Poornesh M., Johnson Xavier Saldanha, Jevy Singh, Gavin Manuel Pinto, Gaurav
Department of Mechanical Engineering, St Joseph Engineering College, Vamanjoor, Mangaluru
Correspondence to: Poornesh M., Department of Mechanical Engineering, St Joseph Engineering College, Vamanjoor, Mangaluru.
Email: |  |
Copyright © 2017 Scientific & Academic Publishing. All Rights Reserved.
This work is licensed under the Creative Commons Attribution International License (CC BY).
http://creativecommons.org/licenses/by/4.0/

Abstract
In the present work, an effort has been made to study about the properties of the composites prepared by reinforcing pure aluminium metal with varying percentage of Coconut Shell Ash and SiC particles. The composites were prepared using stir casting process with bottom pouring at a pre-set melting temperature and stirring speed. The produced composites were then studied for mechanical properties like hardness, density etc. It was noticed from the results, that the inclusion of ash and ceramic particles has a significant influence on the mechanical properties but will make the composites brittle.
Keywords:
Aluminium Composites, Coconut Shell Ash, SiC particles, Stir Casting
Cite this paper: Poornesh M., Johnson Xavier Saldanha, Jevy Singh, Gavin Manuel Pinto, Gaurav, Effect of Coconut Shell Ash and SiC Particles on Mechanical Properties of Aluminium Based Composites, American Journal of Materials Science, Vol. 7 No. 4, 2017, pp. 112-115. doi: 10.5923/j.materials.20170704.09.
1. Introduction
The synthesis and characterization of a wide array of Aluminium based composites has unremitting to engender a lot of attention adjudicating from the large volume of publications in this area of materials science and engineering for the past thirty years [1]. This is owing to the versatile applications Al based composites have been efficaciously utilized in and the huge prospects it has for so many other new applications. From the development of high performance components for automobile, aerospace, defence, marine and other notable industrial applications to the development of facilities for sports and recreation, the areas of application of Al based composites is expected to still continue to grow.Metal matrix composites (MMCs) hold significantly enhanced properties comprising of high specific strength, specific modulus, damping capacity and good wear resistance compared to unreinforced alloys [2]. Similarly, there has been an increasing interest in composites containing low density and low cost reinforcements. Among various discontinuous dispersions used are fly ash, red mud, Rice husk ash are some of the most inexpensive and low density reinforcement available in large quantities as solid waste by- product.Coconut shell has diminutive or no economic value but they are appropriate for preparation of carbon black due to its outstanding natural structure and low ash content [3]. At present, the Nigeria coconut shell is recycled as a source of fuel for the boilers, and residual coconut shell is disposed off as gravel for plantation roads maintenance. Black smiths also purchase the coconut shell as fuel material in their casting and forging operations. Therefore, the objective of this current work is to characterize coconut shell in order to discover its usage in metal matrix composites.In the work conducted by J W Pinto et al [4] when Coconut Shell Ash and E-fiber were reinforced with Al-6061 alloy using the stir casting technique, an appreciable increase in various mechanical properties like micro hardness and Ultimate Tensile strength was noticed. Moreover, the triobogical property i.e. the specific wear rate showed a decreasing trend with the increase of the reinforcements. Prakash Kumar Dalai et al [5] studied about the influence of machining process parameters of agro waste reinforced aluminium metal matrix composites. They clearly stated that, the introduction of agricultural wastes like flyash and coconut shell ash has increased the hardness and tensile strength of prepared composites. The silicon content present in the ash has helped in increased in the strength of the composites but when the amount of ash was increased the ductility of the specimen decreased. The cutting forces involved showed a decreasing trend with the increase of cutting speed. M P Navin et al [6] investigated about the changes in the properties of the Al 360 alloy when it was reinforced with Coconut Shell Ash and SiC particles. The composites was prepared using stir casting technique with various proportions of the reinforcements and were tested for hardness and tribological properties so that it can be used for clutch plate. It was observed that, the hardness of the composite prepared using the coconut shell ash was lower than that of the base alloy but with the addition of SiC particles a considerable increase in the hardness was obtained. The coefficient of friction and the wear resistance was found to be increasing with increase of SiC content in the composite. Ankesh Kumar et al [7] inspected the physical, mechanical and tribological properties of aluminium with coconut shell ash. The density and the hardness of the samples revealed that with the increase of percentage of ash in the matrix reduced the density but increased the hardness of the composites. The machining parameters like depth of cut, speed and feed rate against the surface roughness was compared and the reinforced composites exhibited better properties than the unreinforced base alloy.
