Jaimon D. Quadros1, Vaishak N. L.2, Suhas2
1Department of Mechanical Engineering, Birla Institute of Technology, Offshore campus, Ras-Al-Khaimah, UAE
2Department of Mechanical Engineering, Sahyadri College of Engineering & Management, Mangalore, India
Correspondence to: Jaimon D. Quadros, Department of Mechanical Engineering, Birla Institute of Technology, Offshore campus, Ras-Al-Khaimah, UAE.
Email: |  |
Copyright © 2017 Scientific & Academic Publishing. All Rights Reserved.
This work is licensed under the Creative Commons Attribution International License (CC BY).
http://creativecommons.org/licenses/by/4.0/

Abstract
Aluminium alloy 7075 matrix composites reinforced with carbon fiber were prepared by stir casting method. For proper wettability, the carbon fibers were coated with nickel using the principle of autocatalytic reduction. The presence of nickel coating on the carbon fibers was thoroughly confirmed through Scanning Electron Microscope (SEM) and X-ray diffraction studies. The carbon fibers were used at different wt. % of 0, 1, 2 and 3 respectively. The prepared composites were then tested for mechanical properties viz. compression, Young’s Modulus and hardness. The results of this study revealed that, with the addition of nickel coated carbon fibers to the composites, a maximum increase of 10.47%, 10.38%, and 15.38% was observed in ultimate compressive strength, Elasticity and hardness respectively.
Keywords:
Aluminium alloy, Stir casting, Carbon fiber, Nickel coated, Compression, Elasticity, Hardness
Cite this paper: Jaimon D. Quadros, Vaishak N. L., Suhas, Evaluation of Mechanical Properties of Aluminium Alloy 7075 Reinforced with Short Coated Carbon Metal Matrix Composites, American Journal of Materials Science, Vol. 7 No. 4, 2017, pp. 102-107. doi: 10.5923/j.materials.20170704.07.
1. Introduction
At present, aluminium alloy matrix composites (AMCs) are finding applications in automotive sector and strategic sectors such as defence and aerospace, as well as in different segments of other engineering industries. Three decades of intensive research has provided a wealth of new scientific knowledge on the intrinsic and extrinsic effects of ceramic reinforcement, vis-a-vis physical, mechanical, thermo-mechanical and Tribological properties of aluminium alloy matrix composites. The commonly used reinforcement materials for metal matrix are alumina, aluminosilicate and silicon carbide [1]. Carbon fiber has also been considered as a reinforcement material for making the metal matrix composites [2]. Carbon fiber can be an equally satisfactory reinforcing material in polymer, metal as well as ceramic matrices because of its high specific strength and specific modulus, light weight, high thermal and electrical conductivities and low coefficient of thermal expansion.The presence of alloying elements in the matrix has an influence on the viscosity, contact angle and reaction rate with dispersoid. Carbon fiber reacts with the molten aluminium and forms Al4C3. This reaction damages the fibers severely and deteriorates the mechanical properties of the fiber and composites [3]. Also, the addition of magnesium to an aluminium melt improves wettability because of lower surface tension of magnesium [4]. A few studies that involve addition of alloys have been presented below. Ramesh et al. [5] studied the fatigue behavior of Ni-P coated with Si3N4 reinforcement Al6061 composite. Stir cast method was used to develop the composite with the various percentage of reinforcement. Cast matrix and developed composite were hot forged at a temperature of 500°C with the hydraulic hammer. The as-cast and composites were then subjected to mechanical and as well as micro structural study. The study concluded that the Ni-P coating significantly affected the fatigue behavior of the composites. Rams et al. [6] have conducted experiments on the mechanical properties of the composites through nano-indentation. In this study carbon fiber is coated with the nickel coating. This reinforcement is added with AA6061 aluminum powder, it is made compact and heated to about 650-950°C. Coating improved the wet ability of the reinforcement. The formation of a transient Al-Ni inter metallic surface with the reinforcement and matrix, and also homogeneous distribution of the reinforcement led the composite to have better properties. Apparently, very little literature is available on mechanical properties of fiber reinforced metal matrix composites prepared by Stir casting method. Most of the published data pertain to the mechanical properties of particulate-reinforced MMCs deal with tensile properties while only a relatively small amount of data has been obtained dealing with compression properties, although it is generally known that the compressive strength of an MMC is invariably higher than its UTS. Hence, in the present investigation, importance is also given to the compressive properties of the MMCs, together with the properties such as hardness and Young’s modulus. The microstructure and mechanical properties of the composites have also been studied.
