Pruthvi Serrao, Chiranth B. P., Neil Vaz, Aaron Fernandis, Pavan Rao, Shambulingesh, Vikas
Department of Mechanical Engineering, St Joseph Engineering College, Mangaluru, India (Affiliated to VTU)
Correspondence to: Pruthvi Serrao, Department of Mechanical Engineering, St Joseph Engineering College, Mangaluru, India (Affiliated to VTU).
Email: |  |
Copyright © 2017 Scientific & Academic Publishing. All Rights Reserved.
This work is licensed under the Creative Commons Attribution International License (CC BY).
http://creativecommons.org/licenses/by/4.0/

Abstract
The effect of Equal Channel Angular Pressing (ECAP) and Solutionizing - Artificial aging (T6) dual treatment on the hardness behaviour of Aluminium 6082 alloy was investigated. The alloy was solutionized and aged for different combinations of temperature and time and then ECAP was carried out at different temperatures (100, 150 and 200°C). The variation of hardness was measured using a standard Rockwell Hardness tester. It was observed that a T6 treatment comprising a solutionizing treatment at 520°C for 2 hours followed by artificial aging at 160°C for 6 hours yielded the best results in terms of measured hardness. And further, ECAP at 100°C following the optimum T6 treatment resulted in hardness enhancement of up to 56.2% as compared to its base hardness (untreated). Also, it was observed that the effectiveness of ECAP increases with decreasing temperature but the processing becomes difficult as it requires more energy for deformation. The results were also validated using statistical analysis.
Keywords:
ECAP, Al-Mg-Si Alloy, Aluminium 6082, Age Hardening, T6 Heat Treatment
Cite this paper: Pruthvi Serrao, Chiranth B. P., Neil Vaz, Aaron Fernandis, Pavan Rao, Shambulingesh, Vikas, Effect of Equal Chanel Angular Pressing and Age Hardening on the Hardness of Al-Mg-Si Alloy, American Journal of Materials Science, Vol. 7 No. 5, 2017, pp. 150-155. doi: 10.5923/j.materials.20170705.06.
1. Introduction
Aluminium and its alloys are considered as the most promising light weight structural materials owing to its excellent properties. It has been generally used in manufacturing of automobile and aircraft components as the high end applications; it is also used for household appliances, containers, and electronic devices, etc. The perks of excellent strength to weight ratio, corrosion resistance, and thermal conductivity are amongst the many advantages of aluminium as it is ascending to be the most reliable material for the future.Pure aluminium is generally soft and finds lesser application as a structural material and hence it is alloyed with other elements such as magnesium, silicon, manganese chromium, etc. Aluminium alloy 6082 grade is a Al-Mg-Si alloy and is a popular grade of aluminium amongst the 6000 series as it offers the highest strength in that series. It is a medium strength alloy with excellent corrosion resistance, machinability, formability and weldability; it is generally used for structural and transport applications. Also, it responds well to heat treatment and is an age hardenable alloy. However, unlike the rest of aluminium alloys, alloy 6082 is not suitable for high temperature applications and also, a maximum hardness of only up to 90 BHN can be achieved upon T6 temper treatment [1].Recent studies showed that, properties of aluminium can be tailored by heat treatment and grain refinement [2, 3]. Equal Channel Angular Pressing (ECAP) is one of the effective methods commonly used to produce ultra-fine grain structure without remarkable geometrical change of bulk materials. Materials processed with ECAP become superior to that of conventional coarse-grained materials [4, 5]. Consequently, a T6 temper is also known to influence the hardness of 6082 alloy, wherein a two-step solutionizing and a later artificial aging is carried out for suitable time and temperature; the intermetallic-phase particles precipitated in the process are hinder the dislocation motion and thus strengthen them. A combined ECAP and age hardening heat treatment is known to enhance the hardness of age hardenable aluminium alloys considerably; the effect of finer grains coupled with the precipitation during aging together acts as barriers for dislocation motions, thus enhancing the strength and hardness. J Gubicza et al. [6] have suggested that the dislocations produced during ECAP being the active nucleation sites will promote the precipitation process. The aim of this work is to investigate the effect of ageing and subsequent ECAP of aluminium 6082 alloy on the hardness.
