Bilal Ahmad, Mahammad Ashfaq, Anton Joy, Zuzarte Aaron Carlos, Sudheer M.
Department of Mechanical Engineering, St Joseph Engineering College, Mangaluru, Karnataka, India
Correspondence to: Sudheer M., Department of Mechanical Engineering, St Joseph Engineering College, Mangaluru, Karnataka, India.
Email: |  |
Copyright © 2017 Scientific & Academic Publishing. All Rights Reserved.
This work is licensed under the Creative Commons Attribution International License (CC BY).
http://creativecommons.org/licenses/by/4.0/

Abstract
Successful incorporation of chitosan (crustaceous shells) is accomplished by incorporating these materials (chitosan) into an epoxy matrix and followed by testing of mechanical properties such as tensile strength, impact resistance, hardness and flexural strength. Using test list it is clearly observed that the optimized percentage of chitosan into epoxy is 15% which has got higher ultimate tensile strength and hardness. Decrease in impact resistance and flexural strength was observed with the addition of chitosan particles. The reason could be inherent properties of chitosan which are not known to strengthen the matrix. The Scanning Electron Microscope (SEM) analysis of fracture surface of tensile specimen has shown agglomeration of chitosan particle and high particle size of chitosan (80-200μm).
Keywords:
Chitosan, Epoxy, Mechanical Properties, SEM analysis
Cite this paper: Bilal Ahmad, Mahammad Ashfaq, Anton Joy, Zuzarte Aaron Carlos, Sudheer M., Fabrication and Characterization of an Eco-friendly Biodegradable Epoxy/Chitosan Composites, American Journal of Materials Science, Vol. 7 No. 5, 2017, pp. 166-169. doi: 10.5923/j.materials.20170705.08.
1. Introduction
Chitosan is a natural biopolymer modified from chitin, which is the main structural component of squid pens, cell walls of some fungi and shrimp and crab shells [1]. Chitin is the second most ubiquitous natural polysaccharide after cellulose on earth [2]. Chitosan exhibits a unique set of physicochemical and biological characteristics, such as biocompatibility, biodegradability, antimicrobial activity, non-toxicity, and good mechanical properties [3-4]. Also it has numerous applications in various fields such as medical and pharmaceutical industries, tissue engineering, agriculture, nutritional enhancement and waste water treatment [5]. Chitosan has received great attention for its wound healing properties [6]. Epoxy resin is one of the widely used polymer matrixes in the composite industry, due to its excellent adhesion to many reinforcements [7]. Epoxy resins are one of the most important thermosetting resins and are extensively used for the preparation of coatings, electronic materials, adhesives and structural materials [8].The objective of present work is to study the effect of chemically modified chitosan content in epoxy matrix on the mechanical properties like tensile strength, flexural strength, hardness and impact strength. The tensile fractured surfaces are analyzed using scanning electron microscope (SEM) in order to assess the failure mechanism.
2. Materials and Methods
2.1. Materials Used
Chitosan Powder (Density=0.2-0.4 g/cc, Ash :> 1%, Moisture content: < 10%, Viscosity: > 30cps, DD: > 90%) was procured from Indian Sea Foods, Cochin, India. Epoxy resin (LY556) and Hardener (araldite) HY 951 was obtained from a local industrial supplier from Bangalore.
2.2. Preparation of Neat Epoxy Composites
The weighed quantity of epoxy resin was taken in a cup. To this the hardener was added such that, for way in parts of epoxy there was one part of hardener i.e. in the ratio 10:1. The mixture was stirred thoroughly using a glass rod so that the hardener and the epoxy were properly mixed together. Care was taken that the gel time was not exceeded before the pouring of the mixture into the mould cavity. Meanwhile the cavity was also prepared by applying the mould release wax in order to facilitate the easy removal of the composite after curing. As soon as the mixture being stirred began to show the initial signs of hardening, it was poured into the cavity and allowed to cure at room temperature for 24 hours.
2.3. Preparation of Neat Epoxy/Chitosan Composites
The weighed quantity of epoxy resin was taken in a cup and to this 5, 10 and 15 wt% of Chitosan were added and then mixed thoroughly for a time interval of 10-15min. Then the hardener was added such that the epoxy to hardener ratio of 10:1 was maintained and thorough mixing was carried out. Once the mixture began to solidify it was poured into the mould cavity prepared for pouring as stated above and the mixture was poured into it. Curing was done at room temperature for 24hours.
2.4. Evaluation of Mechanical Properties
Mechanical properties such as hardness, tensile strength, flexural strength and impact strength (un-notched charpy) of samples were tested as per ASTM and ISO standards. All the results were is obtained using computerized system with inbuilt software.
2.5. SEM Analysis
The fractured surfaces obtained from tensile tested specimens were examined under an environmental scanning electron microscope; FESEM (field emission scanning electron microscope, IGMA Make).
