S. O. Adeosun1, Akpan E. I.2, Gbenebor O. P.1
1,3Department of Metallurgical and Materials Engineering, University of Lagos, Lagos, Nigeria
2Department of Materials and Production Engineering, Ambrose Alli University, Ekpoma
Correspondence to: Akpan E. I., Department of Materials and Production Engineering, Ambrose Alli University, Ekpoma.
Email: |  |
Copyright © 2012 Scientific & Academic Publishing. All Rights Reserved.
Abstract
Effect of initial temperature and state of wrought aluminum, die angle and die material on the extrusion characteristics of wrought aluminium alloy has been studied. Extrusion dies were constructed with die angles ranging from 15 to 90o using both tool steel and mild steel materials. Cold, hot and annealed billets extrusion responses were investigated by measuring the extrusion pressure, linear strain, extrusion ratio and surface hardness of extrudes. Results show that tool steel die provides superior extrusion response to mild steel die material. The highest linear strain (202 %) was obtained for samples cold extruded using tool steel die with a 90o die angle followed annealed extruded (161 %) sample using tool steel die at the same die angle. Cold extrusion was observed to be easier at higher die angles than at lower die angles. Hardness result also indicates that structural change due to severe plastic deformation during extrusion was effective for the improvement of hardness.
Keywords:
Extrusion Pressures, Die Material, Die Angle, Plastic Deformation and Annealed
Cite this paper: S. O. Adeosun, Akpan E. I., Gbenebor O. P., Extrusion Characteristics Dependence of Wrought Aluminium Alloy on Extrusion Variables, American Journal of Materials Science, Vol. 3 No. 4, 2013, pp. 77-83. doi: 10.5923/j.materials.20130304.03.
1. Introduction
Extrusion is one of the most important metals forming processes due to its high productivity, lower cost and increased physical properties[1]. Extrusion of aluminium alloys offers a relatively cheap method of producing complex shapes in long lengths with high geometric tolerances. The flexibility of the process with respect to alloys that can be extruded and the possible shapes has resulted in widespread use of aluminium extrusions in the society today. Aluminium extrusions are used in the building industry (window and door frames, building structures, roofing, curtain walling, etc.), shipping and offshore industry, furniture, and in automotive, aerospace applications and rail vehicles.There has been considerable interest in the investigation of the effects of die geometry and other extrusion parameters on the structure, flow pattern, extrusion pressure and mechanical properties of shaped sections[2-3]. Severe Plastic Deformation (SPD) processes have been receiving increasing attention as one method to develop fine-grained microstructures. Determination of the required load is one of the important objectives in metal forming studies. When the necessary force for performing the operation is minimized, the capacity of the forming machine and the relevant costs can be reduced and the die life prolonged[4]. Geometry and profile of an extrusion die constitute very important aspect of die design and determines the extent of redundant work done during the deformation. Although redundant work cannot be totally avoided in extrusion process, it can be minimized by choosing a die profile that minimizes the extrusion pressure [5]. The influence of die half-angle and reduction ratio on extrusion force has been studied for the hydrostatic extrusion process and the data obtained can be used for the forward conventional extrusion process[6]. Experimental investigations have been made to achieve the effect of die reduction ratio, die angle and