2. Experimental Work
2.1. Raw Materials
The aluminium alloy 7075 was selected as the matrix; chopped carbon fibers of mean diameter 7.16μm were used as reinforcements to prepare the composites. The carbon fibers were subjected to electroless nickel coating.
2.2. Electroless Nickel Coating
The carbon fibers were initially cleaned with acetone and then placed in a hot oven for about 200°C for cleaning purpose. The coating procedure included three different stages. In the first stage i.e. i) Sensitization stage (S): The carbon filaments are plunged in a solution of 12gm/l of SnCl2. 2H2O, they are sensitized for 15 min under continuous mixing. In the second stage, i.e. ii) Activation stage (A): The strands are washed with refined water and after that they are presented to the aqueous solution of 0.5 grms/ltr of PdCl2 with agitation in order to activate the specimen to receive metal ions. In order to obtain uniform hardness, the continuous stirring was done at 600 rpm for 10 mins [7]. In the third stage i.e. iii) Metallization (M): Warming of the activated carbon fibers takes place on the hot stove at 150°C for 20 minutes in order to enable the pyrolitic covering around the fibers.
2.3. Stir Casting Process
In the stir casting process, the short coated carbon fiber was pre-heated to a temperature of about 500°C and then introduced into the Al alloying melt. A pre-determined quantity of these metal ingots was pickled in 10% NaOH solution for about 10 mins at room temperature. Pickling was done to remove surface impurities. Smuts formed on the ingots were removed by immersing the ingots in a mixture of nitric acid and water. The ingots were then washed with methanol. These cleaned ingots after drying in air were loaded into different alumina crucibles. These crucibles are kept in furnaces set to a melting temperature. The temperatures were recorded using a chromel-alumel thermocouple. A stainless steel impeller or stirrer coated with short carbon fiber has been used to stir the molten metal in order to form a vortex. The impeller used for this purpose was of centrifugal type consisting of 3 blades welded at 45° inclination and placed 120° apart. The stirrer was rotated at a speed of 500 rpm and a vortex was created in the melt. The impeller was immersed to a depth of approximately one third the height of molten metal above the bottom of the crucible. Stirring was continued until interface interactions between the short carbon fiber and the matrix promoted wetting. The melt was then degassed by using nitrogen for about 3-4 minutes and then poured to a pre-heated lower half die of the hydraulic press. The top die was then placed over the bottom in order to solidify the composite applying pressure of about 100 kg/sq.cm.
