Majid Elyasi
Faculty of Mechanical Engineering, Babol University of Technology, P.O. Box 484, Babol, Mazandaran, Iran
Correspondence to: Majid Elyasi, Faculty of Mechanical Engineering, Babol University of Technology, P.O. Box 484, Babol, Mazandaran, Iran.
Email: |  |
Copyright © 2012 Scientific & Academic Publishing. All Rights Reserved.
Abstract
The V-ring indenter plays an important role to increase the quality of cutting edge surface of the blanked part in fine-blanking process. The present study has been undertaken in order to investigate the new possibilities of increase in quality of the cut-surface of steel elements. For the intended purpose, a numerical simulation of the fine-blanking process was carried out. The numerical calculations were performed with the ABAQUS/EXPLICIT 6.9 software. The mechanism and effects of the V-ring indenter could be clarified on the basis of geometrical (parametric) characteristics of the V-ring. The parameters that were considered are the height, position, tip radius and angle of the V-ring indenter. It is found that the height, position and angle of the indenter have a major influence on the fine-blanking process, followed by tip radius of the V-ring indenter.
Keywords:
Fine-Blanking, V-Ring Indenter, Cutting Edge Surface
Cite this paper: Majid Elyasi, An Investigation on the Parametric Analysis of V-ring Indenter Mechanism in Fine-blanking Process, International Journal of Mechanics and Applications, Vol. 3 No. 4, 2013, pp. 76-80. doi: 10.5923/j.mechanics.20130304.03.
1. Introduction
Fine blanking is a sheet metal process producing smooth-sheared edges over the full workpiece thickness in one single action, whilst conventional blanking results in an approximate one-third smooth zone and a two third fracture zone. The fine blanking process can produce components or parts having a high degree of dimensional accuracy and a good surface finish. Therefore the fine blanking technique has been widely applied to produce small and precision such as components of watches and automobiles, and small items of measuring equipments.[1]The quality of the blanked surface directly affects the product quality. Secondary operations such as machining process are usually needed to obtain a smooth cut surface that would lead to the increase in production time and labour costs. Fine-blanking can ensure the dimensional accuracy to all parts and improves the product quality.[2] The shearing process such as the blanking and piercing of sheet metals has been used often to prepare workpieces for subsequent forming operations. In this process, a sheet material is cut by using a punch and die on a mechanical or hydraulic press. One of the most important things in the shearing process is the quality of sheared edge, which is affected not only by the material characteristics but also by the process parameters such as the clearance between the punch and the die, the blank holding force, and the sharpness of the edge of the punch and the die. So far, the effect of these parameters on the shearing characteristics has been investigated mainly by an empirical approach.[2-4] The special characteristics of the fine-blanking process are a small clearance, and a high pressure on the blankholder and the counterpunch, compared with the conventional blanking process. Moreover, the V-ring indenters are formed as a raised ridge usually on the blankholder and sometimes on the die.[5] In sheet metal forming processes, the forces and forming limit are affected by a number of factors, such as material properties and tool design. Fine-blanking is such a metal forming process in which the punch penetrates entirely into sheet metal material and the blanked part exhibits a high degree of dimensional accuracy and a smooth surface. This process is usually applied to produce precise parts such as components of watches, automobiles and measuring instruments.[6] Some researchers focused on the fine-blanking process. Thipprakmas et al.[6] have studied the geometry and position of V-ring indenter in fine-blanking process using Taguchi method. They concluded that the application of the V-ring indenter increased compressive stress both before and during the cutting phase. The V-ring indenter significantly suppressed the increased rotation of material flow during the cutting phase, thereby causing increased hydrostatic compressive stress. Therefore, crack formation was prevented. The application of an appropriate V-ring indenter which resulted in the closed packed rotation of the material flow and the increasing of hydrostatic compressive stress on the shearing zone could prevent crack formation, and a larger smooth cut surface on the fine-blanked surface could be obtained.Kwak et al.[7] have studied the effect of die clearance on shear planes in fine-blanking process using finite element analysis by a rigid–plastic FEM code, DEFORM-2D. They found that die-roll width and depth of the shear plane increase with increasing die clearance. By decreasing the clearance, the depth of the fracture zone was decreased and the depth of the shear zone was increased. FE analysis showed that by reducing the clearance between the punch and die the quality of the sheared parts was improved.Fan et al.[8] have examined the damage of AISI-1045 and AISI-1025 steels in fine blanking with negative clearance. In their research, they focused on the effect of the blank thickness and tensile strength on forces in fine-blanking process by theoretical formulation and experimental approach. They concluded that the damage value of negative clearance blanking is lower than that of conventional blanking, and the better material plasticity, the lower the damage value and the better blanking quality. From the preliminary investigations, it was revealed that the effect of geometrical parameters of V-ring on cutting edge surface of the workpiece is more than that of the other parameters of the process. Therefore, in this research, the results of the effect of geometrical parameters of V-ring indenter on the cutting edge surface of workpiece are presented.
