Nabeel Gharaibeh1, Jawdat A. Al-Jarrah2, Salameh A. Sawalha3
1Mechanical Engineering Department, Al-Huson University College, Al- Balqa Applied University, Al-Huson, Jordan
2Mechanical Engineering Department, Engineering College, Northern Border University, Ar'ar, KSA
3Mechanical Engineering Department, Faculty of Engineering Technology, Al-Balqa Applied University, Amman, Jordan
Correspondence to: Nabeel Gharaibeh, Mechanical Engineering Department, Al-Huson University College, Al- Balqa Applied University, Al-Huson, Jordan.
Email: |  |
Copyright © 2016 Scientific & Academic Publishing. All Rights Reserved.
This work is licensed under the Creative Commons Attribution International License (CC BY).
http://creativecommons.org/licenses/by/4.0/

Abstract
This paper investigates the effect of the tool pin profile and friction stir welding parameters on the microstructure and mechanical properties of the 6061 aluminum alloy welded joints prepared by friction stir welding. It has been found that a fine grain microstructure obtained by hexagonal pin profile. But using a square pin profile produced a higher strength welded joints.
Keywords:
Friction Stir welding, Aluminum Alloy, Pin profile, Tensile, Hardeness
Cite this paper: Nabeel Gharaibeh, Jawdat A. Al-Jarrah, Salameh A. Sawalha, Effect of Pin Profile on Mechanical Properties of 6061 Al Alloy Welded Joints Prepared by Friction Stir Welding, International Journal of Mechanics and Applications, Vol. 6 No. 3, 2016, pp. 39-42. doi: 10.5923/j.mechanics.20160603.01.
1. Introduction
In recent years, demands for aluminum alloy 6061 have steadily increased in aerospace, aircraft and automobile applications because of their excellent strength to weight ratio, good ductility, corrosion resistance and cracking resistance in adverse environment [1]. But the welding of aluminum alloys still remains a challenge using conventional welding methods [2]. Friction stir welding (FSW) process becomes the most used method in welding aluminum alloys [3, 4]. The welding equality using FSW depends on the welding parameters like rotational speed, welding speed and applied axial force during the welding process [5]. Also, the tool shape influenced the microstructure and mechanical properties of the welding area. Many researchers studied the effect of pin profile like (cylindrical, square, triangle, etc.) on the properties of the welding area. Bayazid et al [6] have found that square pin profile produced more fine grain size on the welding area rather than cylindrical or triangle profiles. However, it was founded numerically that the temperature of the welded zone increases with number of pin sides [7]. The pin profile has related influence on metal flow, Ilangovan et al. [8] founded that the use of threaded pin profile of tool contributes to better flow of materials between two alloys and the generation of defect free stir zone. In joining dissimilar materials, hexagonal pin profile produced a superior strength joints compared by triangle pin profile [9]. However, the pin profile affects both the temperature of the welding area and the material flow during welding process. In this investigation an attempt was made to correlate the influence of pin profile on the equality of welding joints with the other welding process parameters like rotational speed and welding speed.
