Willy Arnold Donda Fonchou1, 2, André Abanda3, Fabien Kenmogne1, Moussa Sali1, 4, Jérémie Madja Doumbaye5
1Department of Civil Engineering, Advanced Teacher Training College of the Technical Education, University of Douala, Douala, Cameroon
2Laboratory of Mechanics, Advanced Teacher Training College of the Technical Education, University of Douala, Cameroon
3Department of Civil Engineering, National Advanced Polytechnical School of Douala, University of Douala, Cameroon
4Laboratory of Materials, Mechanics and Civil Engineering, National Higher Polytechnic School of Maroua, University of Maroua, Cameroon
5Department of Civil Engineering, National Advanced School of Engineering Yaounde, University of Yaounde, Cameroon
Correspondence to: Willy Arnold Donda Fonchou, Department of Civil Engineering, Advanced Teacher Training College of the Technical Education, University of Douala, Douala, Cameroon.
Email: |  |
Copyright © 2023 The Author(s). Published by Scientific & Academic Publishing.
This work is licensed under the Creative Commons Attribution International License (CC BY).
http://creativecommons.org/licenses/by/4.0/

Abstract
The selected waste glass powder is used in the present paper as a partial replacement for cement in order to enhance concrete performances. The waste glass powder is obtained using some specific engineering technics, which includes the recovery of some samples of varied glass waste, cleaning, grinding, and pulverisation. The waste glass powder found has as size closed to 75m, which is nearly equal to that obtained for the local Porland cement grain particle. These fines glasses are then progressively substituted in concrete samples as a partial replacement of cement at certain percentages, namely 0%, 5%, 10%, and 15%. In order to know the chemical constitutions of the waste glasses powder obtained here, the Fourier transform infrared spectrometer, as well as the chemical (XRF analysis) are performed. Some tests are then conducted on samples created, both in the fresh and hardened states. These tests include: the Abrams cone slump test, the density measurement for fresh concrete, the hardened concrete bending, the compression, and water absorption tests. For hardened concrete, the cubic specimens of 40 × 40 × 40 mm3 are used to estimate compressive strength for each sample and those of 40 × 40 × 160 mm3 to assess flexural strength. As results, we found as subsidence 150mm, 152mm, 155mm, and 157mm, respectively, for 0%, 5%, 10% and 15% of selected waste glass powder from the slump test. The specific density yields 2211.34 kg/m3; 2224.20 kg/m3; 2186.24 kg/m3; and 2181.54 kg/m3 for concretes containing 0%, 5%, 10%, and 15% of glass powder, respectively. For hardened concrete, the substitution rate of 10% is found to be the adequate amount of replacement for getting an enhanced concrete in terms of mechanical resistance, density and water absorption rate.
Keywords:
Waste glass powder, Concrete, Fourier transform infrared spectrometer, X-ray fluorescence
Cite this paper: Willy Arnold Donda Fonchou, André Abanda, Fabien Kenmogne, Moussa Sali, Jérémie Madja Doumbaye, Partial Replacement of Cement with Waste Glass Powder in Concrete for Sustainable Waste Management: A Case Study of Concrete Incorporating Sand and Waste Glass from the Douala City of Cameroon, American Journal of Materials Science, Vol. 13 No. 1, 2023, pp. 7-21. doi: 10.5923/j.materials.20231301.02.
1. Introduction
In constructions and structures engineering, concrete is the most often used material. It is made with a mixture of cement paste and aggregates; this is why it is necessary to know the quantity and mixing of the various components which are the crucial phases in the production of concrete [1]. It has been proved that cement serves as the binding agent for other composition elements, and it occupies 7% to 15% as rate in the concrete matrix, meaning that cement is a crucial component [2]. Let us mention that the concrete invented by the British engineer John Smeaton in 1756 is composed of cement or hydraulic binder, sand, and aggregate. In order to have increasingly resistant concrete and also less pollutant, certain materials in the forms of powders were partially added in the concrete to replace cement [2,3]. To name just a few, the substitution of Portland cement with pozzolanic effect waste, such as fly ash and silica fume has been the subject of much investigation, while in the works shown in [2,6,7], glass powder are used to partially substitute cement in concrete.Particularly in Cameroon, glass materials are increasingly used for packaging in industries [3], and they are continually accumulating in nature and landfills due to their non-biodegradability, or ability to resist perishability for an extended period of time, they pose an environmental risk. This continuous and persistent build up might thus have a strong detrimental influence on ecosystem [21]. It is crucial to find adequate solution for environmental concern, and also to develop an appropriate technique to reuse the glass trash. Glass might be recycled in concrete due to its raw material, particularly