Fapohunda Christopher1, Oyelade Akintoye2, Ajibade Charles2
1Department of Building, Caleb University, Imota, Lagos, Nigeria
2Department of Civil and Environmental Engineering, University of Lagos, Akoka, Nigeria
Correspondence to: Fapohunda Christopher, Department of Building, Caleb University, Imota, Lagos, Nigeria.
Email: |  |
Copyright © 2012 Scientific & Academic Publishing. All Rights Reserved.
Abstract
This paper presents the results of investigation conducted to evaluate the properties of concrete containing aluminum Roofing Sheet Waste as partial replacement of cement by weight. The properties investigated included the setting times of cement-ARSW paste, workability, density, compressive strength using 168 numbers of 150 x 150 x 150 mm cube specimens. The chemical compositions and pozzolanic properties were also investigated. The results showed that: (I.) the chemical composition of aluminum Roofing Sheet Waste (ARSW) is suitable for concrete production, (ii.) ARSW has pozzolanic characteristic, (iii.) the concrete produced with ARSW resulted in concrete whose densities are within the range for normal weight concrete, and (iv.) using ARSW to replace cement up to 10% will not affect the compressive strength of the concrete significantly. From these results, it can be concluded that Roofing Sheet Waste is suitable for concrete production, and thus can be used as a mean to remove the potentially harmful waste that ARSW constitutes.
Keywords:
Compressive Strength, Concrete, Roofing Sheet Waste, Setting Times, Workability
Cite this paper: Fapohunda Christopher, Oyelade Akintoye, Ajibade Charles, Some Properties of Concrete Containing Aluminum Roofing Sheet Waste (ARSW) as Partial Replacement of Cement, American Journal of Materials Science, Vol. 4 No. 1, 2014, pp. 18-24. doi: 10.5923/j.materials.20140401.04.
1. Introduction
Generation of construction and demolition wastes (CDW), arising from changes in infrastructure planning and needs for homes, schools, hospitals, offices, and roads required for effective and efficient functioning of the built environment and from other myriads of human activities concomitant to the current civilization continues to be on the increase. According to[1], an estimated 900 million tonnes of CDW are generated every year in Europe, the United States of America and Japan. The works of[2] showed that the annual waste arising from building demolition alone is 400million tons per annum in China. The construction and demolition wastes (CDW) are difficult to dispose and cause serious health hazards and environmental problems[3, 4]. Environmental agencies and governments’ policies seek to minimize the problems of disposal and health hazards of these wastes and by- products. The productive use of these materials is one of the best ways to alleviate some of the problems of the solid waste management. Using these wastes for concrete production, if found suitable, would thus be an effective and innovative solution. Since concrete constitutes the major construction material, whose consumption is second to water, and the production of its constituents – cement and aggregates - requires extraction of huge amount of non-replaceable raw material from the earth and consumption of large amount of energy, leading to environmental degradation and environmental pollution resulting from greenhouse gas emission; utilizing these wastes for concrete making can contribute towards sustainable development and construction. Because of the environmental and economical reasons, there has been a growing trend for the use of construction wastes as supplementary material in the production of the concrete[5]. Some of construction wastes that have been found suitable for concrete production, through research efforts are: crushed concrete[6, 7, 8, 3, 9, 10, 11, and 12]. They are either being used as partial replacement of cement, or as partial replacement of sand. There use have been found to improve workability, improved the strengths, and enhance the performance of all manner of concrete (lightweight, normal weight and heavyweight). However, one of the construction and demolition wastes that is yet to be investigated for potential application in concrete production is aluminum roofing sheet waste (ARSW). Roofing sheet waste is generated from house demolition activities, in an attempt to replace old houses with new ones in the present policy of urban renewal of old structures being pursued in the developing world, especially Nigeria, by all the tiers of government. Thus the aim of this investigation is to find out to what extent ARSW can be used in the production of concrete, as part of strategy to find suitable replacement for cement usage in the developing world, especially in Nigeria, where about 15% of her annual budget is required to meet her cement needs[13]. For this aim to be accomplished, the objectives set to achieve, by working on concrete with ARSW specimens include: determination of its chemical composition and pozzolanic characteristics, investigation of the initial and final setting times of cement-ARSW paste, assessment of its workability and density, and the evaluation of its compressive strength development – which is a reflection of the structural performance of concrete[14].
