Ravikantha Prabhu1, Frazer1, Akshay1, Colaco Joel1, Denzil1, Ovin1, Thirumaleshwara Bhat2
1Department of Mechanical Engineering, St Joseph Engineering College, Mangaluru, India
2Department of Mechanical Engineering, Shri Madhwa Vadiraja Institute of Technology and Management, Udupi, India
Correspondence to: Ravikantha Prabhu, Department of Mechanical Engineering, St Joseph Engineering College, Mangaluru, India.
Email: |  |
Copyright © 2017 Scientific & Academic Publishing. All Rights Reserved.
This work is licensed under the Creative Commons Attribution International License (CC BY).
http://creativecommons.org/licenses/by/4.0/

Abstract
This work is mainly focused on development and evaluation of physical, mechanical, tribological and hydrophilic behavior of epoxy based composites filled with different percentage of Bamboo Fiber (BF) and Coconut Powder (CP). Composite panels were made by hand lay-up process and properties are tested as per ASTM standards. Hardness of the composites was found to decrease with the increase in percentage of BF and CP. Tensile test revealed that the composite 20% BF has the maximum strength and it was found to increase as we increase the percentage of BF. Similarly, for CP 20% showed the highest strength. Water absorption test reveal that, the minimum water absorption was observed for the composite of 10% CP. It is also found that with the increase in BF and CP, the water absorption rate increases. Abrasive wear test revealed that, composite BF 20% has the minimum wear loss. Dry sliding wear test reveals that weight loss increases with increase in sliding distance, but wear rate differs for different specimen. The wear loss for 20% BF was found to be smallest among other wear loss and 30% CP has the highest wear rate among another specimen.
Keywords:
Bamboo fibers, Coconut Powder, Epoxy Resin, Water absorbtion test, Tensile test, Mechanical properties, Tribological properties
Cite this paper: Ravikantha Prabhu, Frazer, Akshay, Colaco Joel, Denzil, Ovin, Thirumaleshwara Bhat, Development and Characterization of Low Cost Bamboo Fibre Reinforced Polymer Composites, American Journal of Materials Science, Vol. 7 No. 5, 2017, pp. 130-134. doi: 10.5923/j.materials.20170705.02.
1. Introduction
Polymer resins are one of the most important classes of thermosetting polymers which are widely used as matrices for fiber-reinforced composite materials and as structural adhesives. They are amorphous, highly cross-linked polymers and this structure results in these materials possessing various desirable properties such as high tensile strength and modulus, uncomplicated processing, good thermal and chemical resistance, and dimensional stability. However, it also leads to low toughness and poor crack resistance, which should be upgraded before they can be considered for many end-use applications, one of the most successful methods of improving the toughness of polymers. Resin is to incorporate a second phase of dispersed rubbery particles into the cross-linked polymer. Using natural fillers to reinforce the composite materials offers the following benefits in comparison with mineral fillers strong and rigid, light weight, environmental friendly, economical, renewable and abundant resource. On the other hand, the disadvantages of the materials are degradation by moisture, poor surface adhesion to hydrophobic polymers, non-uniform filler sizes, not suitable for high temperature application, susceptibility to fungal and insect attack various works on the application of natural fillers and fibers in composites like pineapple, sisal, coconut coir, jute, palm, cotton, rice husk, bamboo, and wood as the reinforcements in composites have been reported in the literature. Sisal fiber is fairly coarse and inflexible. It has good strength, durability, ability to stretch, affinity for certain dye stuffs, and resistance to deterioration in seawater. Sisal ropes and twines are widely used for marine, agricultural, shipping, and general industrial use.