3. Result and Discussions
3.1. Hardness Test
Figure 1 shows increase of hardness number with increase in Chitosan in epoxy matrix.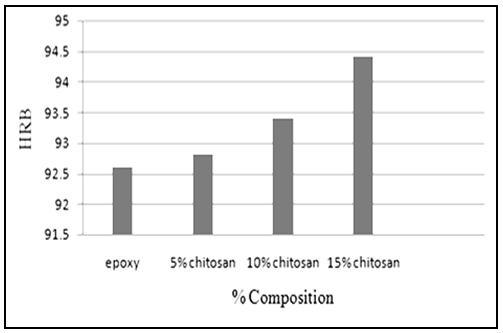 | Figure 1. Effect of Chitosan on Rockwell hardness number |
It can be seen that with increase in wt% of chitosan on epoxy matrix, hardness number increases. The highest hardness number is found to be in 15% CS/Epoxy.
3.2. Impact Test
Figure 2 shows decrease in impact strength with increase in Chitosan in epoxy matrix.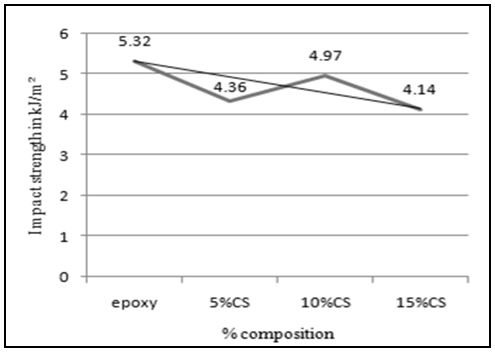 | Figure 2. Impact strength versus wt% of Chitosan |
The maximum energy absorbed by pure epoxy is 5.32kJ/m2 which is higher when compared to all other composites. The energy absorption decreases with increase in Chitosan due to brittleness of chitosan. The results are consistence with increase in percentage of chitosan because fraction of brittle material is increasing in epoxy matrix. There is a small fluctuation in the value of energy absorbed that might have resulted due to improper distribution of chitosan, but the result trend shows there is decrease in energy absorbed.
3.3. Tensile Strength
Figure 3 shows trend in tensile strength with increase in Chitosan in epoxy matrix. The tensile strength of composites decreases with increase in chitosan in epoxy matrix.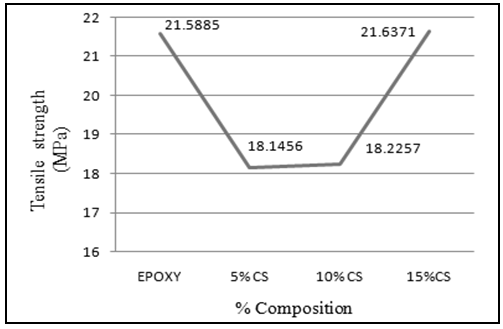 | Figure 3. Variation in tensile strength with increase in wt% of chitosan |
3.4. Flexural Test
Figure 4 shows trend in flexural strength with increase in Chitosan in epoxy matrix. The flexural strength of composites decreases with increase in chitosan in epoxy matrix.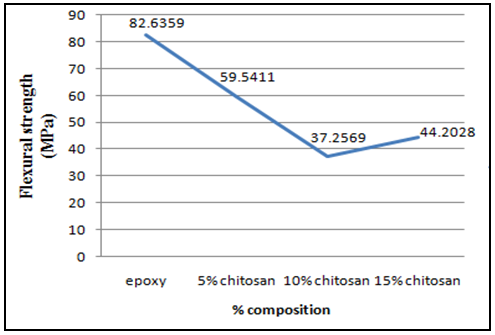 | Figure 4. Flexural Strength v/s wt% of chitosan |
Thus Chitosan in epoxy was not in favour of improving the strength under tension, bending and impact. The inclusion of chitosan might act as stress concentration sites in epoxy thereby contribute to reduce the strength properties.
