Thamir A. Jumah , Maryam B. Abood
Department of Physics, College of Science, University of Al-Nahrain, Iraq
Correspondence to: Maryam B. Abood , Department of Physics, College of Science, University of Al-Nahrain, Iraq.
Email: |  |
Copyright © 2016 Scientific & Academic Publishing. All Rights Reserved.
This work is licensed under the Creative Commons Attribution International License (CC BY).
http://creativecommons.org/licenses/by/4.0/

Abstract
This work investigates the joining between dissimilar materials by using active filler metal paste. Brazing technique was chosen because it is versatile, fast and economical. Butt and interlocking designs were used for joining the assemblies. High purity of silver, copper and titanium powders with different concentrations were used to prepared a paste mixture. The wettability has been achieved between the filler paste and base partners; where the young (contact) angle of pure titanium on the both stainless steel and graphite was found 38°C and 67°C respectively. Then filler paste with different concentrations were placed in between assemblies of graphite and stainless steel as a sandwich form. A steel fixture was used to hold the assemblies and applied some pressure on a assembly to be joined. The vacuum furnace of pressure 10-2 torr was used to investigate the brazing process. Nitrogen gas was pumped into tube furnace at a temperature 500°C for releasing oxygen. Bonding process was performed at different temperatures (850, 900, 950 and 1000)°C with holding vacuum furnace at 10-2 torr. Maximum tensile strength obtained was 15Mpa at the intermediate layer filler - graphite where the filler composed of (75%Ti +25%Ag) by using interlocking design. The new structure phases are found at the intermediate layer compared with base assembly materials. These new phases were enhanced the reliable joint as indicates by XRD and SEM techniques.
Keywords:
Filler brazing, Graphite bonded metal, Brazing, Joining of dissimilar materials, Tensile tests
Cite this paper: Thamir A. Jumah , Maryam B. Abood , Evaluation of the Intermediate Layer of Graphite Bonded Metal, American Journal of Materials Science, Vol. 6 No. 2, 2016, pp. 58-66. doi: 10.5923/j.materials.20160602.03.