2. Geometry of Workpiece
The feasibility of producing a flat part by the fine-blanking process is determined by the geometrical shape of the part and the thickness and strength of the material. These three factors determine whether production by fine blanking can be rated as simple, medium-difficult, difficult or impossible.The blanked part should be analyzed for fine-blanking is assumed to be axisymmetric, its size and some parameters of the die being shown in Fig. 1. Also, the material properties and some process parameters are listed in Table 1.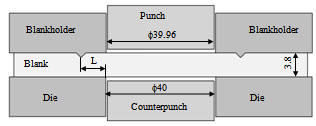 | Figure 1. The illustration of the process (all dimensions in mm) |
It is assumed that the V-ring has already indented into the sheet material. The deformation inside the narrow clearance zone is too high corresponding to the regions away from the zone. Therefore, only the within or near the clearance zone is to be analyzed. For this reason, those areas far from the clearance zone can be ignored and hence the region to be analyzed can be reduced to a smaller section.The blank holder with a V-ring indenter shown in Fig. 2 was used to elimination the sudden release of the elastic energy of the press subsequent to the initiation of fracture. 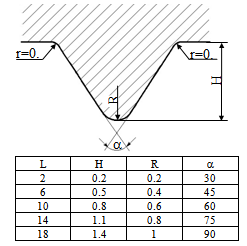 | Figure 2. Geometry used in the fine-blanking simulations; the table defines the different V-ring geometries used (dimensions in mm and angles in degree) |
Table 1. Material data and other process parameters 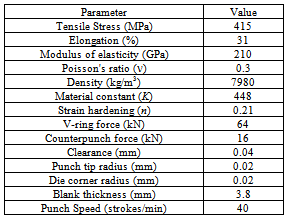 |
| |
|
3. Simulation Procedure
The finite element software, ABAQUS/EXPLICIT 6.9, was used for simulation. The simulation was conducted in two steps. At the first, the V-ring localizes on the blank and then in the second step the punch will move down. The die, punch, blank and blank holder were modelled as 2D model due to axial symmetry of the parts. The parts were modelled by 2D analytical rigid element and because of the type of the element selected; the die was not meshed and analyzed. The blank was modeled as 2D axisymmetric with CAX4R 4-node bilinear axisymmetric quadrateral shell elements. The 4-node mesh was assigned for the sheet but element size gets closer from outer borders of the model to the center. In order to obtain better simulation, the mesh topology of the partition on the sheet that the punch will localize and shearing will occur on there, are fine, while the mesh for the other regions are course. The Displacement mode was used for loading. The shear damage criteria with Ks value of 0.3 was modified for material properties and the 92 fracture strains, shear stress ratios and strains rates were described. Also, the elastic, plastic and density data of material were included.The contact between the die surfaces and the blank was defined as surface-to-surface and tangential behavior in ABAQUS. A penalty-based contact treatment was prescribed between the tooling and the blank. The coulomb friction coefficient between the workpiece and the tool surfaces was considered to be 0.15 in the simulations. The material data and other simulation parameters are stated after in Table 1.