2.4. Testing of Specimens
The tests were conducted as per ASTM standards. The compression tests were conducted initially at room temperature as per ASTM E9 (Figure 1a). Here, the compression loads were increased gradually and the strain was measured until the specimen failed. The results obtained are the averages of four readings. The hardness tests were conducted in accordance with ASTM Standard E 10 (Figure 1b) using a Brinell hardness tester with a ball indenter of 2.5 mm diameter and a load of 31.25 kg. The load was applied for 30 secs. Eight hardness readings were taken for each specimen at different location to circumvent the possible effects of particle segregation. The tensile test is carried out to know the basic property of the material such as Young’s modulus. The tensile test specimen used is as per standard ASTM D1708 shown in the Figure 1c. The experiments were performed with a load capacity of 20 kN.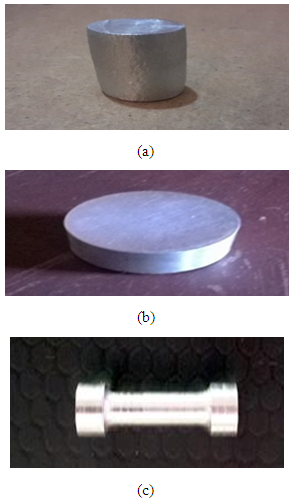 | Figure 1. Specimen for a) Compression test, b) Hardness test and c) Young’s Modulus |
2.5. Microstructure Study
The coating thickness over the carbon fiber was observed under SEM model JEOL JSM 6360 with a magnification capacity of X500, X1000, X2000 and accelerating voltage of 15 kV with a working distance of 10 mm. The X-ray Diffraction graph describes the mixture of solution that underwent for the preparation of nickel coating on the carbon fiber. This can be determined with the graph plotted intensity vs. the angle 2β and the software PCPDFWIN to determine the mixture solution which is allotted for the peaks.
3. Results and Discussion
3.1. Morphology of Electroless Nickel Coating
Figure 2 shows the morphology of uncoated and coated carbon fiber diameter. The Figure 2(a) shows the morphology of uncoated carbon fibers having a mean diameter of 7.16μm. It has already been reported in Suhas et al. [8] that, the optimum thickness of 0.64μm has to be maintained in order to attain uniform wettability over the matrix. This thickness of 8.44μm has been achieved by electroless nickel coating and is shown in Figure 2(b). The X-ray diffraction study clearly shows a high carbon content present in the uncoated carbon fiber (Figure 3a). The presence of nickel on the carbon fiber is confirmed in Figure 3b which shows the presence of almost 92% of Nickel Thiourea Chloride.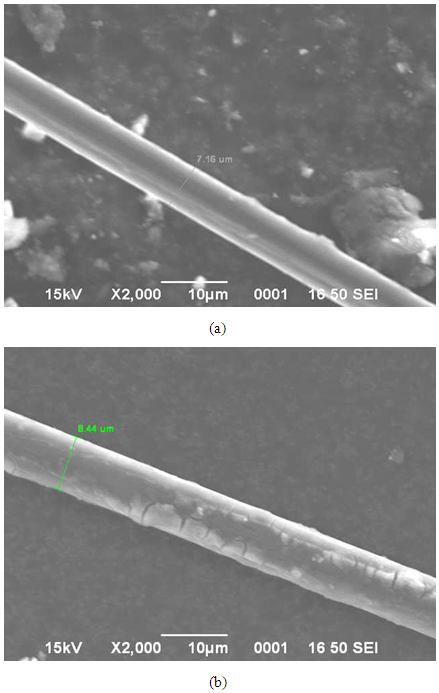 | Figure 2. SEM micrographs of a) uncoated carbon fiber diameter; b) Coated carbon fiber diameter |
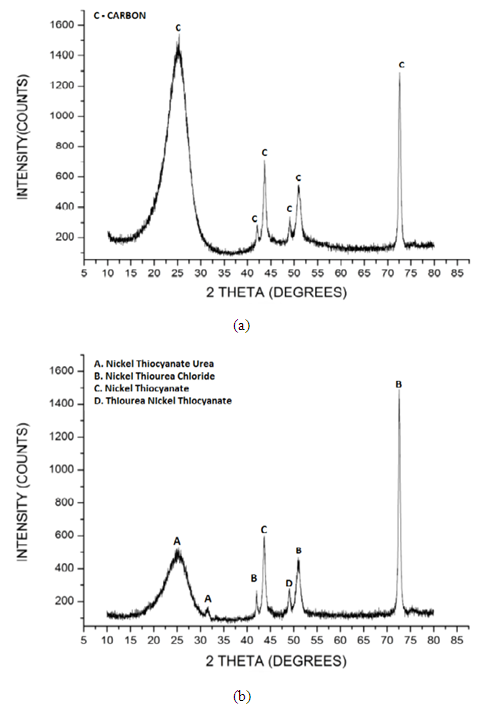 | Figure 3. a) X-ray diffraction of uncoated carbon fiber; b) X-ray diffraction of nickel coated carbon fiber |
3.2. Compression Test