2. Materials and Methods
2.1. Materials
The materials used for this work are cement, fine aggregates, coarse aggregates, water, and ARSW as partial replacement of cement by weight. Ordinary Portland cement produced in accordance to[15] was used. The fine aggregates used in this research study was River Sand obtained from Ogun River located at Ogun State. The particle sizes of sand were those passing through sieve with aperture size of 3.35 mm but retained on sieves of 63µm and having a bulk density of 1540 kg/m3. It was confirmed to be salt free and free from deleterious substances. The coarse aggregates used in this research study were granite chippings with particle size range between 2.36mm and 20mm. The aluminum roofing sheet waste was obtained from a demolition site. It was originally produced by Nigerite Limited Ikeja, Nigeria. The waste was milled to fine powder; 80% passed through 1.18mm sieve, and was store in a cool place. The Sample of the milled ARSW is shown in Figure 1. Portable water which was fresh, colourless and odourless and free of organic matter was used in these experiments. For this purpose of this investigation, a mix ratio of 1:2:4 by weight of cement, sand and gravel; and the water cement ratio of 0.4 was adopted.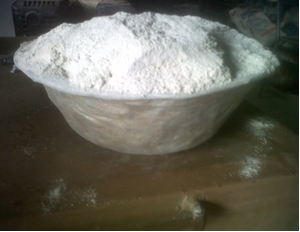 | Figure 1. Roofing sheet waste (milled) |
2.2. Methods
2.2.1. Chemical Analysis
In order to determine the constituents of ARSW, samples were subjected to analysis using the combination of Spectrophotometer, Atomic Absorption Spectrophotometer and Gravimetric methods at the Department of Chemistry, University of Lagos, Nigeria.
2.2.2. Pozzolanic Test
In order to determine its pozzolanic traits a method used by[16] was adopted. 100ml of saturated carbon hydroxide, Ca(OH)2) solution was mixed with 20g of ARSW. The solution was then stirred magnetically. At the intervals 1, 2, 3, and 4hours; 10ml of the solutions was filtered and titrated against 0.25N HCl using phenolphthalein indicator. The amount of the Ca(OH)2 that reacted with ARSW was then calculated from the titre value. The reaction between Ca(OH)2 and ARSW was assessed at the temperatures of 25℃ and 75℃.
2.2.3. Consistency (Water Demand) and Setting Times Tests
Water requirement to achieve the standard consistency of cement paste and setting times (initial and final) was carried out in accordance with[17], by partially replacing cement with ARSW at different cement replacement levels of 10%, 20%, 30%, 40%, and 50%. Water demand for standard consistency was and setting times determined for each percentage replacement of cement with ARSW. The water demand for zero replacement of cement with ARSW serves as the control.
2.2.4. Workability Test
The slump test was carried out in accordance with the provisions of[18]. The replacement was done at the interval of 10% up to 50% cement replacement with ARSW. The sample without ARSW (that is, 0%) serves as the control.
2.2.5. Density and Compressive Strength Test
Density and Compressive strength tests were conducted on 150x150x150 cube specimens, at 7-, 14-, 21-, and 28-day curing ages respectively in accordance with[19, 20]. A total of 168 numbers of 150 x 150 x 150 cube specimens were prepared. All the cubes specimens were cured by immersion in water right from the moment they were removed from the moulds – 24 hours after casting - until the day for their testing when they were removed from the curing water tank and sun dried before being tested for strength. The compressive strength test was carried out on the cube specimens at curing age of 7, 14, 28, and 60 days. The specimens preparations and testings were in accordance with[20]. The cement replacement with ARSW was up to 30% at interval of 5%. The limit of 30% cement replacement with ARSW was determined from the result of the initial and final setting times. The weight of each cube was taken prior to compressive strength test, and was used to calculate the density.
