Zied Driss, Olfa Mlayah, Slah Driss, Makram Maaloul, Mohamed Salah Abid
National School of Engineers of Sfax (ENIS), Laboratory of Electro-Mechanic Systems (LASEM), University of Sfax, Sfax, Tunisia
Correspondence to: Zied Driss, National School of Engineers of Sfax (ENIS), Laboratory of Electro-Mechanic Systems (LASEM), University of Sfax, Sfax, Tunisia.
Email: |  |
Copyright © 2015 Scientific & Academic Publishing. All Rights Reserved.
Abstract
The main objective of this paper is to validate the numerical results developed with the Computational Fluid Dynamics (CFD) code. For thus, a small incurved Savonius wind rotor with a height of 300mm and a bucket diameter of 100 mm is designed and built. This rotor is placed in a wind tunnel test section of 400 mm x 400 mm. The prototype is used to estimate the velocity profiles. For thus, a thermal velocity probe anemometer was used to measure the air velocity. The air speed at the tunnel test section was varied between 0 and 17 m.s-1. The Conformity between the numerical and the experimental results validate the numerical method developed elsewhere.
Keywords:
Savonius wind turbine, Incurved, Wind tunnel, Experimental validation
Cite this paper: Zied Driss, Olfa Mlayah, Slah Driss, Makram Maaloul, Mohamed Salah Abid, Study of a Small Incurved Savonius Wind Rotor: Experimental Validation, International Journal of Mechanics and Applications, Vol. 5 No. 2, 2015, pp. 31-36. doi: 10.5923/j.mechanics.20150502.01.
1. Introduction
The use of wind machines to harness the energy in the wind is not a new concept and can be dated back as far back as the Chinese in 2000 B.C. These early machines were used for pumping water for irrigation purposes and later developed as windmills for grinding grain. It has only really been in the last century that intensive research and development have gone into the use of wind energy for electricity generation. Many experimental and numerical studies have been carried out on Savonius wind rotors to investigate the flowfield. For example, Khan et al. [1] tested Savonius rotor both in tunnel and natural wind conditions with the provision of variation of overlap. Optimum overlap of the rotor blades varied with the shape of the blade profiles. The highest Cp of 0.375 was obtained for blade profile of S-section Savonius rotor at an optimum overlap ratio of 30%. Tests on the full-scale prototype unit in natural wind indicated a maximum Cp of 0.32. Some works had been done on the design improvements of the Savonius rotor. One of the important parameter that affects the performance of the Savonius rotor is geometry of the blade. Goodarzi and Keimanesh [2] proposed to use two large Savonius turbine near the radiators of a natural draft dry cooling tower instead of previously proposed solid windbreakers. A numerical procedure has been used to predict the flow field unsteadily, and calculate the cooling improvement and power generation in turbines. Numerical results showed that rotating turbines could improve cooling capacity as the same order of solid windbreakers. It was surprisingly concluded that presence of cooling tower near Savonius turbine increased its power generation. Wenehenubun et al. [3] conducted an experimental study to investigate the effect of number of blades on the performance of the model of Savonius type wind turbine. The experiments used to compare 2, 3, and 4 blades wind turbines to show tip speed ratio, torque and power coefficient related with wind speed. A simulation using ANSYS 13.0 software showed pressure distribution of wind turbine. The results of study showed that number of blades influence the performance of wind turbine. Savonius model with three blades has the best performance at high tip speed ratio. The highest tip speed ratio is 0.555 for wind speed of 7 m/s. El-Askary et al. [4] proposed three methods of controlling the wind direction to improve the performance of Savonius rotor. The idea behind the new designs was to harvest the incoming wind to generate a wind jet to the concave side of the advanced blade and prevent the convex side of return blade from coming upwind stream. The prevented wind was guided in different designs to impinge the concave side of the return blade and hence to eliminate the negative torque and increase the exerted positive torque. The results showed that the suggested designs improve the performance of Savonius rotor in view of the power coefficient and the operation range. To enhance the aerodynamic performance of the Savonius wind rotor, Tartuferi et al. [5] developed two different approaches. The first one is based on the development of innovative airfoil shaped blades, while the second one concerns the use of a new curtain system, self-orienting relative to the wind direction. For the purpose of the present work has been applied a customized numerical model, previously validated by means of experimental data obtained at the environmental wind tunnel. The obtained results show