Pruthvi Serrao, Mohammed Yazid, Neil Vaz, Chiranth B. P., James Valder
Department of Mechanical Engineering, St Joseph Engineering College, Mangaluru, India (Affiliated to VTU)
Correspondence to: Pruthvi Serrao, Department of Mechanical Engineering, St Joseph Engineering College, Mangaluru, India (Affiliated to VTU).
Email: |  |
Copyright © 2017 Scientific & Academic Publishing. All Rights Reserved.
This work is licensed under the Creative Commons Attribution International License (CC BY).
http://creativecommons.org/licenses/by/4.0/

Abstract
Commercially pure aluminium cylindrical flat pins were subjected to severe plastic deformation by means of Equal Channel Angular Pressing (ECAP) at elevated temperature of 250°C to facilitate easy deformation without failure and tested for adhesive wear on a standard pin-on-disc machine against a steel disc for dry sliding condition in the atmospheric air. The design of experiments (DOE) approach using Taguchi method was employed to predict the wear behaviour against variable parameters such as load, speed, sliding duration and number of ECAP passes. Also, the ANOVA technique was used to study the optimum level of the parameters and their influence on wear loss. The results indicate that the ECAP has a profound influence in enhancing the hardness and consequently the wear resistance of pure aluminium. Additionally, mathematical models have been developed to establish relationship between the processing parameters and the wear loss.
Keywords:
Aluminium, ECAP, Adhesive wear, Taguchi orthogonal array, Pin-on-disc, ANOVA
Cite this paper: Pruthvi Serrao, Mohammed Yazid, Neil Vaz, Chiranth B. P., James Valder, Study of Adhesive Wear Behavior of Pure Aluminium Processed by Equal Channel Angular Pressing, American Journal of Materials Science, Vol. 7 No. 5, 2017, pp. 140-144. doi: 10.5923/j.materials.20170705.04.
1. Introduction
Aluminium, being the most sought light metal has been extensively used particularly for the aerospace applications over the past two decades owing to its high strength to weight ratio, excellent thermal conductivity and corrosion resistance. However, its application areas are rapidly growing now and it is the second most widely used metal, thus making it a general engineering material. Though, one of the major issues concerning the limitation of aluminium and its applications is the poor resistance to wear in its unalloyed form; with suitable alloying additives it is possible to address this issue but certain applications that require the metal to be used in its purest form has necessitated employing suitable techniques to enhance wear resistance [1].There has been extensive study on enhancing the hardness and wear resistance of aluminium by spray coatings, surface quenching and through synthesis of diffusion coatings. However very few research work has been conducted employing the bulk treatment via SPD techniques to enhance wear resistance. Severe plastic deformation (SPD) is a process wherein the specimen is subjected to deformation at high strains and high shear, resulting in very high flaw density and equiaxed ultra-fine grain size. ECAP is one such technique to induce fine grains and effectively enhance the hardness and wear resistance of the bulk material. Moreover, with a fine grained structure it is also expected to be more susceptible to diffusion based surface treatments owing to enhanced grain boundary diffusion. Though, studying the effect of this is out of the scope of present work and is only suggested for future work.ECAP is one of the most effective and extensively studied SPD techniques. It increases the strength, hardness and wear resistance which can be explained with the help of Hall-Petch equation, which relates the yield strength of a metal to its grain-size; with yield strength inversely proportional to the square root of the average grain diameter. The strengthening by this method can be attributed to the impeding of the dislocation motion; the deformation of a metal takes place as the dislocation moves from grain to grain, with the finer grains the dislocations are stopped at a grain boundary, thereby strengthening the metal. This method of strengthening the metal is termed as Grain-boundary strengthening or Hall-Petch strengthening [2]. There have been numerous reports on the enhancement of mechanical properties such as strength and hardness after ECAP due to grain size reduction. Yulu et al. [3] studied the microstructure of aluminium alloy 7005 through ECAP process. The process is conducted at room temperature at different processing routes. The changes in microstructure were observed through optical microscope. After 7 ECAP passes, the grain size was reduced to 0.87μm, the yield strength increased from 170MPa to 379MPa with an elongation of 13 percent. Also, tensile strength increased to 400MPa. Mohamed Ibrahim et al. [4] studied the influence of ECAP on the microstructure and mechanical properties of pure aluminium; they achieved a reduction in the grain size from 390 µm to 0.3 µm with 10 passes.In the present work as the first phase the aluminium is subject to ECAP at elevated temperature to facilitate easy deformation without material failure. The treated aluminium sample is then subjected to adhesive wear against the steel disc to measure its wear resistance. The objective of the present work is to study the effectiveness of the ECAP in enhancing wear resistance and hardness.
