Md. Anwar Jahid, Md. Nahid Pervez
Wuhan Textile University, P. R. China
Correspondence to: Md. Nahid Pervez, Wuhan Textile University, P. R. China.
Email: |  |
Copyright © 2015 Scientific & Academic Publishing. All Rights Reserved.
Abstract
This study about defect’s less fabric in textile finishing by recovering through process control parameters by minimizing defect’s percentage in manufacturing process and It is well known that for getting desirable fabric quality some potential steps follow to reduce fabric fault through process control parameters analysis and reliable measurements for optimizing defects in knitted finished fabrics to scrutinize quality of finished fabrics. At present, quality of fabric is a great concern tones this modern textile arena. Quality is the most perspective demand in the produced textile fabrics which mainly viable by two factors one is fabric properties and other fabric defects. We have done our experimental part with some process controlling data for six knit fabrics and we got shrinkage is the most problem of finishing process. After that we have done analysis about fabric defect’s root cause with visualizing problem. About 80% defects could be resolved by controlling parameters in a daily basis of production area. This paper deals about optimizing defects with process parameters to ameliorate the quality of fabric with delicately and secure customer satisfaction with textile trends.
Keywords:
Finishing, Fabric Defects, Machine control parameters, Finished fabric, Quality, Shrinkage
Cite this paper: Md. Anwar Jahid, Md. Nahid Pervez, Amending of Finishing Quality of Different Knit Fabrics through Process Control Parameters by Optimizing Visualizing Defect’s, American Journal of Materials Science, Vol. 5 No. 3, 2015, pp. 57-65. doi: 10.5923/j.materials.20150503.01.
1. Introduction
Textile finishing can be categorized according to purpose or end result and it is a term which is usually performed after dyeing or printing stage and before to the making garments where cut and sewn are done [1]. By textile finishing, we also mean all the processing operations that, though included in the so-called finishing stage, are generally applied to the fabrics to improve their appearance, hand and Properties. The finishing stage plays a fundamental role in the Excellency of the commercial results of textiles, which strictly depend on market requirements that are becoming increasingly stringent and unpredictable, permitting very short response times for textile manufacturers [2]. We know finishing is a last process in dyeing [3]. The purpose of finishing is the improvement of the serviceability and adaptation of the products to meet the ever-changing demands of fashion and function [4]. It is done to improve specific properties in the finished fabric and involves the use of a large number of finishing agents for softening, cross-linking, and waterproofing [5]. The role of the textile finisher has become increasingly demanding and now requires a careful balance between the compatibility of different finishing products and treatments as well as the application processes used to provide textiles with desirable properties [6]. It represents the most variable area in the production process and ever wide growing range of finishes are now available [7]. Often fibers in textile substrates are deficient in one or more properties or improved properties are desired for the substrate. For getting this approach in finishing provides a method whereby deficiencies in the textile can be corrected or specific properties can be introduced. Physical finishing techniques (dry finishing processes) or chemical finishing methods (wet finishing) are used. Physical finishing is usually carried out on the yarn or formed textile substrate, whereas chemical finishes can be added to the spinning bath prior to fiber formation for man-made fibers or applied to individual fibers, yarns, or completed textile structures [8]. In case of finishing fabric lustrous, attractive, available in different tints and shades of colors, prints, and etc. smooth and wrinkle-free, no defects on the surface, even width, free from stains, etc. Cost of fabric depends upon the type of the fiber along with the number and type of finishes applied [9]. Fabric property depends on the raw material, construction parameters and processing methods. Whereas a fabric defect can occur right from raw material selection to finishing stage, because of improper input parameters with respect to material, machine and man. Any variation to the knitting process needs to be investigated and corrected [10]. Defects fall into the category. Since when they appear, repair is needed, this is time consuming and sometimes results in fabric rejection. Fabric defect detection has been a long – felt need in the textile and apparel industry. Surveys carried out in the early 1975 shows that inadequate or inaccurate inspection of fabrics has led to fabric defects being missed out, which in turn had great effects on the quality and subsequent costs of the fabric finishing and manufacturing processes [11]. Quality inspection is an important aspect of industrial manufacturing. In textile industry fabric defect detection plays an important role in the quality control. The quality of the fabric can be improved by decreasing defects in the fabrics [12].The aim of this research was to study the process control parameters of finishing section and to improve quality of fabric by minimizing faults which appearance in our daily textile industry.