sand [21-23]. Global glass production reached 140 million tonnes in 2016, of which 72 million tonnes were flat glass. Of this amount, 50% was produced in China, followed by 15% in Europe, 10% in North America, 7% in Southeast Asia, 5% in Japan, and 4% in South America. In contrast, in 2010, out of a total production of 56 million tonnes, low-grade flat glass (primarily in China) made up 20 million tonnes, drawn glass made up 1 million tonnes, and laminated glass made up 2 million tonnes [4]. Recycling glass trash could have both economic and environmental benefits along with increasing glass recycling, other factors that help address the key environmental problems associated with solid waste management include the use of cullet as a raw material addition, which enables glass companies to consume less energy and emit fewer greenhouse gases, and the reduction of greenhouse gas emissions [5].Glass scrap from various sources may be gathered and repurposed in the cement and concrete manufacturing industry. Through the substitution of aggregates, cement, and cementitious admixtures, it is probable that several recovery channels will open up, providing the construction sector with practical answers for taking part in sustainable growth. Glass is mostly made of silica, thus using it as a partial substitute for cement in concrete might be an environmentally friendly technical-economical answer. Numerous studies have been conducted to determine the ideal amount of recycled glass that may be used to partially replace cement in concrete. According to works shown in [2,6,7], the ideal ratio of glass powder that can be substituted of cement is 10%, in order to retain mechanical strength. However in [8,9,10] it was proved that 15% of glass powder is the ideal content. Furthermore, it was determined by [11,12] that 20% of waste glass is the ideal amount to add to concrete in order to increase its performance. [13] found that glass powder may substitute cement up to 20% of the time without compromising the concrete's flexural and tensile strength. [14]. It is then obvious that the adequate rate for the glass-wastes powder that can be substituted to cement in concrete is variable, and may be function of the chemical constituents of wastes and the location where experiments are conducted. This is what motivated us to use recycled glass powder in order to create a more durable and lightweight concrete, with a particular attention carried on the characterising of various samples of recycled glass powder beforehand using FTRI and FRX to see their chemical constitution. Let us mention that the manufacturing of glass could be achieved by melting the combination of sodium carbonate, silica, limestone (CaCO3) and dolomite (Ca Mg(CO3)2), while some specific characteristics of glass like its colour can be achieved by using a special additive (see [15] and references therein). There are a lot of variety of glasses all over the world, depending on the rate of glass constitutes, the place and industry where glasses are made. This is why as outlined above, the ideal amount of recycled glass that may be used to partially replace cement in concrete, leading to better mechanical characteristics, varies from one experiment to other, which is probably due to the nature of sand, the rate of constitutes of cement, as well as the place where experiments are conducted, which are variable. The most recent works of G. M. Sadiqul Islam et al in 2017 [16], of S.P. Kanniyappan and T. Muthukumaran in 2018 [17], as well as the work of Daban A. Muhedin and Rahel K. Ibrahim in 2023 [18], which have studied the effects of waste glass powder as partial replacement of cement and sand in concrete prove that the works on the topic are still opened and deserve a particular attention. This is what motivated us to carry an emphasis on the use of glass powder as partial replacement of cement, with a particular attention carried on glass waste and sand over the city of Douala Cameroon, which is new in the context of engineering science. Thus the paper is organized as follows:In section 2, we present the material and methods, among which we present the technics to obtain the glass powder from glass waste, then we present the cement, as well as tests necessary to seek mechanical characteristics. Following in section 3 by the presentation of results and the discussions provided.
2. Material and Methods
2.1. Materials Used in the Study
The materials used here are: waste glass powder, the ordinary Portland cement, sand, gravel and tap water.
2.1.1. Waste Glass Powder
2.1.1.1. Process of Obtaining Glass Powder
In this subsection, the description of the full procedure of acquiring the samples of various materials analysed is done, specifically the samples of recycled glass powder. This sampling was done as follows - The glass samples were collected from the various landfills of Douala, city of Cameroon, as well as in nature, with the aim to gather as many glass samples as possible to make the study more efficiency. Figure 1 (a) shows an example of some samples glasses collected containing beer and wine bottles.- Then a simple cleaning of all the collected samples was done with the sponge and clean water, after which it follow the crushing process, which is most necessary, and which will facilitate the grinding process. Figure 1(b) shows samples of crushed glass found in the laboratory.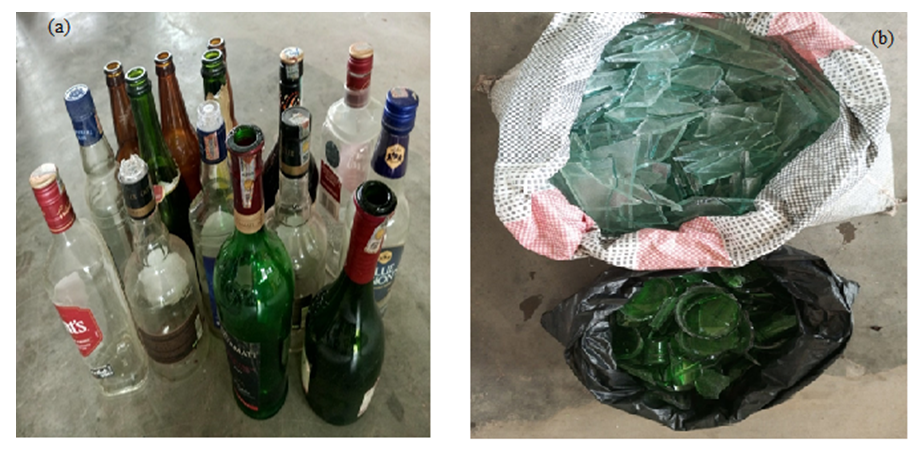 | Figure 1. (a): Waste glass collected, (b): Manually crushed glass bottles |
