Suraj A. Maidarkar1, Kotgi Kotresh1, V. R. Kabadi1, Shaila Hosmani2
1Department of Mechanical Engineering, Nitte Meenakshi Institute of Technology, Yelahanka, Bangalore, India
2Department of Mechanical Engineering, R.R Institute of Technology Chickkabanavar, Bangalore, India
Correspondence to: Suraj A. Maidarkar, Department of Mechanical Engineering, Nitte Meenakshi Institute of Technology, Yelahanka, Bangalore, India.
Email: |  |
Copyright © 2017 Scientific & Academic Publishing. All Rights Reserved.
This work is licensed under the Creative Commons Attribution International License (CC BY).
http://creativecommons.org/licenses/by/4.0/

Abstract
The ever increasing demand from aerospace industries and automotive industries to manufacture components which are lighter and stronger than conventional steel has prompted the significant usage of aluminium alloys. This research work involves the investigation of mechanical properties in aluminium alloys before and after cold work forged. Major alloying elements used in the aluminium alloy are manganese and silicon. The aluminium alloy ingots are prepared through gravity casting. After the ingots are air cooled to room temperature, they are work hardened using cold forging method. The cold forged aluminium alloys are then subjected to tensile tests, wear tests, hardness tests and microstructure analysis using optical Scanning Electron Microscope (SEM). The material properties achieved are compared with the alloys properties that have not been subjected to work hardening. The expected outcome is to achieve a work hardened aluminium alloy that exhibits excellent wear resistance property which can be best suited for numerous industrial manufacturing requirements. It is observed that broken Mn after forging has shown better wear resistance property having toughness property.
Keywords:
Aluminium alloys, Cold forging, Hardness, Microstructure, Wear resistance
Cite this paper: Suraj A. Maidarkar, Kotgi Kotresh, V. R. Kabadi, Shaila Hosmani, Effect of Manganese on Wear Behavior of Al-Si-Mn Alloy, American Journal of Materials Science, Vol. 7 No. 5, 2017, pp. 125-129. doi: 10.5923/j.materials.20170705.01.
1. Introduction
Aluminium alloys are used for manufacturing since pure aluminium alone (1xxx series) tends to have weaker material properties and are non hardenable. Aluminium alloys occur as two types namely, wrought aluminium and cast aluminium. Cast aluminium alloys can be easily heat treated and work hardened unlike wrought aluminium. The cast aluminium is subdivided into heat treatable and non heat treatable alloys. In this research work, castable and heat treatable aluminium alloys are being used. There are eight alloying groups for aluminium out of which only three groups are of interest to this research work. They are Aluminium-Manganese (3xxxeries), Aluminium-Silicon. (4xxxseries) and Aluminium-Magnesium (5xxx series). When subjected to cold working, different alloying elements exhibit different attributes on the alloy property. The strength of 3xxx series aluminium is moderate However, they have good formability characteristics and can be easily work hardened and also used for anodizing and welding. On the other hand, the 4xxx series aluminium comprises of silicon which is primarily used for its good casting properties. This is because silicon has the capability to reduce the melting point of aluminium without introducing brittleness into the alloy. As in the case of 5xxx series