Thamir A. Jumah , Mohammed I. Hashim
Department of Physics, College of Science, University of Al-Nahrain, Iraq
Correspondence to: Mohammed I. Hashim , Department of Physics, College of Science, University of Al-Nahrain, Iraq.
Email: |  |
Copyright © 2016 Scientific & Academic Publishing. All Rights Reserved.
This work is licensed under the Creative Commons Attribution International License (CC BY).
http://creativecommons.org/licenses/by/4.0/

Abstract
Glass to metal joining dealing with oxides growth on the surface of experiments alloys. This mechanism enables joining glass-alloy at a temperature sufficiently 700°C. Borosilicate glass was crushed into sufficient particle size of powdered glass which considered a bonding filler. Good wettability of powdered glass was obtained when its particle size was in between 0.063mm and 0.075mm at the furnace temperature of 700°C under atmospheric air. Maximum fractured stress of monel alloy-borosilicate glass joint is 2 Mpa at the interface region of filler-glass. Fractured surfaces were investigated by the OM, SEM and XRD techniques. It was found a new constituent phases from Fe oxides consists at the intermediate layer. This new phases were enhanced the joint strength. The joint strength of glass bonded alloy was reduced due to the bubbles growth at the intermediate layer.
Keywords:
Dissimilar Material, Thermal Expansion, Wettability, Metal Oxidation, Oxides Growth
Cite this paper: Thamir A. Jumah , Mohammed I. Hashim , Investigation of Fracture and Surface Analysis of Joined Interface Glass-Metal, American Journal of Materials Science, Vol. 6 No. 2, 2016, pp. 49-57. doi: 10.5923/j.materials.20160602.02.
1. Introduction
In general, bonding between dissimilar materials like glass to metal considered an active job in many fields of industry, especially in the vacuum technology. In the same time the joint between dissimilar materials considered a challenge in the field of joining but can obtainable using different technologies. One of the major reasons or needs for joining is to permit dissimilar materials to be used in a complex structure or assembly, creating so-called ‘‘hybrid structures’’ (i.e., structures that, as a result of being composed of more than one material, offer properties, performance, or other attributes not attainable in any individual material). Dissimilar materials enable the achievement of function where design requirements call for diverse and, often, divergent properties, manufacturability, or aesthetics unobtainable in single materials. Dissimilarmaterials often enable the attainment of high structural efficiency in several ways [1, 2]. They do this first by minimizing weight by using the lowest density material with the appropriate strength (i.e., highest specific strength) for strength critical designs, or modulus or stiffness (i.e., highest specific modulus or stiffness) for stiffness-critical designs, or other properties critical to a design, in each area of the assembly or structure [1-4]. Generally joining a metal to a glass or a metal to a ceramic, the fundamental structures and properties are much different, so joining becomes much more difficult. According to this real the problems are most severe when the joining is to be most intimate (i.e., when there is to be actual physical or material continuity from one material or joint element to another). The compatibility of chemical, physical, and mechanical properties is important during the actual process of attempting to fabricate the joint as well as during the operation of the joint in duty. For adhesive bonding, as long as the adhesive keeps the incompatible materials from intimate contact with one another, and provided the adhesive is compatible with each and every material involved in the joint, everything should be fine. If physical properties are drastically different, the same thing applies. Achieving successful joints between dissimilar materials requires several verifying factors such agreement in thermal expansion, oxide growth, joint design and a suitable furnace, a sound understanding of the inherent nature of the materials to be joined and of the various joining options and their means of achieving bonding [1-6]. The fundamentals that need attention when joining surfaces are surface roughness and surface contamination. When two surfaces are brought into contact, the true area of contact is less than the apparent area of contact owing to inherent surface roughness and the nonplanarityon an atomic scale of any surface. This inherent roughness is overcome deformation, diffusion of surfaces (direct bonding), or infiltration of bonding filler between the two surfaces (indirect bonding). [3]In this work, many requirements should have achievement and securing information about an efficient oxide growth of metals, and hence an efficient joint strength can obtainable.