2. Experimental Work
The test specimen were procured as 10 mm diameter bars which were then cut to a length of 50 mm, long enough to be pressed in an ECAP die.
2.1. Test Material
The material used for the present work is AA6082. It is a general purpose aluminium alloy comprising magnesium and silicon as major alloying additives. They have good machinability and weldability; and can be precipitation hardened. The chemical composition of the test specimen is as shown in Table 1.Table 1. Chemical composition of AA6082 test specimen  |
| |
|
2.2. Heat Treatment
The test samples were first subjected to a T6 temper treatment which involved a solutionizing treatment at temperature of 520°C for duration of 2 hours in a muffle furnace upon which it is quenched in water maintained at RT; it is then followed by artificial aging for the different possibilities of temperature and time in order to identify the optimum aging parameters. A total of 36 samples were first machined to specifications, cleaned and solutionized, of which 12 samples were artificially aged at 120°C with a set of four samples aged for a duration of 2, 4 and 6 hours each and then air cooled. Further, the remaining 2 sets of 12 samples each were aged at 150°C and 180°C in a similar manner. A sample each from different possibilities of temperature and time of heat treatment is retained for hardness measurement whereas the remaining samples were subjected to subsequent ECAP.
2.3. Equal Channel Angular Pressing
A single pass ECAP of the T6 temper - 6082 alloy samples was performed for three different temperatures (RT, 100 and 150°C). The die used for ECAP is made from OHNS (Oil Hardened Non-sticking Steel) with a split-type of arrangement to facilitate easy removal of the sample after pressing. Two 10mm diameter symmetric channel were ground on the split-die which were intersecting at an angle of 120° with a curvature angle of 30°; the channel was polished to have a mirror finish to perform the pressing with ease. Oil quenched fasteners were used to hold the die together while pressing the specimen through its channel. In the process, a heating unit clamped to the die heats the specimen to the desired temperature measured with the help of a thermocouple inserted into the die and then the specimen is pressed through the die channel using a plunger in a 60 ton capacity Universal Testing Machine (UTM) at different temperatures. The set up for ECAP of the test samples is as shown in Figure 1. The heating of the specimen facilitates easy processing; however, the effectiveness of ECAP is known to reduce with increasing temperature due to possible recovery and grain growth. Molybdenum disulphide grease (Moly grease) is used as a lubricant during processing to avoid friction and enable easy sliding of the specimen. After pressing the sample along with the die is let to cool down to RT before it can be unclamped for the pressing of next specimen. The samples are held for hardness measurement upon ECAP. 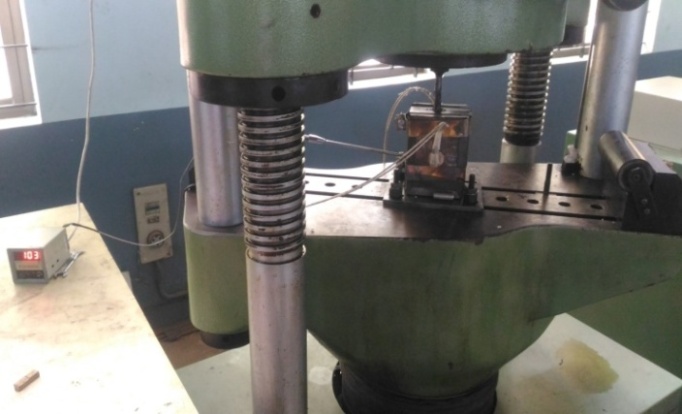 | Figure 1. ECAP carried out in a UTM with heating unit |
3. Results & Discussions
The solutionized, aged and ECAPed samples were tested for variation in the hardness. Hardness of the specimens were measured using a Vickers hardness tester, an indentation based tester equipped with a diamond indenter; a mean of three hardness readings were recorded. The hardness of the as received sample was measured as 71.1 HV and the influence of the aging and ECAP on hardness is presented and discussed below.