that both the approaches here proposed, following two distinct guidelines for the development of new and more efficient rotor geometries, are able to produce sensible enhancements in terms of the energy performance of the Savonius wind turbine. In order to eliminate the low aerodynamic performance of Savonius wind rotors, Mohamed et al. [6] studied several shapes of obstacles and deflectors placed in front of two and three blade Savonius turbine. A rounded deflector structure was placed in front of two counter-rotating turbines. An experimental investigation was carried out by Golecha et al. [7] to identify the position of the deflector plate to yield higher coefficient of power for single stage modified Savonius rotor. When considering only the starting torque, it can be seen that, for some directions of the wind velocity, the starting torque of the standard Savonius configuration would be so low that the rotor could not start alone. Roy and Saha [8] conducted wind tunnel experiments with a newly developed two-bladed Savonius-style wind turbine specifically meant for a small-scale energy conversion. This novel shape of the turbine blade is evolved from a series of experiments with different types of blades in the recent past. The developed two-bladed turbine is tested in an open type test section and its performance is assessed in terms of power and torque coefficients. Experiments have also been conducted with other standard blades such as semi-circular, semi-elliptic, Benesh and Bach types in order to have a direct comparison. In this study, all the reported experimental data are inclusive of wind tunnel blockage corrections. Further, the effects of Reynolds number on the dynamic and static characteristics are also discussed. The present investigation demonstrates a gain of 34.8% in maximum power coefficient with the newly developed two-bladed turbine.Shigetomi et al. [9] measured the flow field around two Savonius turbines in close configurations using particle image velocimetry. The phase-averaged flow fields with respect to the rotation angle of the turbines revealed two types of power-improvement interactions. One comes from the Magnus effect that bends the main stream behind the turbine to provide additional rotation of the downstream turbine. The other is obtained from the periodic coupling of local flow between the two turbines, which is associated with vortex shedding and cyclic pressure fluctuations. Akwa et al. [10] discussed the influence of the buckets overlap ratio of a Savonius wind rotor on the averaged moment and power coefficients, over complete cycles of operation. The influence of the buckets overlap ratio on the moment and power coefficients is checked by changing the geometry of the rotor. The values of the moment and power coefficients obtained as a function of tip speed ratio and the buckets overlap of the rotor indicates that the maximum device performance occurs for buckets overlap ratios with values close to 0.15. Kamoji et al. [11] compared the helical Savonius rotor with the conventional Savonius rotor. D’Alessandro et al. [12] developed a mathematical model of the interaction between the flow field and the rotor blades. The aim of their research was to gain an insight into the complex flow field developed around a Savonius wind rotor and to evaluate its performance. They validated the model by comparing it with data obtained at Environmental Wind Tunnel (EWT) laboratory. Bhuyan and Biswas [13] studied a three bladed H-rotor with unsymmetrical cambered S818 airfoil blades, which shows self-starting characteristics at many of the azimuthal angles. However to make the rotor completely self-starting, the same H-rotor is incorporated in a hybrid system with Savonius rotor as its starter. It is found that the hybrid design fully exhibits selfstarting capability at all azimuthal positions, signified by the positive static torque coefficient values. For improving power performance of the hybrid rotor, the same is subjected to rigorous experimentations on the wind tunnel at different Reynolds numbers (Re).In previous work, Driss et al. [14-15] developed numerical simulation to study the turbulent flow around a small incurved Savonius wind rotor. The CFD code "Solid Works Flow Simulation" has been used to present the local characteristics in different transverse and longitudinal planes. In this paper, an experimental validation is needed to match the numerical results obtained from the simulation with the experiments conducted in the LASEM laboratories. Several values of the velocity were taken in the area surrounding the rotor and were compared with those found numerically. The good agreement between numerical and experimental results proves the validity of the adopted numerical method.
2. Experimental Set up
In this study, a wind tunnel equipped bya small incurved Savoniuswind rotoris designed and built to investigate the aerodynamic characteristics behaviour the wind rotor.