The plot of Ultimate compressive strength (UCS) with a variation of short carbon coated fibers in metal matrix composite is shown in the Figure 4(a). It is clear that, as the wt. % of reinforcement increases, the value of ultimate compressive strength also increases. The percentage variation in Ultimate compressive strength (UCS) with variation of short coated carbon fiber is as shown in Figure 4(b). From the data, it is observed that, for the increase of wt. % of reinforcement 0% to 1%, the ultimate compressive strength has increased by 4.47%. Moreover, the UCS has again increased to 8.55% and 10.47% for the increased wt. % from 0% to 2% and 0% to 3% respectively. This significant increase in the ultimate compressive strength is because of hard carbon particle, which is imparting great stability to the matrix. Here, the short coated carbon fibers are present in different orientations and are capable of receiving the compressive stress. Hence from the test it is clear that, the short fibers have got high crushing strength and rigidity than the matrix material. The outcomes of this study are in line with alternate scientists [9, 10]. The increase in the compression strength is a result of the nearness of hard particles, conferring high strength to the composite. This might be because of little measures of fibers at various locations, which can have colossal effect in stress strain conduct. The rigidity and crushing strength of fiber is much higher than that of matrix material consequently the strength increments.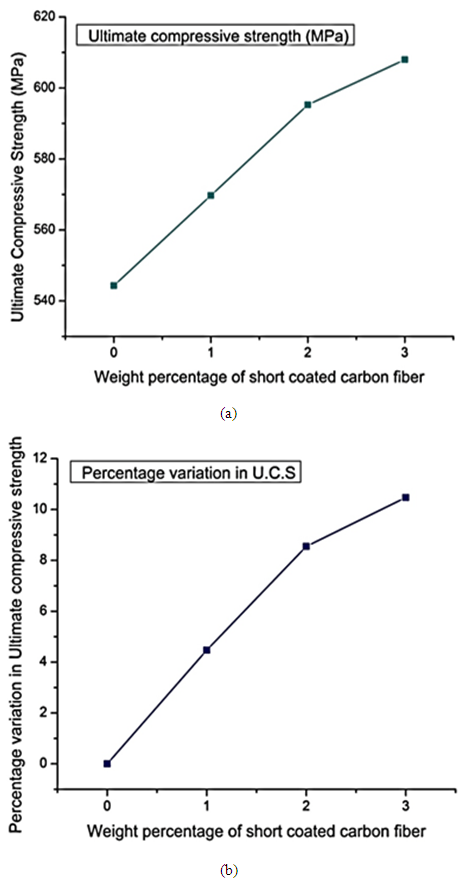 | Figure 4. Variation of a) UCS; b) % variation of UCS, with respect to wt. % of the short carbon fiber |
3.3. Elastic Modulus
The Figure 5 shows the variation of the Young’s modulus value with the increase of wt. % of short coated carbon fiber. Young’s modulus value is increased from 69 to 72 (GPa) which yields about 4% increase for 1% increase of short coated carbon fiber. Similarly, for 2% and 3% increase in wt. % of short coated carbon fiber, the Young’s modulus value has been increased to 74 (GPa) i.e. 6.756% and to 77(GPa) i.e. 10.3896%. This increase in Young’s modulus may be due to the alignment of these short carbon fibers parallel to the axis with minimum segregation in the alloys. McDanels [11] was of the opinion that, the elastic modulus increases with increase in reinforcement content. However, elastic modulus has been found to be independent of the type of reinforcement. There are many micromechanical models available in the literature for the prediction of theoretical value of young’s modulus for composite. In the present investigation two models namely, Neilsen-chen model & computational model have been used for comparison of theoretical value with experimental value