A. Danladi, J. Shu’aib
Department of Textile Science and Technology, Ahmadu Bello University, Zaria, 816000, Nigeria
Correspondence to: A. Danladi, Department of Textile Science and Technology, Ahmadu Bello University, Zaria, 816000, Nigeria.
Email: |  |
Copyright © 2014 Scientific & Academic Publishing. All Rights Reserved.
Abstract
Composites of pineapple fibre (PAF) with High Density Polyethylene (HDPE) were produced using the injection molding machine. The maximum amount of PAF accepted by HDPE was observed to be 50% of the HDPE weight. The composites were subjected to tests to evaluate their physical and mechanical properties. The density was found to decrease from 0.99 to 0.64 g/cm3 as the fibre content increased from 0 to 50%. Water absorption showed increase with increase in fibre content and with increase in the number of days in water. The result obtained from the impact strength, hardness, tensile strength and elongation of the composites were all found to decrease with increased fibre content.
Keywords:
Pineapple fibre, High density polyethylene, Water absorption, Hardness and composites
Cite this paper: A. Danladi, J. Shu’aib, Fabrication and Properties of Pineapple Fibre / High Density Polyethylene Composites, American Journal of Materials Science, Vol. 4 No. 3, 2014, pp. 139-143. doi: 10.5923/j.materials.20140403.04.
1. Introduction
Pineapple is an herbaceous plant that consists of a rosette of stiff succulent leaves on massive upright stem. The tropical perennial pineapple is a member of the family Bromeliaceae. The pineapple originally came from Brazil and Paraguay, today it is cultivated throughout most of the tropics and parts of the subtropics, particularly in Thailand, Philippines, Hawaii, Mexico, India, Nigeria, and Ivory Coast [1].The leaves are sword-shaped arising from a stem and are about 0.9 to 1.5 m long and 2.54 to 5.1cm wide tapering to a point. The leaves may be all green or variously striped with red, yellow or ivory down the middle or near the margins. Pineapple leaves can be used for fibre production [2]. Generally, pineapple fibres are thin in comparison with other hard fibres and with or without marginal prickles depending on the variety. The pineapple leaf fibre is strong, white, fine and lustrous. Fibre strands are from 7.5 to 10cm long. The pineapple fibre can be extracted by hand scraping, decortications and retting. Hand scraping is a crude and tedious method and uses tools such as porcelain plate, coconut shell, plastic comb and seashells. The use of pineapple fibres in textile manufacture or handmade paper has been reported [3]. Properties of pineapple fibres have been studied and reported as shown in table 1 below [2].Table 1. Properties of pineapple fibres 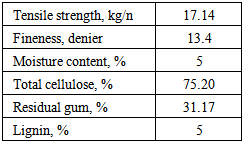 |
| |
|
High Density Polyethylene (HDPE) is defined by a density of great or equal to 0.941g/cm3. It has a low degree of branching and thus stronger intermolecular forces and tensile strength. HDPE can be produced by chromium/silica catalyst, Ziegler-Natta catalysts or metal lone catalysts. The lack of branching is ensured by an appropriate choice of catalyst (chromium or Ziegler-Natta) and reaction conditions. HDPE is used in producing and packaging such as milk jugs, detergent bottles, margarine tubs, garbage containers and water pipes. It is widely used in the firework community. Its melting point is approximately 212-220°C, and it is chemically inert.The development of commercially viable “green products” based on natural resources for both matrices and reinforcements for a wide range of applications is on the rise. This effort includes new pathways to produce natural polymers with better mechanical properties and thermal stability using nanotechnology and use of natural polymers to make biodegradable plastics and their composites with lingo cellulosic fibers.The application of pineapple fibres in composites technology is gaining popularity. The uses of pineapple fibres as biodegradable composites have been reported [4]. Similarly studies of Melt rheological behavior of short pineapple fibre reinforced low density polyethylene composites [5] have been reported. Mechanical properties and water absorption behavior of hybridized kenaf/pineapple leaf fibre-reinforced high-density polyethylene composite has also been studied [6]. Work on electrical properties of pineapple fibre reinforced polyethylene composites have been carried out [7]. Research has also been conducted on mechanical properties of pineapple leaf fibre reinforced polypropylene laminated composites [8]. In this work, composites of pineapple fibres (PAF) as reinforcement in (high density polyethylene) HDPE matrix were produced. The physical and mechanical properties of the composites were tested and analyzed.