2. Literature Review
G. Meenambika Bai, H. Raghavendra Rao [1], studied the chemical resistance of Bamboo/Glass reinforced polyester hybrid composites to acetic acid, Nitric acid, Hydrochloric acid, Sodium hydroxide, Sodium carbonate, Benzene, Toluene, carbon tetrachloride and water. The flexural properties of these composites were also studied. The effect of alkali treatment of bamboo fibers on these properties was studied. It was observed that the flexural properties of the hybrid composites increase with glass fiber content. These properties found to be higher when alkali treated bamboo fibers were used in hybrid composites. The hybrid fiber composites showed better resistance to the chemicals mentioned above. Kolli Balasivarama Reddy S, Abburi Lakshmankumar [2] The objective of this research was to investigate the feasibility of using bamboo fiber mat with different filler like Graphene, Alumina, Silicon oxide materials as reinforcement for fiber reinforced composites (FRCs). It was observed that Graphene reinforced laminates has better mechanical properties over Alumina and Silicon oxide. Water repellent properties are better with silicon oxide reinforced laminates. In his results, it was found that Graphene reinforced laminates have the maximum mechanical strength of 12.06KN compared with Alumina and Silicon oxide. Laminate without filler content shows high tensile bearing capabilities. Water repellent properties of silicon oxide give it the high resistance of 0.28% to water hence blending of different materials can lead to even better all-round performance.Mr. Vikram. S Yendhe, Mr. Nilesh B. Landge, Mr. Manoj B. Thorat [3]. In their study, Short bamboo fiber reinforced epoxy based polymer composite was fabricated and its mechanical behaviour was studied. It has been explored that the mechanical properties of the composites such as tensile strength, flexural strength, impact strength and hardness are highly influenced by the size of the fibers used. Excess of fibers in composite materials deteriorate the mechanical properties of the composite because of lack of proper bonding between the matrix and fiber around their interface. This causes the disruption in transfer of load to the bonding fibers.Raghavendra Yadav Eagala, Allaka Gopichand, Gujjala Raghavendra, Sardar Ali S [4]. Experiments were carried out to study the Abrasive wear behaviour of different composites of bamboo and glass fiber reinforced hybrid composite with silica sand abrasive paper. The composite with 20% reinforced gives the best wear resistance when compared to the density is more for the composite prepared with the 10%. The hardness is more for the composites prepared with the 20% reinforced composites. The wear increases with increasing in load and the maximum wear occurs at 15 N. Dheeraj Kumar [5]. This research paper shows the practical observation which includes characterization of tensile properties of potential bamboo fibre. It consists calculation of tensile strength (MPa) of treated bamboo fibre with sodium hydroxide (NaOH). The fabrication of various bamboo fibre samples were made by hand lay-up technique. Study shows that the tensile strength of bamboo-epoxy composite increases to the certain level of fibre loading and then starts decreasing on further fibre loading. The maximum value of tensile strength is obtained at 25wt% of fibre loading.H. Raghavendra Rao, Y. Indraja, G. Meenambika Bai [6]. In this study, The Flexural properties and Scanning Electron Microscope analysis of Bamboo/glass fibers Reinforced Epoxy Hybrid composites were studied. The effect of alkali treatment of the bamboo fibers on these properties was also studied. In this case also the hybrid composites are found to have good Flexural properties. In the case of maximum strength, the values vary between 60 to 213 MPa. The Flexural strength of these composites are found to be enhanced when alkali treated bamboo fibers were used in the hybrid composites. The hybrid composites with alkali treated bamboo fibers were found to possess higher flexural properties.
3. Materials and Methods
3.1. Materials
Epoxy resins are the major composite material for low-temperature application [usually under 2000F (93°C)] and generally provide outstanding chemical resistance, superior adhesion to fibers and superior dimensional stability. Epoxy can be formulated to a wide range of viscosities for different fabrication processes and cure schedules. They are free from void forming volatiles, have long shelf lives and provide relatively low cure shrinkage. Araldite LY556 is the epoxy resin that was used for the processing of the composite in the presence study. Its density is around 1.15 to 1.20g/cc with viscosity between 10000-12000MPa-s at 25°C. The hardener used for the LY556 epoxy resin was Ardur HY951 with a boiling point greater than 200°C and a density of 1g/cc at 20°C. The epoxy resin and hardener were purchased from a local supplier in Bangalore.