3. Results and Discussions
3.1. Physical Properties of the Materials Used
The physical properties of the materials used in this investigation are shown in Table 1.Table 1. Physical properties of the Materials Used 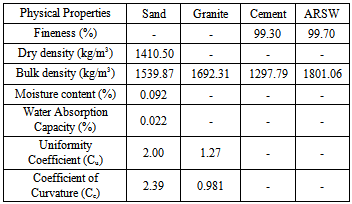 |
| |
|
From the Table, it can be observed that ARSW was found to be a little bit finer than the ordinary Portland cement used, and also possess a higher bulk density. This means that, for the same weight, a lower volume of ARSW is required. The values of uniformity coefficient of sand and granite were 2.0 and 1.27 respectively, and were within the range of suitability for concrete production[16]. Also the coefficient of curvature of 2.39 and 0.981 for sand and granite respectively signify well-graded material[21], and thus suitable for concrete production.
3.2. Chemical Analysis
The result of the chemical analysis is presented in Table 2. From Table 2, it can be observed that ARSW has a lower oxide of calcium with respect to the ordinary Portland cement, but a higher aluminates. The high content of the aluminates is obviously due to the fact of its origin. However, the alkalis (K2O and Na2O) with a combined percentage of 0.41% are low. This reduce the possibility of the destructive alkali-aggregate reaction[22].Table 2. Chemical Composition of Cement and ARSW 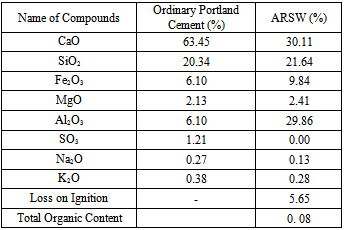 |
| |
|
In order to determine the potential of ARSW as a pozzolan, its chemical properties were compared with[23] specifications (Table 3).Table 3. Comparison of the Pozzolanic Specifications of ASTM C618 -93 with ARSW 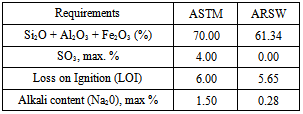 |
| |
|
Although, the combined percent content of Si2O + Al2O3 + Fe2O3 of ARSW, on which pozzolanic activity depends, is less than 70% (Table 3), as recommended by[23] for classification as highly pozzolanic, it however can be classified as Class C, to be used for general purpose concrete. This is because of the fact that the combined percent content of Si2O + Al2O3 + Fe2O3 is more than 50%, and it is high in calcium oxide, CaO (> 10%). The results of further investigations into the pozzolanic properties of ARSW are shown figure 2. Figure 2 shows the relationship between the quantities of calcium hydroxide that reacted with ARSW at different times and temperatures. 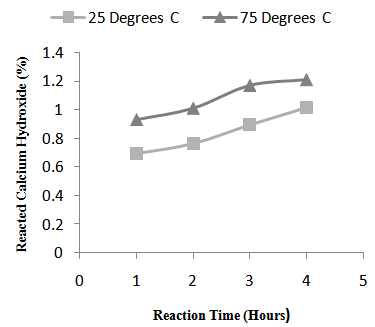 | Figure 2. Reaction between Calcium Hydroxide and ARSW at different times |
From this figure, two observations are made. First, the amount of calcium hydroxide that reacted with ARSW increased with time, irrespective of the temperatures. This is an indication that ARSW is able consume or react with calcium hydroxide to produce the strength-forming C-S-H gel, and that this reaction increases with age. Secondly, the reaction between the calcium hydroxide and ARSW is influenced by temperatures. Higher reactivity occurred at the higher temperature of 75℃. This is to be expected for all chemical reactions which are influenced by temperatures. The conclusion from these two observations is that ARSW is able to react with calcium hydroxide, thus establishing its pozzolanic status. And that the pozzolanicity of ARSW is influenced by temperatures.