2.1. Wind Tunnel
Figure 1 shows the open type wind tunnel in which the experiments were conducted. The total length of the wind tunnel is 3857 mm. The test section is of 400 mm of width, 800 mm of length and 400 mm of height. The wind tunnel is equipped by an aspirator that ensures a stable and uniform air flow. The rotor is placed in the test section to take the experimental values.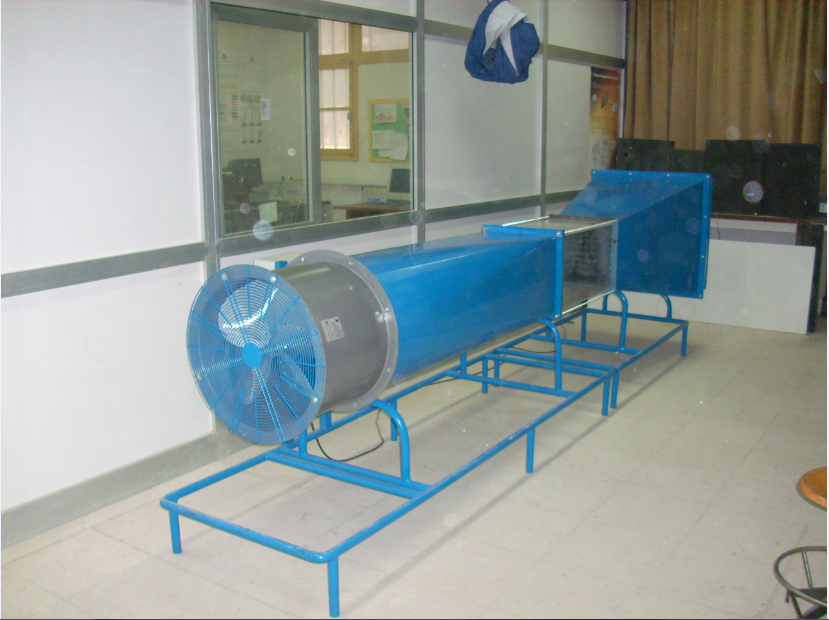 | Figure 1. Experimental device of the wind tunnel |
2.2. Wind Rotor
The turbine handled in this work is an incurved Savonius wind rotor composed by two buckets of incurved cylinder. Each one is of 300 mm of height, a diameter of 100 mm and 6 mm of thickness (Figure 2). The fixation element’s width is of 24 mm. The primary overlap considered is zero (optimal value according to the literature) and the secondary overlap is of 30 mm (the maximum value). 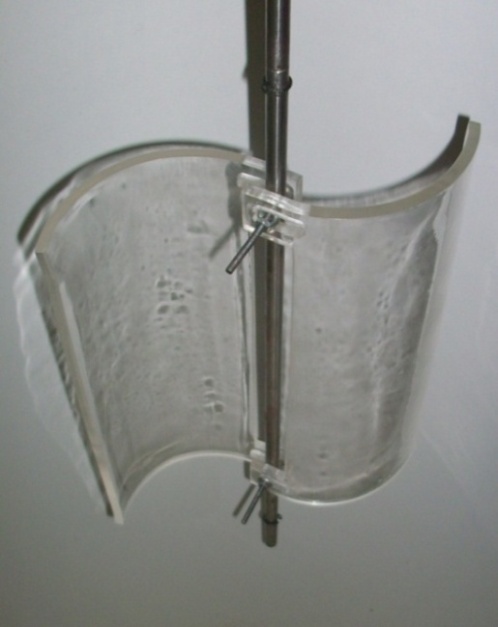 | Figure 2. Incurved Savonius wind rotor |
2.3. Measuring Instrumentation
Figure 3 shows the used anemometer to take the experimental values of air velocity. The characteristics of the anemometer are summarized in table 1. By dropping the probe in the appropriate position of the test section, the velocity value can be read directly from the digital screen of the anemometer [16].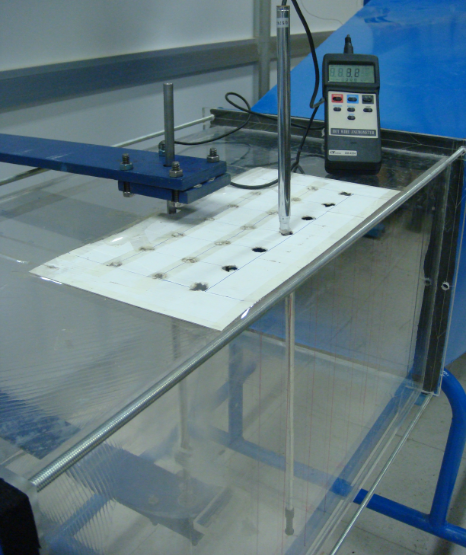 | Figure 3. Used anemometer |