- The grinding of the diverse recycled glass samples collected, cleaned, and crushed is done with a grinder and allowed to get glass particles with granularities ranging from more than 125 mm to less than 0.063 mm. Although sifting will help to produce finer samples, it should be noted that the sieving procedure is not required because the same results may be obtained by just heating and spraying. This grinding is done in the mechanics laboratory of the advanced teacher’s training college of the technical education of the University of Douala, Cameroon.- Next the grinding process of the above crushed glasses samples was done, and this with a grinder belonging to the laboratory of mechanics of the advanced teacher training college of the technical education, of the university of Douala, Cameroon, allowing thus to get glass particles with granularities ranging from 0.063 mm to 125 mm. Figure 2 shows some samples of glass powder obtained.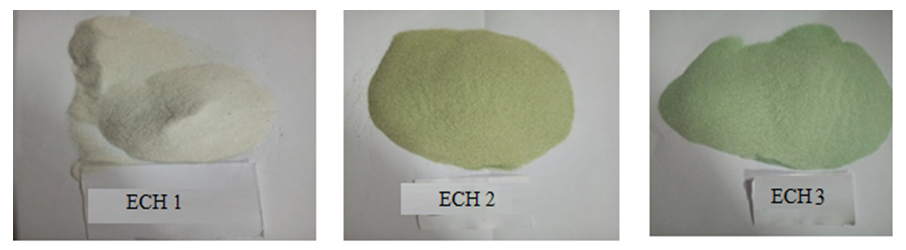 | Figure 2. Crushed and sieved glass powder waste |
- The obtained glass powder samples are heated to temperatures above 100°C to allow careful drying of the samples before sieving.- Then in order to reduce the glass samples to extremely small particles, with sizes nearly equal to that of cement, that is at the order of
the spraying process is performed by using a vibratory compactor as shown in Figure 3 (a and b.), which was done at the private laboratory of the Cameroonian business Bocom Petroleum in Douala Bonaberie.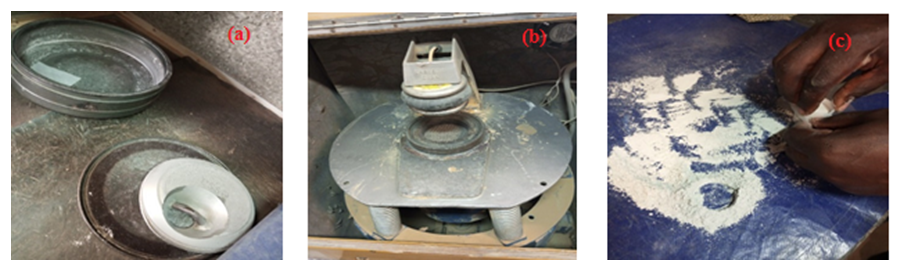 | Figure 3. Spray equipment. (a) Tray, (b): Crusher, (c): Powder found after spraying |
2.1.1.2. Chemical Constituents of the Glass, Sand and Cement Powders: FTIR Analysis
In order to determine the chemical constituents of various samples of glass waste powder found and to compare with that of sand and cement powders, the FTIR analysis is performed in order to know whether glass powders can be used to partially substitute cements or not, following the process used in [28]. Tables (A1 and A2) of the Appendix A show infrared absorption bands characteristic usually found for both anhydrous and hydrated cement [29]. Following this technics, the FTIR analyses were performed here and Fig. (B1(from a to s)) of the Appendix B was plotted, for samples labelled from 1, to 16, which are combined as plotted in Fig.7, with its zooming inside it for the wave numbers belonging to
, from where the following chemical constituents are detected.• Silica detection:- All curves of Fig.7 pass through simple characteristic IRTF bands of
, and
which would reflect the detection of silica in all the analysed samples.- The characteristic triple IRTF bands are observed at (1080 cm-1, 780 cm-1, 470 cm-1); and (1140 cm-1, 810 cm-1, 480 cm-1); which once again reflect the presence of silica in all the samples.• Calcium detection:All curves of Fig.4 pass through the simple characteristic IRTF band of
, with the characteristic double IRTF bands are observed at (3642 cm-1, 1633 cm-1); and (1145 cm-1 - 1120 cm-1, 670 cm-1 – 600 cm-1); which once again would reflect the presence of the element calcium, which would reflect the detection of calcium. Finally, the characteristic triple FTIR bands are observed (1460 cm-1, 875 cm-1, 710 cm-1); which would again reflect the presence of the calcium element. The bold FTIR curve in bold green colour of Fig.4, corresponds to cement (Ech 16), the bold FTIR curve in blue corresponds to the sand powder (Ech 15), and the bold FTIR curve in black represents the first sample of recycled glass powder (Ech 1), and the others at the bottom represent. The curves are for glass powders (From Ech 2 to Ech 15). It is obvious that the sample of recycled glass powder closest to the cement is sample 1, thus the sample 1 is the adequate sample in the case of a cementitious replacement of this recycled glass powder in concrete.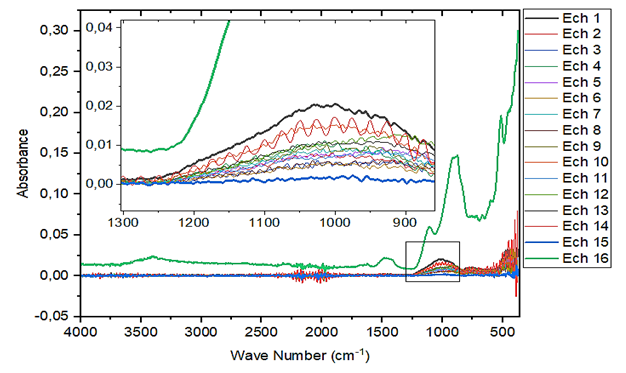 | Figure 4. FTIR curves of samples analyzed |
2.1.1.3. Chemical Composition of the Glass Powders: FRX Analysis
This analysis is performed in order to accurately obtain all chemical composition of the glass waste powder samples. The chemical elements found are summarized in Table A3 (a and b) of the appendix A.
2.1.2. Aggregates
The sand used is that of Sanaga river in the Littoral Region of the Wouri division, widely used for the construction of buildings. While the gravel used is from the Logbadjeck quarry in Cameroon, Figure 5 shows the granular distribution of the sand and gravel used.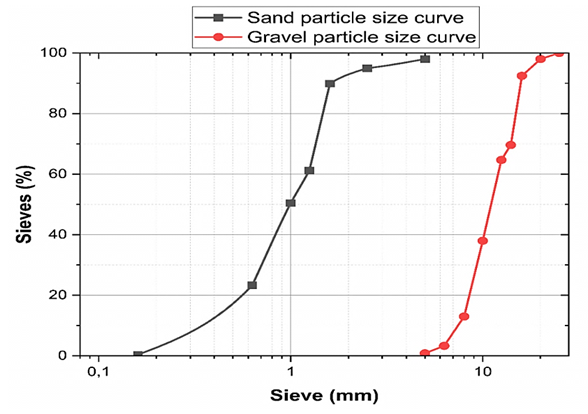 | Figure 5. Particle size curves of sand and gravel used |
2.1.3. Cement
The cement used for this research work is the gray Porland 42.5 produced by CIMAF.