2. Experimental Set-up
6061 Al alloy plates were used in this investigation with chemical composition given in Table 1. Two rectangular aluminum plates of 300 x 150 X 6 mm size were butt- welded by friction stir welding process. A conventional vertical milling machine was used for friction stir welding process, by using a special fixture. The fixture is tightly fixed on the milling machine table to prevent vibration from occurring as a result of the frictional forces of the welding process.Table 1. Chemical compositions of 6061 Al alloy  |
| |
|
Welding tools with flat shoulder of 21 mm diameter, and 20 mm height, made of high carbon steel, were used. Three pin profiles (a) Triangle (b) square and (c) hexagonal shapes were used in this investigation. All the pins cut from a cylindrical shape of 6 mm diameter and 5.8 mm in height as shown in Table 2. A spring-loaded unit was used to maintain the applied pressure on the shoulder face of the welding tool against the upper surface of the work piece constant at 4.7 MPa. The welding process was carried out using five different rotational speeds and five welding (traverse) speed. The rotational speeds were 560, 700, 900, 1120, and 1300 rpm. The welding (traverse) speeds, were 0.5, 1, 1.5, 2 and 2.5 mm/sec. Single stir pass was applied during the dry welding process. Microstructure examinations were done using optical microscope. The specimens, which were taken from the middle of the stirred zone, were prepared by standard metallographic techniques and etched with Keller’s reagents to reveal the grain structure. A statistical analysis was performed in the stirred zone based on light microscopy images performing the measurements on 300 grains for each measured grain size value. Vickers micro-hardness was measured with 0.5 kgf load and a dwell period of 10s. Several measurements were done for each hardness value. In addition, a tensile test was carried out on a WDW -20 computer controlled electromechanical universal testing machine to measure the tensile strength of the welded plates, According to ASTM: E8. The tensile test specimens had a gauge diameter of 12 mm and gauge length of 90 mm as shown in Fig. 1.Table 2. Pin profile 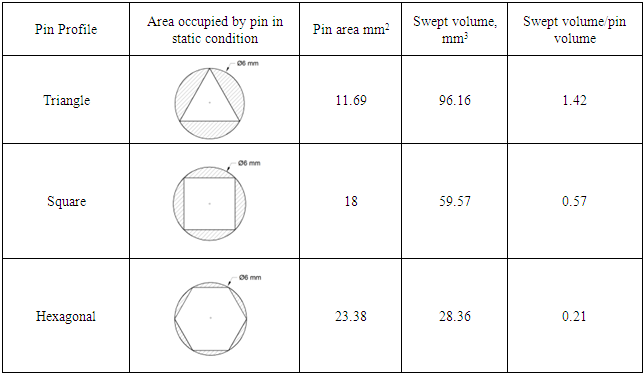 |
| |
|
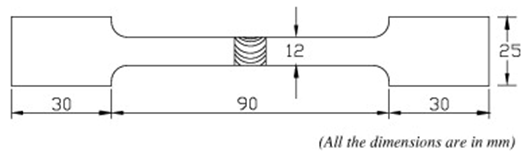 | Figure 1. Tensile test specimen |
3. Results and Discussions
3.1. Microstructure
The microstructure evolution of the welding zone affected mainly by two factors: the first factor is the temperature which depends on the rate difference between the heat generated and heat dissipated during the welding process, the second factor is plastic deformation induced by the stirring action. In this investigation the welded specimens cooled naturally by atmospheric air. Where the heat generated is controlled by the welding process as rotational speed, welding speed and the axial force. The pin profile is affecting the stirring action. It was reported that the weld power input converted to plastic deformation energy in the bulk can be separated into two parts (a) fraction stored in the microstructure, and (b) fraction