Ankith Y. A., Hamritha S., Gnanesh C. M., Kiran Aithal S.
Department of Mechanical Engineering, Nitte Meenakshi Institute of Technology, Bangalore, India
Correspondence to: Ankith Y. A., Department of Mechanical Engineering, Nitte Meenakshi Institute of Technology, Bangalore, India.
Email: |  |
Copyright © 2017 Scientific & Academic Publishing. All Rights Reserved.
This work is licensed under the Creative Commons Attribution International License (CC BY).
http://creativecommons.org/licenses/by/4.0/

Abstract
Functionally graded material is the best in class for its unique characteristic because of its varying composition. This paper describes the effect of teeming temperature against the mould rotational speed for a cast having the Si deposition varying from top to bottom along its height. Solid cylinder castings are generated by considering teeming temperature and mould rotational speed as the basic parameters through centrifuge casting technique. These casts are evaluated for microstructure, hardness and tribological properties. The microstructure revealed a large deposition at the top and gradually decreasing towards the bottom. Hardness value of the cast were examined along its height with varying values due to the variation in percentage of Si. Similarly, specimens were tested for tribological properties, in which cast samples showcased a unique property of decreasing the specific wear rate with the increase in the teeming temperature and mould rotational speed.
Keywords:
Centrifuge Casting, Functionally Graded Materials, Al-Si alloy
Cite this paper: Ankith Y. A., Hamritha S., Gnanesh C. M., Kiran Aithal S., Characterization of Al-18%wt Si through Centrifuge Casting for Different Teeming Temperature and Rotational Speeds, American Journal of Materials Science, Vol. 7 No. 4, 2017, pp. 120-123. doi: 10.5923/j.materials.20170704.11.
1. Introduction
The Functionally Graded Materials like aluminum alloy are under the spotlight for quite some time and the ideas of using aluminum alloys as a permanent replacement for steel have gathered a lot of interest in the area. Aluminum being the most wide spread metal on the surface of the planet earth is not available in its purest form naturally instead it is most commonly present in the form of its sulphates which are used for variety of purposes. The major advantages of aluminum is the fact that it is lightweight material and is durable almost as steel is.It is also very ductile, that makes it easy to process, and it is corrosion resistant because of the thin aluminum oxide layer on the surface. It has a good electric conductivity and can form alloys with almost all other metals.Silicon on the other hand is a metalloid, which means it has both the properties of metals and non-metals. It is brittle in nature, not a very good conductor but has conductivity somewhere in between that of the metals and non-metals, it is a semiconductor. Silicon is also widely available on the earth’s surface in the form of sand. Slightly less dense than aluminum has a melting point twice as much of aluminum has better wear resistance.Adding Si to aluminum decreases the melting point of Al and increases the fluidity. This also helps in the distribution of Si particles [1, 2].
2. Experimental Procedure
The study was carried out using the in-situ centrifuge casting equipment at different teeming temperatures and mould rotational speed. This was enabled to cast solid cylinders to study on mechanical and tribological properties.