Table 1. Anemometer description 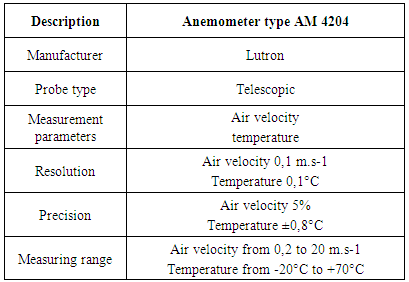 |
| |
|
3. Results
This section is dedicated to the numerical validation. Experimental values of velocity gathered from the experiments conducted in the LASEM laboratories are compared with the numerical values obtained by running a flow simulation program using the optimized meshing. The velocity profiles are chosen for points situated in the test section. The considered planes are defined by z=-50 mm and z=50 mm. The results for each plane are shown respectively in figures 4 and 5. For each transverse plane, values are taken along the directions defined by y=-150 mm, y=-100 mm, y=-50 mm, y=0 mm, y=50 mm, y=100 mm and y=150 mm. Both profiles give symmetrical values relative to the middle plane (x=0 mm). The velocity decreases in this plane because of the presence of the rotor in that region. Also, it has been observed that the velocity is globally constant in the region away from both the test vein walls; in which the velocity is set to zero as a boundary condition. In these conditions, the air speed values range between 0 m/s to 17 m/s. The velocity profiles present a changing allure with regards to the rotor position. Due to the rotor shape for which the curvature is not very important, the velocity values are slightly affected by the rotor. The velocity drops sharply only in the plane defined by x=0 mm, especially when we are close to the rotor. The convexity of the blade is recognizable due to the sudden increase in velocity that appears in the planes z=-50 mm for the points located respectively in the directions defined by x=-50 mm and x=50 mm. 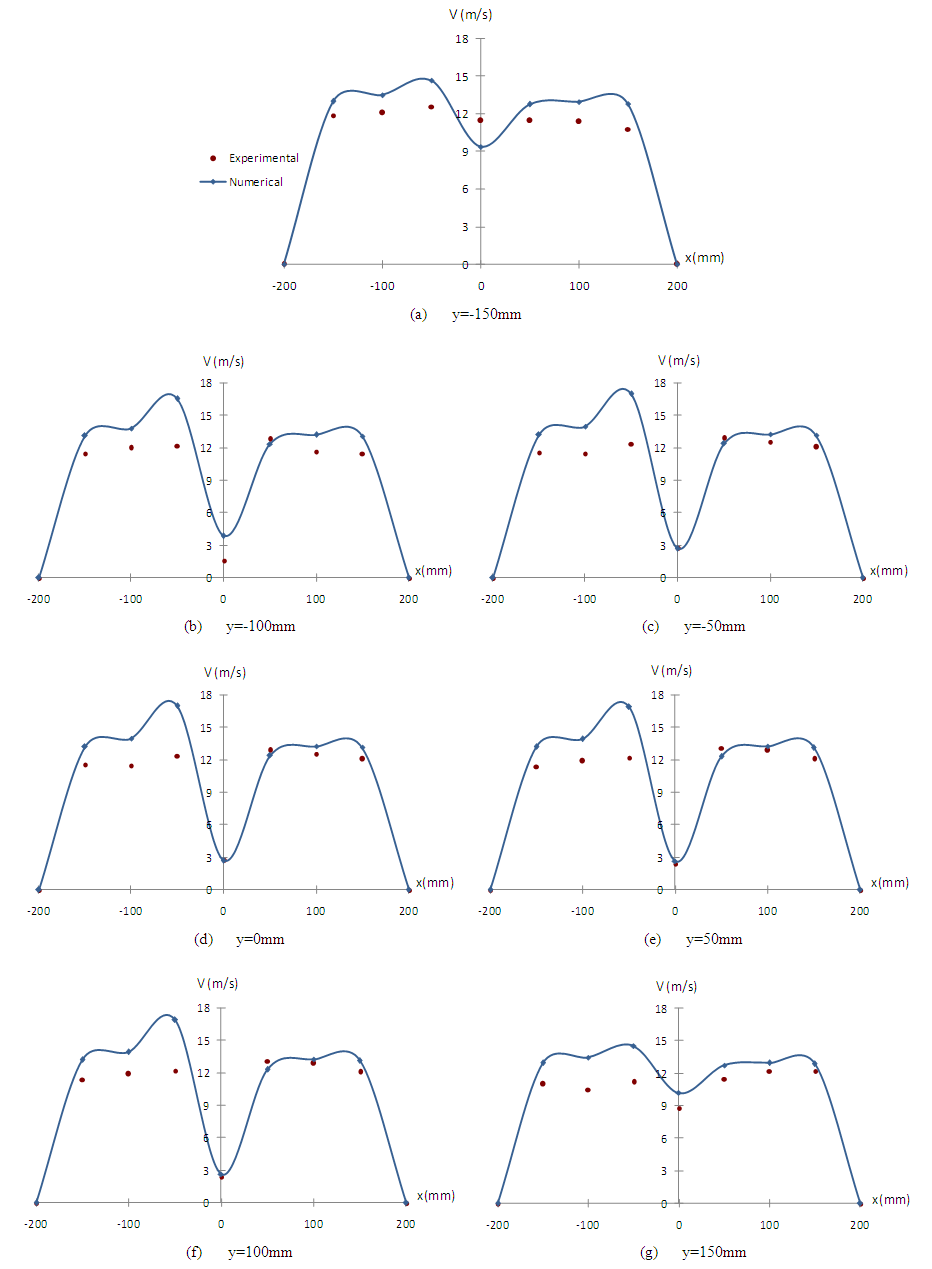 | Figure 4. Comparison between the numerical and the experimental velocity profiles in the plane z=-50 mm |
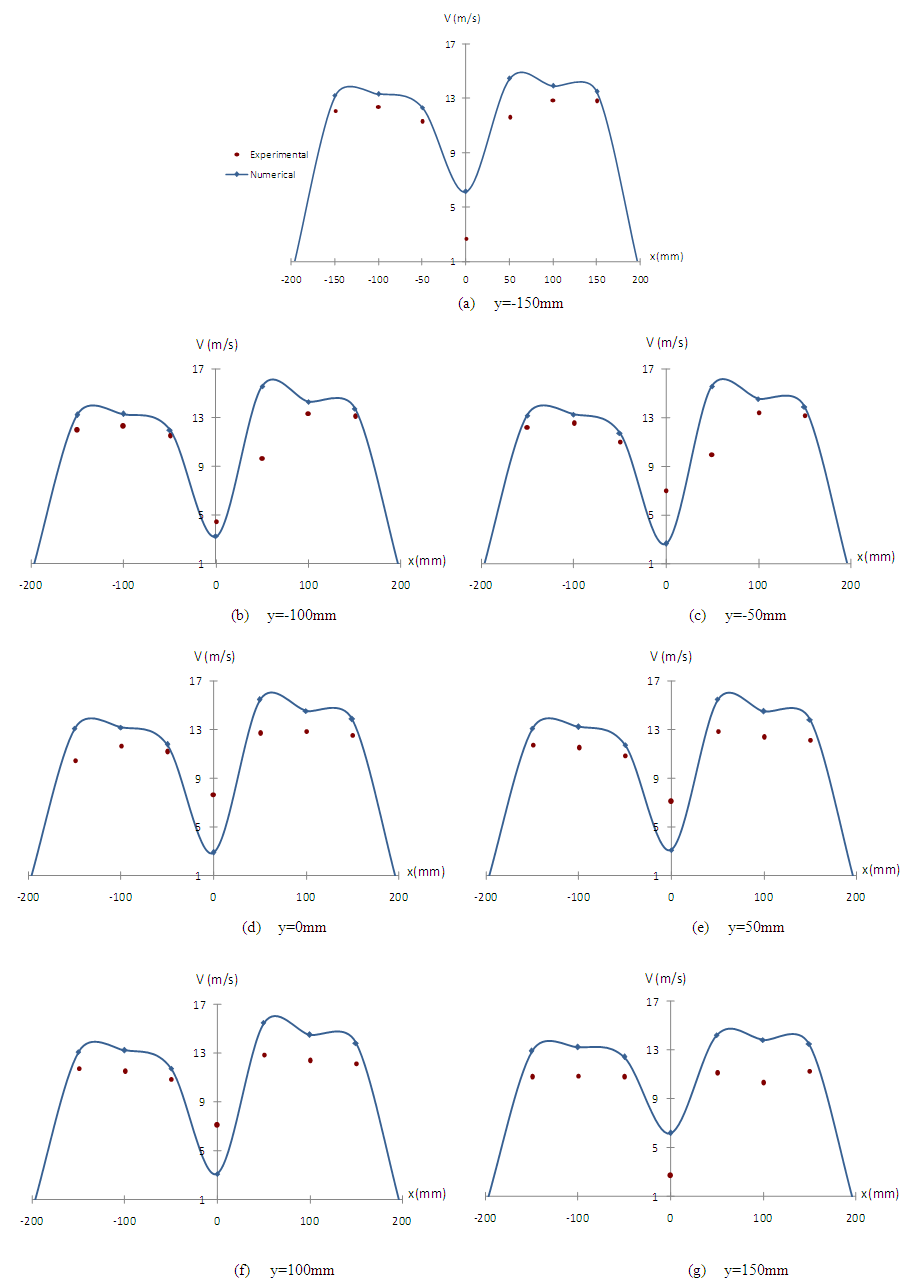 | Figure 5. Comparison between the numerical and the experimental velocity profiles in the plane z=50 mm |
The comparison between the experimental and numerical velocity values lead us to the conclusion that despite some unconformities, the values are comparable. The numerical model seems to be able to predict the aerodynamic characteristics of the air flow around the incurved Savonius rotor.
