Pruthvi Serrao1, Jagannath Nayak2
1Department of Mechanical Engineering, St Joseph Engineering College, Mangaluru, India (Affiliated to VTU)
2Department of Metallurgical & Materials Engineering, NITK, Surathkal, India (Affiliated to NIT)
Correspondence to: Pruthvi Serrao, Department of Mechanical Engineering, St Joseph Engineering College, Mangaluru, India (Affiliated to VTU).
Email: |  |
Copyright © 2017 Scientific & Academic Publishing. All Rights Reserved.
This work is licensed under the Creative Commons Attribution International License (CC BY).
http://creativecommons.org/licenses/by/4.0/

Abstract
The effect of a two stage surface treatment, viz. surface mechanical attrition treatment (SMAT) and aluminizing on surface hardness of commercially pure titanium was investigated. SMAT was carried out in a controlled atmosphere for a duration of 60 mins at an operating frequency of 50Hz to refine the grain structure at the surface to a depth of about 200 μm. Subsequently, the sample was aluminized at 550 and 600°C using CVD-FBR technique to obtain hard aluminide coating. The coatings obtained are studied using Optical Microscopy (OM), X-ray diffraction (XRD) and glow discharge optical emission spectroscopy (GDOES). The SMAT samples were found to greatly enhance the surface hardness upon aluminizing in spite of resulting in comparatively poor diffusion coating thickness than the coarse grained titanium.
Keywords:
SMAT, Nanocrystallization, Aluminizing, Titanium, Surface engineering
Cite this paper: Pruthvi Serrao, Jagannath Nayak, Effect of Surface Mechanical Attrition Treatment and Aluminizing on the Hardness of CP Titanium, American Journal of Materials Science, Vol. 7 No. 5, 2017, pp. 145-149. doi: 10.5923/j.materials.20170705.05.
1. Introduction
Titanium is an excellent structural material offering high strength to weight ratio having a melting point of 1670C. However, it is not used in applications exceeding 550C; above which the gases like oxygen and nitrogen diffuse into titanium and deteriorates its properties. This can be overcome by coating titanium with a protective layer [1]. Aluminizing is an efficient diffusion based thermochemical surface treatment to synthesize aluminide (Al-Ti intermetallic) coating on a titanium substrate. Intermetallic compounds based on titanium and aluminium are light (low density), relatively stiff (high modulus), and have attractive high temperature mechanical properties such as tensile and creep strength [2]. There are many surface coating techniques such as chemical vapour deposition (CVD), physical vapour deposition (PVD), sputtering, pack cementation, etc. which can be employed for aluminizing the surface of a titanium substrate. CVD and pack cementation are more frequently used surface coating techniques but however conventional CVD require high temperatures and high vacuum whereas pack cementation requires high temperatures and long holding times thereby limiting these techniques as these would degrade the mechanical properties owing to high temperatures involved. Therefore, as an alternative CVD-FBR technique can be used; through which it is possible to obtain Al coatings at lower temperature (less than 600C) and relatively short times allowing the conservation of microstructure and mechanical properties. Moreover with the use of fluidized bed reactor it is possible to obtain high and uniform mass and heat transfer rates [3].There has been extensive study on enhancing the effectiveness of diffusion based thermochemical treatments; and several reports have been made regarding improvements in diffusion kinetics after grain refinement. A severe plastic deformation technique, namely: Surface Mechanical Attrition Treatment (SMAT) is an efficient technique to refine the grain structure and induce numerous surface defects on the sample surface [4]. SMAT has been found to be an effective technique for enhancing the microstructure and properties of a material without changing its composition. This technique is being extensively studied and several research works have been carried out on various different materials. Several reports have been made on hardness enhancement through nanocrystallization. The enhancement in mechanical properties of nanocrystalline materials compared to their traditional coarse-grained polycrystalline counterparts is due to the grain size effect [5].The present work involves the study of SMAT and Aluminizing dual treatment towards enhancing the surface hardness of commercially pure titanium.