3.2. Fabrication of Composites
The composites with different percentage of bamboo fibers and coconut powder were fabricated by hand lay-up process. The essential steps in the process involve chemical treatment of fibre, hand layup, rolling and curing. The setup involved two plates of mild steel each having a weight of around 10kg each where one acted as a base plate and another as a plate to cover the plate and aluminium mould was prepared according to the ASTM standard for the preparation of the tensile test specimen. In bamboo fibers they were soaked in NaOH (sodium hydroxide) for a day in order to remove the dirt present in the bamboo. The NaOH soaked fibers were treated with distilled water and were kept for drying. Once it was dried it was ready to be used for the preparation of specimen. While preparation of the specimen the aluminium mould was cleaned properly and cello-tapes were applied to it so that the specimen could be easily removed. The mould was also applied with wilon wax for the easy removal of the specimen. The wax was also applied on the polythene plastic which was placed below and above the aluminium mould since it was not to stick to the base plate (i.e. mild steel). In preparing bamboo fiber composites of 10%, 20% specimen, the epoxy was taken in a cup keeping in mind the ratio of epoxy and hardener to be 10:1. Then the bamboo fibers of 10% (20%) were mixed with epoxy and were stirred well so that the epoxy was totally mixed with bamboo fibers. Once the mixing was done then the hardener was mixed and stirred for 2-3 minutes after which the mixture was poured in the aluminium mould and then it was equally distributed by a roller and the mould for closed and kept for a day. In preparation of specimen with coconut powder where the powder of different grain size was separated by Sieve Shaker machine and for the study 400micron was used. The preparation was similar to bamboo fiber preparation where in here coconut powder (10%, 20%, 30%) was mixed with epoxy so that it completely mixed and then hardener was poured and stirred and thus the mixture was poured into the mould. Similar procedure was followed for hybrid composite where both bamboo fiber and coconut powder was mixed simultaneously and the specimen was prepared.
3.3. Mechanical Characterization of Composites
3.3.1. Hardness
Hardness of a material is defined as the resistance to deformation, particularly permanent deformation, indentation or scratching. The hardness of the different composite specimens was determined on a Rockwell Hardness testing machine using M-scale.
3.3.2. Tensile Test
Tensile tests were conducted using universal testing machine with across head speed of 1mm/min. In each case, five samples were tested and average value tabulated. Tensile test samples were cut as per ASTM D3039 test procedure. Tests were carried out at room temperature and each test was performed until tensile failure occurred.
3.4. Wear Testing Details
The wear properties of different samples were tested on the wear and friction monitor DUCOM TR-201C commonly known as Pin-on-Disk machine. | Figure 1. Wear Testing (Pin-on-Disc) setup |
3.4.1. Abrasive Wear Test
The samples were cut according to the ASTM standard G99. The test samples were then glued to the mild steel pins of 10mm square cross-section and 40mm length. The track radius of 30mm was set and the disc speed was adjusted to 200 rpm. The sliding speed was kept constant at 0.6283m/sec with sliding distance of 40m, 50m, and 60m One of the pins to which the specimen was glued, was held in the arm of the wear testing machine and the specimen was made to slide on an abrasive Silicon Carbide paper of 400 grit size, which had been cut to the required size and firmly glued to the rotating disc of the wear testing machine. Testing was carried out for three different loads viz.10, 20 and 30N. The same procedure was adopted for the rest of the samples under the same test conditions. Every time the abrasive paper on the disc was changed.
3.4.2. Dry Sliding Wear Test
The dry wear test samples were then glued to the mild steel pins of 10mm square cross-section and 50mm length. The track radius of 40mm was set and the disc speed was adjusted to different sliding speeds which had a sliding distance of 1000m. One of the pins to which the specimen was glued, was held in the arm of the wear testing machine and the specimen was made to slide on the rotating disc of the wear testing machine. Testing was carried out for loads of 20N, 40N, 60N. The same procedure was adopted for the rest of the samples under the same test conditions.