3.3. Effects of ARSW on Consistency of Cement Paste
The effects of ARSW on the consistency of cement paste are presented in Figure 3 and Figure 4. From Figure 3, it can be observed that water demand for standard consistency increased with increasing ARSW in the paste in relation to the control sample (0% ARSW). This is an indication that inclusion of ARSW in the mix increase the amount of water required to obtain a paste of standard consistence.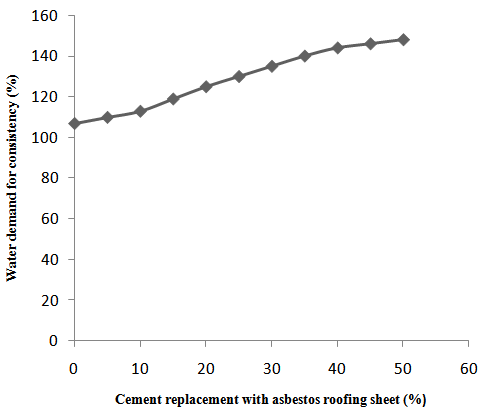 | Figure 3. Water demand of Cement-ARSW Paste |
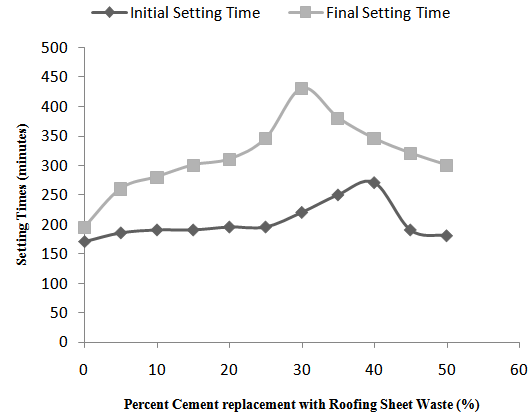 | Figure 4. Effects of ARSW on the Setting Times of Cement-ARSW Paste |
This behavior might be due to the fact that ARSW was found to be finer than Portland cement (Table 1). The effect of ARSW on the initial and final setting times is presented in Figure 4.From the figure, it can be observed that both the initial and final setting times increased with cement replacement with ARSW up to a point and then decreased. For example, for the initial setting time, the decrease began at 40% cement replacement with ARSW. However, the decrease in the final setting time occurred at 30% cement replacement with ARSW. At the 50% cement replacement with ARSW, the initial and final setting times were 187minutes and 345 minutes respectively. Comparing these values with the control values of 170minutes and 195minutes respectively for initial and final setting times, the ARSW has a retarding effect on the paste.
3.4. Effect of ARSW on Workability of Concrete
At all the replacement levels, the slump type was “true slump”, indication that the inclusion of ARSW has no effect on the cohesiveness of the mix to the extent of resulting in shear slump, or collapse slump. The effect of ARSW on the workability of concrete measured in terms of loss of slump is as shown in the Figure 5.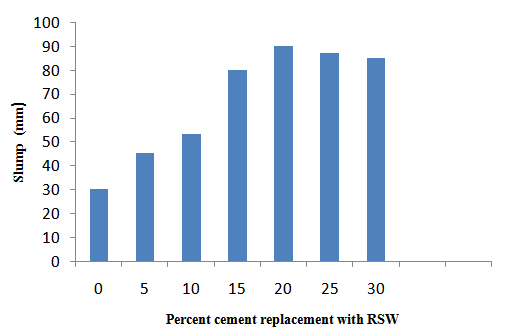 | Figure 5. Variation of Slum with ARSW Replacement |
It can be observed from the Figure that slump loss increased upon the inclusion of ARSW as partial replacement of Ordinary Portland Cement until 20% cement replacement with ARSW, when it began to decrease. The slump value increased from 30mm at 0% cement replacement with ARSW to 90mm at 20% cement replacement with ARSW. A reduction of 85mm was however observed at 30% cement replacement with ARSW. With these slump values, the workability is affected greatly by the inclusion of ARSW in the mix, when compared with the control. The control sample (0%) with loss of slump of 30mm is of low workability according to[24] and[22]. However, the addition of ARSW changes the classification from medium (35 – 75mm) to high (80 – 155mm). Thus the inclusion of ARSW increases the slump values of concrete. This trend is consistent with the Figure 3 in which increase in water demand accompanied increased in ARSW.