2. Experimental Methods
The material used for the current study is commercially pure titanium. However, even in its purest form titanium will have traces of elements such as Aluminium, Chromium, Iron, Silicon, etc. The element composition of the specimen obtained by spectro-analysis is as shown in Table 1. A titanium disc, 100mm in diameter and 4mm thick was procured for the present work. The sample was first subjected to grain refinement by SMAT on one side; then cut into smaller pieces of size 10mm x 12mm which was further aluminized at different temperatures. Table 1. Elemental composition of test sample  |
| |
|
2.1. SMAT
SMAT was carried out in SMAT equipment at the Institute for Frontier Material (IFM), Deakin University, Australia. The sample was fixed on to the SMAT chamber filled with steel shots of 8mm diameter and clamped firmly. The chamber was vibrated with a frequency of 50Hz, the repeated impact of the randomly flying steel shots on to the specimen surface severely deforms it resulting in grain refinement; the chamber was sealed and vacuum was applied to avoid any possibility of oxidation of the surface as titanium is very reactive and with the surface being heated during processing the oxidation potential would further increase. The schematic of the treatment is as shown in Figure 1.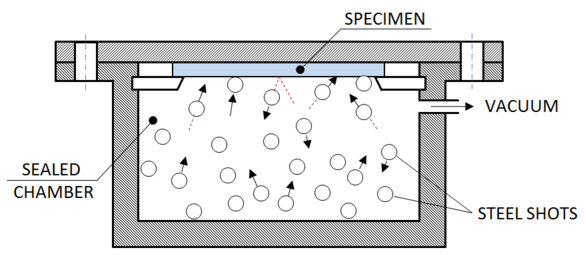 | Figure 1. Schematic sketch of SMAT |
2.2. Aluminizing Treatment
Aluminizing was carried out in a fluidized bed furnace employing CVD-FBR (Chemical Vapour Deposition – Fluidized Bed Reactor) technique; wherein, metal sub-halide chemistry is used to produce diffusion coatings. Sub-halide chemistry consists of using powders of metals as the fluidizing particles and any hydrogen halide as the reactive gas. In the present work pure aluminium was used as the fluidizing particles (pure Al) in the powder form and HCl (g) was used as hydrogen halide. The treatment was done at two different temperatures; 550 and 600°C for duration of 4 hrs each.In the process the powdered aluminium particles are loaded in the reactor through a detachable top and the system is heated to the desired temperature while purging it with argon gas to keep the bed fluidized thus avoiding pre-sintering of the aluminium particles. Once the desired temperature is reached, as a purification measure a flow of hydrogen gas is let in to reduce any impurities present in the system. Then the test samples are immersed into the bed by means of shaft and hydrogen halide is added to the Ag + H2 gas mixture. The halide reacts with the aluminium particles in the bed producing the sub-halide species; the reactive metal chlorides (AlCl4) are formed in-situ and decomposed on the sample surface [6].
2.3. Specimen Preparation
After SMAT and Aluminizing the sample is subjected to hardness, microstructural and compositional analysis. Hardness is measured using a Vickers Microhardness tester and it hardly requires any specimen preparation. However, a detailed microstructural analysis requires a well-polished surface. A detailed practice involved in the preparation of titanium surface for microstructural observation has been explained in our previous work [7, 8]. The microstructure of the polished samples and the phases developed were not accessible through optical microscopy in the unetched condition so the samples were etched with Kroll’s etchant (100ml distilled water, 2ml Hydrofluoric acid and 6ml Nitric acid) for 3 minutes [9].
3. Results and Discussion
The samples were tested for the effectiveness of grain refinement and diffusion treatment towards enhancing the surface hardness. OM, GDOES and XRD were employed to inspect the coating thickness, amount diffused across the depth, and compounds formed respectively; also, the hardness across the depth from the surface was measured using Vickers Microhardness tester.
3.1. Physical Appearance
The SMAT samples depicted a shiny and wavy surface due to multiple impacts of the steel shots. The aluminized samples turned dark silver (greyish) from silver at both 550 and 600°C. The colours of the coatings may be the result of the light interference phenomenon within the surface layer above the substrate.