alloy, magnesium is seen to be the primary alloying element. Such alloys have higher strength when compared to that of 3xxx series or 4xxx series alloy. They also have an excellent corrosion resistance property because of which they are preferred in numerous marine industry and naval applications. Because of their high strength, they are most commonly employed in the production of pressure vessels and tanks that can withstand very high pressures. The overall applications of aluminium alloys prove that it is one of the most versatile materials which are highly sought after. Sometimes basic standards of aluminium might not meet the requirement in an industry level environment. Therefore aluminium is alloyed with multiple alloying elements together to obtain materials with properties that meet the requirement of purpose. In this research paper, three different alloying elements are used to obtain three unique alloys whose mechanical properties are investigated in detail. The same materials are subjected to work hardening and investigation of mechanical properties is also conducted for the same. A critical comparison of mechanical properties such as material hardness, tensile strength and wear resistance is performed between the work hardened and non work hardened aluminium alloys. The microstructure is also viewed critically with the help of a Scanning Electron Microscope (SEM) which will provide a better understanding of influence of work hardening on the dendrite formation, distribution and orientation. After the comparison of multiple samples of aluminium alloys are performed, a best work hardened aluminium alloy composition with excellent material properties is suggested which can be best suited for innumerable cross-domain applications in the manufacturing industry. Table 1. Yield Stress, Ultimate Tensile Stress and Hardness Values of Alloys  |
| |
|
2. Experimental Procedure
A prefixed methodology that includes the systematic conduction of various activities of the research work is shown in the form of a hierarchy tree in figure 1. It signifies the activities ranging from fabrication of specimen to discussion of results.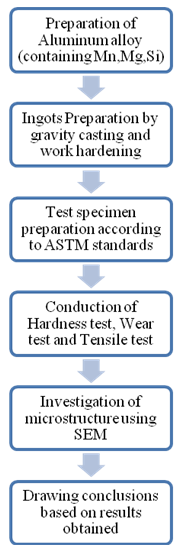 | Figure 1. Research Methodology Heirarchy |
To understand the wear behavior of the Al alloy, pin on disc (DUCOM TR-20LE) wear testing machine was used. All the specimens were run for the sliding distance of 5000 meters. Because wear rate is either height loss or volume loss per unit sliding distance hence, sliding distance was taken same for all the wear tests. Two sliding speeds were considered for the research work. One is low sliding speed of 0.5 m/s and another is 3 m/s. Track distance of 130 mm is selected for the wear test. To cover the same sliding distance of 5000 meters for both the sliding speeds, time is estimated as shown in table-2. During wear test the height loss in µm is noted with the time, also frictional force is noted along with the wear tests. To estimate the wear rate, the slope of the wear line is considered i.e., µm/min. later this was converted into µm/m Three alloys of AlSiMn were selected for the research work varying in percentage of Mn in 3,6 and 8%. Each specimen is forged to break the Mn particles. Totally 6 specimens were selected such as three as received and three forged specimens. Each specimen is wear tested under the same load of 0.5 kg and 0.5 and 3 m/s. totally 12 wear tests were conducted for the research work. Hardness of each specimen is measured. It is understood that hardness of the as received specimen is increased with the Mn% whereas almost the same is observed in forged specimens. In forged specimens broken Mn is embedded in softer matrix of aluminium. 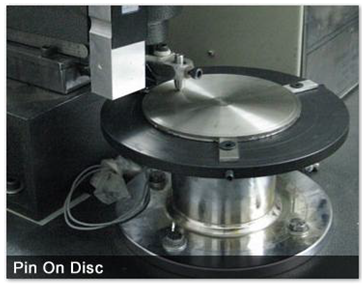 | Figure 2. Wear testing machine |