2. Experimental Part
Borosilicate glass was choose as a major partner to be joined. Borosilicate was available corning glass number 7052 designated by ASTM F105 [8]. Borosilicate powdered glass also selected as an active filler in which be joined between glass to metal in this investigation. Stainless steel grade316,304 and monel alloys were choose as a third partner to be joined with glass. Stainless steel and monel alloys are a commercially available. A borosilicate glass tube of diameter 2 cm with length 2cm was prepared as shown in fig. (1). Grinding process was achieved to obtain a flat edge. Decontamination processes were performed to remove the hydro carbonate material such oil and grease by immersing the glass tube and alloy pieces in ethanol alcohol then in acetone and finally immersed in distilled water and followed kept the specimens in the desiccator until to be used. Borosilicate powdered glass was obtained by crushing a clean glass in a ball mill machine into different particle sizes among (0.038mm-0.075mm) as shown in fig. (2). The powdered glass was sieved to obtain a suitable particle size, for this purpose sieves of (0.038mm-0.063mm-0.075mm) were used. Powdered glass was decontaminated initially degreased in alcohol and then in acetone followed by washing in distilled water. For drying, the glass powder was lied in an oven at 150- 200°C for 15 minutes. Stainless steel grade 316, 304and monel alloys were selected to be joined. The dimension of each type alloy was (3*3*0.2) cm3 cut from a strip as shown in fig. (2.3).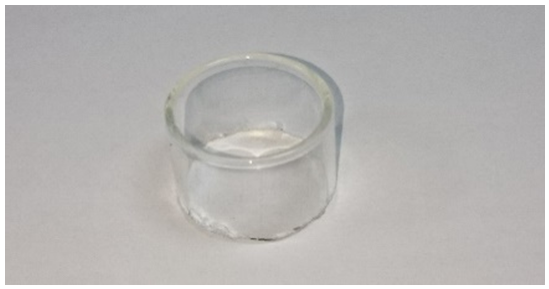 | Figure 1. Tube of Borosilicate Glass |
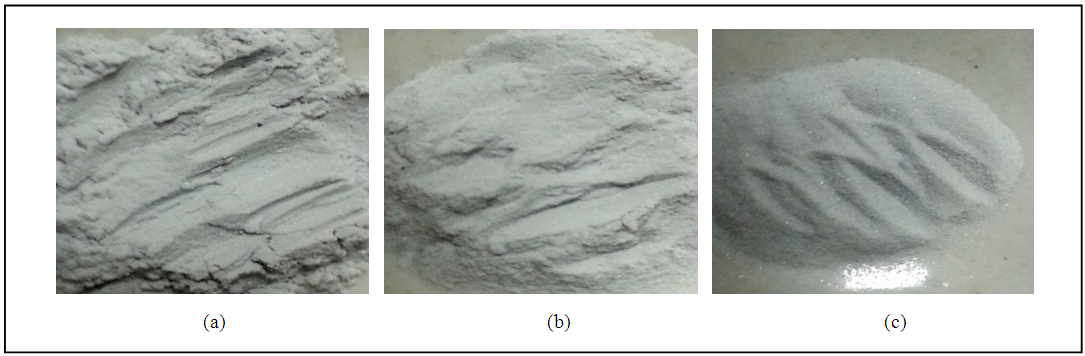 | Figure 2. Borosilicate Glass Powder (a) 0.038mm (b) 0.036mm (c) 0.075mm |
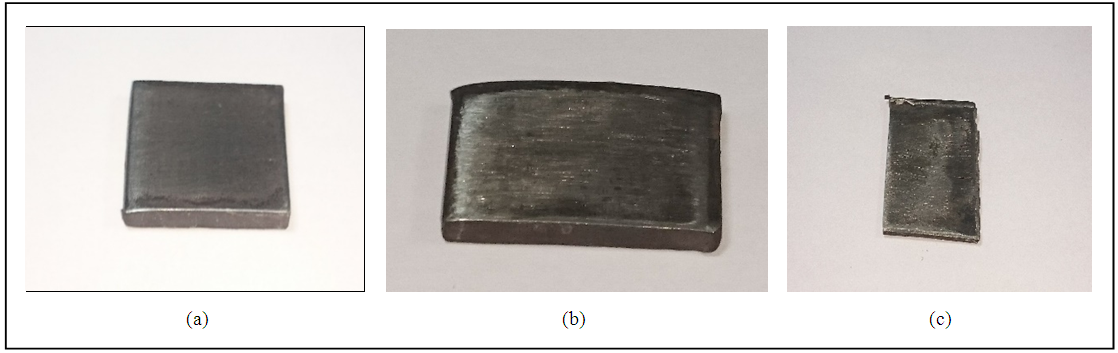 | Figure 3. Two gradess of stainless steelalloy and monel (a) 316SS (b) 304SS (c) monel |
The surface of the base alloys should be oxidized at an attempted temperature. The oxide growth considered affecting factor on the wetting concept and then bonding strength. Oxides growth was carried out in an electrically tube furnace controller Eurotherm-2116, UK product. This furnace provided with K-type thermo couple, the accuracy in a furnace temperature was found with in (±5). Static air was selected as an ambient furnace atmosphere along the project time. Oxidation temperature was selected in the range of 600°C up to 700°C for all alloy experiments. The temperature furnace setting at 700°C, and the wetting was measured at each desired holding time. The holding time was selected from 30 up to 60 minutes and followed was choose 60 minutes as a best holding time for oxidation. The oxide weight gain was measured for all specimens after the samples were cooled naturally in air. The weight gain per unit area was measured as a function of holding time. For this purpose Stanton 462AL-UK product 4-digit balance of accuracy of (±0.2) mg was used. The oxides growths was characterized by employing such techniques, oxides roughness attempted by using AFM, phase identification using x-ray diffraction (XRD), and surface analysis using optical and electron microscopies. Many experiments were performed to attempt verify the best wetting of the filler of powdered glass on the surface of both alloys, and the wettability of the filler of powdered glass is tested by depending on the young equation that is the best wettability when the contact angle between the tangential filler and the surface of the metal must be smaller than 90̊. In this research the contact angle was determined and measured by using a computer program to transfer two dimensional image to 3D image as shown in fig.(5). Joining of the borosilicate glass to both st.st and monel by the filler powdered glass was achieved in an atmospheric tube furnace as the same condition of wetting experiments.