2. ECAP Process
ECAP is a process in which metal billet is pressed by using hydraulic pressure through a die channel of suitable angle (about 90° to 120°) to change the grain structure. The process may be repeated several times to get the optimum results. The effectiveness of ECAP increases with multiple passes and also the route followed for the subsequent passes. Accordingly, there are route A (orientation unchanged), route B (specimen rotated by 90° - BA for same direction & BC for alternate rotations) and the route C (specimen rotated by 180°). But it was observed that with multiple passes the strength increases substantially and it becomes difficult to process after certain passes [5].
2.1. Die Preparation
A split die was prepared from OHNS (oil hardening non sticking steel) with the angle (die angle) as 120° and ψ (curvature angle) as 30° for the present work as shown in figure above. The die channel is made very smooth for the specimen to pass easily. Plunger is also prepared from the same material; the plunger is required to apply load on specimen by using Universal Testing Machine. Both the die and plunger are heat treated and oil quenched to improve their hardness. The Hardness of the die is 55HRC.It is usually observed in the literature that with the increasing die angle the rate of grain refinement increases, but the energy required for deformation increases subsequently. Also, a few literatures have reported the possible failure of materials by cracking with decreasing angles. The usually preferred die angle is usually varied in between 90° to 135°.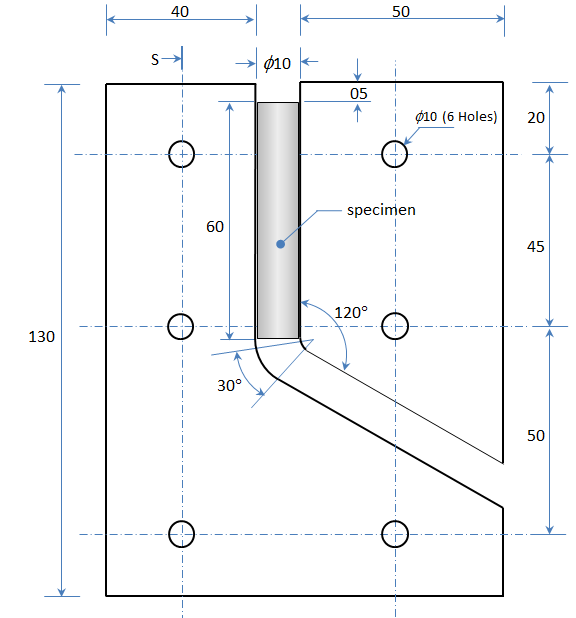 | Figure 1. Schematic sketch of the ECAP die |
2.2. Specimen Preparation and Processing
Commercially pure Aluminium was used for the study having the chemical composition as shown in Table 1. Table 1. Chemical composition of the specimen  |
| |
|
The aluminium billets of 10mm diameter are procured and cut to a length of 60mm. The cut samples doesn’t require any preparations; however, as a precautionary measure in order to remove any burrs or debris it is mildly polished using a water proof Silicon carbide emery paper of P1000 grit size, the surface as well as tip of the specimen are made smooth. It is then cleaned by using acetone. The cleaned sample is then clamped in a split-die and heated to higher temperature in a muffle furnace. The effect of temperature is to enhance the plastic flow of materials. However with the increasing temperature it is observed that the effectiveness of ECAP decreases. Also, there are possibilities of material failure, hence the sample is annealed to a temperature of 250°C for a duration of 1 hour and then subjected to multiple pass ECAP following route B as it is found effective than other routes. The ECAP is carried out using a 60 Ton capacity universal testing machine for up to 2 passes. Also, molybdenum disulphide paste is used as lubricant as it can withstand temperature as high as 300°C; the lubricant is applied on both specimen and as well as die channel to avoid friction.