loading rate on the quality of cold extruded parts, extrusion pressures and flow patterns for both lead and aluminum[7]. Previous research has shown that extrusion die geometry, frictional conditions at the die billet interface and thermal gradients within the billet greatly influence metal flow in cold extrusion[8]. Another investigation reported the effects of die geometry and other extrusion parameter on the structure, flow pattern, extrusion pressure and mechanical properties of shaped extrusion[9]. In addition, 300, 450 and 600 die angles has been used to study the effect of die angles on the surface finish and hardness of cold extrusion of aluminum AA 6351 and AA1100[10]. These and many other works has presented the need to investigate fully the characteristics of extrusion at various die angles and their effect on emerging properties.On the other hand the interaction between the die and surrounding plays a major role in initiation of soldering, micro-cracking, crack propagation and catastrophic failure, especially in high temperature working environment which results in premature failure such as heat and gross cracking, erosive wear, solder and corrosion[11]. To serve such working environment, the selection of material becomes crucial. The chosen material must be able to withstand high mechanical and thermal loading, good resistance to wear and failure. Bjork et al.[12] states that the wear resistance of extrusion die play a major role in terms of technological and economical aspect because it affects both the surface finish and dimension of the extrudate. Tool steel is the material widely used to serve such working environment and signifies a family of highly alloyed steels that can be hardened and tempered with guaranteed hardening characteristic to provide improved strength and wear resistance[13]. However, mild steel which is cheap and affordable has not been investigated as the working environment in relation to the conventional tool steel die material.In this study the authors investigate the effect of extrusion die angle, extrusion conditions (cold, hot and annealed) and die material on the extrusion characteristics (extrusion pressure, extrusion ratio, surface hardness of extrudates and linear strain) of wrought aluminium alloy using experiments designed by the authors. The major objective of this research is to experimentally investigate how changes in die angle and die material affect extrusion force, extrusion ratio and linear strain. Results are purely experimental and does not depend on any model hence we will only present results as they were acquired from the experiments. Extrusion dies were constructed with 15, 30, 45, 60, 75, and 90o using both tool steel and mild steel materials for the study. Some billets were extruded cold while some were extruded hot and some annealed before extrusion.
2. Experimental methods
Materials Table 1. Chemical composition of wrought aluminium  |
| |
|
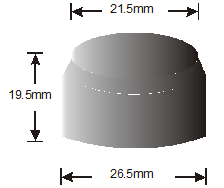 | Figure 1. Sketch of billets prepared for extrusion |
Wrought aluminium alloy billets of composition shown in Table 1 were obtained from Aluminium Rolling Mills Ota, Ogun State Nigeria for the study. Billets of the received alloy were melted and cast into cylindrical shapes of 3 by 30 mm in a sand mould and left to solidify. Cast samples were removed and machined to have a chamfer at the edge to allow entrance into the extrusion orifice (see Figure 1)Die DesignDies (see Figure 2) with entry angles of 15, 30, 45, 60, 75, and 90 degrees were designed with annealed mild and normalized tool steel materials of compositions shown in Table 2. All mild steel dies were heated in a furnace to 850℃, held for three hours and allowed to cool in the furnace. All tool steel dies were heated to 750℃, held for three hours and cooled in air.Table 2. Chemical composition of tool and mild steel die 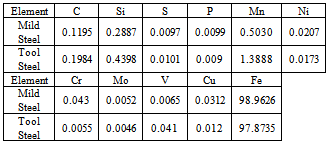 |