2. Methodology
2.1. Extraction of Pineapple Fibres
Pineapple leaves were immersed in a water retting bath for 10-14 days. During this period, the leaves softened. Using a knife, the outer layers of the leaves were peeled off and the fibres carefully separated, rinsed and allowed to dry.
2.2. Moulding of PAF/HDPE Composites
The composites were produced with the varying ratios of polymer matrix to fibre reinforcement. The injection molding machine was heated to about 220℃, there after the pineapple fibre/HDPE in the designed ratios were poured into the Auger of an injection molding. The melted HDPE together with the fibre were then injected into the molding chamber, were it is steam cooled.
2.3. Characterization of PAF/HDPE Composites
The samples were left after conditioning for 24hrs before subjected to the following tests.
2.3.1. Density Measurement
Density of the composites was determined according to ASTM D792 - 13; about 0.5g of the composite was cut and immersed into the cylinder containing the distilled water, and the displacement of water volume was observed, the volume of the water displaced was and the density of the composite were the calculated using the formula:
Where ρ = density, m = mass and v = volume. The results are shown in figure 1.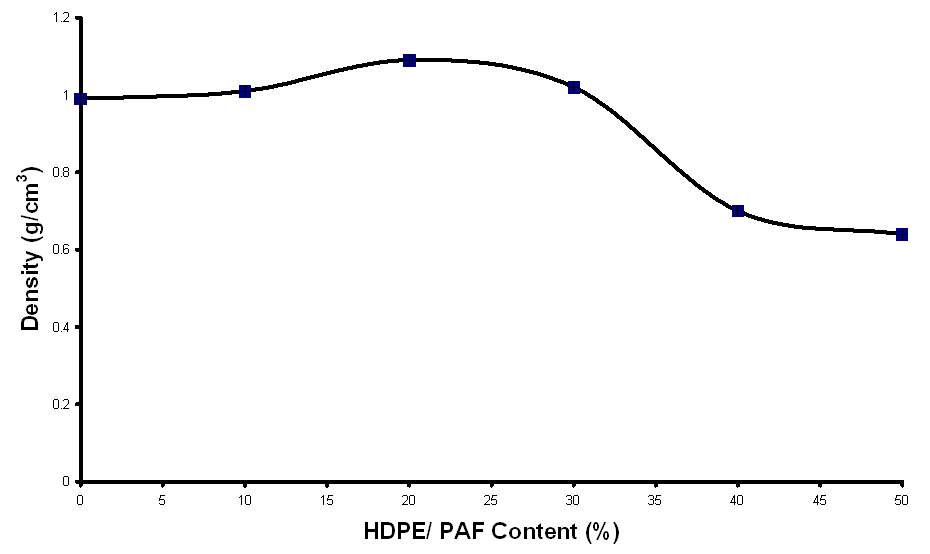 | Figure 1. Density of PAF /HDPE Composites |
2.3.2. Water Absorption Test
This test was carried out according to ASTM D2842. Samples were cut and weighed. The weighed samples were placed in a stainless steel container and enough water was added so that they were completely immersed and left in the water for 24hrs. Thereafter, they were re-weighed every twenty four hours for fourteen days and the percentage water absorption was calculated using the equation.% water absorption = (W2 - W1) /W1Where W1 = initial weight and W2 = final weightThe results are shown in figure 2.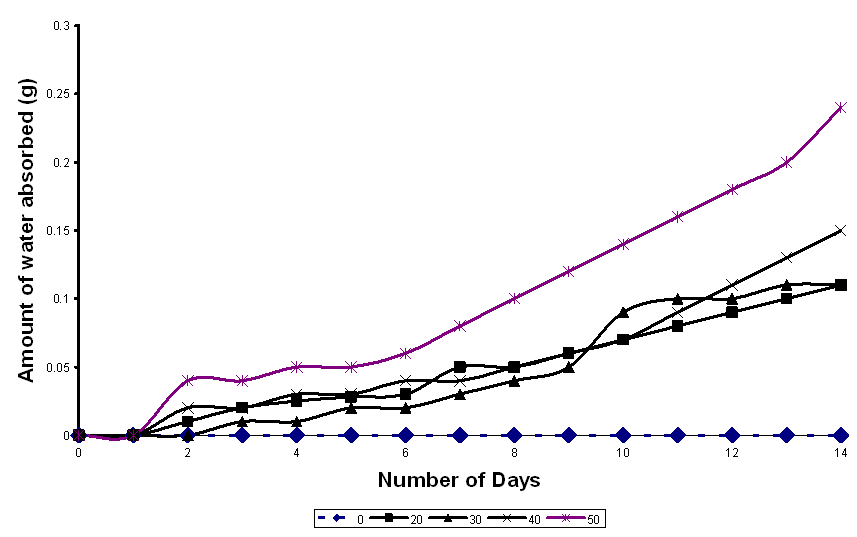 | Figure 2. Water absorption of PAF/HDPE Composites |
