Firas M. F. Al Quran
Al-Balqa Applied University, Al-Huson University College, Department of Mechanical Engineering, Al-Huson-Irbid, Jordan
Correspondence to: Firas M. F. Al Quran, Al-Balqa Applied University, Al-Huson University College, Department of Mechanical Engineering, Al-Huson-Irbid, Jordan.
Email: |  |
Copyright © 2015 Scientific & Academic Publishing. All Rights Reserved.
This work is licensed under the Creative Commons Attribution International License (CC BY).
http://creativecommons.org/licenses/by/4.0/

Abstract
Burnishing is a chip less machining process in which a rotating roller or ball is pressed against a metal piece. It is a cold working process and involves plastic deformation to the surface irregularities. Simple roller-burnishing tool was used for the experimental work of the present study. Surface texture and micro hardness tests, were applied to demonstrate the effects of the burnishing force and feed rates on the surface roughness and surface hardness of commercially available aluminum. A detailed experimental program was used in this study where specimens were subjected to different levels of feeding speed and burnishing force. The roughness and micro hardness were measured at the end of each burnishing combination of feeding speed and burnishing force. Significant enhancement in the surface roughness values were clearly observed, meanwhile, very little enhancement to the surface hardness were encountered. The best results were obtained at the lowest value of the burnishing feed rate and maximum burnishing force used in this investigation.
Keywords:
Burnishing, Plastic deformation, Surface roughness, Surface hardness
Cite this paper: Firas M. F. Al Quran, The Effect of Roller Burnishing on Surface Hardness and Roughness of Aluminum Alloy, International Journal of Mechanics and Applications, Vol. 5 No. 2, 2015, pp. 37-40. doi: 10.5923/j.mechanics.20150502.02.
1. Introduction
Burnishing is considered as a cold working process which can be used to improve surface characteristics. Surface roughness and hardness plays an important role in many areas and is factor of great importance for the functioning of machined parts [1]. Most of the work on burnishing that has already been published was concerned with the effect of the burnishing process on the surface roughness and surface hardness. It was suggested by many investigators that an improvement in wear resistance can be achieved by burnishing [2, 3], but very little actual work has been done in this field. Some researchers also studied the influence of several parameters of ball burnishing such as the diameter of the ball, the feed, the burnishing force and the initial surface finish on the finished surface hardness and wear resistance of steel components [4]. The burnishing process can be achieved by applying a highly polished and hard roll on to a metallic surface under pressure. This will cause the peaks of the metallic surface to spread out permanently, when the applied burnishing pressure exceeds the yield strength of the metallic material, allowing the valleys to be filled [5].Wear has important technological and economical significance because it changes the shape of the work piece, and the tool and the interference [6]. The parameters affecting the surface finish are: burnishing force, feed rate, ball or roller material, number of passes, work piece materials, and lubrication, machine stability and tool stability [7]. To ensure quality of machining products and to reduce the machining costs and increase the machining effectiveness, it is very important to select the optimal machining parameters [8].Corrosion resistance of burnished surface is higher than the open surfaces produced by grinding or honing. Due to plastic deformation by this operation, residual compressive stresses are included in the surface of the part. The compressive stresses greatly increase the strength properties and fatigue life of the part. Thousands of parts can be finished with little or no burnishing tool wear. Setting up of the burnishing tool takes less than a minute time. Unskilled operators can produce close tolerance. Situation makes necessary to look for new tool designs or more cheaply for combinations of cutting parameters and types of tools that optimize the machining parameters [9]. In general, the process improves surface hardness, surface quality, and maximum compressive residual stress. It is also associated with higher wear resistance, good surface roughness, and better roundness. It also, improves tensile strength and improves fatigue strength by inducing compressive stress on the surface of the work piece [10-14].