| |
|
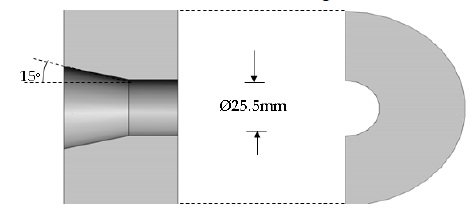 | Figure 2. Sketch of the die design |
Extrusion ProcessAn Avery Dension machine was adapted to exert compressive load on the ram for the extrusion process. The die was fixed into the form tool with a die holder fastened at the edge with three Allen screws (see Figure 3) and the billet inserted through the upper part of the assembly. The extrusion load was read directly from the machine as the load was applied. A strain gauge was attached to the ram to read the strain rate. Shea butter oil was used as the lubricant for the extrusion. Three types of extrusion were made including;1. Hot extrusion2. Cold extrusion3. Annealed extrusionIn hot extrusion the billets were heated in a Muffle reheating furnace to 350℃and transferred to the extrusion assembly for extrusion. In annealed extrusion the billets were heated to 350℃ and allowed to cool in the furnace before transferring it for extrusion. Cold extruded billets were used in as-cast condition at ambient temperature (32℃). A Leco micro hardness tester LM 700AT machine was used for the Rockwell hardness test of extruded samples.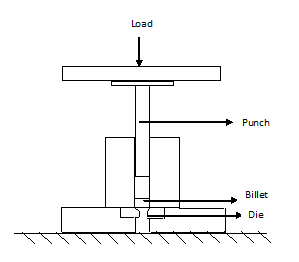 | Figure 3. Sketch of the extrusion assembly |
3. Results and Discussion
Effect of die angle on cold extrusion characteristicsThe extrusion behaviour of wrought aluminium alloys cold extruded at different die angles is shown in Figure 4. Extrusion in 15o die shows a steady increase in extrusion pressure with ram displacement throughout the extrusion process to maximum of 480 MPa before remaining constant. The 15o die shows behaviour different from the others indicating the difficulty in extrusion at the onset of the extrusion process but afterwards became normal after a ram travel of about 19 mm. This behaviour was earlier noted by Akbar and Yaseen[14] for AA2014 and AA1015 alloys and may be attributed to the fact that small die angle give rise to a dead metal zone formation and process of adhesion with the die wall leading to a higher ram load. Extrusion at die angles of 30, 45, 60, 75, and 90o show sharp rise at the beginning of the ram travel to a peak value and remain steady afterwards. The highest extrusion pressure is seen in 30o die extrudes (499 MPa) whereas that of 45o has the lowest extrusion pressure (403 MPa) with a low final ram travel (13mm). Experimental results of Onuh et al[7] on the variation of extrusion load with ram displacement of aluminium and lead show similar behaviour. Figure 5 shows the variation of extrusion pressure with ram displacement of wrought aluminium alloy cold extruded in mild steel tool dies. Extrusion in 15, 30, and 45o dies show similar behaviour. The extrusion pressure rose gradually with ram displacement initially (between 1 and 13 mm) but sharply afterwards. For extrusions done in 60, 75, and 90o dies, the pressure rises sharply at start of ram travel but gradually towards the end of the ram travel. A gradual rise in extrusion pressure indicates ease of extrusion within that region whereas sharp rise indicate a turbulent extrusion progression. At low die angles (15, 30, and 45o) there is ease of extrusion at the beginning of the extrusion process but turbulent extrusion at the end of the ram travel and vice versa for high die angles (60, 75, and 90o ). The highest extrusion pressure (543.9 MPa) occurs when extrusion was done in 75o die followed by that of 15o die (489.5 MPa) different from that done with tool steel die (see Figure 4). 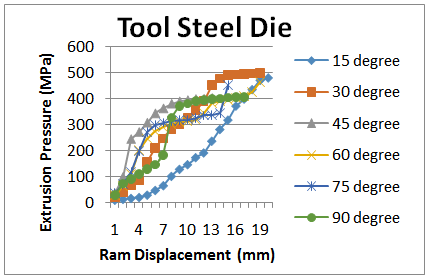 | Figure 4. Variation of Extrusion pressure with Ram displacement for cold extrusion in tool steel die |