3.1. Effect of T-6 Temper on Hardness
A T-6 temper is a well-known hardening treatment given to AA6082 alloy owing to its excellent response to aging by formation of intermetallic phase particles. Several research works have been carried out on studying the effect of aging of aluminium alloys on its mechanical properties. Dadbakhsh et al. [7] have studied the effect of aging on the hardness behaviour of 6082 aluminium alloy and have reported a peak hardness for an aging carried out between the temperature ranges of 160 to 180°C for duration of 3 to 6 hours. In the present work at the primary stage an optimization of aging treatment was carried out for the given samples and it was found that an aging treatment conducted at 160°C for 6 hours was found best suited. However, from the hardness trend as seen in the Figure 2, an increment of aging time would have further enhanced the hardness at 160°C.The aging at 120°C had no effect on hardenability; whereas, at 180°C peak hardness close to the base hardness was obtained when aged for 4 hours which decreased upon further increase in aging time.
3.2. Effect of Pre-aging and ECAP on Hardness
The aged samples were subsequently processed by ECAP technique and the variation in hardness was noted. It was observed that the hardness was substantially increasing upon further processing by ECAP however it is very much dependent on the temperature at which pressing was carried out. It is evident in the literatures regarding the effect of ECAP on hardness with maximum strengthening being achieved under room temperature processing as compared to the higher processing temperatures; however, with lower temperatures processing becomes very difficult as it would require more energy. A single pass ECAP at 100°C after aging displayed a constant trend of hardness increment (Figure 3) with the aging time from 2 hours to 6 hours; an increase from base hardness of 71.1 HV to as high as 112 HV was recorded. The aging time were fixed to be 2 to 6 hours from the observations made through the literatures; however, in the present case a slight increment in hardness may be observed upon extended aging time but not in excess of 10 to 12 hours. The subsequent ECAP at 100°C of samples aged at 160°C yielded the optimum hardness of 112 HV followed by 99.4 HV and 