Naglaa Fathy
Physics Department, College of Science, University of Hail, P.O. Box 2440, Hail, Saudi Arabia
Correspondence to: Naglaa Fathy , Physics Department, College of Science, University of Hail, P.O. Box 2440, Hail, Saudi Arabia.
Email: |  |
Copyright © 2012 Scientific & Academic Publishing. All Rights Reserved.
Abstract
A new semi-solid cyclic heat treatment method was presented for 6061 aluminum alloy. The cyclic heat treating process was studied, structure evolution was observed, and a comparison study with isothermal heat treatment of 6061 aluminum alloy was conducted. The results showed that cyclic heat treatment is a relatively finer and more globular non-dendrites microstructure compared with isothermal heating one for all heating time conditions. Semi-solid cyclic heat treatment is showing lower coarsening rate constant than that of the isothermal heat treated one because of coarsening discontinuous action of cyclic heat treatment(K Cyclic ~ 30%K Isothermal). Cyclic heating shows a relatively higher hardness for all heating times compared with isothermal heating one. Future research is required to investigate the effect of semi-solid cyclic heat treatment for sort heating time (less than 20 min) to decrease both coarsening and cracks that appear for heating time over than 30 min.
Keywords:
Cyclic heat treatment, Semi-solid, Microstructure, 6061Al alloy
Cite this paper: Naglaa Fathy , Microstructural Evolution of 6061 Al Alloy during Cyclic Semi-Solid Heat Treatment, American Journal of Materials Science, Vol. 4 No. 1, 2014, pp. 39-44. doi: 10.5923/j.materials.20140401.06.
1. Introduction
Aluminum is considered to be the second most plentiful metallic element on earth, became an economic competitor in engineering applications as recently as the end of the 19th century. It was to become a metal for its time. The emergence of three important industrial developments would, by demanding material characteristics consistent with the unique qualities of aluminum and its alloys, greatly benefit growth in the production and use of the new metal. Among the most striking characteristics of aluminum is its versatility. The range of physical and mechanical properties that can be developed, from refined high-purity aluminum to the most complex alloys, is remarkable. More than three hundred alloy compositions are commonly recognized, and many additional variations have been developed internationally and in supplier/consumer relationships. The properties of aluminum that make this metal and its alloys the most economical and attractive for a wide variety of uses are appearance, light weight, fabricability, physical properties, mechanical properties, and corrosion resistance[1].Generally speaking aluminum alloys have good mechanical properties, high corrosion strength and low density. Nowadays the fields of application of this kind of alloy are mainly the ones in which weight reduction is a critical factor, such as in aerospace applications, and in the field of transport in general. Al 6061-T6 belongs to the aluminum series 6000 with silicon and magnesium as the principal alloying components. The T6 suffix describes the heat treatment applied to the alloy, T6 stands for a two phase treatment. The entire process is based upon the precipitation hardening phenomenon and it results in a larger increment in strength with only a minimal reduction of the break elongation[2]. 6061 aluminum alloy is widely used in automotive and aerospace applications because of their high properties such as good strength, formability, weldability and corrosion resistance[3]. The influence of semi-solid isothermal heat treatment on microstructure of 6061 Alloy has been studied. It was found that the optimal partial remelting parameters should be 630℃ and 10–15 min for 6061 alloy cold rolled with 60% reduction in height of pre-deformation, otherwise, increasing the heating time above 15 min increase the chance for grain coarsening[3]. Regarding those mentioned above, this work is carried out to study microstructural (grain size and gain grain sphericity) evolution of 6061 Al Alloy during cyclic Semi-solid heat treatment for heating time above 15 min to maintain the optimum of both grain size and grain sphericity.