3. Results and Discussion
The surface of alloy specimens should be oxidized in an atmospheric tube furnace at a sufficient temperature. Atomic force microscope (AFM) was used for examine the oxide growth on to alloy surface. Fig. (4a and 4b) represents the topographic of alloy surfaces before and after oxidized respectively.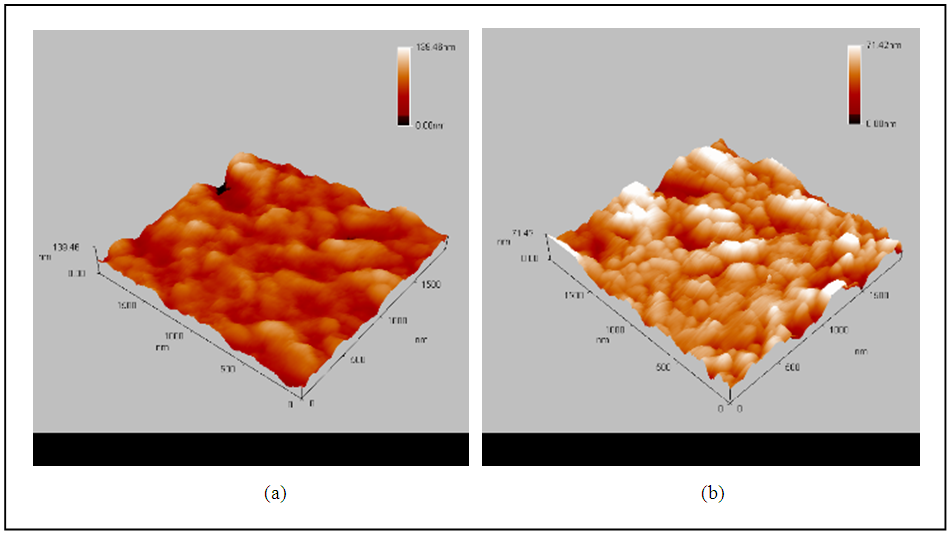 | Figure 4. AFM test (a) before oxidized (b) after oxidized |
The bonding between the partners to be joined was found dependently on the oxides growth which capable wet the metal surface. So the emerging model of oxide-metal interaction processes can be tested more thoroughly. For this purpose three dimensional schematic was used for each alloy used. As shown in fig. (5), the contact angles is (47) for st.st 304, (47) for st.st 316 and (23) for monel. These tests was achieved by using optical microscope of magnification 125x, and by using a computer program to transfer two dimensional image to 3D image. According to the Young equation, when the contact angle much smaller than 90̊, then the good wettability is verified and good bonding between the parameters is achieving.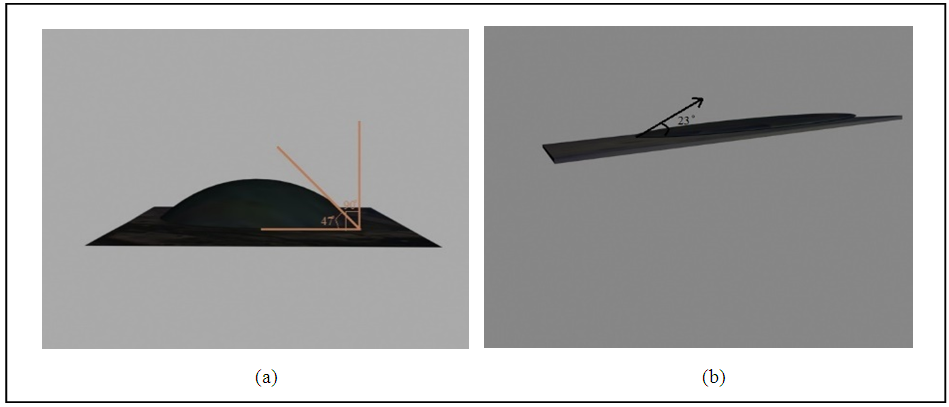 | Figure 5. 3D Images for wettability (a) for 304SS and 316SS (b) for monel |
Two mechanisms of bonding glass-metal were achieved. The first mechanism was performed by lied all joint parts into furnace before pre-oxidized of alloy surface. It was found the bonding is very weak and about 0.1 and 0.2 MPa for all types of project alloys as shown in the figure (8).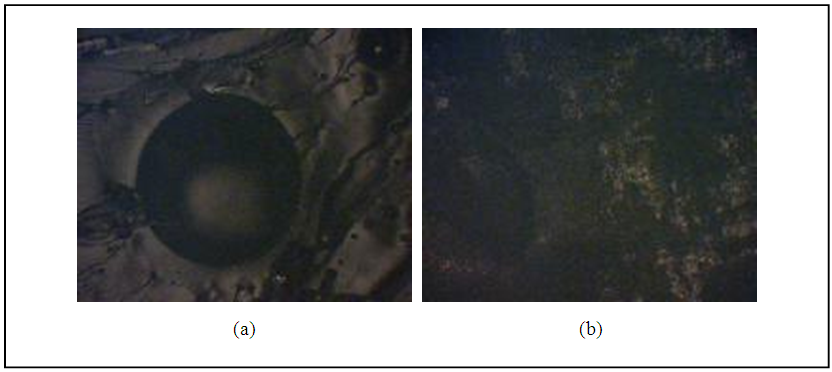 | Figure 6. Optical microscope image for wettability (a) stainless steel alloy (b) monel alloy |
