L. Laxmana Naik1, 2, K. Gopalakrishna2, B. Yogesha1
1Department of Mechanical Engineering, Malnad College of Engineering, Hassan, Karnataka, India
2Jain University, Bangalore, Karnataka, India
Correspondence to: B. Yogesha, Department of Mechanical Engineering, Malnad College of Engineering, Hassan, Karnataka, India.
Email: |  |
Copyright © 2016 Scientific & Academic Publishing. All Rights Reserved.
This work is licensed under the Creative Commons Attribution International License (CC BY).
http://creativecommons.org/licenses/by/4.0/

Abstract
This work deals with the effect of sisal-glass fabric reinforced polymer composites fabricated by vacuum bagging method. Each laminate consists of five plies of fabrics and resin mixture with 3 mm thickness as per different layering designation. The water absorption tests were performed on immersing specimens into normal water. Specimen preparation and water absorption studies carried out as per ASTM standards. The present work reveals that the mixture of glass with sisal decreases the maximum water absorption.
Keywords:
Sisal fiber, Glass fiber, Vacuum bag, Epoxy, Polyester
Cite this paper: L. Laxmana Naik, K. Gopalakrishna, B. Yogesha, Physical and Water Absorption Behaviour of Sisal – Glass Fiber Reinforced Polymer based Composites, American Journal of Materials Science, Vol. 6 No. 4, 2016, pp. 91-94. doi: 10.5923/j.materials.20160604.02.
1. Introduction
The developments of new materials are on the anvil and are growing day by day. Natural fiber composites became more attractive due to their high specific strength, lightweight and biodegradability. Natural fibers like sisal, jute, hemp, flax have been often used as reinforcements in polymer matrices. Natural fibers are available in abundance and inexpensive compared to other relatively advanced man-made fibers.The mechanical properties of a natural fiber-reinforced composite depend on many parameters, such as fiber strength, modulus, fiber length and orientation, in addition to the fiber-matrix interfacial bond strength. A good interfacial bond is required for effective stress transfer from the matrix to the fiber whereby maximum utilization of the fiber strength in the composite is achieved [1]. Modification to the fiber also improves resistance to moisture induced degradation of the interface and the composite properties [2]. In addition, factors like processing conditions/techniques have significant influence on the mechanical properties of fiber reinforced composites [3]. Mechanical properties of natural fibers, especially flax, hemp, jute and sisal, are very good and may compete with glass fiber in specific strength and modulus [4, 5]. A number of investigations have been conducted on several types of natural fibers such as kenaf, hemp, flax, bamboo, and jute to study the effect of these fibers on the mechanical properties of composite materials [6, 7]. Mansur and Aziz [8] studied bamboo-mesh reinforced cement composites, and found that this reinforcing material could enhance the ductility and toughness of the cement matrix, and increase significantly its tensile, flexural, and impact strengths. On the other hand, jute fabric-reinforced polyester composites were tested for the evaluation of mechanical properties and compared with wood composite [9]. Jawaid et al. [10] studied the mechanical behaviour of hybrid composites based on jute and oil palm fiber. It has been found that the use of hybrid system was effective in increasing the tensile and dynamic mechanical properties of the oil palm-epoxy composite because of enhanced fiber/matrix interface bonding. Verma et al. [11] examined the mechanical properties of glass/jute hybrid composites. The jute fabrics were modified by treatment with different chemicals. It has been observed that titanate treatment of jute fabric results in enhanced performance characteristics and mechanical properties of hybrid composites. Ashmed et al. [12] investigated the elastic properties and notch sensitivity of untreated woven jute and jute-glass fabric reinforced polyester hybrid composites, analytically and experimentally. The jute composites exhibited higher notch sensitivity than jute–glass hybrid composites.