2. Experimental
The 6061 aluminum alloy studied in the present study was the commercial rod 6061-T6 (Cu 0.15-0.4%, Mg 0.8-1.15%, Mn 0.12%, Zn 0.25%, Cr 0.04-0.35%, Ti 0.15%, Si 0.4-0.8%, Fe 0.7%) of 20 mm diameter. The measured solidus and liquidus temperatures are 582.8℃ and 652℃, respectively as indicated by pervious study using differential scanning calorimetric analysis (DSC) for the semi-solid 6061 alloy[3]. Specimens of approximate dimensions φ20x20 mm rod were cut for cyclic and isothermal heat treatment as well as microstructure examination and hardness measurements. All specimens were heated to 630℃ in an electrically heated resistance furnace with heating rate of 10℃. min-1. For isothermal heat treatment sample was hold for 20, 30, 40 and 50 mins, respectively, otherwise for cyclic heat treatment in a complete cycle samples after 10 min holding at 630℃ were cooled to a temperature of 536℃ in still air cooling and were heated again to 630℃ for next 10 min heating time we tried one cycle lasts for 20 min, one and half cycle lasts for 30 min, two cycles lasts for 40 min, and two and half cycles lasts for 50 min. After the semi-solid heat treatment, the samples were taken out immediately for water quenching (see Fig. 1).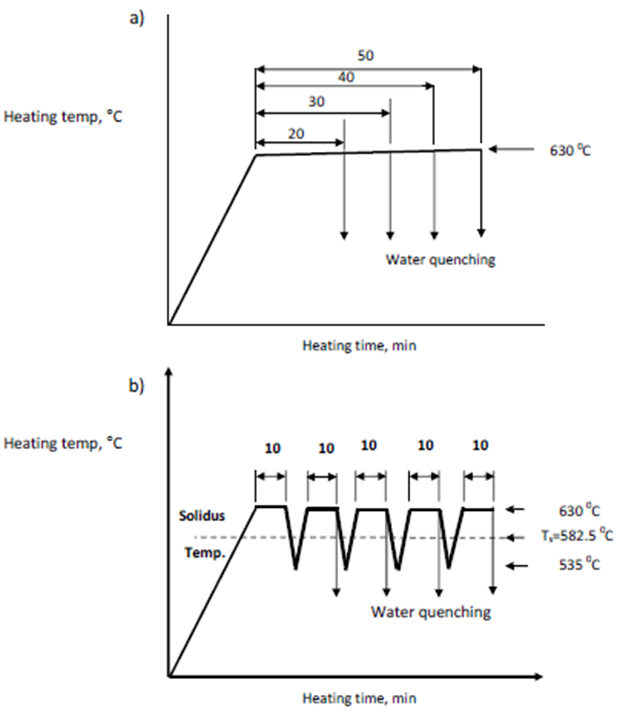 | Figure 1. Schematic illustration of the a) isothermal heat treatment process and b) cyclic heat treatment process |
Specimens in either as received or heat treated condition were grinded, polished, etched with a solution consist of 2% HF, 25% HNO3 and 73% H2O and examined metallographically using an optical microscope and photomicrographs were taken. Grain size and grain sphericity (S=4π (area of the grain/grain circumference2)) were measured and analyzed with Scentis image analyzer software (with errors 3%). Rockwell hardness test were also performed using 1/16 inch diameter ball and 60 kgf load.
3. Results and Discussion
The as-received microstructure of the experimental 6061 Al alloy shown in Fig. 2. It can be seen from Fig. 2a that the grains of as-received 6061 Al alloy clearly exhibits the rosette character for micrograph took for area at the edge and near the edge of specimen (Fig.2.b) but exhibits near spheroid for area at centre of specimen (See Fig. 2c). 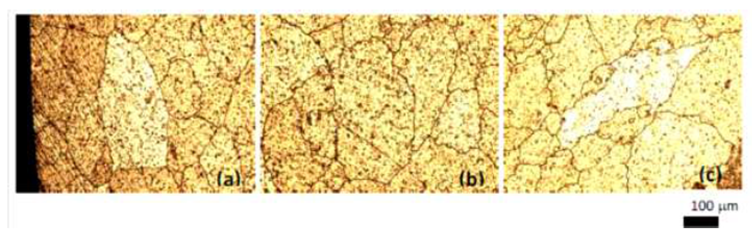 | Figure 2. Microstructure of as-received 6061 Al alloy, a) edge ,b)5mm from dege, and c) at centre |
Figures 3-5 show the microstructures of 6061Al alloy heat treated at 630℃ for 10, 20, 30, 40 and 50 min, respectively, of isothermal heating and cyclic heating. Fig.3 shows microstructure of isothermal heat treated and cyclic heat treated samples for different heating time at the edge of samples. It is noticed that the grain size and grain sphericity increase with increasing heating time for both isothermal and cyclic heat treated samples. Sample treated for 40 and 50 mins show macro and micro cracks formations. It is noticed also that microstructure of cyclic treating have fine and more globular gain structure compared with the isothermal heating one.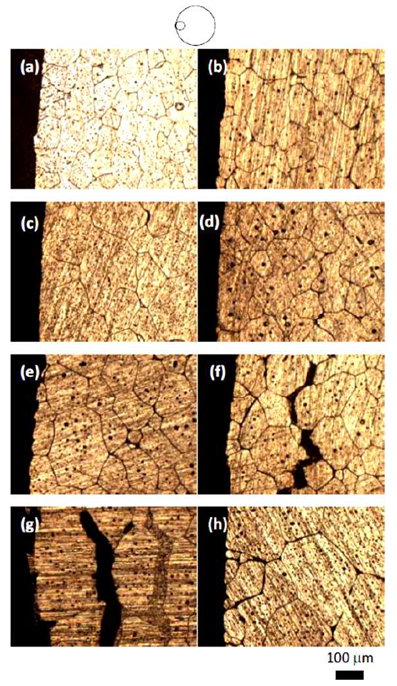 | Figure 3. Microstructure of isothermal heat treated (a, c, e, g) and cyclic heat treated (b, d, f, h) 6061 Alloy heat treated at the edge of samples for heating time of 20, 30, 40, 50 min respectively |
