Song Hak Jin, Jo Un Jong
Department of Mechanics of Materials, Kim Chaek University of Technology, Pyongyang, Korea
Correspondence to: Song Hak Jin, Department of Mechanics of Materials, Kim Chaek University of Technology, Pyongyang, Korea.
Email: |  |
Copyright © 2015 Scientific & Academic Publishing. All Rights Reserved.
This work is licensed under the Creative Commons Attribution International License (CC BY).
http://creativecommons.org/licenses/by/4.0/

Abstract
Thermal cycling creep lifetime of Al-Si cast alloys was estimated in experimental ways. Thermal cycling creep tests on the samples of AlSi7 and AlSi18 alloys in different solution treatment conditions were conducted in the temperature range of 50~300°C. Stress exponents of AlSi7 and AlSi18 alloys were computed and found to be in the range of 4.4~5.2 and 2.0 ~3.1 according to the solution treatment conditions, respectively. Mathematical model for prediction of thermal cycling creep lifetime of the alloys was proposed on the base of conservation of strain energy during the creep process. The theoretical predictions were compared with the ones of the experiment results, and good agreement was obtained. Metallography pictures of the tested materials have been taken to check the influence of microstructures on the creep resistance and ductility of the materials.
Keywords:
Aluminum Silicon Alloy, Thermal cycling Creep, Strain Rate, Lifetime, Stress Exponent
Cite this paper: Song Hak Jin, Jo Un Jong, Assessment of Thermal Cycling Creep Lifetime of Al-Si Alloys, International Journal of Mechanics and Applications, Vol. 5 No. 2, 2015, pp. 41-47. doi: 10.5923/j.mechanics.20150502.03.
1. Introduction
Al-Si cast alloys are used widely due to their light weight, high strength, etc. Especially, these materials are used in automobile industry because of their good cast ability and relatively high strength to elevated temperature. That’s why the investigations on these materials are conducted in many detailed fields including thermal stability, isothermal and thermal cycling creep resistance of as-cast or solution treated Al-Si alloys.Huber and Nam have illustrated some test results which show the influence of contents of consisting elements and thermal treatment conditions of the test samples on the thermal stability of aluminum alloys [1, 3]. Lasagni’s test results show evident difference of Young’s moduli of Al-Si alloys according to the contents of silicon [2].The Al-Si binary system is designed as non age hardening. The main reason for a solution treatment of these materials is not to dissolve the Si phase, the solubility of which is only 1.6 wt.%. Actually, the solution treatment of Al-Si alloys containing more than 2 wt.% Si is a spheroidization treatment of the eutecticly segregated Si, the main objective of which is to improve the ductility of the eutectic material. The eutectic is formed between an aluminum solid solution containing just 1.65% silicon (at the eutectic temperature ~577°C) and virtually pure silicon as the second phase. According to the test results of Lasagni and Guillermo, the strengthening role of the eutectic silicon is based on a transfer of load from the aluminum matrix to the more rigid eutectic silicon, which depends on the orientation of the Si particles and their aspect ratio [4-8]. The eutectic composition, which has a high degree of fluidity and low shrinkage on solidification, has particular application for thin walled castings such as pistons for internal combustion engines.Since most of the Al-Si alloys work at elevated temperature which increases creep strain rate and shortens the creep lifetime of components, there have been many studies on the creep properties of the materials in different mechanical and thermal load conditions and reliable prediction of the creep lifetime. Jaglinski has studied creep behaviors of Al-Si die-cast alloys and determined activation energy for the creep processes of the materials at different temperatures [10]. Prader and Guillermo have investigated the isothermal and thermal cycling creep behaviors of Al-Si alloys, and have compared the test results with the ones of short fibre and particle reinforced Al-Si alloys [9, 11]. Terada has conducted creep tests for Mg-Al-Mn alloys and evaluated the creep rupture life by using Larson-Miller parameter [12, 13, 16], while Nanxian and Zhang have proposed some methods to predict creep lifetime of different alloys by using finite element analysis [14, 15].Although there have been many studies on the properties of Al-Si alloys at high temperatures, further investigations on thermal cycling creep (TCC) behaviors of hypo and hypereutectic Al-Si alloys are needed to ensure the reliability in service applications of these materials. The aim of the present work is to study TCC behaviors of AlSi7 and AlSi18 cast alloys in different solution treatment conditions. TCC tests on the samples of AlSi7 and AlSi18 alloys in three different solution treatment conditions were conducted in the temperature range of 50~300°C under mechanical loads of 20, 30 and 40MPa. Mathematical model for prediction of thermal cycling creep lifetime of the alloys was proposed on the base of conservation of strain energy during the TCC test processes.