2.2. Preparation of Test Specimens
2.2.1. Fresh Test Specimen
The Dreux Gorisse formulation [30] is chosen here, even though it is not suitable since it doesn’t take into account the additions, which are nevertheless fundamental constituents of the desired concrete. Only waste glass particles of varied chemical composition change in the other combinations but are set at 10%, while the W/C ratio is set at 0.483 for all tested concretes. Table 1 summarizes the compositions of various concretes.Table 1. Concrete composition by unit volume and weight 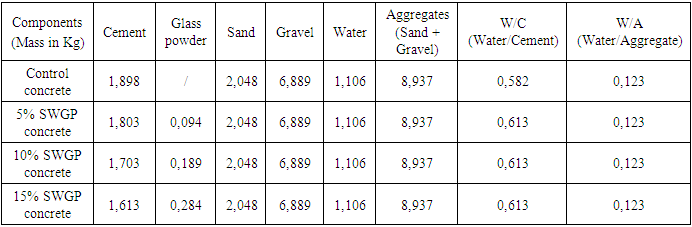 |
| |
|
According to the results of the various formulations, the quantities of aggregates are same for all formulations, although that of cement varies according to the quantity of selected waste glass powder to be substituted, and the glass powder-containing concretes use more water than the control concrete. This may be because of the rise in the surface of the glass powder, as well as the angular shape of the glass particles [31]. For mechanical characterizations, 60 samples are made as shown in Fig.6, for each 0%, 5%, 10% and 15% of SWGP concretes. | Figure 6. Test specimens produced |
2.2.2. Mechanical Properties
The mechanical properties of concrete specimens are found by using the simple compression and flexural three points.
2.2.2.1 Compression Test
The compressive strength of all specimens was measured when the specimens are crushed after periods of 7 days, 14 days and 28 days. The test thus consists of subjecting the concrete specimen to a continuous and progressive load using an electro-hydraulic press until it is crushed. Compressive strength is the ratio between the breaking load and the cross section of the specimen. Designating by
the area of the parallelepiped specimen and by F (N) the maximum load that it supports until rupture. The compressive strength expressed in (Mpa) is therefore | (1) |
2.2.3. Three-Point Flexural Test
Flexural strength tests are carried out on concrete specimens of dimensions
using a mechanical press as shown in Figure 7. The test piece is placed on two metal rods spaced 50 mm apart on the lower platen of the machine; A third rod, on which pressure will be exerted, is then placed above the test tube. The maximum flexural stress
(MPa) due to bending is calculated by using the following equation: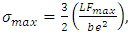 | (2) |
where
(N) is the breaking force. While L (mm), b (mm) and e (mm) are the length, the width and the thickness of the concrete specimen, respectively.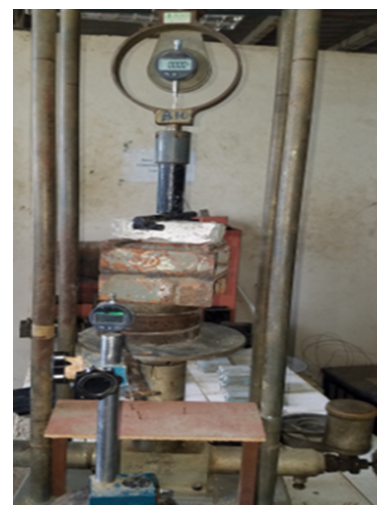 | Figure 7. Flexural test apparatus |
2.2.4. Water Absorption
Water absorption by immersion is the result of capillary movements in the pores of the concrete specimen opened to the surrounding environment. The operations are carried here out as follows:- Submerge concrete specimens in a tank of water for at least 48 hours or until a constant wet mass, and weigh them at the nearest gram, the resulting concrete specimens being carefully wiped with a cloth absorbing all surface water.- Then dry the wet concrete specimens for at least 72 hours or until the mass becomes constant in a ventilated oven whose temperature is maintained at 105°C.The water absorption rate by immersion (Ta%) is calculated by the following relationship: | (3) |
where
and
are the constants wet and dry masses of the test specimen found after immersion, and after drying in an oven, respectively.
3. Results and Discussions
In this section, the results obtained from the tests described in the previous section are presented.
3.1. Slump Cone Test