3.2. Optical Microscopy
The etched samples were observed under optical microscope at 1000x magnification. A uniform aluminized coating was obtained at 550°C and 600°C. The effect of aluminizing was low at 550°C in both SMAT and CG samples and a coating of thickness of about 3 μm were obtained. Whereas, at 600°C a coating of about 15 μm thick was obtained in CG sample as shown in Figure 2 but SMAT sample showed a coating only up to 7 μm thick.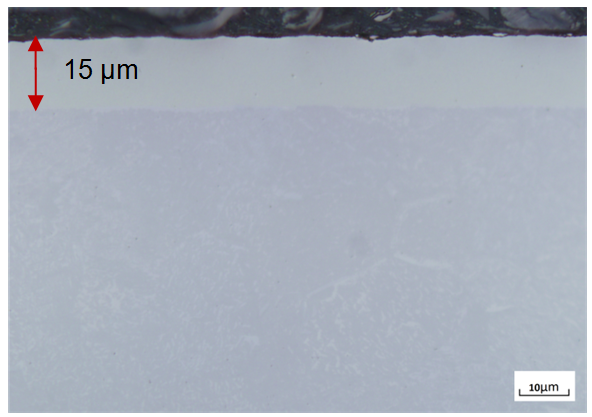 | Figure 2. Optical microstructure of course grained titanium aluminized at 600°C for 4 hours showing an aluminide coating |
3.3. GDOES
A spectroscopy analysis showing the quantity of elements diffused (atomic percent) across the depth from the surface of the sample after Aluminizing for both SMAT and CG samples is shown in Figure 3.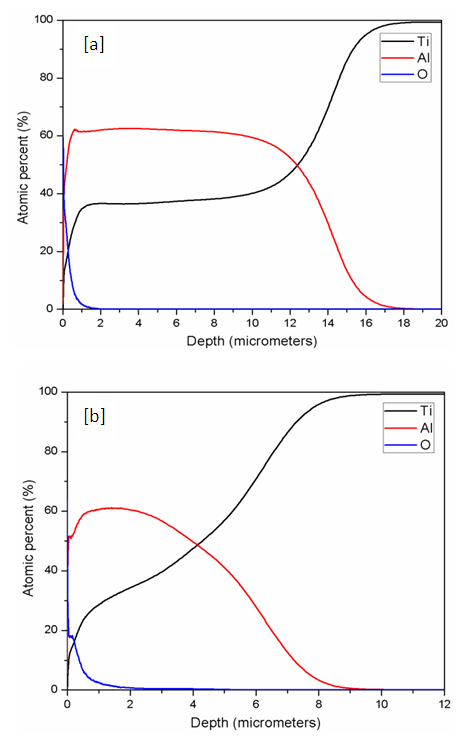 | Figure 3. A quantitative depth profile showing the diffusion of aluminium (atomic percent) across the depth from the surface after aluminizing at 600°C; (a) un-SMAT; (b) SMAT |
From the quantitative depth profile a clear difference in the effect of aluminizing in case of CG and SMAT samples was observed. The CG samples showed higher amount of atomic diffusion and also to a larger depth than the SMAT samples. In both the samples a maximum diffusion amount of about 60% (atomic percent) was observed thus indicating the maximum solubility of aluminium in titanium. At 600°C the aluminium diffusion in a CG sample reaches maximum and remains constant up to a depth of several microns thus indicating the formation of a strong coating.
3.4. X-ray Diffractometry
The compounds formed during aluminizing were identified as Al3Ti and Al5Ti2. The Al3Ti appears to be the major compound. In a CG sample strong peaks of Al3Ti besides the Ti peaks were observed at 550°C; few peaks of Al5Ti2 were also identified. At 600°C as shown in Figure 5(a) the peaks of the two compounds formed were dominant and hardly few peaks of Ti of relatively very low intensity were visible. In case of SMAT samples very low aluminizing effect was seen at 550°C as the peaks of Ti were strong and dominant and a very few low intensity peaks of Al3Ti and Al5Ti2 were identified. At 600°C as shown in Figure 5(b) the peaks of Ti were still prevalent and an increase in the intensities of Al3Ti and Al5Ti2 peaks was noted.