2. Materials and Methods
2.1. Fabrics
We have taken different types of fabric like single jersey, Rib, Interlock, Lacoste, Pique and Fleece. We used here dyed sample which incorporated dyeing process with proper chemicals, machine.
2.2. Methods
The sequence of processes for carrying out the studies are shown in Figure 1 For processing open fabric finishing first fabric is passed through slitting for opening fabric then pass through stentering and compaction where GSM diameter, shrinkage controlled. Then according to buyer requirements fabric can be packing and delivery. 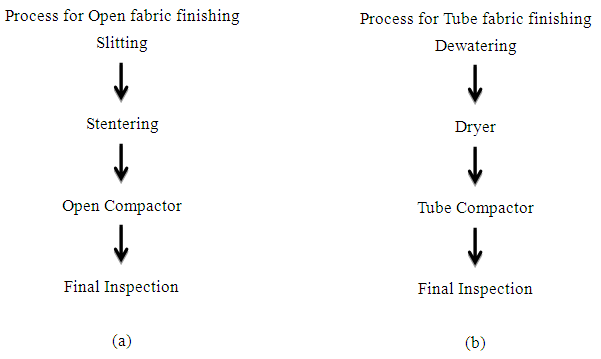 | Figure 1. Flow chart of fabric finishing (a) Open & (b) Tube Compactor |
For processing tube fabric finishing first fabric is passed through dewatering for removing water from fabric and then drying for dryer then pass through stentering and compaction where GSM diameter, shrinkage controlled. Then according to buyer requirements fabric can be packing and delivery.
2.3. Machinery
These fabrics were dyed by dyeing machine then we observe the finishing process of these fabrics. For finishing some process are followed and some machines are used to complete the output appearance of these fabrics these are shown in Table 1.Table 1. List of Machines 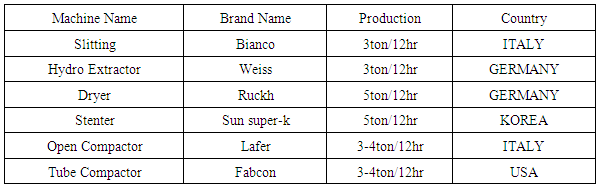 |
| |
|
3. Experimental Work
Table 2. Technical parameters of slitting machine 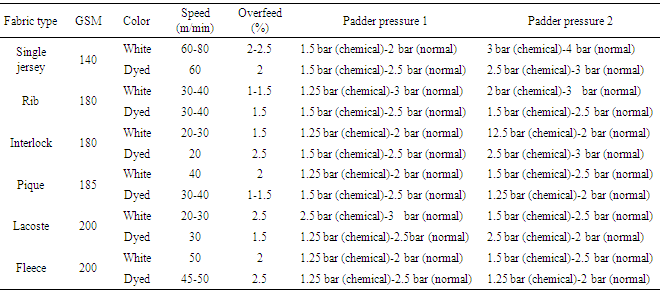 |
| |
|
Table 3. Technical parameters of Hydro-extractor machine 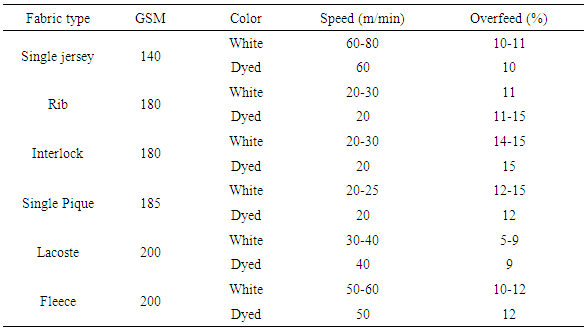 |
| |
|
Table 4. Technical parameters of dryer machine 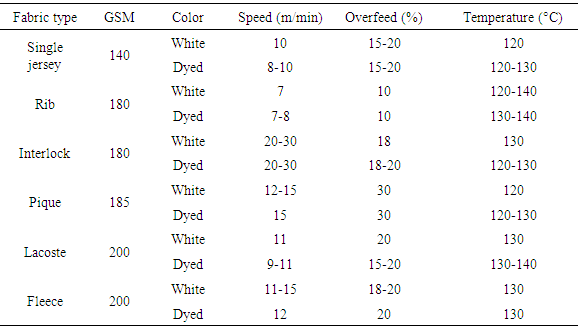 |
| |
|
Table 5. Technical parameters of stenter machine 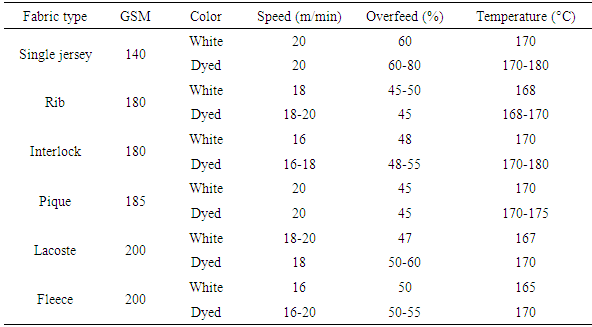 |
| |
|