2.1. Principle
The principle of the centrifuge casting is based on the centrifugal force. When materials with difference in densities are poured in the mould, due to rotational speed of the mould the material with the higher density will move to the bottom end and the material with lesser density will be towards the top portion of the mould. This variation in densities form a gradual increase in the proportion of the material from one end to another end, which is also known as the Functionally Graded Material (FGM). Thus, it helps to generate castings of MMC’s with denser Aluminum concentrating on the bottom of the casting and the lighter Silicon concentrating on the top portion of the casting.The equation governing the centrifugal force or the ‘G’ force is given by, | (1) |
Where,R – radius of curvature of rotating arm, mω – rotational speed of arm, rad/secg – acceleration due to gravity, m/s2The mould is located at one end of the rotating arm of the setup to which 250gms of material was poured, resulting in an L/D ratio of 1.33. The functionality of the cast material also depends on the L/D ratio of the cast and it is significantly better with L/D ratios more than 1. [3]
2.2. Material and Method
Centrifuge casting process is used to create the Al-18%wt Si alloy, which increases the distribution of hypereutectic primary Si gradually towards the bottom end and the hypoeutectic Si particles concentrated more towards the top end [3].The raw material used in this experiment is Al-18wt% Si alloy from Fen-Fee Metallurgist. The matrix alloy is an Al-Si with a composition of 18%wt Si, 0.1% Fe and the remaining is Al. Al-Si is a material with good castability. Si improves the characteristics of the casting like fluidity, hot tear resistance and feeding [3]. Table 1 shows the Material Composition. Aluminum alloy is used in those environments where corrosion is a constraint, good thermal conductivity and high strength. Pistons, bearings and engine components are the major platform for Al-Si alloys.Table 1. Material Composition  |
| |
|
Al-Si alloy was melted in a furnace at 750°C and 850°C respectively and poured into the mould made of Mild Steel. This mould was attached to the one end of the arm with counter mass on the other side of centrifuge casting setup which is pivoted at the centre to a 0.5HP single phase electric motor as shown in the Fig. 1.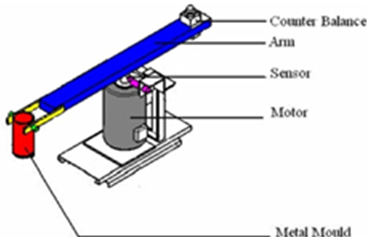 | Figure 1. Centrifuge Casting Setup |
Considering the process parameters as shown in the Table 2, Al-Si solid cylinders were cast for, arm was made to rotate at variable speeds of 200rpm and 400rpm respectively to obtain the casting samples of radius 45mm and height 55mm. The casting then used to prepare the specimens to study the mechanical and tribological properties for their respective tests. Fig. 2 shows the casting sample obtained for 850°C and 400rpm.Table 2. Process Parameters 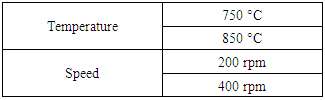 |
| |
|
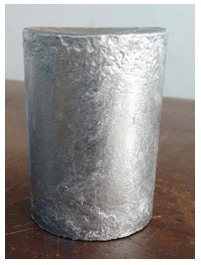 | Figure 2. Cast sample for 850°C at 400 rpm |
The cast samples were prepared according to the specific standards. The specimens were cut alog the length of the casting. The specimens were polished using the standard metallographic methods. The microstructure was characterized by optical microscope interfaced with computer to determine the percentage of Al-Si, image analyser is used at different places of the casting.The samples were cut with uniform flatness to determine Brinnel Hardness Number by polishing the surface exposed to the indenter. The hardness test was carried out using standard harness ball indenter of 10mm with 50kg.The solid cylindrical castings were machined to a pin size of 6mm diameter and 36mm length. Wear test was conducted on pin-on-disk equipment at 800rpm with track diameter of 100mm.Considering the parameters for casting process and ASTM standards, specimens were tested in two sets, three trials and the best results are discussed in the further stages of the paper.
3. Result and Discussion
The microstructure and primary Si particles distribution in the Al matrix depends on numerous factors. [4] These factors may be particle size, melt temperature, the centrifugal force, fluidity of the matrix, pouring rate, cooling rate.The present work focuses on the effect of temperature and arm rotational speed with centrifugal force at a constant percentage of Si (18%) and L/D ratio (1.33).