3.5. Microhardness
Hardness was measured before and after the surface treatments. Before aluminizing the measured hardness values were about 160 HV for a CG sample whereas the SMAT sample was found to have a peak hardness of 240 HV at the surface. Hardness values up to 620 - 670 HV were obtained at the sample surface after aluminizing. The SMAT samples were found to have better hardness (harder by a value approx. 50 HV than CG sample). Comparing the hardness profiles it appears that, though SMAT samples show greater hardness than the CG samples, the CG samples gain hardness quickly than SMAT samples upon surface treatment. 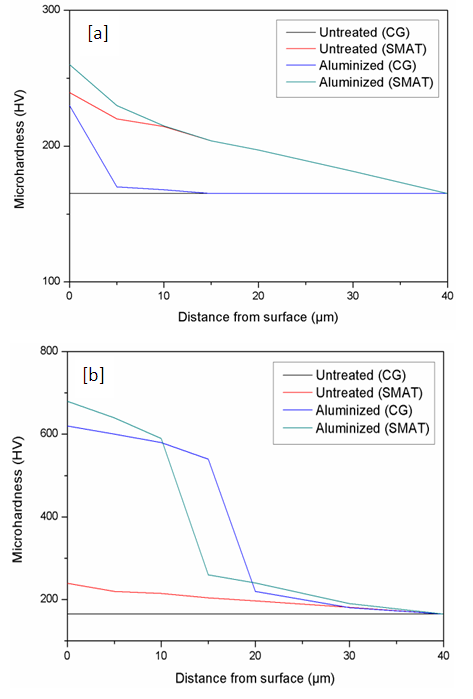 | Figure 4. Hardness profiles for SMAT and un-SMAT titanium before and after aluminizing; (a) at 550°C; (b) at 600°C |
At 550°C as shown in Figure 4(a) the CG sample show a peak hardness of 230 HV and reduces quickly to bulk hardness at a depth of 10 microns whereas the SMAT sample found a slight hardness increment to 260 HV at the surface from which it gradually reduces merging with the untreated SMAT hardness profile at a depth of 10 microns. At 600°C as shown in Figure 4(b) a nearly stable hardness profile was found from the surface to a depth of 15 μm and 9 μm in CG and SMAT samples respectively from which it falls suddenly to their near bulk hardness values which suggests a thicker coating in a CG sample as compared to SMAT sample. The sudden fall in the hardness values can be due to a receding compound layer and an encounter with the diffusion zone wherein aluminium being a softer material has no contribution in enhancing hardness.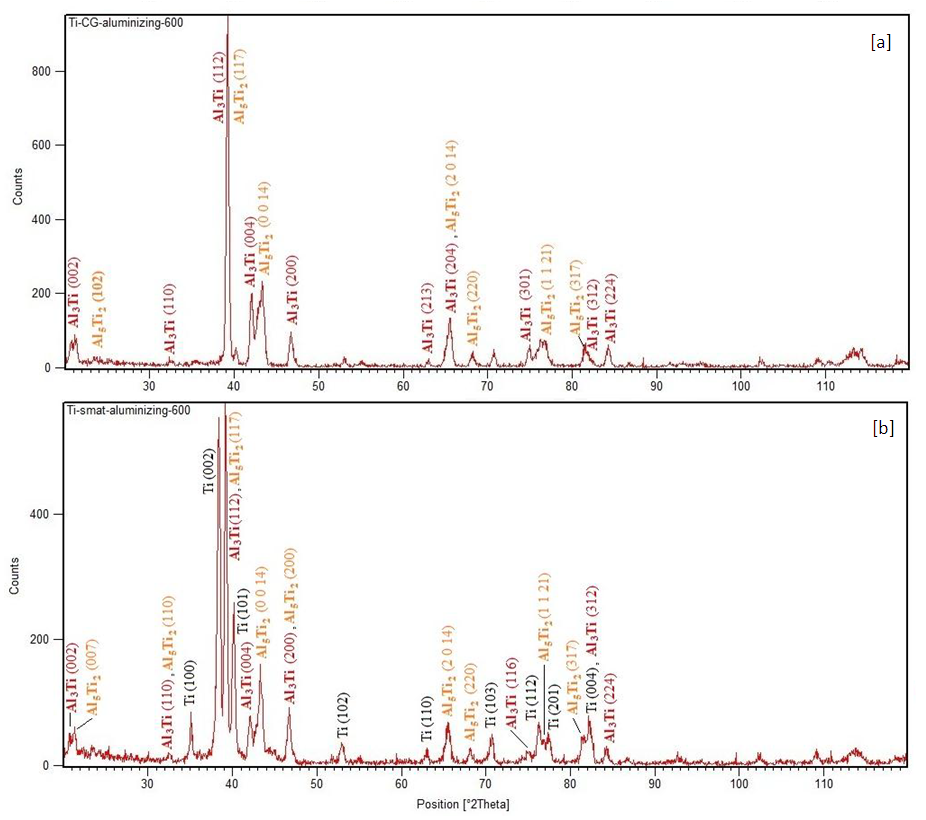 | Figure 5. The XRD patterns of titanium aluminized at 600°C; (a) un-SMAT; (b) SMAT |
4. Conclusions
In the present work, a successful grain refinement was achieved via SMAT and subsequently a thick aluminium-titanium intermetallic coating was developed on titanium substrate at low temperature (550 to 600°C) aluminizing, carried out for a duration of 4 hours. Following conclusions can be drawn after detailed investigation: Aluminizing was more effective without SMAT in terms of the thickness of coating obtained but the SMATed samples developed slightly better hardness upon aluminizing when compared to its CG counterparts. The thickness of the coating developed were 15 