4. Results and Discussion
4.1. Tensile Test
Tensile test was conducted using universal testing machine for various percentage of bamboo fibers (10%, 20%) and coconut powder (10%, 20%, 30%) and even for the hybrid composites.The tensile strength for epoxy and hardener combination shows strength of 21.15MPa. The strength for 10% BF was found to be 45.98MPa and 20% BF increased to 62.31MPa i.e. there is increase in strength with increase in percentage of BF. As in case of coconut powder 20% CP shows the maximum strength of 16.44MPa among other two percentages. The strength decreased with 30% CP because the powder has no tensile strentgth as compared to that of BF.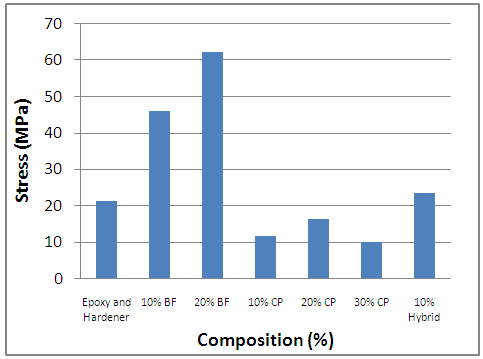 | Figure 2. Comparison of tensile strength with different compositions |
4.2. Abrasive Wear Test
For different percentage of composites the wear loss was found by abrasive wear test using 400 grid size emery paper with a constant velocity of 200rpm and 20N load for varying sliding distance (i.e. 40, 50, 60m) as shown in the figure below.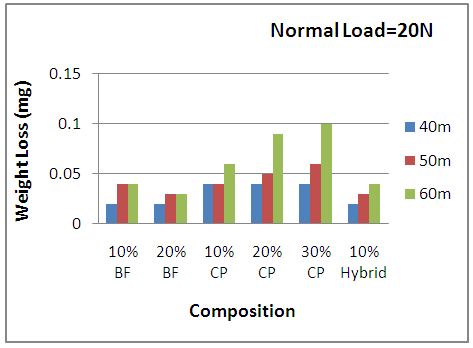 | Figure 3. Comparison between wear losses of different specimen (20N) |
At a normal load of 20N, we can see that weight loss increases with increase in sliding distance. The wear rate decreases with the increase in percentage of bamboo fiber because the grits of the sand paper act as a solid lubricant. The wear rate in coconut powder increases with increase in percentage of coconut powder.
4.3. Dry Sliding Wear Test
For different percentage of composites, the wear loss was found by dry wear test by keeping a constant sliding distance of 1000m and 1.5m/s velocity for varying loads (20, 40, 60N) as shown in the Fig. below.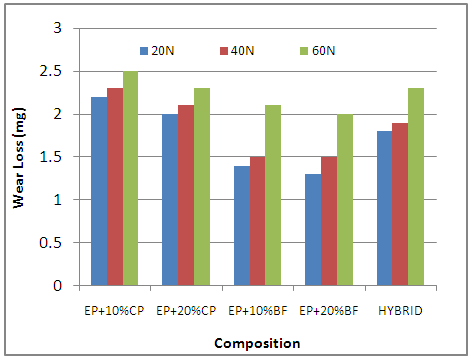 | Figure 4. Weight loss vs load for constant velocity of 1.5m/s |
In the above Fig: 5.9 the weight loss against load, the values are plotted for various test specimens used. We can find that, weight loss increases with the increase in normal load, but wear rate decreases with increase in percentage of the filler material.
4.4. Water Absorption Test
The percentage of water absorbtion in the composites was calculated by weight difference between the samples immersed in water and the dry samples using the following equation. | (1) |
Where, Mt is the moisture content in the specimen, Wt is the weight of the specimen at the immersion time and Wo is the weight of the specimen before the water absorbtion test.The variation of water absorbtion rate is shown in figure 5. For 10% BF, it shows that the absorbtion was high for first five days after which the absorbtion was negligible. For 20% it shows that water absorbtion is high for first five days and thereafter negligible. We can also see that 20% BF has more water abrsorbtion rate than 10%BF because BF are water loving in nature and therefore there is increase in absorbtion rate. For hybrid 10% water absorbtion was high for first five days and thereafter small increase in absorbtion till seventh day.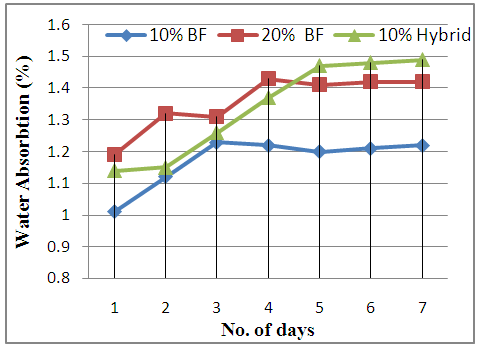 | Figure 5. Comparison of water absorbtion of different composites |
4.5. Hardness Test
The test was conducted on various specimens and it was found that the epoxy and hardener is the hardest among all. In bamboo fiber composites, hardness increases with increase in the fiber content and the 20% BF has hardness of 72.33RHN. For coconut powder the maximum hardness was found for 10% CP and is found that it decreases with increase in percentages of the CP.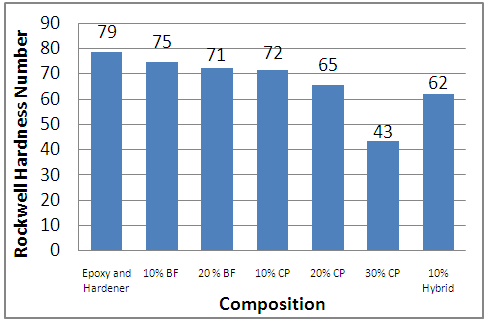 | Figure 6. Comparison of hardness with different composite specimen |