3.5. SEM Analysis
The fractured surfaces of tensile tested specimens were examined under a scanning electronic microscope. Micrographic image of pure epoxy in Figure 5 shows the river-bed pattern. Figure 6 shows the deformed surface. Figure 7 shows agglomeration in 15 wt% epoxy/Chitosan sample.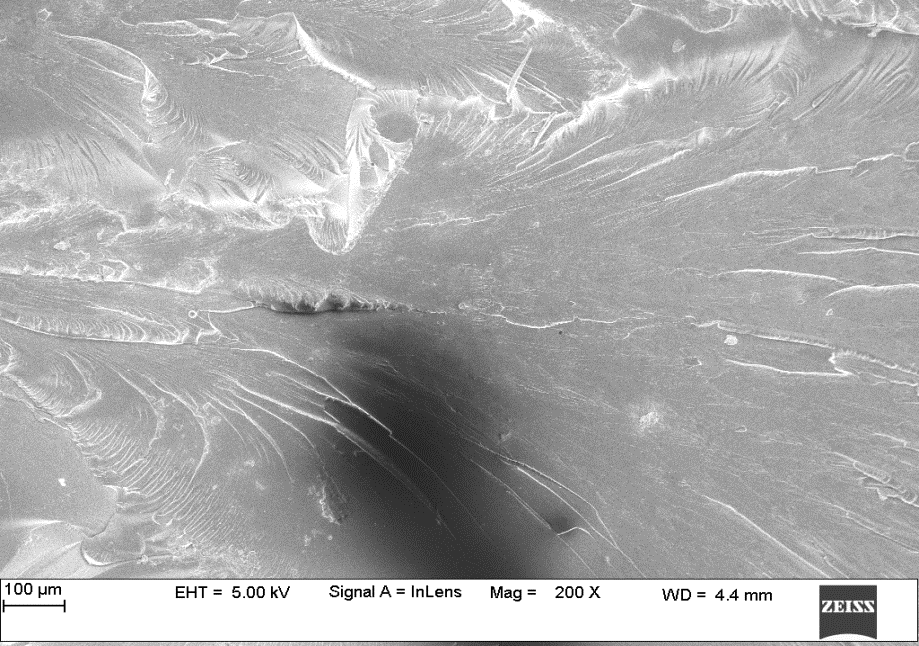 | Figure 5. Micrographic image of pure epoxy |
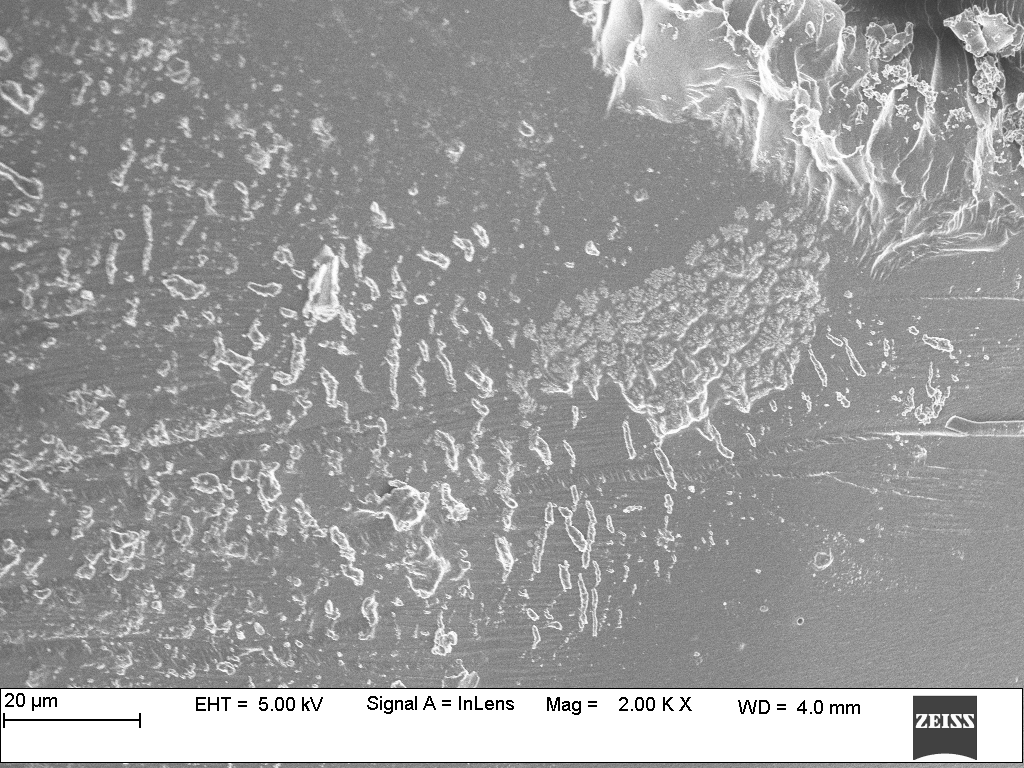 | Figure 6. Micrographic image of epoxy/Chitosan (5 wt. %) |
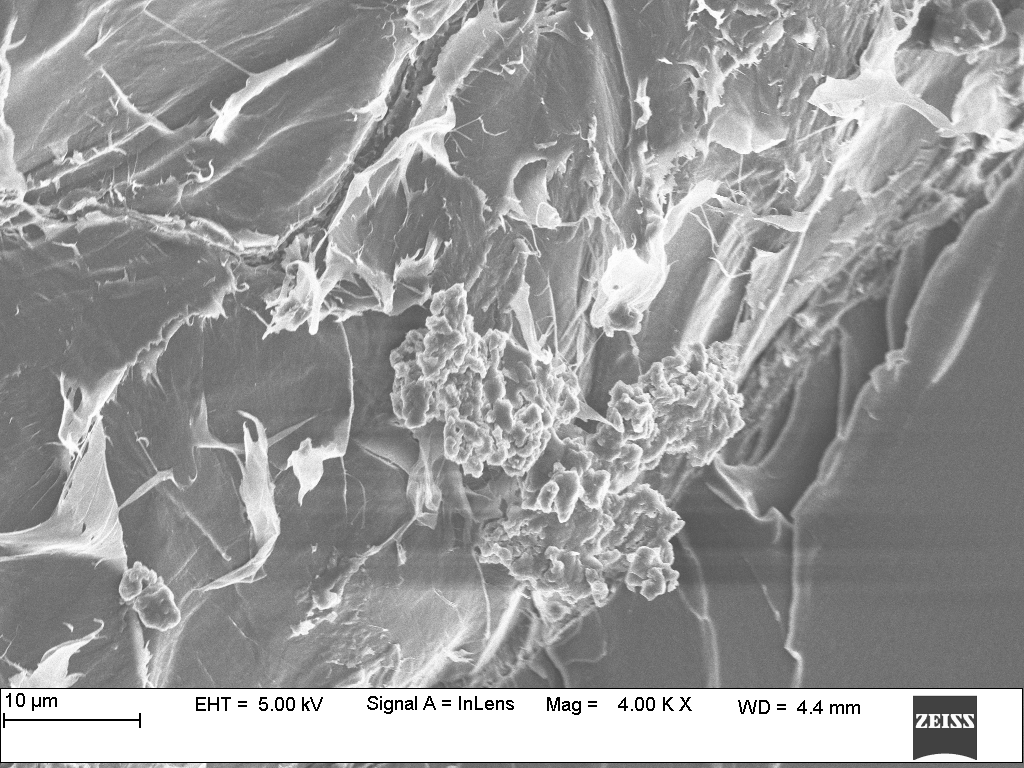 | Figure 7. Micrographic image of epoxy/Chitosan (15 wt. %) |
4. Conclusions
The present work deals with the preparation of chitosan/epoxy composite. The study of mechanical behavior of the composite has led to the following conclusion.Chitosan as a filler is helpful in increasing the surface hardness of the epoxy material. However, it was not beneficial in improving the strength properties under different loading conditions. SEM analysis has shown the traditional plastic flow pattern on the tensile fractured surface. The improvement in the fabrication technique such as mixing can improve the results. The surface treatment of the chitosan before blending with epoxy can further change/improve the results.
References
[1] | S. Boonlertnirun, C. Boonraung and R.Suvanasara, “Application of Chitosan in Rice Production”, Journal of Metals, Materials and Minerals, Vol.18, pp.47-52, November 2008. |
