Poornesh M., Johnson Xavier Saldanha, Jevy Singh, Gavin Manuel Pinto, Gaurav
Department of Mechanical Engineering, St Joseph Engineering College, Vamanjoor, Mangaluru
Correspondence to: Poornesh M., Department of Mechanical Engineering, St Joseph Engineering College, Vamanjoor, Mangaluru.
Email: |  |
Copyright © 2017 Scientific & Academic Publishing. All Rights Reserved.
This work is licensed under the Creative Commons Attribution International License (CC BY).
http://creativecommons.org/licenses/by/4.0/

Abstract
In the present work, an effort has been made to compare the properties of the composites prepared by reinforcing pure aluminium metal with varying percentage of Coconut Shell Ash and SiC particles. The composites were prepared using stir casting process with bottom pouring at a pre-set melting temperature and stirring speed. The produced composites were then studied for mechanical properties like hardness, density etc. It was noticed from the results, that the inclusion of ash and ceramic particles has a significant influence on the mechanical properties but will make the composites brittle.
Keywords:
Aluminium Composites, Coconut Shell Ash, SiC particles, Stir Casting
Cite this paper: Poornesh M., Johnson Xavier Saldanha, Jevy Singh, Gavin Manuel Pinto, Gaurav, Comparison of Mechanical Properties of Coconut Shell Ash and SiC Reinforced Hybrid Aluminium Metal Matrix Composites, American Journal of Materials Science, Vol. 7 No. 4, 2017, pp. 116-119. doi: 10.5923/j.materials.20170704.10.
1. Introduction
MMC (Metal matrix composites) are metals reinforced with other metal, ceramic or organic compounds. They are made by dispersing the reinforcements in the metal matrix. Reinforcements are usually done to improve the properties of the base metal like strength, stiffness, conductivity, etc [1]. Aluminium and its alloys have attracted most attention as base metal in metal matrix composites. Aluminium Composite materials have been considered the “material of choice” in some applications of the automotive and aircraft industries by delivering high-quality surface finish, styling details, and processing options [2]. Improvement of mechanical and tribological properties of aluminium can be achieved through creating hybrid composites with two or more types of reinforcements. Hybrid composites have improved strength, increased wear resistance, low density, corrosion resistance and high stiffness over metal matrix composites. Ceramic fibres, such as alumina and SiC (Silicon Carbide) are advantageous in very high temperature applications, and also where environment attack is an issue. Since ceramics have poor properties in tension and shear, most applications as reinforcement are in the particulate form (e.g. zinc and calcium phosphate). Ceramic Matrix Composites (CMCs) used in very high temperature environments, these materials use a ceramic as the matrix and reinforce it with short fibres, or whiskers such as those made from silicon carbide and boron nitride.Currently, AMCs are being reinforced using waste products derived from industrial processes (red mud, fly ash) and agro based materials (rice husk ash, bamboo leaf ash, ground nut shell ash, bagasse, among others) [3]. All the enumerated advantages have made AMCs become very popular and among top choice materials for a wide range of engineering applications by virtue of its excellent combination of material properties, ease processing, reduced cost, and accommodation of waste materials as reinforcement resource materials.Keneth Kanayo Alaneme et al [4] studied about the behaviour of Al alloy when reinforced with rice husk ash and alumina particles. They found that the introduction of these particles into the melt has decreased the density and hardness of the produced composites to an appreciable amount whereas the specific strength and the ultimate tensile strength have seen to be increasing with the increase of the reinforcements with the matrix. T.M. Adewale et al [5] worked on the influence of rice husk ash and SiC particles on the aluminium alloy using stir casting technique. They concluded that, for the various combination of the reinforcements used, the density decreased with the increase of reinforcement and the porosity level seems to be in control with the average difference of only 1%. The fracture toughness of the composites prepared using only ash gave an improved result when compared to the samples reinforced with both ash and SiC particles. The similar trend in the result was also obtained even in the values of tensile strength of the prepared composites. Al-Mg-Si alloy was reinforced with Bamboo leaf ash and SiC particles by means of a double stir casting process by K.K. Alaneme et al [6] to compare the results of their properties. The following results were obtained by their study. The density, hardness and ultimate tensile strength of composites decreased with the increase of ash. Under the corrosion test it was found that the produced composites show more resilience towards the acidic based liquids. Hence, the objective of the present work is to study the influence of Coconut Shell Ash and SiC particles on the mechanical properties when they are reinforced with pure aluminium metal using stir casting process.