4. Conclusions
In order to test the model reliability, an experimental validation has been realized. The velocity values have been taken from the area around the rotor in the test section. Using an anemometer, several velocity values have been gathered in different planes. The experimental validation has shown comparable results between experimental and numerical velocity values. The numerical model can be considered as reliable. Indeed, it seems that this model is able to predict the aerodynamic characteristics of the flow.
References
[1] | Khan N, Tariq Iqbal M, Hinchey M, Masek V. Performance of Savonius Rotor as Water Current Turbine. Journal of Ocean Technology 4 (2009) 27-29. |
[2] | Goodarzi M, Keimanesh R. Numerical analysis on overall performance of Savonius turbines adjacent to a natural draft cooling tower. Energy Conversion and Management 99 (2015) 41-49. |
[3] | Wenehenubun F, Saputra A, Sutanto H. An experimental study on the performance of Savonius wind turbines related with the number of blades. Energy Procedia 68 (2015) 297-304. |
[4] | El-Askary WA, Nasef MH, AbdEL-hamid AA, Gad HE. Harvesting wind energy for improving performance of Savonius rotor. J. Wind Eng. Ind. Aerodyn.139 (2015) 8-15. |
[5] | Tartuferi M, D'Alessandro V, Montelpare S, Ricci R. Enhancement of Savonius wind rotor aerodynamic performance: a computational study of new blade shapes and curtain systems. Energy 79 (2015) 371-384. |
[6] | Mohamed MH, Janiga G, Pap E, Thévenin D. Optimization of Savonius turbines using an obstacle shielding there turning blade, Renewable Energy 35 (2010) 2618-2626. |
[7] | Golecha K, Eldho TI, Prabhu SV. Influence of the deflector plate on the performance of modified Savonius water turbine. Applied Energy 88 (2011) 3207-3217. |
[8] | Roy S, Saha UK. Wind tunnel experiments of a newly developed two-bladed Savonius-style wind turbine. Applied Energy 137 (2015) 117–125. |
[9] | Shigetomi A, Murai Y, Tasaka Y, Takeda Y. Interactive flow field around two Savonius turbines. Renewable Energy 36 (2011) 536-545. |
[10] | Akwa JV, Júnior GA, Petry AP. Discussion on the verification of the overlap ratio influence on performance coefficients of a Savonius wind rotor using computational fluid dynamics. Renewable Energy 38 (2012) 141-149. |
[11] | Kamoji MA, Kedare SB, Prabhu SV. Performance tests on helical Savonius rotors. Renewable Energy 34 (2009) 521-529. |
[12] | D’Alessandro V, Montelpare S, Ricci R, Secchiaroli A. Unsteady Aerodynamics of a Savonius wind rotor: a new computational approach for the simulation of energy performance. Energy 35 (2010) 3349-3363. |
[13] | Bhuyan S, Biswas A. Investigations on self-starting and performance characteristics of simple H and hybrid H-Savonius vertical axis wind rotors. Energy Conversion and Management 87 (2014) 859-867. |
[14] | Driss Z, Mlayeh O, Driss D, Maaloul M, Abid MS. Numerical simulation and experimental validation of the turbulent flow around a small incurved Savonius wind rotor. Energy 74 (2014) 506-517. |
[15] | Driss Z, Mlayeh O, Maaloul M, Abid MS. Dynamic study of an incurved Savonius wind rotor, pp. 1-8. International Symposium on Computational and Experimental Investigations on Fluid Dynamics (CEFD’2013)", March 18-20, 2013, Sfax, TUNISIA. |
[16] | Driss Z, Abid MS. Numerical and experimental study of an open circuit tunnel: aerodynamic characteristics. Science Academy Transactions on Renewable Energy Systems Engineering and Technology 2 (2012) 116-123. |