 | Figure 5. Variation of Extrusion pressure with Ram displacement for cold extrusion in mild steel die |
Effect of die angle on hot extrusion characteristicsHot extruded samples show lower extrusion pressures and low final ram travels relative to that of cold extruded samples (see Figure 6 and 7). For extrusions with tool steel die (see Figure 6) all extrudes have the same behaviour except for that extruded in 15o die. The extrusion pressure rises steadily to a peak value (407.9 MPa) lower than others with a low final ram displacement of 12 mm. The highest extrusion pressure is seen in 60 o and 75 o (453.2 MPa) dies, however that in 75 o die show a preferred final ram displacement (17 mm). Extrusions with mild steel die show similar behaviour with that of tool steel die (see Figure 7). 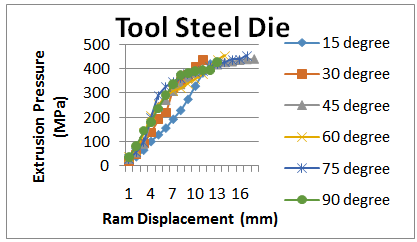 | Figure 6. Variation of Extrusion pressure with Ram displacement for hot extrusion in tool steel die |
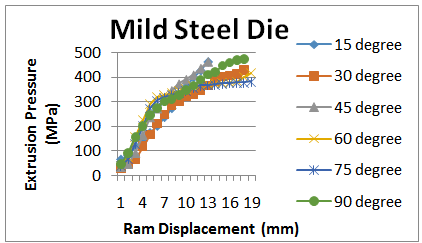 | Figure 7. Variation of Extrusion pressure with Ram displacement for hot extrusion in mild steel die |
Effect of die angle on annealed extrudesExtrusion of annealed samples using tool steel die show that extrusion proceeds with ease for all samples except for samples extruded in 15 o die (see Figure 8). Extrusion characteristics are the same for all these samples with maximum extrusion pressure attained for extrusion in 15 o tool steel die (527 MPa) and 90o mild steel die (496 MPa). Final ram displacements were low as compared to those of cold and hot extrudes and the maximum attained extrusion pressures were lower. In the case of mild steel die (see Figure 9), extrusions done at die angles of 15 o and 45 o show similar behaviour but different from others.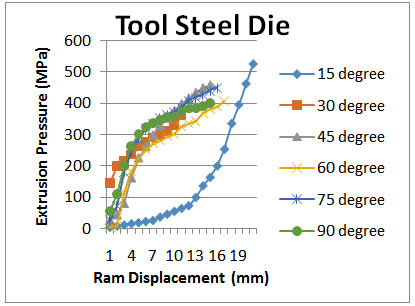 | Figure 8. Variation of Extrusion pressure with Ram displacement for annealed extrusion in tool steel die |
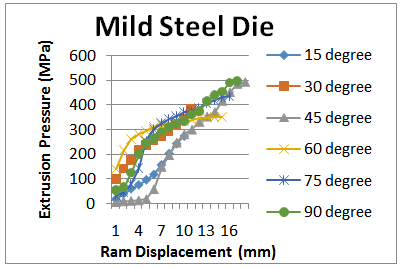 | Figure 9. Variation of Extrusion pressure with Ram displacement for annealed extrusion in mild steel die |
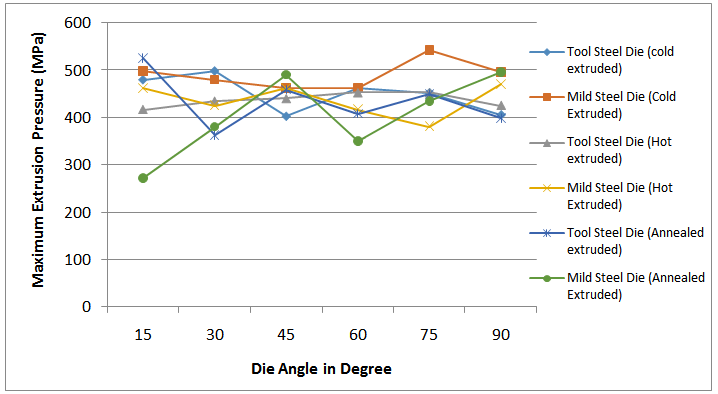 | Figure 10. Variation of Maximum Extrusion Pressure with Die Angle |
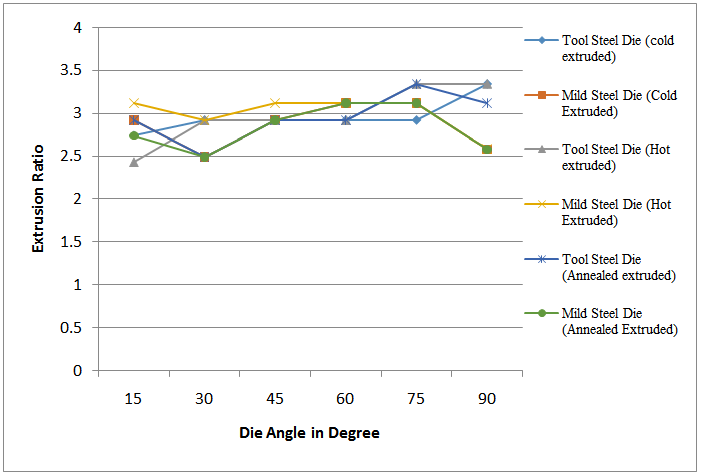 | Figure 11. Variation of Extrusion Ratio with Die Angle |
The variation of maximum extrusion pressure with die angles is shown in Figure 10. Reduce extrusion pressure occurred at 90o die angle, independent of the initial state of billet. This is consistent with the result of Onuh et al[7] study on the effect of die angle on the extrusion characteristics where extrusion pressure decreases to a minimum extrusion pressure at 90o die angle. Extrusion pressure at this die angle may be due to the least redundancy energy at this particular die angle. Low die angle means large surface area, leading to increased friction at die-billet interface resulting in larger ram force but at Large die angle there is small surface area leading to decreased friction at the die-billet interface resulting in lower ram force requirement.Effect of die angle on the extrusion ratioThe extrusion ratio of a shape is a clear indication of the amount of mechanical working that will occur as the shape is extruded. The effective strain is a function of the extrusion ratio while the extrusion pressure is a function of the strain. The variation of extrusion ratio with die angle is shown in Figure 11. Extrusion ratio for cold extrusion using tool steel die increased initially to 2.92 at 30o die angle and remains constant at 45, 60, 75o die angles but later increased to a maximum (3.34) at 90o die angle. Extrusion of hot and annealed billets using tool steel die show similar behaviour to that