4. Experimental Investigation
In order to judge the reliability of the numerical simulation, a relative experiment of fine-blanking was conducted. The fine-blanking die-set that was designed and manufactured for producing the workpiece is shown in Fig. 3(A). 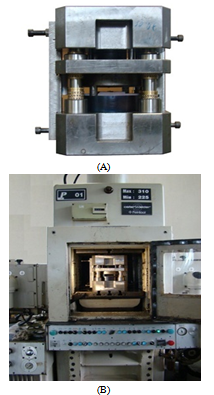 | Figure 3. (A) The fine-blanking die-set, (B) the die-set mounted on the fine-blanking press |
A fine-blanking press with 160 T was used for carrying out the experiments which is shown in Fig. 3(B). The width of the blank was 52 mm and it was fed into the press by a feeder. An outer guidepost, an inner guidepost and a bush are used jointly to maintain the accuracy of movement. Punch and die are made with cemented carbides. SKD2 is used to make a push plate and die plate. The punch speed was 40 strokes/min and the V-ring indenter force and counterforce was set at 64 and 16 kN, respectively. Some process parameters which were used in the experiments are listed in Table 1.For producing the workpiece, adequate care was taken on cutting procedure to eliminate any damage on cutting tool due to shear-shock and vibrations. For repeatability of tests, each test was performed three times and the average of results was considered. In addition, for measuring of the workpiece profile, a profile projector was used.
5. Results and Discussions
To investigate the effect of V-ring indenter parameters on the fine blanked surface feature, FE-simulations were carried out. The position, tip radius, height and angle of the V-ring were set at the variation parameters.The variation of fine-blanked surface ratio versus V-ring position is shown in Fig. 4. It can be seen from the plot that by increasing the distance of V-ring position from the edge of die hole, the burnished zone slightly increased and then decreased. In addition, the rollover zone and burr slightly decreased and then increased. It is obvious while V-ring gets far from the edge of the die hole, the amount of burnished zone decreases where as the amount of rollover zone and burr increases. Therefore V-ring by getting far from the edge of the die hole makes the process of fine-blanking close to the process of blanking. 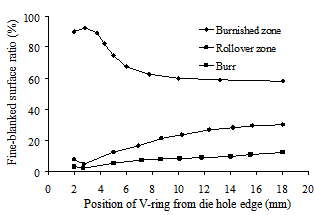 | Figure 4. Variation of fine-blanked surface ratio according to V-ring position, obtained from simulation |
Fig. 5 shows the effect of the V-ring’s height on the fine blanked surface ratio. It is quite visible in the figure that the low height of V- ring makes the closeness of fine- blanking process to the blanking process, therefore the smoothness of cutting surface edge decreases, but the large height of V-ring makes the smoothness of cutting surface edge better. It is also clear in the figure that the amount of burnished zone has been increased whereas the amounts of rollover zone and burr have been decreased. Again, the smoothness of cutting surface edge decreases with a low slope if there is too much height of V-ring, because the flow of metallic material also decreases.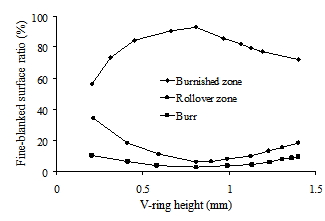 | Figure 5. Variation of fine-blanked surface ratio according to V-ring height, obtained from simulation |
Fig. 6 shows the percentage changes of cutting surface edge on the radius of the top of V-ring. A glance on the figure shows that by increasing the radius of the top of the V-ring, the pressure of the top of the V-ring will be decreased in the act of sinking the top into the sheet therefore the action of V-ring also decreases a little bit. Indeed, the effect of this parameter is inappreciable. As the result, by increasing the radius of the top of V-ring makes the amount of burnished zone decreases and the amounts of rollover zone and burr increase.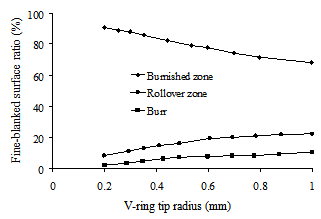 | Figure 6. Variation of fine-blanked surface ratio according to V-ring tip radius, obtained from simulation |