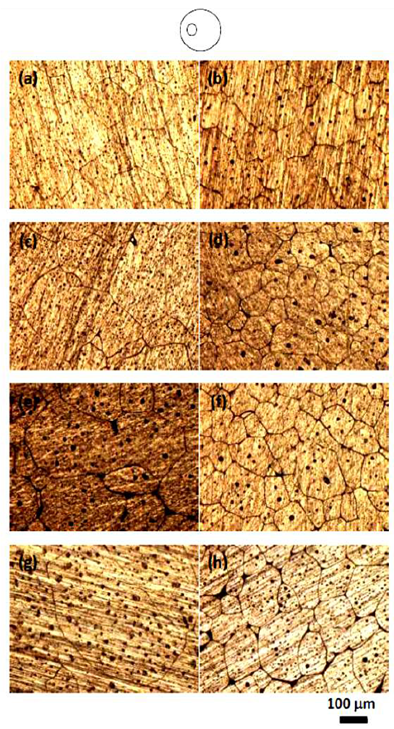 | Figure 4. Microstructure of isothermal heat treated (a, c, e, g) and cyclic heat treated (b, d, f, h) 6061 Alloy heat treated at the zone between edge and center of samples for heating time of 20, 30, 40, 50 min respectively |
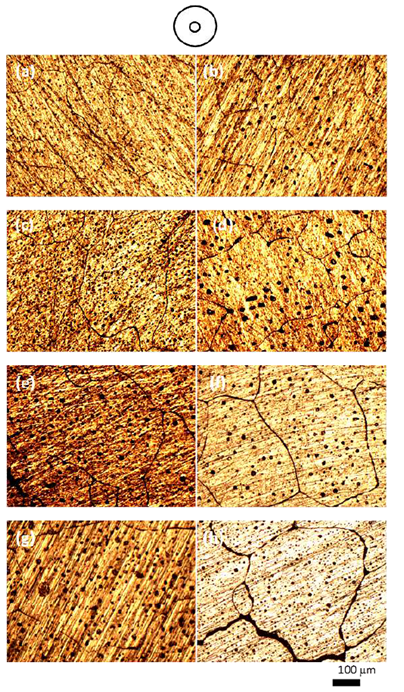 | Figure 5. Microstructure of isothermal heat treated (a, c, e, g) and cyclic (b, d, f, h) heat treated 6061 Alloy heat treated at the center of samples for heating time of 20, 30, 40, 50 min respectively |
Fig.4 shows microstructure of isothermal heating and cyclic heating for different heating time at the zone between the edge and the centre of samples (about 5mm from edge). It is noticed that microstructure of cyclic heat treated have fine and more globular gain structure compared with the isothermal heat treated one. A significant improvement of grain structure has been achieved using cyclic heating in spite of the coursing effect due to heating time in isothermal heating. Fig. 5 shows microstructure of isothermal heat treated and cyclic heat treated samples, for different heating time at the centre of samples. During reheating of both isothermal and cyclic heat treated samples, the microstructure evolves; extensive coarsening by increasing heating time that will have a deleterious effect on the final mechanical properties of the heat treated samples. In addition, if the grain size is too large, it will limit production of thin section products with considerable mechanical and physical properties. At the centre of sample, it is noticed also that microstructure of cyclic treated samples have finer and more globular gain structure compared with the isothermal treated one especially for samples treated for heating time of 20 and 30 min. For heating time of 40 and 50, the macro and micro cracks are observed. 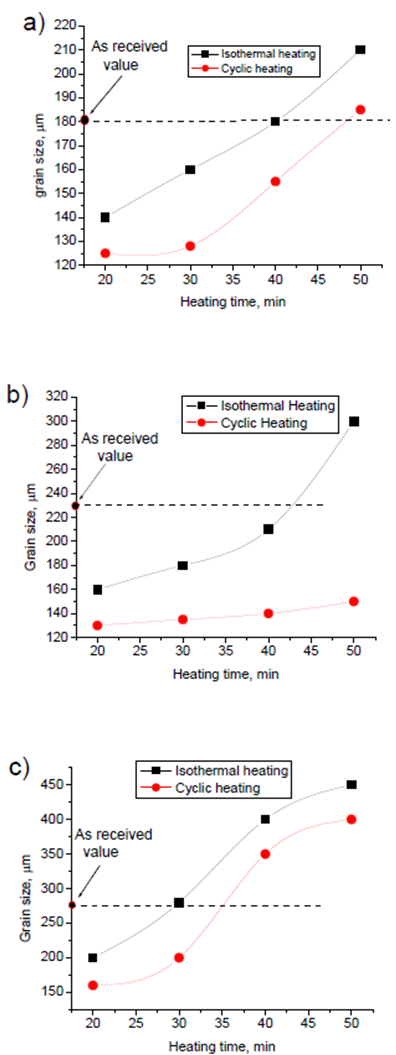 | Figure 6. Grain size for isothermal and cyclic heating for 6061 Al alloy at a) the edge, b) 5mm from the edge, and c) the centre |
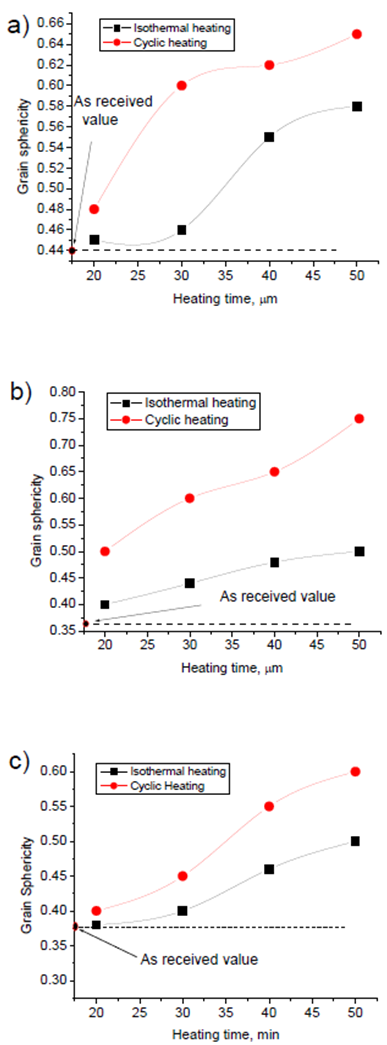 | Figure 7. Grain sphericity for isothermal and cyclic heating for 6061 Al alloy at a) the edge, b) 5mm from the edge, and c) the centre |