2. Experimental Methodology
2.1. Materials and Heat Treatments
AlSi7 and AlSi18 cast alloys were used for the TCC tests. These alloys were produced using a squeeze casting process by LKR, Ranshofen, Austria. The chemical composition of the alloys is shown in Table 1.Table 1. Composition of the alloys [wt.%] 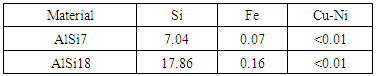 |
| |
|
All the samples for the tests were cut into the ones with gauge length of 20mm and gauge diameter of 8mm.Three different thermal treatment conditions were selected for these samples; first one is as-cast (AC) condition, second one is solution treatment for 20 minutes, third one is solution treatment for 4 hours (T4a). Solution treatments (ST) of the samples were carried out in a Linn High Therm furnace 70.26 at 540°C followed by air cooling.
2.2. Metallography
Light Optical Microscopy of the AlSi7 and AlSi18 squeeze casting alloys in different solution treatment conditions was performed by means of Zeiss Axioplan microscope with digital imaging system. Optical zoom of 50x was selected. Metallography samples made from the tested materials were polished with DP-diamond paste of 3 and 1 μm particle diameter and DP-lubricant blue (Struers) as coolant.
2.3. Thermal Cycling Creep Tests
Thermal cycling creep tests were performed in a Gleeble 1500 apparatus.The tests were carried out at a constant load of 20, 30 and 40MPa and in a temperature interval between 50 and 300°C. Heating and cooling rates of 12.5K/s were selected with a holding time