Susilendra Mutalikdesai1, Gururaj Hatti2, Mutturaj Kudal1, Tavanappa Adappanavar1, Vijaykumar N. H.1, Husain S.1
1Department of Mechanical Engineering, Yenepoya Institute of Technology, Moodbidri, India
2Department of Mechanical Engineering, Vishwanathrao Deshpande Rural Institute of Technology, Haliyal, India
Correspondence to: Susilendra Mutalikdesai, Department of Mechanical Engineering, Yenepoya Institute of Technology, Moodbidri, India.
Email: |  |
Copyright © 2017 Scientific & Academic Publishing. All Rights Reserved.
This work is licensed under the Creative Commons Attribution International License (CC BY).
http://creativecommons.org/licenses/by/4.0/

Abstract
The use of polymer composite materials has increased considerably over the last decade. The unique properties of Fiber Reinforced composite materials enable their application in various technological areas such as space, aircraft, marine and automotive. There is lot of research going on, to improve the various properties of composite materials by using different filler materials. In present investigation different fillers such as silica fume, fly ash, quartz powder, and GGBS were used to disperse with matrix material epoxy to prepare epoxy glass composite laminates. Mechanical characterization such as tensile test, flexural test and impact test were carried on prepared laminates. Mechanical characteristics were evaluated for fabricated specimen. Improvement in mechanical properties with addition of fillers to the composite was observed. Highest flexural strength was observed for Fly ash dispersed epoxy glass composite while highest impact strength was observed for GGBS dispersed epoxy glass composite.
Keywords:
GFRP, Handlay up technique, Tensile test, Flexural test, Impact test
Cite this paper: Susilendra Mutalikdesai, Gururaj Hatti, Mutturaj Kudal, Tavanappa Adappanavar, Vijaykumar N. H., Husain S., Influence of Various Filler Materials on Mechanical Characteristics of Epoxy Glass Composites, American Journal of Materials Science, Vol. 7 No. 4, 2017, pp. 99-101. doi: 10.5923/j.materials.20170704.06.
1. Introduction
Fiber reinforced plastics have been employed in manufacturing of various aircraft and spacecraft structural parts because of their particular mechanical and physical properties such as high specific strength and high specific stiffness. [1]. Composite materials are constituted of two phases: the matrix, which is continuous and surrounds the other phase, often called as reinforcing phase [2]. Epoxy resins are widely used as matrix in many fibre reinforced composites; they are a class of thermoset materials of particular interest to structural engineers owing to the fact that they provide a unique balance of chemical and mechanical properties combined with wide processing versatility [3]. Within reinforcing materials, glass fibres are the most frequently used in structural constructions because of their specific strength properties [2].E-glass fiber reinforced epoxy composites filled with varying concentrations of bone and coconut shell powder. The composites were fabricated by hand lay-up technique and the mechanical properties such as ultimate tensile strength, flexural strength, impact strength and hardness of the fabricated composites were tested. From the results it was found that the mechanical properties of the composites increased with the increase in filler content. Composites filled with coconut shell powder exhibited maximum flexural strength; inter laminar shear strength (ILSS), tensile modulus and hardness. Maximum impact strength was achieved by addition of filler of bone powder [4].With the addition of fly-ash in epoxy resin –fly-ash composite the compressive strength has been found to increase with increase in fly ash particles. This increase is attributed to hollowness of fly-ash particles & strong interfacial energy between resin & fly-ash. After reinforcing glass fibre both compressive & impact strength has been increased due to energy absorbed in fibre pull out [5, 6].Glass fibre polymer composites are reinforced with granulated blast furnace slag ball milled to size of 5nm in different weight fractions, i.e. (0%, 5%, 10% and 15%) and fabricated by using hand lay-up technique. These fabricated slabs are cut into required dimensions and the tests for mechanical properties like Tension test, Flexural test, Compression test, Impact test and Hardness test were performed. Tension test, compression test and Flexural test were performed on Computerized Universal Testing Machine (UTM), Impact test was performed for Izod and Charpy specimens and Hardness test was performed on Brinell’s Hardness Testing Machine. From the experimental results obtained, it was noticed that the mechanical properties were enhanced when the blast furnace slag percent was increased [7].The effect of the amount of quartz powder in an epoxy resin matrix was studied by compression testing. Compressive tests near room temperature and at several strain rates were performed on samples with different filler volume fractions. The data show that both the composite Young's modulus and yield stress increase with increasing volume fraction of filler [8].Based on cited literature it was found that using of filler materials has significant influence on various properties of polymer composites. In present work various filler materials were used to study their influence on mechanical characteristics of glass fibre reinforced epoxy composites.