2. Experimental Details
The composites for the study were fabricated using a bottom pouring stir casting machine. The matrix material i.e. the pure aluminium metal was weighed in a weighing scale according to required amounts and was then placed inside the crucible which was electrically conducted. The melting temperature employed to melt the aluminium was 750°C. The reinforcements i.e. Coconut Shell Ash and SiC used in making the composite were commercially available with particle size of 40μm and 60μm respectively. A small amount of Mg was added into the molten metal mix in order to increase the wettability of the melt. The particles before adding into the molten metal mix were preheated in the oven to a temperature of 200°C to avoid the presence of any sort of moisture in them. The stirring action was performed by using a mechanical stirrer which was rotating at a speed of 600rpm. The stirring of the molten mix was continued for 5 minutes to ensure equal and uniform distribution of reinforcements with the matrix. The mix was then passed into the mould cavity and was allowed to solidify. Upon solidification the composite was subjected to sudden quenching in water to avoid any effects of chilling. The same procedure was employed to produce all the composites used in this study.
3. Results and Discussions
3.1. Density
Table 1. Composition of Coconut Shell Ash [7]  |
| |
|
Table 2. Samples Prepared 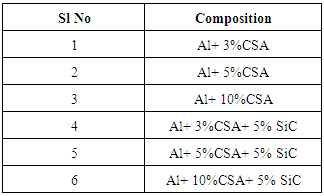 |
| |
|
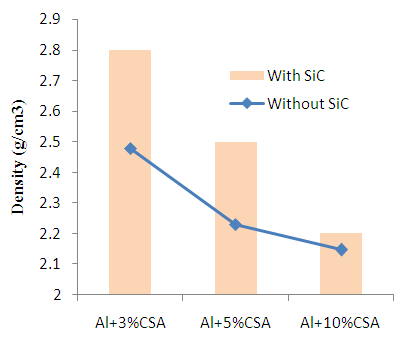 | Figure 1. Comparison of density for different composition of coconut shell ash and silicon carbide |
From the Fig 1 it is particularly clear that the increase in percentage of the coconut shell ash decreases the density of the composites. From the Table 1, which represents the composition of CSA, it is observed that the major component of the ash is made of Silica or Silicon Oxide. The density of this SiO is found to be varying the range of 0.32-0.35 g/cm3. The density of the CSA on its own from the water displacement test was found to be around 0.2 g/cm3. Because of these reasons, when a lower density reinforcing particles when mixed with the heavier matrix material tends to decrease the overall density of the hence produced composite.Similarly, the density of the produced samples seems to be decreasing with the increasing content of CSA and SiC. The decreasing tendency of the composites is because of the presence of SiO in the CSA which was used as the reinforcing particles. Because of the presence of the SiC particles along with CSA in the composite, there is a slight increase in the density. This is for the reason that, the density of the SiC particles is higher than the matrix material and the reinforcing CSA with values in the range of 3.2 g/cm3. This dense particle when used as reinforcement goes on to increase the density.But when comparing the composites manufactured using CSA particles and hybrid composite as shown in Fig 1, it can be seen that the inclusion of SiC particles increases the density of the composites. But this increase in density is only in a smaller margin. While the presence of SiO and other particles in ash reduces the density of the composites, the SiC particle due to its inherent higher density increases the density of the composites. The higher the percentage of ash lower will be the density as seen through the Fig 1, but introduction of SiC particles into the matrix slightly increase the density.