3. Wear Testing
The Taguchi approach was used in order to design the experimental wear analysis by forming an orthogonal array of experiments. This technique is widely used in order to obtain optimum results by performing minimum number of experiments; thus, saving time, money and resources instead of performing a full factorial designed experiment [7].
3.1. Plan of Experiments
The testing of the as-received and the ECAP specimens for adhesive wear was carried out after suitably selecting the parameters and their levels as shown in Table 2. For a sliding contact wear analysis - the load, speed and sliding duration are the most common parameters chosen as the variables while the other parameters such as contact area and sliding distance are fixed; also, the material and environment conditions are maintained in a controlled manner. The number of ECAP passes was also considered to be a parameter for the evaluation. A L9 orthogonal array (OA) was constructed to organize the selected four parameters and the levels with which these parameters need to be varied systematically in order to complete the experiment with a total of 9 trials. The L9 OA for the adhesive wear analysis is as shown in Table 3.Table 2. Parameters for wear analysis and their levels 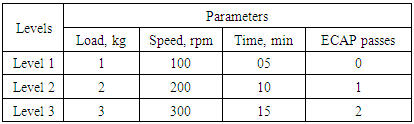 |
| |
|
Table 3. L9 orthogonal array for adhesive wear analysis 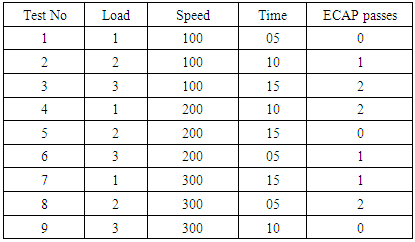 |
| |
|
3.2. Pin-on-Disc Tester
The adhesive wear test was conducted on a DUCOM make Pin-on-Disc tester. The setup details and the specifications of the tester have been presented in our previous work [6]. For testing, the specimen is clamped and held against a rotating steel disc, while the load is applied on the specimen through the cantilever mechanism. The track radius of 100 mm was maintained for all the trials when the remaining parameters were varied according to the order specified in the L9 array. The wear loss was measured as a function of weight loss which was recorded before and after conducting the experiment using a precision weighing scale with an accuracy of 0.01 mg.
4. Results and Discussion
The pure aluminium was held for evaluating the increment in its hardness values and wear resistance upon multiple pass ECAP.
4.1. Effect of ECAP on Hardness
The hardness of the sample was measured using Rockwell hardness tester. It is an indentation test wherein a diamond indenter is used along with the suitable weights applied on the specimen surface for certain duration. The hardness of the CP Aluminium was measured to be 30HRB and after first pass ECAP it was greatly enhanced to about 90 HRB and with another pass only a marginal increment to 98 HRB was observed. The hardness profile of the test specimen is as shown in Figure 2.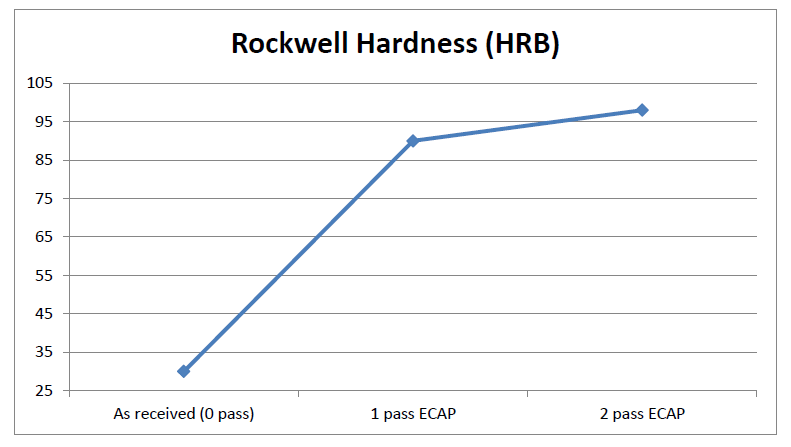 | Figure 2. Hardness profile of the test specimen |
