Abdelfattah Bilal Abdelsalam 1, Elkhawad Ali Elfaki 2, Mohammed Misbah Ridwan 3
1College of Engineering, Karary University
2College of Engineering, Sudan University of Science and Technology
3College of Graduate Studies and Scientific Res. Karary University
Correspondence to: Elkhawad Ali Elfaki , College of Engineering, Sudan University of Science and Technology.
Email: |  |
Copyright © 2015 Scientific & Academic Publishing. All Rights Reserved.
Abstract
Friction Welding is a solid state bonding in which heat is generated by conversion of mechanical energy into thermal energy at the interface of the work pieces during rotation under pressure. Friction welding of high speed to carbon steels was carried out by many researchers and they couldn’t reach 100% joint efficiency due to welding defects. This research is aimed at studying the influence of the friction phase parameters on the joint strength of the joint of samples consisting of high speed steel and medium carbon steel, welded by friction welding process. The parameters under question are: rotational speed, friction time and friction pressure. The forging pressure was fixed at 187 MPa and the forging time was fixed to15 seconds. The experiments were designed for the three parameters at three levels by Taguchi array method with three replications. 81 samples were welded, heat treated and subjected to tensile tests. The results were analyzed for mean and S/N ratio in order to study the influence of the parameters on the joint strength, using Minitab 16.1 software. Results show that: time has significant effect and pressure comes next. Speeds have no significant effect. The maximum joint efficiency was found to be 83%.
Keywords:
Friction phase parameters, Joint efficiency, Taguchi
array method, Minitab 16.1 software, S/N ratio
Cite this paper: Abdelfattah Bilal Abdelsalam , Elkhawad Ali Elfaki , Mohammed Misbah Ridwan , The Influence of Friction Phase Parameters on the Joint Strength of High Speed Steel Welded to Medium Carbon Steel, International Journal of Mechanics and Applications, Vol. 5 No. 1, 2015, pp. 10-15. doi: 10.5923/j.mechanics.20150501.02.
1. Introduction
In the continuous drive friction welding process, investigated in this research, one of the parts that are to be welded is rotated at constant speed, while the other is pushed toward the rotated part by a sliding action. The components are brought together under axial friction pressure for a predetermined friction time. Then, the drive is closed, and the rotating part is seized while the axial pressure being increased to a higher upsetting pressure for a predetermined time. Various researchers carried out different studies about friction welding. In 1971, Jenning and Lucas investigated the properties of the dissimilar materials welded by friction welding and the process parameters on friction welding method [3, 4]. Friction welding of high speed to carbon steels was carried out by many researchers and they couldn’t reach 100% joint due to welding defects. The main types of defects in the friction welded joints are considered due to the so-called shiny rings (carbides accumulations) on the side of the high–speed steel and a ferritic (complete decarburization) interlayer on the side of the structural steel .In 1970. Vill’ V I et al , examined the defects of the type of shiny rings and is due to the deposition of the high-speed steel on the structural steel in the form of a layer at the initial moment of the process. [5]. In1977 A. N. Popandopulo and G. D. Tkachevskaya studied the nature of shiny rings. They concluded that the shiny non-fusion rings consist of high-carbon martensite, a large amount of retained austenite and dispersed carbides mainly vanadium carbides. [6]. In 1989 O. N. Tanicheva, N. E. Orlova, and L. A. Kyun studied the nature of the defect "bright ring" and the ways of eliminating it. They concluded that the defect "bright ring" in fracture is not due to incomplete fusion, as has been commonly assumed. Bright rings are due to overheating of high speed steel to temperatures causing the formation of eutectic melts at places where carbides accumulate (carbide lines). [7]. In 1990 I. O. Khazanov and N. I. Fomin, their work was to determine the mechanism of formation of carbide films and to work out regimes of friction welding that eliminate the possibility of bright rings forming in the welded joint of the semi products of high-speed and structural steels, and of the zone of complete decarburization forming in the structural steel. They concluded that Carbide films forming in welded joints and manifesting themselves in the form of "bright rings" are secondary structures originating as a result of internal restructuring of the surface layers of the friction pair. Friction welding of blanks of steels R6M5 and 45 with the use of the effect of superplasticity of high-speed steel eliminates the formation of bright rings at the contact of the welded joints and of a zone of complete decarburization in the structural steel [8]. Many recommendations on the welding conditions resulting in a decrease the ‘shiny rings’ in the welded joints have been suggested. The recommendations are: to reduce the frequency of rotation of one of the welded components, to increase the pressure and duration during the heating and forging stages, to carry out heat treatment after welding to dissolve the carbides and immediately after welding to prevent decarburization. The objective of this work is to study, experimentally, the influence of friction phase parameters on the joint strength of samples of high speed steel, friction welded to medium carbon steel.
