Ravikantha Prabhu1, Prathviraj H.1, Basil John1, Akhil K.1, Chris1, Adithya C.1, Prajwal1, Thirumaleshwara Bhat2
1Department of Mechanical Engineering, St Joseph Engineering College, Mangaluru, India
2Department of Mechanical Engineering, Shri Madhwa Vadiraja Institute of Technology and Management, Udupi, India
Correspondence to: Ravikantha Prabhu, Department of Mechanical Engineering, St Joseph Engineering College, Mangaluru, India.
Email: |  |
Copyright © 2017 Scientific & Academic Publishing. All Rights Reserved.
This work is licensed under the Creative Commons Attribution International License (CC BY).
http://creativecommons.org/licenses/by/4.0/

Abstract
This work mainly focuses on development and evaluation of mechanical and tri-bological behavior of epoxy based composites with different hybrid reinforcement and filler materials. Two specimens combining jute mat and glass mat (J-G-J-G) are fabricated with one containing 5% rice husk charcoal as filler material. Similarly two specimens combining jute, glass and flax mat (G-J-F-G) are fabricated with one containing 5% rice husk charcoal. Composite panels are prepared by hand layup process and specimens are prepared to carry out various tests according to ASTM standard.
Keywords:
Rice husk charcoal, Jute mat, Glass mat, Flax mat, Tensile test, Flexural test, Mechanical properties, Tribological properties
Cite this paper: Ravikantha Prabhu, Prathviraj H., Basil John, Akhil K., Chris, Adithya C., Prajwal, Thirumaleshwara Bhat, Fabrication and Analysis of Jute, Glass and Flax Hybrid Composites Using Rice Husk Charcoal as Filler Material, American Journal of Materials Science, Vol. 7 No. 5, 2017, pp. 135-139. doi: 10.5923/j.materials.20170705.03.
1. Introduction
Natural fiber reinforced composite materials are considered as one of the new class of engineering materials. Among all the natural fiber reinforcing materials, jute appears to be a promising material because it is relatively inexpensive and commercially available in the required form. Glass Fiber Reinforced Polymers (GFRP) is a fiber reinforced polymer made of a plastic matrix reinforced by fine fibers of glass. Fiber glass is a lightweight, strong, and robust material used in different industries due to their excellent properties. Fiber-reinforced composites are being increasingly used as alternatives for conventional materials primarily because of their high specific strength, specific stiffness and tailorable properties. Using natural fillers to reinforce the composite materials offers the following benefits in comparison with mineral fillers strong and rigid, light weight, environmental friendly, economical, renewable and abundant resource.
2. Materials and Methods
2.1. Materials
In this study jute, flax and glass fibers were used as reinforcement material in mat form were purchased from Gogreen Products, Chennai. The epoxy resin Araldite LY556 is used for the processing of the composite in the presence study. Its density is around 1.15 to 1.20g/cc with viscosity between 10000-12000MPa-s at 25°C, and Ardur HY951 hardener were purchased from Renuka Enterprises Bangalore. Rice husk charcoal used as a filler material was purchased from Kanhangad.
2.2. Fabrication of Composites
Composite laminates were prepared with a dimension of 270mm x 270mm x 3mm using hand layup technique. Wax was applied to the metal mould for the easy removal of the composite after curing. Mixture of epoxy resin and hardener in the ratio 10:1 is mixed. A little amount of this mixture put on the material using brush. Then one fibre mat was placed over the poured resin and again resin is poured over it. Similarly two more layers are laid. After this the covering plate was placed over the material and weight is put on the plate. Four composites each of J-G-J-G and G-J-F-G combination with rice husk charcoal (5%) and without rice husk charcoal were prepared. Jute fabrics and E-Glass fibers are cut as per the mould size and placed at the surface of mould. Epoxy in liquid form is mixed thoroughly in suitable proportion with a prescribed hardener (curing agent) and poured onto the surface of mat placed on the mould. The process is repeated for each layer of epoxy and mat, till the required layers are stacked.
2.3. Preparation of Sample for Testing
Once the composite material is prepared, next important step is to cut them into test samples of sizes according to ASTM standards. Cutting was carried out using high speed cutter and 24TPI hacksaw blade. Five samples of each type were cut and prepared for the test. The list of ASTM standards used is mentioned in Table 1.Table 1. ASTM standards used 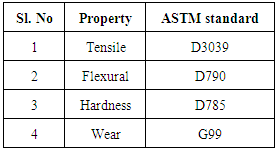 |
| |
|
2.4. Mechanical Characterization for the Composites
2.4.1. Hardness
Hardness of a material is defined as the resistance to deformation. The hardness of the different composite specimens was determined on a Rockwell Hardness testing machine using M-scale.