4.2. Statistical Wear Analysis
A statistical analysis of adhesive wear was carried out using the MINITAB14 software. The test conditions along with the output results are presented in Table 4 using L9 orthogonal array.Table 4. L9 orthogonal array with mean wear loss and S/N ratio 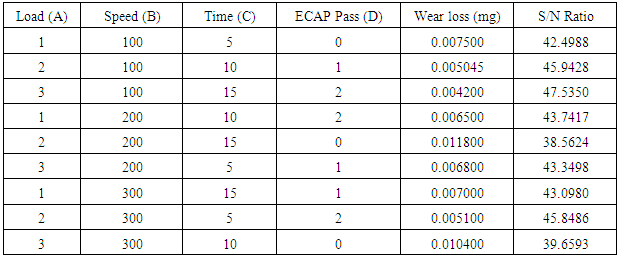 |
| |
|
4.2.1. S/N Ratio Analysis
The wear losses experienced for the different combination of trials were then converted into a logarithmic transformation of mean square deviation called signal-to-noise ratio for analysis of the results. The S/N ratio with a criterion of ‘smaller-the-better’ was calculated using the equation 1 for wear loss as response for all the trials. | (1) |
Where n is the number of experiments, and Yi is the response for ith experiment. The S/N ratios and the response were plotted for each factor against each of its levels with a smaller-the-better condition for wear loss and are as shown in Figure 3. A larger S/N ratio value corresponds to better quality characteristics. Therefore, the optimal level of process parameter is the level of highest S/N ratio [7].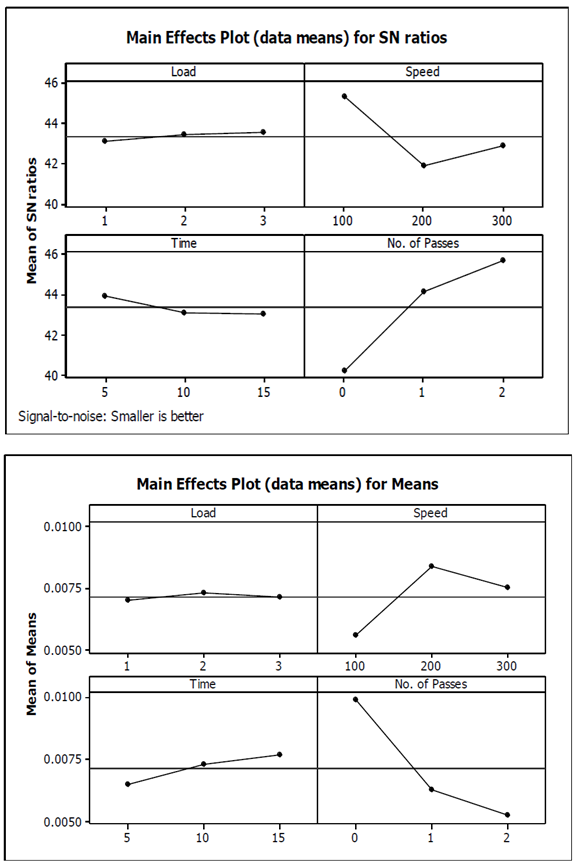 | Figure 3. Main Effect Plot for (a) SN Ratios, (b) Means |
From the Table 5 it is evident that the number of ECAP passes has profound influence on enhancing the wear resistance. And, in order to minimize the wear loss a combination of B1, C1and D3 is preferred. However, the contribution of selected range of loads (factor A) for the present work was not significant towards wear loss.Table 5. Response Table for S/N Ratio (Smaller is better)  |
| |
|
4.2.2. Analysis of Variance (ANOVA)
A statistical analysis of variance in order to evaluate the contribution of each processing parameter towards wear loss was performed. The analysis is carried out for a confidence level of 95% and the sources with a p-value less than 0.05 were considered to have a statistically significant contribution to the performance measures. The percentage contribution of each processing parameter for wear loss is shown in the ANOVA results in Table 6.Table 6. Analysis of Variance for S/N Ratio, using Adjusted SS for Tests 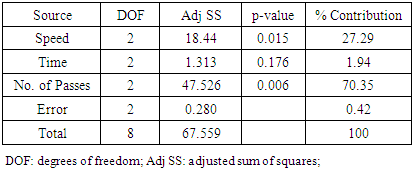 |
| |
|
The ECAP pass (70.35%) has the highest statistical influence on wear of Aluminium followed by the speed (27.29%). The time duration (1.94%) has low statistical significance contribution. The load was not considered for the ANOVA study as it had the least S/N ratio values.
