Basavarajappa M. P.1, K. I. Parashivamurthy2
1Department of Mechanical Engineering, Adichunchanagiri Institute of Technology, Chikkamagalur, India
2Department of Mechanical Engineering, Government Engineering College, Chamarajanagara, India
Correspondence to: Basavarajappa M. P., Department of Mechanical Engineering, Adichunchanagiri Institute of Technology, Chikkamagalur, India.
Email: |  |
Copyright © 2017 Scientific & Academic Publishing. All Rights Reserved.
This work is licensed under the Creative Commons Attribution International License (CC BY).
http://creativecommons.org/licenses/by/4.0/

Abstract
In the present research work, synthesis and characterization of in-situ Al-TiC composites was carried out. In-situ Al-TiC with 3%, 6% and 8% composite were produced by introducing carbon bearing activated charcoal in to an Al-Ti melt, thereby forming TiC particles in the melt. Wear characteristics of Al-TiC composites have been investigated under dry sliding. Dry siding wear tests have been carried out using pin-on-disk wear tester at constant sliding velocity and constant load. Weight loss of the samples has been measured and the variation of cumulative wear loss has been found to be linear. It is observed from the tests that increase in the percentage of TiC decreases the wear rate. SEM tests were performed on the prepared Al-TiC test specimens and micrographs show the formation of TiC in the composite.
Keywords:
In-situ synthesis, Al-TiC composites, Wear
Cite this paper: Basavarajappa M. P., K. I. Parashivamurthy, Synthesis and Tribological Characterization of In-situ Prepared Al-TiC Composites, American Journal of Materials Science, Vol. 7 No. 4, 2017, pp. 108-111. doi: 10.5923/j.materials.20170704.08.
1. Introduction
Aluminium based particulate reinforced MMC’s are becoming favourite choice in many applications such as aviation, space, automotive and chemical industries [1]. The superiority of aluminium matrix composite material over conventional ones is their high strength, high elastic modulus, excellent friction and wear resistance and low expansion co-efficient [2]. TiC is used as reinforcement phase because of its high hardness, elastic modulus, low density, good wettability with molten aluminium and its low chemical reactivity [3].Aluminium matrix composites are synthesized using ex-situ synthesis methods such as, powder metallurgy, stir casting, pressure infiltration etc. but the size of reinforcement in the composites is large, which leads to a limited improvement and bad interface between aluminium matrix and reinforcements [4]. Compared to ex-situ synthesis techniques, in-situ synthesis method is a new technique to prepare composites owing to many advantages like fine reinforcements, clean interface between matrix and reinforcement and good mechanical characterization [5]. In-situ processing is able to produce reinforcements in the order of 0.5-5 μm [8].Fabrication of in-situ composites involves synthesizing the reinforcing phases directly within the matrix. This approach is in contrast to ex-situ composites, where the reinforcements are synthesized separately and then introduced in to matrix during secondary process [9]. In-situ techniques involve a chemical reaction resulting in the formation of very fine and thermodynamically stable reinforcing ceramic phase within the matrix. This consequently provides thermodynamic compatibility at the metal reinforcement interface. Since reinforced surface is also likely to be free of contamination, a stronger matrix-reinforcement bond can be achieved [22].In the present work Al-TiC composites have been developed via in-situ route. The microstructure and tribological properties have been studied and the results are presented.
2. Experimental Procedure
The in-situ process involves introducing carbon bearing activated charcoal in to an aluminium melt, there by forming TiC particles in the melt. In this procedure, a known quantity of Al-Ti master alloy is melted in the electric resistance furnace to 1200°C and carbon bearing activated charcoal powder was added in to the melt to meet the stoichiometry of TiC to complete the reaction for the formation of TiC particles inside the melt. The melt is allowed for the reaction time of 20 minutes. The degasser hexachloroethane was used to remove dissolved hydrogen gas from the melt. A small amount of potassium fluoride and sodium fluoride was added as a flux cover to remove the oxide film from the molten metal surface and to act as protective barrier to gas absorption and facilitating spontaneous incorporation of particles in to the melt. Afterwards the melt was cast in to rod form (20 mm in diameter and 250 mm length) in metallic moulds to complete the process. Al-TiC composites were with varying weight percentages of reinforced particles Al-3TiC, Al-6TiC and Al-8TiC. The experimental setup for fabricating in-situ Al-TiC composites is shown schematically in Figure 1.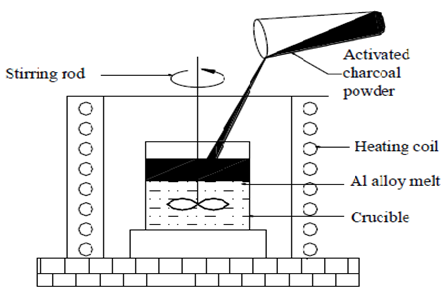 | Figure 1. Schematic diagram of the apparatus for fabricating in-situ Al-TiC composites |
Microstructures of Al-TiC composites in the as cast condition were examined using scanning electron microscope (SEM). Dry sliding wear tests for the composites have been conducted using a pin-on-disk wear testing machine. Wear tests have been conducted using cylindrical pin shaped samples (30mm x ф 10mm) that had flat surfaces in the contact region. The pin is held stationary against the counterface of a 100 mm diameter rotating disk made of En-32 steel having hardness of 65HRC as provided on the pin-on-disk machine. The wear tests have been conducted under a constant speed of 300 rpm of the disk, for different loads of 1 kg, 2kg and 3kg. Pin weight losses have been measured at different intervals of time to determine weight loss. Again the wear tests are repeated on the composites for constant load condition using a load of 2 kg, for different speeds of 300, 400 and 500 rpm.