2. Experimental Details
The present study was conducted by reinforcing the commercially available pure aluminium metal with various percentages of Coconut Shell Ash and SiC particles to form hybrid metal matrix composites. The Coconut Shell Ash particles employed for the preparation of the composites had a particle size varying from 50-60μm whereas the SiC particles added was ranging from 40-60μm. The composition of the Coconut Shell Ash is given in Table 1.Table 1. Composition of Coconut Shell Ash [8]  |
| |
|
The composites were prepared using the following configuration:Table 2. Samples Prepared 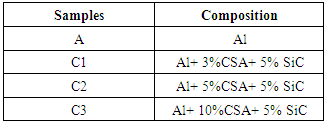 |
| |
|
The castings were synthesised by means of a stir casting machine which had a flange that was linked to a shaft of synchronous DC motor. The speed could be mottled from 200 to 1000 rpm. The die used had a length of 250mm, width 25mm and breadth of 35mm. The casting was made by liquefying Al to a temperature of 750°C. The reinforcement particles used for the preparation was preheated to a temperature of 180°C to remove any amount of moisture present in them. The reinforcing particles where then successively added by using a stirring speed of 600 rpm and a holding time of 5 minutes.
3. Results and Discussion
3.1. Hardness
 | Figure 1. Comparison of hardness for different composition of coconut shell ash and silicon carbide |
The hardness of the prepared composites was found using Vicker’s Hardness Test. Fig 1 gives the variation of hardness value of the samples. An increasing trend of hardness is observed with increase in wt fraction of coconut shell ash mixed with silicon carbide. It is observed that the fact that the combination of silicon carbide with coconut shell ash particles possess higher hardness than aluminum. This is because silicon carbide particles have higher density and are hard. The coconut shell ash particles have various hardening elements as mentioned. Due to which the mixture has higher hardness compared to pure aluminum.The SiC particles present in the composite tend to take the load acting on it. Owing to the higher density and higher hardness of the particles, the load acting on the specimen will be nullified.It is evident form the Fig 1, that an 7.8% increase in the hardness between the base metal and C1 is obtained with successive increase of 6.4% and 3.9% between the other two compositions.
3.2. Density
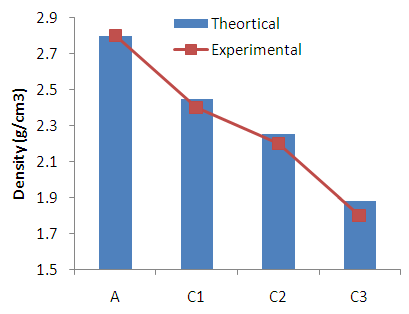 | Figure 2. Comparison of density for different composition of coconut shell ash and silicon carbide |
Figure 2 gives a comparative result between the theoretical and experimental results of the density. It can be noticed that in both the cases, the density of the specimen decreases with the increase of reinforcing particles. From Table 1, it can be clearly seen that the Coconut Shell Ash contains higher percentage of SiO particles in them. The density of the SiO carbide particles is 0.32 g/cm3 and the density of the Coconut Shell Ash through water displacement tests was found to be 0.45 g/cm3. The density of the composite automatically decreases when the matrix is reinforced with a lower density particle. Thus, with the increase of the reinforcing particles the density decreases. However, the presence of 5% SiC particles slightly increases the density of the composite because of its inherent higher density. But, as the amount of SiC particles added into the mix is lower than that of the ash a decreasing trend is obtained. It is evident from Figure 2 that the experimental density value is lower than that of the theoretical values because of the presence of pores or any sort of abnormalities occurred because of casting.
3.3. Impact Test
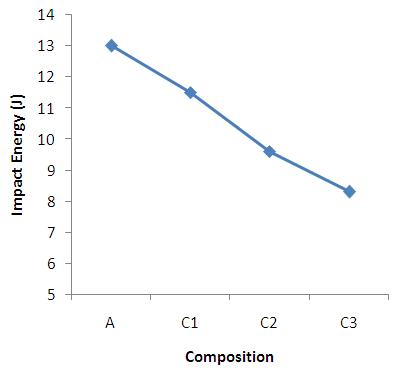 | Figure 3. Comparison of Impact Energy for different composition of coconut shell ash and silicon carbide |
Because of the addition of 5wt% SiC, it can be noticed that there is a discernible drop in the value of the impact energy. This decrease in the toughness of the hybrid composite in the result is due to the presence of the ceramic reinforcement particles. The addition of the ceramic reinforcement particles tends to improve its strength under the slow loading conditions as in the case of tensile test. But under the sudden loading applied during to the impact test, due to its inherent brittleness the reinforcing particles fails to impart the strength to its matrix material.The ceramic particles that is added to the matrix material i.e., SiC particles on its own is a very brittle particle. Even though these particles have beneficiary properties like improved hardness, higher load taking ability and extensive tensile nature, the only drawback is the existence of brittleness in it. This inelastic or brittle property of these particles causes the prepared composites to behave in the exact same way. Hence, the result of impact energy of hybrid composites is comparatively lower than the ones without the inclusion of ceramic particles.