of as-cast extrudes. These indicate that large extrusion ratio corresponds to low extrusion pressure and high linear strain for tool steel die (see Figures 10 and 12). Extrusions using mild steel die show the same extrusion ratio (2.58) at 90o which is lower than those at other die angles. The lowest extrusion ratio (2.43) is shown by hot extrudes in 15o tool steel die. Extrusion pressures for mild steel 90o die are high (see Figure 10) compared to others which substantiates the fact that low extrusion ratio leads to lower linear strain and consequently high extrusion pressure. Effect of die angle and tool type on deformationFigure 12 shows the variation of linear strain with extrusion die angle for all the extrudes. Linear strain tends to increase with increase in die angle. The highest linear strain (202 %) was obtained for samples cold extruded using tool steel 90o die followed by annealed extruded (161 %) sample using tool steel in same die. Samples extruded with tool steel die have superior linear strain compared to that extruded with mild steel die. It is also observed that as-cast billet extrusion at ambient temperature favours high linear strain. This response is followed by annealed extruded but least in hot extruded. The maximum extrusion pressures (406, 426, 399 MPa for cold, annealed and hot extrudes respectively) at this die angle are lower than that of all other samples, showing that there is ease of flow of material at 90o die angle compared to other die angles used in this study (see Figures 4, 6 and 8). Effect of die angle and tool type on micro hardnessFigure 13 shows the hardness (HV) variation with die angle and type of tool material. It is evident that surface hardness of extrudes does not follow a well-defined trend but shows a zigzag variation with increase in die angle. The highest hardness (61.2 HV) occurs in cold extruded samples using 75o tool steel die. It is also clear that samples extruded with tool steel die exhibit superior hardness compared to those extruded in mild steel die. The lowest hardness value (37.3 HV) occurred in the sample extruded in mild steel die at 30o die angle. This result indicates that structural change due to severe plastic deformation during extrusion was effective for the improvement of hardness. | Figure 12. Variation of Linear Strain with Die Angle |
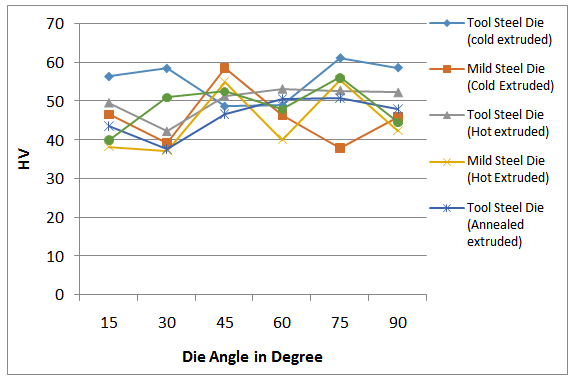 | Figure 13. Variation of Micro-Hardness of extrude with Die Angle |
4. Conclusions
In this experiment, the effect of die angle has been studied to determine the effect of die angle and tool material on the extrusion characteristics of wrought aluminium alloys using cold, hot and annealed billets. The following can be deduced from the study;1. Extrusion pressure is dependent on extrusion die angle, whereas extrusion at larger die angles (90o) produces higher extrusion pressure, extrusion at lower die angles produces less extrusion pressure2. Extrusion pressures are dependent on the tool material used. Extrusion with tool steel die exhibited superior properties to mild steel die.3. Linear strain show significant dependence on the extrusion die angle and die material. It is observed that cold billet extrusion favours high linear strain most followed by annealed extruded with hot extruded showing inferior strain in this regard. Linear strain as much as 200 % was recorded for some extruded samples in 90o tool steel die.4. Result of surface hardness of extruded alloy does not show a pre-defined trend but indicates that structural change due to severe plastic deformation during extrusion was effective for the improvement of hardness.5. Large extrusion ratio was found to correspond to low extrusion pressure and high linear strain for tool steel die.