μm and 9 μm in the CG and SMAT samples respectively after aluminizing at 600°C for 4 hours. The SMAT-Aluminized samples showed a peak hardness of 670 HV at 600°C whereas in the CG-Aluminized samples the peak hardness was 620 HV. The XRD analysis has confirmed the formation of a compound layer made of Al3Ti and Al5Ti2 intermetallic of aluminium and titanium in both CG and SMAT samples after aluminizing.
ACKNOWLEDGEMENTS
The author wishes to acknowledge the research lab facilities and equipments provided by Institute for Frontier Materials (IFM), Deakin University Geelong, Australia.
References
[1] | Oshida, Yoshiki. “Oxidation and Oxides,” Bioscience and Bioengineering of Titanium Materials. 1st ed., Elsevier, 2007, 4, pp. 81-103. |
[2] | Gerd Lütjering, James C. Williams. Titanium. 2nd ed., Springer, 2007. |
[3] | Pérez, F.J. Hierro, M.P. Trilleros, J.A. Carpintero, M.C. Sánchez, L. Brossard, J.M. and Bolívar, F.J., “Iron aluminide coatings on ferritic steels by CVD-FBR technology,” Intermetallics, Vol. 14, pp. 811-817, 2006. |
[4] | Lu, K. and Lu, J., “Nanostructured surface layer on metallic materials induced by surface mechanical attrition treatment,” Materials Science and Engineering, Vol. 375–377: pp. 38–45. 2004. |
[5] | Tong, W.P. Han, Z. Wang, L.M. Lu, J. and Lu, K., “Low-temperature nitriding of 38CrMoAl steel with a nanostructured surface layer induced by surface mechanical attrition treatment”, Surface & Coatings Technology. Vol. 202: pp. 4957-4963, 2008. |
[6] | Pérez, F.J. Hierro, M.P. Pedraza, F. Gómez, C. and Carpintero, M.C., “Aluminizing and chromizing bed treatment by CVD in a fluidized bed reactor on austenitic stainless steels,” Surface and Coatings Technology, Vol. 120-121, pp. 151-157, 1999. |
[7] | Pruthvi Serrao, Jagannath Nayak, “Effect of Surface Mechanical Attrition Treatment on High Temperature Oxidation of CP Titanium,” American Journal of Materials Science, Vol. 6, pp. 20-24, 2016. |
[8] | Pruthvi Serrao, Jagannath Nayak, Daniel Fabijanic, “Effect of surface mechanical attrition treatment and subsequent nitriding on microstructure and surface hardness of CP titanium,” Conference Proceedings – ERCAM, McGrawhill publishing, 2017 (Article in Press). |
[9] | George F. Vander Voort, (1999), “Metallography - Principles and Practice” ASM International, Materials Park, OH, p 692. |