Table 6. Technical parameters of Open compactor machine 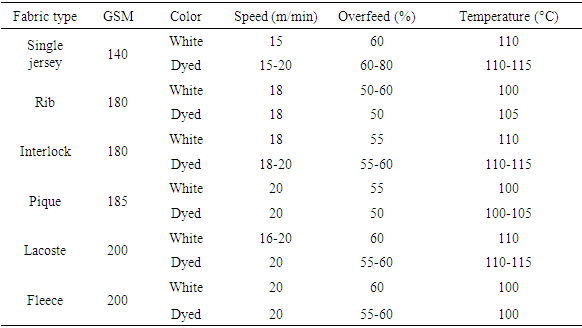 |
| |
|
Table 7. Technical parameters of Tube compactor machine 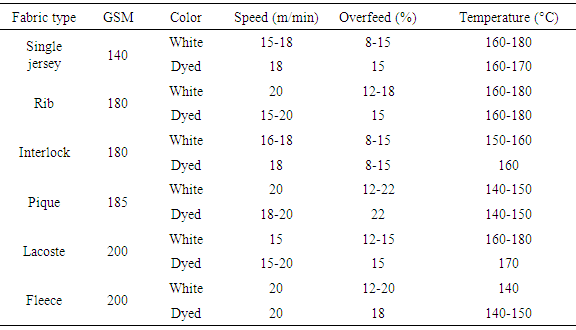 |
| |
|
4. Result & Discussion
4.1. Different Type of Finished Fabric Faults
4.2. Fault’s Percentage of Different Knit Fabrics
After doing experiment we got major faults of finished fabrics are shown in Figure 2. In finishing section many faults occurred but we conducted here visible faults of individually fabrics such as shrinkage, GSM variation, Width variation, Bowing, Skewing, Wet squeezer marks and others. We observed that most of the fault occurred in shrinkage about 40% that is most carried by single jersey fabric is shown in Figure 3. Then second fault occurred in GSM variation about 28% is most carried by Rib fabric is shown in Figure 4. Again we observed that third fault width variation about 8% is most carried by Interlock is shown in Figure 5. Furthermore we have seen that fourth fault Bowing about 8% is most carried by Pique fabric is shown in Figure 6. Then we can be seen that fifth fault Skewing about 7% is most carried by Lacoste fabric is shown in Figure 7. Furthermore we have seen that sixth fault wet squeezer marks about 5% is most carried by Fleece fabric is shown in Figure 8. Then other faults are most occurred in single jersey fabric. It is seen from Table 8 different type of faults occurred and their causes are described. Our paper is demanded to minimize this faults. After some process analysis some steps recommended that could achieve our purpose. For reducing wet squeezer marks have to use the padding mangle when use softener and use a hydro extractor (centrifuge) for the extraction to avoid the squeezer roll marks and For minimizing GSM variation make sure that all the fabric rolls in