1. Introduction
Brazing is a technique of joining two similar or dissimilar materials pieces together by heating them and by using a non-ferrous filler metal having its melting point above 450°C but below the melting points of metals to be brazed [1, 2]. Brazing generally offers the reliable joint strength if the fundamental problem of achieving wetting can be overcome. Carbon and graphite are among the most difficult materials to wet with molten metal [3, 4]. There are several parameters which consider the fundamentals of brazing such as braze joint design, surface preparation, thermal expansion, capi lary action and wettability should be studied [3-5]. Oxides layers and surface contaminants can impede the wetting, spreading and flow of liquid braze filler metals or alloys and must be removed for successful brazing [5]. The purpose of cleaning the surface of base material to increase of the capillary action thus increases the wettability of filler metals on base pieces to be joined. Capillary flow is the dominant brazing mechanism, provided that both faying surfaces are wetted by the molten filler alloy. Furthermore, the joint must be properly spaced to enable the capillary action to be efficient [6]. The objective of this research is to knowledge more information about the effects of filler paste on the wetting and hence boning strength between the pieces to be joined.
2. Experimental Part
A stainless steel rod grade 410 was prepared as a circular disk with diameter 2.5 cm and thickness 0.5 cm. The second part is graphite which was prepared into cubic form of dimension (1*1*1)cm3. High purity powder metals include copper (Cu) titanium (Ti) and silver (Ag) were mixed carefully in different ratios concentration to prepare an active filler paste as listed in Table 1 and 2. Thermal analysis was performed on the active filler alloy for determine the melting point and endo - exothermic property of material under test. In order to obtain the suitable surfaces of the partner to be joined. The stainless