of 3 seconds after reaching the desired maximal and minimal temperatures. In this way, the total time for a complete cycle was 46 seconds. The temperature of the samples was measured using type J thermocouple. Axial elongation and contraction of the samples were measured using a high temperature extensometer combined with a HBM bridge amplifier. The creep strain of the samples can be determined using next formula from the test results (Fig. 1) [8]. | (1) |
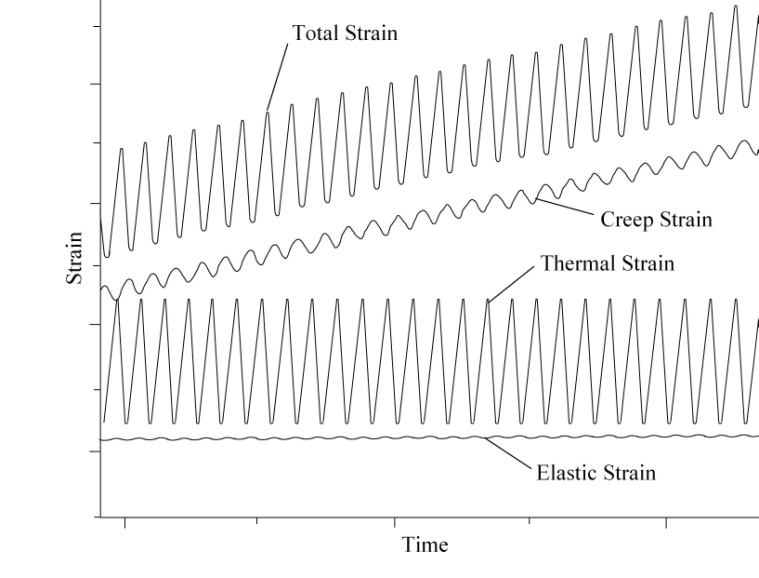 | Figure 1. Determination of creep strain from the measured strain |
Here,
is a total measured strain, which can be obtained from the measured elongation as 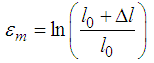 | (2) |
is an elastic strain, which can be obtained as  | (3) |
where
is an applied stress (20, 30 or 40MPa),
is Young’s modulus of tested material at temperature
, which can be determined fitting Lasagni’s test curves as following [2]. | (4) |
Fitting coefficients for the equation (4) are shown in Table 2.Table 2. Fitting coefficients for Young’s modulus of the tested materials 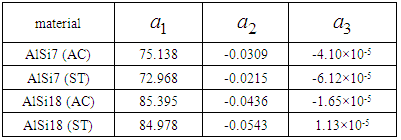 |
| |
|
is a thermal strain, which can be obtained as 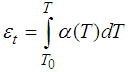 | (5) |
where
is a room temperature and
is a temperature at every step of TCC tests,
is coefficient of thermal expansion of the tested material at temperature
which can be determined fitting Lasagni’s dilatometry test curves as following [7]. | (6) |