2. Material, Burnishing Tool and Equipment
2.1. Materials
Aluminum alloy was used in the experiment, supplied as 20 mm diameter bar and (1m) long; the chemical compositions are shown in Table 1. Appropriate specimens were cut from this bar to an approximate length of 200 mm using a sawing machine as shown in Figure 1.Table 1. Chemical Composition of Aluminum Alloy  |
| |
|
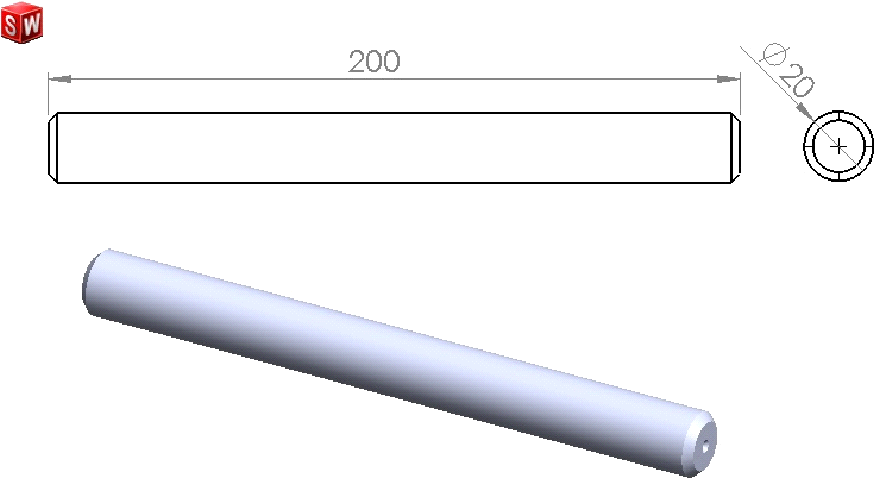 | Figure 1. Specimen Dimensions |
2.2. Burnishing Tool
A 20 mm diameter hardened roller of 5 mm width was used for burnishing.When the roller is pressed against the surface of the metallic specimen, a pre- calibrated dial indicator will be compressed, this indicator being used mainly to measure the applied burnishing force. The shanks of the burnishing tools are designed to be simply mounted or fixed onto the tool holder of a machine tool such as a lathe machine.
2.3. Burnishing Procedure
1. Saw the original rod (1m long) into 5 specimens (each 20cm).2. Turning each specimen to a diameter of 18.6 mm on the TRIUMPH 2000 lathe.3. Each specimen is subjected to the turning conditions listed in Table 2. Table 2. The Turning Conditions  |
| |
|
4. Directly after each specimen turning; the cutting tool was replaced by the roller burnishing tool to enable the burnishing process to be carried out on the specimens using the same lathe while maintaining the same centricity of the specimen. Throughout the experimental program of this study the turning and burnishing were carried out dry.5. Three indentations were made on the surface of each specimen and measurements of the roughness and micro hardness at 10 Newton were then carried out.6. Cleaning the roller was carried out continuously in order to prevent any hard particles from entering the contact surface between the tool and the specimen, such hard particles usually leaving deep scratches, which may damage the burnished surface of the specimen.7. The operating parameters range was collected from the machine Catalogue.Figure 2 shows the final dimensions of the specimen after turning and the final shape after burnishing process and Table 3 shows the burnishing process conditions.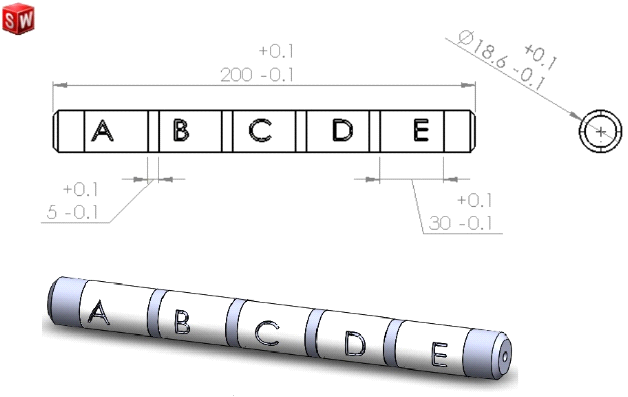 | Figure 2. The Final Dimensions of the Specimen after Turning and Burnishing Process |
Table 3. Burnishing Process Conditions 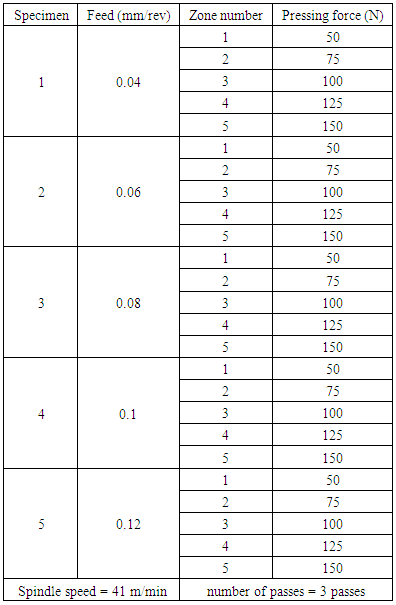 |