[2] | M. Rinaudo, “Chitin and Chitosan -Properties and Applications”, Journal of Scientific & Industrial Research, Vol. 63, pp. 20-31, January 2004. |
[3] | S. Abdolmohammadi, S. Siyamak, N. A. Ibrahim, W. M. Z. W. Yunus, M. Z. A. Rahman, S. Azizi and A. Fatehi, “Enhancement of Mechanical and Thermal Properties of Polycaprolactone/Chitosan Blend by Calcium Carbonate Nanoparticles”, International Journal of Molecular Sciences, Vol. 13, pp. 4508-4522, March 2012. |
[4] | X. Huang, D. Ge and Z. Xu, “Preparation and characterization of stable chitosan nanofibrous membrane for lipase immobilization”, European Polymer Journal, Vol. 43, pp. 3710–3718, June 2007. |
[5] | H. R. LE, S. QU , R. E. Mackay, R. Rothwell, “Fabrication and mechanical properties of chitosan composite membrane containing hydroxyapatite particles”, Journal of Advanced Ceramics, Vol. 1, pp 66-71, March 2012. |
[6] | I. A. Alsarra, “Chitosan topical gel formulation in the management of burn wounds”, International Journal of Biological Macromolecules, Vol. 45, pp 16–21, March 2009. |
[7] | M. Sudheer, R. Prabhu, K. Raju, and T. Bhat , “Effect of Filler Content on the Performance of Epoxy/PTW Composites”, Advances in Materials Science and Engineering, Volume 2014, pp.1-11, 2014. |
[8] | Y. Wan, L. Tang , L. Gong, D. Yan, Y. Li , L. Wu , J. Jiang, G. Lai, “Grafting of Epoxy Chains onto Graphene Oxide for Epoxy Composites with Improved Mechanical and Thermal Properties”, Carbon 69, pp. 467-480, December 2014. |