5. Conclusions
Through the current study, it can be concluded that theThe tensile strength for 20%BF filled with epoxy found to give the best result of 63.31MPa. When the percentage of 10% was used, it was found that the strength was 45.98MPa which was less than the 20%BF. The tensile strength of BF specimen was found to increase with increase in percentage. Study for CP shows that 20%CP has a strength of 16.44MPa. Likewise, for 10%CP was found to be 11.85MPa and 30% was found to be 10.30MPa. The strength in CP increases from 10% to 20% than decreases to 30%CP.From the wear test, it is clear that weight loss increases with increase in sliding distance, but wear rate differs for different specimen. The wear rate for 20%BF was found to be smallest among other wear rate and 30%CP has the highest wear rate among another specimen. The wear rate for 10% hybrid was found to in between 20%BF and 30%CP.The test for hardness shows that epoxy hardener specimen had the highest hardness of 78.5RHN compared to another specimen. The test for BF shows that with increase in percentage of fiber decreases the hardness number where 20%BF has a hardness of 72.33RHN. The test for CP shows that with increase in filler content, there was decrease in hardness of specimen where 30%CP has a hardness of 43.33RHN. The 10%hybrid has a hardness of 62RHN.While for the water absorption, it appears that, as the filler loading increased, the composites tend to absorb more water which attributed to the ability of BF and CP fillers to absorb water and also it is clear that initial absorbtion is high and after the time interval of five days absorbtion is almost stable.
ACKNOWLEDGEMENTS
The authors extend heartfelt thanks and appreciations to Director and Principal of St Joseph Engineering College, Mangaluru for their continuous support and encouragement during research work.
References
[1] | G. Meenambika Bai, H. Raghavendra Rao, Mechanical and Chemical Properties of Bamboo/Glass Fibers Reinforced Polyester Hybrid Composites, Industrial Engineering Letters, Vol.4, No.4, 2014. |
[2] | Kolli Balasivarama Reddy S, Abburi Lakshmankumar, Effect of filler material in bamboo fiber reinforced polymer composites, Journal of Chemical and Pharmaceutical Sciences, Vol. 9 Issue-4, October - December 2016. |
[3] | Mr. Vikram. S Yendhe, Mr. Nilesh B. Landge, Mr. Manoj B. Thorat, Development and Investigation of Mechanical Behaviour of Bamboo Based Fiber Composites, International Journal for Research in Applied Science & Engineering Technology, Vol. 3, Issue-6, June 2015. |
[4] | Raghavendra Yadav Eagala, Allaka Gopichand, Gujjala Raghavendra, Sardar Ali S, Abrasive Wear Behaviour of Bamboo-Glass Fiber Reinforced Epoxy Composites Using Taguchi Approach, International Journal of Advances in Engineering & Technology, Vol. 5, Issue-1, pp: 399-405, November 2012. |
[5] | Dheeraj Kumar, Characterization of Tensile Properties of Treated Bamboo Natural Fiber Polymer Composite, International Journal of Mechanical Engineering and Technology, Vol. 5, Issue-4, pp: 110-115, April 2014. |
[6] | H. Raghavendra Rao, Y. Indraja, G. Meenambika Bai, Flexural Properties and Sem Analysis of Bamboo and Glass Fiber Reinforced Epoxy Hybrid Composites, IOSR Journal of Mechanical and Civil Engineering, Vol. 11, Issue-2, pp: 39-42, April 2014. |