Fitting coefficients for the equation (6) are shown in Table 3.Table 3. Fitting coefficients for coefficient of thermal expansion of the tested materials 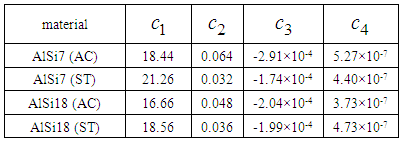 |
| |
|
3. Results and Discussion
Fig. 2 and 3 show microstructures of AlSi7 and AlSi18 alloys in different conditions. The α-phase of AlSi7 alloy in AC condition is enclosed by the eutectic structure of lamellar Si, whereas the β-phase is dominant in hypereutectic AlSi18 alloy. Spheroidization of Si during solution treatment can be noticed in the pictures for both AlSi7 and AlSi18 alloys. After 4 hours’ solution treatment remarkable spheroidization was observed which leads to increase of ductility of the alloys. 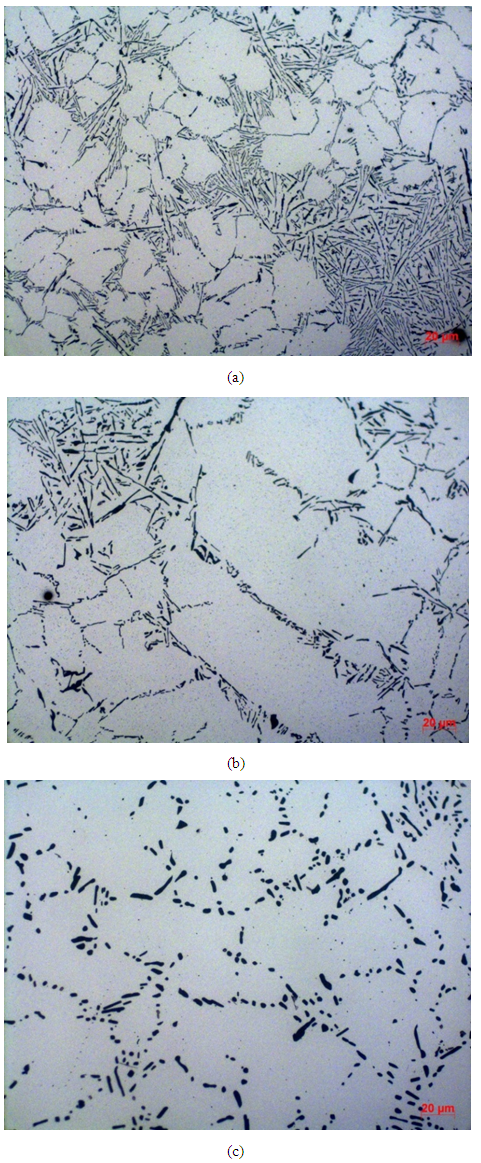 | Figure 2. Microstructures of AlSi7 in AC (a), 20 minute’s ST (b) and 4 hour’s ST (c) conditions |
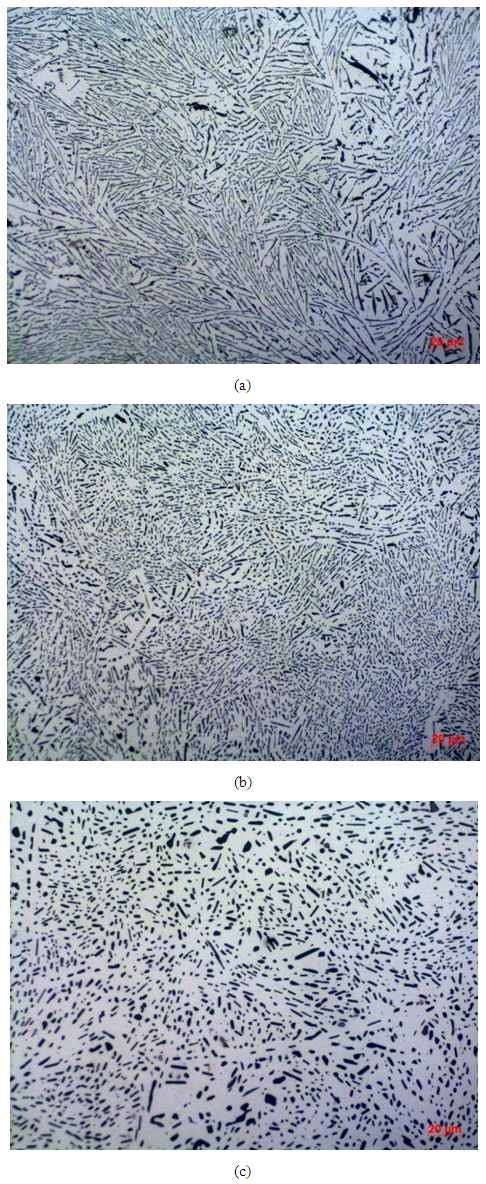 | Figure 3. Microstructures of AlSi18 in AC (a), 20 minute’s ST (b) and 4 hour’s ST (c) conditions |
Fig. 4 and 5 depict the calculated strain rates from the TCC tests performed on AlSi7 and AlSi18 cast alloys in three different heat treatment conditions. For every load condition (20, 30 and 40MPa), AlSi7 and AlSi18 alloys in AC condition exhibit the longest TCC life achieving 50, 7 and 1.2 hours for AlSi7, 22, 8 and 4 hours for AlSi18, respectively. TCC lives of the materials solution treated for 20 minutes and 4 hours were much shorter than the ones in AC condition; about 10 and 4 hours for AlSi7, 8 and 6 hours for AlSi18 under 20MPa, about 1.7 and 0.8 hours for AlSi7, 2.5 and 1.5 hours for AlSi18 under 30MPa, about 0.3 and 0.15 hours for AlSi7, 1 and 0.4 hours for AlSi18 under 40MPa, respectively.