as shown in Table 1. The Young’s modulus value predicted theoretically for various % of dispersoid basalt fiber has been superimposed for the sake of comparison. It can be observed that the trend of the theoretical results predicted by adopting micromechanical models by earlier investigators available in the literature is similar to the trend value obtained in this investigation with a percentage error of less than 10%.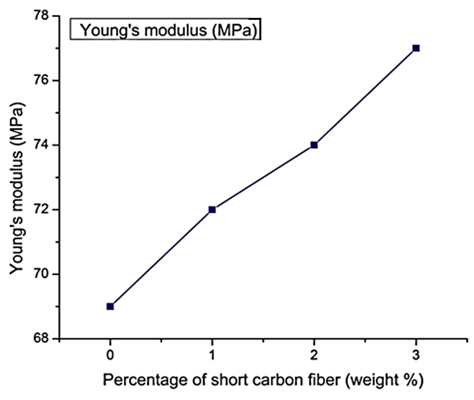 | Figure 5. Variation of Young’s Modulus with respect to wt. % of the short carbon fiber |
Table 1. Comparison of experimental and theoretical values of Young’s Modulus of as cast AA 7075/ short coated carbon fiber metal matrix composite 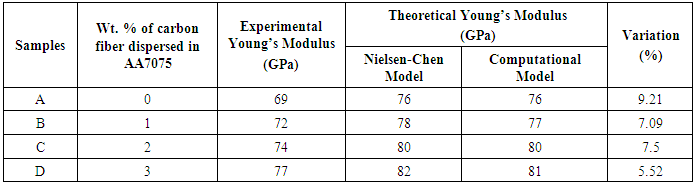 |
| |
|
3.4. Hardness
The Figure 6(a) shows the effect of presence of short coated carbon fiber reinforcement on the hardness of the composite. From the test, it is observed that as the wt. % of the short coated carbon fiber increased, the hardness value also increases. In fact, as the percentage of reinforcement content is raised from 0% to 1 %, the hardness is increased by 9.58%. Similarly, increase from 0% to 2% and 0% to 3% of short coated carbon fiber content has led to an increase in the hardness by 12% and 15.38% respectively and is shown in Figure 6(b). Hence it is clear that, due to the increase in wt. % of reinforcement, composite will have a significantly higher value of hardness than the monolithic alloy to certain level. The reason for increase in hardness number might be the nearness of short coated carbon fiber, which goes about as obstruction to space development. Zhu and Liu [12] observed a comparable improvement in hardness when ZA alloy was reinforced with short alumina fibers. Different specialists have likewise reported that the expansion of hard ceramic particulates or short fibers to metal alloys could prompt enhanced strength, wear resistance and hardness. A comparative impact was seen by Sood et al. [13] for TiC strengthened aluminum composite MMCs.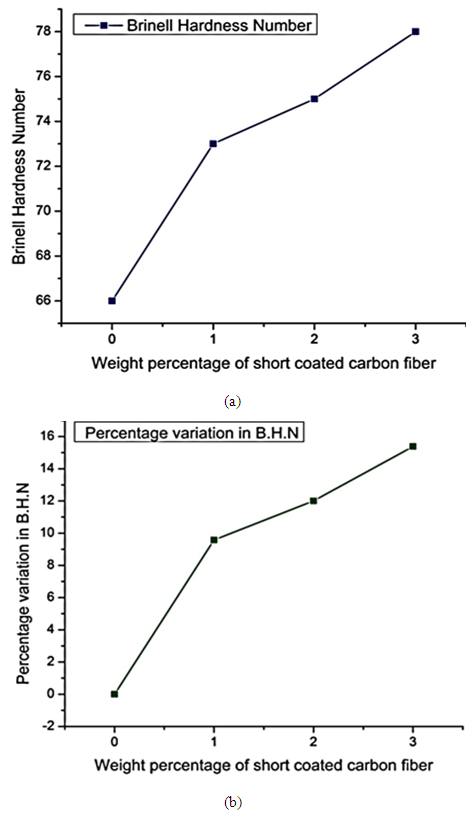 | Figure 6. Variation of a) BHN; b) % variation of BHN, with respect to wt. % of the short carbon fiber |
4. Conclusions
The mechanical properties viz. compressive, Elastic Modulus and Hardness of the AA7075 short coated carbon fiber prepared by Stir casting method are altered by addition of the different wt. % of carbon fiber. The main findings include:1. A nickel content of almost 92% on carbon fibers was obtained through stir casting process.2. As the nickel coated carbon fiber content was increased, a maximum increase of 10.47%, 10.38%, and 15.38% was observed in ultimate compressive strength, Elasticity and hardness respectively.