4.2.3. Multiple Linear Regression Model Analysis
In order to establish the correlation between the wear parameters (load, speed, duration and ECAP passes) with the wear loss multiple linear regression model was used.  | (2) |
S = 0.00160489 R-Sq = 79.5%The multiple regression equation derived above correlate the evaluation of the wear of the aluminium with a reasonable degree of approximation, as the calculated error is less than 10% for wear loss. The Table 7 shows that the predicted results are in close comparison with the experimental values. From the regression equation we can predict the intermediate values within the range of the levels. Table 7. Comparison of results 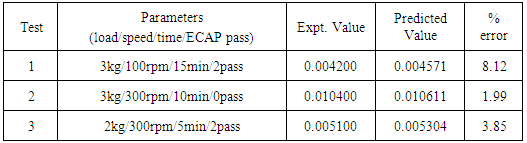 |
| |
|
5. Conclusions
Commercially pure Aluminium can be successfully pressed in a universal testing machine through the ECAP die (having die angle of 120°) for up to 2 passes at 250°C.The following conclusions can be drawn for this present work: The material hardness increases substantially after first pass of ECAP with only a marginal increment after the second pass. For better hardness, ECAP at lower temperature could be tried; however, the energy required for deformation increases substantially with a risk of material failure. In Adhesive wear, the major contributing factor for wear analysis among the selected parameters is the number of passes of ECAP; and also it is found that the wear rate decreases with more number of passes. ANOVA results indicate that the ECAP has the highest statistical influence (70.35%) on wear of aluminium followed by the speed of wear test (27.29%). Multiple linear regression equation has been developed which is in close correlation with the experimental values with observed error less than 10%.
ACKNOWLEDGEMENTS
The authors wish to acknowledge the resources provided by the Research Centre, Department of Mechanical Engineering, St Joseph Engineering College, Mangaluru.
References
[1] | Egemen Avcu, “The influences of ECAP on the dry sliding wear behaviour of AA7075 aluminium alloy,” Tribology International, Vol. 110, pp. 173-184, 2017. |
[2] | M. Furukawa, Z. Horita, M. Nemoto, and T. G. Langdon, “Review Processing of metals by equal-channel angular pressing,” Journal of Materials Science, Vol. 36, pp. 2835-2843, 2001. |
[3] | Yulu, Lei Tang, Guofu, Ying, and Zhimin, "Microstructure and mechanical properties of 7005 aluminum alloy processed by room temperature ECAP and subsequent annealing," Journal of Alloys and Compound., 664, pp.518-529, 2016. |
[4] | Mohamed Ibrahim ABD EL AAL., and M.M. Sadawy, “Influence of ECAP as grain refinement technique on microstructure evolution, mechanical properties and corrosion behavior of pure aluminum,” Transactions of Nonferrous Metals Society of China, Vol. 25 (12), pp. 3865-3876, 2015. |
[5] | Sanusi KO, Makinde OD, Oliver GJ. “Equal channel angular pressing technique for the formation of ultrafine grained structures,” S Afr J Sci. vol. 108 (9/10), http:// dx.doi.org/10.4102/sajs. v108i9/10.212, 2012. |
[6] | Pruthvi Serrao, Ravikanth Prabhu, Chiranth B. P., and Yazid Mohammed, “Application of Taguchi Method to Predict the Abrasive Wear Behavior of CP Titanium,” Journal of Mechanical Engineering and Automation, Vol. 6 (5A), pp. 13-17, 2016. |
[7] | Ganta Venkateswarlu, M Joseph Davidson, and Pulla Sammaiah, “Effect of Friction Stir Processing Process Parameters on the Mechanical Properties of AZ31B Mg Alloy,” Journal of Manufacturing and Industrial Engineering, 1-2(13): 1-5, doi:10.12776/mie.v13i1-2.338, 2014. |