3.5. Effects of ARSW on Density of Concrete
The results of the density test, for all the cement replacement with ARSW, are presented in Table 4.Table 4. Variation of Density in kg/m3 with addition of RSW 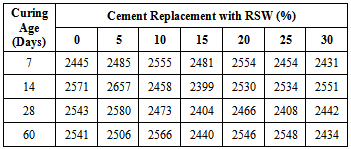 |
| |
|
Although, no consistent pattern is noticeable in the results, either with respect to curing age or with the addition of ARSW, it is however obvious from the values of the densities that all were in the range recommended for normal weight concrete[25]. Thus the use of ARSW will result in the production of normal weight concrete.
3.6. Effects of ARSW on Compressive Strength
The effect of ARSW on the compressive strength development of concrete is presented in Figure 6. From the figure, it can be observed that compressive strengths increased with curing ages at all the replacement level. There is however strengths reduction with cement replacement with ARSW at all the curing ages. For example, at 5% replacement level, there was 4.63% reduction in the strength development in relation to the control specimens (0%) at 28 days of curing. However, at 60 days of curing, the strength reduction was a just 0.51%. At 10% cement replacement with ARSW, the strengths reductions were 25.14% and 17.75% respectively for 28 days and 60 days of curing. These trends of strength reduction were observed for all the specimens. 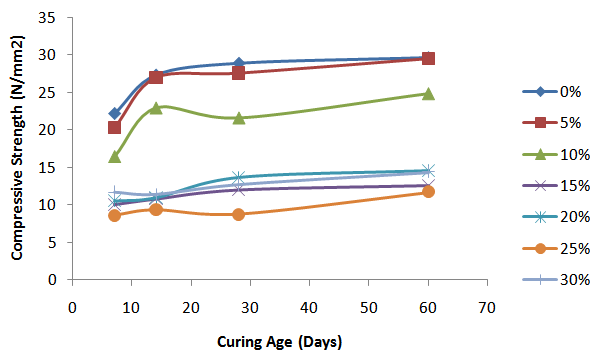 | Figure 6. Variation of Compressive Strength with Curing Age |
Using a 5% confidence interval, the critical value is 4.303. But at 28 and 60 days of curing, the computed critical values were less than 4.303 for cement replacement with ARSW up to 10%, being -1.39 and -0.80 for 28 days curing age and -4.125 and -3.2527 for 60 days curing age. This is an indication that for up to 10% cement replacement with ARSW, there is no significance difference in strength compared with the control sample. Beyond 10% cement replacement with ARSW however, the difference was found to be statistically significant.
4. Conclusions
The main conclusions derived from this investigation are as follows:1) The chemical composition of Roofing Sheet Waste (ARSW) is suitable for concrete production2) Roofing Sheet Waste (ARSW) has pozzolanic characteristic.3) Roofing Sheet Waste (ARSW) has a retarding effect on cement-ARSW paste. This property can find a good usage in hot weather concreting.4) The use of Roofing Sheet Waste (ARSW) to produce concrete will result densities in the range for normal weight concrete.5) The use of Roofing Sheet Waste (ARSW) to replace cement up to 10% in the production of concrete will not affect the compressive strength of the concrete.Although, the present work looked at the quality of concrete produced with ARSW as partial replacement of cement from the point of view of compressive strength, further investigations need to be carried further on the tensile and flexural characteristics of concrete containing Roofing Sheet Waste (ARSW) as partial replacement of cement. This is necessary so as to develop proper relations between compressive strengths and tensile strengths.