The result of slump test is given in this subsection. Let us remember that this test measures the consistency of concrete, that is the behaviour of a compacted inverted cone of concrete, giving thus an idea about the workability condition of the concrete mix. The results found here allowed us to plot the histogram of Fig.8. As one can see the slump increases with the increasing of the rate of the glass powder, and this could be due to the pozzolanic character of the waste glass powder, which is perfectly in agreement with results found in [19,32], although the contrary results were found in [2,10].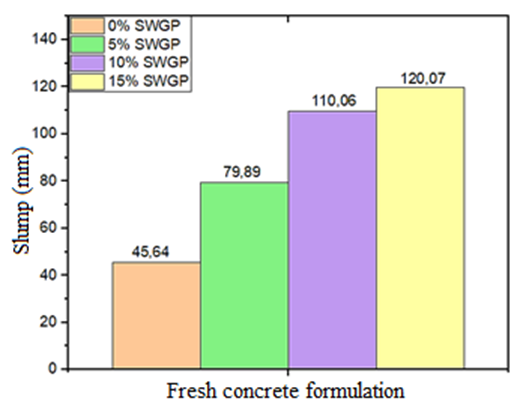 | Figure 8. Slump of formulated concretes |
3.2. Density Determination for Fresh Concrete
Table 2 shows the test density results for fresh concrete, from where it is found that the maximum density is reached at 10% of waste glass powder, which is
, followed by the concrete containing 5% of selected waste glass powder, whose density is
. This proves that the selected waste glass powder contributes to the production of heavy concrete; not suitable for the construction of buildings where the great need is the lightweight concrete, with the aim of reducing the area of the reinforcements, and therefore the cost of the project.Table 2. Fresh Density Results 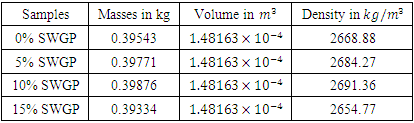 |
| |
|
3.3. Compression Results
The results found for compression test are plotted on Fig 9, from where it is clear that the compressive strength is improved at 10% of glass powder added. This result is perhaps due to the fact that the powder adjusts the grain size of the cement, which leads to an increasing in the compactness of the paste (physical effect), as outlined in [6,7,10,12,20,31,34,35,38]. We found also that (but not shown here) the pozzolanic activity varies from one glass to another and that green glass and white glass present considerable pozzolanic activities.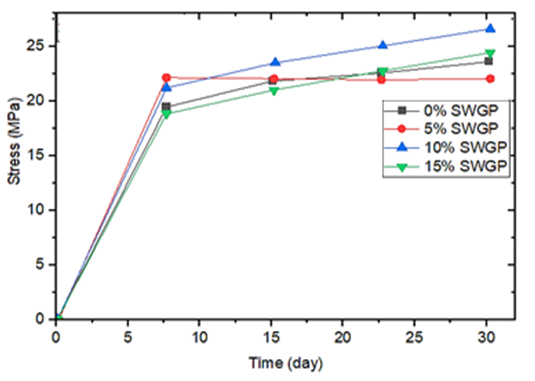 | Figure 9. Compressive strengths at 7, 14 and 28 days for certain rate of glass powders |
3.4. Three-Point Flexural Test
The curves for flexural strengths are shown in Fig. 10 for all bending tests performed here at 7, 14 and 28 days, respectively. From this figure, it is obvious that the control concrete (0%) has the lowest flexural strength. Meaning that on the contrary to what we expected, the waste glass powder nearly increases the flexural strengths of the concrete, and this could be due to the fact that the glass powder under consideration makes the concrete more brittle and the resulting materials have low resistance to flexion, which is well in agreement with results found in [7,9,33,34,35,36]. 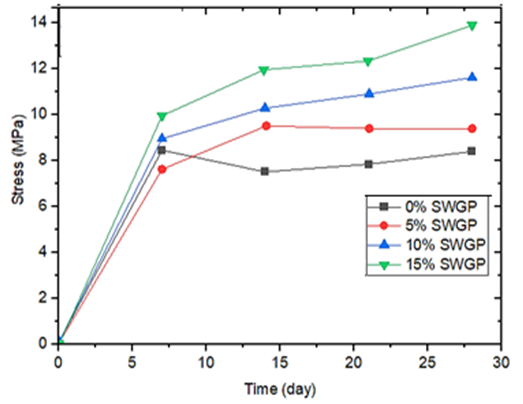 | Figure 10. Flexural strengths at 7, 14 and 28 days for certain rate of glass powders |
3.5. Absorption Tests
The absorption rate found here for 7, 14 or 28 days of drying at room temperature is shown in Fig. 11, from where one observes that the absorption rate is lowest at 10% of waste glass powder. This means that the addition of glass powder to concrete improves its absorption rate.Ø In Fig.11 a corresponding to the 7th day of drying, one observes that the control concrete (0%) absorbs more than the selected waste glass powder-containing concrete, with an absorption rate of 4.942%, followed by that of 5% of selected waste glass powder-containing concrete, with a rate of 4.702%, and the 10% of selected waste glass powder-containing concrete, with a rate of 4.51, agreeing thus the results found in [39].Ø In Fig.11 b obtained for the 14th day of drying, it is obvious that concrete containing 15% of selected waste glass powder absorbs most water with an absorption rate of 4.186%, followed by concrete containing 5% selected waste glass powder, with an absorption rate of 4.154% which is slightly greater than that of the control concrete, while the concrete with the lowest absorption rate is the concrete containing 10% of selected waste glass powder with an absorption rate of 3.556%.Ø In Fig 11 c, the absorption results at 28 days is plotted, from where, it is discovered that concrete containing 15% selected waste glass powder absorbs the most, with an absorption rate of 4.372%, followed by concrete containing 5% selected waste glass powder, with an absorption rate of 4.292%, while concrete containing 5% of selected waste glass powder, with an absorption rate of 3.758%. 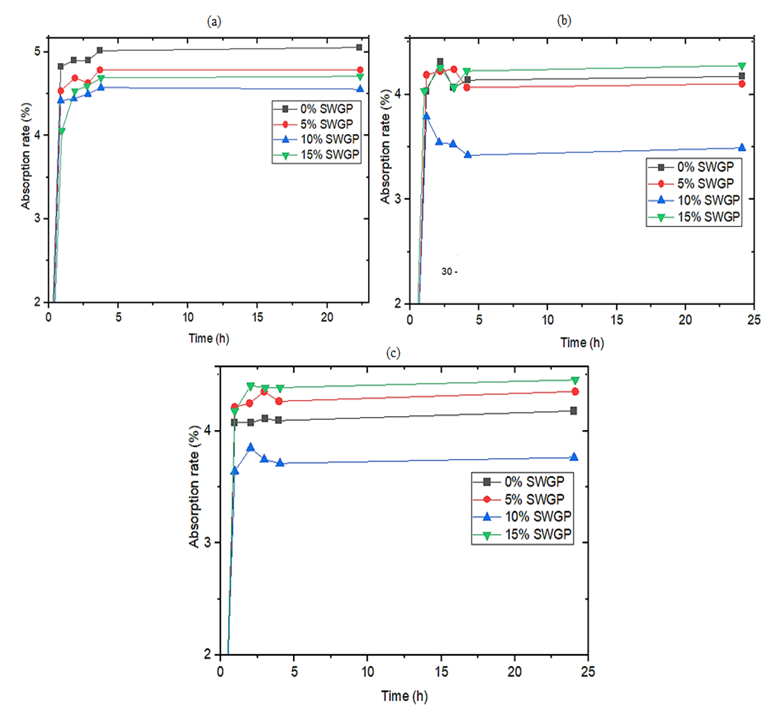 | Figure 11. Time evolution of the absorption rate at: (a), (b): 14 days, and (c): 28 days |