converted to heat [10, 11]. The metal plastic deformation in friction stir welding process occurred in two zones. One occurred due to frictional force between shoulder face and the top surface of the welded parts. The other one is the plastic deformation happened as extrusion of metal by pin faces during mixing process. The pin profile playing a main role in the quantity of metal deformed during welding. Table 2 shows that a triangle pin profile exposed to a large metal to be extruded by its faces in each rotation during mixing process. The optical microstructure of the base metal and the stir zone of the welded parts produced by different pin profile are shown in Fig. 2. The stirring zone has experienced high temperatures and extensive plastic deformation, and is characterized by dynamically recrystallized grains [12]. Fine equiaxed grain structure was acquired in the stir zone [13]. The pin profile affects the stir zone microstructures greatly [5]. Fig.2 (b) shows a fine equiaxed grain microstructure where a square pin profile was used in this experiment. While using a triangle pin profile resulted in a prolonged grain microstructure due to more extrusion happened to metal during mixing as shown in Fig. 2(c). Definite change in weld made with hexagon tool was observed. The grains in the stir zone experienced high temperatures and turbulent material flow resulting in severe plastic deformation. Very fine grains are formed due to dynamically re-crystallization compared to weld stir zone made with other pin profile as shown in Fig. 2(d). From microstructural changes and results of stir zone width it is clearly shown that the microstructure of the welded zone is dependent on the tool pin profile and the welding parameters [14].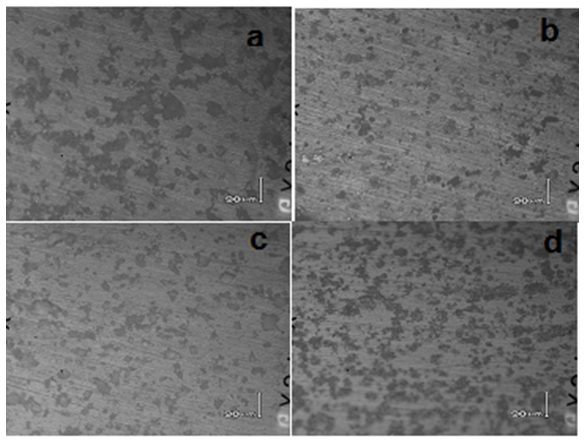 | Figure 2. Microstructure of (a) base metal and welding zone produced by (b) square, (c) Triangle and (d) hexagonal pin profiles |
3.2. Mechanical Properties
Vicker's microhardness tests were conducted for a specimens prepared from the welded joints. The microhardness has been evaluated for triangular, square and hexagonal tool pin profile. Fig.3 shows the effect of rotational speed on the microhardness of the welding region produced at different shapes of tool pin profiles. It has been found that the microhardness decreased as the rotational speed increased for all the shapes of tool pin profiles. However it has been noticed that the joints fabricated using hexagonal pin profile have the higher values of microhardness and the lower values have been recorded in the joints produced by triangle pin profile. The heat generated during friction stir welding playing a vital role in grain growth which affects the microhardness of stir zone [15]. The effect of the welding speed on the microhardness of the stir zone has been shown in Fig. 4. The variation of hardness is related to the microstructural changes in the stir zone induced by welding conditions, where the size of grain varies with heat input. For a fixed rotational speed and the applied axial force the heat input during the friction