2.3.3. Hardness Test
The test was carried in accordance with ASTM 5901, in which the test sample was placed on the flat surface and the indenter was forced on the surface of the specimen, the load was maintained at maximum time of 10 to 15seconds, and the result was recorded. The results are shown in figure 3.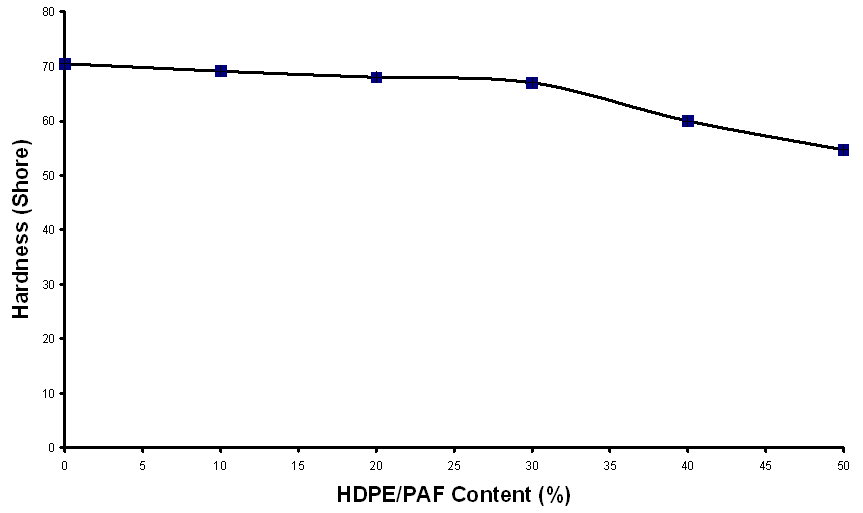 | Figure 3. Hardness of PAF /HDPE composites |
2.3.4. Impact Strength Test
This test was carried out according to ASTM 6957. Test samples of about 6.4mm were placed on the machine and held tightly with the aid of knots, while the ends were observed to be of equal length, the hammer was raised and then released to hit the sample, which led to breaking of the sample. The work done in breaking the test sample was recorded and the results are shown in figure 4.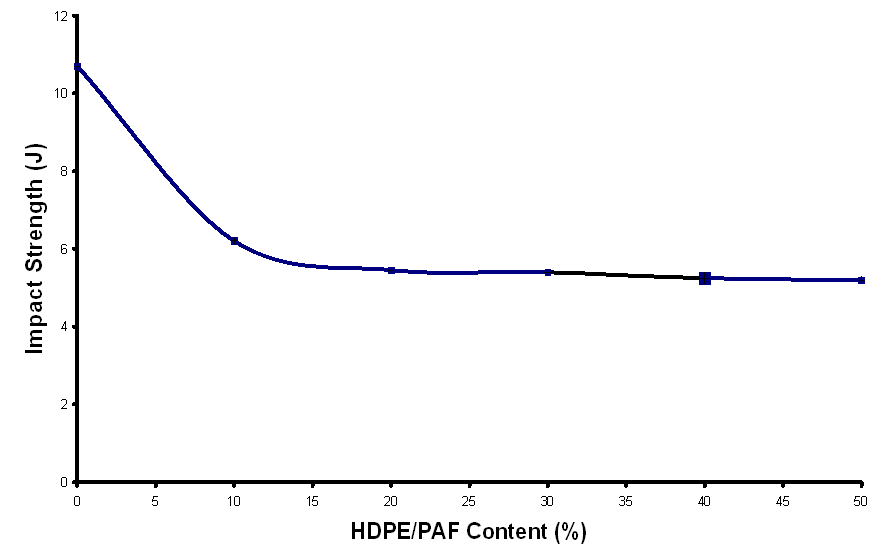 | Figure 4. Impact Strength of PAF /HDPE composites |
2.3.5. Measurement of Tensile Properties
Tensile strength and elongation tests were carried out using Hounsfield Tensometer. The test specimen was clamped between the upper and lower jaw of the Tensometer and the machine was started. The specimen was stretched till it reached its breaking point. Reading of maximum load and elongation at break were taken accordingly. The results are shown in figures 5 and 6 respectively.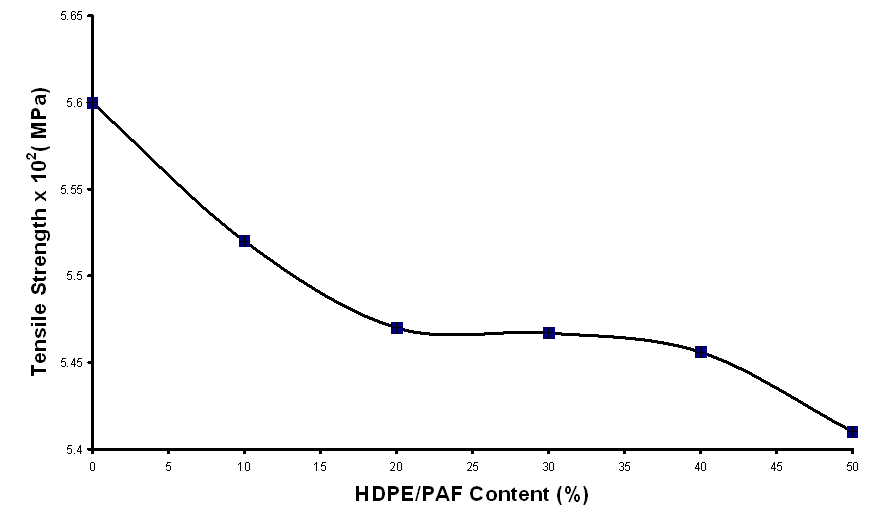 | Figure 5. Tensile Strength of PAF /HDPE composites |
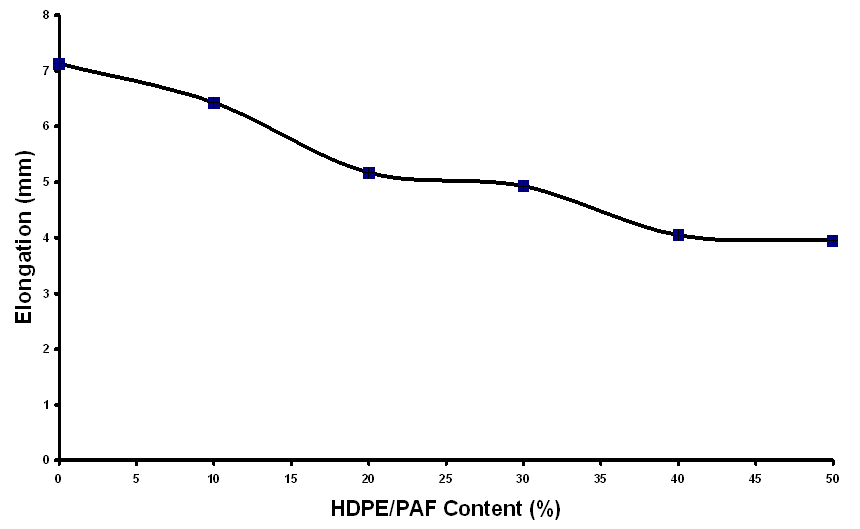 | Figure 6. Elongation of PAF /HDPE composites |
3. Results and Discussion
3.1. Density