3.4. Tensile Test
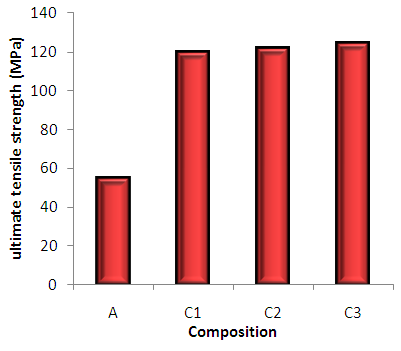 | Figure 4. Comparison of Impact Energy for different composition of coconut shell ash and silicon carbide |
The Figure 4 clearly shows the introduction of SiC particles has drastically increased the tensile strength of the composite materials.It is a known fact that SiC particles are ceramic in nature which purely indicates that it will be a load bearing and load taking element in the composites. The fact has been proved by the results of hardness. The SiC particle due to its intrinsic property goes on to be a hard and brittle material. When this material is reinforced on to a comparative softer matrix material leads in tremendous improved in the property of the base material. The above is clearly proved by results shown in the Fig 4. The presence of SiC particles obstructs the motion of dislocations in the period of plastic deformation and thus allowing the matrix to behave like an isotropic material. This is the reason for the increased ultimate tensile strength in the composite.
4. Conclusions
The following conclusions can be drawn from the present study:i. The composite was successfully cast using the stir casting technique under a teeming temperature of 750°C and a stirring speed of 600 rpm.ii. From the results of Vickers Hardness Test, it was noticed that inclusion of reinforcing particles has helped in increasing the hardness of the composites. A significant increase from 37 HV to 44 HV was found when the composite was reinforced with 10% of CSA and 5% of SiC.iii. The impact energy as well as the density of the composites exhibited an decreasing trend in the result because of the inherent properties demonstrated by the additives. iv. The tensile tests results revealed that, with the increase of the reinforcements in the matrix material, the UTS increases. However, increase of the reinforcing particles slowly decreases the brittleness of the composite.
ACKNOWLEDGEMENTS
The authors are grateful to the management of St Joseph Engineering College, Vamanjoor, Mangaluru and Nitte Meenakshi Institute of Technology, Bengaluru for allowing us to use the facility from the research centre for the completion of this study.
References
[1] | K.K. Alaneme, B.O. Ademilua, M.O. Bodunrin, “Mechanical Properties and Corrosion Behaviour of Aluminium Hybrid Composites Reinforced with Silicon Carbide and Bamboo Leaf Ash”, Tribology in Industry, Vol. 35, No. 1 (2013) 25‐35. |
[2] | P.B Madakson, D.S. Yawas, A. Apasi, “Characterization of Coconut Shell Ash for Potential Utilization in Metal Matrix Composites for Automotive Applications”, International Journal of Engineering Science and Technology (IJEST), Vol. 4 No.03 March 2012. |
[3] | L. Lancaster, M. H. Lung, D. Sujan, “Utilization of Agro-Industrial Waste in Metal Matrix Composites: Towards Sustainability” International Journal of Environmental, Chemical, Ecological, Geological and Geophysical Engineering, Vol:7, No:1, 2013. |
[4] | J. W. Pinto, G. Sujaykumar, Sushiledra R. M, “Effect of Heat Treatment on Mechanical and Wear Characterization of Coconut Shell Ash and E-glass Fiber Reinforced Aluminum Hybrid Composites”, American Journal of Materials Science, 6(4A): 15-19, 2016. |
[5] | Prakash Kumar Dalai, Ajit Senapati, “Experimental Investigation & Analysis of Process Parameter in Machining Of Aluminum Based Metal Matrix Composite”, International Journal Of Engineering Sciences & Research Technology, January, 2014. |
[6] | M P Navin, R Deivasigamani, “Material Characterization of Aluminium Hybrid Composite for Clutch Plate” International Journal Of Engineering Sciences & Research Technology, Vol. 4, No. 1, February 2015. |
[7] | Ankesh Kumar, Kanhaiya Kumar, Suman Saurav, Siva Sankar Raju R, “Study of Physical, Mechanical and Machinability Properties of Aluminium Metal Matrix Composite Reinforced with Coconut Shell Ash particulates”, Imperial Journal of Interdisciplinary Research (IJIR), Vol-2, Issue-5, 2016. |
[8] | P.B Madakson, D.S. Yawas, A.Apasi, “Characterization of Coconut Shell Ash for Potential Utilization in Metal Matrix Composites for Automotive Applications”, ISSN: 0975-5462, Vol. 4 No.03, March 2012. |