3.2. Hardness
It is clear from the Fig 2 that the increase in the reinforcing particles increases the hardness of the composites. The Table 1 gives the composition of the Coconut shell ash.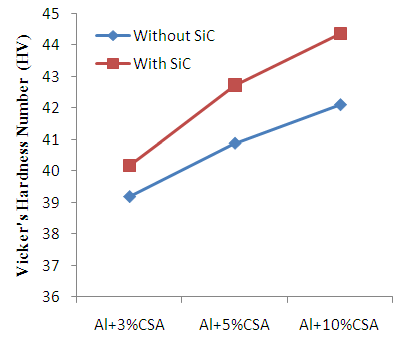 | Figure 2. Comparison of Hardness for different composition of coconut shell ash and silicon carbide |
From the composition of CSA particles it can be certainly perceived that it contains major amount of SiO in it which is a very hard ceramic particle of its own accord. When these CSA particles are used as reinforcement material in Al metal, the hardness is ought to increase due to the presence of hardening elements like SiO, MgO, MnO in reinforced ash as there is a uniform distribution of particles in the matrix of Aluminium. The load is taken by the SiO particles that are uniformly distributed in the matrix. The hardness of the base metal aluminium was found to be 37.23 HV and when it is compared with the hardness of the samples prepared using only CSA there is a 5.2% increase in hardness value between Al and when reinforced with 3% CSA. This basically means that when the unreinforced matrix is mixed with hard reinforcement there is a commendable change in its property. Likewise, a 4.4% and 3% increase in the hardness value is observed between sample 3% and 5% and 5% and 10% respectively. Hence, a conclusion can be drawn that adding CSA as reinforced to pure aluminium base material will increase the hardness of the base matrix material.An increasing trend of hardness is observed with increase in wt fraction of coconut shell ash mixed with silicon carbide. It is observed that the fact that the combination of silicon carbide with coconut shell ash particles possess higher hardness than aluminium. This is because silicon carbide particles have higher density and are hard. The coconut shell ash particles have various hardening elements as mentioned. Due to which the mixture has higher hardness compared to pure aluminium. The SiC particles present in the composite tend to take the load acting on it. Owing to the higher density and higher hardness of the particles, the load acting on the specimen will be nullified.
3.3. Tensile Strength
It is very evident that introducing ash particles into the aluminum matrix increases the load taking capacity of the composite or in other words it increases the tensile strength of the composites. With the increase of the reinforcing particles the strength increases because of the various compositions of materials present in CSA as shown in Table 1. The presence of particles like SiO, MgO, MnO, Al2O3 etc in the ash which are clearly oxide based or ceramic based gets variegated with the aluminium matrix and binds the particles with the matrix material. Hence, when the tensile test is being conducted, the pulling force or load when applied on the specimen gets transferred from the matrix and hence will be taken upon by the reinforcing particles. These reinforcing particles aid the matrix material to resist any sort of deformation up to the yield point. Even though these reinforced particles takes up majority of the load during loading, it is nevertheless a ceramic particle, which means that post yielding the composites may not show any necking and will lead to sudden failure. It is a known fact that SiC particles are ceramic in nature which purely indicates that it will be a load bearing and load taking element in the composites. The fact has been proved by the results of hardness. The SiC particle due to its intrinsic property goes on to be a hard and brittle material. When this material is reinforced on to a comparative softer matrix material leads in tremendous improved in the property of the base material. The above is clearly proved by results shown in the Fig 3. The presence of SiC particles obstructs the motion of dislocations in the period of plastic deformation and thus allowing the matrix to behave like an isotropic material. This is the reason for the increased ultimate tensile strength in the composite.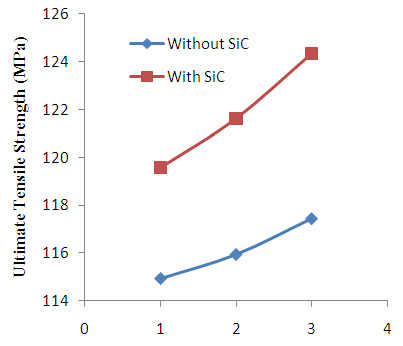 | Figure 3. Comparison of Hardness for different composition of coconut shell ash and silicon carbide |