Figs. 6 and 7 show grain size and grain sphericity for isothermal and cyclic heating at edge, 5mm from edge and at the centre of samples. For all measurements, the cyclic heat treated samples has a relatively finer and more globular grain compared with isothermal heat treated one. Area between the edge and centre (about 5 mm form edge) of specimen shows significant effect of cyclic heat treatment on improving the grain microstructure. This significant effect because of its moderate heating and cooling rate otherwise, the edge that exposed to relatively higher heating and cooling rate and the centre that exposed to relatively slow heating and cooling rate. Fig. 8 show hardness measurements of both isothermal and cyclic heat treated for heating time range from 20 to 50 mins. Hardness values for both isothermal and cyclic heating decrease with increasing heating time. Hardness values for both isothermal and cyclic heat treated samples are relatively higher than the hardness value of as-received one for all heat treating time range (20-50 mins.). Cyclic heat treated samples shows a relatively higher hardness for all heat treating times compared with isothermal heat treated one.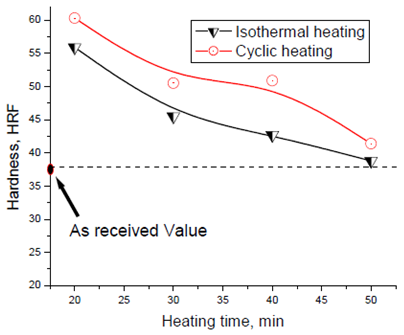 | Figure 8. Hardness as a function of heating time for isothermal and cyclic heating |
Previous research[4] indicated that during partial melting and then holding in the semi-solid state, coarsening first proceeds through the coalescence of dendrite arms. After coalescence, phase coarsening will take place through the dissolution of the small globules and the grain numbers will then decrease. During partial remelting[3], the alloy was heated up to a temperature at which the solid and liquid phases coexist in equilibrium. Its features lie in obtaining the desirable nominal liquid fraction through the control of temperature, and realizing long-time holding to ensure complete transition from dendritic or rosette to spherical. However, a long-time holding often results in the coarsening of grains, which is detrimental to the mechanical properties of produced parts. Many researchers[5] have studied the coarsening behavior of different semisolid alloys by using the Lifshitz, Slyozov and Wagner (LSW) theory[6, 7] which gives a simple form as follows. | (1) |
Where d is the average particle diameter at time t, d0 at time t=0 and K is the coarsening rate.The coarsening rate for isothermal and cyclic heating of 6061 Al alloy was calculated by using Eq. (1). It was found that cyclic heat treated 6061 Al alloy is showing lower coarsening rate constant than that of the isothermal heat treated one because of coarsening discontinuous action of cyclic heat treatment (K Cyclic ~ 30%K Isothermal). During the isothermal treatment in semi-solid state, increasing heating temperature resulted in higher liquid fraction in the parts. As the liquid fraction is increased most of the precipitated phases, which are strengthening phases in the structures, are continuously dissolved in the liquid phase[8] resulting in higher coarsening rate. Otherwise, during the cyclic heat treatment, the short time heating followed by cooling will relatively decrease the rate of precipitates migration to liquid. The relatively high precipitates remain in solid phase could be the reason of relatively decreases the coarsening rate in cyclic heat treatment.In