steel was subjected and conducted by the mechanical and chemical cleaning processes. Firstly, metallographic papers of grades 800, 1000 and 1200 were used to achieve grinding process and followed polishing by wet cloth. The second step of cleaning performed was chemically process by immersing the stainless steel in thinner for 15 minutes and followed immersing in acetone solution for 10 minutes to remove any adherent hydrocarbon contaminates materials [7]. An atmospheric furnace setting on 450°C was used for carry out the cleaning of graphite. Butt and interlocking designs were used to attempt the bonding behaviour of the joint. Many sets of assemblies were prepared to investigate the wetting and bonding processes as listed in Table 3. Vacuum tube furnace of pressure 10-2 torr was setting at different brazing temperatures according to the temperature - time schedule shown in (Figure 1) to a achieve the brazing process on the assemblies. Starting by pumping nitrogen gas in order to release remain oxygen in the tube furnace. Wetting and bonding behaviour had been attempted by placing some filler paste (copper and silver, titanium and silver with different concentration) on each surfaces of stainless steel and graphite pieces. Steel fixture was fabricated used for holding and applied some pressure on the assembly. Different furnace temperature had been used 850, 900, 950 and 1000°C and held the temperature for 15 min socking time. To examine the joint bonding strength, tensile stress was applied on the joint. Fractured zones were analyzed by using XRD technique, optical and scanning microscopes.Table 1. Represents the active filler paste (Titanium, silver) with different concentrations  |
| |
|
Table 2. Represents the active filler paste (Copper, silver) with different concentrations 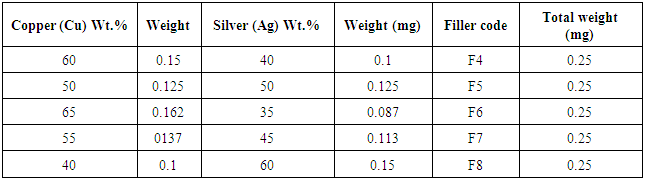 |
| |
|
Table 3. Illustrate the number and dimensions of specimens of St.St and G for wetting and bonding 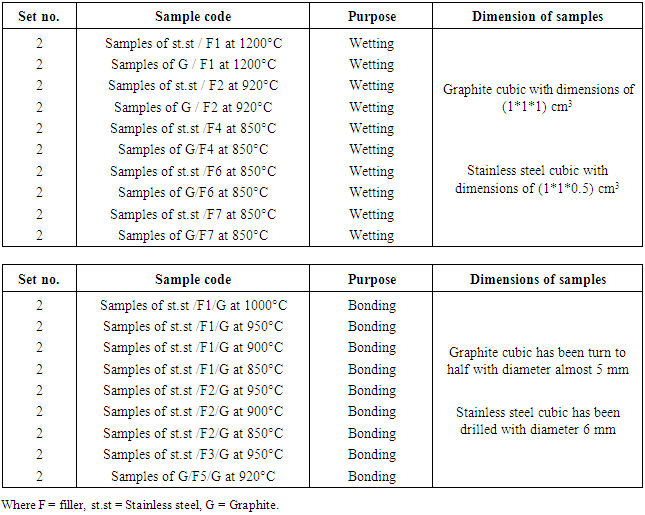 |
| |
|
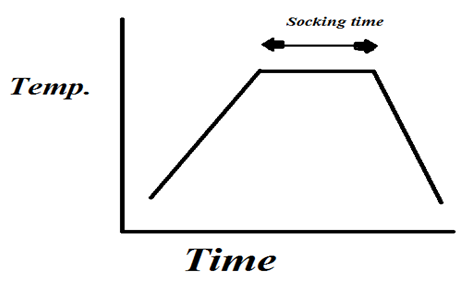 | Figure 1. Temperature - time schedule |
3. Results and Discussion