Figure 1 shows that there is no significant increase in the PAF/HDPE composites as the fibre content increased from 0 to about 30%. However between 30 and 50% fibre content, the composite’s density decreased. This may be as a result of high pineapple content which increased the bulkiness of the composites, thus increasing the volume which eventually caused a decrease in the density of the composites. Similar observations have been reported by other researchers [9].
3.2. Water Absorption
Figure 2 reveals that as the composites are soaked in water for about15 days, the amount of water absorbed by the composites increased with increase in the quantity of the pineapple fibres in the composites. This is in conformity with results of similar works [10]. Pineapple fibre is highly rich in cellulose content, so it should be expected that as its content increased, the amount of water absorbed will increase. Similarly it is clear that as the pineapple content increased, the amount of water absorbed increased, this can be as a result of opening up the HDPE structure at higher content levels of the pineapple fibres. The ability of water to penetrate into fibre composites is a great disadvantage as this eventually lowers the life span of the composites, because the microorganisms present in water can attack the cellulose of the pineapple fibre and degrade i.
3.3. Hardness
Similar to the results of density of the PAF/HDPE composites, the hardness values can be seen to remain about the same until at above 30% PAF content as depicted in Figure 3. At above 30% fibre content, the intermolecular structure of the HDPE has been compromised due to the presence of the PAF which might have caused void and dispersion problems, thus the hardness is equally compromised.