| |
|
3. Results and Discussions
3.1. The Effect of the Burnishing Force on the Surface Roughness
It is clear as shown in Figure 3, that there was an obvious decrease in the surface roughness with the increase in burnishing force (0.04, 0.06, 0.1, 0.12 mm/rev). It was observed from 0.08 mm/rev that the surface roughness of the last segment of specimen No.3 increased after a force of 150N; became worse; due to the failure and crack initiation on the inspected segment, since that the peaks begin to show up on the surface, due to the grain deterioration on that surface.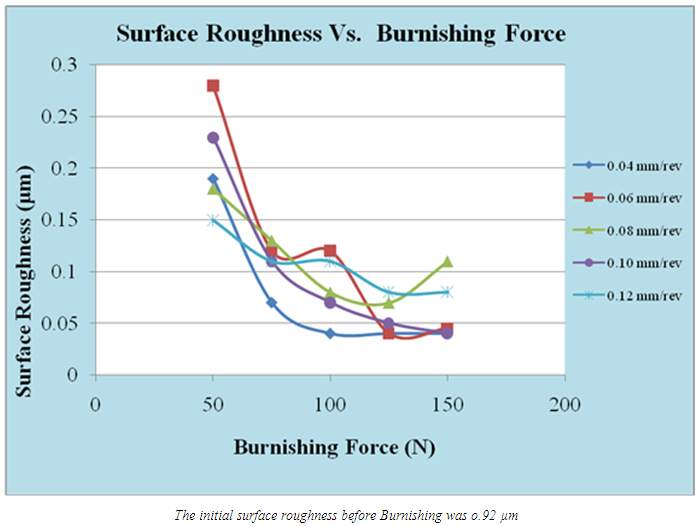 | Figure 3. The Effect of the Burnishing Force on the Surface Roughness |
3.2. The Effect of the Burnishing Force on the Surface Micro Hardness
Figure 4 shows unexpected variation in the values of the micro hardness test. This can be due to the compressive residual stresses on the burnished surface; where the compressive residual stresses were not uniformly distributed along the surface. This may be further explained by the possibility that the pressure exerted by the tool (burnishing force) on the unit area for each segment along the specimens was not at the same value and magnitude. This may leads to unequal distribution of the compressive residual stresses, hence, the stresses were not applied uniformly and this causes the grains stratigraphy to be non-homogenous (i.e. the grains correlation in a specific point on the segment is stronger than other place on the same segment) which makes the metal penetration resistance unequal along the whole segment, which gives irregular hardness values as shown in the figures.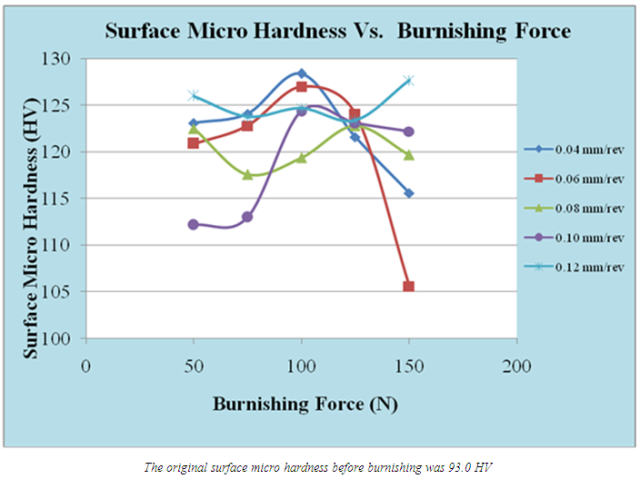 | Figure 4. The Effect of the Burnishing Force on the Surface Micro Hardness |
4. Conclusions
1. Under the different roller burnishing parameters, the obtained surface roughness is dependent on work piece hardness and pre-machining conditions.2. Burnishing is a very sensitive finishing processes where as if there is any vibration within the set of the technological system or in the case of impurities existence on the surface, it will affect directly on the surface finishing.3. The best results were obtained at the lowest value of the burnishing feed and maximum burnishing force used in this investigation.