Table 2. Time estimation to cover distance 5000meters  |
| |
|
3. Material Selection and Composition
Various compositions of manganese and silicon are used as alloying elements for the aluminium alloys from which specimens are fabricated. Since they play a big role in enhancing the material properties, the following composition table describes the percentage composition in the entire alloy.Table 3. Weight percentage of composition 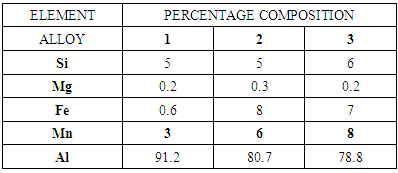 |
| |
|
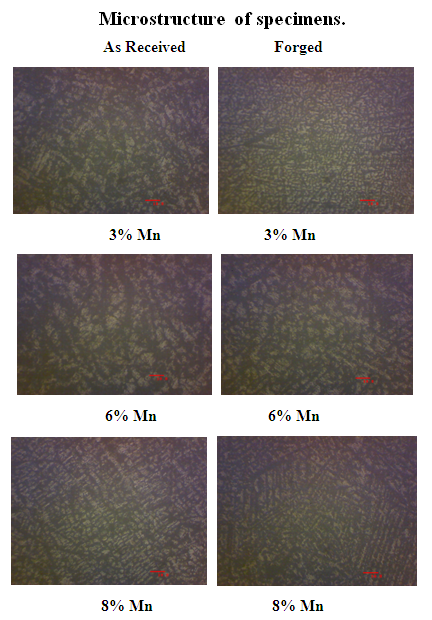 | Figure 3. Represent the microstructure for both as received and forged alloys |
4. Results and Discussion
From the figures 4 and 5 it is observed that wear rate is decreased with increase in the % Mn for both as received and forged specimens. With increase in the percentage of Mn the alloy becomes hard. Also Mn is more prone to work hardening. It is known from the Archard’s wear law is that wear loss is directly proportional to the normal load and inversely proportional to the hardness of the alloy. With increase in the percentage of Mn it is observed that hardness is increased. Also it is observed that wear rate for low speed of 0.5 m/s has higher values than the wear rate for high speed of 3.0 m/s. During wearing, micro weld occurs at the asperities between the wearing surfaces due to the normal load and frictional temperature. These micro welds grow with the residential time between the wearing surfaces. With increase in the sliding speed the residential time between the wearing surfaces will reduce. During wearing asperities will separate in the form of wear debris. If the speed is low, then bigger size wear debris will separate from the wearing surface due to the more residential time between the wearing surface of pin and disc. If the speed is high then small size wear debris will separate from the wearing surfaces due to less residential time between the wearing surfaces. Therefore wear rate for 3 m/s has fallen below the wear rate for 0.5 m/s. Also it is observed that wear rate for 3 m/s for both as received and forged specimen is almost constant with the increase in the Mn percentage. From the fig 9 it is observed the oxidative wear mechanism. Oxidative wear mechanism is the formation of oxide layer between the wearing surfaces which avoids the direct contact between the wearing surfaces hence, minimum wear occurs in the oxidative wear mechanism for as received and forged specimen at 3 m/s. Wear rate for as received specimen at low Mn is high. This is due to softness of the specimen and wear mechanism is two body abrasive wear mechanism. In two body abrasive wear, asperity will not separate from the wearing surface, but adheres to the disc and abrade the wearing surface like grinding operation. The two body wear mechanism is observed in the Fig 8. For forged specimen at 3% Mn the wear mechanism is delaminative fig 10. This is because Mn is embedded in the softer matrix of ferrite. Ferrite is soft phase and it deforms plastically more. The wear rate is more but quite less than when compared with the as received specimen because Mn modifies the AlSi alloy [1]. Wear rate for forged