Susilendra Mutalikdesai, G. Sujaykumar, Amal Raju, C. J. Moses, Jithin Jose, Vishak Lakshmanan
Department of Mechanical Engineering, Yenepoya Institute of Technology, Moodbidri, India
Correspondence to: Susilendra Mutalikdesai, Department of Mechanical Engineering, Yenepoya Institute of Technology, Moodbidri, India.
Email: |  |
Copyright © 2017 Scientific & Academic Publishing. All Rights Reserved.
This work is licensed under the Creative Commons Attribution International License (CC BY).
http://creativecommons.org/licenses/by/4.0/

Abstract
Over the last two three decades composite materials has been used widely in various engineering field. Composite materials possess low weight, corrosion resistance property and specific strength, and due to these facts composite materials are becoming popular among researchers and scientists. Now-a-days, the natural fibers offer the potential to act as a reinforcing material for composites alternative to the use of glass fiber, carbon fiber and other man-made fibers. In present work hybrid composites of Epoxy/basalt fiber/flax fibers were prepared by Hand-layup technique. Mechanical characterization of prepared hybrid composites were carried out. Mechanical results improved mechanical properties for hybrid composites. Mechanical properties increased with increased in basalt fibre content in the flax/basalt fibre hybrid epoxy composites.
Keywords:
Hybrid composite, Natural fibres, Hand lay-up technique, Tensile test, Flexural test, Impact test
Cite this paper: Susilendra Mutalikdesai, G. Sujaykumar, Amal Raju, C. J. Moses, Jithin Jose, Vishak Lakshmanan, Mechanical Characterization of Epoxy/ Basalt Fiber/ Flax Fiber Hybrid Composites, American Journal of Materials Science, Vol. 7 No. 4, 2017, pp. 91-94. doi: 10.5923/j.materials.20170704.04.
1. Introduction
A composite is a material made by combining two or more dissimilar materials in such a way that the resultant material is endowed with properties superior to any of its parental ones. Fiber-reinforced composites, owing to their superior properties, are usually applied in different fields like defence, aerospace, engineering applications, sports goods, etc. Now a days a lot of research going on natural fiber composites and they have gained increasing interest due to their eco-friendly properties. Natural fibers such as jute, sisal, silk and coir are inexpensive, abundant and renewable, lightweight, with low density, high toughness, and biodegradable. Natural fibres such as jute, flax, basalt fibres have the potential to be used as a replacement for traditional reinforcement materials in composites for applications which requires high strength to weight ratio and further weight reduction.A huge changeover was reported on the usage of natural fibers all over the world for the production of composites [1-3]. Moreover, natural fibers can be a suitable comparator to synthetic fibers, such as glass, in many ecological characteristics but not in respect of mechanical strength. However, significant improvements in the strength of polymer composites can be achieved while reinforcing natural fibers under different conditions, i.e. by using various chemical treatments on the fibers and hybridization with synthetic fibers. Still, the need for these treatments was identified as a lack of strength in these composites compared to other synthetic composites, whereas, weaving of natural fibers in different orientations makes the composites stronger and comparable to those of synthetic fibers [4, 5].Basalt fibres are continuously extruded from a high temperature melt (around 1500°C) of selected basalt stones (volcanic, over-ground, effusive rocks saturated with 45– 52% silica) [6]. In particular, their similar chemical