4. Conclusions
The possibility of using glass powder in concrete as a partial substitute of cement is studied in this paper, with the aim of finding the adequate rate of glass powder to better produce concrete with the right characteristics. The glass powders were obtained from collected glass waste, using some specific techniques. In order to study the interactions between local CEMII 42.5 type cement (with well-known chemical components) and ordinary Sanaga sand, the glass waste and local sand were crushed separately to obtain fines, with a diameter of the order of 75 µm, equivalent to that of a cement particles, after which physical and chemical characterizations are investigated. The chemical characteristics including mineralogical analyses, through specifically XRF and ITRF analyses were done, allowing us to affirm that the chemical components of the glass powder vary with its colour, and for some of them, they are almost similar to those of the local cement and can thus be used as it partial substitute in concrete. In order to justify the possible using of glass powder as partial replacement of cement, via the physical and mechanical characteristics, the concrete meeting the standards was formulated, consisting of the Sanaga sand, the 5/15 gravel, the CEMII 42.5 cement from CIMAF, and tap water, in which the varying fraction of the powder of glass was introduced to substitute the similar volume of cement. To begin, we ensured that the aggregates used were clean and the granularity of the sand used was determined by carrying out granulometry tests. Then we performed experiments on concrete in both the fresh and hardened states in which it was substituted 0%, 5%, 10%, and 15% of glass powder, respectively, with that of 0% of glass powder chosen as the control concrete. Then the workability of fresh concrete was investigated by using slump cone test, which showed that the slump increases with the fraction of glass powder added. Next the fresh concrete was weighed and we found that the density increased with the rate of glass powder and reached it maximum value at 10%, and decreased afterward.Then we performed physical and mechanical tests on the hardened concrete, by measuring compressive and flexural strengths as well as the absorption rate of water at 7, 14, and 28 days. From these tests, it was obvious that the maximum compressive strengths as well as the lowest rate of water absorption were reached at 10%. However the flexural strength increased with the increasing of the rate of glass powder added. This means that the right rate which could be advised to engineers is 10% of glass powder.
Appendix A: Tables
Table A1. Infrared absorption bands characteristic of anhydrous cement components [29] 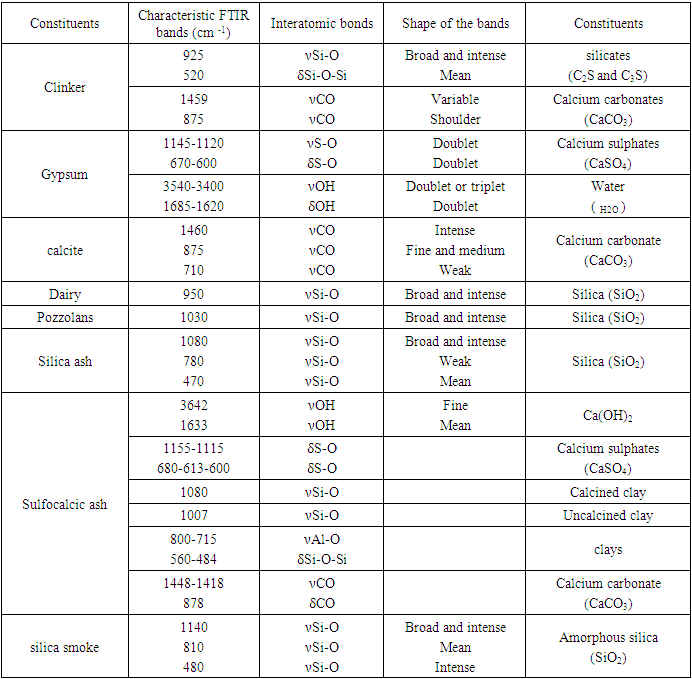 |
| |
|
Table A2. Infrared absorption bands characteristic of the components of hydrated cements [29] 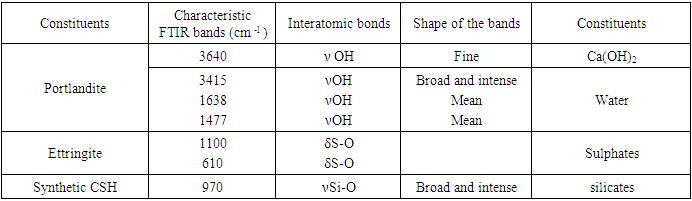 |
| |
|
Table A3.a. Chemical composition of each sample analyzed by Fluorescence X 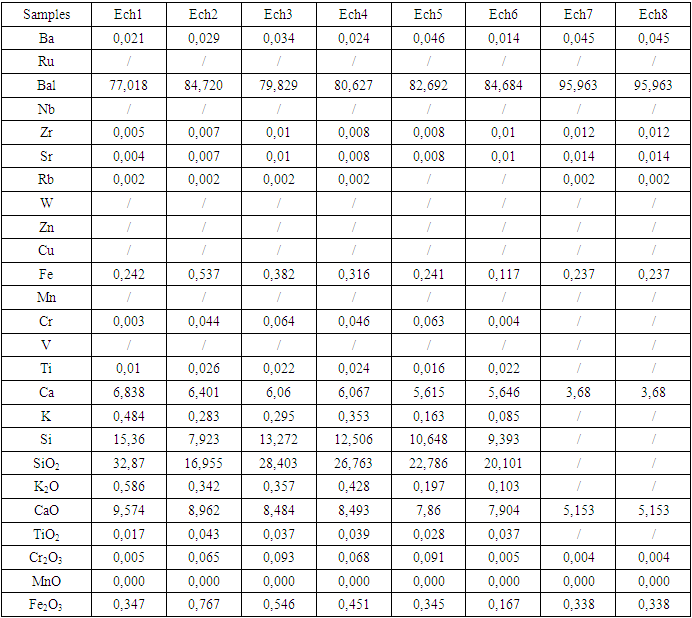 |
| |
|
Table A3.b. Chemical composition of each sample analyzed by Fluorescence X 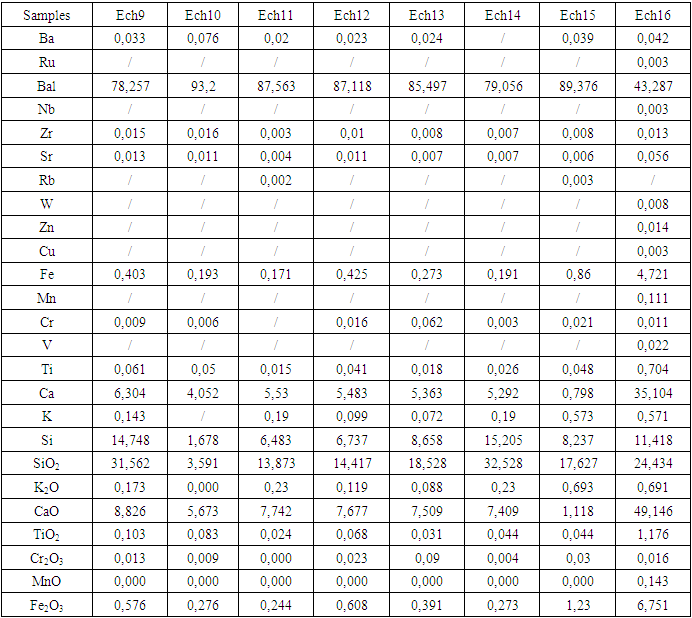 |
| |
|
Appendix B: Figures