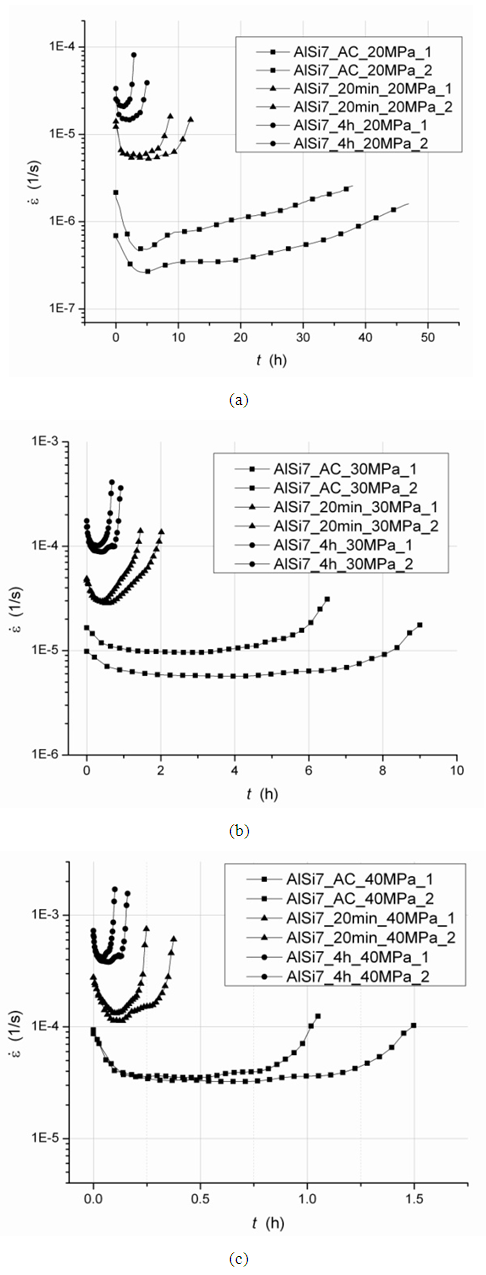 | Figure 4. Strain rates during thermal cycling creep tests of AlSi7 under 20MPa (a), 30MPa (b), 40MPa (c) |
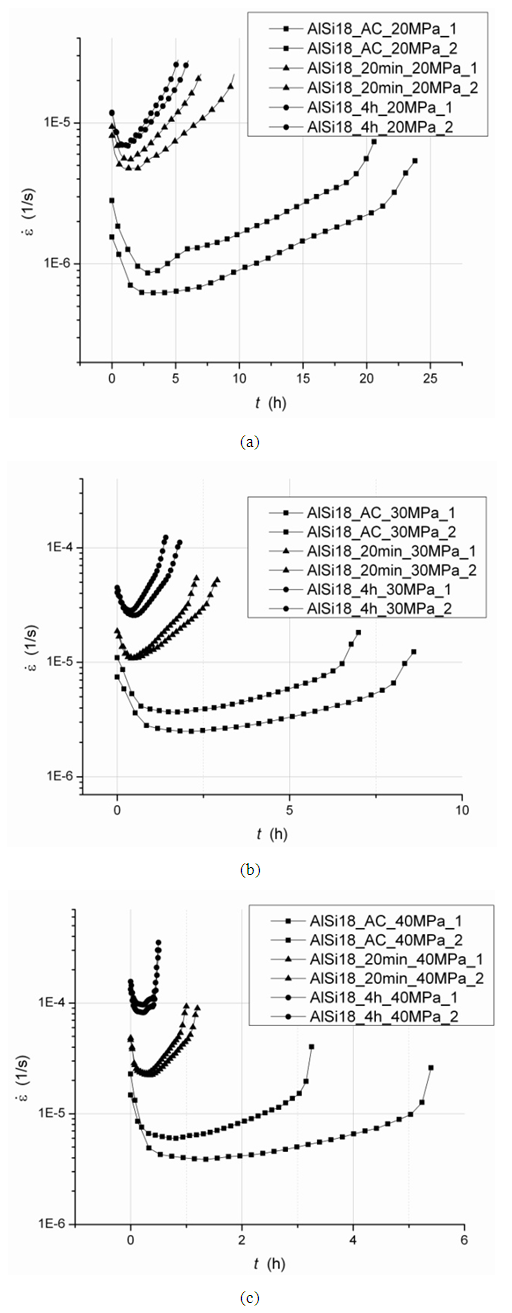 | Figure 5. Strain rates during thermal cycling creep tests of AlSi18 under 20MPa (a), 30MPa (b), 40MPa (c) |
This behavior can be explained by means of the load transfer from the aluminum phase to the Si inclusions in the alloys. In as-cast, microstructural analysis of Al-Si alloys reveals the formation of Si skeleton formed of thin Si lamellae with relatively high aspect ratio compared to that of the spheroidizated Si particles of solution treated samples. On the other hand, the ductility of both AlSi7 and AlSi18 alloys in solution treated conditions is increased by 30~40% in comparison with samples tested in AC condition.Regarding the strain rate, AlSi7 alloy in AC condition exhibits the lowest value of about 4x10-7s-1 under a load of 20MPa, whereas AlSi18 alloy in AC condition shows 7x10-7s-1 at the same load. For 40MPa, however, AlSi18 alloy in AC condition exhibits lower strain rate of 5x10-6s-1 and longer creep life of 4 hours as compared with AlSi7 alloy in AC condition which shows 3x10-5 s-1 and 1.2 hours, respectively. This can be explained by higher load carrying capacity of Si fibre network in AlSi18 alloy than the one in AlSi7 alloy.