welding decreased as the welding speed increased. So, the microhardness increased as the welding speed increased as depicted in Fig. 4. However, the higher pulsating action experienced in the stir zone of hexagonal pin profile tool produced fine grain microstructure uniformly distributed precipitates yield a higher microhardness compared by other welds obtained by square and triangle pin profiles. Also, hexagonal pin profile experienced smallest magnitude of shear stress during welding process which reduces the transverse force and enhancing the structural stiffness of the welded joints [7].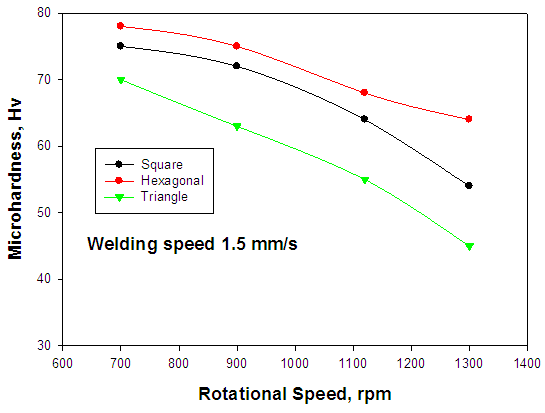 | Figure 3. Effect of rotational speed on the microhardness of the stir zone |
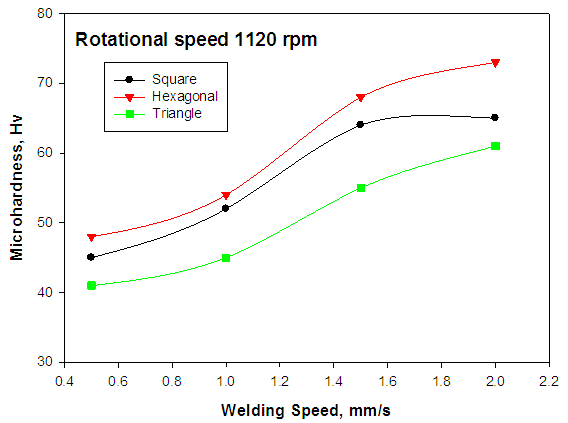 | Figure 4. Effect of welding speed on the microhardness of the stir zone |
Transverse tensile properties of FSW joints have been evaluated. Three specimens were tested at each condition and average of the results of three specimens is presented. Fig. 5 shows the variation of the ultimate tensile strength of the welded joints with rotational speed for the tested pin profiles. Also, the effect of the welding speed on the ultimate tensile strength of the stir zone has been depicted on Fig.6. The strength of the joints prepared by square pin profile have a higher ultimate tensile strength compared by one prepared by the other two pin profiles. The highest ultimate tensile strength observed at 1120 rpm and 1.5 mm/sec for stir zone produced by square pin profile then by hexagonal and the lowest value obtained for joints produced by triangle pin profile. This result agreed with the results obtained by previous research [16]. However the effect of the rotational speed on the ultimate tensile strength shows the joints produced by triangle pin profile has highest strength at rotational speed of 900 rpm then starts to decrease for further increase in rotational speed. This is because as triangular pin has highest shoulder area so it generates sufficient heat for welding at 900 rpm and produces defect free joint [8].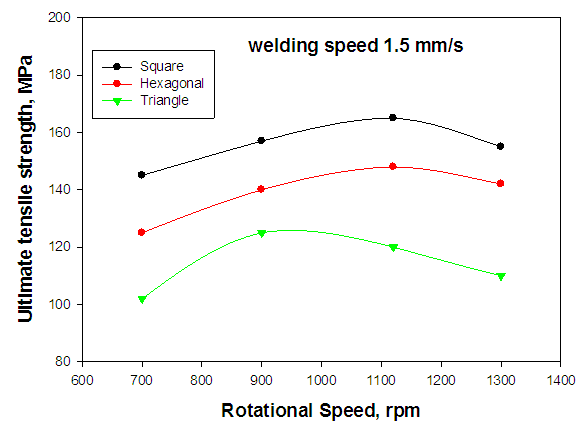 | Figure 5. Effect of rotational speed on the ultimate tensile strength |
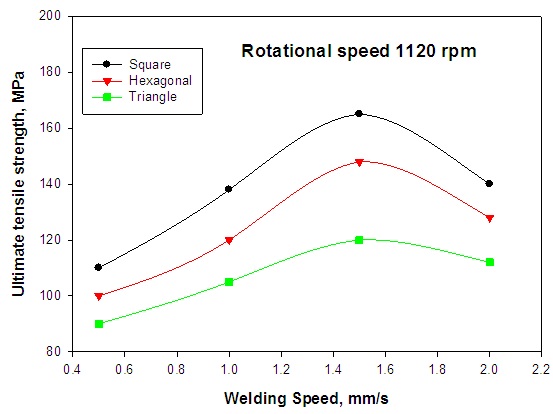 | Figure 6. Effect of welding speed on the ultimate tensile strength |
4. Conclusions
In the present study, the effect tool pin profile and welding process on friction stir welding of AA 6061 Al alloy was studied and based on the results the following conclusions can be drawn: 1. The weld prepared by hexagonal pin profile possessed better microhardness and microstructure compared to the one prepared by square or triangle pin profiles. 2. The strength of the joints prepared by square pin profile have higher ultimate tensile strength compared by one produced by hexagonal and triangle pin profiles3. The micro-hardness of the welded joints decreased as the rotational speed increased, irrespective of the pin profile used to prepare the joints.4. The highest ultimate tensile strength observed at 1120 rpm and 1.5 mm/sec for stir zone produced by square pin profile.