References
[1] | Al-Qawabah S.M.A. 2011. “Experimental and FEM Investigation of ECAE on the Mechanical Properties, Extrusion Pressur and Microhardness of Pure Lead”, Research Journal of Applied Sciences, Engineering and Technology 3(4): 356-368, |
[2] | Goswami R.K, R.C. Anandani, R. Sikand, I.A. Malik and A.K. Gupta, 1999. “Effects of extrusion parameters on the mechanical properties of 2124 AlsiCp stir cast MMCs material”. Trans. JIM, 40: 254- 257. |
[3] | Pacanowski J., and J. Zasadzinski, 1998. “The effect of selected parameters of aluminum extrusion on temperature changes in the die system”, Arch. Metall., 43(4): 389-398. |
[4] | Fereshteh-Sanie F., M. Karimi, M. Sabzalipor 2009. “An Investigation On The Effects Of Process Variables On The Required Load In Axisymmetric Forward Rod Extrusion” Paper Ref: S2411_P0348 3rd International Conference on Integrity, Reliability and Failure, Porto/Portugal, 20-24 July 2009 -1 |
[5] | Kumar S. P., Vijay, 2007. “Die design and experiments for shaped extrusion under cold and hot condition”, Journal of Materials Processing Technology 190:375–381 |
[6] | Elkholy A.H, 1997. “Parametric optimisation of power in hydrostatic extrusion”, J. Mater. Process. Technol. 70:111–115 |
[7] | Onuh S.O., M. Ekoja, M.B. Adeyemi, 2003. Effects of die geometry and extrusion speed on the cold extrusion of aluminum and lead alloys, J. Mater. Process. Technol. 132:274–285. |
[8] | Altan, T. S. I. Oh, H. Gegel, 1983. “Metal Forming; Fundamentals and Applications”, American Society for Metals, Metals park, Ohio, |
[9] | Karhausen K. A., L. Dons, T. Aukrust, 1996. “Microstructure control during extrusion with respect to surface quality”, Mate. Sci. Forum 217-222: 403-408. |
[10] | Chaudhari G. A., S.R. Andhale, N.G. Patil 2012. “Experimental Evaluation of Effect of Die Angle on Hardness and Surface Finish of Cold Forward Extrusion of Aluminum”, International Journal of Emerging Technology and Advanced Engineering, 2(7):334 -338 |
[11] | Moore D. J. J. 2003. “Die Coating Dies. Rosemont: North American Die Casting Association”; |
[12] | Bjork T, Westergard R, Hogmark S. 2001. “Wear of surface treated dies for aluminium extrusion – a case study”, Wear 249:316-23 |
[13] | Budinski K. G. Budiskin M. K. 2002. “Engineering Materials: Properties and Selection”, 7th Edition ed. New Jersey: Prentice-Hall International, Inc; |
[14] | Akbar, A. A., Rabiha S. Yaseen, 2012. “Study of the Direct Extrusion Behavior of Aluminum and Aluminum Alloy-2014 Using Conical Dies”, Eng.&Tech. Journal, 30:950 - 958 |