3.1. Microstructure
Fig. 3 shows the microstructure of Al-18%wt Si at different temperatures and rpm. The thick dark spots are the primary silicon in the hypereutectic phase and the thin lines are the hypoeutectic Si distributed randomly in the Al matrix.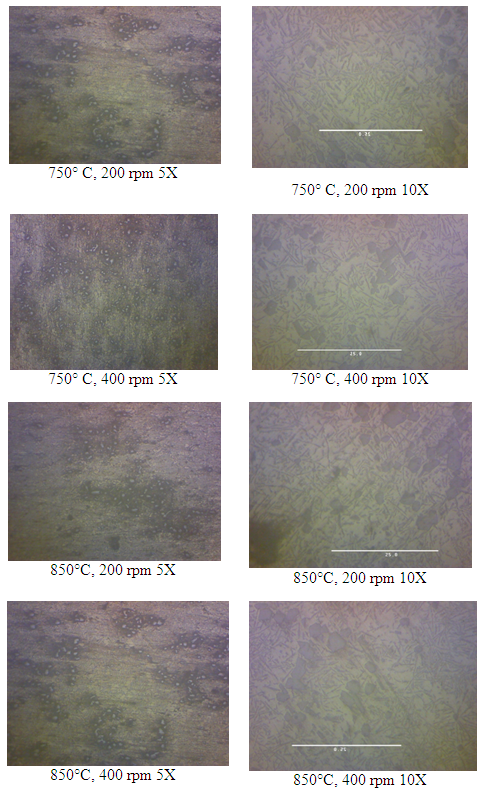 | Figure 3. Microstructure |
In microstructure the accumulation of the primary Si particles are increased towards the top part of the casting due to the centrifugal force, as the density of Al particles is high it moves towards the bottom end of the casting. By this combination, the cast samples obtained have higher concentration of Si at the top end of the casting resulting in higher percentage of Primary hypereutectic Si particles.
3.2. Hardness Test
In this paper focus is on the study of the material tested along the length of the specimen and the results have been tabulated and shown in the graph Fig.4, the study has unearthed the improvement shown from 750°C, 200rpm to 850°C, 400rpm. The linear improvement of the hardness is discussed below.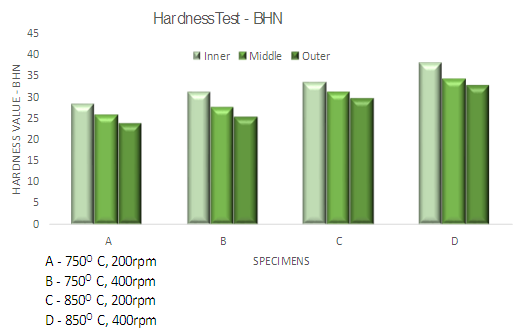 | Figure 4. Brinnel Hardness at different temperature, position and rpm |
By comparing the results,ο There is 4% increase in the hardness value for the cast samples at 750°C by varying the arm rotational speed from 200rpm to 400rpm.ο There is 8% increase in the hardness value for 200rpm from 750° to 850°C.ο There is 2% increase in the hardness value for the cast samples at 850°C by varying the arm rotational speed from 200rpm to 400rpm.ο There is 10% increase in the hardness value for 400rpm from 750° to 850°C.From the above result, we can see that rotational speed and teeming temperature have played an important role in achieving the higher values of hardness at one side of the specimen. This can be attributed for the lower solidification rate and higher centrifugal force.
