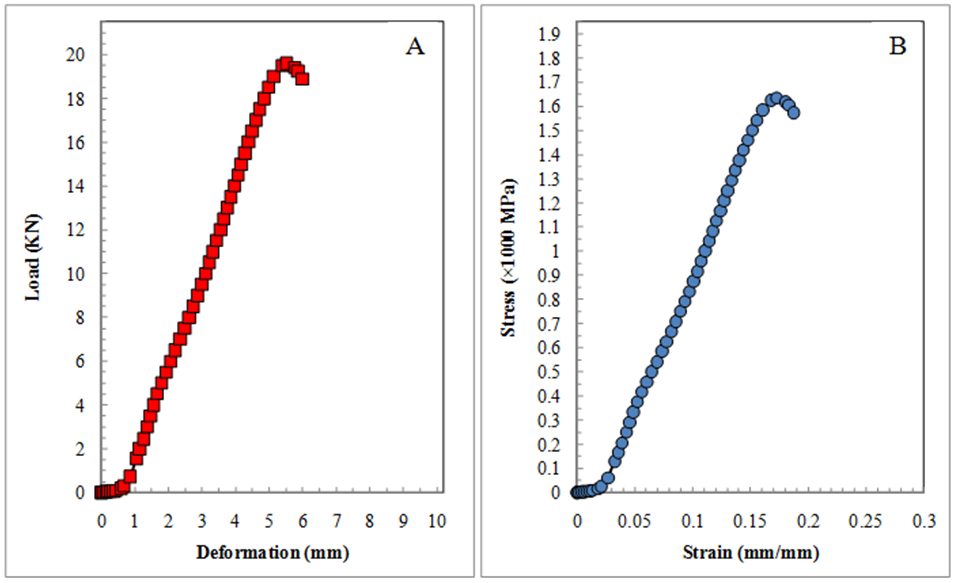 | Figure 6. Applied force vs. deformation (A) and stress-strain curve (B) for the 1000°C treated H-13 sample |
Impact testTable 2 shows the result of impact test for the original, 850, 900, 950, and 1000°C temperature-treated samples.Table 2. Impact test results for all samples 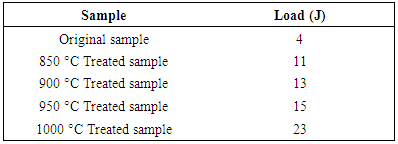 |
| |
|
Hardness TestTable 3 shows the result of hardness test for the original, 850, 900, 950, and 1000°C temperature-treated samples.Table 3. Hardness test results for all samples 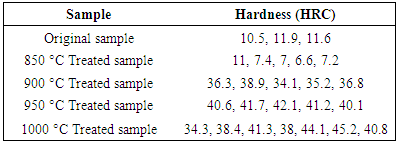 |
| |
|
Tensile TestTable 4 shows the result of tensile test for the original, 850, 900, 950, and 1000°C temperature-treated samples.Table 4. Tensile test results for all samples 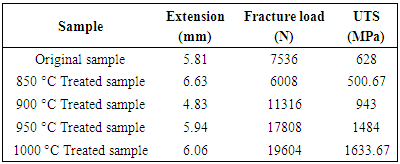 |
| |
|
As seen in the tables, the 850°C heated H-13 sample ability to withstand load was less than the original sample ability. The plastic deformation range was reached at 500.67 MPa, while fracture occurred at 6008 N. In contrast, the 900°C heated H-13 sample ability to withstand load was more than the original sample ability. The plastic deformation range was reached at 943 MPa, while fracture occurred at 11316 N. Similarly, both the 950 and 1000°C heated H-13 samples abilities to withstand load were significantly higher compared to the original sample ability. They reached the plastic deformation range at 1484 and 1633.67 MPa, respectively, while fracture occurred for both at 17808 and 19604 N, respectively. Impact test results showed the resistance of the sample material to fracture under impact loading, and under quickly applied dynamic loads. Among the heated H-13 sample, the 1000°C treated sample endured the highest load, followed by the 950, 900, and 850°C treated H-13 samples. The original sample had the lowest endurance to the impact load. In the hardness test, hardness reached 45.2 HRC, while the 950, 900, and 850°C treated H-13 reached 42.1, 38.9, and 11 HRC, respectively.
4. Conclusions
Three main conclusions can be drawn from this work: First, the impact test showed that the 1000°C treated sample had highest resistance to fracture under impact loading. Second, hardness test showed that the 1000°C treated sample was harder than the original sample, and other treated samples. Third, tensile test showed that the 1000°C treated sample withstand the plastic deformation more than the original and other treated samples.
References
[1] | Yi Zhong, Zai Xian, Han Sheng, Qui Ngan, Xiao Ping, Effect of heat treatment on properties and microstructure of H-13 tool steel. Journal of Northeastern University (Natural science). 1996. |
[2] | Brown AF, Hayes DJ. Observations on the decarburisation and graphitisation of steels by sodium. Journal of Nuclear Materials. 1968. |
[3] | Abbott RR. Modern steels and their heat treatment. Journal of the Franklin Institute. 1915 April 1915. |
[4] | Yong-an Min, Xiao-chun Wu, Rong Wang, Lin Li, Xu L-p. Prediction and analysis on oxidation of H13 Hot Work Steel. Journal of Iron and Steel Research. 2006. |
[5] | Siddiqui, R.A. (2009) Effect of heat treatment on mechanical proprieties of H-13 steel. |
[6] | Guanghua Y, Xinmin. H, Yanquing. W, Xingguo. G, Ming. Y, Zuoming. C, Kang. J, (2010) Effect of heat treatment of mechanical properties of H-13 steel. |
[7] | Cui X, Wang H, Wei S, Yang Z.R, (2010) wear characteristic and mechanisms of H-13 steel with various tempred strecture ASM international. |
[8] | Bahrami A, Mousavi Anijdom S.H, Golozor M.A, Shananian M, Varahram N, (2004) Effect of conventional heat treatment on wear resistance of AISI H-13 tool steel, science direct. |
[9] | Meyers Marc A, Chawla Krishan Kumar (1998). Mechanical Behaviors of Materials. Prentice Hall. |