4. TCC Lifetime Prediction
Generally, the creep rupture life is dependent to the applied stress and temperature. In this study, the failure strain energy is assumed to be conserved for all the TCC test conditions in case of the same samples. Strain energy is calculated by the integration of the stress multiplied by the infinitesimal strain at each time until failure occurs. Here,
and
are rupture lifetime and rupture strain of the TCC test samples.Strictly speaking, the failure strain energy should also include the contribution from the primary and tertiary creep processes, but this will make the whole analysis very complicated. For simplicity, only the secondary creep stage which has the largest portion of the creep curve is considered, then the creep failure strain energy can be determined by using the following Norton’s equation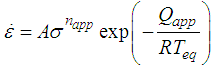 | (8) |
where napp and Qapp are the apparent stress exponent and activation energy of the tested materials at equivalent temperature Teq of the TCC processes.Substituting the equation (8) into (7), we can denote the failure strain energy as following. 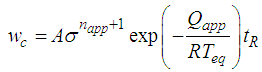 | (9) |
From the assumption of the conservation of strain energy, we obtain following equation for the same samples in different TCC test conditions.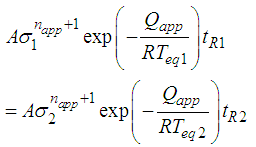 | (10) |
Consequently, lifetime prediction of the TCC test samples can be done by the following equation.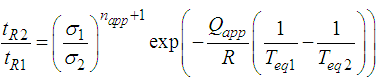 | (11) |
Considering that all the TCC tests have been conducted for the same temperature conditions (50~300°C) in this study, the equation for prediction of lifetime can be simplified as following.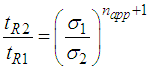 | (12) |
Therefore, it is possible to predict the TCC lifetime of AlSi7 and AlSi18 alloys only by knowing the apparent stress exponent napp of the materials, which can be determined by plotting the relation between stress and minimal strain rate in the logarithmic coordinate system (Fig. 6). The apparent stress exponents of AlSi7 and AlSi18 alloys were found to be in the range of 4.4~5.2 and 2.0~3.1 according to the solution treatment conditions, respectively.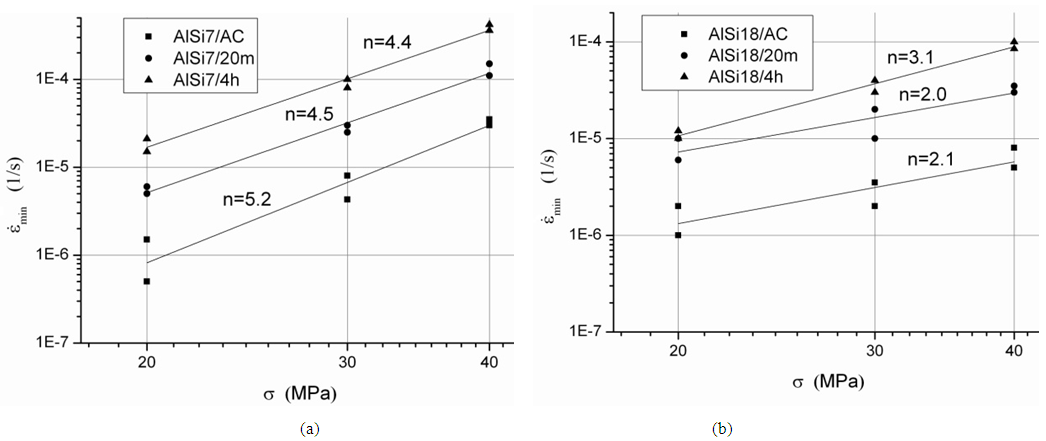 | Figure 6. Determination of stress exponents of AlSi7 (a) and AlSi18 (b) alloys in different ST conditions |
Fig. 7 shows the prediction of the TCC lifetime of AlSi7 and AlSi18 alloys in different solution treatment conditions. It was found that predictions obtained from the equation (12) agree well with the experimental results.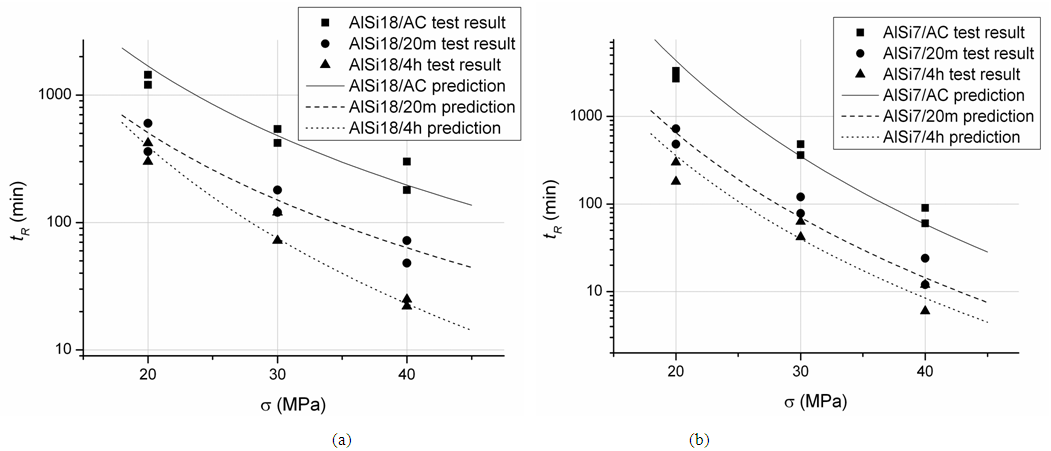 | Figure 7. Prediction of TCC lifetime of AlSi7 (a) and AlSi18 (b) in different ST conditions |
5. Conclusions
TCC tests on AlSi7 and AlSi18 squeeze casting alloys were conducted to find out creep characteristics of the materials. Apparent stress exponents of AlSi7 alloy were found to be 5.2, 4.5 and 4.4 in AC, 20 minutes’ ST and 4 hours’ ST conditions, respectively. Smaller values of 2.1, 2.0 and 3.1 were obtained for AlSi18 alloy in 3 different conditions, respectively.An equation for prediction of TCC lifetime based on the conservation of creep strain energy was proposed. The theoretical predictions show good agreement with the experimental results. It was found that the TCC lifetime is inversely proportional to n+1th power of the applied stress.Thermal cycling creep tests for all the samples of Al-Si alloys have been conducted at single temperature range (50~300°C). But the tests should be conducted at two or three different temperature ranges in order to determine apparent activation energy for the creep processes of the materials, which enables us to predict the creep lifetime for a different temperature condition by using the equation (11). This issue will be addressed in a future paper.