91.8 HV at 120°C and 180°C respectively, where all samples were aged to 6 hours.Similar trend was observed for the samples aged at 160°C upon subjecting to ECAP at 150°C as shown in Figure 4; a max hardness of 110 HV was recorded for an aging of 6 hours. Whereas, the samples aged at other extreme temperatures followed a decline in hardness with the aging time. Nevertheless, the hardness was fairly higher than the base hardness. Also, it was noted that the aging at 180°C for 2 hours featured fairly better hardness than the samples aged at 160°C. ECAP at 200°C was not favourable for hardness enhancement as only a marginal increment or constant drop in hardness was observed with increasing aging time for the selected temperature range of aging treatment. Peak hardness was reported for 4 hours aged samples at 160 and 180°C.On an overall observation, even though best hardness results were obtained for ECAP at 100°C, the effect of aging were prominent for ECAP at 150°C as a marginally close hardness values were obtained for the entire aging range from 2 to 6 hours.In order to support the direct findings from the hardness plots and to assess the contribution of the individual parameters towards enhancing hardness along with their interactions a detailed statistical analysis was carried out.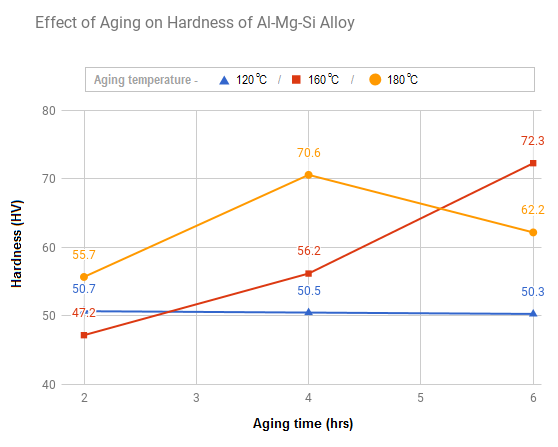 | Figure 2. Effect of aging on the hardness of 6082 aluminium alloy |
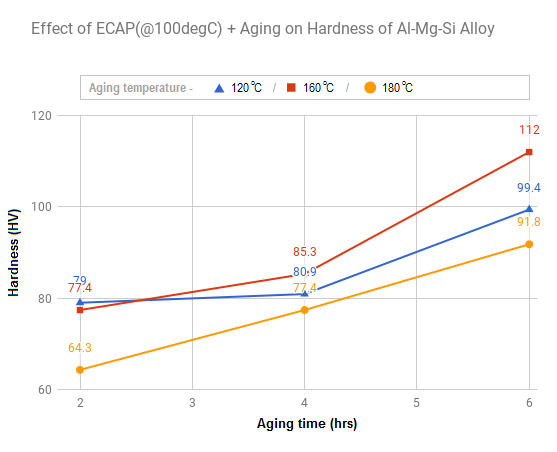 | Figure 3. Effect of aging followed by ECAP at 100°C on the hardness of 6082 aluminium alloy |
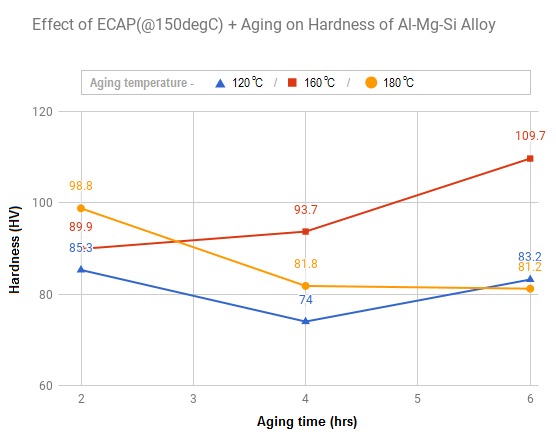 | Figure 4. Effect of aging followed by ECAP at 150°C on the hardness of 6082 aluminium alloy |
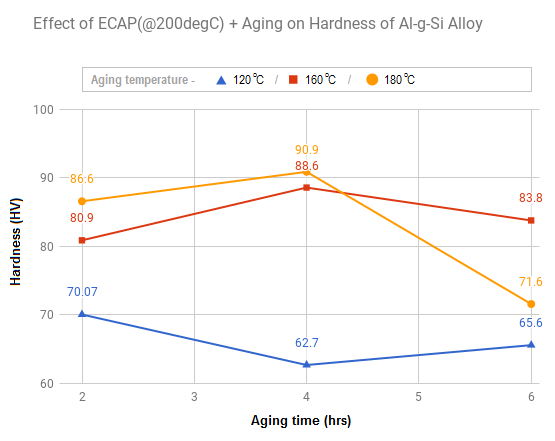 | Figure 5. Effect of aging followed by ECAP at 200°C on the hardness of 6082 aluminium alloy |
3.3. Statistical Analysis of Hardness
With the measured hardness as (Table 3) response, a statistical analysis was conducted using Minitab 15 software for a full factorial design. The factors considered and their levels are as shown in Table 2. The Main effect plots, Interaction plots were obtained and ANOVA results are used to support the findings. An interaction plot was constructed as shown in Figure 6, to understand the relationship between factors and the hardness (response); it