Peterson Mutembei Kugeria 1, Peter Waithaka Njoroge 2
1School of Pure and Applied Sciences, University of Embu, Embu, Kenya
2Department of Physical Sciences, Murang'a University, Murang'a, Kenya
Correspondence to: Peterson Mutembei Kugeria , School of Pure and Applied Sciences, University of Embu, Embu, Kenya.
Email: |  |
Copyright © 2022 The Author(s). Published by Scientific & Academic Publishing.
This work is licensed under the Creative Commons Attribution International License (CC BY).
http://creativecommons.org/licenses/by/4.0/

Abstract
Rutile is a mineral which is used in making paints, ointments, tooth paste, sunscreens, just to mention a few products. Titanium metal makes alloys with less density and resistance to corrosion, which are used in making aircraft and marine vessels. Rutile is obtained from ores by concentration method using chemicals, a process which is very expensive. In this paper, we have investigated on alternative method of concentrating rutile from titanium ores. This was done by reduction of the mixture of titanium ore and laterite using biomass. The titanium ores were obtained from Maragwa location in Tharaka Nithi County and mineralogical and chemical composition carried using XRD and AAS. The mixture of 25 g of the ore, 2 g of laterite and 1.0 g of ground dry biomass was put into clay pots. The samples were placed in a charcoal burner and heated at temperature range 800 - 900°C for two hours and the temperature monitored using a thermocouple. After two hours the sample mixtures were cooled to room temperature and serial magnetic separation done. The samples were digested and analyzed for rutile using AAS and XRD. The results show that rutile composition increased from about 0.40% in raw ore to about 2.62%, which represents 2.22% increase. This percentage increase varies depending on the ore mineralogy and chemical composition. Therefore, titanium ores with low concentration of iron can be concentrated using laterite rich in iron. Besides obtaining rutile, the method offers a successful way of cleaning the environment by using biomass from municipal waste.
Keywords:
Laterite, Biomass, Reduction, Rutile, Concentration
Cite this paper: Peterson Mutembei Kugeria , Peter Waithaka Njoroge , Rutile Concentration by Reduction of Titanium Ore - Laterite Mixture Using Biomass, American Journal of Materials Science, Vol. 12 No. 1, 2022, pp. 1-6. doi: 10.5923/j.materials.20221201.01.
1. Introduction
The concentration of titanium in low grade titanium ores in laterite has been done by heating the raw laterite sample with lantana camara and separated using a strong magnet [7]. In their work, the concentrate obtained after reduction at temperature rage 500 to 800°C was manly maghemite and titanomagnetite. Another study done on the effects of temperature on the ilmenite containing laterite, confirmed that concentration of titanium was possible using biomass at the temperature range of 800 - 1200° [3]. A South African company known as Richards Bay Minerals (RBM), extract rutile from ilmenite containing ores by reduction using carbon at temperature range of 730°C to 800°C [8].The recovery of rutile from synthetic industrial waste has been investigated using caustic hydrothermal method [1]. The method involved decomposition of the industrial ilmenite waste and then followed by the sulphate process to obtain rutile. Studies on extraction of rutile from beach sand has been done [4]. In their investigation, Perez & Sharadqah [4] first heated the samples to remove impurities which were difficult to be removed by conventional physical or mechanical treatments. The second step involved mixing the samples with sodium hydroxide pellets and later heating at 1100°C. The products obtained were then hydrolyzed to obtain hydrated titanium dioxide. The hydrated product was then digested using acid in the presence of iron metal as reducing agent to obtain about 92 percent TiO2.Another method of obtaining very high-grade synthetic rutile has been developed [6]. In their study, Ilmenite was roasted at temperature ranges of 800°C to 1,000°C to selectively magnetize the ilmenite fraction. The ilmenite was able to be removed through magnetic separation leaving out the gangue. Iron and other impurities were removed by leaching process at normal conditions and hydrochloric acid. The leached solid content was washed, filtered, and calcined to produce a synthetic rutile grading at about 97 percent.
2. Methodology
2.1. Sample Collection and Preparation
Samples for analysis were obtained from Maragwa location, Tharaka North Sub - County in Tharaka Nithi County at locations 0°18’S38°8’E and 0°21’S38°11’E. Random sampling was done from five quarries which were within one to two kilometers apart from each other. Three sampling sites from each quarry were selected within a distance of about 10m apart. A mattock and a shovel were used to break the rocks and scoop out the mineral respectively. Mineral samples were obtained from a depth of 30cm from each of the 3 sites and crushed into small particles using a hammer. The crushed mineral particles were mixed carefully and then about two kilogram of it was obtained and packed in labeled plastic bags for analysis.