References
[1] | J. Stephen Leon, V. Jayakumar, 2014, Investigation of mechanical properties of aluminium 6061 alloy friction stir welding, American J. Of Mechanical Engg. and Automation, pp 6-9. |
[2] | R.S. Thube, 2014, Effect of tool pin profile and welding parameters on friction stir processing zone, tensile properties and micro-hardness of AA 5083 joints produced by friction stir welding, Int. J. of Engg. and advanced technology, pp 35-40. |
[3] | P. Manikkavasagan, G. Rajamurugan, K. Satheesh Kumar, D. Yuvaraj, 2015, Experimental study on the effect of tool pin profile on aluminum AA 6063 friction stir welded butt joints, Material Science forum, pp 302-305. |
[4] | Sc Rajakumar, S., Muralidharan, C., Balasubramanian, V., 2010, Optimization of the friction-stir-welding process and tool parameters to attain a maximum tensile strength of AA7075–T6 aluminium alloy. Journal of Engineering Manufacture, 224, pp. 1175-1191. |
[5] | S. M. Bayazid, H. Farhangi, A. Ghahramani, 2015, Effect of pin profile on defects on friction stir weld 7075 aluminum alloy, Procedia material science,11, pp.12-16. |
[6] | M. Mehta. G.M. Reddy, A.V. Rao, A. De, (2015), Numerical modeling of friction stir welding using the tools with polygonal pins, Defence Technology, 11, pp. 229-236. |
[7] | M. Ilangovan, S. Rajendra Boopathy, V. Balasubramanian, 2015, effect of tool pin profile on microstructure and tensile properties of friction stir welded dissimilar AA 6061 –AA5086 aluminum alloy joints, Defence Technology 11, pp 174-184. |
[8] | .Sabeerushen, J.R. Vinod Kumar, 2016, Influence of tool pin profile on the tensile behavior of dissimilar friction stir welded joints of aluminum alloys, Int. J. of Innovative Research in Science, Engineering and Technology, vol.5, pp. 5376-5382. |
[9] | J. Hodowany, G. Ravichandran, A.J. Rosakis, P. Rosakis, 2000, Partition of plastic work into heat and stored energy in metals. Exp. Mech. 40, pp.113–123. |
[10] | R. Kapoor, S. Nemat-Nasser, 1998, Determination of temperature rise during high strain-rate deformation Mech. Mater. 27, pp. 1–12. |
[11] | J. Al-Jarrah, S. Swalha, T. Mansour, M. Ibrahim, M Al-Rashdan and D. Al-Qahsi, 2014, Welding equality and mechanical properties of aluminum alloys joints prepared by friction stir welding, Material and Design, pp.929-936. |
[12] | Zhang Z, Xiao BL, Ma ZY, 2012, Effect of welding parameters on microstructure and mechanical properties of friction stir welded 2219Al-T6 joints. J Mater Sci. 47, pp.4075-4086. |
[13] | G. Rambabu, D. Balaji Naik, C.H. Venkata Rao, K. Srinivasa Rao, and G. Madhusudan Reddy, Optimization of friction stir welding parameters for improved corrosion resistance of AA2219 aluminum alloy joints, Defence Technology, 2015, pp. 330-337. |
[14] | J. Al-Jarrah, S. Swalha, T. Mansour, M. Ibrahim, M Al-Rashdan and D. Al-Qahsi, 2013, Optimization of friction stir welding parameters for joining aluminum alloys using RSM., Adv. Theor. Applied mechanics, pp. 13-26. |
[15] | K. Elangovon, V. Balasubramanian and S. Babu, 2009, Prediction tensile strength of friction stir welded 6061 aluminium alloy joints by mathematical model, Materials and design, 30, pp 188-193. |