Many experiments of wetting and spreading have been achieved in tube vacuum furnace under pressure of 10-2 torr at different temperatures. The filler paste of copper - sliver with different concentration uncapable to wet graphite surface as noticed in (Figure 2). This result is agreement with the researcher [6] but disagree with another researcher [8] the later used (Ni- Cr- P- Cu) filler foil alloy to join the graphite with copper surfaces. While due to some of the assemblies joints were separated at the stainless steel - filler when the assembly cooled to the room temperature. This phenomena is appeared where the filler paste consist of Cu - Ag in different concentration. This results may be happened due to mismatch in thermal expansion coefficients between the pieces [5]. In other hand, good wettability was achieved of filler paste contains some titanium in silver matrix with different concentration. In case of pure titanium paste best wetting was obtained on the both surfaces of graphite and stainless steel shown in (Figure 3). The contact angle of Ti on graphite is about (67°) while (38°) on the stainless steel. The young (contact) angle was measured by transfer the assembly image of two dimension into three dimension by means a suitable computer program, then the contact angle was measured directly by protector bevel between the drop tangential and the x-axis as shown in (Figure 4). Many experiments were performed to examine the effects of silver and titanium ratios in the mixture of prepared filler to respect of the contact angle and bond strength. The tensile strength of the braze joint increased rapdily as Ti content ratio increased as demonstration in (Figure 5). On the other hand, the tensile strength of braze joint increase slightly with increasing Ag content as demonstration in (Figure 6). As increasing the tensile strength between the pieces be joined together, its mean the contact angles of active filler paste on the pieces surfaces should be reduced at the minimum values as illustrated in (Figures 7, 8). One can conclude the increases of titanium in the active filler will be enhanced the contact angle and bonding strength. This results are confirmed by other research [3].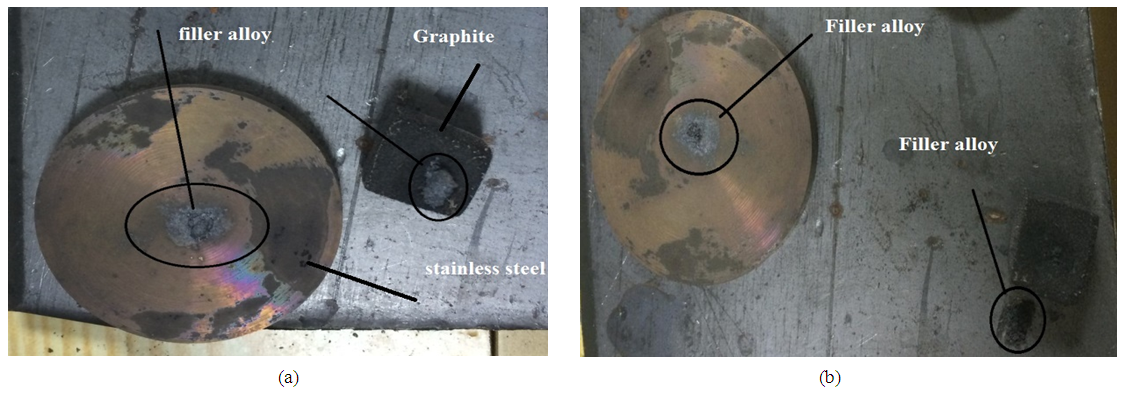 | Figure 2. Illustrate the wettability of filler metal of copper on the graphite and stainless steel |