2.2. Sample Preparation for XRD and Analyses
About 30g of pulverized mineral samples to 250 micro millimeters using a ball mill was put into the sample holders. The samples were then loaded in X - ray difractometer for analysis of minerals using data collector software [5], [2].
2.3. Sample Preparation for AAS and Analyses
About 0.1 g of the sample was weighed and put in a 125-ml plastic container. One ml of concentrated aqua-regia (1:3, Nitric acid to hydrochloric solution) was added followed by 3.0 ml of hydrofluoric acid. The sample was then left to digest for at least 8 hours. 50.0 ml of saturated boric acid was added then allowed to react for one hour. The solution content was then topped up to make 100.0 ml using distilled water. Samples were then analyzed alongside the standards [2].
2.4. Concentration of Titanium from Ore - Laterite Mixture Using Biomass
2.4.1. Optimisation Studies
A mixture of 5.0 g of the ore, 2.0 g of ground laterite and 1.0 g of ground biomass was put into clay crucibles. The clay crucibles were placed into the charcoal burner and heated at a temperature range of 800 - 900°C for two hours. The temperature was monitored using a thermocouple. After two hours the sample mixtures were cooled to room temperature and serial magnetic separation done as per [5] and [2]. The samples were digested and analyzed for rutile using AAS and XRD.The experiment was repeated by varying the mass of ore from 5.0 g to 40 g at an interval of 5.0 g. The masses of the biomass mixture were held constant at 1.0 g and that of laterite at 2.0 g. The reduction temperature was maintained at 800 - 900°C. The separation was done as explained above and samples digested and analyzed for rutile using AAS and XRD.
3. Results and Discussion
3.1. Mineralogical and Chemical Composition of Laterite
The laterite from Gitong’o in Tharaka Nithi County was used to enrich the ilmenite ore during reduction. The results of its mineralogical and chemical composition are given in fig. 1 and table 1.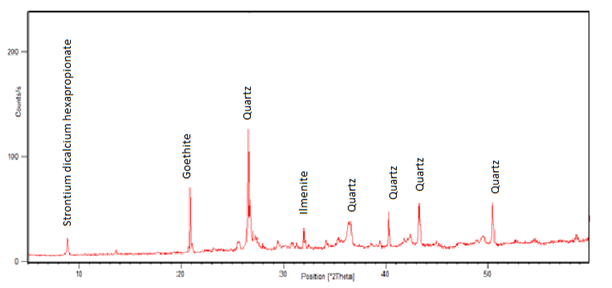 | Figure 1. A spectrum of raw laterite sample from Gitong’o |
 | Table 1. Chemical Composition of the Laterite Soil |
The results of, rutile composition was low while that of silica was high followed by iron oxides. The sample also contained alumina which was likely to influence the rutile composition in the laterite. The laterite was used to investigate on the chemical transformation during concentration of titanium in the ores in the presence of biomass. The XRD results of the sample 3231, before reduction and that of the tailing and the concentrate is given in fig. 2, 3 and 4 respectively.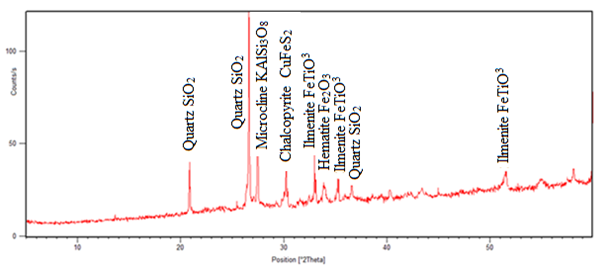 | Figure 2. Spectrum of raw ore sample before heat treatment (3231) |
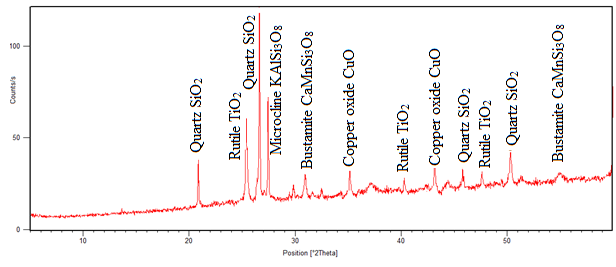 | Figure 3. Mineralogical composition of the tailing after magnetic separation |
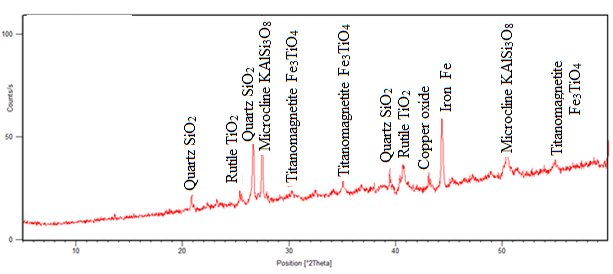 | Figure 4. Mineralogical composition of the magnetic sample after magnetic separation |