a lot are processed under the same process parameters then for bowing and skewing faults minimizing the fabric should be feeding it from the opposite end and Use a drop needle line as a reference line to keep the grain lines straight while feeding the fabric slowly on the compactor machines. For minimizing over compaction give maximum overfeed to the fabric during the processing on the stenter and compactor machines. In case of others faults correct setting of machine and re-compaction with lesser over-feed. The stretched width of the fabric should remain constant for each roll during finishing in the stenter and in the compactor. The cloth should be padded in a solution of hot water and dried on an even surface. Finishing floor and trolley should be clean and machine surface should be clean. In case of machine process controlling parameters should be adjustable to obtain less fabric defects. In machine running process some checking parameters must be maintained to control fabric quality such as Bucket dia. should be adjusted according to the dia of the fabric. Fabric should be cut according to needle line. The needle line move away from the cutter bucket is moved to set the m/c needle line in front of cutter M/c speed should be controlled according to the fabric structure. Overfeed, speed, pick controllers, chamber temperature control, width controlling, chain rolls, weft correction, Spreader roller, scroll roll, Feed roll, shoe pressure, Edge line check, Design & slanting, Inlet tightener, Temperature, Width check, shade check, Nozzle distance etc. Padder Pressure: Generally padder pressure is kept 2-5.5 bars for all kind of fabrics ballooning: Air is applied to the fabric to make balloon of fabric before it passes through padder Otherwise Crease mark will be created in the fabric. These pints can be controlled by observing production floor people and must be maintenance on the daily basis in a month.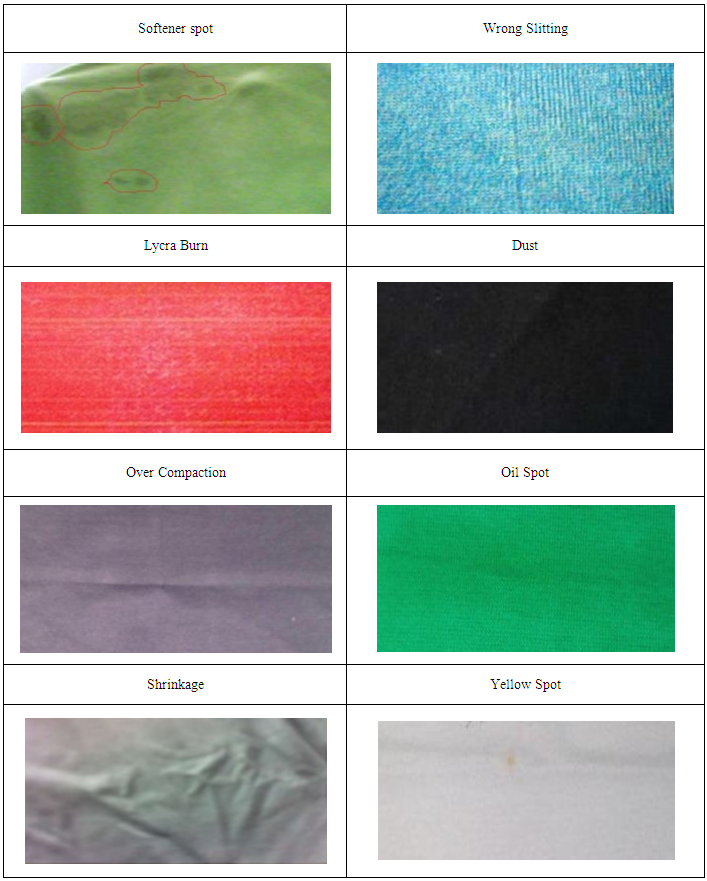 | Figure 2. Different types fault of finished fabric |