can be clearly seen that the interaction effects are significant. Thus, considering the interaction plot and the main effects plot (Figure 7) it can be suggested that an aging temperature and time of 160°C and 6 hours respectively, with an ECAP temperature of 150°C can be selected in order to obtain optimum hardness.Table 2. Factors and their levels considered for full factorial design 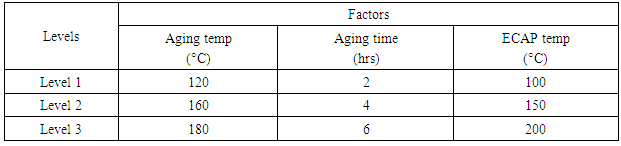 |
| |
|
Table 3. Measured hardness values of the processed samples 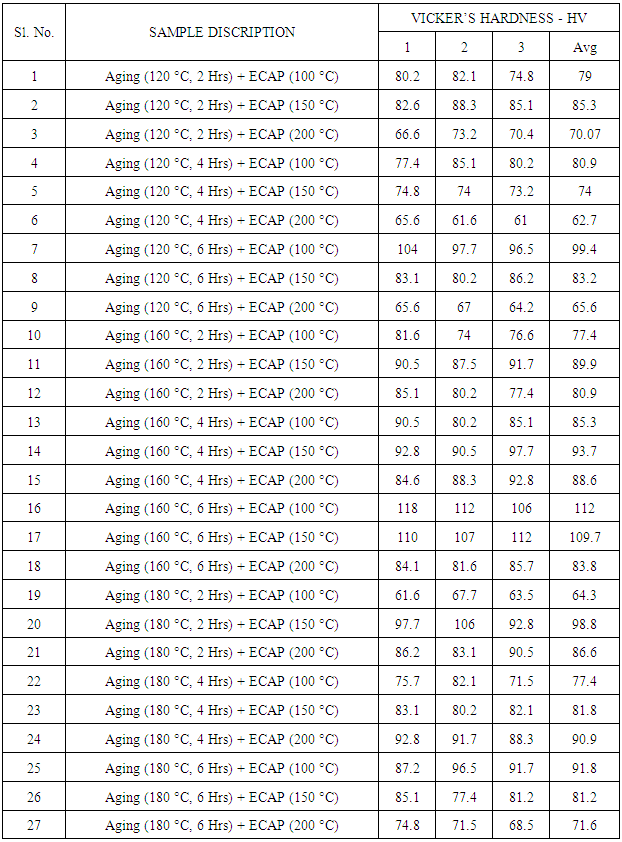 |
| |
|
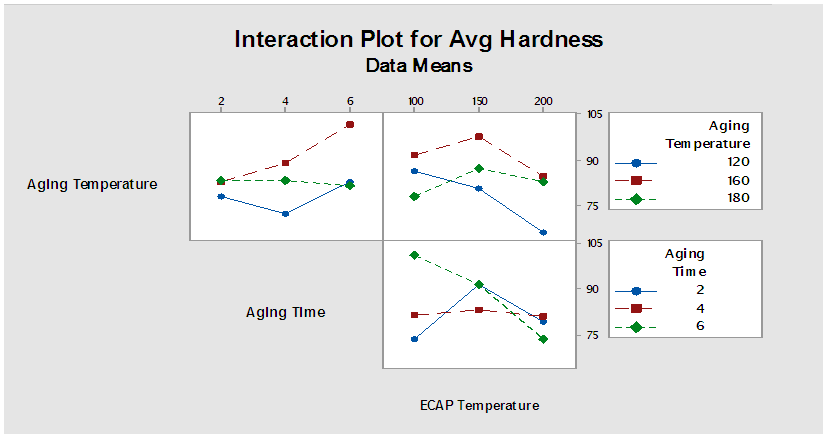 | Figure 6. Interaction plot of factors considered for average hardness measurements |
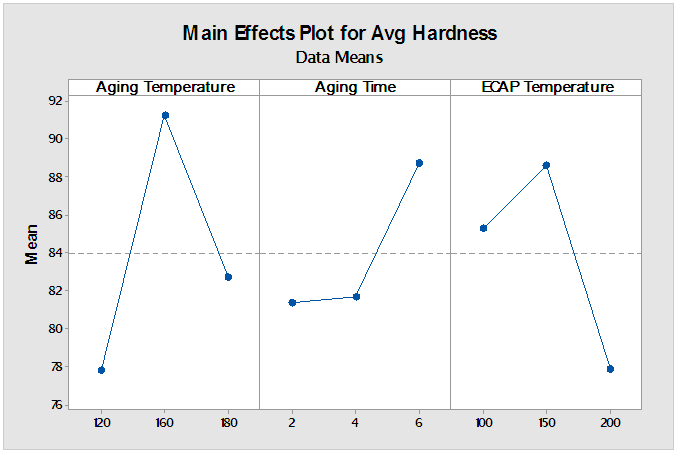 | Figure 7. Main effect plot for the average hardness using data means |
Also, the analysis of variance (ANOVA) was performed in order to evaluate the statistical significance of the factors and their interactions. The analysis was carried out with a confidence level of 95% by considering p-values less than 0.05 towards significant contribution [8]. The percentage contribution of the factors and their interactions is as shown in Table 4 and it can be seen that a significant two-way interaction (52%) was observed among the factors with interaction between aging time and ECAP temperature being significant towards hardness optimization.Table 4. Analysis of Variance for data mean, using Adjusted SS 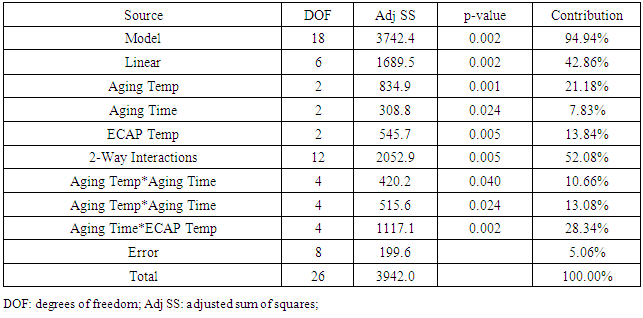 |
| |
|
4. Conclusions
It is observed that the combination of T6 heat treatment and a subsequent ECAP can effectively increase the hardness of AA6082 alloy. Following observations were made during the study: A solutionizing treatment at 520°C for 2 hours followed by artificial aging at 160°C for 6 hours yielded the best hardness. ECAP carried out at 100°C of the samples aged at 160°C for 6 hours resulted in substantial hardness enhancement form 71.1 HV to 112 HV (56.2%). Even though best hardness results were obtained for ECAP at 100°C, the effect of aging were prominent for ECAP at 150°C as a marginally close hardness values were obtained for the entire aging range from 2 to 6 hours. Statistical analysis performed suggests the selection of aging temperature and time of 160°C and 6 hours respectively, with an ECAP temperature of 150°C in order to obtain optimum hardness.On a concluding remark, post-ECAP aging was not carried out in the present work due to possible softening of the material owing to annealing effects and with the sole objective of hardness enhancement the present work was limited to pre-aging and ECAP.