The results from figure 3 show that, after heat treatment ilmenite and hematite peaks disappeared and rutile peak appeared at two angle theta 25°, 40.5° and 48° in fig. 4. In the same fig. 4, Titanomagnetite peak appeared at angle theta 30°, 35° and 55° and the iron peak was found at two angle theta 44.5°. This means that iron minerals were able to be reduced to iron at temperature range of 800 – 900°C. The intensity of rutile peak in non-magnetic sample shows that much of rutile was collected in the tailing. The chalcopyrite mineral peak disappeared and copper oxide peaks are both found in fig. 3 and 4 at two angle theta 35° and 43.5°. The formation of CuO was probably due to the re-oxidation of copper during cooling. Chemical analysis was done, and the results given in table 2.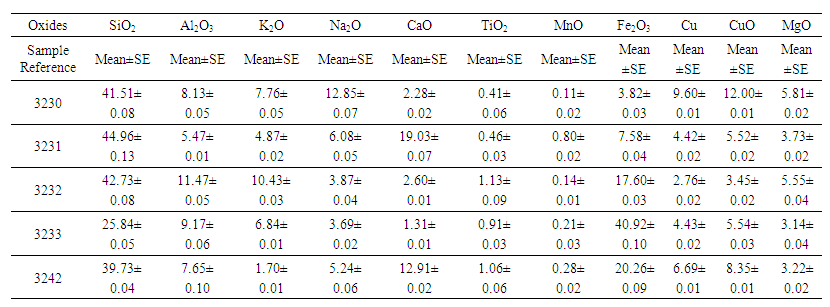 | Table 2. Elemental Analysis of Raw Samples Using AAS |
The results show that rutile composition ranged from 0.41 to 1.13 percent. These values though very low, were used to investigate the concentration of ore-laterite mixture using biomass. The optimized results of sample 3231 are given in the table 3. Table 3. Optimized Results After Reduction of Ore - Laterite Mixture Using Biomass 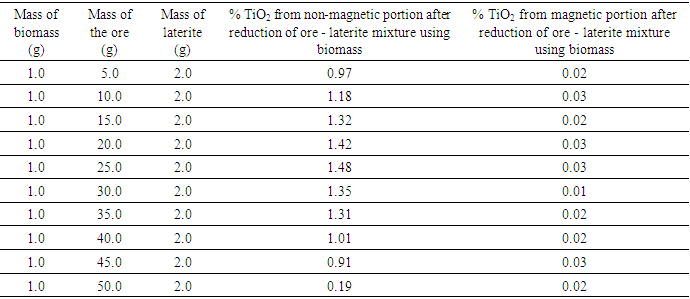 |
| |
|
The results show an increase from 0.46 percent obtained in raw sample to 1.48 percent after reduction using ore, laterite and biomass mixture. The results from table 3 show that the mixture of 25 g of the ore, 2 g of the laterite and one gram of biomass gave good results of the concentrated rutile. From literature, goethite and hematite minerals are converted to magnetite minerals at temperature range of 500 – 700°C [7], [5], [2]. This is shown in equation 1 and 2. | (1) |
 | (2) |
According to [7], ilmenite minerals are also oxidized by syngas to form magnetic susceptible titanomagnetite minerals at the same temperature range. This is shown in equations 3, and 4. | (3) |
 | (4) |
In this study, reduction temperatures were increased to the range of 800 – 900°C in the presence of the syngas. The rutile and metallic iron were formed as shown in equation 5 to 7. | (5) |
 | (6) |
 | (7) |
The reduction of the ore-laterite mixture using biomass was done using the optimized parameters and results given in table 4 and 5. Comparison of the percentage results is given in table 6.Table 4. Magnetic Separated Sample After Reduction of the Ore - Laterite Mixture Using Biomass 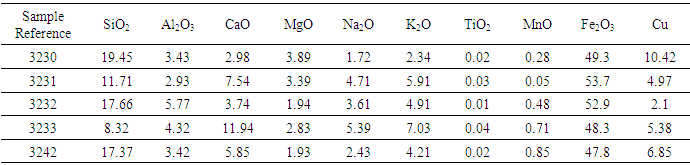 |
| |
|
Table 5. Non-Magnetic Separated Sample After Reduction of the Ore - Laterite Mixture Using Biomass 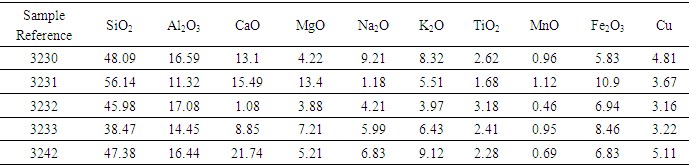 |
| |
|
Table 6. Comparison of Percentage Rutile Per Ore After Concentration 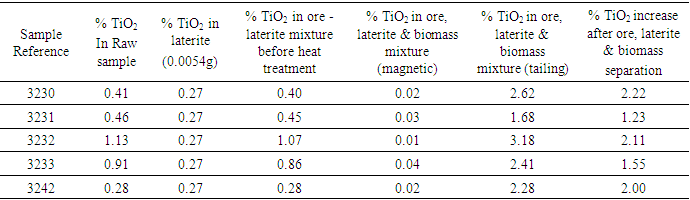 |
| |
|
The results from table 4 shows that iron concentrate generally increased while rutile decreased significantly in all the ore samples. In table 5 rutile, silica and alumina composition increased significantly in the tailing and reduced in the concentrate making the method of concentration successful. The results from table 6 show that rutile composition increased from about 0.40% in raw (sample 3230) to about 2.62% in the tailing after concentration. This composition represents 2.22% increase after concentration. The increase has been contributed by 0.27±0.01 value of rutile from the laterite. Since the concentration of rutile in the concentrate is very low (0.02-0.04%), then the method is good for the concentration of rutile from ores. The lateritic materials can therefore be used to enrich titanium minerals from ores with low iron content during rutile concentration.