References
[1] | WBCSD (2009). “Dedicated to Making A difference – The Cement Sustainability Initiative”. www.wbcsdcement.org (assessed 10/8/2013). |
[2] | Ma, X. and Wang, Z. (2013). “Effect of Ground Waste Concrete Powder on Cement Properties”. Advances in Materials Science and Engineering, 2013. |
[3] | CCAA (2008). “Use of Recycled Aggregates in Construction”. Cement Concrete & Aggregates Australia. |
[4] | Corinaldesi V, Moriconi G, Naik TR (2010). “Characterization of Marble powder for its Use in Mortar and Concrete”. Const. Build. Mat., Vol. 24, pp. 113-117. |
[5] | Krishna, V. and Sabnis, G. M. (2013). “Utilization of Waste Products and By- Products in Concrete: The Key to a Sustainable Construction”. International Conference on Civil and Architecture Engineering (ICCAE'2013), Kuala Lumpur, Malaysia. |
[6] | RMC (2007). “Crushed Returned Concrete as Aggregates for New Concrete”. Final Report to the RMC Research & Education Foundation, Project 05-13. |
[7] | Finoženok, O; Žurauskienė, R. and Žurauskas, R. (2011). “Influence Of Various Size Crushed Concrete Waste Aggregates On Characteristics Of Hardened Concrete”. 3rd International Conference CIVIL ENGINEERING`11 Proceedings BUILDINGMATERIALS. |
[8] | Katz, A. (2002). “Properties of Concrete made with Recycled Aggregates from Partially Hydrated old Concrete”. Cement and Concrete Research, 33: 703–711. |
[9] | CCANZ (2011). “Best Practice Guide for the use of Recycled Aggregates in New Concrete”. A Technical Report published by the Cement & Concrete Association of New Zealand. |
[10] | Bazaz, J. B., Khayati, M.and Akrami, N (2006) “Performance of concrete produced with crushed bricks as the coarse and fine aggregate”. IAEG2006 Paper number 616, The Geological Society of London, 1 – 10. |
[11] | Rashid, M. A., Hossain, T., and Islam, M. A. (2009). “Properties of Higher Strength Concrete made with Crushed Brick as Coarse Aggregates”. Journal of Civil Engineering (IEB), 37 (1): pp. 43 – 52. |
[12] | Jankovic, K., Bojovic, D., Dragan, N., Loncar, L. and Ramakov, Z. (2010). “Frost Resistance of Concrete with Crushed Bricks as Aggregates”. Facta University: Architecture and Civil Engineering, 8 (2): 155 – 162. |
[13] | Falade, Funso, Ikponmwosa, Efe. and Fapohunda, Chris (2013) “Low-Cost Construction through the Use of Pulverized Bone Foamed Aerated Concrete (PB-FAC)”. Civil and Environmental Research, Vol. 3, No. 10, pp. 107 – 113. |
[14] | Wright, J. K. and MacGregor, J. G. (2009). “Reinforced Concrete: Mechanics and Design”. New York: Pearson Education International. |
[15] | NIS 444 (2003). Standard for Cement. Standard Organization of Nigeria, Lagos. |
[16] | Salau, M. A. and Olonade, K. A. “Pozzolanic Potentials of Cassava Peel Ash”. Journal of Engineering Research, No. 1, March 2011, pp. 10 – 20. |
[17] | BS 12 (1996). “Specification for Portland Cement”. British Standard Institution, London. |
[18] | BS EN 12350: Part 2 (2000). “Method for Determination of Slump”. British Standards Institution, London. |
[19] | BS EN 12390-7 (2009) “Testing Hardened Concrete: Density of Hardened Concrete”. British Standard Institution, London. |
[20] | BS EN 12390-3 (2009). “Testing Hardened Concrete: Compressive Strength of Test Specimens”. British Standard Institution, London. |
[21] | Terzaghi, K., Peck, R. B. and Mesri, G. (1997). “Soil Mechanics in Engineering Practice”. New York: John Wiley. |
[22] | Neville, A. M. (2010) “Properties of Concrete”. London: Pearson International. |
[23] | ASTM C618-93 (1993) “Standard Specification for Fly Ash and Raw or Calcined Natural Pozzolan for Use as a Mineral Admixture in Portland cement Concrete”. American Society for Testing and Materials, USA. |
[24] | Shetty, M. S. (2005). “Concrete Technology – Theory and Practice”. Bombay: S. Chand and Company Ltd. |
[25] | Falade, F., Ikponmwosa, E. and Arogundade A. (2011). “Investigation of Some Structural Properties of Foamed Aerated Concrete”. Journal of Engineering Research, 16(1): 67 – 81. |