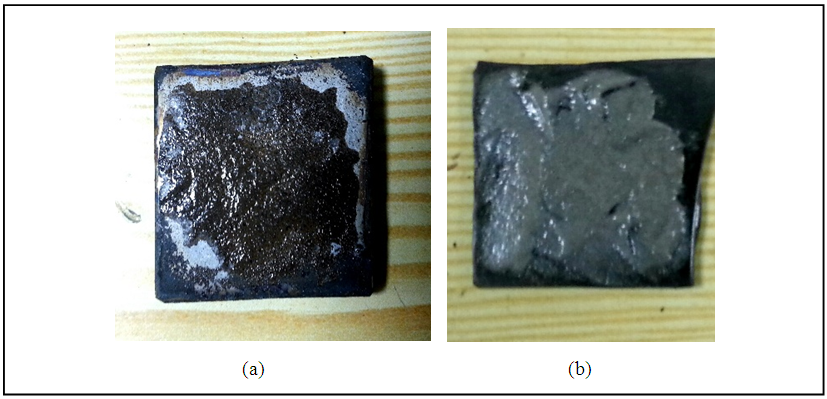 | Figure 7. Photographic image for wettability (a) stainless steel alloy (b) monel alloy |
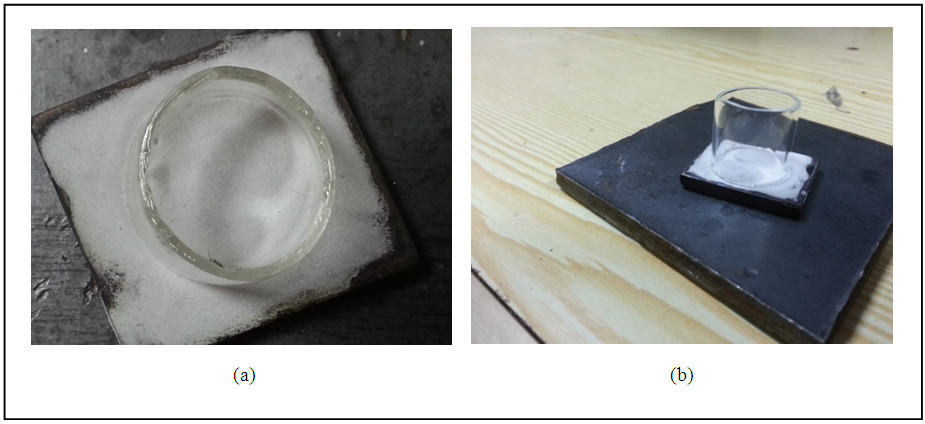 | Figure 8. Bonding process for (a) 316SS (b) 304SS |
The second mechanism of bonding glass-metal is by pre-oxidized of project alloys and oxides gain on to metal surface doing as an active filler, the tube glass can easily bonded to the metal. The bonding form are illustrated in the figure (9).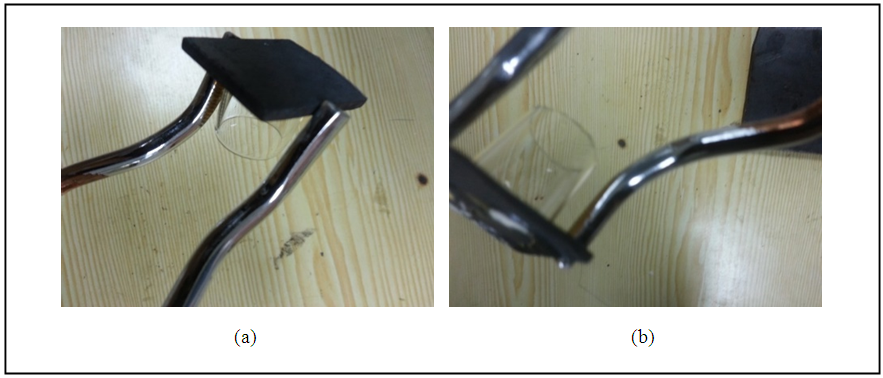 | Figure 9. Bonding process for (a) 316SS (b) monel |
According to the stated results, one can conclude that the maximum bond strength was found between glass-monel alloy at temperature of 700°C and holding time 1 hour, where the value of joint strength is 2 MPa. The reasons affected on obtaining good bond may summarized in the following:1. Good cleaning of alloy surface.2. Good wettability of powdered glass to both metal and glass.3. The ambient condition of bonding process such furnace temperature and holding time.4. Particle size of powdered glass.Due to above parameters, the good bonding obtained because a new phases consists at the interface layer of glass-metal joint as indicate this real in a pattern of XRD as shown in Figures (10-12).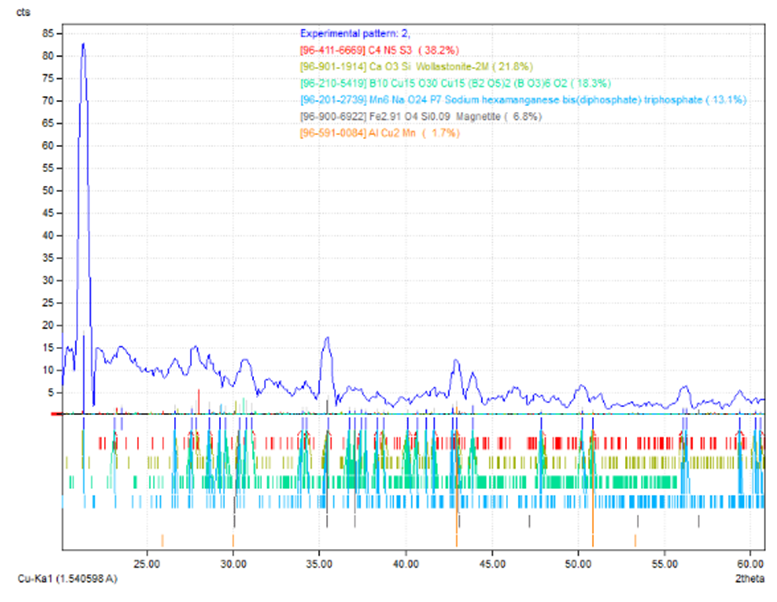 | Figure 10. XRD test for new phases of 304SS |