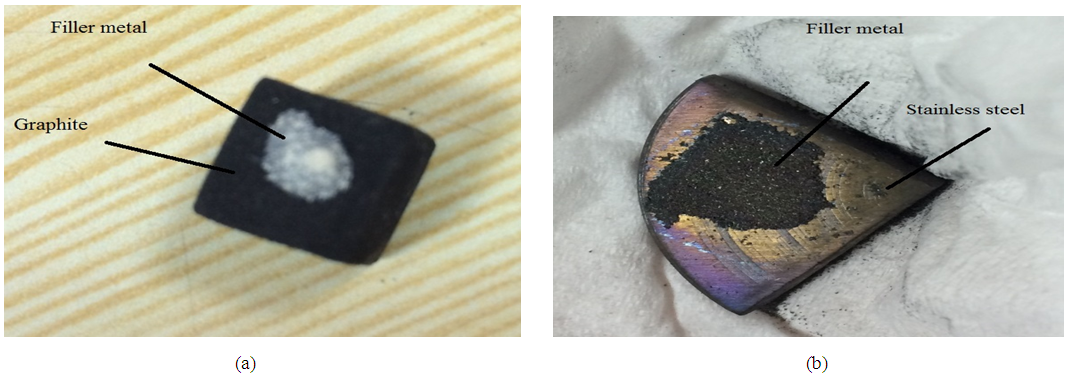 | Figure 3. The wettability of titanium on both graphite and stainless steel |
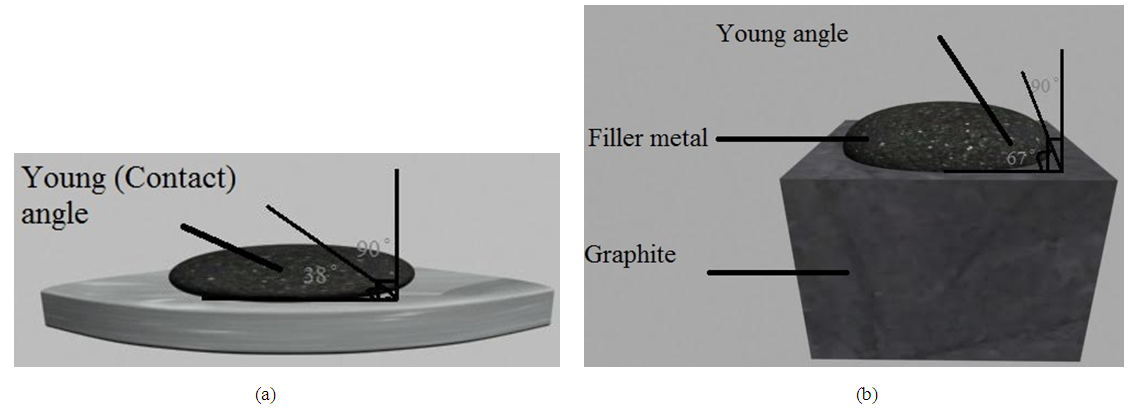 | Figure 4. Illustrate the contact angle of wettability of filler paste metal (titanium) on (a) stainless steel (b) graphite |
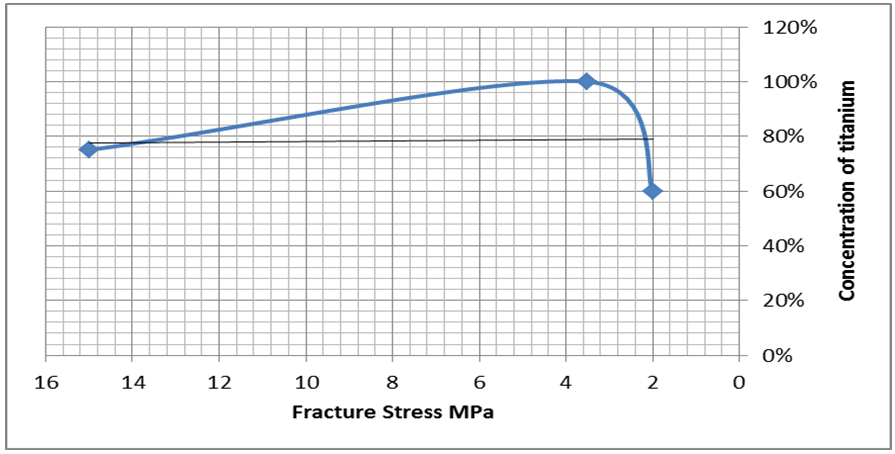 | Figure 5. Illustrate the schematic of relation between the concentration of titanium against fracture stress |
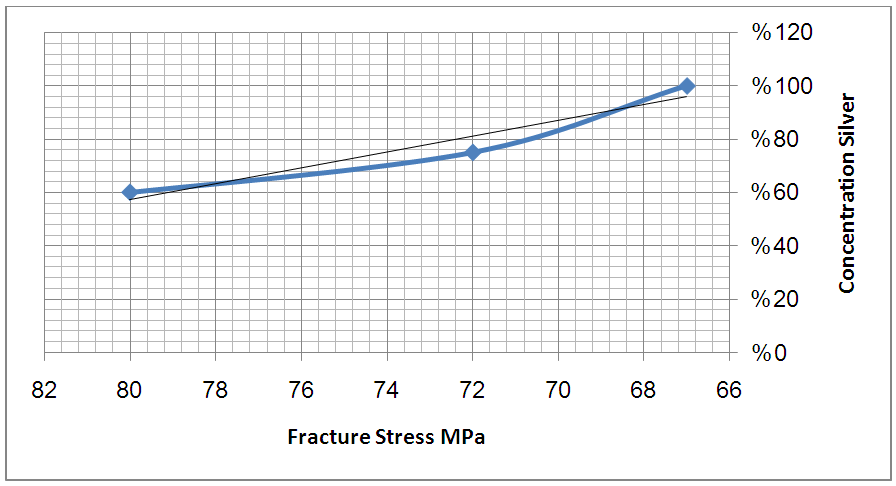 | Figure 6. Illustrate the schematic of relation between the concentration of Silver against fracture stress |
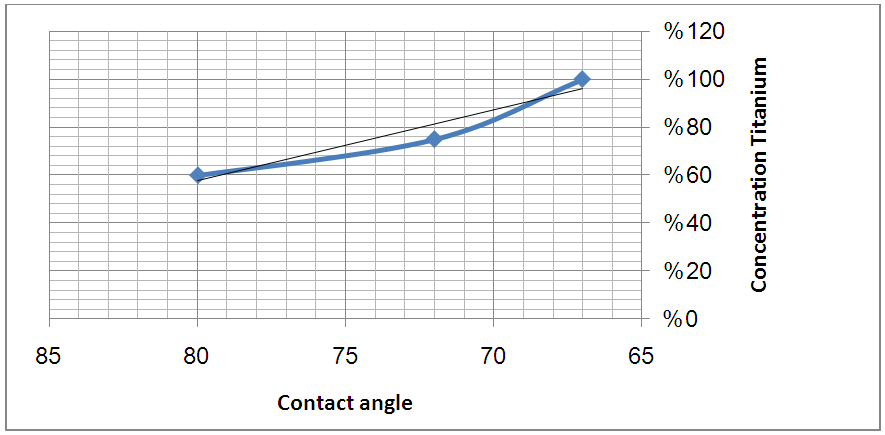 | Figure 7. Illustrate the schematic of relation between the concentration of titanium against contact angle for graphite |
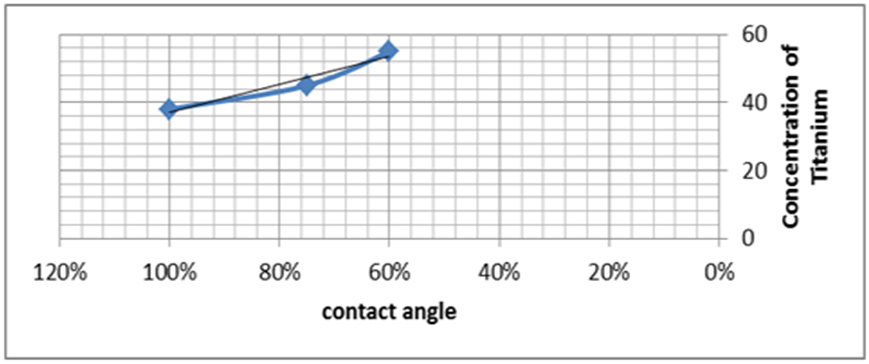 | Figure 8. Illustrate the schematic of relation between the concentration of titanium against contact angle for stainless steel |
The bond strength of joint between stainless steel and graphite given 15 MPa when the filler involved 75wt% Ti and 25wt% Ag. The results listed in Table 4. reveal that when increases ratio of titanium element in the filler will be increased both wettability and bonding strength. It was found that the maximum bond strengths related to the reactivity of the constituent elements with both surfaces of graphite and stainless steel, and that the concentration of Ti in the filler enhanced the joint strength by which the Ti element most markedly affected wetting behavior especially when used the butt-lab (interlocking) design as shown in (Figure 9).Table 4. The bonding strength relative to type of active filler 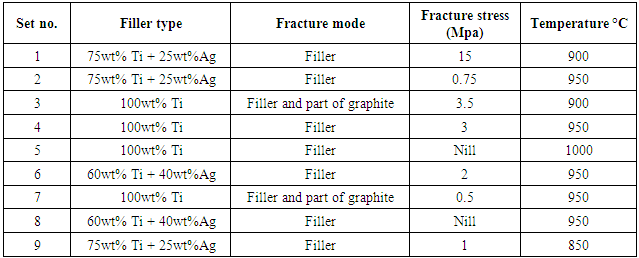 |
| |
|
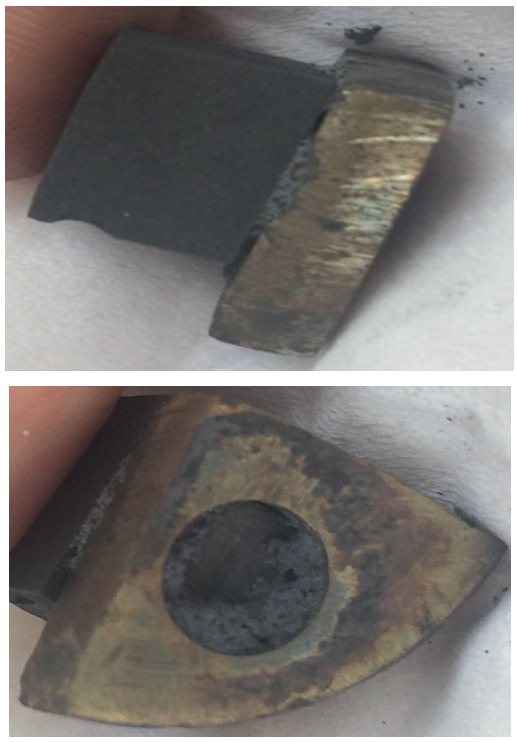 | Figure 9. Interlocking braze design graphite into stainless steel |