3.4. Impact Strength
The effect of PAF content on its composites with HDPE is clearly visible as shown in Figure 4. Increasing the PAF content to about 10% drastically lowered the impact strength of the PAF/HDPE composites. The values are then seen to remain at about 6 J even at higher PAF content. This may be attributed to poor interfacial bonding between the PAF and the HDPE matrix. The results imply that such composites may not be conveniently applicable in applications where high impact strength is required. Alternatively the incorporation of compatilisers may be needed to improve the impact strength of the composites. Hybridization of fibre fillers have been shown to optimize the impact strength of pineapple fibre composites with kenaf fibres in HDPE [6].
3.5. Tensile Strength
The strength of PAF/HDPE composites was found to decrease with increase in PAF content as seen in Figure 5. As explained earlier, this may be attributed to poor inter facial bonding between the fibres and the HDPE matrix. Similarly as the content of PAF increased, there is higher tendency for voids and dispersions to be created; all these could be part of the reasons that lead to decrease in the overall strength of the composites. Similar study on mechanical properties of pineapple leaf fibre reinforced polypropylene laminated composites [8] showed similar results.
3.6. Elongation
The ability of PAF/HDPE composites to elongate on loading can be seen to decrease with increase in PAF content as depicted in Figure 6 Inclusion of the PAF in to the HDPE matrix interferes with the intermolecular structure and bonding of the polymer, hence the ability to extend and return to its original length is impaired. Composites of PAF/HDPE can therefore be seen to be of little applicability in areas where elongation is of paramount importance.
4. Conclusions
PAF/HDPE composites produce and tested show that useful materials could be produced out of the PAF. The composites have low density values, which is one of the major requirements of composites materials. The hardness values are moderate, while the impact and tensile strength values are on the low side. With the abundance of pineapple fibres and High density polyethylene, additional useful materials can be produced out these materials which can find applications in areas where strength is not the prime factor. Modification of the PAF can be carried out to improve the interface bonding between the PAF and HDPE. This will improve the mechanical properties of the composites.Applications like partition walls, table tops and automobile can be areas where PAF/HDPE composites can find useful applications, thus adding value to the hitherto neglected pineapple fibres.
References
[1] | Kannojiya R., Kumar Gaurav, Ravi Ranjan, Tiyer N.K. and Pandey K.M. 2013, Extraction of Pineapple Fibres for Making Commercial Products, Journal of Environmental Research and Development 7 (4), 1385- 1890. |
[2] | Dey. S. K. and Satapathy. K. K. 2011 A Combined Technology Package for Extraction of Pineapple Leaf Fibre- An Agrowaste, Utilization of biomass and for application in Textiles. National Institute of Research on Jute and Allied Fibre Technology Indian Council of Agricultural Research 1-9. |
[3] | Nkeonye, P.O., 1993, Introductory Textile. S. Asekome and Co. Publishers, Samaru, Zaria. P 78-94. |
[4] | Kestur G. S., Gregorio G.C. A.Fernando .W. (2009), Biodegradable composites based on lignocellulosic fibers-An overview Progress in Polymer Science, Volume 34, Issue 9, Pages 982–1021. |
[5] | G. Jayamol, 2014Melt rheological behaviour of short pineapple fibre reinforced low density polyethylene composites, Polymer, 37 (24), 5421–5431. |
[6] | I. Aji, E.S. Zainudin, K. Abdan, S.M. Sapuan, M. D. Khairu, (2012), Mechanical properties and water absorption behavior of hybridized kenaf/pineapple leaf fibre-reinforced high-density polyethylene composite. 231-240. |
[7] | G. Jayamol, S.S. Bhagawan, S. Thomas 2011, Electrical Properties of Pineapple Fibre Reinforced Polyethylene Composites, Journal of Polymer Engineering, 17 (5), 383–404. |
[8] | M. Rejab, M. N. Arib 2004 Mechanical Properties of Pineapple Leaf Fibre Reinforced Polypropylene Laminated Composites.Masters thesis, Universiti Putra Malaysia. |
[9] | Danladi. A, Kolawole. E. G and K. A. Bello, (2009), Preparation and study of the mechanical properties of kenaf/natural rubber composites. Pakistan Textile Journal, URL: http://www.ptj.com.pk 42-45. |
[10] | Danladi. A. and Tunde. A. S, 2013, Effect of Fibre Length on the Physical and Mechanical Properties of Sisal/Polyethylene Composites, Pakistan Journal of Scientific and Industrial Research. Series A: Physical Sciences, 56 (1):42-46. |