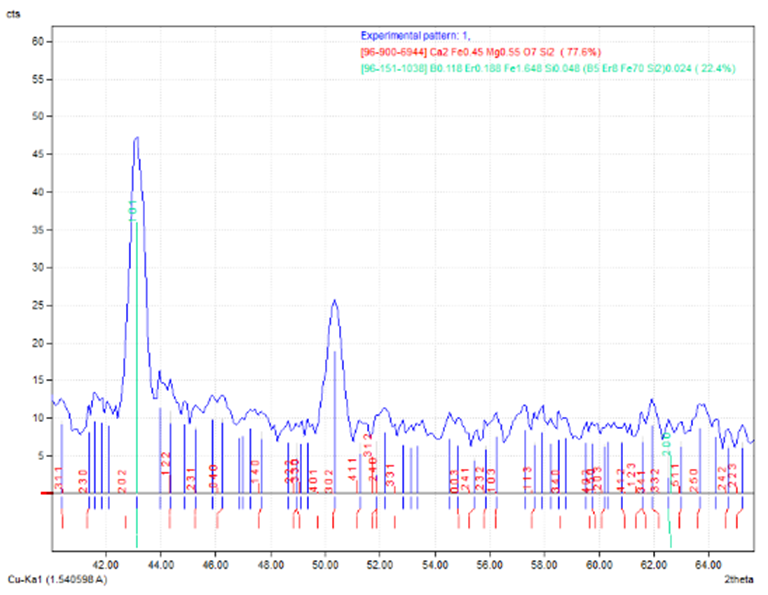 | Figure 11. XRD test for new phases of 316SS |
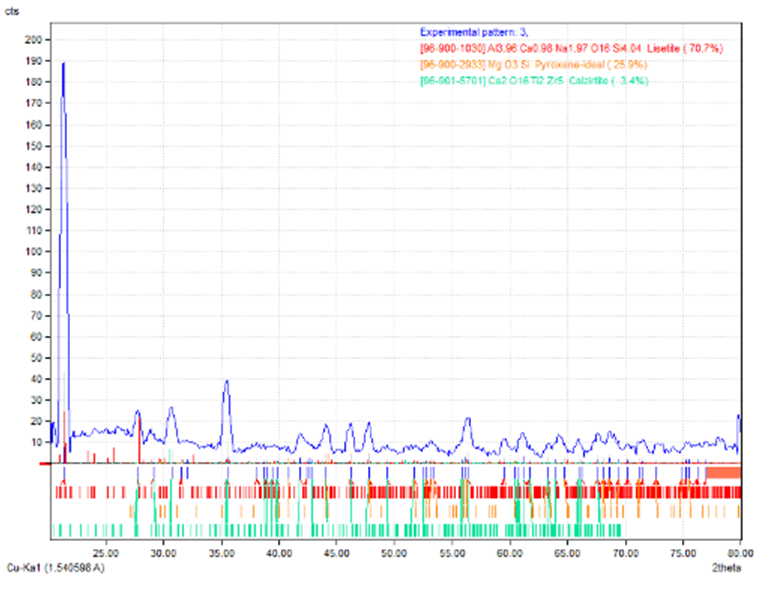 | Figure 12. XRD test for new phases of monel |
The chart of XRD reveal the new phases MgO3Si, AlCu2Mn, Mn6NaO24P7 , due to the interaction between the components at the intermediate layer of powdered glass-metal.Three main regions are very clear and determined in the SEM micrographs. The opaque region represent the metal part, the second region represent the intermediate layer which is consist the oxide growth on the surface of metal in which interacts with the glass part (the third part) as shown in the fig. (13). The intermediate layer considered an important region in the mechanism of glass-metal bonding. Thickness of the adherent oxide growth is classified as an active bonding filler attributed the joint reliability. One can see the bubbles diffused in the intermediate layer. This bubbles may be presented as a cavities occupies some of the spots regions at the intermediate layer and then will becreation un-adherent constituent and then cause weak joint.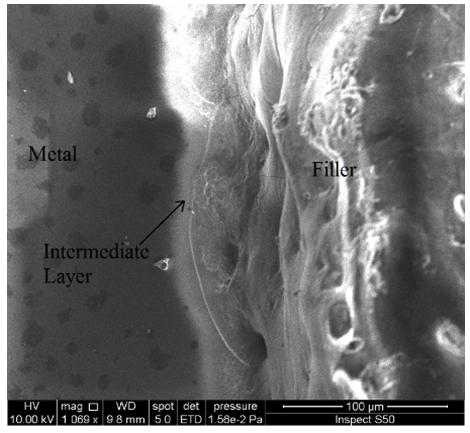 | Figure 13. Microscopic test |
There are three types of fracture modes are observed as following:First mode is from glass base as shown in fig. (14)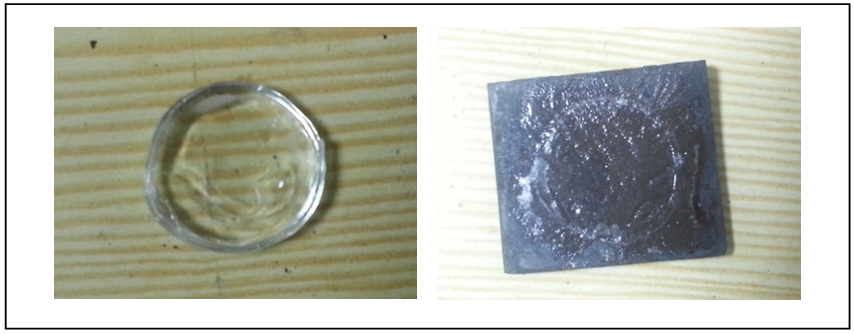 | Figure 14. First mode |
Second mode is from the filler of oxides as in fig. (15)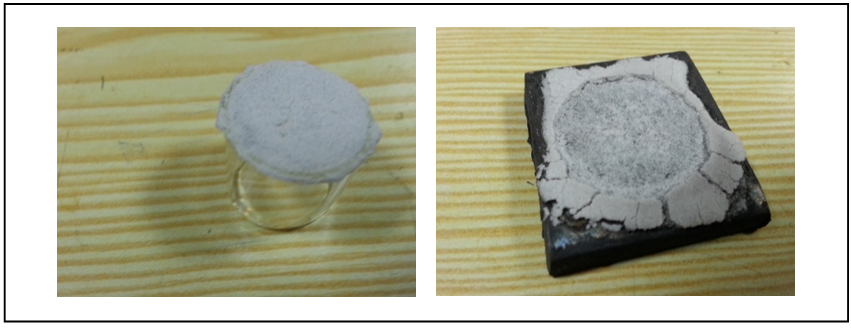 | Figure 15. Second mode |