References
[1] | Colin, M., 2006, Continuous fiber reinforcements for metal-matrix composites. In: ASM Handbook, ASM International, OH, 21, 56–58. |
[2] | Cheng, H.M., Kitahara, A., Akiyama, S., Kobayashi, K., Uchiyama, Y., and Zhou, B.L., 1994, Characteristics of several carbon fiber-reinforced aluminium composites prepared by a hybridization method, Journal of Material Science, 29(16), 4342–4350. |
[3] | Pai, B.C., Pillai, R.M., Satyanarayan, K.G., Sukumaran, K., Pillai, U.T.S., Pillai, S.G.K., and Ravilumar, K.K., 2001, Discontinuously reinforced aluminium alloy matrix composites, Metals Materials and Processes, 13, 255–278. |
[4] | Hashim, J., Looney, L., and Hashmi, M.S.J., 2001, The wettability of SiC particles by molten aluminium alloy, Journal of Material Processing Technology, 119(1-3), 324–328. |
[5] | Ramesh C.S., Keshavamurthy R., and Madhusudhan J., 2014, Fatigue behavior of Ni-P coated Si3N4 reinforced Al6061 Composites, Procedia Materials Science, 6, 1444 -1454. |
[6] | Rams J., Urena A., Escalera M.D., and Sanchez M., 2007, Electroless nickel coated short carbon fibers in aluminium matrix composites, Composites: Part A, 38(2), 566–575. |
[7] | Balasivanandha S., Prabu, Karunamoorthy L., Kathiresan S., and Mohan B., 2006, Influence of stirring speed and stirring time on distribution of particles in cast metal matrix composite, Journal of Material Processing Technology, 171(2), 268–273. |
[8] | Suhas, Quadros J. D., and Vaishak N. L., 2016, Evaluation and characterization of tensile properties of short coated carbon fiber reinforced aluminum 7075 alloy metal matrix composites via liquid stir casting method, Material Science Research India, 13(2), 66-73. |
[9] | Seah, K.H.W., Sharma, S.C., and Ramesh, A., 2000, Mechanical properties of cast aluminium alloy 6061-Albite particulate composites, Proceedings of the Institution of Mechanical Engineers, Part L, 214(1), 1-6. |
[10] | Sharma, S.C., Girish, B.M., Kamath, R., and Satish, B.M., 1999, Fractography, fluidity, and Tensile Properties of Aluminum/Hematite particulate composites, Journal of Materials Engineering and Performance, 8(3), 309-314. |
[11] | McDanels, D.L., 1985, Analysis of stress-strain, fracture, and ductility behavior of Aluminum matrix composites containing discontinuous Basalt short fiber carbide reinforcement, Metallurgical Transactions A, 16(6), 1105-1115. |
[12] | Zhu, H.X., and Liu, S.K., 1993, Mechanical Properties of Squeeze Cast Zinc Alloy Matrix Composites Containing α- Alumina Fibers, Composites, 24(5), 437-442. |
[13] | Sood, J., Tiwari, A.N., and Teredesai, A., 1991, TiC-Reinforced Al Matrix Composites. In: Proceedings of 2nd International Conference on Aluminium INCAL-91, Aluminium Association, Bangalore, 31 July-2 August 1991, 781-785. |