Two main regions are cleared on the top view surfaces of both stainless steel and graphite as shown in the (Figures 10, 11), the first region is enriched by active filler of pure titanium as shown in the white color. The second region is nearly free of active filler as shown in dark region. This results indicates that the active filler could not ability to wet the surfaces completely, and hence poor bonding strength between the partners is expected.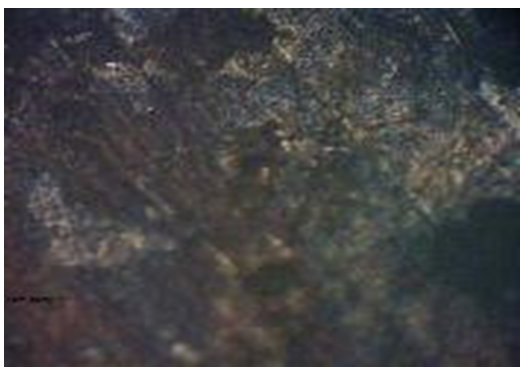 | Figure 10. Optical microscopy image for wettability of filler paste (titanium) on stainless steel (x10) |
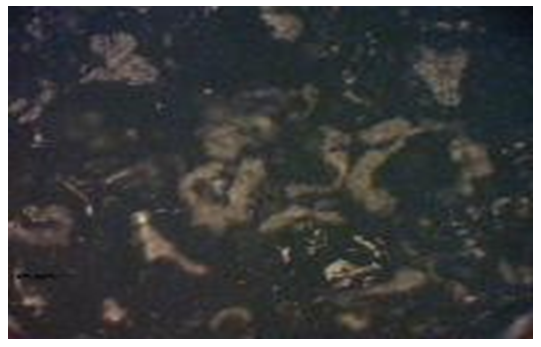 | Figure 11. Optical microscopy image for wettability of filler paste (titanium) on graphite (x 10) |
On the graphite surface with some adherent titanium is clearly noticed at the right side of micrographic illustrated in (Figure 12- a) while the left side of the same micrograph seem to be free of the adherent filler.(Figure 12-b) reveal of the lamella of adherent filler on the graphite surface, due to this adherent filler is maybe contributed in bonding mechanism where the electrons occupies the valance bond in the metal filler and stainless steel will be joint together in order to compose orbital (may be ionic or covalent bonds). (Figure 12-c) involved the bright spots which consist of titanium filler on the graphite substrate, while more texture of titanium filler is clearly noticed as illustrate in (Figure 13-a). The regular distribution of active filler titanium on the graphite surface will be gives an indicate about the good bonding between the partners. The micrograph illustrates in (Figure 13–b) showed the fractured surfaces; one can noticed there are many dark regions have been built on the active filler, this regions due to graphite fracture mode and indicates to obtain a good bonding between titanium (filler) and graphite surface.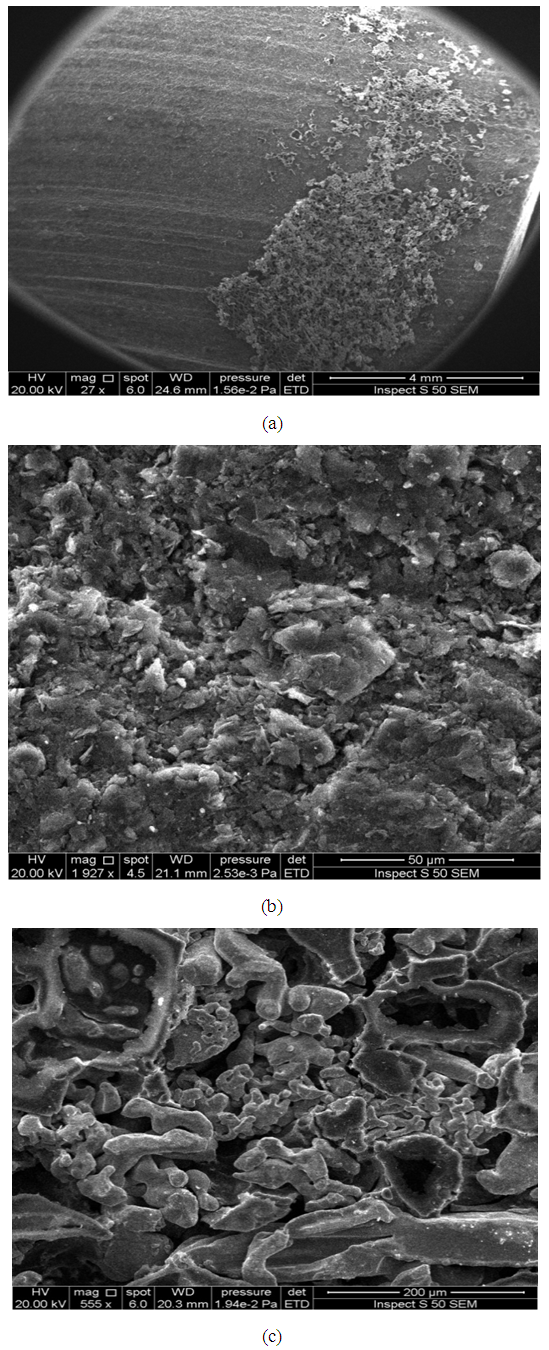 | Figure 12. The scanning electron microscopy for surface of graphite after bonding with titanium filler paste |
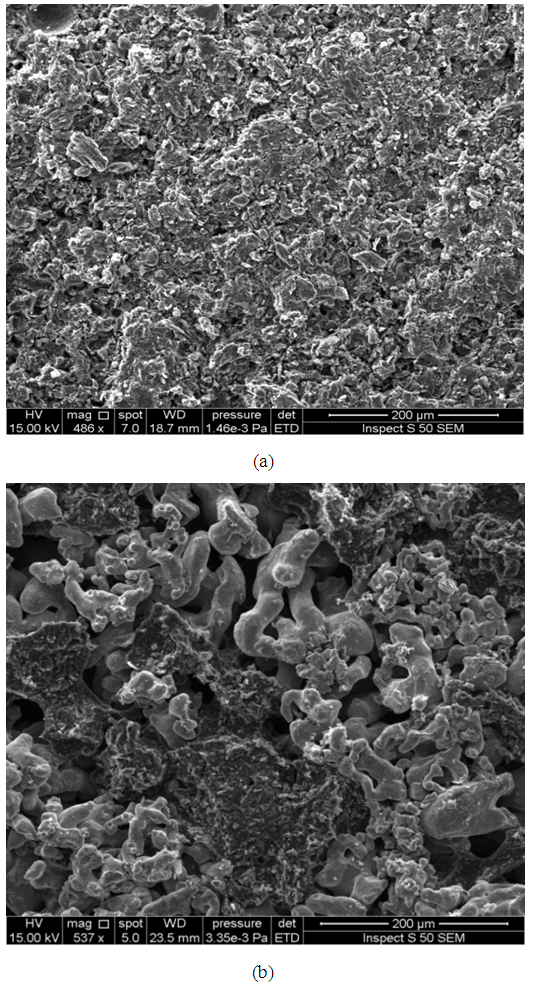 | Figure 13. SEM image for surface of (a) stainless steel (b) graphite after bonding with titanium filler paste |