Fig. 7 illustrates the effect of V-ring angle on the fine-blanked surface ratio. As it is shown in the figure, by increasing the V-ring angle the mentioned ratio corresponding to burnished zone increases, but the amount of rollover zone and burr decreases. Figs. 4 to 7 show that the effects of parameters such as the position and the height of V-ring is more than the other parameters which are the radius of top of the V-ring and its angle. Also in a comparison, the effect of V-ring’s height is more than the effect of its position, because by decreasing the height of V-ring, it will loose its height gradually until it will be omitted. This leads to the changing of the process of fine-blanking into the process of blanking. However increasing the distance of V-ring’s position from the edge of the die hole, decreases its effect, but is never zero.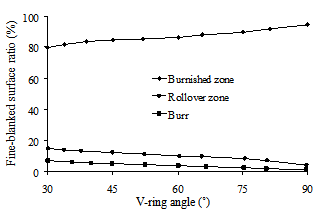 | Figure 7. Variation of fine-blanked surface ratio according to V-ring angle, obtained from simulation |
Fig. 8 shows the comparison between the profile of the cutting surface obtained from simulation and experiment at L= 3 mm, H=0.8 mm, R=0.2 mm α=90˚. By considering this figure, it is understandable that in the best condition of the chosen parameters, the amount of burnished zone is more than the amounts of rollover zone and burr. It means that the parameters are optimum which can be accounted by one of the ways of optimization. Moreover, the accounted amounts of burnished zone and burr also depend on other parameters such as the die’s looseness and type of the workpiece. As shown, it is seen that, there is a good agreement between the results of simulation and experiment.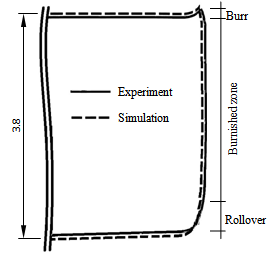 | Figure 8. The profile of cut edge surface obtained from simulation and experiment at L=3mm, H=0.8mm, R=0.2mm and α=90˚, dimension in mm |
6. Conclusions
Finite element analyses were performed to investigate the effect of geometrical parameters of V-ring indenter on the cutting edge surface. The obtained results indicated that when the V-ring position from die hole edge was increased, the smooth sheared zone decrease. In contrast, the rollover and burr increases. Also, when the V-ring height was decreased, the smooth sheared zone decrease and the rollover and burr increases. In addition, when the V-ring tip radius was increased, the smooth sheared zone decrease and the rollover and burr increases. Also, when the V-ring angle was increased from 30˚ to 90˚, the smooth sheared zone increases and the rollover and burr decrease. Moreover, a good correlation between the experimental and simulation results was obtained.
References
[1] | M. Elyasi and V. Daeizadeh, Effect of shape of workpiece on forming force in fine blanking process, Materials Research Innovations (2011), Vol. 15, pp. 386-389. |
[2] | V. Daeizadeh and M. Elyasi, Research on influence of material properties and blank geometry on forming force in fine blanking process, Materials Research Innovations (2011), Vol. 15, pp. 370-372. |
[3] | M. Elyasi and V. Daeizadeh, A study of forming force in the fine-blanking process using the theoretical predication and experimental approach, AMPT conference, (2010) October 24-27; Paris, France. |
[4] | V. Daeizadeh, M. Elyasi and M. Mollaei, Forming Force Analysis in Fine-blanking Process by Experimental Approach and Analytical Formulation, Applied Mechanics and Materials (2012), Vols. 110-116, pp. 2723-2729. |
[5] | T.C. Lee, L.C. Chan and B.J. Wu, Further investigation of the fine-blanking process employing large deformation theory, Journal of Materials Processing Technology (1997), Vol. 66, pp. 258-263. |
[6] | S. Thipprakmas, Finite element analysis of V-ring indenter mechanism in fine-blanking process, Materials and Design (2009), Vol. 30, pp. 526-531. |
[7] | T.S. Kwak, Y.J. Kim and W.B. Bea, Finite element analysis on the effect of die clearance on shear planes in fine blanking, Journal of Materials Processing Technology (2002), Vols. 130-131, pp. 462-468. |
[8] | W.F. Fan and J.H. Li, An investigation on the damage of AISI-1045 and AISI-1025 steels in fine-blanking with negative clearance, Materials Science and Engineering A (2009), Vol. 499, pp. 248-251. |