3. Results and Discussion
3.1. Microstructure analysis
The SEM micrographs of the Al-TiC composites are as shown in Figure 2 (a-c). It was observed that Al-TiC composites prepared at 1200°C with 20 minutes of holding time have both Al3Ti and TiC particles. It is felt that the temperature was not sufficient to dissolve all the Al3Ti particles inside the melt.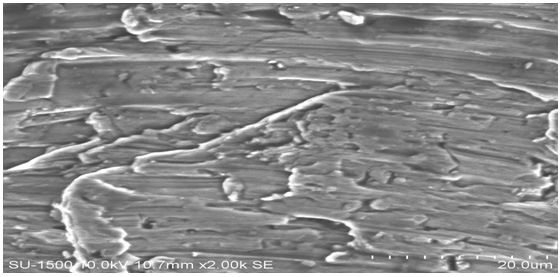 | Figure 2(a). SEM micrograph of Al-8TiC |
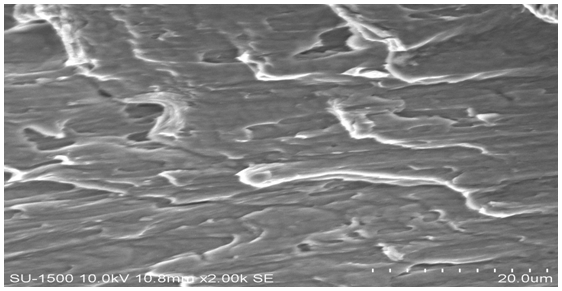 | Figure 2(b). SEM micrograph of Al-6TiC |
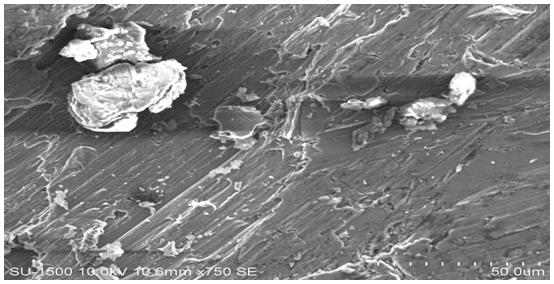 | Figure 2(c). SEM micrograph of Al-3TiC |
3.2. Wear Properties
The results of the wear test are presented in the Table 1. The effect of increase in percentage of TiC on wear rate for constant load and constant speed condition is shown in the table. It is observed that with the increase in percentage of TiC in Al-TiC composites the wear rate decreases.Table 1. Wear test results of Al-TiC composites for constant load and constant speed condition 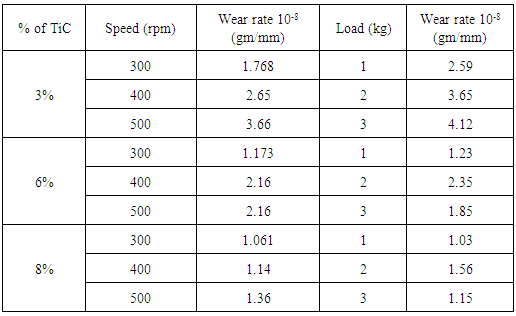 |
| |
|
Figures 3 and 4. show the variation of wear rate with variation in percentage of TiC at different speeds and loads. The wear rate decreases sharply as the percentage of TiC increases. This may be attributed to the incorporation of hard TiC particles resulting in improvement in the tribological properties of the composite.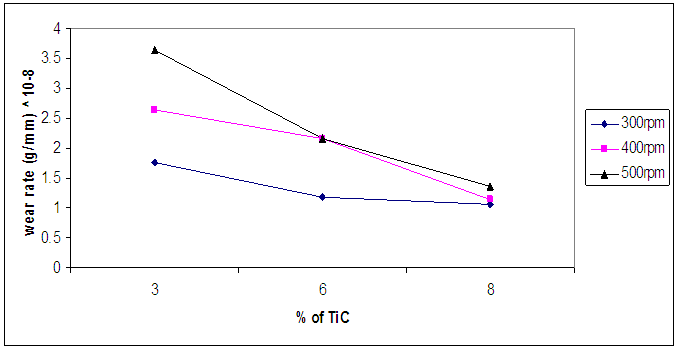 | Figure 3. Variation of wear rate with TiC volume fraction at different speeds |
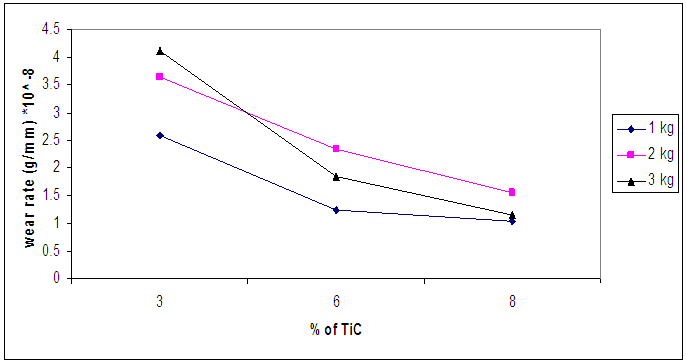 | Figure 4. variation of wear rate with TiC volume fraction at different loads |
4. Conclusions
TiC reinforced aluminium matrix composites were produced by the addition of carbon bearing activated charcoal powder in to Al-Ti melt successfully with different percentage of TiC. The following findings are concluded;1. In this method, TiC forms by the reaction between carbon and titanium in the solution.2. SEM micrographs confirm the formation of TiC in the prepared composites.3. The wear rate increase linearly with the increase in normal load following archard’s law.4. The wear rate is decreasing with the increase in percentage of TiC.