2. Experimental Work
Friction welding was carried out to joint M2 high speed steel and AISI 1040 medium carbon steel specimens. The experiments were carried out by a lathe machine modified to work as continuous friction welding machine. The axial friction pressure was obtained by the hydraulic attachment. The friction times were set and varied by timers supplied with the electrical and the hydraulic circuits of the machine. Figure (1) shows the main features of the machine. The dimensions of the specimen before welding is shown in figure (2). Friction phase is affected by three factors (parameters): rotational speed, friction pressure and friction time. The three factors were chosen at three levels as shown in Table (1). The design of experiments was based on Taguchi
array method, and using Minitab 16.1 Software, the experiment was designed to investigate the effect of friction phase parameters on the joint strength. The experiment was designed with 3 replications. 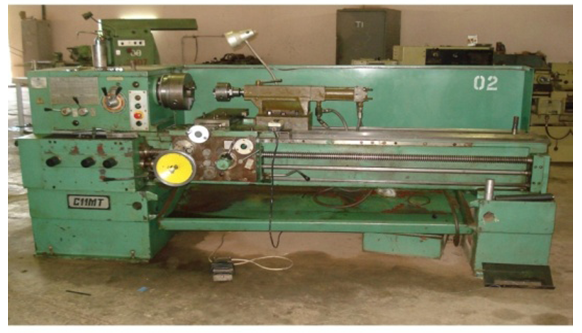 | Figure 1. The lathe machine modified into a friction welding machine |
Table 1. Factors and their levels and values 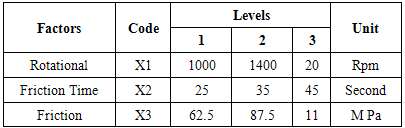 |
| |
|
3. Results
Samples were welded at constant forging pressure of 187 MPa and 15 second forging time .The surface temperatures were measured by an infrared device, and was found to be in the range of (1000 – 1100℃). The samples were tempered and annealed before being tested for strength. A Sample consisting of 27 pieces, was selected from each welded group, then checked for internal welding defects using x-ray techniques. The specimens were, then, loaded in tension up to fracture using a ZAPADPRIBOR tensile testing machine model MP-200, the ultimate tensile strengths were calculated and recorded as shown in Table (2).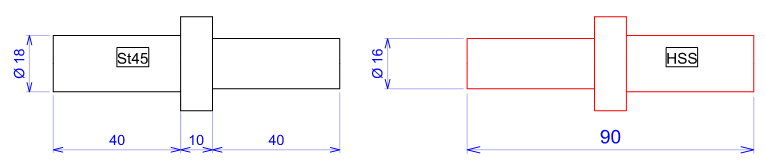 | Figure 2. Dimenstions of welding sample |
Table 2. The matrix of factors and response 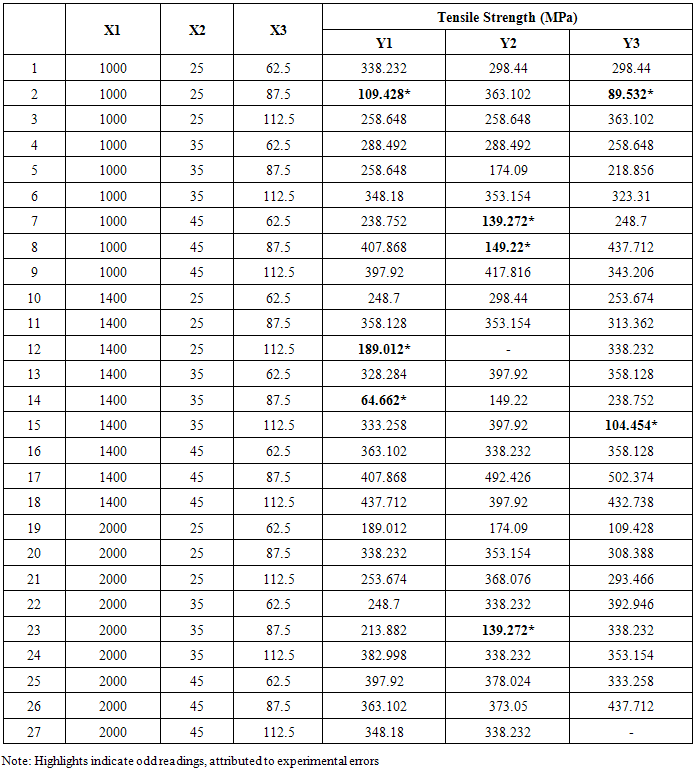 |