structure to glass, even though their density is slightly higher (2.8 g/cm3 compared to 2.54 g/cm3 of glass), eases such a replacement. Also, the chemical stability of the basalt fibres is higher than that of glass fibres, especially in an acidic environment [7]. This characteristic allows basalt fibres to more effectively binding to sizing agents, such as organ silanes, resulting in the need for a reduced amount of these chemicals with respect to glass fibres [8]. Even more than glass, basalt fibres can be used in a wide range of temperatures, from 200°C to 600°C [9].Flax, one of the types of natural fibres with a good mechanical characteristics, has been widely used to produce composites. Unlike artificial fibres, flax fibres are not continuous fibres but they have a composite like hierarchically organized structure. Their macroscopic properties emerge from their micro and nano-structural level. The morphology of the fibres shows similarities and composites produced using them show similar properties. The industrially important flax fibres are placed as fibre bundles in the outer surface of the plant stem. The bundles (technical fibres) are between 60 and 140 cm long and their diameter ranges from 40 to 80 µm. The flax stem contains 20-50 bundles in their cross section. Each bundle consists of 10-40 spindle shaped single fibres of 1-12 cm length and 15-30 µm diameters.Hybrid composites are more advanced composites as compared to conventional FRP composites. Hybrids can have more than one reinforcing phase and a single matrix phase or single reinforcing phase with multiple matrix phases or multiple reinforcing and multiple matrix phases. They have better flexibility as compared to other fiber reinforced composites. Normally it contains a high modulus fiber with low modulus fiber. The high- modulus fiber provides the stiffness and load bearing qualities, whereas the low-modulus fiber makes the composite more damage tolerant and keeps the material cost low. The mechanical properties of a hybrid composite can be varied by changing volume ratio and stacking sequence of different plies.Comparing life cycle environmental performance of natural fiber composites with glass fiber reinforced composites and found that natural fiber composites are environmentally superior in the specific applications studied. Natural fiber composites are likely to be environmentally superior to glass fiber composites in most cases for the following reasons: natural fiber production has lower environmental impacts compared to glass fiber production, natural fiber composites have higher fiber content for equivalent performance, reducing more polluting base polymer content, the light- weight natural fiber composites improve fuel efficiency and reduce emissions in the use phase of the component, especially in auto applications and end of life incineration of natural fibers results in recovered energy and carbon credits [10]. Natural fibers can be used as a “filler” fiber, replacing the glass as well as the resin in a filament wound component. The main problem of plant based fibres has been that it is difficult to introduce a large quantity of plant based fibre like jute or flax fibres into the polymer matrix composites because these fibers, unlike glass fibers, soak up large amount of resin. This problem is partly can be overcome by “hybridsing” with other fibers [11].From literature it is found a lot of research going on natural fibre and hybrid composites in last few years. In present work hybrid fibre composite with flax and basalt fibres as reinforcement and epoxy LY556 as matrix material is fabricated and Mechanical properties were investigated.
2. Materials, Fabrication and Mechanical Characterization