2. Materials and Fabrication
2.1. Materials
Bi directional woven E-glass fibre made of 360 gsm size was employed as reinforcement to fabricated fibre reinforced polymer composites. The properties that enable the use of E-Glass fibres as reinforcement in polymer composites are Low cost. high strength and relatively low density, resistance to heat and non-flammable, chemical resistant, insensitive to moisture and high production rates. Epoxy LY556 was used as matrix material. It possesses good adhesion to other materials, good chemical and environmental resistance, good chemical properties and good insulating properties. Araldite HY951 was used as hardener. In present investigation different fillers used to disperse in epoxy are fly ash, ground granulated blast furnace slag (GGBS), quartz powder, silica fume.
2.2. Fabrication
Hand lay-up technique was adopted to fabricate epoxy glass composites with different filler materials. For present investigation fly ash, GGBS, quartz powder and silica fume powder 4% by weight were dispersed in epoxy resin separately as different sample. After separately dispersing each filler in epoxy LY556 then 10% wt of hardener HY951 was added which initiates cross-linking process, then specimens were cured for 24 hours at room temperature. Glass fibre reinforced epoxy composite with different fillers fabricated by hand layup method.
2.3. Mechanical Characterization
Mechanical characterizations were performed on prepared laminates. Tensile and flexural tests were conducted on the universal testing machine as per ASTM standards ASTM D638 and ASTM D790 respectively. Tensile test is one of the most commonly used mechanical test in which specimen is subjected to gradual loading until it fails or gives fracture. Flexural strength is one of the major mechanical properties of any material. It is found by applying bending load on specimen until it fractures or yielding using with three point flexural test technique. Impact strength is capability of the material to withstand a suddenly applied load or it can also defined as the ability of the material to absorb mechanical energy in the process of deformation and fracture under impact loading. Impact tests were conducted on the impact testing machine according to ASTM D256. Moisture absorption studies were performed according to ASTM D 570-98 standard test method for moisture absorption of plastics. The weights of the samples were taken and then dipped them to normal water. After 24 h, the samples were taken out from the moist environment and all surface moisture was removed with the help of a clean dry cloth or tissue paper. Then the samples were reweighed to the nearest 0.001 mg within 1 min of removing them from the environment chamber. The samples were regularly weighed at 24, 48, 72, 96 hrs. respectively. The moisture absorption was calculated by the weight difference.
3. Results and Discussion
3.1. Tensile Test
By analysing tensile test results for different epoxy glass composites it was observed that there was not significant improvement in tensile strength with dispersion of filler materials. Figure 1 indicates Tensile strength of epoxy glass composite with different fillers. It can be seen clearly that composite with no filler has maximum tensile strength followed by silica fume, GGBS, quartz powder and fly ash.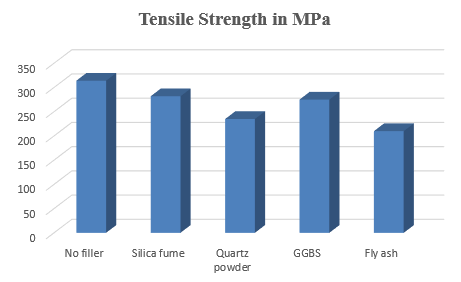 | Figure 1. Tensile Test results |
3.2. Flexural Test