| |
|
4. Analysis of Results
The results of the experiments were analysed using the Taguchi method of analysis in order to estimate the contribution of individual factors, and to estimate the response under the optimum conditions. Minitab 16.1 software was used to analyse Taguchi approach for the mean and S/N ratio. The average S/N ratios, the larger-the-better characteristics, were used to maximize the tensile strength (Y) of the joint and the significant interactions. Minitab was also used to study the contribution of each factor on the tensile strength. The results are shown in tables (3), (4), (5), (6), and figure (3).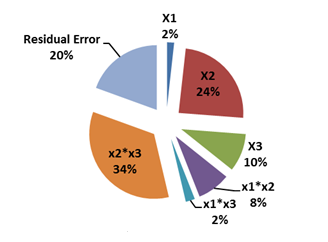 | Figure 3. Contributions of the process factors in the joint strength |
Table 3. Taguchi analysis results for MEANS and SN ratio 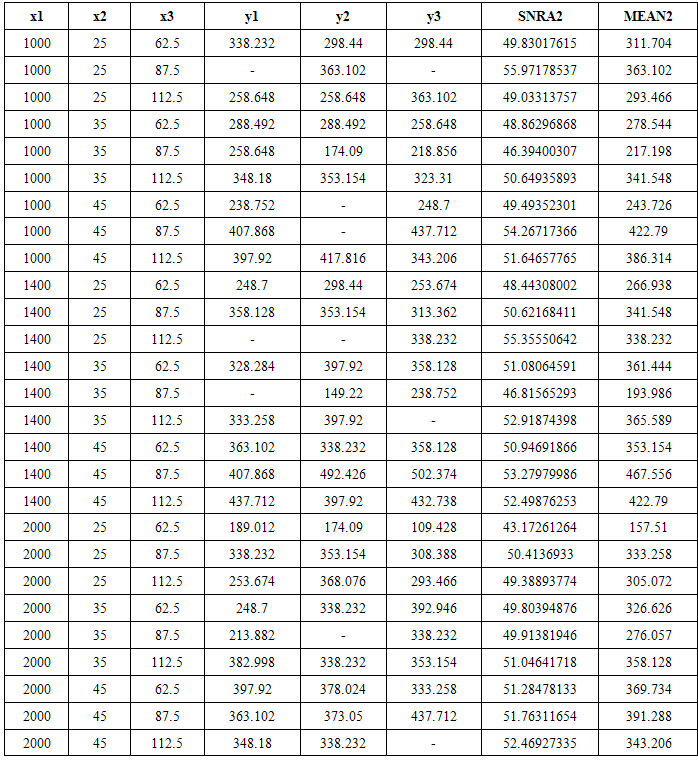 |
| |
|
Table 4. Analysis of Variance for SN ratios 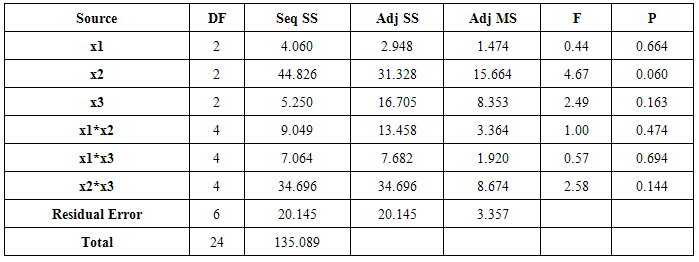 |
| |
|
Table 5. Analysis of Variance for Means 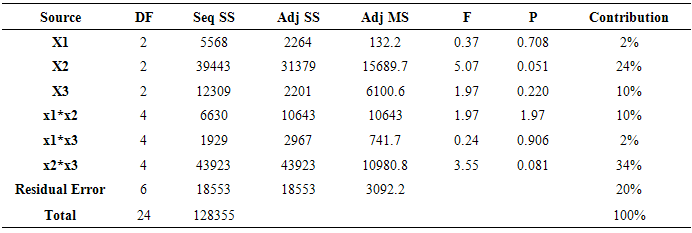 |
| |
|
Table 6. Response Table for Means 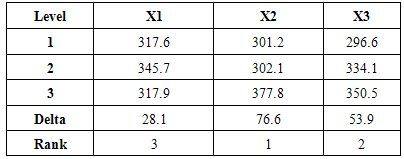 |
| |
|
5. Discussion
From table (4) result for S/N ratios, shows only the time (X2) (p = 0.06) is significant at a-level of 0.10, because their p-values are less than 0.10. From table (5) result for means, shows the time (X2) (p = 0.051), and the interaction between the time and pressure (X2X3) (p = 0.081), are significant at a-level of 0.10, because their p-values are less than 0.10. The Percentage Contribution of the Process Parameters of graph of figure (3) shows that the time has the highest contribution (24%), then the pressure (10%) and eventually the speed (2%) on the strength of the joint. The response of table (6) shows the average of the response characteristic for the mean for each level of each factor. For the mean, the ranks indicate that time has the greatest influence; pressure has the next greatest influence, and the speed is last.