2.4.2. Tensile Test
Tensile tests were conducted using universal testing machine with across head speed of 2mm/min. Tensile test samples were cut as per ASTM D3039 test procedure. Tests were carried out at room temperature and each test was performed until tensile failure occurred.
2.4.3. Flexural Strength Test
Flexural analysis was carried out at room temperature through three-point bend testing as specified in ASTM D790, using universal testing machine. The speed of the crosshead was 1.28 mm/min.
2.5. Wear Testing Details
The wear properties of different samples were tested on the wear and friction monitor DUCOM TR-201C commonly known as Pin-on-Disk machine. The samples were cut according to the ASTM standard G99. The test samples were then glued to the mild steel pins of 10mm square cross-section and 40mm length. The track radius of 40mm was set, the specimen is held stationary and the disk is rotated while a normal force is applied through a lever mechanism. A series of tests were conducted with three different sliding velocities of 2 and 2.5 m/s under three normal loading 20N, 40N and 60N at different speed. The material loss from the composite surface is measured using a precision electronic balance with accuracy ±0.1mg.
3. Results and Discussion
This chapter presents the mechanical and wear characterization of the class of polymer matrix composite developed for the present investigation. The properties discussed include hardness, abrasive wear loss, dry sliding wear loss, tensile and flexural tests of composites.
3.1. Mechanical Properties of Composites
Development of composites made from natural fibers with increased strength, stiffness and durability requires necessary understanding of mechanical behavior. A good interfacial bond is required for effective stress transfer from the matrix to the fiber by which maximum utilization of the fiber strength in the composite can be obtained. This leads to developing an alternative material to wood. The analysis of mechanical properties of composites is important for understanding the behaviour of composite materials. It is a well-known fact that the mechanical properties of fiber-reinforced composite materials. It is a well-known fact that the mechanical properties of fiber-reinforced composites depend on the nature of matrix material, the distribution and orientation of the reinforcing fibers and the nature of the fiber matrix interfaces.
3.1.1. Hardness Test
Hardness Test was conducted using Rockwell Hardness tester under 100kgf load with ¼ inch ball intender and scale M. In Hardness test, a specimen of 20mm x 20mm x3mm dimension is prepared. The experimental results show that maximum hardness is for J-G-J-G (5% husk). Hardness value for J-G-J-G (5% husk) is more that of J-G-J-G. Similarly G-J-F-G (5% husk) shows more hardness value compared to G-J-F-G.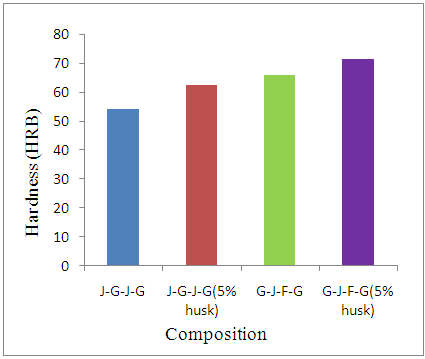 | Figure 1. Comparison between the hardness strength of different composite specimens |
3.1.2. Tensile Strength of Composites