2.1. Materials
2.1.1. Epoxy
In present work epoxy LY556 is used as matrix material to fabricate hybrid fibre epoxy composites. Epoxy resins are the most commonly used thermoset plastic in polymer matrix composites. Epoxy resins are a family of thermoset plastic materials which do not give off reaction products when they cure and so have low cure shrinkage. They also have good adhesion to other materials, good chemical and environmental resistance, good chemical properties and good insulating properties. Hardener used for present investigation for initiating gel formation is Araldite HY951.
2.1.2. Basalt Fibre
In the present investigation Basalt fibre chosen as one of the reinforcement. Basalt fabric of size 360GSM is used in present work. Basalt fibre is mineral fibre a type of natural fibre. Basalt fiber is a cost effective and offers excellent properties as compared to glass fibers. The major advantages of basalt fibre reinforced composites include high specific strength, good chemical properties, biodegradability, and non-abrasive qualities to name a few.
2.1.3. Flax Fibre
Flax fibre selected as another reinforcement material along with basalt fibre to fabricate hybrid fibre polymer composites. Flax fibre is plant based fibre. Bi-directional woven flax fibre matt was selected for present work.
2.2. Fabrication
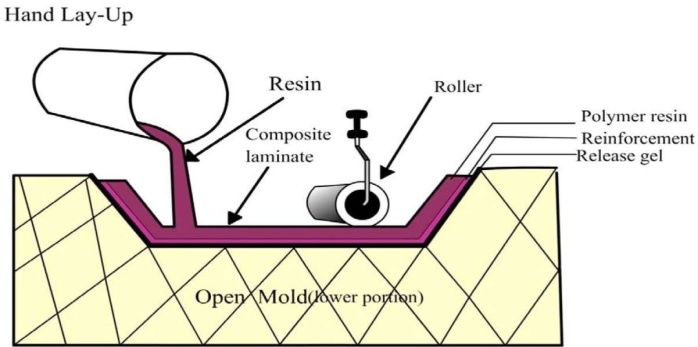 | Figure 1. Hand Lay-up Method |
The fabrications of composite slab are carried out by conventional hand layup technique. Cutting the Flax fiber and basalt fibre fabric for dimensions of 250*250 mm and arrange fibres in desired sequence to prepare hybrid composite. Adding 10% hardener of hardener which will initiate cross linking reacting and gel formation will begin. Then spread the mixture on the mould, then place first ply of fiber, then second ply will be kept and resin will be spread and this process will be continued till required thickness is achieved. After the completion of laminate apply the load on the laminate and kept it for 24 hours for curing. After the curing, Specimens are prepared for each laminate to conduct different testing according standards.Table 1. Designation of composites and its composition 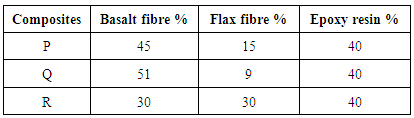 |
| |
|
2.3. Mechanical Characterization
Mechanical properties of basalt and flax fibre hybrid composites were performed on prepared laminates. Tensile and flexural tests were conducted on the universal testing machine according ASTM standards ASTM D638 and ASTM D790 respectively. Tensile test is the most commonly used mechanical test in which specimen is subjected to gradual loading until it breaks/fails. Flexural strength is one of the major mechanical characteristics of any material. Flexural strength is an ability of the composite material to withstand bending forces applied perpendicular to its longitudinal axis until it fractures or starts yielding permanently using with three point flexural test technique. Impact strength is ability of the material to withstand a suddenly applied load or it can also defined as the ability of the material to absorb mechanical energy in the process of deformation and fracture under impact loading. According ASTM D256 impact tests were conducted on the impact testing machine. Figure 2 shows specimens for different mechanical testing.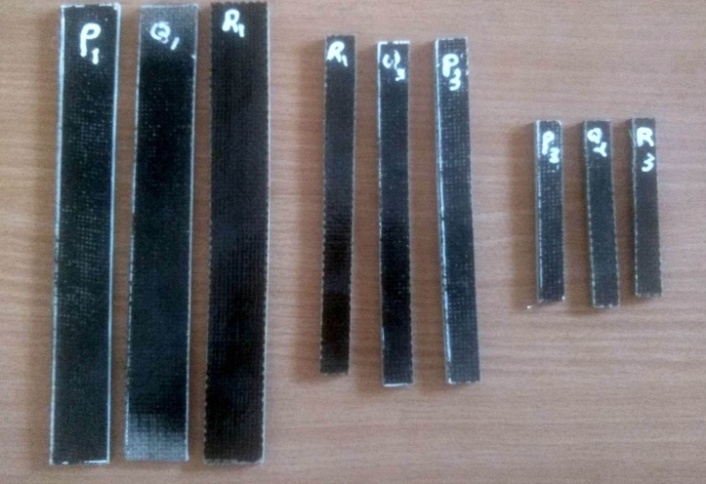 | Figure 2. Hybrid composite specimen P, Q and R for Tensile, Flexural and impact test |
3. Results and Discussion
Mechanical properties such as tensile strength, flexural strength and impact strength were analysed for Flax/Basalt hybrid fibre epoxy composites and their results discussed as follows.
3.1. Tensile Test