6. Conclusions
The following could be concluded:- Time has significant effect on the strength of the joint, Pressure has next effect on the joint and Speed has less effect- To maximize the joint strength, the trend is to increase the time and pressure and hold the speed at specific value- The analysis show that x1 (the speed) has no significant effect on the model - The optimal value of the joint strength was obtained at the highest value of the time and the pressure and middle value of the speed. This emphasis that the effect of speed is not significant
References
[1] | AWS, ‘’Friction Welding Of Metals ‘’, New York, 1962. |
[2] | Tylecote. R.Y., “the Solid Phase Welding of Metals’’, London: Edward Arnold (Publisher) Ltd.; P. 1–150, 1968. |
[3] | Jenning, P., “Some Properties of Dissimilar Metal Joints Made by Friction Welding ", Advances In Welding Processes, Solid Phase Joining Processes, Proceeding of Conference, The Welding Institute, Abington Hall, Cambridge, 1971. |
[4] | Lucas, W., “Process Parameters and Friction Welds’’, Met Const Brit, Weld Journal, 1971. |
[5] | S.F. Gnyusov and Eatrushchenko, “Friction welding R6M5 steel in the superplastic condition: the mechanism of formation of structural imperfections and methods of removing them”, Welding International, Selected from Svarochnoe Proizvodstvo, vol, 18, 2004. |
[6] | N. Popandopulo and G. D. Tkachevskaya, “Structure of Shiny Nonfusion Rings in Friction Welded High-Speed Steels”, Leningrad Polytechnic Institute, Translated from Metallovedenie i Termicheskaya Obrabotka Metallov, No. 2, pp. 64-65, February, 1977. |
[7] | O. N. Tanicheva, N. E. Orlova, and L. A. Kyun, “Nature of the Defect (Bright Ring) Forming In Friction Welding Of Tool Steel”, Plenum Publishing Corporation, March,1989. |
[8] | O. Khazanov and N. I. Fomin, “Structure and Properties of Joints of Steels R6m5 and 45 Obtained by Friction Welding”, Plenum Publishing Corporation, June, 1990. |
[9] | S. F. Gnyusov; E. A. Trushchenko; B. F. Sovetchenko; N. A. Azarov, “Friction welding R6M5 steel in the superplasticity condition. Development of the welding algorithm and determination of the range of variation of the welding conditions”, Welding International, 2004. |
[10] | R. ĆIRIĆ, N. RADOVIĆ, “Dynamic Recrystallization in M2 Tool Steel during Friction Welding”, Journal of Metallurgy, Association of Metallurgical Engineers Serbia and Montenegro AME. |
[11] | Ranjit. K. Roy, “A Prime on the Taguchi Method”, Van Nostrand Reinhold, 1990. |
[12] | Genichi Taguchi, Subir Chowdhury, Yuin Wu, “Praise for Taguchi’s Quality Engineering Handbook”, John Wiley, 2005. |
[13] | W.J. De Coursey,” Statistics and Probability for Engineering Applications with Microsoft® Excel”, Elsevier Science (USA), 2003. |
[14] | SANFORD WEISBERG, “Applied Linear Regression - Third Edition”, John Wiley & Sons, 2005. |
[15] | Howard J. Seltman, “Experimental Design and Analysis”, http://www.stat.cmu.edu/~hseltman/309/Book/Book.pdf, 2012. |
[16] | Andreas Antoniou, Wu-Sheng Lu, “PRACTICAL OPTIMIZATION Algorithms and Engineering Applications”, Springer Science +Business Media, LLC, 2007. |
[17] | Robert L. Mason, San Antonio, “Statistical Design and Analysis of Experiments with Applications to Engineering and Science - Second Edition”, JOHN WILEY & SONS PUBLICATION, 2003. |
[18] | Andrey Popov, “GENETIC Algorithms For Optimization Programs for MATLAB ® Version 1.0 - User Manual”, TU – Sofia, 2003. |