References
[1] | S. Thamizhmanii, S. Saparuding, S. Hasan, Journal of achievements in Materials and Manufacturing Engineering, 20 (2007) 503-506. |
[2] | R.L. Murthy, B. Kotiveerachari, Burnishing of metallic surfaces– a review, Precision Engineering 3 (1981) 172-179. |
[3] | M. Fattough, M.M. El-Khabeery, S.M. Serage, Residual stress distribution in burnishing solution treated and aged 7075 aluminum alloy, International Journal of Machine Tools Manufacturing, 29 (1) (1985) 153-160. |
[4] | R. Rajasekariah, S. Vaidyanathan, Increasing the wear resistance of steel components by ball burnishing, wear 43 (1975) 183-188. |
[5] | A.M. Hasan, The effects of ball and roller burnishing on the surface roughness and hardness of some non-ferrous metals, Journal of Materials Processing Technology 72 (1997) 385-391. |
[6] | A.M. Hasaan, Z.S. Sulieman, Al. Dhifi, Improvement in the wear resistance of brass components by the ball burnishing process, Journal of Materials Processing Technology 96 (1999) 73-80. |
[7] | M.H. El-Axir, A.A. Ibrahim, Some surface characteristics due to center rest ball burnishing, Journal of Materials Processing Technology 167 (2005) 47-53. |
[8] | M. Milfelner, J. Kopac, F. Cus, U. Zuperl, Intelligent system for machining and optimization of 3D sculptured surfaces with ball end milling, Journal of Achievements in Materials and Manufacturing Engineering 14, (2006) 171-177. |
[9] | S. Dolinsèk, J. Kopac, Mechanisms and types of tool Wear; particularities in advanced cutting materials, Journal of Achievements in Materials and Manufacturing Engineering 19 (2006) 11-18. |
[10] | A.M. Hassan, H.F. Al-Jalil, A.A. Ebied, Burnishing force and number of ball passes for the optimum surface finish of brass components, Journal of Materials Processing Technology 83 (1998) 176 -179. |
[11] | S.S.G. Lee, S.C. Tam, N.H. Loh, Ball burnishing of 316 L stainless steel, Journal of Materials Processing Technology 37 (1993) 241. |
[12] | M.M. El-Khabeery, M.H. El-Axir, Experimental techniques for studying the effects of milling-roller burnishing parameters on surface integrity, International Journal of Machine Tools and Manufacture 41 (2001) 1705- 1719. |
[13] | A.M. Hassan, A.S. Al-Bsharat, Improvement in some properties of non-ferrous metals by the application of the ball burnishing process, Journal of Materials Processing Technology 59 (1996) 250. |
[14] | A.M. Hassan, The effects of ball and roller burnishing on the surface roughness and hardness of some non-ferrous metals, Journal of Materials Processing Technology 72 (1997) 385- 391. |