the present work, values of grain size for both cyclic and isothermal heating is relatively higher compared with other pervious research[3,8] of the same 6061 Al alloy. The relatively higher values are believed to relatively long heat time range (20 to 50 min.). This is the reason of presence the higher coarsening rate and the crack formation specially for heating time more than 30 min. For this concept, future research become necessary for short heating time of cyclic heating in order to achieve a relatively finer and globular gain structure of 6061 Al alloy.
4. Conclusions
In this research new cyclic semi-solid heat treatment were presented for a commercial 6061 aluminum alloy. The following results were obtained:1. Cyclic heat treatment shows a relatively finer and more globular grain compared with isothermal heating one.2. Cyclic heat treated 6061 Al alloy showing lower coarsening rate constant compared with isothermal heat treated one due to coarsening discontinuous effect.3. Heating time should be limited for 30 min. or less in order to maintain fine grain size and globular structure without cracks and severe grain coarsening. 4. Cyclic heating shows a relatively higher hardness for all heating times compared with isothermal heating one due to its finer and globular structure.5. Future research is required to investigate the effect of cyclic heat treatment for sort heating time (less than 20 min).
ACKNOWLEDGMENTS
The author would like to thank staff of college of Engineering at University of Hail, Saudi Arabia for their kind help in measurements.
References
[1] | ASM Metals Handbook, Vol 02-Properties and Selection Nonferrous Alloys and Special-Purpose Materials, 1990, USA. |
[2] | A. Gilioli, A. Manes, M. Giglio , Numerical simulation of a fracture toughness test of an Al6061-T6aluminium alloy using a ductile criterion, Mechanics Research Communications, to be published. |
[3] | N. Wang, Z. Zhou and G. Lu, Microstructural Evolution of 6061 Alloy during Isothermal Heat Treatment, J. Mater. Sci. Technol., Vol. 27, Issue 1, PP 8-14, 2011. |
[4] | H. V. Atkinson, D. Liu, Coarsening rate of microstructure in semi-solid aluminium alloys, Trans. Nonferrous Met. Soc. China Vol. 20 PP1672−1676,2010. |
[5] | G.W. Greenwood: Acta Metallurgica, The growth of dispersed precipitates in solutions, Vol. 4, Issue 3, PP 243–248, May 1956. |
[6] | C. Wagner: Acta Metallurgica, The evaluation of data obtained with diffusion couples of binary single-phase and multiphase systems, Vol. 17, Issue 2, PP 99–107, February 1969. |
[7] | I.M. Lifshitz and V.V. Slyozov: Phys. Chem. Solids. The kinetics of precipitation from supersaturated solid solutions, Volume 19, Issues 1–2, PP 35–50, April 1961. |
[8] | D. Abolhasani, H.R.Ezatpour, S.A.Sajjadi and Q.Abolhasani, Microstructure and mechanical properties evolution of 6061 aluminum alloy formed by forward thixoextrusion process, Materials and Design, Volume 49, PP 784–790, 2013. |