4. Conclusions
Laterite soils rich in iron can be used to concentrate rutile from titanium ores with little composition of iron. The method improves rutile concentration with about 1.2 to 2.22%. The method is also suitable as it helps to clean the environment of the biomass waste especially municipal waste.
Conflicts of Interest
The authors declare no conflicts of interest.
ACKNOWLEDGEMENTS
The author acknowledges the contribution of the co author, peter Waithaka Njoroge for their immense support during the study. He also acknowledges the department of Mines and Geology in the Ministry of Environment and Natural Resources where the experiment was done. The author also acknowledges the funding of the National Research Fund through the University of Embu.
References
[1] | Ahmad, M. H., Awang, H. B., Yusof, S., & Farid, E. M. (2017). Experimental Analysis of Titanium Dioxide Synthesis from Synthetic Rutile Waste using a Moderate Acid Concentration and Temperature. Acta Physica Polonica A, 132(3–II), 833–835. https://doi.org/10.12693/APhysPolA.132.833. |
[2] | Mutembei, P. K. (2013). Concentration of iron in laterites containing titanium from different localities of Tunyai Division in Tharaka Nithi County in Kenya using magnetic separation. Kenyatta University. |
[3] | Mutembei, P. K., Muriithi, N. T., Njoroge, P. W., & Muthengia, J. W. (2014). Effects of Temperature on Ilmenite During Concentration of Iron in Laterites Using Charcoal and Separation using Magnetic Separation. International Journal of Scientific Engineering and Technology. Volume No.3 Issue No.6, pp: 707-711 711(3), 707–711. (ISSN: 2277-1581). |
[4] | Perez, S. M., & Sharadqah, S. (2018). Successive Methods for the Separation of Titanium Oxide from the Black Sands of Ecuador. Journal of Ecological Engineering, 19(1), 186–190. |
[5] | Waithaka, P. N., Mutembei, P. K., Wachira, J. M. and Wanjau, R. 1. (2014). Magnetic Concentration of Iron in Lateritic Soils from Kamahuha, Murang’a County, in Kenya using Carbon Monoxide Generated In-Situ. International Journal of Scientific Engineering and Technology, 1046(3), 1043–1046. |
[6] | Walpole, E. A., & Winter, D. (2000). The Austpac ERMS and EARS Processes for the Manufacture of High-Grade Synthetic Rutile by the Hydrochloric Acid Leaching of Ilmenite. In International Conference on the Practice and Theory of Chloride/Metal Interaction (pp. 1–14). Montreal: Austpac Resources N.L. |
[7] | Warui, K. S. (2015). Beneficiation of low grade titanium ores from selected sites in Meru, Murang’a Tharaka Counties kenya. Thesis. Kenyatta University Kenya. |
[8] | Williams, G. E., & Steenkamp, J. D. (2006). Heavy Mineral Processing at Richards Bay Minerals. Southern African Pyrometallurgy 2006, (March), 5–8. |