Tensile test results for hybrid composites are as shown in Figure 3. By analyzing results it is observed that composite Q with 51% of basalt 9% of flax and 40% of epoxy resin is exhibited good tensile strength 253MPa compared to others. And also by observing pattern it can clearly see with increase in basalt fibre percentage in composite tensile strength was improved significantly.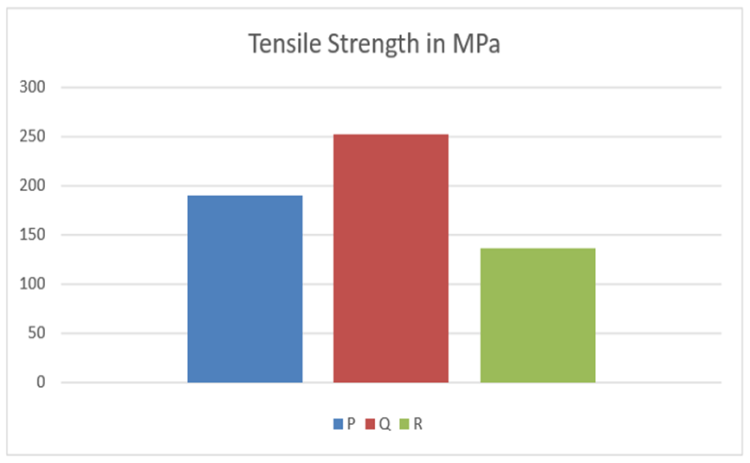 | Figure 3. Tensile Test results |
3.2. Flexural Test
From flexural test results conducted on all hybrid composites graph as in Figure 4 is plotted. By analyzing results obtained it can be seen that composite Q has exhibited good Flexural strength 263MPa followed by Composite P with 257 MPa and specimen R having low flexural strength of value 142.5 MPa.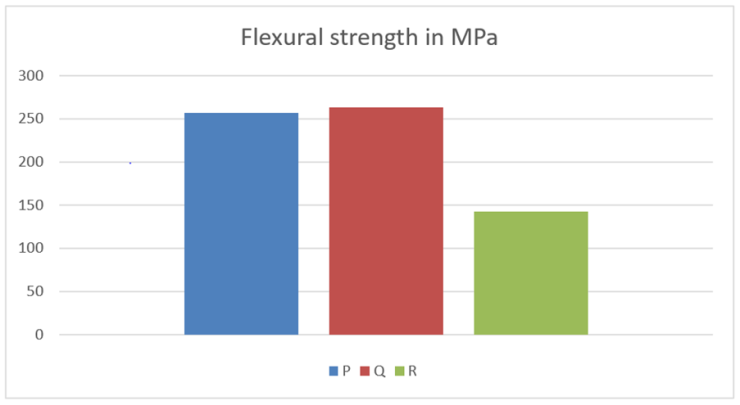 | Figure 4. Flexural Test Results |
3.3. Impact Test
From Impact test results on all hybrid composites above graph in Figure 5 is plotted. From test and graph analysis it is observed that composite Q with 51% of basalt 9% of flax and 40% of epoxy resin has exhibited good Impact strength 94.52KJ/m2 compared to others.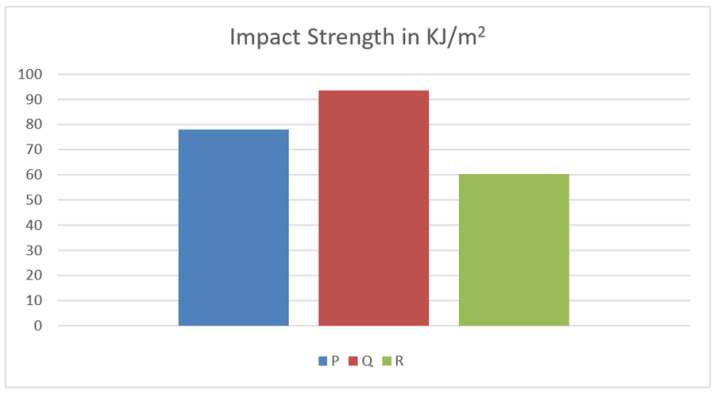 | Figure 5. Impact Test Results |
4. Conclusions
Based on the experimental results and analysis, the following conclusions were arrived at: Hybrid composite with varying fibre ply with different combination of flax and basalt fibre and epoxy as matrix fabricated by using hand lay-up technique. Tensile strength test. By analyzing tensile test results it is seen that laminate Q with 51% Basalt fibre 9% flax fibre shown highest strength followed by laminate P with 45% basalt fibre and 15% flax fibre and least strength shown by laminate R having 30% basalt fibre and 30% flax fibre. Flexural strength obtained was maximum for laminate Q followed by laminate P and R respectively. Impact test results also exhibited similar result pattern with maximum impact strength obtained is for laminate Q with basalt fibre 51% and flax fibre 9%. From mechanical characterization it is seen that with increase in basalt fibre in flax basalt fibre hybrid composite there is significant improvement in the mechanical properties.
References
[1] | Maya Jacob John, Sabu Thomas, “Biofibers and biocomposites”. Carbohydr. Polym 2008; 71(3):343-64. |
[2] | Uma Devi L, Bhagawan S S, Sabu Thomas, “Mechanical properties of pineapple leaf fiber-reinforced polyester composites”. J. Appl. Polym. Sci 1997; 64(9):1739-48. |
[3] | Murali Mohan Rao K, Mohana Rao K, Ratna Prasad A V, “Fabrication and testing of natural fiber composites: vakka, sisal, bamboo and banana”. Mater. Des2010; 31(1): 508-813. |
[4] | Dittenber D B, Ganga Rao HV S, “Critical review of recent publications on use of natural composites in infrastructure”. Composites Part A 2012; 43(8): 1419-29. |
[5] | Faruk O, Bledzki A K, Fink H P, Sain M. “Biocomposites reinforced with natural fibers”. Progr. Polymer. Sci 2012; 37(11):1552-96. |
[6] | Czigány T, Vad JPK. Basalt fiber as reinforcement of polymer composites. Period Polytech Mech Eng 2005; 49:3–14. |
[7] | Wei B, Cao H, Song S. Environmental resistance and mechanical performance of basalt and glass fibers. Mater Sci Eng A 2010; 527:4708–15. |
[8] | Ivashchenko E. Sizing and finishing agents for basalt and glass fibers. Theor Found Chem Eng 2009; 43:511–6. |
[9] | Deak T, Czigany T. Chemical composition and mechanical properties of basalt and glass fibers: a comparison. Text Res J 2009; 79:645–51. |
[10] | S.V. Joshi, L.T. Drzal, A.K. Mohanty, S. Arora “The mechanical properties of vinylester resin matrix composites reinforced with alkali-treated jute fibres” Part A 32 (2001) 119–127. |
[11] | A. N. Shah and S. C. Lakkad, Mechanical Properties of Jute-Reinforced Plastics, Fibre Science and Technology 15 (1981) 41 46.A. |