specimen is low when compared with the as received specimen. During wearing the impact shocks will act on broken Mn and the softer ferritic matrix gives cushioning effect to broken Mn the grains, hence, reduces the wear rate. Mn is hard particle gets direct contact with the disc after wearing ferrite softer matrix. This Mn deform plastically and overlays on ferrite phase later it delaminates. Manganese, if present in the alloy above 0.8%, it forms a compound whose primary crystals appear as hexagonal globules that reduce embrittlement in Al-Si alloy [2].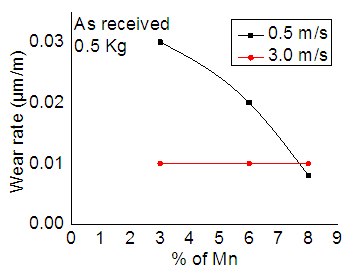 | Figure 4. Effect of % Mn on wear rate for as received specimen at 0.5 kg |
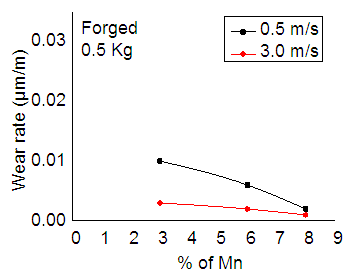 | Figure 5. Effect of % Mn on wear rate for as received specimen at 0.5 kg |
The figures 6 and 7 represent corresponding frictional force for low speed of 0.5 m/s is above the high speed of 3 m/s. This is because of size of the asperities. More the cross sectional area of the asperities more the frictional force is required to slide. Frictional force for forged specimen is less when compared with the as received specimen. Because forged specimen is softer than the as received specimen. In forged specimen broken Mn particles embedded in the softer matrix of ferrite. Hence the bulk hardness of the forged specimen is softer than the as received specimen and almost equal with increasing in Mn. Mn improves the wear resistance at AlSi alloy [3]. High Mn content Al alloy can be used for industrial application [4].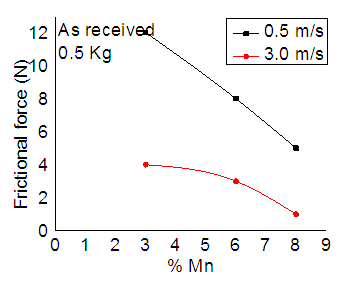 | Figure 6. Effect of Mn on frictional force of as received specimen at 0.5 kg |
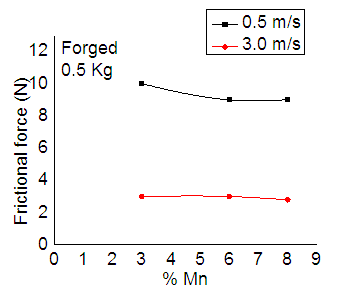 | Figure 7. Effect of Mn on frictional force for forged specimen at 0.5 kg |
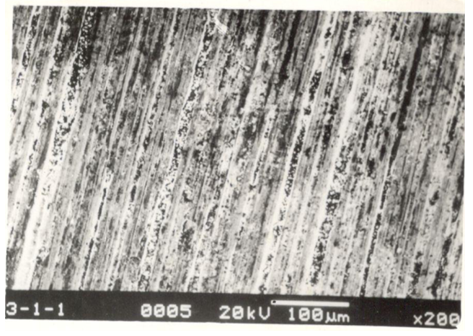 | Figure 8. Two body abrasive wear mechanism |
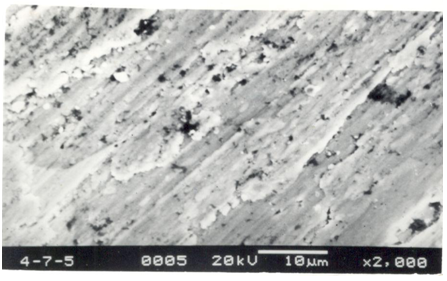 | Figure 9. Oxidative wear mechanism |
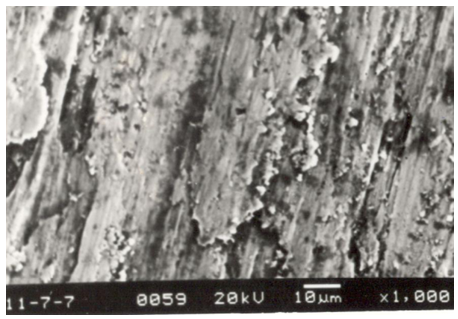 | Figure 10. Delaminative wear mechanism |
5. Conclusions
The results from this work have clearly explained the following facts:1. There was an improvement of mechanical properties with increase of Mn in the Al-Si alloy2. With increase in the Mn percentage the wear rate is decreased.3. With increase in the speed the wear rate reduced.4. Forged specimens have lower wear rate than as received specimens.5. Oxidative wear mechanism occurred at the sliding speed of 3 m/s.6. Under low speed two body wear mechanism occurred.7. Under high speed delaminative wear mechanism occurred8. Forged specimen has almost same hardness even though increasing in Mn.
References
[1] | Prabhkiran kaur, D K Dwivedi, P M Pathak and Sunil Kumar “Tribological Behaviour of Al-Si Alloy with Rare Manganese Proceedings” of the International and 16th National Conference on Machine and Mechanism, IIT Roorkee India Dec 18-20-2103. |
[2] | C N Nwambu, J U Odo, S M Obhirah, S O Nwakpa, A S Adizo and AO Agbo “Structural Modification of Aluminium-Manganese Silicon Alloy with Sodium Fluoride” www.ijesi.org Volume 3 issue4 april 2014 PP 25-30. |
[3] | Prabhkiran kaur, D K Dwivedi, P M Pathak and Sunil Kumar “Improvement in wear properties of Hypereutectic Aluminium silicon alloy with Manganese” Bonfring International Journal of Industrial Engineering And Management Science Vol 4No 3Aug 2. |
[4] | S H Algie, J A Eady, L M Hogan “Couple Growth in Al-Mn Alloy” Material Science and Engineering “73(1985) Pg 165-176. |