Third mode is from the metal where a layer of oxides metal separated from the alloy as shown in fig. (16)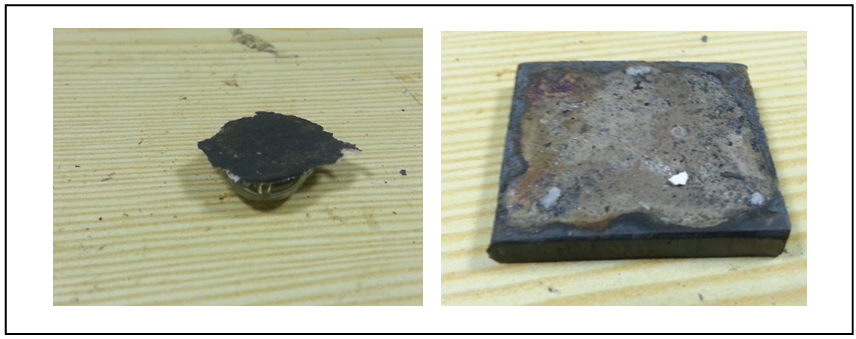 | Figure 16. Third mode |
The third mode is not actually because the separated layer is due to high oxidation temperature, therefore should have determine carefully the oxidation temperature for ensure the oxides growth. The bubbles have negative effective features on the joint strength. For this reason one can determine the parameters which affected on growth of bubbles. As clear from the fractography of the regions involved bubbles in fig.(17). The bubbles have many sizes and hence diameter. As the bubble diameter increases the bond strength decreases. One of the important reasons of growth bubbles is the particle size of powdered glass. It is found when the particle size of the powdered glass decreases, the joint bond strength will be decreases, therefore one should have determine the critical size of filler in which approach to excellent joint bond. 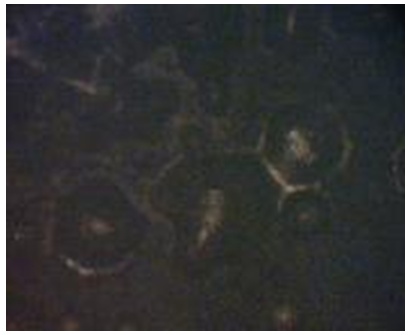 | Figure 17. Glass bubbles for particle size 0.038mm |
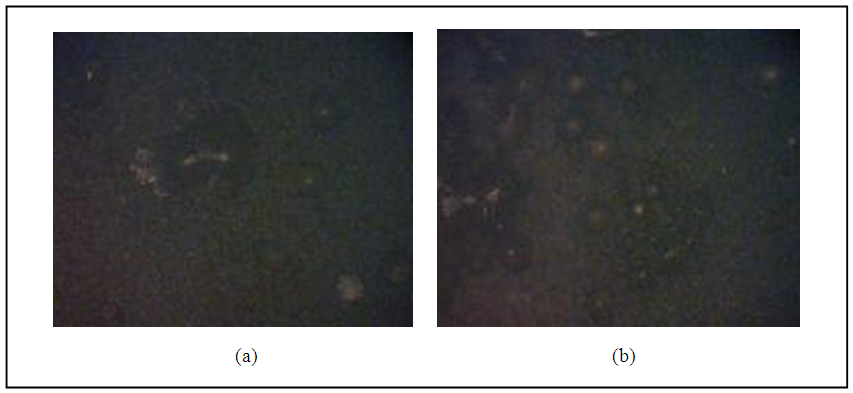 | Figure 18. Glass bubbles for particle size (a) 0.063mm (b) 0.075mm |