(Figure 14) represent the elemental analysis of active filler by EDX technique. This pattern revealed the main and additives element composed the interlayer region between the partners.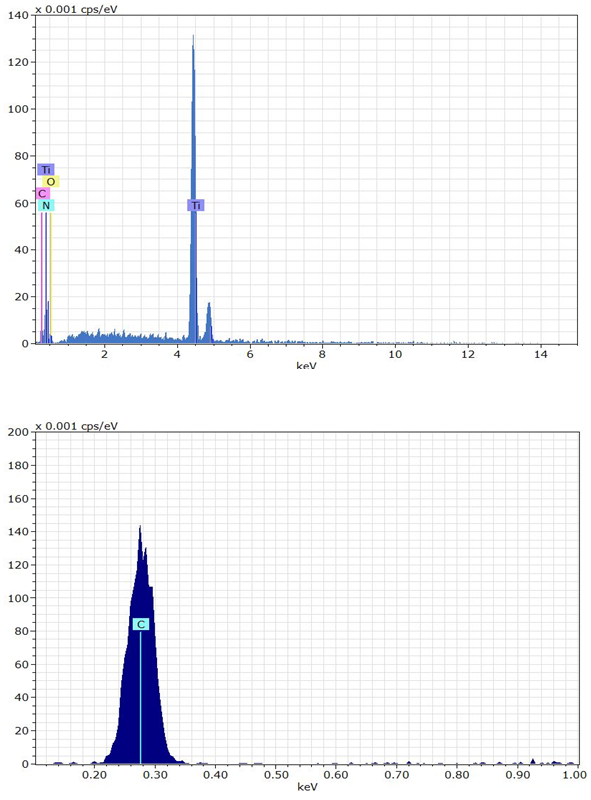 | Figure 14. The energy dispersive x-ray for the surface of graphite after bonding |
The chart of XRD technique showed more information about the structure of intermediate layer graphite - stainless steel. From these charts shown in (Figures 15, 16) one can noticed new structural phases such ((O20P4Ti5, O5STi and CrO9P3), (TiO2 and Ag3O4) which are established compared with the base pieces. This new structural phases at the intermediate layer was contributed to enhance bonding graphite - stainless steel. The intensity of each new phases pointed to the concentrations of that new phase in an intermediate layer. The values of 2 theta and miller indices of new phases are listed in Table 5. The obtained results and tested are agreements with some researchers [2, 4, 10].Table 5. Illustrate the miller indices and 2 theta of phases 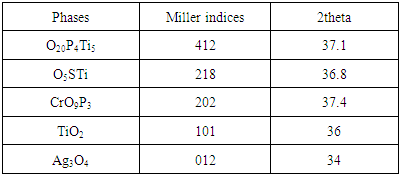 |
| |
|
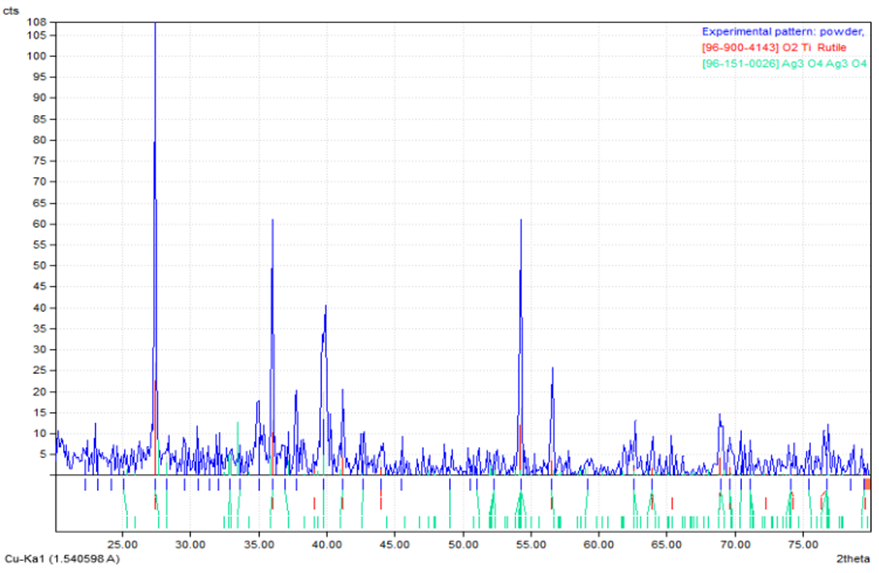 | Figure 15. X-ray diffraction for the fracture surfaces of joint consist stainless steel and Ti-Ag filler |
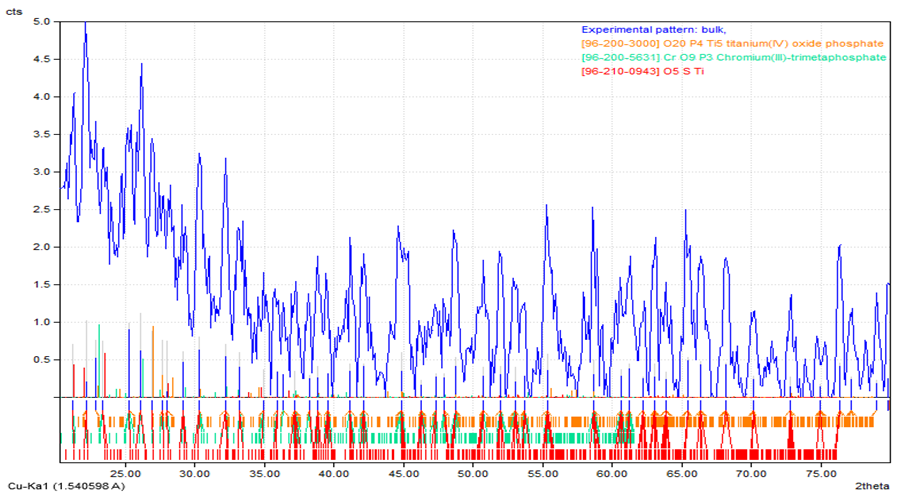 | Figure 16. X -ray diffraction for stainless steel with using Ti-Ag filler metal |
4. Conclusions
1. As the value of young's angles between the filler and partner surfaces decreases down of 90, its means the wettability and hence bonding strength increased.2. The small value of contact angle of titanium filler metal indicated to good wettability on the surface of stainless steel and graphite.3.The joint bonding strength was increased as concentration of titanium increased in filler paste where the Maximum tensile strength was obtained with filler metal (75%Ti +25%Ag) was 15Mpa.4. The diffusivity of titanium into stainless steel and graphite surfaces composed new phases and hence gives efficient wetting and bonding strength due to the new phases.5. The good bonding between stainless steel – graphite encouraged to use this assembly in the field of refractory industries and space rocks field.