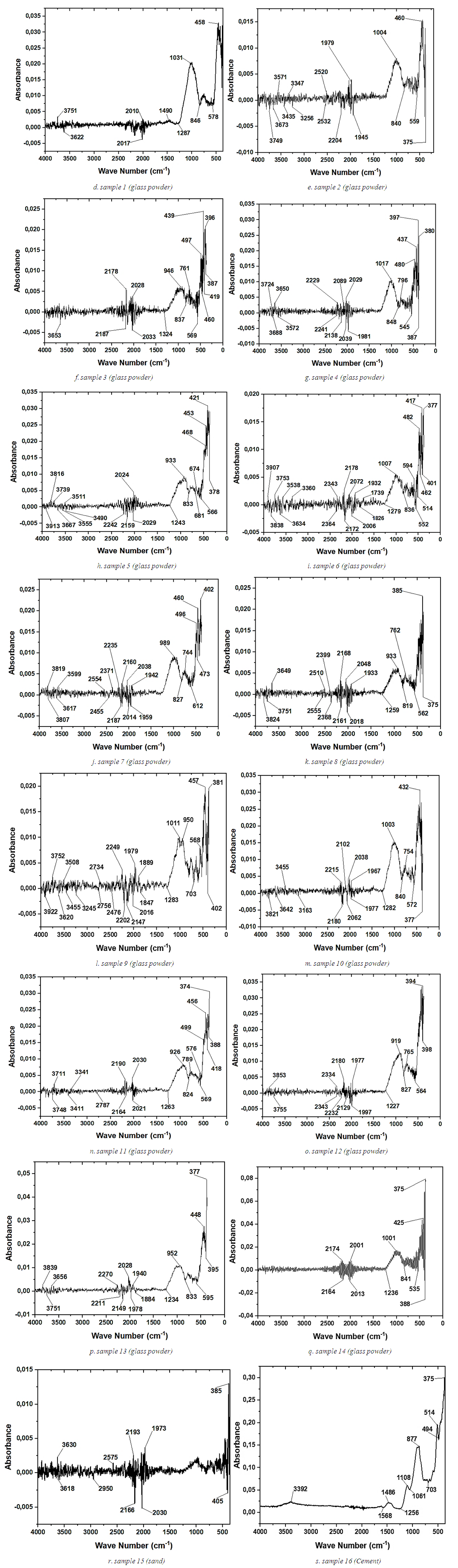 | Figure B1. FTIR curves of each sample analysed of glass, cement and sand powders |
References
[1] | Donadkar MU and Solanke SS (2016) Review of e-waste material used in making of concrete. International Journal of Engineering Trends and Technology 16: 196-199. |
[2] | Olutoge FA (2016) Effect of waste glass powder (WGP) on the mechanical properties of concrete. American Journal of Engineering Research 11: 213–220. |
[3] | Glas Trösch Holding AG (2013) Glass and its Applications. Conseil. Bützberg. 380 pages. |
[4] | French Chemical Company (2017) Available at: http://www.societechimiquedefrance.fr/extras/Donnees/mater/verre/texver.htm (accessed 13 December 2022). |
[5] | Sibelco Green Solutions (2019) Promoting glass: Your future our talent. Available at: https://www.sibelco.com/wp-content/uploads/Sibelco-Green-Solutions-Brochure FR.pdf?x17555 (accessed 13 September 2022). |
[6] | Vandhiyan R, Ramkumar R and Ramya R (2013) Experimental study on replacement of cement by glass powder, International Journal of Engineering Research and Technology 2: 234-238. |
[7] | Gahoi G and Kansal R (2016) Waste glass powder as a partial replacement of PPC. International Journal of Science and Research 5: 1414–1418. |
[8] | Meena MK, Gupta J and Nagar B (2018) Performance of concrete by using powder- an experimental study. International Research Journal of Engineering and Technology 5: 840 – 844. |
[9] | Karde AD, Bagwan MI, Gowda MR, Kudale RR and Jagtap PM (2018) To study properties of concrete using waste glass powder replacement to cement. International Journal for Scientific Research and Development 6: 992-996. |
[10] | Khan FA, Fahad M, Shahzada K, Alam H and Ali N (2015) Utilization of waste glass powder as a partial replacement of cement in concrete. International Journal of Advanced Structures and Geotechnical Engineering 4: 181–185. |
[11] | Prudhvi K, Saiprasad K, Reddy KS, Manoj Kumar K and Vinay D (2016) Laboratory study on compressive strength of concrete with glass powder as partial replacement of cement. Journal of Emerging Technologies and Innovative Research 3: 272–277. |
[12] | Sakale R, Jain S and Singh S (2016) Experimental investigation on strength of glass powder replacement by cement in concrete with different dosages. International Journal of Science Technology and Engineering 2: 76–86. |
[13] | Kumar V and Sood H (2017) Effect of waste glass powder in concrete by partial replacement of cement. International Journal of Civil Engineering 4: 13–22. |
[14] | Rahman S and Uddin MN (2018) Experimental investigation of concrete with glass powder as partial replacement of cement. Civil Engineering and Architecture 6: 149–154. |
[15] | Al-jburi Najad A. A., Hasan Kareem, J.K., Noor Azline and Nima Ostovar, Waste glass as partial replacement in cement – A review, IOP Conf. Series: Earth and Environmental Science 357 (2019) 012023. |
[16] | G. M. Sadiqul Islam, M. H. Rahman, Nayem Kazi, Waste glass powder as partial replacement of cement for sustainable concrete practice, International Journal of Sustainable Built Environment (2017) 6, 37–44. |
[17] | S.P. Kanniyappan1, T. Muthukumaran, A Study on Glass Powder Waste as Partial Replacement of Cement for Sustainable Development, International Journal of Innovative Research Explorer, volume 5, issue 4, April (2018). |
[18] | Daban A. Muhedin, Rahel K. Ibrahim, Effect of waste glass powder as partial replacement of cement & sand in concrete, Case Studies in Construction Materials, Volume 19, December 2023, e02512. |
[19] | Aliabdo AA, Abd Elmoaty AE and Aboshama AY (2016) Utilization of waste glass powder in the production of cement and concrete. Construction and Building Materials 124: 866-887. |