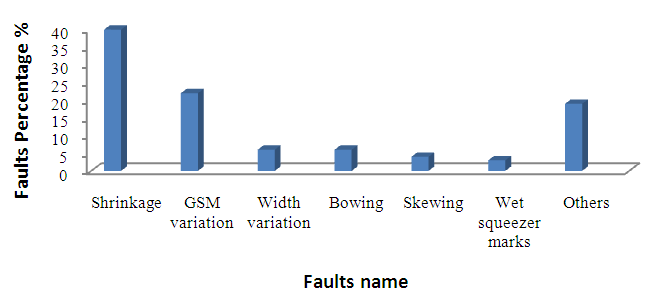 | Figure 3. Single jersey faults percentage |
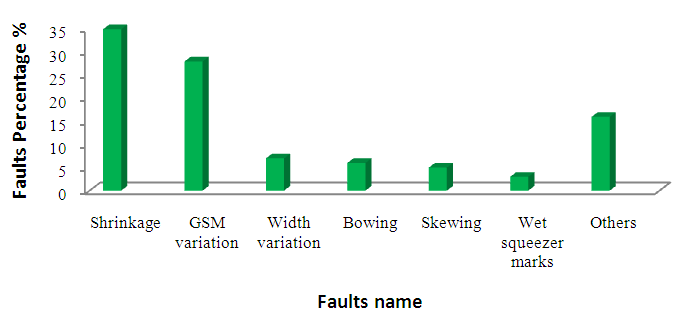 | Figure 4. Rib faults percentage |
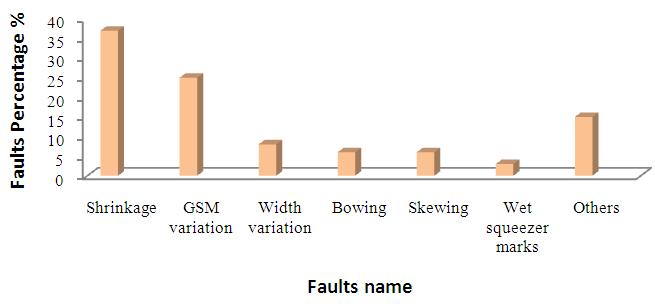 | Figure 5. Interlock faults percentage |
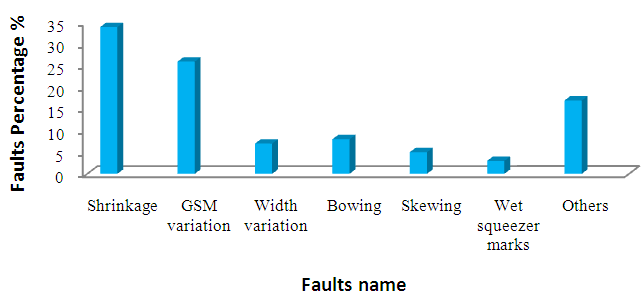 | Figure 6. Pique faults percentage |
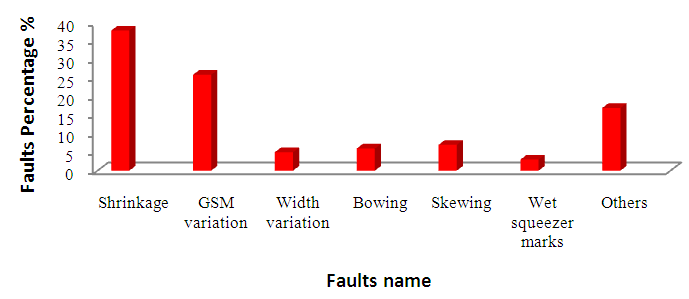 | Figure 7. Lacoste faults percentage |
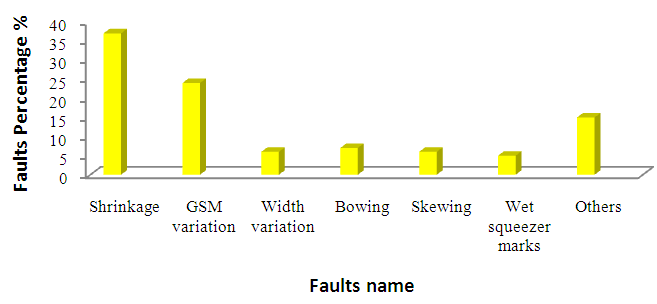 | Figure 8. Fleece faults percentage |
Table 8. Different types of fault and their causes 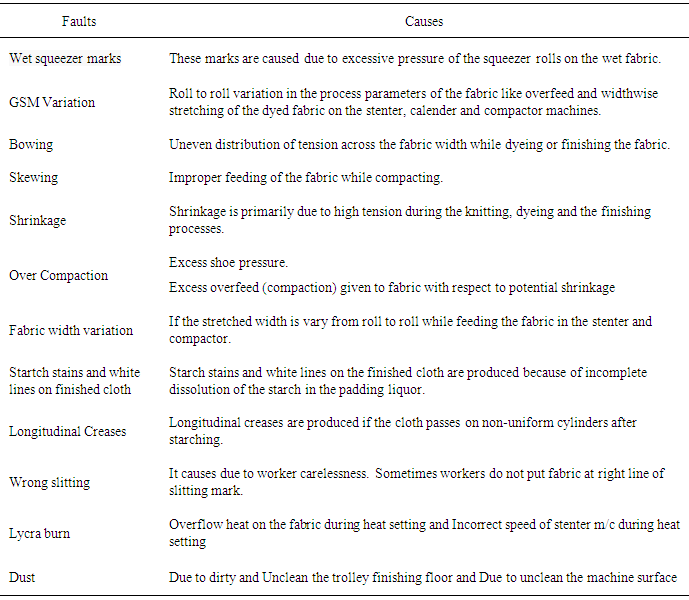 |
| |
|
5. Conclusions
In finishing used to improve appearance, impart functionality and enhance durability as well as process ability of the textile products Different processes associated with complete production of fabrics are required to get finished fabric. An effort is made to formulate all the finishing production steps. This paper also gives an idea of different processes and machineries used usually in a fast growing and mass productive knit-dyeing factory. Major processes control parameters in all machines are discussed briefly to optimizing the faults through this machine control process and some visible hindrance.Finally based on the overall performance it is concluded that the this paper tries to gather all the information related to knit-finishing factory and analysis fault’s causes and suggest some ideas which can meet modern textile trends and customer demand.
References
[1] | W. S. Perkins, Textile Coloration and Finishing. 1996, Carolina, USA: Carolina Academic Press. 199. |