Tensile tests were conducted using Zwick Roell Z020 universal testing machine for the fiber reinforced polymer matrix composite. In tensile testing, a specimen of 250mm x 25mm x 3mm dimension is prepared. Comparing the ultimate strength of the composites, the maximum was shown by J-G-J-G. Adding rice husk charcoal decreased strength of J-G-J-G and increased strength of G-J-F-G.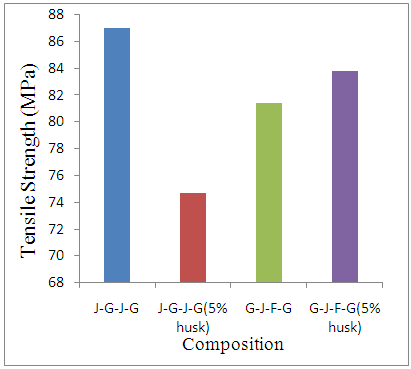 | Figure 2. Comparison between the tensile strength of different composite specimens |
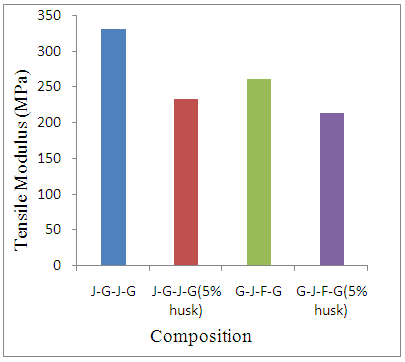 | Figure 3. Comparison between the tensile modulus of different composite specimens |
3.1.3. Flexural Strength of Composites
Flexural tests were conducted using Zwick Roell Z020 universal testing machine for the fiber reinforced polymer matrix composite. In flexural testing, three-point bending was performed at room temperature on a specimen of 127mm x 12.7mm x 3mm dimension. Comparing the ultimate flexural strength of the composites, the maximum was shown by G-J-F-G from Figure 4. From the graph it is evident that staking sequence is having significant effect on flexural strength and flexural modulus of the composite material. Change of stacking sequence from J-G-J-G to G-J-F-G resulted in improvement in significant improvement.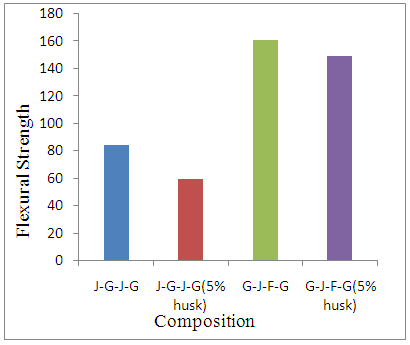 | Figure 4. Comparison between the flexural strength of different composite specimens |
Flexural modulus is found to be maximum for G-J-F-G. Addition of rice husk charcoal decreased the flexural modulus.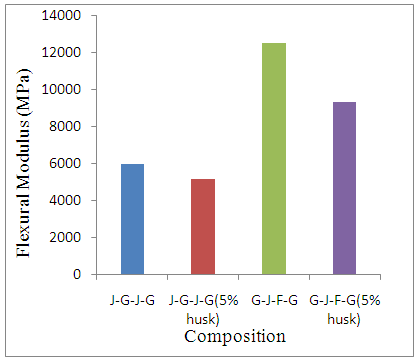 | Figure 5. Comparison between the flexural modulus of different composite specimens |
3.2. Wear Property
3.2.1. Abrasive Wear Test
Abrasive wear occurs when a hard rough surface slides across a softer surface. ASTM International (formerly American Society for Testing and Materials) defines it as the loss of material due to hard particles or hard protuberances that are forced against and move along the solid surface. In Wear testing, a specimen of 10mm x10mm x 3mm dimension is prepared.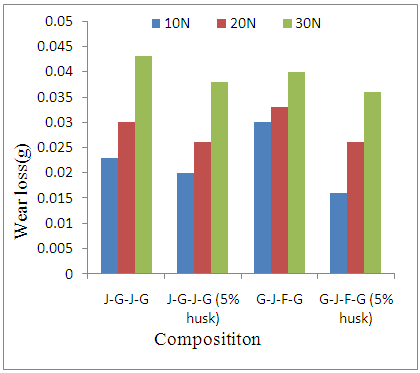 | Figure 6. Comparison between the wear losses of different composite specimens (Abrasive wear test) |
The grid size of abrasive paper used is 400µ. 1) The wear loss is found to be more for J-G-J-G than J-G-J-G (5% husk). 2) The wear loss is found to be more for G-J-F-G than G-J-F-G (5% husk).
3.2.2. Dry Sliding Wear Property
The effect of war loss for different composites at a constant load of 60N and 1000m sliding distance for varying sliding velocities (i.e. 2, 2.5m/s) is as shown in the Figure 7.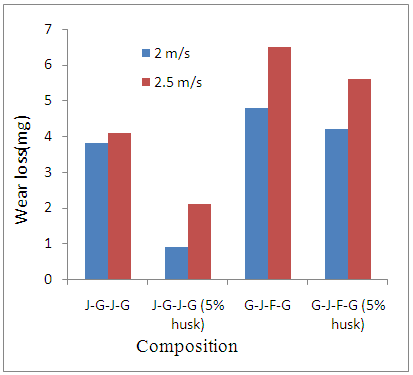 | Figure 7. Comparison between the wear losses of different composite specimens (Load 60N, 1000m sliding distance) |
The experimental results showed that the wear loss was maximum for G-J-F-G.J-G-J-G and G-J-F-G with rice husk charcoal (5%) is found to have more wear resistance compared to specimens without rice husk charcoal.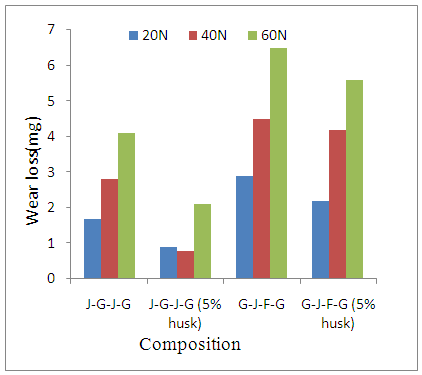 | Figure 8. Comparison between the wear losses of different composite specimens (Sliding velocity 2.5m/s, 1000m sliding distance) |
4. Conclusions
Conclusions based on present projectThe various composites were prepared by hand layup process. The mechanical properties of the composites were examined for different conditions of load, sliding distance and for grid size of abrasive paper. Based on the results the following conclusions were drawn.