References
[1] | J. p. Kaushish," Manufacturing Processes", 2nd edition, page 616, by phl learnin private limited, New Delhi, Isbn- 978-81-203-4082-4, 2010. |
[2] | Jie Zhang, Tianpeng Wang, Chunfeng Liu, Yanming He, "Effect of Brazing Temperatuure on Micrstructure and Mechanical Properties of Graphite/Copper Joints", materials Science & Engineering A 594, pp 26-31, (2014). |
[3] | Kimiaki Nagatsuka, Yoshihisa Sechi, Yoshinari Miyamoto, Kazuhiro Nakata, "Characteristics of Dissimilar Laser – Brazed Joints of isitropic Graphite to WC-Co Alloy, materials Science & Engineering, B177, pp 520-523, (2012). |
[4] | Bo Chen, Huaping Xiong, Yaoyong Cheng, Wei Mao and Shibiao Wu, "Microstructure and Property of AlN Joint Brazed withAu- Pd- Co- Ni- V Brazing Filler", Journal of Materials Science & Technology, 31(10):1034-8, Oct (2015). |
[5] | Stella Crosara Lopes, Valéria Oliveira Pagnano, João Manuel Domingos de Almeida Rollo , Mônica Barbosa Leal and Osvaldo Luiz Bezzon," Correlation between metal-ceramic bond strength and coefficient of linear thermal expansion difference", J appl Oral Sci, vol.17 , no.2, pp 122-8, Issn 1678-7765, (2009). |
[6] | Fadhil A. Hashim, jalal A. Yousef and Raad K. salem , " The Brazing of Graphite / Graphite by Using Cu – Ti Active Filler Alloy", Journal of university of Thi-qar, Vol.4, NO.2, Issn 66291818, p.p 1-8, (2008). |
[7] | Rain N., "Chemical Cleaning of Oxided Kover" J.Sci. Inst., Vol 36, pp 479, (1959). |
[8] | Zhang J, Wang T, Liu C and He Y "Effect of brazing temperature on microstructure and mechanical proper ties of graphite/copper joints", Materials Scienceand Engineering, 594, p.p 26-31 (2014). |
[9] | Tian XY, Feng JC, Shi JM, Li HW and Zhang LX, " Brazing of ZrB 2–SiC–C ceramic and GH99 super alloy to form reticular seam with low residual stress", Ceramics International, 41(1):145-53, (2015). |
[10] | Yu WY, Liu SH, Liu XY, Liu MP and Shi WG, "Interface reaction in ultrasonic vibration-assisted brazing of aluminum to graphite using Sn–Ag–Ti solder foil", Journal of Materials Processing Technology, 221, 285-90, Jul (2015). |