2. Materials Used
Plain woven sisal fabrics were supplied by Sri Lakshmi Group Exports & Imports, Guntur, Andhra Pradesh, India. E-glass fabrics in plain woven form were supplied by Suntech Fiber Pvt. Ltd., Bangalore, India. The epoxy resin identified as: Araldite LY556 (Manufacturer: Huntsman) of density 1.2 gm/cc and hardener resin identified as: K6 (Manufacturer: atul Ltd) of density 0.98 gm/cc were supplied by Chemicote Engineers, Bangalore, India. For the preparation of matrix system, the epoxy and hardener were mixed in a ratio of 10:1. Isophthalic Polyester Resin, accelerator (Cobalt Napthanate) and catalyst (Methy Ethyl Ketone Peroxide i.e., MEKP) are also supplied from Chemicote Engineers, Bangalore, India. For the preparation of matrix system, the resin, accelerator and the catalyst were mixed in a ratio of 10:1. Table 1. Basic parameters of sisal and E-glass fabrics 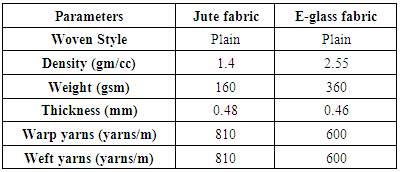 |
| |
|
3. Laminate Fabrication
The composite laminates were prepared 300x300x3 mm3 using the method of vacuum bag. In this process, a pressure of 80 bars is applied to fabrics laminated via a vacuum bag which is duly sealed with mastic sealant. In the preparation of composite materials such as laminated designation, the fabric layer is placed one by one on the flat mold and then the resin is applied after each layer followed by tissue hand lay-up method. Then place the release fabric and breathable fabric on the laminated layers have restrictions on the amount of resin that can be pulled out of the basket. Later, the composite is then cured under vacuum at room temperature for 24 hrs. Thereafter, the laminates were then removed from the mold and post-autoclaved at 80°C for 5 hours before cutting into dimensions required specimen. Each laminate consists of five layers laminated fabric as designation as shown in Table 2.Table 2. Laminate Designation 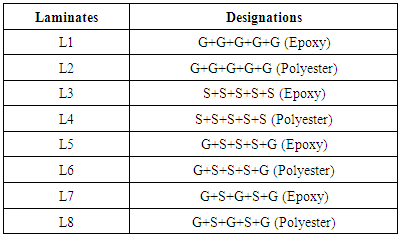 |
| |
|
Table 3 show that the weight fraction of composite laminates for desired dimension i.e., 300x300x3 mm3. wf is the weight of fiber (Weight of glass (wg) is 36±2 gm and weight of sisal (ws) is 15±1 gm for an each fabric layer dimension of 300x300 mm2) and wm is the weight of matrix. where, Wf is the fiber weight fraction (Wg is the glass weight fraction and Ws is the sisal weight fraction), Wm is the matrix weight fraction.Weight fraction is calculated by using Eqs. (1) [13]: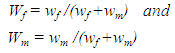 | (1) |
Table 3. Composite laminates weight and weight fraction 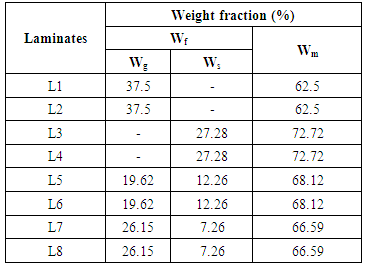 |
| |
|
4. Experimentation
4.1. Density and Void Fraction
The physical properties of a composite material system can be as important as mechanical properties in assessing suitability for a particular application. Density plays a key role for designing an engineering component or deciding the application of a material particularly where weight is an important factor. Thus, it is necessary to determine the density of the composites fabricated for this study. The theoretical density (ρct) of composites in terms of weight fraction is calculated as per equation (2).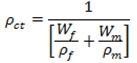 | (2) |
where, W and ρ designates the weight fraction and density, respectively. The suffix f, m and ct represent the fiber, matrix and the composite materials, respectively. The actual density (ρac) of the composites is determined by simple water immersion technique. By using the theoretical and experimental density of composites, the volume fraction of voids (Vv) in the composites is determined using the following equation (3) [14]: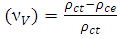 | (3) |
4.2. Water Absorption Test