ACKNOWLEDGEMENTS
The authors wish to acknowledge the resources provided by the Research Centre, Department of Mechanical Engineering, St Joseph Engineering College - Mangaluru towards heat treatment and material processing. Special thanks to HEBIC Industrial Training Institute for preparing the ECAP die and V&G Industrial Testing Laboratories Pvt. Ltd. for testing of samples.
References
[1] | G. Mrówka-Nowotnik, J. Sieniawski, M. Wierzbiñska., 2007, Intermetallic phase particles in 6082 aluminium alloy., Archives of Materials Science and Engineering, 28(2), 69–76. |
[2] | M. H. Shaeri, M. Shaeri, M. Ebrahimi, M. T. Salehi, S. H Seyyedein., 2016, Effect of ECAP temperature on microstructure and mechanical properties of Al–Zn–Mg–Cu., Progress in Natural Science: Materials International, 26, 182–191. |
[3] | S. Far`e, N. Lecis, M. Vedani., 2011, Aging Behaviour of Al-Mg-Si Alloys Subjected to Severe Plastic Deformation by ECAP and Cold Asymmetric Rolling., Journal of Metallurgy, doi:10.1155/2011/959643. |
[4] | R.Z. Valiev, T.G. Langdon., 2006, Principles of equal-channel angular pressing as a processing tool for grain refinement., Progress in Materials Science, 51, 881–981. |
[5] | R.B. Figueiredo, T.G. Langdon., 2009, Principles of grain refinement and superplastic flow in magnesium alloys., Materials Science and Engineering, A501, 105–114. |
[6] | J. Gubicza, I. Schiller, N.Q. Chinh, J. Illy, Z. Horita, T.G. Langdon., 2007, The effect of severe plastic deformation on precipitation in supersaturated Al–Zn–Mg alloys., Materials Science and Engineering, A 460–461, 77–85. |
[7] | S. Dadbakhsh, A. Karimi Taheri, C.W. Smith., 2010, Strengthening study on 6082 Al alloy after combination of aging treatment and ECAP process., Materials Science and Engineering, A527, 4758–4766. |
[8] | Pruthvi Serrao, Ravikanth Prabhu, Chiranth B. P., Yazid Mohammed., 2106, Application of Taguchi Method to Predict the Abrasive Wear Behavior of CP Titanium., Journal of Mechanical Engineering and Automation, 6 (5A), 13-17. |