4. Conclusions
The following results were concluded by the above study:a. Stir casting technique can be successfully employed to prepare the composites having aluminium as the matrix material and Coconut Shell Ash and SiC particles as the reinforcing elementsb. The density of the composites produced with only CSA as reinforcements showed an decreasing trend with the increase of the content of the reinforcements. The addition of the SiC particles into the mix have increased the density of the samples to an palpable level but even these composites shows the same trend because the higher content of ash. c. The results of the hardness of the composite on the other hand revealed that, with the increase of the content of ash in the mix, the hardness increases. Similarly, the introduction of ceramic particles also increases the hardness of the composites because they act as the load bearing elements in the produced samplesd. The Ultimate Tensile Strength of the composites increased with trivial with the increase of percentage of Coconut Shell Ash. But a noticeable improvement in the values where found when reinforced along with SiC particles because of the hard ceramic particles tend to block any sort of elongation in the composite produced when subjected to load.
ACKNOWLEDGEMENTS
The authors are grateful to the management of St Joseph Engineering College, Vamanjoor, Mangaluru and Nitte Meenakshi Institute of Technology, Bengaluru for allowing us to use the facility from the research centre for the completion of this study.
References
[1] | B. Vijaya Ramnath, C. Elanchezhian, RM. Annamalai, S. Aravind, T. Sri Ananda Atreya, V. Vignesh, C.Subramanian, “Aluminium Metal Matrix Composites - A Review”, Rev. Adv. Mater. Sci. 38, Pg.55-60, 2014. |
[2] | M. G. Anantha Prasad, Nityanand Bandekar, “Study of Microstructure and Mechanical Behavior of Aluminum/ Garnet/Carbon Hybrid Metal Matrix Composites (HMMCs) Fabricated by Chill Casting Method”, Journal of Materials Science and Chemical Engineering, 2015, 3, 1-8. |
[3] | Kenneth Kanayo Alanemea, Tolulope Moyosore Adewale, Peter Apata Olubambi, “Corrosion and wear behaviour of Al–Mg–Si alloy matrix hybrid composites reinforced with rice husk ash and silicon carbide” Journal of Material Research and Technology, 3(1):9–16, 2014. |
[4] | Keneth Kanayo Alaneme, Idris B. Akintunde, Peter Apata Olubambi, Tolulope M. Adewale, “Fabrication characteristics and mechanical behaviour of rice husk ash – Alumina reinforced Al-Mg-Si alloy matrix hybrid composites”, Journal of Material Research and Technology, 2(1):60-67, 2013. |
[5] | T.M. Adewale, K.K. Alaneme, “Influence of Rice Husk Ash – Silicon Carbide Weight Ratios on the Mechanical behaviour of Al‐Mg‐Si Alloy Matrix Hybrid Composites” Tribology in Industry, Vol. 35, No. 2, 163‐172, 2013. |
[6] | K.K. Alaneme, B.O. Ademilua, M.O. Bodunrin, “Mechanical Properties and Corrosion Behaviour of Aluminium Hybrid Composites Reinforced with Silicon Carbide and Bamboo Leaf Ash”, Tribology in Industry, Vol. 35, No. 1, 25‐35, 2013. |
[7] | P.B Madakson, D. S. Yawas, A. Apasi, “Characterization of Coconut Shell Ash for Potential Utilization in Metal Matrix Composites for Automotive Applications”, ISSN: 0975-5462, Vol. 4 No.03, March 2012. |