Figure 2 shows results for flexural test. From results it can be clearly seen significant improvement in flexural strength with addition of filler to matrix material. Glass fibre reinforced epoxy composite with flyash given maximum flexural strength while laminate with no filler shown low flexural strength.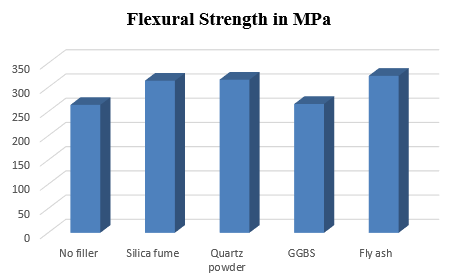 | Figure 2. Flexural Test results |
3.3. Impact Test
Impact test results for different laminates is as shown in Figure 3. After analysing results for impact test it is seen that laminate with GGBS as filler is shown the maximum impact energy per notch length and laminate with quartz as filler filler is shown least impact energy.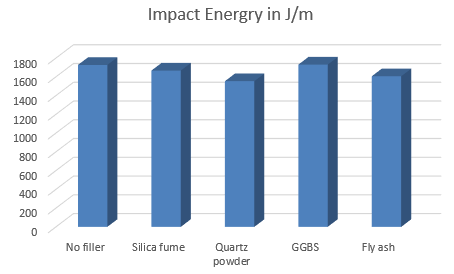 | Figure 3. Impact test results |
3.4. Water Absorption Test
Graphs Figure 4 shows water absorption test results. By analysing graph it can be clearly seen influence filler materials on water absorption resistance property. Fly ash and silica fume filled epoxy glass composites exhibited better water absorption resistance property as compared to other laminate composites.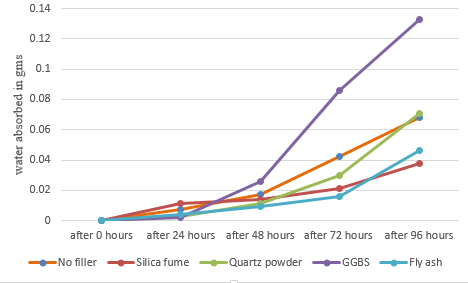 | Figure 4. Water absorption test results |
4. Conclusions
Experimental studies of glass fibre reinforced plastic composites dispersed with 0%wt, 5%wt fly ash, 5%wt silica fume, 5%wt quartz powder, 5%wt GGBS were carried out. Mechanical test such as tensile test, flexural test and impact tests were performed. Based on the experimental results and analysis, the following conclusions were arrived at, tensile tests helped to determine the tensile strengths of different fillers. Tensile strength of laminates with no filler, silica fume, fly ash, quartz powder, and GGBS are 314MPa, 282MPa, 211MPa, 235MPa and 275MPa respectively. Results show that the tensile strength of the material with addition of fillers to the composites are not much appreciable. Flexural strength obtained was maximum for fly ash of 324 MPa followed by quartz powder has 316 MPa, silica fume has 314 MPa, and GGBS is having 266 MPa respectively. Clearly indicating addition of filler improves flexural strength of composite. Impact strength also improved with addition of fillers. GGBS shown better impact strength as compared to other laminates. Fly ash and silica fume filled epoxy glass composites exhibited better resistance to water absorption as compared other laminates.
References
[1] | A.M. Abrao et.al,. Drilling of fiber reinforced plastics: A review, Journal of Materials Processing Technology 186 (2007) 1–7. |
[2] | M.A. Boyle, C.J. Martin, J.D. Neuner 2003, Epoxy resin, in: H. Hansmann (Ed.), Composites Compendium, ASM Handbook FB MVU, Werkstofftechnologien, Kunststofftechnik. |
[3] | S. Jain, D.C.H. Yang 1994, Delamination-free drilling of composite laminates, Trans. ASME J. Eng. Ind. 116 (4) (1994) 475–481. |
[4] | Sudeep Deshpande and T Rangaswamy, Effect of fillers on E-glass/Jute fibre reinforced epoxy composites, Int J Engg Res App, 4(8), 2014, 118-123. |
[5] | Kishore, Kulkarni SM, Sharathchandra S, Sunil D. On the use of an instrumented set-up to characterize the impact behavior of an epoxy system containing varying fly ash content. Polym Test 2002; 21: 763–71. |
[6] | Kulkarni SM, Kishore. Effect of filler–fiber interactions on compressive strength of fly ash and short-fiber epoxy composites. J Appl Polym Sci 2003; 87:836–41. |
[7] | A.V. Pradeep, “Effect of Blast Furnace Slag on Mechanical Properties of Glass Fiber Polymer Composites”, Procedia Materials Science 10, 230 – 237(2015). |
[8] | Gerardo H Rubiolo, Jorge D Marconi, Silvia N Goyanes, “Yield stress of epoxy composites filled with quartz powder”, Polymer International, 51,11, 1290-1294, 2012. |