[20] | Olofinnade OM, Ndambuki JM, Ede AN and Booth C (2017) Application of waste glass powder as a partial cement substitute towards more sustainable concrete production. International Journal of Engineering Research in Africa 31: 77–93. |
[21] | Butler JH and Hooper PD (2019) Glass Waste. In: Waste. Elsevier Inc.; 307–322. |
[22] | Christensen TH and Damgaard A (2010) Recycling of Glass. In: Christensen TH. Solid Waste Technology and Management. Blackwell Publishing Ltd. 212-219. |
[23] | Worrell E and Reuter MA (2014) Handbook of Recycling: State-of-the-art for Practitioners, Analysts, and Scientists. Elsevier, United States of America, 581 pages. |
[24] | Meyer, C. (2008), Recycled materials in concrete, in: Developments in the formulation and reinforcement of concrete, Edited by Sidney Mindess, University of British Columbia, canada. |
[25] | Hasanuzzaman M, Rafferty A, Sajjia M and Olabi AG (2016) Properties of Glass Materials. In: Reference Module Materials Science Materials Engineering. 1–12. |
[26] | H. Lafuma, (1962), ''Chemistry applied to building materials lime and cement, ceramics and glassware'', Ed/Masson and C Editors. |
[27] | AS Benosman, H. Taibi, M. Mouli, M, Belbachir, ''Valorization of infrared spectrometry (IRTF) for the qualitative analysis of compounds in cements, clays and cement/clay mixtures'', Revue Technologiques, Scientifiques et Linguistique, Communication Sciences & Technologie, COST, vol 3, p. 37-47, December 2004. |
[28] | J. Loiseleur, (1963), ''Laboratory Techniques'', T1, Fascicule 1, pp. 154-158. Ed. Masson. |
[29] | Y.F, Farcas and Ph. Touze. The transform infrared spectrometry of Fourier (IRTF) an interesting method for the characterization of cements. Bulletin of the laboratories of the bridges and roadways- 230-REF.4350-PP.77-88, January. February 2001. |
[30] | Jean Perchate, ‘’Traité béton de béton armé selon l’Eurocode 2’’: 2e édition, juillet 2013. |
[31] | Khezzane Hiyam, Zellouma Réguisa, ‘’Etude de la durabilité d’un béton de sable à base de poudre de verre’’ Université Echahid Hamma Lakhdar d’El Oued, Faculté de technologie, département d’hydraulique et de génie-civil, spécialité matériaux en génie-civil, 2001 p87. |
[32] | Keerio MA, Khoso S, Khan JS, Ansari AA, Bhatti NK (2017) The effect of waste glass as partial replacement of cement on properties of concrete. Engineering Science and Technology International Research Journal 1: 59–63. |
[33] | Mounika M, Lalith BV, Rao VR and Lalitha G (2017) Experimental study on strength parameters of concrete by partial replacement of cement recycled crushed glass powder. International Journal of Civil Engineering and Technology 8: 444–450. |
[34] | Zakir M, Qadri SI and Siwach ER (2016) Experimental evaluation of waste glass powder as a partial replacement of cement in concrete. International Journal of Recent Innovation in Engineering and Research 1: 71–75. |
[35] | Rokdey MS, Dhawale GD and Wagh MS (2018) Partial replacement of cement by using refused glass powder in concrete for strengthening. International Journal of Scientific and Engineering Research 5: 77–82. |
[36] | Mwizerwa F and Garg A (2017) Experimental study on effects on properties of concrete with different colours of glass powder as a partial replacement of cement. International Journal of Civil Engineering and Technology 8: 1639–1644. |
[37] | Du H and Tan KH (2014) Waste glass powder as cement replacement in concrete. Journal Advanced Concrete Technology 12: 468-477. |
[38] | Liaqat M, Shah ML and Baig MA (2018) Effect of waste glass as partial replacement for coarse aggregate in concrete. International Journal of Technical Innovation in Modern Engineering & Science 4: 609–619. |
[39] | Saand A, Keerio MA, Juj R, Khoso S and Bangwar DK (2017) Utilization of waste glass as partial replacement of fine aggregate in concrete. Engineering Science and Technology International Research Journal 1: 28–31. |