The relation between the bubbles diameter and the number of bubbles per unit area against the particle size of powdered glass are plotted in figs. (19, 20) respectively. It was found the favorite particle size is nearly 0.045mm leads to reduction of the number of bubbles per unit area and its diameter. For this reason the effects of particle size of powdered glass should be regarding carefully. 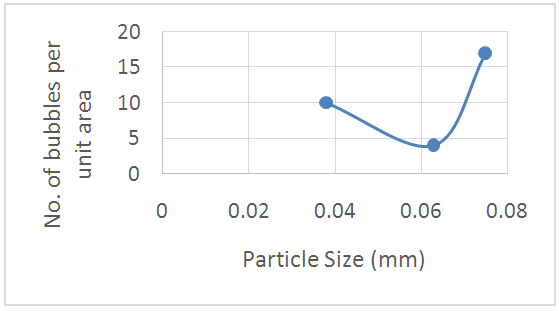 | Figure 19. A Schematic of the relationship |
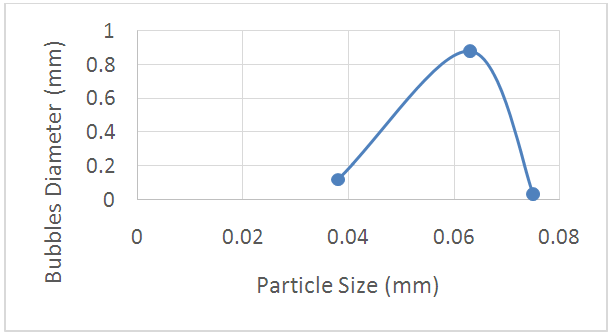 | Figure 20. A Schematic of the relationship between particle size and the bubbles diameter between particle size and the No. of bubbles per unit area |
4. Conclusions
1. Good oxidation of the alloy surface can enhanced bonding strength of glass bonded to metal, this technique was developed by selected carefully both furnace temperature and holding time.2. New phases consist at intermediate layer were enhanced the bonding strength of glass-metal.3. The number of bubbles per unit area and its diameter play an important role in the mechanism of joining glass-metal.
References
[1] | Robert W. Messler, Jr., “Joining of Materials and Structures”, 1st edition, pages (697,699,700), Elsevier Inc., 2004. |
[2] | R. D. Adams, “Adhesive Bonding: Science, Technology and Applications” 1st edition, page (91), woodhead Publishing Limited, 2005. |
[3] | By Committee on Opportunities in Protection Materials Science and Technology for Future Army Applications, National Materials and Manufacturing Board, Board on Army Science and Technology, Division on Engineering and Physical Sciences, National Research Council, “Opportunities in Protection Materials Science and Technology for Future Army”, page (95), National Academy of sciences, 2011. |