Moisture absorption studies were performed according to ASTM D 570-98 (28x30x3 mm3) standard test method for moisture absorption of plastics [14]. The tests specimens of composites are shown in Fig. 1. The weights of the samples were taken and then dipped them to normal water as shown in Fig. 2. After 24 h, the samples were taken out from the moist environment and all surface moisture was removed with the help of a clean dry cloth or tissue paper. Then the samples were reweighed to the nearest 0.001 mg within 1 min of removing them from the environment chamber. The samples were regularly weighed at 24, 48, 72, 96,120, 144, 168, 192 hrs respectively. The moisture absorption was calculated by the weight difference. The weight gain in percentage of the samples was measured at regular time intervals of time by using the following equation: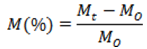 | (4) |
Where Mt is the weight of specimen at a given immersion time and Mo is the oven-dried weight.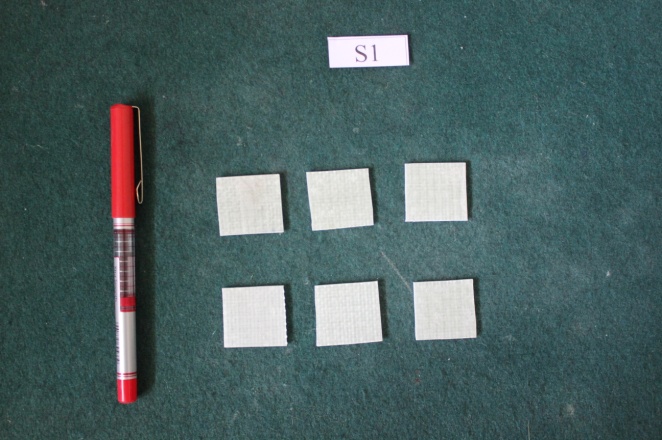 | Figure 1. Water absorption test specimens |
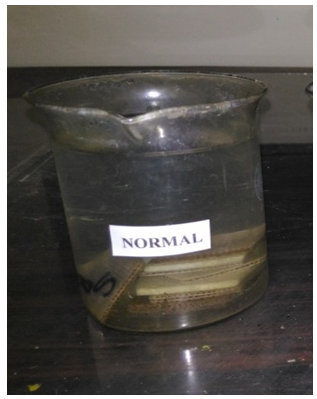 | Figure 2. Test specimens immersed in normal water |
5. Results and Discussion
5.1. Density and Void Fraction
The theoretical density, experimental density and the corresponding void fraction of the composites is presented in Table 4. It is to be noted that the values of theoretical density are not equal to the experimental density of the prepared composites. This difference in the theoretical and experimental density of the composites is the measure of voids or pores present in it. The presence of voids in composites significantly affects its mechanical properties directly or indirectly. The natural fibers consist of lumens in its cellular structure which acts as void. It means such fiber carries these voids naturally.Table 4. Comparison between experimental and theoretical density of composites 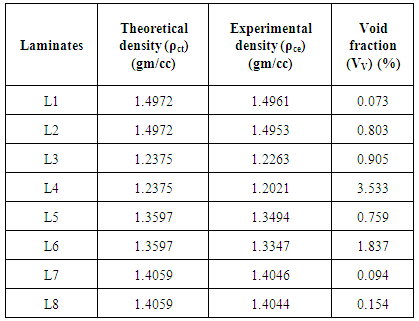 |
| |
|
5.2. Water Absorption Test
Water absorption test is very important to determine the water absorptivity of the water absorption of the material. The percentage of weight gain in various composites with time duration is shown in Figure 3. It is observed that with increase in weight fraction of glass fiber the water absorption gradually increases irrespective of laminating sequences. This behaviour was expected because the water absorption of these composites is mainly due to the presence of sisal fibers. There are three main reasons in the composite because of which water can reside in composite. Those are the lumen, the cell wall and the gaps between fiber and resin in the case of weak interface adhesion is found. The maximum water absorption obtains at L3 and L4 laminates. As far as effect of hybridization on the water absorption of composites is concerned there is much influence is observed.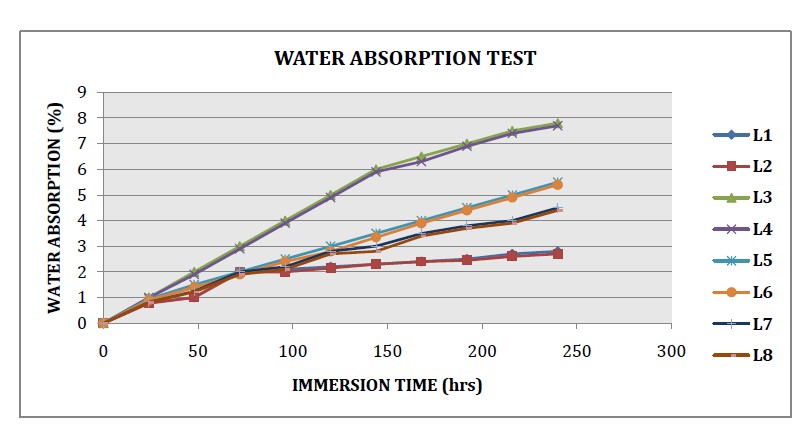 | Figure 3. Effect of immersion time on water absorption properties of composites |
6. Conclusions
A multilayered hybrid composite has been fabricated successfully by reinforcing low cost, light weight, eco-friendly sisal fibres with glass fiber, using an epoxy and polyester resin matrix. In the case of hybrid fiber composites, polyester matrix leads to improved performance than epoxy resin. The maximum water absorption obtains at L3 and L4 laminates. As far as effect of hybridization on the water absorption of composites is concerned there is much influence is observed. It is suggested that these hybrid composites can be used as an alternative material for synthetic fiber reinforced polymer composites, especially for medium load structural applications, as they significantly reduce the problems related to environmental concerns.