ACKNOWLEDGEMENTS
H. J. Song is grateful for funding provided by OEAD (Austria) and to Prof. Brigitte Winklehner for her kind help to make the funding possible. The authors are grateful to Prof. Hans Peter Degischer for his support in this study.
References
[1] | T. Huber (2003) Thermal Expansion of Al-alloys and Composites, PhD Thesis, TU-Vienna. |
[2] | F. Lasagni and H. P. Degischer (2010) Enhanced Young’s Modulus of Al-Si Alloys and Reinforced Matrices by Co-continuous structure, Journal of Composite Materials Vol.44, No.6: 739-755. |
[3] | T. H. Nam and G. Requena (2008) Thermal expansion behaviour of aluminum matrix composites with densely packed SiC particles, Composites: Part A 39: 856-865. |
[4] | G. Requena and G. Garces (2009) 3D Architecture and Load Partition in Eutectic Al-Si Alloys, Advanced Engineering Materials, Vol.11, No.12: 1007~1014. |
[5] | G. Requena and G. Garces (2009) The effect of eutectic Si on the strength of short-fibre-reinforced Al, Acta Materialia, 57: 3199~3210. |
[6] | F. Lasagni and B. Mingler (2008) Precipitation kinetics of Si in aluminium alloys, Materials Science and Engineering A 480: 383~391. |
[7] | F. Lasagni (2006) The role of Si on the micro-structure of Al casting alloys and short fibre composites, PhD Thesis, TU-Vienna. |
[8] | G. Requena (2004) Creep Behaviour of Discontinuously Reinforced Aluminium Alloys, PhD Thesis, TU-Vienna. |
[9] | G. Requena and H. P. Degischer (2006) Creep behaviour of unreinforced and short fibre reinforced AlSi12CuMgNi piston alloy, Materials Science and Engineering A 420: 265~275. |
[10] | T. Jaglinski (2004) Creep Behaviour of Al-Si Die-Cast Alloys, Transactions of the ASME, Vol.126, 10: 378~383. |
[11] | P. Prader (2000) Thermal Cycling Creep Behaviour of Particle Reinforced Aluminium Alloys, PhD Thesis, TU-Vienna. |
[12] | Y. Terada and Y. Murata (2011) Analysis of creep rupture life of Mg-Al-Mn alloy produced by die-casting, Materials Chemistry and Physics, 128: 32~34. |
[13] | Y, Terada and T. Sato (2010) Assessment of creep rupture life of heat resistant Mg-Al-Ca alloys, Journal of Alloys and Compounds, 504: 261~264. |
[14] | H. Naixian and Y. Kun (2011) Fatigue-creep life analysis for powder metallurgy material with inclusion, Procedia Engineering, 17: 292~296. |
[15] | S. Zhang and M. Sakane (2007) Multiaxial creep-fatigue life prediction for cruciform specimen, International Journal of Fatigue, 29: 2191~2199. |
[16] | Y. Terada and T. Sato (2008) Relationship between Minimum Creep Rate and Rupture Life for a Die-Cast Mg-Al-Mn Alloy, Materials Trans-actions, Vol.49, No.3: 439~442. |