[4] | Morsy Amin Morsy, Kenji Ikeuchi, Masao Ushio and Hideyuki Abi, “Mechanism of Enlargement of Intimately Contacted Area in Anodic Bonding of Kovar Alloy to Borosilicate Glass”, Materials Transactions, Vol.37, No. 9, PP. (1511-1517), 1996. |
[5] | G. Leichtfried, G. Thurner and R. Weirather, “Molybdenum Alloys for Glass-to-Metal Seals “, International Journal of Refractory Metals & Hard Materials, Vol.6, PP. (13-22), 1998. |
[6] | Seiji Ioka, Keiji Masuda and Shiro Kubo, “Singular Stress Field Near the edge of Interface of Bonded Dissimilar Materials with an Interlayer”, International Journal of Solids and Structures, Vol.44, PP. (6232-6238), 2007. |
[7] | Scarlett J. Widgeon, Erica L. Corral, Michael N. Spilde and Ronald E. Loehman, “Glass to Metal Seal Interfacial Analysis Using Electron Probe Microscopy for Reliable Solid Oxide Fuel Cells”, J. Am. Ceram. Soc., Vol.92, No.4, PP. (781-786), 2009. |
[8] | ASTM F105-72, “Standard Specification for Borosilicate Sealing Glass”, 1983. |
[9] | A. Elrefaey, J. Janczak Rusch and M.M. Koebel, “Direct Glass to Metal Joining by Simultaneous Anodic Bonding and Soldering with Activated Liquid Tin Solder”, Journal of Materials Processing Technology, Vol.214, PP. (2716-2722), 2014. |
[10] | Kai Zhao and L. Roy XU, “Size Effect of the Adhesive Bonding Strengths of Metal/Polymer Similar and Dissimilar Material Joints”, The Journal of Adhesion, Vol.91, PP. (978–991), 2015. |