References
[1] | Karnani R., Krishnan M and Narayan R., Biofiber-reinforced polypropylene composites., Polymer Engineering and Science, 37 (2), 1997, pp. 476-483. |
[2] | Joseph K., Mattoso L H C., Toledo R D., Thomas S., Carvalho L H de., Pothen L., Kala S and James B., Natural fiber reinforced thermoplastic composites., In Natural Polymers and Agrofibers Composites., ed. E. Frollini, A.L. Leao and L H C Mattoso., 159-201, 2000. |
[3] | George J., Sreekala M S and Thomas S., A review on interface modification and characterization of natural fiber reinforced plastic composites., Polymer Engineering and Science, 41(9), 2001, pp. 1471-1485. |
[4] | Van de Velde K and Kiekens P., Thermal degradation of flax: The determination of kinetic parameters with thermogravimetric analysis., Journal of Applied Polymer Science, 83 (12), 2002, pp. 2634-2643. |
[5] | Frederick T W and Norman W., Natural fibers plastics and composites., Kluwer Academic Publishers, New York, 2004. |
[6] | Satyanarayana K G., Sukumaran K., Mukherjee P S., Pavithran C and Pillai S G K., Natural Fiber-Polymer Composites”, Journal of Cement and Concrete Composites., 12(2), 1990, pp. 117-136. |
[7] | Satyanarayana K G., Sukumaran K, Kulkarni A G., Pillai S G K and Rohatgi P K., Fabrication and Properties of Natural Fiber-Reinforced Polyester Composites., Journal of Composites, 17(4), 1986, pp. 329-333. |
[8] | Mansur M A and Aziz M A., Study of Bamboo-Mesh Reinforced Cement Composites., International Journal of Cement Composites and Lightweight Concrete., 5(3), 1983, pp. 165–171. |
[9] | Gowda T M., Naidu A C B and Chhaya R., Some Mechanical Properties of Untreated Jute Fabric-Reinforced Polyester Composites., Journal of Composites Part A: Applied Science and Manufacturing, 30(3), 1999, pp. 277- 284. |
[10] | Jawaid M., Khalil H P S A., Hassan A., Dungani R and Hadiyane A., Effect of jute fiber loading on tensile and dynamic mechanical properties of oil palm epoxy composites. Composites, 45(1), 2013, pp. 619–624. |
[11] | Varma I K., Anantha Krishnan S R and Krishnamoorthy S., Composites of glass/modified jute fabric and unsaturated polyester resin., Composites, 20 (4), 1989, pp. 383-388. |
[12] | Ahmed K.S., Vijayarangan S and Naidu A C B., Elastic properties, Notched strength and fracture criterion in unsaturated woven jute-glass fabric reinforced polyester hybrid composite., Materials and Design, 28(8), 2007. pp. 2287-2294. |
[13] | Robert M Jones., Mechanics of Composite Materials., McGraw-HILL Book Company, 1975. |
[14] | ASTM D2734-94. Standard methods for void content of reinforced plastics. |
[15] | ASTM D570-98. Standard methods for water absorption of plastics. |