References
[1] | Rajnesh Thyagi, “Synthesis & Tribological characterization of in situ cast Al-TiC composites”, Wear 259(2005), P569-576. |
[2] | X. W. Zeng, W. G. Zhang, “Preparation of In situ TiCP /LY12 composite and its microstructure and mechanical properties”, Material science and Engineering A (2006). |
[3] | B. Yang, F. Wang, J. S. Zhang, “Microstructural characterization of in situ TiC/Al composites prepared by spray deposition”, Acta materilia, %1(20030, P4977-4889. |
[4] | Zhang Xiuqing, Liao Lihua, “New in situ synthesis method of magnesium matrix composites reinforced with TiC particulates”, Material research, 9(2006), P357-360. |
[5] | In-Hyuck Song, Dokyung Kim, Yoo-Dong Hahn, “investigation of Ti3AlC2 in the insituTiC-Al composite prepared by exothermic reaction process in liquid aluminium”, materials letters, 58(2004), P593-597 |
[6] | Ming Zhen MA, Riping Liu, Hongli zhao, “In situ TiCP/Al composites prepared by TE/QP method”, Journal of material science Technology, 21(2005), P652-656. |
[7] | P. Sahoo, M. J. Koczak, “Microstructure property relationships of in situ reacted TiC/Al-Cu Metal Matrix Composites”, Material science and Engineering A 131(1991), P69-76. |
[8] | K.L. Tee, Lilu, M. O. Lai, “Improvement in mechanical properties of in situ Al-TiB2 composite by incorporation of carbon”, Material science and Engineering A, (2003) P227-231. |
[9] | R. F. Shyu, C. T. Ho, “in situ reacted titanium carbide reinforced alluminium alloys composites”, Journal of materials processing technology, 171(2006), P411-416. |
[10] | Piejie Li, E. G. Kandalova, V. I. Nikitin, “In situ synthesis of Al-TiC in aluminium melt”, Materials letters, 59(20050, P2545-2548. |
[11] | Piejie Li, E. G. Kandalova, V. I. Nikitin, A. G. Makarenko, “Preparation of Al-TiC composites by self propagating high temperature synthesis”, Scripta Materilia, 49(2003), P699-703. |
[12] | A. R. Kennedy, D. P. Weston, M. I. Jones, “Reaction in Al-TiC metal matrix composites”, Material science and Engineering A 316 (2001), P32-38. |
[13] | M. K. Premkumar, M. G. chu, “Al-TiC particulate composite prepared by a liquid state in situ process”, Material science and Engineering A 202 (1995), P172-178. |
[14] | A. R. Kennedy, S. M. Wyat, “Characterizing particle matrix interfacial bonding in particulate Al-TiC MMCs produced by different methods’, composites parta 32(20010, P555-559. |
[15] | Bin Yang chen, Zhang, “Effect of Ti/C additions on the formation of al3Ti of insitu TiC/Al composites”, Materials and Design 22(2001), P645-650. |
[16] | Subhash khatri, Michael Koczak, “Formation of TiC in insitu processed composites via solid-gas, solid-liquid and liquid-gas reaction in molten Al-TiC”, Material science and Engineering A, 162(1993), P152-162. |
[17] | Srinidhi sampath, Michael Koczak, “Processing and analysis of insitu composites”, the minerals, metals and materials society, 1994, P37-60. |
[18] | K. I. Parashivamurthy, R. K. Kumar, Sitharamu, M.N. chandrashekaraiah, “Review on TiC reinforced steel composites’, Journal of material science, 36(2001) P4159-4530. |