[2] | Pietro Bellini, et al., Finishing Reference Book for Textile Technologies. Third ed. 2002, Via Tevere 1, 20123 Milano (Italia): Fondazione Acimit. 1. |
[3] | K. A. Rade, V. A. Pharande, and D. R. Saini, Energy Optimization in Dyeing Process By Using Controlled Parameters. International Journal of Innovative Research in Science, Engineering and Technology, 2014. 3(6). |
[4] | I.-I. Savin and R. Butnaru, Wastewater characteristics in textile finishing mills Environmental Engineering and Management Journal 2008. 7(6): p. 859-864. |
[5] | B. Ramesh Babu*, et al., Cotton Textile Processing: Waste Generation and Effluent Treatment. The Journal of Cotton Science 2007. 11: p. 141-153. |
[6] | D. Kaur and N. Grewal, Effect of Ecofriendly Microencapsulated Textile Products In Joint Pain and Aesthematic Respondents. IOSR Journal of Polymer and Textile Engineering, 2014. 1(2): p. 41-45. |
[7] | A. Walters, D. Santillo, and P. Johnston, An Overview of Textiles Processing and Related Environmental Concerns. 2005, University of Exeter: Uinited Kingdom. p. 25. |
[8] | Textile Finishes and Finishing, in New Cloth Market 2009: Sarangpur, Sherkotda, Ahmedabad, Gujarat 380002, India. |
[9] | Notes fabric finishes 2015, National institute of open: A-24/25, Institutional Area, Sector - 62, NOIDA Distt. Gautam Budh Nagar, Uttar Pradesh - 201 309. p. 190. |
[10] | Color histogram, in Wikipedia, the free encyclopedia.mht. |
[11] | P. Banumathi and D. G. M. Nasira, Fabric Inspection System using Artificial Neural Networks. International Journal of Computer Engineering Science, 2012. 2(5): p. 20. |
[12] | M. PM, K. SR, and P. PM, A review of automatic fabric defect detection techniques. Advances in Computational Research, 2009. 1: p. 18-29. |