3.3. Wear Test
The wear specimen were prepared according to ASTM standards for Pin-on-disk equipment. The dimensions of the wear samples were finalised to Radius r = 3mm, Height h = 36mmThe material for the specimen were taken from the top surface of the casting where the concentration of primary silicon was higher. Fig 5 shows the wear specimen and the worn surface.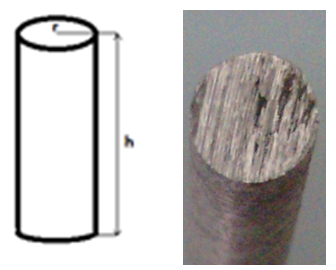 | Figure 5. Wear Specimen |
From the results in Fig. 6 for 1kg load,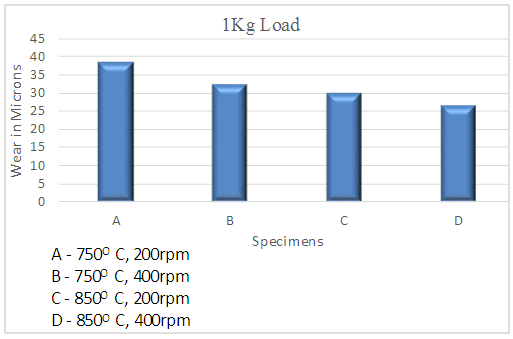 | Figure 6. Wear results for 1kg |
ο There is 18% increase in the wear resistance for the variation of rpm from 200 to 400 for casting done at 750°C.ο There is 12% increase in the wear resistance for the variation of rpm from 200 to 400 for casting done at 850°C.ο For the maximum rpm of 400, there is 22% increase in the wear resistance from 750° to 850°C.From the results in Fig. 7 for 2kg load,ο There is 10% increase in the wear resistance for the variation of rpm from 200 to 400 for casting done at 750°C.ο There is 5% increase in the wear resistance for the variation of rpm from 200 to 400 for casting done at 850°C.ο For the maximum rpm of 400, there is 15% increase in the wear resistance from 750° to 850°C.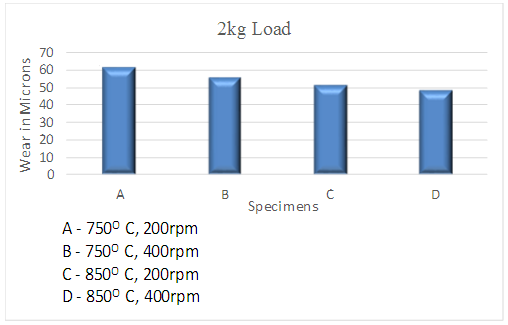 | Figure 7. Wear results for 2kg |
The increased wear resistance is highly due to more segregation of Si particles at the top end of the casting, which is the resultant of centrifugal force and teeming temperature. Much of the load and wear is taken by primary silicon, which is one of the hardest material.At the bottom part, as it is of a hypoeutectic Al-Si alloy, you can see that wear resistance is very less.
4. Conclusions
Centrifuge casting process is one among the best methods for producing solid casting to obtain better properties compared to conventional gravity castings. This also gives heterogeneous properties, which is advantageous in applications like brake shoes and wear resistant surfaces. The microstructure confirms the presence of primary silicon near the top end of the casting. The silicon concentrated region gives better wear resistance without increase in the weight. The wear resistance is linearly increased by 22% with the increase of teeming temperature from 750°C to 850°C. A 10% increase in the hardness values at higher rpm is observed.
References
[1] | R. S. Rana, Rajesh Purohit and S Das, “Reviews on the Influences of alloying elements on the microstructure and mechanical properties of aluminum alloys and aluminum alloy composites,” International Journal of Scientific and Research Publications, Volume 2, Issue 6, June 2012. |
[2] | N. Radhika & R. Raghu, “Development of functionally graded aluminium composites using centrifugal casting and influence of reinforcements on mechanical and wear properties,” Trans. Nonferrous Met. Soc. China 26(2016). |
[3] | Kiran Aithal, Narendranath, Vijay Desai and P G Mukunda “Effect of L/D ratio on Al-Si functionally graded material cast through centrifuge technique”, Advanced Materials Research Vol. 213 (2011). |
[4] | A Halvee, “A Halvaee: Effect of process variables on microstructures and segregation in centrifugal casting of C92200 alloy, J Material Processing Technology, 118 (2001) 123-127. |
[5] | G. Chirita, D. Soares, F.S. Silva, “Advantages of the centrifugal casting technique for the production of structural components with Al–Si alloys”, Materials and Design 29 (2008). |
[6] | Blesson Mathai, Prof. Cijo Mathew , Prof. Pratheesh K, Dr. Cibu K Varghese, “ Effect of Silicon on Microstructure and Mechanical Properties of Al-Si Piston Alloys”, International Journal of Engineering Trends and Technology (IJETT) – Volume 29 Number 6 - November 2015. |