4.1. Wear Properties
1. Abrasive wear test: The grid size of abrasive paper used is 400µ. The wear loss is found to be maximum for J-G-J-G whereas minimum wear loss was found in G-J-F-G (5% husk). 2. Dry sliding test: The wear resistance is more for specimens added with rice husk charcoal.
4.2. Tensile and Flexural Properties
Comparing the Ultimate Tensile Strength of Composites, J-G-J-G shows maximum value and decreases with the addition of rice husk charcoal. The tensile strength of G-J-F-G increases with the addition of rice husk charcoal. It is due to the stacking sequence of composites.1. Tensile modulus is found to be maximum for J-G-J-G. Tensile modulus decreases with addition of rice husk charcoal.2. Flexural strength is found to be maximum for G-J-F-G. As the rice husk charcoal is added the flexural strength decreases.3. Flexural modulus is found to be maximum for G-J-F-G. As the rice husk charcoal is added the flexural modulus decreases.
4.3. Hardness
Hardness value for J-G-J-G (5% husk) is more that of J-G-J-G. Similarly G-J-F-G (5% husk) shows more hardness value compared to G-J-F-G. Hardness of composite material increases with the addition of rice husk charcoal.
ACKNOWLEDGEMENTS
The authors extend heartfelt thanks and appreciations to Director and Principal of St Joseph Engineering College, Mangaluru for their continuous support and encouragement during research work.
References
[1] | Mishra S, Mohanty A.K, Drzal, L.T., Misra M, Parija S, Nayak, S.K. and Tripathy, S.S. (2003) “Studies on Mechanical Performance of Biofiber/Glass Reinforced Polyester Hybrid Composites”. Journal of Composites Science and Technology. |
[2] | Khin Aye Tue and Moe Moe Thwe, “Recycle of Plastic Waste and Agricultural Waste” Energy Research Journal, vol. 4, no. 1, pp. 24-29, 2013. |
[3] | G.Meenambika Bai, H. Raghavendra Rao, Mechanical and Chemical Properties of Bamboo/Glass Fibers Reinforced Polyester Hybrid Composites, Industrial Engineering Letters, Vol.4, No.4, 2014. |
[4] | Kolli Balasivarama Reddy S, Abburi Lakshmankumar, Effect of filler material in bamboo fiber reinforced polymer composites, Journal of Chemical and Pharmaceutical Sciences, Vol. 9 Issue-4, October - December 2016. |
[5] | Vikram. S Yendhe, Nilesh B. Landge, Manoj B. Thorat, Development and Investigation of Mechanical Behaviour of Bamboo Based Fiber Composites, International Journal for Research in Applied Science & Engineering Technology, Vol. 3, Issue-6, June 2015. |
[6] | Raghavendra Yadav Eagala, Allaka Gopichand, Gujjala Raghavendra, Sardar Ali S, Abrasive Wear Behaviour of Bamboo-Glass Fiber Reinforced Epoxy Composites Using Taguchi Approach, International Journal of Advances in Engineering & Technology, Vol. 5, Issue-1, pp: 399-405, November 2012. |
[7] | Dheeraj Kumar, Characterization of Tensile Properties of Treated Bamboo Natural Fiber Polymer Composite, International Journal of Mechanical Engineering and Technology, Vol. 5, Issue-4, pp: 110-115, April 2014. |
[8] | Hemalata Jena, Arun Kumar Pradhan, Mihir Kumar Pandit, Studies on Water Absorption Behaviour of Bamboo-Epoxy Composite filled with Cenosphere, Vol. 33, Issue-11, April 2014. |
[9] | H. Raghavendra Rao, Y. Indraja, G. Meenambika Bai, Flexural Properties and Sem Analysis Of Bamboo And Glass Fiber Reinforced Epoxy Hybrid Composites, IOSR Journal of Mechanical and Civil Engineering, Vol. 11, Issue-2, pp: 39-42, April 2014. |
[10] | B. Aldousiri, A. Shalwan and C. W. Chin “Mechanical Properties of Palm Fibre Reinforced Recycled HDPE”, Advances in Materials Science and Engineering, Volume 2013, Article ID 508179, 7 pages, 2013. |